Взвешенная плавка никелевого концентрата в Печи взвешенной плавки(ПВП)
Министерство образования Российской Федерации
Норильский индустриальный институт
Кафедра металлургии
Курсовая работа
по дисциплине: «Металлургия»
на тему:
«ВЗВЕШАННАЯ ПЛАВКА НИКЕЛЕВОГО КОНЦЕНТРАТА В ПЕЧИ ВЗВЕШАННОЙ ПЛАВКИ»
Выполнил: Бельтюков С.Н.
Проверил: Рогова Л.И.
Группа: Экм-99-У ВО Подпись: _______________
Шифр: 060800 Дата проверки:
Дата выполнения
Норильск, 2000г.
СОДЕРЖАНИЕ
Выбор технологии производства…………………………2
Описание основного агрегата……………………………..3
Физико-химические основы процесса……………………5
Технико-экономические показатели……………………..11
Металлургический расчет…………………………………12
Библиографический список
1. ВЫБОР ТЕХНОЛОГИИ ПРОИЗВОДСТВА
Плавка во взвешенном состоянии на подогретом дутье была осуществлена в промышленном масштабе финской фирмы «Оутокумпу» на заводе «Харьявалта». В первоначальном варианте для плавки применяли воздушное дутье, подогретое до 400—500 °С. Начиная с конца 60-х годов, этот процесс по лицензии фирмы «Оутокумпу» стали широко применять на металлургических заводах многих стран. В настоящее время он внедрен более чем на 30 предприятиях для переработки медных, никелевых и пиритных концентратов, в т.ч. на Надеждинском металлургическом заводе. Финскую плавку на сегодня можно считать самым распространенным в промышленности и наиболее технологически и аппаратурно отработанным автогенным процессом плавки сульфидных концентратов.
Особенностями взвешенной плавки являются:
- высокая производительность ( удельный проплав 10-15 т/м2 в сутки);
- низкий расход топлива - процесс плавки сульфидного концентрата протекает в режиме, близком к автогенному;
- возможность полного автоматического управления процессом плавки с помощью системы "Проскон-103'';
- возможность получения штейна требуемого состава;
- утилизация серы из высококонцентрированных серных газов.
Конструкция ПВП и комплекс других технических решений обеспечивают получение пара энергетических параметров и высокую степень утилизации серы из отходящих газов, что резко снижает выброс двуокиси серы в окружающую среду и значительно улучшают условия труда обслуживающего персонала.
В плавильном цехе НМЗ имеется две печи взвешенной плавки одинаковой конструкции для плавки медного и никелевых концентратов.
Передел взвешенной плавки - структурное подразделение плавильного цеха HMЗ.
2. ОПИСАНИЕ ОСНОВНОГО АГРЕГАТА
Конструкция печи для плавки во взвешенном состоянии на подогретом дутье достаточно сложна — она сочетает в себе две вертикальные шахты (реакционную и газоход-аптейк) и горизонтальную камеру-отстойник.
Тонкоизмельченная шихта, предварительно высушенная до содержания влаги менее 0,2%, подается по системе ленточных конвейеров и пневмотранспорта в бункер шихты. Из бункера шихта двумя скребковыми транспортерами "Редлер" подается через свод реакционной камеры с помощью четырех специальных горелок. Основное назначение горелки — приготовление и подготовка шихтововоздушной смеси для ускорения процесса горения сульфидов. Перемешивание шихты с дутьем достигается разбиванием струи шихты о конус-рассекатель и подачей дутья через воздушный патрубок и распределительную решетку.
Схема горелки печи завода
1 — дутье; 2 — шихтовая воронка; 3 — загрузочный патрубок;
4 — воздушный патрубок; 5 — конус-рассекатель;
6 — распределительная решетка; 7 — диффузор
Вся печь взвешенной плавки выполнена в виде кладки из магнезитового кирпича. Футеровка реакционной шахты и аптейка заключена в металлические кожухи из листовой стали. В кладку всех элементов печи заложено большое количество водоохлаждаемых
Печь для плавки во взвешенном состоянии
1 — горелка; 2 — реакционная камера; 3 — отстойная ванна; 4 — аптейк;
5 — котел-утилизатор; 6 — паровой воздухоподогреватель;
7 — топливный воздухоподогреватель
элементов, что позволяет значительно удлинить срок службы агрегата. Аптейк непосредственно сочленен с котлом-утилизатором туннельного типа. В боковой стене отстойной камеры установлены две медные водоохлаждаемые плиты с отверстиями для выпуска шлака, а в передней торцевой стене — чугунные шпуры для выпуска штейна.
Габариты печи определены на основании технологических расчетов произведенных с помощью ЭВМ, исходя из проектной производительности печи и других исходных параметров для проектирования.
В реакционной шахте, для окисления компонентов концентрата, используется воздух обогащенный кислородом и подогретый до 200°С. Согласно теплового баланса - степень обогащения дутья кислородом на ПВП никеля составляет 26% при среднем составе шихты, что позволяет реакционной шахте работать автогенно, без применения дополнительного топлива Оборудование рассчитано на максимальное обогащение кислородом до 40%, если по каким-либо причинам:
1. Теплопотребление шихты увеличится
2. Увеличатся тепловые потери печи;
3. Подогрев воздуха уменьшится.
Если обогащения дутья кислородом до 40% из-за вышеперечисленных факторов окажется недостаточным, то для восполнения недостатка тепла в реакционной шахте, используют природный газ.
Расплавленные частицы падают на поверхность ванны отстойника. В отстойной зоне печи происходит расслоение сульфидно-силикатного расплава на шлак и штейн. Для поддержания заданной температуры шлака и штейна в отстойной зоне смонтировано 18 горелок природного газа. При выходе из реакционной шахты направление движения газов изменяется на 90° - газовый поток проходит горизонтально над ванной в отстойной зоне печи. Затем направление движения газа вновь изменяется на 90° - газ поднимается по вертикальному аптейку печи вверх. В аптейк инжектируется угольная пыль, где и происходит восстановление сернистого газа до элементарной серы. Благодаря такой конструкции печи происходит достаточно полное отделение сульфидно-силикатных частиц, находящихся во взвешенном состоянии, от газового потока.
Пылевынос из печи взвешенной плавки составляет 12-15% от веса загружаемой шихты.
После аптейка газы поступают в котел-утилизатор, где охлаждаются с 1350°С до 550°С, а затем после очистки в электрофильтрах от пыли, поступают в серный цех для улавливания из газов элементарной серы.
Печь взвешенной плавки является головным агрегатом в цепи переработки серосульфидных концентратов. Агрегат обладает высокой интенсивностью плавления. В связи с этим печь имеет сложную и многообразную систему охлаждения.
Агрегат должен обладать высокой герметичностью. Нарушение герметичности ведет к подсосам, что нарушает тепловой баланс печи, разубоживает отходящие газы и увеличивает их объемы, увеличивает расход восстановителя. Вышеперечисленные причины отрицательно сказываются не дальнейшей обработке газов в серном цехе,
Все три части печи взвешенной плавки должны иметь высокую герметичность, требуют жесткого поддержания заданных параметров, что обеспечивается работой печи в автоматическом режиме с помощью ЭВМ.
3. ФИЗИКО-ХИМИЧЕСКИЕ ОСНОВЫ ПРОЦЕССА
Процесс плавки сульфидных концентратов с утилизацией серы из отходящих газов очень сложен, поэтому на производительность печи, полноту протекания окислительных и восстановительных реакций влияют многие факторы, основными из них являются;
- размеры частиц и время нахождения частиц в газовом потоке;
- время нагрева частиц;
- скорость, направление и последовательность окислительных реакций, влияние температуры на конечное химическое равновесие;
- минералогический состав концентратов;
- вид восстановителя сернистого ангидрида и влияние температуры на конечное равновесное состояние восстановительных реакций.
Размеры частиц и величина удельной поверхности компонентов шихтовых материалов
Обычно руды измельчают перед флотацией в пределах нижнего класса крупностью от 60% класса - 0,0605 мм до 90% класса -0,088мм. Средней величиной зерна флотационных концентратов можно считать от 0,07мм до 0,03мм.
Процессы нагревания сульфидных частиц, диссоциации высших сульфидов и взаимодействия сульфидов с кислородом печной атмосферы в ходе взвешенной плавки являются типичными гетерогенными процессами, скорость которых при прочих, равных условиях линейно зависит от величины поверхности раздела на границе твердое - газ.
Произведя несложный расчет, можно убедиться что 1 кг материала с удельным весом 4 г/см3 при среднем диаметре зерна 0,04мм, что соответствует размеру зерен флотационных концентратов., имеет удельную поверхность 59,5 м2/кг, Будучи взятым в виде компактного шара, тот же I кг материала имеет поверхность всего 0,019 м2. Таким образом, измельчение материала влечет за собой резкое увеличение его удельной поверхности, Однако, излишнее переизмельчение шихтовых материалов нежелательно, так как в этом случае возрастает пылеунос,
Движение частиц в газовом потоке.
Очень важным параметром процесса плавки во взвешенном состоянии является время пребывания шихтовых частиц в потоке от момента поступления в пространство реакционной шахты до соударении с поверхностью расплава в отстойной зоне печи.
Поскольку и газы, и частицы шихты движутся в одной направлении сверху вниз, очевидно, что время пребывания шихтовых частиц в полете определится суммой скоростей свободного падения частицы и движения газового поток. В условиях плавки сульфидных флотационных концентратов скорость собственного падения самых крупных зерен концентрата не превышает I м/сек. Сульфидные частицы, вдуваемые в реакционную шахту, незначительно опережают газовый поток и время, необходимое для прохождения частиц концентрата по всей высоте плавильной шахты, равно 0,8 - 0.9 времени прохождения газом этого же пути, И если газ проходит шахту печи за 2,8 сек., то частицы флотационного концентрата будут находиться во взвешенном состоянии примерно 2,20 – 2,50 сек.
Нагрев пылевых частиц и теплопередача
В начальной стадии загрузки шихты в реакционную шахту, шихта подогревается за счет тепла, получаемого ею при конвективном теплообмене с подогретым до 200 С технологическим воздухом. Воспринимаемый частицей тепловой поток описывается уравнением .
Q= x S x (T1-T2)
- коэф-т передачи тепла конвекцией, ккал/м2/час
S – воспринимающая тепловой поток поверхность, м2
- время, час
Тепла этого явно недостаточно для воспламенения сульфидного материала, т.к. даже сера в зависимости от содержания кислорода в газовой фазе воспламеняется в интервале температур от 260 до 360 °C. Сульфидные же частицы в зависимости от размера зерен воспламеняются при температурах от 280 до 740 С.
Опускаясь ниже, распыленная шихта попадает в зону высоких температур, где она за счет излучения от факела или футеровки реакционной шахты нагревается до температур воспламенения сульфидов.
Количество передаваемого тепла за счет радиационного нагрева описывается уравнением Стефана-Больцмана:
Q= S x K x x (T1/100)4-(T2/100)4
Тепло, полученное поверхностью частицы, передается к ее центру, Передаче тепла в глубь частицы, даже если она и очень мала, осуществляется за счет теплопроводности и для случая шаровидной частицы подчиняется уравнению:
qx = Q/(4Пх2 х t)= (Тп-Тх)/r2(1/x-1/r)
Из уравнения следует, что удельный тепловой поток к центру частицы обратно пропорционален квадрату радиуса ее. Это означает, что при малых размерах частиц, которые имеют зерна флотационных концентратов, нагрев материала будет проходить в доли секунды.
Реакции окисления сульфидов протекают со значительным выделением тепла. Так как для окисления сульфида необходим подвод кислорода в зону реакции, тo становится понятным, что эти процессы могут протекать только на поверхности зерен. Из этого следует, что на некотором отрезке времени, начиная с момента воспламенения, от поверхности сульфидной частицы возникает дополнительный тепловой поток в глубь сульфидного зерна.
При воспламенении сульфидной частицы температура ее поверхности скачкообразно возрастает достигая в малые доли секунды 1500-1700°С. Процесс окисления сульфидов приобретает наивысшую скорость, так как в этот момент поверхность зерен максимальна, содержание кислорода в газах еще высокое и окисная пленка на поверхности сульфидного зерна только что зарождается. Средняя температура факела в этой зоне резко повышается до 1400°С и более за счет тепла, выделяющегося при интенсивном окислении всей массы сульфидных зерен. В зоне максимальных температур выделяется основная часть тепла экзотермических реакций плавки, т.к. именно здесь протекают с максимальными скоростями большинство реакций.
В последней зоне, называемой зоной усреднения температур, скорости всех окислительных процессов быстро падают, так как, во-первых, падает содержание кислорода в газовом потоке и, во-вторых, на поверхности окисляющихся сульфидных зерен нарастает пленка продуктов реакции, тормозящая диффузию кислорода в глубь зерна. Если на поверхности частицы образуется плотная корка твердого окисла, лишенная трещин и прочих дефектов, то диффузия кислорода через нее будет чрезвычайно затруднена и процесс окисления может прекратиться, не дойдя до конца. Рыхлые, трещиноватые пленки тормозят процесс в меньшей степени, так же, как и жидкие окисные пленки, скорость диффузии через которые примерно на три порядке выше, чем через твердую пленку. В целом процесс окисления в реакционной шахте печи лимитируется диффузией кислорода через пленки продуктов реакции и обратной диффузией -сернистого ангидрида в ядро газового потока.
В устье реакционной шахты окислительные реакции полностью заканчиваются. Об этом свидетельствуют результаты анализа газа на содержание свободного кислорода: парциальное давление кислорода на выходе из реакционной шахты снижается до 10 мм рт.ст.
Диссоциация сульфидов при плавке во взвешенном состоянии
В составе концентратов присутствуют высшие сульфиды, которые диссоциируют при нагревании на низшие сульфиды и серу. Ниже приведены реакции диссоциации.
FeS2FeS+S
Fe11S1211FeS+S
Fe7S87FeS+S
3NiFeS23FeS+Ni3S2+1/2S2
2CuFeS2Cu2S+2FeS+S
2CuSCu2S+S
3NiSNi3S2+S
2CuFe2S3Cu2S+4FeS+S
2Cu5FeS45Cu5S+2FeS+S
В интервале температур от 550 С до 650 С первым диссоциирует пирит, давление диссоциации которого при 631°С до 0,1 атм. Наиболее устойчив борнит, диссоциирующий в температур 8400-850°С. Все реакции идут с поглощением тепла. Отщепляющаяся сера воспламеняется, в зависимости от содержания кислорода в дутье, в интервале температур 280 С-560 С.
Конечными продуктами диссоциации высших сульфидов во всех случаях являются низшие сульфиды которые в дальнейшем частично окисляются, образуя окислы соответствующих металлов переходящие в шлак.
1/2S2+O2=SO2 (без катализатора)
1/2S2+3/2O2=SO3 (с катализатором)
Ni3S2+7/2O2=3NiO+2SO2
Cu2S+1,5O2=Cu2O+SO2
FeS+1,5O2=FeO+SO2
3FeS+5O2=Fe3O4+3SO2
Неокислившиеся низшие сульфиды переходят в штейн. Окисление сульфидов сопровождается образованием больших количеств магнетита, особенно в поверхностных слоях частиц. Переокисление железа до магнетита зависит также от степени десульфуризации при плавке. С возрастанием степени десульфуризации и получением более богатых штейнов все большая часть железа переводится в форму магнетита.
К числу важнейших элементарных стадий, протекающих в отстойной камере печи, относятся:
1) сульфидирование образовавшихся в факеле оксидов ценных металлов;
2) растворение тугоплавких составляющих (CaO, Si02, AI2О3, и MgO и др.) в первичных железистых шлаках и формирование шлака конечного состава;
3) восстановление магнетита сульфидами;
4) формирование штейна конечного состава и укрупнение мелких сульфидных частиц;
5) разделение штейна и шлака.
9NiO+7FeS=3Ni3S2+7FeO+SO2
Cu2O+FeS=Cu2S+FeO
Образование фаялита
2FeO+SiO2=(FeO)2SiO2
Разложение магнетита
3Fe3O4+FeS+5SiO2=5(FeO)2xSiO2+SO2
Плавкость сульфидов
В сравнении с окислами сульфиды являются более легкоплавкими соединениями. Температуры плавления основных сульфидов, входящих в состав медных и никелевых штейнов:
Сульфид железа 1171 С
Халькозин – 1135 С
Сульфид кобальта – 1140 С
Хизлевудит – 788 С
Эвтектические сплавы, образованные двумя различными сульфидами, а так же эвтектики между сульфидом и его металлом более легкоплавки, чем отдельные компоненты.
Штейны при плавке сульфидных компонентов всегда является многокомпонентными системами. Составы штейнов не всегда отвечают составам эвтектик, но тем не менее, температуры плавления штейнов все же ниже, чем температуры плавления входящих в них сульфидов. Обычно при температуре 850-900°С штейны находятся в жидкотекучем состоянии,
Термодинамика окислительных реакций при плавке во взвешенном состоянии
В общем виде основную реакцию, протекающую в реакционной шахте печи, можно представить следующим уравнением:
MeS+1,5О2= MeO+SO2+Q
Эта реакция экзотермическая и ее тепловой эффект во многих случаях, при условии нагрева материала до температуры воспламенения, обеспечивает самопроизвольный ход процесс без затрат тепла извне.
Об интенсивности протекания той или иной реакции принято судить по величине измерения изобарно-изотермического потенциала системы, которая выражает энергетические превращения в ходе химического процесса. При всех самопроизвольных процессах величина Z имеет отрицательный знак, что говорит о высвобождении энергии и отдаче ее системой на сторону, В этом случае мы наблюдаем выделение тепла в ходе реакции. Чем больше числовое значение Z при отрицательном знаке, тем энергичнее и глубже протекает реакция. Таким образом, сравнивая между собой величиныZ отдельных реакций, можно определить преимущественность протекания одной реакции по сравнению о другой. При положительном значении реакция не может протекать самопроизвольно, так как для ее совершения необходимы энергетические поступления извне,
Величина изменения изобарно-изотермического потенциала
Z позволяет определить величину константы равновесия реакции, которая характеризует конечное состояние системы, когда в ней завершился самопроизвольный процесс и установилось равновесие между исходными и конечными составляющими реакции. Эта связь выражается уравнением:
Lq Kкр=-Z/RT
По величине константы равновесия можно судить о направлении и глубине протекания процесса.
Восстановление технологических газов угольной пылью.
Технологические газы плавки во взвешенном состоянии до восстановления имеют следующий состав:
SO2 – 12,6; H2O- 8,5; СО2- 5,5, O2- 0,7; N2- 72%; t= 1450°
Процесс восстановления сернистых газов осуществляется в аптейке печи взвешенной плавки. В качестве восстановительного реагента используют измельченный уголь с минимальным содержанием летучих компонентов и золы. Так как летучие компоненты представлены углеводами, то их участие в процессе восстановления технологических газов, ведущих к образованию повышенных количеств H2S, CS2 и COS, нежелательны. Повышенное содержание золы в угле приводит к увеличению количества пыли и шлака, а, следовательно, снижает извлечение цветных металлов и увеличивает энергозатраты. К тому же зола угля является основной причиной образования настылей в аптейке.
По расчетным данным пылевынос печи взвешенной плавки составляет 12-15% от количества загружаемой шихты, где на долю золы приходится значительная часть. Так как вся пыль улавливается и возвращается в процесс, то увеличение зольности угля ведет к пропорциональному увеличению оборотной пыли.
Зола различных углей обладает различной температурой плавления. При температуре 1350°С зола находится в полурасплавленном состоянии, и при выходе из аптейка на границе радиационной части котла-утилизатора при соударении со стенками, будет налипать на поверхность футеровки (горловины) и образовывать настыли. При удалении настылей тем или иным способом, будь то обдув паром высокого давления или воздухом, также не исключена возможность применения буровзрывных работ, а это связано о открыванием смотровых люков, отверстий, что в свою очередь может привести к расстройству процесса и вынужденным остановкам печи.
Углерод и летучие компоненты угольной пыли взаимодействуют с сернистым ангидридом, восстанавливая его до элементарной серы.
Восстановление протекает в общей форме по уравнениям:
SO2+C=1/2S2+ CO2
SO2 +2Н2=1/2S2+2H2O
При этом имеют место побочные реакции, что значительно снижает извлечение серы.
При взаимодействии сернистого ангидрида с пылеуглем в интервале температур 1300-700°С доля образующихся компонентов H2S, CO, COS довольно высокая. Степень восстановления сернистого ангидрида в элементарную серу обычно не превышает 20-25%, т.к. основная масса угля расходуется на образование побочных продуктов.
Когда в газовой фазе присутствуют водородные соединения, в том числе и вода., количество нежелательных реакций увеличивается, что приводит к снижению содержания элементарной серы в газовой фазе.
В результате восстановления получается многокомпонентный газ, и, с практической точки зрения, особую важность в этом составе представляет сернистый ангидрид и элементарная сера. Восстановленный газ из аптейка ПВП с температурой 1330°С поступает в котел-утилизатор. В котле-утилизаторе газ охлаждается до температуры 350°С. При этой температуре СО и COS почти отсутствуют, а содержание элементарной серы почти достигает максимума.
При охлаждении газа в котле-утилизаторе протекают основные реакции:
CO+1/2 S2 = COS
COS+H2O=CO2+H2S
H2+1/2S2=H2S
Из представленных реакций первая реакция протекает быстро, а следующая реакция очень медленно и для полного протекания реакции необходим катализ.
При температуре 1330°С в аптейке ПВП наступает термодинамическое равновесие между компонентами упомянутыми выше.
Кроме восстановления газа в аптейке ПВП происходит восстановление окислов пыли.
В общем виде реакцию восстановления компонентов пыли можно представить уравнением:
4МеО + 3S2 4МеS + 2 SO2
Этот процесс идет с поглощением тепла, что снижает температуру отходящих газов,
Восстановленная оборотная пыль содержит в себе следующие соединения: NiS, CuS, FeS, CoS, ZnS, PbS, As2S2, Cu2Se, SiO2, Аl2O3, CaO, MqO, прочие и свободный углерод.
При сравнении компонентов окисленной и восстановленной пылей видно, что в процессе восстановления происходит поглощение серы и выделение свободного кислорода для связывания которого требуется дополнительная затрата углерода. Следовательно, можно сделать вывод, что снижение пылевыноса в процессе плавки выгодно как с экономической точки зрения по расходу угля, так и с точки зрения снижения безвозвратных потерь цветных металлов.
4. ТЕХНИКО-ЭКОНОМИЧЕСКИЕ ПОКАЗАТЕЛИ ПРОЦЕССА
-
Показатель
Значение
Производительность печи, т/сут
445,44
Удельный проплав, т/(м2 х сут)
10-15
Содержание О2 в дутье, %
26
Температура дутья, С
25-40
Содержание Ni, %:
В штейне
34,9
В шлаке
1,4
Пылеунос, %
10-15
5. Металлургический расчёт.
Исходные данные для расчёта: содержание Ni в концентрате – 8 %;
cодержание Сu в концентрате – 4 %;
Расчёт производим на 100 кг концентрата.
Химический состав концентрата:
Cu – 4 %; Ni – 8 %; Fe – 46 %; S – 30 %; SiO2 – 3,5 %; CaO – 2,3 % ; MgO – 2 %; Al2O3 – 1,38 %; прочие – 2,82 %.
По минералогическому составу ориентировочно 60% меди находится в кубаните, 40% в халькопирите, никель находится в пентландите
Состав концентрата.
Таблица №1
Комп.
Cu
Ni
Fe
S
Оксиды
Прочие
Общ. мас.
Si
Ca
Mg
Al
NiFeS2
8,00
7,60
8,72
24,33
CuFeS2
1,60
1,40
1,61
4,61
CuFe2S3
2,40
4,21
3,62
10,23
Fe11S12
32,78
16,04
48,83
SiO2
3,50
3,50
CaO
2,30
2,30
MgO
2,00
2,00
Al2O3
1,38
1,38
Прочие
2,82
2,82
%
4,00
8,00
46,00
30,00
3,50
2,30
2,00
1,38
2,82
100,00
NiFeS2
58,7 Ni – 178,5NiFeS2 X= 24,33 (кг)
8 Ni – X NiFeS2
55,8 Fe - 178,5NiFeS2 X = 7.6 (кг Fe)
X Fe – 24,33 NiFeS2
64 S - 178,5 NiFeS2 X=8,73 (кг S)
X S - 24.33 NiFeS2
Проверка: 8,73+7,6+8=24,33
CuFeS2
63.6 Cu – 183.4 CuFeS2 X= 4.61 (кгСu)
1,6 Cu – X CuFeS2
55.8 Fe – 183.4 CuFeS2 X= 1.4 (кгFe)
X Fe – 4.61 CuFeS2
64 S – 183.4 CuFeS2 X= 1.61 (кг S)
X S - 4.61 CuFeS2
Проверка: 1,6+1,4+1,61=4,61
CuFe2S3
63,6 Cu – 271.2 CuFe2S3 X= 10.23 (кг)
2.4 Cu – X CuFe2S3
111.6 Fe – 271.2 CuFe2S3 X= 4.21 (кг)
X Fe – 10.23 CuFe2S3
96 S - 271.2 CuFe2S3 X= 3.62 (кг)
X S – 10.23 CuFe2S3
Проверка: 3,62+4,21+2,4=10,23
Fe11S12
Fe= 46-7.6-1.4-4.21=32.78
S = 30-8.72-1.4-4.21=16.04
Fe11S12 = 32.78+ 16.04= 48. 83 кг
Химический состав оборотной пыли ПВП:
Cu – 2,3%; Ni – 5,2 %; Fe – 26 %; S – 18,5 %; SiO2 – 24,5 %;
CaO – 2,6 % ; MgO – 2,1 %; Al2O3 – 2,3%; прочие – 16,5 %.
Учитывая, что шихта состоит на 85% из концентрата и на 15% из оборотной пыли, то рассчитываем химический состав шихты:
m (Cu) = 4*0,85 + 2,3*0,15 = 3,75 (кг);
m (Ni) = 8*0,85 + 5,2*0,15 = 7,58 (кг);
m (Fe) = 46,0*0,85 + 26*0,15 = 43 (кг);
m (S) = 30*0,85 + 18,5*0,15 = 28,28 (кг);
m (SiO2) = 3,5*0,85 + 24,5*0,15 = 6,65 (кг);
m (CaO) = 2,3*0,85 + 2,6*0,15 = 2,35 (кг);
m (MgO) = 2*0,85 + 2,1*0,15 = 2,02 (кг);
m (Al2O3) = 1,38*0,85 + 2,3*0,15 = 1,52 (кг);
m (проч.) = 2,82*0,85 + 16,5*0,15 = 4,87 (кг);
Химический состав шихты.
Таблица №2
Комп.
Cu
Ni
Fe
S
Оксиды
Прочие
Общ. мас.
Si
Ca
Mg
Al
Конц-т
4
8
46
30
3,5
2,3
2
1,38
2,82
100
Обор. Пыль
2,3
5,2
26
18,5
24,5
2,6
2,1
2,3
16,5
100
Шихта
3,75
7,58
43,00
28,28
6,65
2,35
2,02
1,52
4,87
100
Предварительный расчёт по выходу штейна.
Извлечение в штейн из шихты :
Cu – 91%
Ni – 91 %
Всего в штейн перейдет :
Cu 3,75х0,91= 3,41
Ni 7,58х0,91= 6,9
Вес штейна на 100 кг концентрата при 50 % содержании металлов :
(3,41+6,9)х0,5= 20,61
По данным Б.П. Недведецкого, в штейнах с 50% металла содержится 2% О2 и 23,7% S
В этом случае содержание железа в штейне составит:
Fe: 100-(50+2+23,7)= 24,3%
Предварительный состав штейна.
Таблица № 3
-
Хим. Сост.
Масса кг.
%
Ni
6,9
33,48
Cu
3,41
16,55
S
4,88
23,7
O2
0,41
2
Fe
5,01
24,3
Итого
20,61
100
Перейдет в шлак железа: 43-5,01=37,99 кг
Флюсы:
Для получения кондиционных отвальных шлаков и в связи с высоким содержанием Fe в исходном сырье в шихту вводятся флюсующие присадки. Основным флюсующим компонентом в шихте служит песчаник.
Примем следующий состав песчаника:
SiO2 – 80 %, MgO – 1,5%, Al2O3 – 8,7%
CaO – 1,3 %, FeO – 2,5%,
Расчет ведем на получение шлака, содержащего 30% SiO2.
Примем, что Х – общая масса шлака, кг; У – масса загружаемого песчаника, кг. Составляющие песчаника переходят в шлак целиком. Тогда общая масса шлака будет, кг:
Х=У+37,99х71,85/55,85+5,88+6,65= У+61,4
37,99х71,85/55,85 – количество FeO, образовавшаяся из железа концентрата, перешедшего в шлак.
6,65 – количество SiO2 в концентрате
5,88 – количество CaO, MgO, Al2O3
Второе уравнение получаем из баланса:
0,30 Х=6,65+0,8У
Решая систему уравнений получаем:
У=23,54 (песчаник) Х = 84,94 (шлак)
Результат проверяем подсчетом количества и состава шлака:
FeO
48,87+23,54х0,025=49,46
58,23
SiO2
6,65+23,54х0,8=25,48
30,00
Al2O3
1,52+23,54*,087=3,57
4,19
CaO
2,35+23,54х0,013=2,66
3,12
MgO
2,02+23,54х0,015=2,37
2,79
Прочие
1,42
1,67
Итого
84,94
100
Для расчета состава и количества отходящих газов примем, что весь кислород, необходимый для осуществления реакций, поступает с подогретым дутьем. При этом необходимо учитывать, что на практике имеются неорганизованные подсосы холодного воздуха, количество которого может колебаться от 2% до 6%.
Влажность шихты 0,2%, следовательно в печь поступит ее
(100+23,54)х0,002=0,25 кг
С учетом содержания серы в штейне и шлаке ее перейдет в газы:
28,28 – 4,88- 0,67=22,73 кг
32S-64 SO2
22,73 S - X SO2, что составляет 45,46 кг SO2
На окисление железа, переходящего в шлак, расход кислорода составит 48,87-37,99=10,88кг
Общая потребность кислорода на плавку 100 кг концентрата будет, кг:
На окисление серы – 22,73
На окисление железа – 10,88
Переходит в штейн – 0,41
Итого:34,02 кг
Вместе с кислородом в печь поступит азота
34,02/0,23 х 0,77=113,8 кг
Из практики работы известно, что со шлаком теряется: Cu – 2%, Ni – 4,5%
Cu= 3,75 x 0,02= 0,075
Ni= 7,58 x 0,045=0,34
S в шлак = 28,28- (4,88+22,73)=0,67
В технические газы отходит:
Cu: 3,75-(3,41+0,08)= 0,26
Ni: 7,58-(6,9+0,34)=0,34
Статьи баланса
Всего
В том числе
Cu
Ni
Fe
S
SiO2
CaO
MgO
Al2O3
O2
N2
H2O
прочие
Загружено:
Шихты
100,22
3,75
7,58
43,00
28,28
6,65
2,35
2,02
1,52
-
-
0,20
4,87
Песчаника
21,59
18,83
0,31
0,35
2,05
-
-
0,05
Воздуха
147,82
34,02
113,80
Всего:
269,63
3,75
7,58
43,00
28,28
25,48
2,66
2,37
3,57
34,02
113,80
0,25
4,87
Получено:
Штейна
20,61
3,41
6,90
5,01
4,88
-
-
-
-
0,41
-
Шлаков
88,91
0,08
0,34
37,99
0,67
25,48
2,66
2,37
3,57
10,88
4,87
Технические газы
160,11
0,26
0,34
22,73
22,73
113,80
0,25
Всего:
269,63
3,75
7,58
43,00
28,28
25,48
2,66
2,37
3,57
34,02
113,80
0,25
4,87
Материальный баланс плавки концентрата в печи
Взвешенной Плавки никелевой линии
Библиографический список.
И.А.Стригин и др. «Основы металлургии»,т.1 Общие вопросы
Металлургии, Москва, Металлургия, 1975г.
И.А.Стригин и др. «Основы металлургии»,т.2 Тяжелые металлы, Москва, Металлургия, 1975г.
И.А.Стригин и др. «Основы металлургии»,т.7 Технологическое оборудование предприятий цветной металлургиии, Москва, Металлургия, 1975г.
Н.В.Гудима “Технологические расчёты в металлургии тяжёлых цветных металлов», Москва, Металлургия, 1977г.
Ф.М.Лоскутов, А.А.Цейдлер «Расчёты по металлургии тяжёлых цветных металлов», Москва, Металлургиздат, 1963г.
Технологическая инструкция №0401-3.1.109-34-80
А.В. Ванюков, Н.И. Уткин «Комплексная переработка медного и никелевого сырья», Челябинск, Металлургия,1988г.
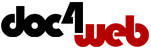
Нравится материал? Поддержи автора!
Ещё документы из категории металлургия :
Чтобы скачать документ, порекомендуйте, пожалуйста, его своим друзьям в любой соц. сети.
После чего кнопка «СКАЧАТЬ» станет доступной!
Кнопочки находятся чуть ниже. Спасибо!
Кнопки:
Скачать документ