работа по дисциплине «котельные установки»











































АНОО «Нижегородский колледж теплоснабжения и автоматических систем управления»
Курсовая работа
по дисциплине «котельные установки»
тема: «Проект производственно-отопительной котельной в г.Уфа»
Выполнил: студент 4 курса
Гр. Т-4Б
Челышев Д.В.
Руководитель:
Бабичева Л.А.
Нижний Новгород
2008
Введение
В курсовом проекте рассматривается котельная установка с паровыми котлами, которые предназначены для выработки пара по теплоснабжению района. Данный расход пара покрывает нагрузки О и В и технологические нагрузки. Система теплоснабжения района - закрытая с параметрами теплоносителя τ1/ τ2=150/170. В закрытой системе теплоснабжения предусмотрен теплофикационный подогрев (подогрев сетевой воды) в котором вода из обратной магистрали тепловых сетей с температурой 70оС нагревается до 100оС и подается потребителю. Таким образом, в тепловых сетях не используется химически очищенная вода. Сетевая вода готовится в отдельных установках. Эта система подготовки воды в тепловой схеме не указана.
Работа тепловой схемы
Исходная вода подается подпиточными насосами сначала в водоводяной подогреватель, где подогревается конденсатом и из СНП от температура исходной воды зимой+5,и +15летом,затем поступает в пароводяной подогреватель, где подогревается исходная вода до температуры не выше 40оС. Из условия предотвращения конденсации водяных паров на оборудование химводоочистки. Вода в химводоочистке освобождается от солей накипи (Mg и CO). Затем поступает в деаэратор атмосферного типа, где освобождается от свободного кислорода и двуокиси углерода, которые способствуют процессам коррозии оборудования. Из деаэратора питательная вода подается в экономайзер парогенератора в 2 котла (Е 6.5-14) подключенных питательной линией параллельно. В барабане котла образуется насыщенный пар с параметрами: Рн= tн= . Свежий пар после котельных установок поступает через редукционноохладительную установку (РОУ), подается к потребителю технологической нагрузки с давлением Р=0.7 мПа в количестве 5.4 т/ч. Из той же линии свежий пар поступает в теплофикационный подогреватель для подогрева сетевой воды. Из барабана котла постоянно осуществляется продувка через СНП. Дренаж после сепаратора поступает в продувочные колодцы. После всех подогревателей осуществляется отвод конденсата. Конденсат после конденсатосборщиков возвращается в сборные конденсатные баки, затем могут быть использованы в подогревателях котельной и поступают через головку деаэратора в блок аккумулятор деаэратора.
1
Расчет тепловой схемы котельной
1.1Определение производительности котельной установки.
Dв.н=Dтех+Dов+Dгвс; т/ч, где:
Dтех- дано-4 т/ч
Dов=Qов*103 /(h”-Ср*tк)*η; Qов- дано- 7 ГДж/ч
Dов=Qов*103 /(h”-Ср*tк)*η=7000/2790-4.19*90)*0.98=2,8 т/ч
При Р=1,4 h”=2790 кдж/кг – теплосодержание насыщенного пара, Рн = 0,14 МПа
h”-теплосодержание пара идущего на теплофикацию- 2790 кдж/кг
Ср*tк= h’ Ср=4.19 кДж/кг tк=100о C
η=КПД- 0.98
Dгвс= Qгвс*103/(h”-Ср*tк)*η=6000/(2790-4.19*90)*0.98=2.4 т/ч
Dз=Dтех+Dов+Dгвс=7+2.8+2.4=12.2 т/ч
Dл=Dз-Dов=3.2+2.58=5.78 т/ч
Dвп=11 т/ч – внешн. потреб.
Потери внутри котельной:
Dпотерь=12.2*0.02=0.24 т/ч
Dmax=Dвып+Dпотерь=11+0.24=11.24 т/ч
n=Dmax/Dку=14.27/4=4 котла (зимний период)
Dmin= Dmax-Dов=14.27-2.8=11.47
n=10.18/4=3 котла (летний период)
1.2 Расход питательной и продувочной воды.
Gпит=Dку+Gпр Gпр=(Р*Dку)/100
Gпр-расход продувочной воды, принимаем согласно СНИП «Котельные установки»- 10%
Gпр=0.1*17.36=1.4 т/ч
Gпит=14.27+1.4=15.6 т/ч
1.3 Определение расхода пара и воды на сепаратор непрерывной продувки.
Х=0.98
Dc=(Gпр*(h”1.4-h’0.15))/(X*(h”0.15-h’0.15))*n=1.5(814.5-462.2)/2227.93=
=493.22/2227.93=0.22 т/ч
G’пр=Gпр-Dc=1.4-0.22=1.18 т/ч
1.4 Определение производительности ХВО и деаэратора.
Gпк=(Dтех*(100- М))/100=(4*30)/100=2.8 т/ч
µ-% возврата конденсата
G’пр- 1.4 т/ч
Gподп=0.75%- от общего объема воды в тепловых сетях
Gподп=0.75%*Vc
Vc=gc*(Qов+Qгвс)
gc- удельный объем воды в систему на единицу мощности- 65 м3/мВт с учетом того что 103*1мВт=гДж, то:
Vc=65*(7+6)/3.6=234.7
Gподп=0.0075*234.7=1.7 т/ч
Gg=Gпит+Gподп=15.6+1.7=17.3 т/ч
Dвып=0/003* Gg=0.005*17.3= 0.08 т/ч
Gхво=Gпк+ G’пр+ Gподп+Dпот+Dвып=2.8+1.18+1.7+0.24+0.08=6 т/ч
1.5 Определение расхода пара на подогреватели (водяной и пароводяной)перед ХВО.
1.Тепловой баланс водоводяного подогревателя
Gив*c*(t'ив-tив)= G’пр*c(t'пр-t''пр)η
с=4.19 кДж/кго G’пр- 1.4 т/ч tив=5оС t’ив=X
t'пр=h’0.15/4.19=467.2/4.19=111.5оС t''пр=60оС
Gив=(1.1/1.15) Gхво=1.1*15.6=17 т/ч
t’ив=( G’пр*с*(t'пр-t''пр)/ Gив*с)+ tив=(1.25*4.19*(110-60)/20.9*4.19)+5=8.2оС
t’ив=11.7оС
2.Тепловой баланс пароводяного подогревателя
Gив*с(t’’ив-t’ив)=D(h’’0.7-ctк)η
t’’ив=40оС t’ив-Х
D=( Gив*c(t’’ив-t’ив))/ (h’’0.7-ctк)η=(20.9*4.19(40-8.2))/(2764-4.19*90)*0.98=
=2539/2339.2=0.36 т\ч
D=0.36 т/ч
1.6 Определение расхода на деаэрацию
(Dов+Dгвс)*с*tк+ Gхво*с*tg+Dpg*h’’0.12+ Dтех*30/100*c* tк+ Dc*h’’0.15+D*c* tк=
= Dвып* h’’0.12+ Gg*c*tg
(7.18+3.8)*4.19*90+7.9*4.19*44.3+Х*2785+4*µ=30%*4.19*tk=90°C+0.25*2693+1.1*4.19*90==4140.55+1466.37+Х*2785+452.52+673.25+414.81→
Dpq=1.15т/ч
Определение температуры воды перед деаэратором
Gхво*с*( tq- t’’хво)= Dвып(h’’0.12-ctк)η
tg= (Dвып(h’’0.12-ctк)η)/ (Gхво*с)+ t’’хво=(0.06*(2785-4.19*90)*0.98)/(7.9*4.19)+40=47.4оС
Неувязка
((Dив+Dg)-(D+ Dpg)/(D+ Dpg))*100=(3.19-3.6/(0.36+1.15))*100=20.19%
2.
Подбор основного оборудования тепловой схемы.
2.1 Подбор сепаратора непрерывной продувки.
Для поддержания заданного солесодержания котловой воды, нужной для получения чистого пара осуществляется продувка котлоагрегата. Для этой цели предусмотрен СНП, он подбирается по объему пара
Vп=Dc*V*X; м3,- где V- удельный объем пара- 1.181 м3/кг
Х=0.98- степень сухости пара
Vн=0.25*1.181*0.98=0.28 м3
Определяем необходимый объем сепаратора
Vсеп= Vп*103/ω*0.8=0.28*1000/750*0.8=280/600=0.42 м3
ω -паронапряжение СНП- 750 м3/ м3
Принимаем СНП- СП-0.7
2.2 Подбор водоводяного теплообменника.
Теплообменник для подогрева исходной воды перед ХВО продувочной водой из СНП с tо-100оС принимаем по действительному расходу водоводяного подогревателя
Gив=9 т/ч
2.3 Выбор пароводяного подогревателя (t ив=40°С)
Подбирается по расходу пара
D= Gив*Cp-(t’’-t’)/(h0.7-Cp*tx)η=9*4.19(40-8.2)/(2764-4.19*90)*0.98=0.5 т/ч
D=0.5 т/ч
В пароводяном подогревателе вода подогревается до 40оС (не выше) что бы не было конденсации водяных паров на поверхности оборудования ХВО, что бы предотвратить коррозию.
2.4 Подбор деаэратора.
В котельных с паровыми котлами устанавливаются деаэраторы атмосферного типа. В деаэраторе происходит удаление из питательной воды растворенных в ней корродирующих газов: О2 СО2 N2. Деаэратор подбирается по расходу деаэрироваемой воды и полезному объему бака-аккумулятора, которая должна быть больше получасовой производительности всех котлов.
Vбака=0.5*Dmax=0.5*14.27=7.135 м3
Марка деаэратора: ДА-25
2.5 Подбор конденсатных баков
Для сбора поступаемого от потребителя конденсата технологий тепловой нагрузки устанавливается 2 конденсатных бака. Емкость каждого бака должна быть не меньше половины возврата конденсата.
Vкб=Dтех*М/100*0.5=4*30/100*0.5=0.6 м3
2.6 Подбор блока водоподогревательной установки
Подбираем по расходу исходной воды
Q=Qов+Qгвс/4.19=17+9/4.19=6.3 гДж/т
n=Qов+Qгвс/ Qгвс=17+9/9=3
Подбираем блочную установку ВПУ-10-М
2.7 Подбор сетевых насосов
Сетевые насосы необходимы для подачи воды потребителям для отопления, вентиляции и ГВС. Устанавливаем минимальное количество насосов 2 (1 рабочий+1 резервный). Подбираем по расходу сетевой воды
а)Для зимнего режима
Gсет=( Qов+Qгвс)*103/Ср(τn-τо)=(17+9)*103/4.19*80=26*1000/4.19*80=26000/335.2=
=77.5 т/ч
б)Для летнего режима
Gсет= Qгвс*103/ Ср(τn-τо)=9*1000/4.19*30=9000/125.7=71.5 т/ч
Подбираем центробежные насосы: МКУ-90
2.8 Подбор питательных насосов
Питательный насос в котельной предусмотрен для подачи воды из деаэратора в экономайзер котла, т.е. снабжает котел водой
Насосов должно быть не менее 2(1 рабочий+1 резервный). Суммарная подача должна быть менее 110% наминарной производительности котлов
Gпит=1.1*3*20.9=69 т/ч
Напор насосов определяется по формуле:
Рк- рабочее давление 13 кг/см
Нг- гидравлическое сопротивление
Нк- разность отметок уровней воды в котле и деаэратора
(Нг+ Нк)- принимаем 20 м.в.ст
Н=1.1(1.1*10* Рк+ Нг+ Нк)=1.1(1.1*10*14+20)=191.4
Подбираем насос: ПЭ 100-56(1 рабочий+1рабочий)
2.9 Подбор подпиточных насосов
Насосов должно быть не менее 2 (1 рабочий+1рабочий).
Подбираем насос по расходу подпиточной воды
Gподп=3.5 т/ч
Напор насосов принимаем 25 м.в.ст
Подбираем насос: К-8-20
2.10 Подбор конденсатного расчета насоса
Напор-15 м.в.ст
По расходу конденсата
Gк=Dтех*M/100=4*30/100=1.2 т/ч
Подбираем насос: К-8/18
Подбор насоса исходной воды
Н-25 м.в.ст Gив=20.9 т/ч
Подбираем насос: К-20/30
3.
Расчет оборудования водоподготовки
1-Солерастворитель
2- Элиектор раствора соли
3-Ионообменный фильтр
-В- водопровод
-С- трубопровод соляного раствора
В практике применяются 2 системы умягчения воды, одно и двух ступенчатое натрий катионирование воды. Число ступеней определяется требованиями к обработанной воде. Для паровых экранизированных котлов требуется глубокое умягчение, обычно применяют 2-х ступенчатую схему натрий катионирования.
В этом случае два фильтра включаются в схему последовательно по воде.
І- ступень ІІ- ступень
Na Na
2-х ступенчатая схема.
Схему обработки воды в котле выбирают в зависимости от 3-х показателей:
Величина продувки- Ротн≤10%
Щелочностьотн- ≤20% Що=2.8%
СО2≤20 мг/кг
P=(Sов*αов*100)/(Sкв- Sов*αов)
Sив- сухой остаток исходной воды- 204.2
Sов- сухой остаток обратной воды- 1.1*263=224.62
αов- доля обработанной воды в питательной воде- Gхво/ Gпит=6/15.6=0.38
Sкв- сухой остаток воды принимаем- 3000
P=(289.3*0.41*100)/(3000-289.3*0.41)=8535.56/2914.65=2.9%
Щотн=(40*Щов*100)/ Sов
Щов=0.72 мл/кг
Щотн=(40*1.03*100)/289.3=14.2%
СО2=(22* Щотн* αов(1+б))/100
б- определяется по формуле (≈0.7)
СО2=(22*14.2*0.41*1.7)/100=2.01 мг/кг
В водопроводной воде нет взвешенных частиц, т.е. предварительной очистки воды не будет.
Расчет фильтров
Определить площадь фильтрования
FNa= Gхво/(ω*а); где
ω- нормальная скорость фильтрования, принимаем ≈10м/ч
а- количество рабочих фильтров- 2(+1 резервный)
FNa=6/10*2=0.3 м2
Принимаем фильтр диаметром 700 мм
FвстNa=0.39 м2
Выбираем типоразмер, проверяем на скорость фильтрования
1)Нормальная скорость
ω н= Gхво/ (FвстNa*а)=6/(0.39*2)=7.6 м/ч
2)Максимальная скорость
ω макс= Gхво/ (FвстNa*(1-а))=6/(0.39*(2-1)=15.3 м/ч
3) Количество солей жидкости удаленных на фильтрах первой ступени
А=24*Що*Gхво=24*2.5*6=360 л/с
4) Число регенераций каждого фильтра в сутки
n=А/( FвстNa*Нсл*ЕрNa*а); где
Нсл- высота слоя катионита- 2 м
ЕрNa- обменная способность катионита 200÷300 г.экв/м3
n=360/(0.39*2*250*2)=0.9
5) Расход поваренной соли 100% на одну регенерацию
GNaCl=( ЕрNa* FвстNa* Нсл*gc)/1000; где
gc=уд. расход- 100
6) Количество жесткости удаленную фильтрами второй ступени
ω ‘o-0.1 мг.экв/сут
А=24* ω ‘o*Gхво=24*0.1*7.9=14.4 мг.экв/сут
7)Принимаем число регенераций каждого фильтра в сутки
Принимаем: n=0.12, то 1 регенерация в 12 суток
8)Расход NaCl 100% поваренной соли на 1 регенерацию
NaCl=250*0.39*2*100/1000=19.5 кг
9)Расход воды на регенерацию
Gpp=( GNaCl*100)/100*В*Ррр
В- концентрация соли-6% Ррр- .041 г/см3
Gpp=(19.5*100)/(100*6*1.041)=1950/624.6=3.1 м3
10) Расход воды на промывку
Gот=qот* FвстNa*Нсл , м3
qот- 7 м3/м3
Gот=7*0.39*2=5,46 м3
11) Расхода воды на ХВО
Gсн=Gвзр+Gpp+Gот=2.8+3.1+5.46=11.4 м3
12)Часовой расход сточных вод от регенераций в сутки
Gчсн=( Gсн*а*n)/24=11.4*2*1/24=0.95 м3
4
Выбор метода удаления дымовых газов и подачи воздуха для горения. Аэродинамический расчет.
Принципиальная схема отвода дымовых газов из котла.
Топочная камера
Экономайзер
Воздухоподогреватель
Дымовая труба
Дутьевой вентилятор
Дымосос
Золоуловитель
Для организации рабочего процесса горения в топочной камере в топку необходимо подавать воздух, а из неё отводить продукты горения уходящих газов. Это приводит к образованию в топке по газоходам котла давление ниже атмосферного. Такие условия называют тягой, она может быть принудительной и естественной. Естественная тяга создается дымовой трубой и зависит от ее высоты. Для создания принудительной тяги перед дымовой трубой устанавливается дымосос. Для регулирования подачи воздуха на горелку устанавливается дутьевой вентилятор.
Дымосос создает принудительную тягу и его напор рассчитывается таким образом, чтобы преодолеть сопротивление в хвостовых поверхностях (экономайзер, взп). Они устанавливаются в газоходе котла и в них используется теплота уходящих дымовых газов. В экономайзере подогревается питательная вода , а в воздухоподогревателе подогревателе подогревается воздух подаваемый в топку
Расчет высоты дымовой трубы
Hтp=
А =120
F- коэффицент рассеивания(для газового топлива принимаем(F=1))
Ζ- общее количество дымовых труб = 1
V – объем удаляемых дымовых газов
V=n*hka
Δt – разность температур (tух-tов=146ºC-21.6=124.4)
ПДКso2 =0.05г/с
Мso2 =0.085 г/с
ПДКno2 =0.085 г/с
ПДКco = 1.02 г/с
ПДК3 = 0.15 г/с
Mno2 = β1*k*Bр*Qнρ(1-qn/100)(1-β2*ч)*β3)=0.49 г/с
Β1=0.85(для газа)
Β2=0.002(коэффициент зависящий от расположения горелок )
Β3=0.85(для прямоточных горелок)
K=0.06(коэффициент характеризующий выход оксидов на 1 гДж теплоты сожженного условного топлива)
Qнр=0.312 м/с- расход топлива на два котла=36.13 мДж/м³
Нтр(min)=
Dтр.у=
Vтр= м³/c
ωвых=15 м/с
nka=2
Dтр.осн=2hтр*i +Dтр.у=2*26.68*0,02+0,87=1.9
i=0.02
5. Топливоснабжение
Подразумевается, что котельная установка работает на природном газе. Газовое топливо – смесь различных горючих и балластных газов. Природный газ отличается высоким содержанием метана СН 4, что обеспечивает высокую теплоту сгорания. Состав природного газа строго регламентируется по ГОСТ 5542. Газ содержит метан, этан, бутан, пропан, пентан, сернистый водород, кислород, азот и механические примеси.
Свойства природного газа:
1. Легче воздуха примерно в два раза.
2. Без цвета и запаха (одорируется на заводах, согласно ГОСТ, этилмеркаптаном для того, чтобы можно было определить утечку по запаху).
3. Взрово - и пожаро - опасен.
4. Удушлив.
Преимущества природного газа: сравнительно дешевая добыча, удобство транспортировки, отсутствие угарного газа, возможность автоматизации процессов горения.
Температура самовоспламенения - 645º С
Температура горения -150º С
Теплота сгорания 8500 Ккал/м³
От мест добычи газ транспортируется по газораспределительной сети к месту использования.
. Газопроводы подразделяются по давлению:
1. Высокого 1 категории – от 1,2 до 0,6 МПа
ΙΙ категории – от 0,6 до 0,3 МПа
2. Среднего – от 0,3 до 0,005 МПа
3. Низкого – от 0,005 МПа
Давление в газоиспользующих установках и во внутренних газопроводах должно соответствовать давлению, необходимому для устойчивой работы, указанному в паспорте завода – изготовителя.
Для котельных:
Отдельно стоящих на территории промышленных предприятий
1,2 МПа
Отдельно стоящих на территории поселений
0,6 МПа
Пристроенных, встроенных, крышных производственных зданий
0,6 МПа
Пристроенных, встроенных, крышных общественных, административных и бытовых зданий
0,005 МПа
Жилых зданий
0,3 МПа
В помещении котельных предусмотрены газопроводы низкого и среднего давления. Газопроводы окрашиваются в желтый цвет с предупреждающими красными кольцами. Внутренние газопроводы прокладываются, открыто в местах, удобных для обслуживания и исключающих возможность повреждений. В местах прохода людей высота прокладки 2,2м ширина основного прохода не менее 1м, крепление к стенам предусмотрено на кронштейнах, либо на стойках. Приваривание газопровода к креплениям запрещено.
Снижение давления газа и поддержание его на заданном уровне осуществляется при помощи ГРУ (монтируемой в помещении котельной), ГРП (в отдельно стоящем здании) и ШРП (монтируемом снаружи здания в металлическом шкафу заводского изготовления).
1. Манометр на вводе, замеряющий давление в уличных сетях
2. Задвижка на вводе
3. Фильтр для очистки газа от механических примесей с 2 манометрами, до и после фильтра
4. ПЗК – предохранительный запорный клапан. Прибор общекотельной автоматики безопасности, служит для прекращения подачи газа в случае повышения или понижения давления относительно рабочего 5. Регулятор давления универсальный Казанцева – РДУК – понижает давление
6. ПСК – предохранительный сбросной клапан – предусмотрен для сброса газа в атмосферу при повышении давления в газопроводе выше рабочего на 10%, чтобы реже срабатывал ПЗК. Кран перед ПСК всегда открыт и опломбирован
7. Задвижка после регулятора – служит для отключения основной нитки ГРУ при ремонте
8. Манометр после ГРУ – служит для определения давления газа, идущего к котлам
9. Импульсные линии, идущие к ПЗК РДУК, импульс берется с газопровода за регулятором
10. Задвижки на байпасе – служат для регулирования подачи газа при ремонте основной нитки ГРУ или понижения давления в уличных сетях ниже возможностей РДУК. При работе основной нитки ГРУ задвижки закрыты и опломбированы
11. Свеча байпаса
12. Задвижки до и после счетчика
6.
Пояснения о применении схемы теплового контроля и автоматики.
При автоматическом регулировании работы котельной установки создается экономически надежный режим работы в условиях периодически меняющейся нагрузки. Кроме того, автоматизация совместно с механизацией сводит к минимуму затраты физического труда обслуживающего персонала и требует повышения культуры эксплуатации. В котельных с паровыми котлами ДКВР 6,5-13 предусмотрена автоматика «Кристалл». Она включает в себя автоматику безопасности, автоматику регулирования, автоматики сигнализации (звуковой + световое табло). Автоматика служит для поддержания работы котла на заданных параметрах и отсекания подачи топлива в случае аварийных ситуаций.
Автоматика безопасности срабатывает на следующие параметры: 1. Максимальное и минимальное давление топлива перед горелкой 2. Минимальное давление воздуха перед горелкой 3. Минимальное разряжение в топке 4. Погасание факела горелки 5. Неисправность цепей защиты 6. Отключение электричества
Принцип работы:
На каждый контролируемый параметр установлен датчик, преобразующий сигнал в электрический импульс. На мембрану датчика идет сигнал, мембрана приходит в движение, замыкает головку датчика. В щит управления идет электрический импульс на реле контроля. Получая сигнал, реле подает питание в электромагнитный клапан, клапан остается открытым - котел в работе.
При нарушении параметров нормальной работы микро выключатель отклоняется от рабочего положения и размыкает электроцепь. Электромагнитная катушка перед ПКН котла обесточивается, прекращается подача газа. При нарушении тяги происходит отсрочка отключения подачи газа на 10-12 секунд, в остальных случаях – мгновенно.
Автоматика регулирования служит для поддержания рабочих параметров в заданных пределах: 1. Давление пара в барабане котла 2. Соотношение газ-воздух Разряжение в топке 4. Уровень воды в котле
Принцип работы регулятора давления пара: МЗД устанавливается на верхнем барабане котла, соединен с паром. Настроен на рабочее давление пара. Если давление отклоняется от рабочего, подается сигнал с МЗД на щит управления. Автоматика «сравнивает» сигнал с заданным и подает команду на исполнительный механизм газового коллектора.
Принцип работы регулятора подачи воздуха:
Командными приборами являются дифференциальный трансформатор топлива и дифференциальный трансформатор воздуха. При колебании давления газа импульс подается в щит управления, откуда команда подается в исполнительный механизм автоматической подачи воздуха и меняет свое положение.
Принцип работы регулятора тяги:
При изменении соотношения газ-воздух меняется объем дымовых газов и, как следствие, меняется тяга. Датчик по тяге – дифференциальный трансформатор. Командный прибор стоит на щите управления. Получая сигнал от датчика, регулятор включает исполнительный механизм поворотной дымовой заслонки или дымососа.
7.
Описание архитектурно- строительной части здания котельной установки.
Определение состава и размеров помещения котельной
Компановкой котельной называют взаимное расположение основного и вспомогательного оборудования, установленного в здании котельной. Расположение оборудования котельных установок должно отвечать требованиям СНиП и быть удобным и безопасным при эксплуатации, предусматривать простую схему трубопроводных коммуникаций и занимать минимально возможную площадь.
Паровые котлы, размещенные в зале, имеют индивидуальный дымосос и вентилятор. Дымовые газы от паровых котлов удаляются через общую дымовую трубу в атмосферу. Питательные баки деаэратора устанавливают выше питательных насосов на 6-8 метров, что исключает кавитацию при термической дегазации питательной воды. При наличии свободного места экономайзеры, водо-подогреватели, насосы, ХВО устанавливаются в одном помещении. Фронты всех котлоагрегатов должны находиться на одном уровне. Расстояние от стен до фронта котлов, работающих на газе, 2м. Расстояние между котлами производительностью более 4 т/ч - 2м, между кронштейном и стеной – 1,3м, проходы между вспомогательным оборудованием не менее 1м, площадки для обслуживания арматуры и КИП должны иметь ширину 600-800мм, ширина лестниц котлов – 600мм. Для защиты от атмосферных осадков и замерзания воды, котлы и вспомогательное оборудование располагаются в специальных зданиях. Котельная с располагаемым внутри основным и вспомогательным оборудованием называется закрытой. Строят такие котельные на территории жилых массивов и производственных предприятий. В котельных с котлами ДКВР предусмотренная высота здания - 8 – 10м.
В помещении котельной должны находиться: котельный зал с котлами и насосной группой, мастерские, трансформаторная подстанция, ГРП, служебные и бытовые помещения. Размер оборудования и отдельных помещений должен учитывать возможность расширения котельной без прекращения работы. Для этих целей 1 из торцевых стен оставляют свободной. Не разрешается устройство блокировки котельной с другими помещениями, так как котельные должны иметь охранную зону в соответствии с правилами эксплуатации газоиспользующих установок. Так как котельная относится к взрыво- и пожаро- опасным объектам, необходимо предусмотреть конструктивные решения по уменьшению силы взрыва. С этой целью создаются искусственно ослабленные места в ограждающих конструкциях. Практикой установлено, если площадь остекления составляет 5м на каждые 10м объема помещения, при взрыве не происходит разрушения строительных конструкций.
Двери в котельной должны открываться наружу. В котельной площадью более 200м² и длиной боковой стены более 12м
предусматривается 2 выхода.
8.
Рекомендации по отоплению и вентиляции
В здании котельной предусмотрено отопление посредством имеющихся котельных агрегатов, за счет исходящего от них тепла. Температура в помещении котельной зимой не должна быть ниже + 12º С, летом + 5º С к температуре окружающего воздуха.
Для удаления загрязненного воздуха в котельной предусмотрена система приточно-вытяжной вентиляции, предусматривающая троекратный обмен воздуха в час. Приток воздуха осуществляется через специальные щели в стенах, вытяжка – через дефлекторы в крыше.
9
Себестоимость (калькуляция)
Стоимость 1т вырабатываемого пара: А = И *10³ ; руб/т
Дгод
И – ежегодные издержки пр-ва (расход ) пара; Дгод – год выработоного пара т/га
год год год
Дгод + 1,11 * (Дтехн + Дов +Дгвс)
год
Дтехн = Дтехн * 24 * 360 = 60480 т/год
год
Дов = Дов * (18 – tcp * o.n) * 24 * n
(18 – tнор)
tcp.o:n – средняя температура отопительного периода (-4,7°С) Уфа
tнор = (-31°С)
n – продолжительность отопительного периода
n = 218 сут.
год
Дов = 4,2 (18 + 4,7) = 95,34 = 19 * 24 * 218 =9940,8
(18 + 31) 49
год
Дгвс = Дгвс * 24 * 365 = 2,4 * 24 * 365 =21024
Дгод = 1,11 (60480 + 9940,8 + 21024) = 91444,8 т/год
Иам – годовые амортизационные отчисления т.р/год
Им – затраты на топливо, электроэнергию, материалы необходимые для производственного процесса
Иэ – затараты на эксплуатацию ( электричество, технический ремонт, зарплаты и остальное)
Амортизационные отчисления это денежные выражения постепенного износа сооружения и оборудования переносимые на изготовление продувки
( т.е. пар). Нормы амортизационных отчислений различаются по виду капитальный влажный.
зд об
Иам = Иам + Иам
Зд зд
Иам = К *
К – удельные затраты на котельную
К=8465 тыс.руб
мвт
Q =
Д = Дк.у * n = 14 * 2 + 20
K = 8465
Полная ожидаемая стоимость котельной
Ks = 8465 * 173,7 = 1470370,5 т.р.
Иам = К
Ииз = 28% доля амортизационных расходов на здание
зд
Аам = 5,5% - норма амортизационных расходов на здание
Иам = 8465
И м = К * Иоб * Аоб = 487,6 тыс.руб
100 100 год
n – для расхода на оборудование
n = 72%
А об = 8%
Зд об
И ам = И обм + И ам = 130 + 487,65 = 61787 тыс.руб
год
И м = И г + И э + И в
И г = 1,06 * В * hка hгод * Сг + Сгр тыс.руб
100 год
max
В – часовой расход топлива на 1 кательную при Д ку м³/с
В = 432 м³/час = 0,12 м³/с
n ка - количество котлов
h год – число часов установленной мощн. В год ч/год
h год = Дгод = 77754 =2222,7
Дку max 20
Ст = 1200 руб/м³
Стр = 0 – ст – ть перев.
Ит = 1,06 * 432 * 2 * 2222,7 * 1200 – 0 = 2442765 тыс.руб
1000
Иэ = C * N * h³ год = 2,51 * 200 * 5500 = 2761110 тыс.руб/год
N – суммарная мощность двигателей (напряжением 2 квт)
С – стоимость электроэнергии (тариф) = 2,51 руб/кВт для предприятия
h год – число часов использования кабельной установки (принимаем h э = 5500 час/год)
И в = (Gив * hгод * Св) = (17*2222,7*14) = 5290 тыс/год
100 100
Gив – расход исходной воды
h год = h год (при расчете Ит)
Св – тариф на воду = 14 руб/м³
Им = Ит + Иэ + Ив = 2442766 + 2761110 + 5290=5209,056
Из = 0,2 * Иам = 0,2 * 618 = 123,6 тыс. руб./год
Изп = Кшт * Qуст * Сзп = 0,6 * 173736 * 1400 = 145,9
1000 1000
Сзп = 1400 тыс.руб
А = И * 10³ = 5950,1 * 10³ = 76,5 руб/т
Дгод 77754
И = Иам + Им + Из = 618 + 5209 + 123,6 = 5951,4 тыс.руб/год
Удельный расход топлива
n = В уст год = 6707,3 = 0,03 т.уб/гДж
Qгод 1829556
Qгод = Д год (hп – hg) =91444,8 (2790 – 437) = 1829551 гДж/год
1000
усл Qгод * 1000 182955*1*1000
В год = h * 7000 * 4,19 = 0,93 * 8000* 4,19 = 6707,3 т.у.т/год
А=5951,4*103/91444,8=65
Список литературы
1 СНиП 2-35-76 Котельные установки. Нормы проектирования.
2 Правила устройства и безопасной эксплуатации паровых и водогрейных котлов
3 Правила технической эксплуатации электрически станций и сетей
4 ГОСТ 21. 403-80 Обозначения условные и графические в схемах
5 21. 606-95 СПДС Правила выполнения рабочей документации тепломеханических решений котельных. М.1995.
6 Роддатис К.Ф. Котельные установки. Учебное пособие для вузов. М., Энергия, 1997.
7 Брюханов О.Н., Кузнецов В.А. Газифицированные котельные агрегаты. М.,ИНФРА-М, 2005 г.
8 Методика определения выбросов загрязняющих веществ в атмосферу при сжигании топлива в котлах производительностью менее 30 тонн пара в час или менее Гкал в час. М.,1999.
9 Стандарты предприятия ( система студенческой проектной документации):
СТП ННГАСУ 1-1-98; СТП ННГАСУ 1-2-98; ННГАСУ 1-3-98;
СТП ННГАСУ 1-4-98; СТП ННГАСУ 1-5-98; ННГАСУ 1-6-98;
СТП ННГАСУ 1-7-98.
10 Лифшир О.В. Справочник по водоподготовке котельных установок.
Изд. 2-е перераб. и доп. М. Энергия 1976.
11 Роддатис К.Ф. Котельные установки. Учебное пособие для вузов. М. Энгргия 1977.
12 Роддатис К.Ф. Полтарецкий А,Н, Справочник по котельным установкам малой производительности. М. Энергоатомиздат 1989.
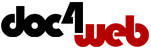
Нравится материал? Поддержи автора!
Ещё документы из категории разное:
Чтобы скачать документ, порекомендуйте, пожалуйста, его своим друзьям в любой соц. сети.
После чего кнопка «СКАЧАТЬ» станет доступной!
Кнопочки находятся чуть ниже. Спасибо!
Кнопки:
Скачать документ