Расчет зубчатых и червячных передач в курсовом проектировании
Министерство Образования Российской Федерации
Липецкий Государственный Технический Университет
Кафедра прикладной механики
РАСЧЕТ ЗУБЧАТЫХ И ЧЕРВЯЧНЫХ ПЕРЕДАЧ
В КУРСОВОМ ПРОЕКТИРОВАНИИ
Составители В.Я. Баранцов, Т.Г. Зайцева
ЛИПЕЦК - 2003
621.81(07)
Б-243
РАСЧЕТ ЗУБЧАТЫХ И ЧЕРВЯЧНЫХ ПЕРЕДАЧ В КУРСОВОМ ПРОЕКТИРОВАНИИ. Методические указания/Сост. В.Я.Баранцов,
Т.Г. Зайцева.
Предназначены для студентов 3 курса дневной и очно-заочной форм обучения немеханических и немашиностроительных специальностей.
Даны методические указания по выбору электродвигателя и материалов для элементов зубчатых и червячных передач редукторов, а также последовательность их проектного расчета.
Рецензент А.В.Щеглов
© Липецкий государственный
технический университет,2003
Оглавление
1. Цель и задачи курсового проектирования…………………………… .4
2. Тематика, объем и содержание курсового проекта………………….. 4
3. Выбор электродвигателя, кинематический и силовой расчет
привода……………………………………………………………………. .4
4. Последовательность проектного расчета закрытых цилиндриче-
ских передач…….…………………………………………………………..7
5. Последовательность проектного расчета закрытых конических
прямозубых передач……………………………………………………….20
6. Последовательность проектного расчета червячных передач...……..24
Библиографический список……………………………………………….31
1. Цель и задачи курсового проектирования
Курсовое проектирование является заключительным этапом в изучении общеинженерных курсов «Прикладная механика», «Механика», «ДМ и основы конструирования» и имеет своей целью приобретение студентом навыков практического применения знаний, развитие умения пользоваться справочной литературой и стандартами, ознакомление с основными правилами и приемами проектирования механизмов и машин.
Знания и опыт, приобретенные студентами при выполнении курсового проекта или работы, послужат базой для изучения устройства, принципов работы и основ проектирования специального технологического оборудования.
2. Тематика, объем и содержание курсового проекта (работы)
Наиболее характерными темами курсовых проектов или работ являются приводы машин металлургического, литейного, сварочного, коксохимического производства или общего назначения.
Курсовой проект состоит из графической части (1…2 листа формата А1) и расчетно-пояснительной записки (30…40 страниц формата А4).
Содержание графической части проекта (работы) и расчетно-пояснительной записки изложено в специальных методических указаниях [1].
3. Выбор электродвигателя, кинематический и силовой
расчет привода
Основными исходными данными для выбора электродвигателя являются мощность на выходном валу привода и частота его вращения , которые могут быть заданы либо непосредственно, либо в виде тягового усилия на приводном барабане (тяговых звездочках) транспортера и скорости ленты (тяговой цепи), между которыми существует связь:
P=Ft·v,
где Р – мощность, кВт; Ft - окружная сила (тяговое усилие), кН;
v – окружная скорость на барабане или звездочках, м/с.
Связь между частотой вращения приводного барабана (тяговых звездочек) транспортера и скоростью ленты (тяговых цепей) выражается зависимостью:
для ленточного транспортера n=60v/(π·Dб);
для цепного транспортера (при тяговой пластинчатой цепи по ГОСТ 588-74) n=60·103 v/(z·р);
где n – частота вращения, мин-1; v – скорость ленты (тяговой цепи), м/с; Dб – диаметр приводного барабана, м; z – число зубьев тяговой звездочки; р – шаг тяговой цепи, мм.
Если на выходном валу привода задан момент, то мощность определяется из соотношения Р=Т·ω;
где Р – мощность, Вт; Т – вращающий момент, Н·м; ω – угловая скорость, рад/с.
Требуемая мощность электродвигателя
Ртр=Р/ηобщ,
где Р - мощность на выходном валу привода; ηобщ – общий КПД привода.
При последовательном соединении механизмов общий КПД привода определяется как произведение значений КПД входящих в него механизмов (передач):
ηобщ= η1· η2· η3·… ηк,
где к – число передач, составляющих привод.
Рекомендуемые значения КПД некоторых видов передач приведены в пособиях [2], c.6; [3], c.5.
Требуемая частота вращения вала электродвигателя
nдв.тр.= n·iобщ,
где n – частота вращения выходного вала привода, мин-1; iобщ –общее передаточное отношение привода, определяемое как произведение значений передаточных отношений входящих в него передач:
iобщ= i1· i2· i3… iк.
Рекомендуемые значения передаточных отношений для различных передач приведены в пособии [2], c.7. Предварительно нужно принимать средние значения передаточных отношений.
По полученным значениям Ртр и nдв.тр. подбирается электродвигатель трехфазный асинхронный короткозамкнутый серии 4А (закрытый обдуваемый) по ГОСТ 19523-81 [2], c.417; [3], c.390.
По принятой частоте вращения вала электродвигателя при номинальной нагрузке nдв и частоте вращения выходного вала n определяется фактическое передаточное отношение привода
iобщ= nдв./n,
которое необходимо перераспределить между отдельными передачами, приняв для проектируемого редуктора значение из стандартного ряда.
Для червячных редукторов можно принять следующие стандартные значения i: 8; 10; 12,5; 16; 20; 25; 32; 40; 50…
Угловые скорости вращения валов привода:
вала электродвигателя ωдв=π·nдв/30, рад/с;
последующих валов ω1= ωдв/i1; ω2= ω1/i2 и т.д.
Вращающие моменты на валах определяют из условия постоянства мощности с учетом потерь:
Тдв=Ртр/ ωдв; Т1= Тдвi1·η1; Т2= Т1i2·η2; и т.д.
4. Последовательность проектного расчета закрытых
цилиндрических передач
4.1. Выбор материала зубчатых колес и вида термической
обработки
При выборе материала для шестерни и колеса следует ориентироваться на применение одной и той же марки стали, но с различной термической обработкой, чтобы твердость шестерни была не менее чем на 20… 30 единиц НВ больше твердости колеса при прямых зубьях и более 40 единиц НВ – при косых и шевронных зубьях.
При твердости шестерни и колеса 45НRC и более не требуется обеспечивать повышенную твердость материала шестерни.
Рекомендации по применению незакаленных (с твердостью до 350 НВ) и закаленных (с твердостью активных поверхностей зубьев более 350НВ) приведены в [2], c.11…12.
Механические характеристики сталей для зубчатых колес приведены в табл.1. Для сравнения твердости, выраженной в единицах НВ и НRC, можно пользоваться зависимостью: 1 HRC≈10HB.
4.2.Определение допускаемых контактных напряжений для шестерни и колеса
Определение допускаемых контактных напряжений [σ]H регламентируется ГОСТ 21354-75:
[σ]H= σHOКHL/SH, (1)
где σHO – предел контактной выносливости при базовом числе циклов нагружения (см. табл. 2); КHL – коэффициент долговечности, определяемый по формуле
. (2)
Таблица 1
Механические характеристики сталей для зубчатых колес
Марка
стали
Вид термической обработки
Предельный диаметр заготовки шестерни, мм
Предельная толщина или ширина обода колеса, мм
σВ,
МПа
σТ ,
МПа
σ-1 ,
МПа
Твердость поверхности
НВ (НRC)
45
45
40Х
40Х
40ХН,35ХМ
40ХН,35ХМ
45ХН
Нормализация
Улучшение
Улучшение
Улучшение и ТВЧ закалка
Улучшение
Улучшение и ТВЧ закалка
Улучшение
Любой
125
80
200
125
125
315
200
200
315
200
Любая
30
50
125
80
80
200
125
125
200
125
600
780
890
790
900
900
800
920
920
830
950
320
540
650
640
750
750
630
750
750
660
780
270
350
400
355
400
400
350
410
410
370
420
179…207
235…262
269…302
235…262
269..302
45…50
235…262
269…302
48…53
235…262
269…302
Продолжение табл. 1
Марка
стали
Вид термической обработки
Предельный диаметр заготовки шестерни, мм
Предельная толщина или ширина обода колеса, мм
σВ,
МПа
σТ ,
МПа
σ-1 ,
МПа
Твердость поверхности
НВ (НRC)
18ХГТ,
20ХНМ
40ХНМА
38ХМЮА
20Х, 12ХН3А
50Г
30ХГТ
30ХГС
30ХГС
Цементация и закалка
Мягкое азотирование
Жесткое азотирование
Цементация и закалка
Нормализация
Улучшение
Цементация и закалка
Нормализация
Улучшение
200
200
200
200
120
400
200
120
200
300
60
160
250
140
300
125
125
120
125
80
200
125
60
120
160
30
90
140
80
160
1000
980
1050
1000
780
610
690
1100
900
850
980
890
790
1020
930
800
780
900
800
640
320
390
800
750
700
840
690
640
840
740
440
440
460
445
370
270
310
490
400
380
430
400
355
440
415
56…63
26…30
63…65
56…63
50…63
190…229
241…285
56…63
56…63
56…63
215…229
235…280
Таблица 2
Значения предела контактной выносливости и коэффициента
безопасности
Термическая и термохимическая обработка
Средняя твердость
σHO,
МПа
[S]H
Нормализация и улучшение
Объемная закалка
Поверхностная закалка
Цементация или нитроцементация
Азотирование
<350НВ
40…50HRC
40…56HRC
54…64HRC
50…58HRC
2(HB)+70
17(НRС)+100
17(НRС)+200
23(НRС)
1050
1,1
1,1
1,2
1,2
1,2
Значения базового числа циклов нагружения NHO=(НВ)3 или см. [2], рис.2.1 в зависимости от средней твердости. Эквивалентное число циклов нагружения за весь срок службы передачи NHЕ:
при постоянной нагрузке
NHЕ=60·n·t·c; (3)
при переменной нагрузке
NHЕ=60Σ(Ti/Tmax)m·n·ti·c , (4)
где n – частота вращения шестерни (колеса), мин-1; ti- срок службы передачи под нагрузкой, ч; с – число зацеплений (число одинаковых зубчатых колес, одновременно находящихся в зацеплении с данной шестерней (колесом); Ti,Tmax,ti- заданы циклограммой нагружения (Tmax- наибольший длительно действующий момент); m – показатель степени, m=3.
При реверсивной нагрузке значение NHE уменьшается в 2 раза.
Значения КHL, принимаемые к расчету, могут быть в пределах 1<КHL<2,3 для мягких и 1<КHL<1,8 для твердых (>350НВ) колес.
Расчет прямозубых передач ведут по меньшему из полученных для шестерни и колеса значений [σ]H.
Для непрямозубых передач
[σ]H=0,45([σ]H1+[σ]H2) , (5)
при этом должно выполняться условие
[σ]H<1,23[σ]Hmin,
где [σ]Hmin, как правило, является [σ]H2.
4.3. Определение допускаемых напряжений при расчете зубьев на
изгиб
Допускаемые напряжения изгиба [σ]F определяются по формуле:
[σ]F= σF0KFL/SF, (6)
где σF0- предел выносливости на изгиб при базовом числе циклов нагружения (табл.3); SF- коэффициент безопасности (табл.3); KFL – коэффициент долговечности
, (7)
здесь m – показатель степени, зависящий от твердости: m=6 при твердости <350НВ; m=9 при твердости >350НВ; NFЕ – эквивалентное число циклов нагружения зубьев за весь срок службы передачи, определяемое по формулам (3) или (4), но при этом в формуле (4) m=6 при твердости <350НВ; m=9 при твердости >350НВ.
Значения KFL, принимаемые к расчету, могут быть в пределах
1< KFL<2,08 при твердости <350НВ и 1<КFL <1,63 при твердости >350HB.
Для реверсивных передач значения [σ]F уменьшают на 20%.
4.4. Определение предельно допускаемых напряжений
При кратковременных перегрузках (расчет на пиковые нагрузки) предельно допускаемыеуле:
, (8)
где i – передаточное отношение ступени редуктора; А – численный коэффициент, А=310 для прямозубых передач; А=270 для косозубых и шевронных передач; Т2 – вращающий момент на валу колеса, Н·мм; ψba=b2/aw – коэффициент ширины зубчатого венца. По ГОСТ 2185-66* ψba может принимать значения: 0,1; 0,125; 0,16; 0,2; 0,25; 0,315; 0,4; 0,5; 0,63; 0,8; 1,0; 1,25. Для прямозубых передач ψba=0,125…0,25; для косозубых ψba=0,25…0,4; для шевронных ψba=0,5…1,0; КН – коэффициент нагрузки
КН = КНα· КНβ· КНυ,
где КНα- коэффициент, учитывающий неравномерность распределения нагрузки между зубьями. Для прямозубых передач КНα=1, для непрямозубых КНα=1,0…1,15; КНβ коэффициент, учитывающий неравномерность распределения нагрузки по ширине зубчатого венца (табл. 4). КНυ- коэффициент динамичности нагрузки, КНυ= 1…1,1.
Таблица 4
Ориентировочные значения КНβ
Расположение колес
относительно опор
Твердость
<350НВ
>350НВ
Симметричное
Несимметричное
Консольное
1,0…1,15
1,1…1,25
1,2…1,35
1,05…1,25
1,15…1,35
1,25…1,45
По полученному значению аw принимается ближайшее стандартное по ГОСТ 2185-66 (мм): 40; 50; 63; (71); 80; (90); 100; (112); 125; (140); 160; (180); 200; (224); 250; (280); 315; (355); 400 (значения в скобках менее предпочтительны).
4.6. Выбор модуля зацепления
При твердости зубьев шестерни и колеса <350НВ m=(0,01…0,02)аw; при твердости зубьев шестерни >45 HRC и колеса <350НВ m=(0,0125…0,025)аw; при твердости зубьев шестерни и колеса > 350 НВ m=(0,016…0,0315)аw.
По ГОСТ 9563-80* принимается ближайшее стандартное значение модуля, (мм): 1,5; (1,75); 2,0; (2,25); 2,5; (2,75); 3,0; (3,5); 4,0; (4,5); 5,0; (5,5); 6,0; (7,0); 8,0; (9,0); 10… (значения в скобках менее предпочтительны).
Для косозубых и шевронных колес стандартным считают нормальный модуль mn.
4.7. Определение суммарного числа зубьев
Для прямозубых передач zΣ= z1+z2=2аw/m; для косозубых и шевронных zΣ= z1+ z2=2аwсоsβ / mn, где β – угол наклона зубьев. Для косозубых передач β=8…18º, для шевронных β=25…40º.
4.8. Определение чисел зубьев шестерни и колеса
z1= zΣ/(i +1); z2=zΣ - z1,
при этом z1>zmin=17cos3β.
По округленным до целых значениям чисел зубьев уточняется передаточное отношение i= z2/z1. Расхождение с принятым ранее номинальным передаточным отношением не должно превышать +2,5%.
4.9. Проверка межосевого расстояния
Для прямозубых колес аw=0,5(z1+z2)m, для косозубых и шевронных аw=0,5(z1+z2)mn/cosβ. Если полученное значение аw не соответствует ранее принятому стандартному, расхождение устраняется изменением угла наклона зубьев
сosβ=0,5(z1+ z2)mn/ аw,
где аw – стандартное значение.
Вычисление сosβ производится с точностью до пяти значащих цифр. Действительный угол наклона зубьев β при этом определяется с точностью до 1секунды. Рекомендуется проверить расчеты, определив
d1=z1mn/cos β; d2=z2mn/cos β
c точностью до сотых долей миллиметра и убедиться, что расчетное межосевое расстояние 0,5(d1+ d2)= аw соответствует принятому ранее.
4.10. Проверка значения ψba
Если принятое ранее значение ψba<0,4, должно выполняться условие ψba>2,5mn/(awsinβ).
Ширина зубчатого венца колеса b2=ψbaaw, шестерни
b1= b2+(5…10)мм с последующим округлением до целых значений.
4.11. Проверка правильности принятых ранее значений размеров
заготовок
Диаметр заготовки для шестерни
dзаг1≈ dа1+(5…10)мм;
ширина заготовки для зубчатого колеса bзаг2= b2+5мм; толщина заготовки для обода колеса sзаг2=5mn+(7…10)мм. Полученные значения размеров заготовок не должны превышать принятых ранее по табл.1.
4.12. Определение окружной скорости в зацеплении
v=πd1·n1/(60·1000), м/с.
4.13. Назначение степени точности передачи в зависимости от
окружной скорости (табл.5)
Для редукторов назначение степени точности ниже 8-й нецелесообразно.
Таблица 5
Степень точности зубчатых передач по ГОСТ 1643-81
Передача
Зубья
Предельная окружная скорость, м/с при степени точности
6
7
8
9
Цилиндрическая
Коническая
Прямые
Непрямые
Прямые
Непрямые
15
30
13
20
10
15
8
10
6
10
4
7
2
4
1,5
3
4.14. Уточнение коэффициента нагрузки
Кн= Кнα· Кнβ· Кнυ, (9)
где Кнα=1 – для прямозубых передач; для непрямозубых см. табл.6.
Таблица 6
Значение коэффициента Кнα для непрямозубых колес
Степень точности
Окружная скорость, м/с
до 1
5
10
15
20
6
7
8
9
1,0
1,02
1,06
1,10
1,02
1,05
1,09
1,16
1,03
1,07
1,13
-
1,04
1,10
-
-
1,05
1,12
-
-
Значения Кнβ и Кнυ принимаются по табл. 7, 8.
4.15. Проверка величины расчетного контактного напряжения
, (10)
полученное значение расчетного напряжения должно находиться в пределах (0,8…1,05) [σ]Н.
Таблица 7
Значения коэффициента Кнβ
ψbd=b2/d1
Твердость <350
Твердость >350
Расположение колес
Расположение колес
консоль-ное
несиммет-ричное
симмет-ричное
консоль-ное
несимме-тричное
симмет-ричное
0,4
0,6
0,8
1,0
1,2
1,4
1,6
1,8
2,0
1,15
1,24
1,30
-
-
-
-
-
-
1,04
1,06
1,08
1,11
1,15
1,18
1,22
1,25
1,30
1,0
1,02
1,03
1,04
1,05
1,07
1,09
1,11
1,14
1,33
1,50
-
-
-
-
-
-
-
1,08
1,14
1,21
1,29
1,36
-
-
-
-
1,02
1,04
1,06
1,09
1,12
1,16
1,21
-
-
4.16. Проверка контактной прочности при кратковременных
перегрузках
, (11)
где σН – расчетное напряжение, полученное по формуле (10).
4.17. Проверка зубьев на выносливость при изгибе
, (12)
где YF – коэффициент формы зуба, зависящий от числа зубьев (для непрямозубых колес – от эквивалентного числа зубьев zυ=z/cos3β).
z… 17 20 22 24 26 28 30
YF… 4,26 4,07 3,98 3,92 3,88 3,81 3,71
z… 40 50 60 80 100 и более
YF… 4,70 4,65 3,62 3,61 3,60
Yβ – коэффициент, учитывающий наклон зубьев.
Для прямозубых колес Yβ =1, для непрямозубых Yβ =1-β/140˚.
КFL – коэффициент нагрузки, КF = КFα· КFβ· КFυ,
где КFα - коэффициент, учитывающий неравномерность распределения нагрузки между зубьями. Для прямозубых передач КFα=1, для непрямозубых значения КFα следующие:
Степень точности 6 7 8 9
КFα 0,7 0,8 0,9 1,0.
КFβ·- коэффициент, учитывающий неравномерность распределения нагрузки по ширине зубчатого венца (табл.9). КFυ, - коэффициент динамичности нагрузки (табл.10).
Расчет по формуле (12) выполняется для менее прочного из пары зубчатых колес, т.е. для того, у которого отношение [σ]F/YF имеет меньшее значение.
Таблица 8
Значения коэффициента Кнυ
Степень точности
Зубья
Твердость, НВ
Окружная скорость, м/с
до 3
3…8
8…12,5
12,5…20
6
Прямые
Непрямые
<350
>350
<350
>350
1,0
1,0
1,0
1,0
1,2
1,15
1,0
1,0
1,3
1,25
1,1
1,0
1,45
1,35
1,2
1,1
7
Прямые
Непрямые
<350
>350
<350
>350
1,15
1,15
1,0
1,0
1,35
1,25
1,0
1,0
1,45
1,35
1,2
1,1
-
-
1,3
1,1
8
Прямые
Непрямые
<350
>350
<350
>350
1,25
1,2
1,1
1,1
1,45
1,35
1,3
1,2
-
-
1,4
1,3
-
-
-
-
4.18. Проверка зубьев на изгиб при кратковременных перегрузках
где - расчетное напряжение по формуле (12).
Таблица 9
Значения коэффициента КFα
Твердость
Расположение колес
симмет-ричное
несиммет-ричное
консольные,
шариковые подшипники
консольно-роликовые
подшипники
0,2
0,4
0,6
0,8
1,0
1,2
1,4
1,6
1,8
<350HB
1,0
1,03
1,05
1,08
1,10
1,13
1,19
1,25
1,32
1,04
1,07
1,12
1,17
1,23
1,30
1,38
1,45
1,53
1,18
1,37
1,62
-
-
-
-
-
-
1,10
1,21
1,40
1,59
-
-
-
-
-
0,2
0,4
0,6
0,8
1,0
1,2
1,4
>350HB
1,03
1,07
1,09
1,13
1,20
1,30
1,40
1,05
1,10
1,18
1,28
1,40
1,43
-
1,32
1,70
-
-
-
-
-
1,20
1,45
1,72
-
-
-
-
Таблица 10
Значения коэффициента КFυ
Зубья
Степень точности
Твердость,
НВ
Окружная скорость, м/с
3
3…8
8…12,5
Прямые
6
7
8
<350
>350
<350
>350
<350
>350
1,0
1,0
1,15
1,15
1,25
1,2
1,2
1,15
1,35
1,25
1,45
1,35
1,3
1,25
1,45
1,35
-
-
Непрямые
6
7
8
<350
>350
<350
>350
<350
>350
1,0
1,0
1,0
1,0
1,1
1,1
1,0
1,0
1,0
1,0
1,3
1,2
1,1
1,0
1,2
1,2
1,4
1,3
4.19. Определение и сведение в таблицу основных параметров
передачи (табл.11)
Таблица 11
,Основные параметры зубчатой передачи
Наименование параметра
Обозначение и численное значение
Вращающий момент на ведомом валу, Н·м.
Угловые скорости валов, рад/с.
Межосевое расстояние, мм.
Модуль, мм: нормальный,
торцовый.
Угол наклона зубьев, град.
Направление наклона зубьев шестерни
Число зубьев: шестерни
Колеса.
Диаметр делительный, мм: шестерни
колеса
Диаметр вершин, мм: шестерни
колеса
Диаметр впадин, мм: шестерни
колеса
Ширина зубчатого венца, мм: шестерни
df1=
df2=
b1=
b2=
Ft=
Fr=
Fa=
5. Последовательность проектного расчета закрытых
конических прямозубых передач
5.1. Выбор материала зубчатых колес и назначение термической обработки (см. п. 4.1.)
Для конических зубчатых колес твердость шестерни должна быть выше твердости колеса не менее чем на 100 единиц НВ.
5.2. Определение допускаемых напряжений (см. п. 4.2…4.3)
5.3. Определение внешнего делительного диаметра колеса
, (13)
где Т2 – вращающий момент на валу колеса, Н·мм; i – передаточное отношение; КН – коэффициент нагрузки. При твердости активных поверхностей зубьев <350НВ предварительно принимают КН=1,2, при твердости >350 КН= 1,35; ψbRe= b/Re<0,3 – коэффициент ширины зубчатого венца. Для стандартных редукторов ψbRe=0,285.
Окончательно принимают ближайшее значение de2 по ГОСТ 2185-66 (см. п. 4.5).
5.4. Определение внешнего окружного модуля
.
Далее нужно выписать значения me по ГОСТ 9563-80* (см. п. 4.6), попадающие в полученный интервал. Окончательно принимается значение модуля, обеспечивающее получение целого числа z2=de2/me. После этого определяется z1=z2/i, округляется до целого числа и уточняется передаточное отношение, отклонение которого от принятого номинального не должно превышать +3%.
Если ни одно из стандартных значений me в нужном интервале не обеспечивает целого числа z2 или Δi>[ Δi], принимается нестандартное значение me (вычисляется до тысячных долей миллиметра).
5.5. Определение углов при вершине делительных конусов
ctg δ1= tg δ2= i= z2/ z1.
5.6. Проверка правильности выбора размеров заготовок
dзаг1≈ dе1+(3…3,5)me; sзаг2≈ 5me+(5…7) мм.
Полученные значения размеров заготовок не должны превышать принятых ранее.
5.7. Определение внешнего конусного расстояния
.
5.8. Определение ширины зубчатого венца
b= 0,285Re,
при этом должно выполняться условие b<10me.
5.9. Определение среднего модуля
m=me – b ∙sinδ1/z1.
5.10. Определение средней окружной скорости передачи
vср=πmz1n1/(60∙1000), м/с.
5.11. Назначение степени точности передачи (см. табл. 5)
5.12. Уточнение величины коэффициента нагрузки
Кн= Кнα· Кнβ· Кнυ, (см. табл. 6…8).
5.13. Проверка величины расчетного контактного напряжения
,
при этом должно выполняться условие:
.
5.14. Проверка контактной прочности при кратковременных перегрузках (см. п. 4.16)
5.15. Проверка прочности зубьев шестерни и колеса на изгиб
,
где Ft=2T2/(mz2) – окружная сила, Н; значение КF определяется так же как и для цилиндрических зубчатых колес (см. пояснения к формуле (12); коэффициент формы зуба YF определяется в зависимости от эквивалентного числа зубьев zυ=z/cosδ.
5.16. Проверка прочности зубьев на изгиб при кратковременных перегрузках (см. п. 4.18)
5.17. Определение основных геометрических параметров конической передачи (табл. 12) и сведение основных результатов расчетов
в табл. 13
Таблица 12
Геометрические параметры конических прямозубых колес по
ГОСТ 19624-74 (при α=20˚, δ1+ δ2=90˚)
Параметр
Обозна-чение
Формула
Внешний делительный диаметр, мм
de
de2 по формуле (13)
de1= de2/i
Внешний окружной модуль, мм
me
по п. 5.4
Число зубьев: шестерни
колеса
z1
z2
по п. 5.4
Внешнее конусное расстояние, мм
Re
Re=0,5 de/ sinδ
Ширина зубчатого венца, мм
b
b=0,285 Re
Cреднее конусное расстояние, мм
R
R= Re-0,5b
Средний окружной модуль, мм
m
m=meR/ Re
Cредний делительный диаметр, мм
d1
d2
d1=mz1
d2=mz2
Угол делительного конуса, град.
δ
δ2=arctg(z2/z1)
δ1=90- δ2
Внешняя высота зуба, мм
he
he=2,2me
Внешняя высота головки зуба, мм
hае
hae=me
Внешняя высота ножки зуба, мм
hfe
hfe=1,2me
Внешний диаметр вершин зубьев, мм
dae1
dae2
dae1= de1+2haecosδ1
dae2= de2-2hfecosδ2
Таблица 13
Основные параметры конической передачи
Наименование параметра
Обозначение и величина
Вращающий момент на колесе, Н·м
Угловые скорости валов, рад/с
Внешние делительные диаметры, мм
шестерни,
колеса.
Внешнее конусное расстояние, мм
Внешний окружной модуль, мм.
Средний окружной модуль, мм.
Угол делительного конуса, град
шестерни,
колеса.
Ширина зубчатого венца, мм.
Число зубьев шестерни
колеса.
Внешний диаметр вершин зубьев колеса, мм
шестерни,мм
Степень точности
Силы в зацеплении, Н
Т2
ω1=
ω2=
de1=
de2=
Re=
me=
m=
δ1=
δ2=
b=
z1=
z2=
dae2=
dae1=
Ft=
Fr1= Fa2=
Fr2= Fa1=
6. Последовательность проектного расчета червячных
передач
6.1. Выбор материалов червяка и зубчатого венца колеса. Определение допускаемых напряжений
Для червяков принимают те же марки сталей, что и для зубчатых колес (см. табл. 1). Улучшенные червяки (<350HB) применяют для передач мощностью до 1 кВт при малой длительности работы.
Для длительно работающих передач большей мощности применяют червяки с твердостью >45HRC с шлифованной или полированной поверхностью витков.
Выбор материала для зубчатого венца колеса (см. табл.14) связан со скоростью скольжения, которую ориентировочно можно определить по формуле:
,
где n1 – частота вращения червяка, мин-1; Т2 – момент на валу червячного колеса, Н·м.
Коэффициент Сυ учитывает интенсивность изнашивания материала, зависит от скорости скольжения:
vs, м/с 4 5 6 7 8
Сυ 1,0 0,95 0,88 0,83 0,9
Допускаемые напряжения на изгиб
[σ]F=(0,25 σT+0,08 σB)KFL для 1 и П групп;
[σ]F=0,22 σВИKFL для Ш группы.
Предельно допускаемые напряжения при кратковременных перегрузках:
[σ]Нпр=4σT; [σ]Fпр=0,8σT - для 1 группы;
[σ]Нпр=2σT; [σ]Fпр=0,8σT - для П группы;
[σ]Нпр=1,65σВИ; [σ]Fпр=0,75σВИ - для Ш группы.
KНL- коэффициент долговечности при расчете на контактную прочность:
KFL- коэффициент долговечности при расчете на изгиб:
Здесь NHE и NFE – число циклов нагружения зубьев колеса за весь срок службы передачи, определяются по формулам (3) или (4), но при определении NHE в формуле (4) m=4, при определении NFE m=9.
Значения KНL, принимаемые к расчету, могут быть в пределах
Таблица 14
Материалы и допускаемые контактные напряжения для венцов червячных колес
Группа
Материал
Способ отливки
σВ,
МПа
σТ,
МПа
[σ]Н,
МПа
1
Бр 010Н1Ф1
υs, <25м/с
Ц
285
165
Сυ0,9 σВКHL
Бр 010Ф1
υs, <12м/с
К
З
275
230
200
140
Бр 05Ц5С5
υs, <8м/с
К
З
200
145
90
80
Сυ0,9 σВКHL
(Сυ0,9 σВКHL)*
П
Бр А10Ж4Н
υs, <5м/с
Ц
К
700
650
460
430
300-25 υs,
(300-25 υs)*
Бр А10ЖЗМц1,5
υs, <5м/с
К
З
550
450
360
300
Бр А9Ж4
υs, <5м/с
Ц
К
З
530
500
425
245
230
195
Л66А6ЖЗМц2
υs, <4м/с
Ц
К
З
500
450
400
330
290
260
275-25 υs,
(250-25 υs)*
Ш
СЧ 18
СЧ 15
υs, <2м/с
σВИ=355
σВИ=315
200-35 υs,
(175-35 υs)*
Способы отливки: К – в кокиль, Ц – центробежный, З – в землю (единичное производство).
* Для закаленных ТВЧ червяков с шлифованными витками.
0,67< KНL-<1,15, значения KFL в пределах 0,543< KFL-<1.
Для реверсивных передач значение [σ]F уменьшают на 20%.
6.2. Определение межосевого расстояния
, мм,
где Т2 – момент на валу червячного колеса, Н·мм.
По ГОСТ 2144-76 выбирают ближайшее значение аw из ряда, мм: 80, 100, 125, 140, 160, 180, 200, 225, 250, 280, 315…
6.3. Назначение числа заходов червяка в зависимости от
передаточного отношения
i 3…14 15…30 30
z1 4 2 1
и определение числа зубьев червячного колеса z2= z1·i.
6.4. Определение значений модуля m=(1,4…1,7)aw/z2
и коэффициента диаметра червяка q=(2aw/m)-z2
По ГОСТ 2144-76 окончательно принимают значения m и q из рядов:
m, мм
q
2,5; 3,15; 4; 5
8; 10; 12,5; 16; 20
6,3; 8; 10; 12,5
8; 10; 12,5; 14; 16; 20
16
8; 10; 12,5; 16
При этом из условия жесткости червяка должно выполняться условие
q> 0,212z2.
6.5. Определение коэффициента смещения инструмента
x=(aw/m) –0,5(z2+q),
при этом должно выполняться условие
-1<x<1.
6.6. Определение фактического передаточного отношения
i=u=z2/z1.
При этом отклонение не должно превышать +4% от ранее принятого.
6.7. Определение основных параметров червячной передачи
делительный диаметр червяка d1=mq;
делительный диаметр червячного колеса d2=mz2;
начальный диаметр червяка dw1=m(q+2x);
диаметр вершин витков червяка dа1= d1+2m;
диаметр впадин витков червяка df1= d1-2,4m;
длина нарезной части червяка: при z1=1; 2 b1>(11+0,06 z2)m;
при z1=4 b1>(12,5+0,09 z2)m;
угол подъема витков червяка γ=arctg(z1/q);
диаметр вершин зубьев колеса dа2=m(z2+2+2x);
диаметр колеса наибольший dам2< dа2+6m(z1+2);
диаметр впадин зубьев колеса df2=m(z2-2,4+2x);
ширина зубчатого венца колеса при z1=1; 2 b2=0,335аw;
при z1=4 b2=0,315аw;
6.8. Определение окружных скоростей на червяке и колесе υ1=0,5ω1d1·10-3, м/с; υ2=0,5ω2d2·10-3, м/с и скорости скольжения
vs= v1/cosγ
Если скорость скольжения отличается от ранее принятой, необходимо уточнить значение допускаемого напряжения для материала колеса.
6.9. Назначение степени точности
Степень точности червячных передач определяется в зависимости от скорости скольжения:
vs, , м/с 2 5 10
степень точности 9 8 7.
6.10. Определение КПД передачи
η=(0,95…0,96)tq(γ+φ΄),
где φ΄ - приведенный угол трения [2], c.35; [3], табл.4.4.
6.11. Силы в зацеплении
Окружная на колесе и осевая на червяке Ft2= Fa1=2T2/d2; окружная на червяке и осевая на колесе Ft1= Fa2=2T1/d1; радиальные силы Fr1= F r2= Ft2tgα; где α – угол профиля витка червяка.
6.12.Расчетное контактное напряжение
,
где К – коэффициент нагрузки. При υ2<3м/с К=1; при υ2>3м/с К=1,1…1,3; [σ]Н – уточненное по действительной скорости скольжения υs значение допускаемого напряжения.
6.13. Проверка зубьев колеса на изгиб
,
где YF – коэффициент формы зуба, выбираемый по эквивалентному числу зубьев колеса zυ2=z2/cos3γ:
zυ2 20 26 30 35 40 45 50 60 80 100 150
YF 1,98 1,85 1,76 1,64 1,55 1,48 1,45 1,40 1,34 1,3 1,27.
ξ – коэффициент, учитывающий износ зубьев. Для закрытых передач ξ=1.
6.14. Проверка прочности зубьев колеса при кратковременных перегрузках
где σН, σF – расчетные напряжения (см. пп. 6.12, 6.13).
6.15. Сведение в таблицу основных параметров передачи (табл. 15)
Таблица 15
Основные параметры червячной передачи
Наименование параметра
Обозначение и величина
1. Вращающий момент на валу колеса, Н·м.
2. Угловые скорости валов, рад/с
3.Межосевое расстояние, мм
4. Модуль осевой, мм
5.Число витков червяка
6. Число зубьев колеса
7. Диаметр делительный, мм: червяка
колеса
8. Диаметр начальный червяка, мм
9. Диаметр вершин витков червяка, мм
10. Диаметр впадин витков червяка, мм
11. Длина нарезанной части червяка, мм.
12. Диаметр вершин зубьев колеса, мм
13. Диаметр впадин зубьев колеса, мм
14. Диаметр колеса наибольший, мм
15. Ширина зубчатого венца, мм
16. КПД передачи
17. Степень точности
18. Силы в зацеплении, Н
Т2=
ω1=
ω2=
аw=
m=
z1=
z2=
d1=
d2=
dw1=
da1=
df1=
b1=
da2=
df2=
daм2=
b2=
η=
Ft1= Fa2=
Ft2= Fa1=
Fr1= Fr2=
Библиографический список
Баранцов В.Я. Методические указания к разработке и оформлению курсовых проектов и работ по дисциплинам «Механика», «Прикладная механика», «ДМ и основы конструирования» / Баранцов В.Я., Зайцева Т.Г. Липецк: ЛГТУ, 2002,-32 с.,(№2782).
Дунаев П.Ф. Конструирование узлов и деталей машин. Учебное пособие для техн. спец. вузов/П.Ф.Дунаев, О.П.Леликов.-М.: Высш. шк., 2000.- 447с.
.Чернавский С.А. Курсовое проектирование деталей машин/Под ред. С.А. Чернавского. М.: Высш. шк., 1988.- 416 с.
Иосилевич Г.Б. и др. Прикладная механика. Учебник для вузов/ Г.Б.Иосилевич, Г.Б. Строганов, Г.С. Маслов. Под ред. Г.Б. Иосилевича.-М.: Высш. шк. – 1989.- 315 с.
Владимир Яковлевич Баранцов
Тамара Герасимовна Зайцева
Расчет зубчатых и червячных передач в курсовом проектировании
Методические указания
Редактор Бирлева Н.Ю.
Подписано к печати. Формат 60х801/16.Ризография. Бесплатно. Объем 2,0 п.л. Тираж 800 экз. Заказ. Бумага газетная.
Липецкий государственный технический университет. 398600. Липецк, ул. Московская, 30. Типография ЛГТУ. 398600. Липецк,
ул. Московская, 30.
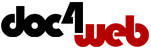
Нравится материал? Поддержи автора!
Ещё документы из категории разное:
Чтобы скачать документ, порекомендуйте, пожалуйста, его своим друзьям в любой соц. сети.
После чего кнопка «СКАЧАТЬ» станет доступной!
Кнопочки находятся чуть ниже. Спасибо!
Кнопки:
Скачать документ