Проект портового элеватора
ОГЛАВЛЕНИЕ
ВВЕДЕНИЕ
Основное назначение портовых элеваторов - приемка с железнодорожного транспорта крупных партий зерна и отгрузка его на морские суда.
Портовые элеваторы располагают в месте стыковки морских магистралей и железной дороги. Для портовых элеваторов характерны мощные приемно-отпускные устройства. Приемная способность элеваторов-от 3до4 маршрутов в сутки, что примерно составляет 10% вместимости; отгрузочная способность-5…6тыс.т/сут и более. Необходимость подготовки однородных партий зерна обуславливает наличие в портовых элеваторах зерноочистительного оборудования и зерносушилок, позволяющих доводить зерно до требуемой кондиции.
Коэффициент оборота портовых элеваторов составляет 4…8 и зависит от многих факторов. На отдельных элеваторах он достигает 10 и более.
Главная задача технологического проектирования элеватора– получение оптимального решения порта как единого комплекса, удовлетворяющего требованиям безопасного приема, быстрейшей разгрузки – загрузки и комплексного обслуживания современных и перспективных транспортных судов и отвечающего условиям прогрессивных способов перевозок на морском и смежных видах транспорта.
При этом должен быть обеспечен: заданный грузооборот на расчетный год, возможность развития элеватора за пределами расчетного периода на отдаленную перспективу, экономическая целесообразность принятых решений.
Современный портовый элеватор представляет собой сложный комплекс гидротехнических и береговых сооружений, складских и административно-бытовых зданий и транспортных путей, энергетических и инженерных коммуникаций.
Успешная работа водного транспорта в значительной степени определяется совершенством всех видов береговых портовых сооружений, обеспечивающих быструю и экономную перевалку грузов, качественное хранение и сортировку их на складах .
Каждый из портов при всем разнообразии имеет общие для всех портов основные элементы:
водные подходы к порту;
акваторию – это защищенная от волнения водная площадь, которая состоит из внешних рейдов и внутренней акватории;
территорию – участок берега, на котором располагается береговое хозяйство: сооружения, здания, дороги, инженерные коммуникации, то есть всё то, что обеспечивает эффективное осуществление погрузочных работ, снабжение судов и создает нормальные условия для высокопроизводительной и безопасной работы сотрудников порта;
сухопутные подходы, которые включают сооружения различных видов наземного транспорта: железнодорожного, автомобильного, трубопроводного, образующих в порту транспортный узел.
1 ОСНОВНЫЕ РАСЧЕТЫ
1.1 Расчет вместимости зернохранилищ перевалочного и портового элеватора
Для портового элеватора заданием на проектирование устанавливается грузооборот зерна за год – Q=1150000 т и коэффициент оборота емкости – Ко=6.
Исходя из этого, вместимость портового элеватора рассчитывается:
, (1)
т
1.1.1 Определение состава емкости
После расчета необходимой вместимости зернохранилищ в целом по предприятию устанавливается состав емкости. В первую очередь, исходя из заданного соотношения элеваторной и складской емкости – Кэл/Кскл (в долях единицы) , определяются их величины в натуральном выражении:
Е пр.эл. = Е пр∙Кэл/ск . Е прскл. = Е пр - Е пр.эл , (2)
где Епр.эл и Епрскл - проектируемая вместимость элеваторная и складская, соответственно.
По заданию Кэл/Кскл=100/-.Значит определяем только элеваторную вместимость
Е пр.эл. =19666,7*100%=19666,7 т
Следует иметь в виду, что конкретные зернохранилища имеют строго определенные габариты и вместимость, и поэтому подбор их количества ведется с определенными допущениями. Допустимое расхождение между вместимостями выбранных (типовых) зернохранилищ и рассчитанных по проекту не должно превышать 5% .
1.1.2 Расчет вместимости силосного корпуса
Вместимость силосного корпуса определяется его конструкцией, т.е расположением силосов, рядностью и числом силосов в ряду, а также формой и размерами силосов. Эти параметры выбираются самостоятельно, руководствуясь общепринятыми типоразмерами. Примем круглые силоса диаметром 6 м и высотой 30 м, расположение рядовое
Вместимость силоса можно определить по приближенной формуле:
Ес = g∙γ · Fс ∙ Нс , (3)
где g - коэффициент использования объема, принимаем равным 0.91
γ- объемная масса зерна , т/м3;
Fс- площадь поперечного сечения силоса, м2;
Н- высота силоса от надсилосной плиты до выпускного отверстия, м.
Вычислим площадь поперечного сечения силоса
Fс =м2
Площадь поперечного сечения силосов- «звездочек» можно определить по приближенной формуле:
Fзв = 0,2· D2 , (4)
Fзв =0,2*62=7,2 м2
Ес =0,91*0,75*28,26*30=578,6 т,
Езв=0,91*0,75*7,2*30=147,42 т
После определения вместимости одного силоса приступаем к выбору сетки силосов и расчету их числа. Выбор начинаем с предварительного подбора числа силосных корпусов Nск , исходя из общей вместимости элеватора. Примем однокрылый силосный корпус Вместимость каждого силосного корпуса Еск определяем делением общей вместимости элеватора Еэл на Nск. Затем уточняем вместимость каждого силосного корпуса. При рядовом расположении круглых силосов, с сеткой силосов n х m, ее определяют по формуле:
Еск =n ·m· Ec + (m-1)·(n-1)·Eзв, (5)
где n – количество силосов в длину;
m – количество силосов в ширину.
Принимаем сетку силосов3*11
Еск =(3*11)* 578,6+(11-1)*(3-1)* 147,42 =22042,2т
1.2 Установление количества и производительности основного и вспомогательного оборудования
1.2.1 Оборудование для приемки зерна с автомобильного транспорта
При проектировании приемных устройств автомобильного транспорта предусматривают выгрузку зерна из большегрузных автомобилей, самосвалов и автопоездов без расцепки из расчета обеспечения нагрузки в размере максимального часового поступления. Современное приемное устройство с автомобильного транспорта представляет собой полностью механизированный цех, который включает универсальный автомобилеразгрузчик, приемный бункер, работающий по принципу самотека, специализированные транспортные механизмы (конвейеры, нории) и накопительные емкости для формирования разнокачественных партий зерна.
Максимальное суточное поступление зерна, устанавливается по формуле:
, (6)
где Аф-годовое поступление зерна с автотранспорта ,т/год.
Кс - коэффициент суточной неравномерности поступления зерна, принимается из табл. 1.
Пр – продолжительность расчетного периода заготовок, сут. Для восточной зоны
Пр=15сут.
Таблица 1 Значения коэффициентов суточной неравномерности поступления зерна (Кс)
Объем заготовок (0,8 Аф), тыс.т.
Продолжительность периода заготовок (Пр)
для климатических зон страны, сут
Южная до 15
центральная до 20
Восточная до 30
до 25
1,7
1,6
1,6
св. 25 до 50 вкл.
1,6
1,6
1,6
св. 50 до 100 вкл.
1,5
1,5
1,6
св. 100
1,4
1,5
1,6
=373,3т/сут
Производительность приемных устройств рассчитывают по максимальному объему часового поступления зерна.
Максимальное часовое поступление зерна (ач,) при разработке типовых проектов определяют по формуле:
, (7)
где кч -коэффициент часовой неравномерности поступления зерна (принимается по табл.2).
t - расчетное время подвоза зерна в течение суток. Принимаем t=12 ч
Таблица 2 Значения коэффициентов часовой неравномерности поступления зерна (Кч)
Величины
Кч
Объем суточного поступления зерна- ас , тыс.т.
до 1
до 2
до 3
до 4
до 5
до 6
до 7
до 10
до 13
свыше 13
2,9
2,3
2,0
1,9
1,8
1,7
1,6
1,5
1,4
1,3
=467,4т/ч
Величина ач определяет необходимое количество линий (потоков) зерна, оснащенных автомобилеразгрузчиками определенной марки и оборудованием, которое должно обеспечивать транспортировку зерна из завального бункера в накопительные емкости или силосы элеватора без задержки.
Эксплуатационная производительность автомобилеразгрузчика рассчитывается по формуле:
, (8)
где Qа/р – техническая производительность автомобилеразгрузчика, т/ч (принимается по табл. 3);принимаем Qа/р=205 при средней грузоподъемности автотранснпорта 12 т
Кр – коэффициент, учитывающий изменение производительности в зависимости от разгрузки зерна культур, с натурой, отличающейся от пшеницы (выбирается из табл. 4).Принимаем Кр=0.9
Квт – коэффициент, учитывающий снижение производительности при разгрузке зерна различного по влажности и засоренности (выбирается из табл. 5); Квт=1
1,2 – коэффициент, учитывающий разнотипность средств доставки зерна.
Таблица 3 Техническая производительность автомобилеразгрузчиков.
Марка автомобилеразгрузчика
Средняя грузоподъемность автотранспорта, т
6
8
10
12
14
16
18
20
АВС-50, АВС-50м-1, БПФШ-2, БПФШ-3м, У15-УРАГ с АВС-5
130
160
185
205
220
230
240
250
У15-УРАГ, У15-УРВС, ГУАР-30м, НПБ-2см-1
110
140
160
180
195
205
215
220
Таблица 4 Коэффициенты изменения вместимости зернохранилищ и производительности оборудования в зависимости от культуры – Кр
Культура
Емкости вагоны
Сушилки
Сепараторы
Нории, конвейеры, автомобилеразгрузчики
1Пшеница
1.1 рядовая
1.2 сортовая, ценная, сильная
1,0
1,0
1,0
1,0
1,0
0,8
1,0
1,0
2.Ячмень
2.1 продовольственный
2.2 пивоваренный
1,2
1,0
0,8
0,8
1,2
0,6
0,8
0,8
3.Овес
1,5
1,0
0,7
0,65
4.Рожь
1,1
1,1
0,9
0,9
5.Просо
1,1
0,8
0,3
0,8
6.Горох
1,0
0,5
1,0
0,9
7.Гречиха
1,2
1,25
0,7
0,7
8.Рис-зерно
1,5
0,4
0,2
0,7
9.Подсолнечник
2,0
0,5
0,5
0,6
Таблица 5 Коэффициенты изменения производительности оборудования на приемке зерна различной влажности и засоренности с автомобильного транспорта - Квз
Содержание примеси сорной и зерновой, %
Влажность зерна, %
до 15
свыше 15 до 17
Свыше 17 до 19
свыше 19 до 22
свыше 22 до 25
свыше 25
До 5
1
1
0,9
0,8
0,8
0,7
Свыше 5 до 10
1
0,9
0,9
0,8
0,8
0,7
Свыше 10 до 15
1
0,9
0,8
0,8
0,7
0,6
Свыше 15
0,9
0,8
0,8
0,7
0,7
0,6
т
Приемные устройства оснащены транспортирующим оборудованием паспортной производительностью (Qт): 150 т/ч При обосновании необходимого количества приемных потоков следует учитывать число партий зерна, поступающих на предприятие в течение суток. Приемка нескольких партий зерна на одном устройстве сопряжена с необходимостью переключать маршруты движения зерна, что сказывается на эксплуатационной производительности линии. Число партий зерна, поступающее за сутки периода заготовок (Рс) можно определить по табл. 6.
Таблица 6 Возможное число партий, поступающих на предприятие за сутки (Рс)
Объем заготовок (0,8·Аф) тыс. т.
Продолжительность расчетного периода заготовок - Пр, сут.
до 15
до 20
до 30
Число партий, поступающих за период заготовок (Рр)
10
15
20
25
10
15
20
25
30
5
10
15
20
25
Число партий, поступающих на предприятие за сутки (Рс)
до 25 вкл
8
9
9
10
8
9
9
9
10
3
7
8
8
8
26…50
11
13
14
15
9
11
11
12
12
4
8
9
9
9
51…100
12
15
17
19
9
13
15
16
16
5
9
11
12
13
более100
13
16
18
20
10
15
17
18
18
5
10
13
15
16
В зависимости от числа партий зерна, поступающего за сутки (Pс) и грузоподъемности автотранспорта (Ga), доставляющего зерно, определяется поправочный коэффициент- Кп ( табл. 7) и рассчитывается эксплуатационная производительность линии (Qлэ):
Qлэ = Qл∙Кп, , (9)
Qлэ =175*0.76=133т/сут
Таблица 7 Коэффициент, учитывающий изменение производительности линии приемки зерна с автомобильного транспорта – К
Число партий поступающих на линию в сутки -Pс
Средняя грузоподъемность автотранспорта- Ga
6
8
10
12
14
16
18
20
1
1,00
1,00
1,00
1,00
1,00
1,00
1,00
1,00
2
0,96
0,91
0,88
0,85
0,83
0,81
0,80
0,79
3
0,92
0,88
0,84
0,80
0,77
0,75
0,73
0,72
4
0,90
0,86
0,82
0,78
0,75
0,72
0,70
0,69
5
0,88
0,84
0,80
0,77
0,74
0,71
0,69
0,68
6 и более
0,87
0,83
0,79
0,76
0,73
0,70
0,68
0,67
Необходимое количество технологических линий приемки зерна с автомобильного транспорта (Nл) определяют по формуле:
, (10)
Принимаем одну технологическую линию приемки зерна с автотранспорта.
Выполненный расчет оборудования для приемки зерна с автомобильного транспорта носит предварительный характер и может корректироваться после расчетов оборудования по другим операциям с зерном, обоснования производительности основных норий элеватора, проверки работоспособности технологической схемы движения зерна на основании анализа графика суточной (сменной) работы.
1.2.2 Устройства для погрузки железнодорожных вагонов
Проектирование устройств для погрузки железнодорожных вагонов ведут с учетом расчетного (максимального) суточного отпуска зерна, рассчитанного по формуле:
, (11)
где Аж.д – годовой объем отпуска зерна с железнодорожного транспорта;
Км1 и К с1 – коэффициенты месячной и суточной неравномерности. Они принимаются по данным МПС, устанавливаемым изысканиями. Для типовых проектов коэффициенты неравномерности следует принимать: К м (коэффициент месячной неравномерности) = 2; Кс (коэффициент суточной неравномерности) = 2,5.
т/сут
По железной дороге на предприятие зерно поступает в вагонах, как правило, маршрутами вместимостью 1000 т (15 ваг.), 1500 т (20 ваг.), 2000 т (30 ваг.) , 3000 т (40 ваг.). Целиком маршрут подать и разместить на приемных путях предприятия не всегда возможно. Поэтому маршрут делят на подачи вагонов Для конкретных адресов строительства и реконструкции грузоподъемность, число и вместимость подач устанавливают органы МПС. В свою очередь, каждая подача может состоять из такого числа вагонов, которое целиком разместить на рабочих путях внутри предприятия также нельзя. Поэтому подачу вагонов могут делить на группы. Зерно в вагонах одной группы обычно грузят одинакового качества и разгружают (грузят) его через одну точку. Расчетную вместимость вагонов по зерну принимают равной 70 тоннам. Общую продолжительность обработки одной подачи принимают равной: при погрузке 3,66 часа; при разгрузке – 3,16,часа.Величину интервала между подачами принимают равной не менее 2 часов. Взвешивание с остановкой и расцепкой для одного вагона занимает 3 мин. Время на маневровые работы определяется путем деления протяженности железнодорожных путей на расчетную скорость движения состава (12 км/ч)
Количество поступающих за сутки вагонов определяется:
(12)
где Г –грузоподъемность вагона (принимается равной 70 т.).
шт.
Исходя из принятого в задании допустимого количества вагонов в подаче (Пв.под) определяют число подач вагонов, которое будет поступать за сутки на предприятие:
, (13)
2.9
Принимаем три подачи две подачи по восемь вагонов,одна подача по семь
Для типовых проектов разгрузка (погрузка) одного, или более железнодорожного маршрута в сутки должна осуществляться не более чем в 2 – 3 подачи.
Величина интервала между подачами (Тпз ) следует рассчитывать по формуле:
Тпз = 0,114 ∙ ( 10 + Пв.под ), (14)
Тпз = 0,114 ∙ ( 10 +7)=2 ч.
Общее время, необходимое на обработку всех подач за сутки, определяется:
при погрузке -
Т об.под = (Т под ∙ Nпод ) + Тпз = (3,67∙ Nпод)+ 0,114 ∙ ( 10 + Пв.под) (15)
Т об.под = (Т под ∙ Nпод ) + Тпз = (3,67∙ 3)+ 0,114 ∙ ( 10 + 7)=13 ч.
В техническом задании на проектирование установлено допустимое количество вагонов в группе ( Пв.гр). Исходя из этого значения, определяют, из скольких групп вагонов будет состоять одна подача:
(16)
Примем 1 группу вагонов в одной подаче
Общее число групп вагонов за сутки можно определить по формуле:
SNгр = Nгр ∙ Nпод (17)
SNгр = 1*3=3
Так как в данном случае только одна группа вагонов в одной подаче , то величина интервала времени между группами составит 0 ч.
Общие потери времени на перестановку всех групп вагонов за сутки (SТгр) можно рассчитать:
SТгр = Тгр ∙ (SNгр - 1 ) = 0,17 ∙ (SNгр - 1 ) ( 18)
SТгр = Тгр ∙ (SNгр - 1 ) = 0,17 ∙ (3- 1 ) =0,34 ч.
Время, которое отводится для обработки одной группы вагонов (Т1груп ) (собственно на работу и на подготовительно-заключительные операции), можно определить по формуле:
при погрузке-
Т1гр = Т пр под - ТГ = 3,67 - 0,17 ∙ (Nгр - 1 ) (19)
Т1гр = Т пр под - ТГ = 3,67 - 0,17 ∙ (1- 1 )=3,67
При обработке группы вагонов на точке разгрузки (погрузки) интервал времени между вагонами (Тваг ) следует принимать равным 0,13 ч. Общие потери времени по группе (ТВ): на перестановку вагонов, открытие люков, пломбирование и другие подготовительно-заключительные операции можно определить:
ТВ= Тваг (Пв.гр –1) = 0,13 (Пв.гр –1) (3.10)
ТВ= Тваг (Пв.гр –1) = 0,13 (7 –1)=0,78 ч.
Тогда рабочее время на обработку группы вагонов (ТРгр) будет равно:
при погрузке-
ТРгр = Т1гр – ТВ = 3,67 - [0,17 ∙ (Nгр - 1 )]- [0,13 ∙ (Пв.гр –1)].(20)
ТРгр = Т1гр – ТВ = 3,67 - [0,17 ∙ (1- 1 )] - [0,13 ∙ (7 –1)]=2,89ч.
Рабочее время устройства на обработку одного вагона (ТРв) следует рассчитать по формуле:
(21)
ч.
Тогда необходимая производительность устройств погрузки вагонов определяется :
, (22)
где Гв - количество зерна в вагоне.
т/ч
Производительность приемных и отгрузочных устройств, рассчитанная на обработку вагона с зерном пшеницы представлена в табл.8
Таблица 8 Производительность устройств для разгрузки (погрузки) вагонов, т/ч
Производи-тельность транспортирующего оборудования, т/ч
Назначение устройства
Разгрузка
Погрузка
Марка
для вагонов-зерновозов, самотеком через пары люков
для вагонов общего назначения
ЛД-5(8)
ШВЗ
одну
две
три
мех. лопата
ВРГ
100
80
80
80
70
80
80
80
175
130
130
130
70
131
130
130
350
130
205
258
70
166
160
130
Необходимое количество отпускных устройств определяют по формуле:
(23)
Принимаем одно отпускное устройство на железнодорожный транспорт. Объемно-планировочное решение по расположению устройств на железнодорожных путях выбирается исходя из проведенных расчетов и компоновки их по отношению к зернохранилищам.
1.2.3 Погрузка и разгрузка речных и морских судов
При проектировании причалов и устройств для разгрузки и погрузки судов руководствуются Нормами технологического проектирования. Количество причальных сооружений и устройств, а также количество технологического оборудования, определяющие пропускную способность причала рассчитываются, исходя из:
- Объемов годового поступления зерна с водного транспорта (устанавливается заданием на проектирование);
- Обеспечения разгрузки заданного расчетного судна в действующие нормативные сроки.
Суточную расчетную пропускную способность устройств погрузки (разгрузки) судов рассчитывают по формуле:
, (24)
где А - годовое поступление зерна с водного транспорта (т) ;
А=(125000+28000)*Коб=918000т.
Км - месячный коэффициент неравномерности поступления зерна с водного транспорта, принимаем Км =2,5;
М – число месяцев навигации в году, (М=9 месяцев);
Кмет – коэффициент использования рабочего времени причалов по метеорологическим условиям (для типовых проектов принимают равным 0,85);
Кзан – коэффициент занятости причала по времени грузовыми и вспомогательными операциями в течение расчетного времени (принимать равным 0,7).
т/сут.
Общее расчетное время нахождения судна у причала tобщ определяется по формуле:
, (25)
где D – грузоподъемность судна, принимаем D=3000 т.
Рсут – суточная пропускная способность устройств для погрузки (разгрузки) судов.
ч
Необходимую производительность технологического оборудования, занятого на обработке речного судна, определяется по формуле:
, (26)
где D - грузоподъемность судна (т);
tгр – время выполнения грузовых операций при обработке судна (ч), определяемое по формуле 25;
Кив– коэффициент использования оборудования по времени (при выгрузке судов принимать- 0,7; при погрузке – 0,6).
т/сут.
Необходимое количество технологических линий, занятых на обработке одного судна, следует определять по формуле:
,(27)
где Qп – паспортная производительность оборудования, принятого к установке, т/ч, принимаем Qп=350т/ч .
принимаем 5 технологических линий
При подборе типа судоразгрузчика или судопогрузчика следует учитывать тип причала, геометрию судна, колебание уровня воды в течение навигационного периода, характер водных подходов, оборудование элеватора. В портовых элеваторах для погрузки и разгрузки зерна на водный транспорт следует предусматривать накопительные емкости на 8-10 часов работы погрузочных (разрузочных) подъемно транспортных систем.
1.2.4 Оборудование для очистки зерна
Очистке подвергают все зерно, поступающее от хлебосдатчиков в период заготовок до кондиций, обеспечивающих их длительную сохранность и использование по целевому назначению. Предварительную очистку проводят в потоке приемки. Для определения потребного оборудования, применяемого для очистки зерна необходимо знать:
количественно–качественную характеристику партий зерна, поступающих в период заготовок;
количество и характер примесей в заготавливаемом зерне;
повторность проведения операции очистки партий зерна с учетом их засоренности и целевого назначения;
суточный объем очистки зерна на проектируемом предприятии.
тип зерноочистительных машин, их паспортную и эксплуатационную производительность;
С целью получения сухих отходов, предпочтительнее основную очистку проводить после сушки.
Эксплуатационную производительность зерноочистительных машин, установленных в технологической линии для очистки партий зерна, различающихся по наименованию культуры, целевому назначению, влажности, засоренности, определяют по формуле:
QЭС = Ки · Qпс · Кк · Квз · Кн , (28)
где Qпс – паспортная производительность зерноочистительной машины, т/ч, принимаем Qпс=100 т/ч;
Ки - коэффициент, зависящий от марки машины и ее места в технологическом процессе (для машин типа БЦС, БИС. БЛС – 0,8),
Кр – коэффициент, зависящий от обрабатываемой культуры (табл. 4);
Квз – коэффициент, зависящий от влажности и засоренности зерна (табл. 9), Квз=1;
Кн – коэффициент, учитывающий назначение зерна (для продовольственных партий – равен 1,0, для партий семенного зерна, пивоваренного ячменя – равен - 0,5), Кн=0.75.
Таблица 9 Коэффициент изменения производительности зерноочистительных машин в зависимости от состояния зерна по влажности и засоренности (Квз )
Содержание отделимой примеси
Влажность зерна, %
до 15
15 - 17
св.17-19
св.19-22
св.22-25
св. 25
Машины для предварительной очистки (скальператоры)
до 5
1,0
1,0
0,9
0,9
0,8
0,7
св.5 до 10
0,9
0,9
0,8
0,8
0,7
0.6
св.10 до 15
0,8
0,8
0,7
0,7
0,6
0,5
Машины для основной очистки (сепараторы)
до 10
1,0
0,9
0,8
0,7
0,6
0,5
св.10 до 15
0,9
0,8
0,7
0,6
0,5
0,4
св.15 до 20
0,8
0,7
0,6
0,5
0,4
0,3
св. 20
0,7
0,6
0,5
0,4
0,3
0,2
QЭС = 0.8*100*0.9*1*0.75=54т/ч.
Суммарную потребную производительность зерноочистительных машин QЭС для проектируемого предприятия определяют как сумму производительности отдельных машин, установленных для раздельной обработки разнокачественных партий. Массу партий зерна поступающих за весь период заготовок и за сутки устанавливают по заданному соотношению количества зерна разной влажности и засоренности (табл.5.2).
Необходимое количество сепараторов определяют по формуле:
, (29)
где Ас – объем очистки зерна;
Qс – паспортная производительность сепаратора, т/час;
Кко – коэффициент, зависящий от культуры, влажности и содержания отделимой примеси; принимается 0,8;
t - число часов работы машины в сутки, 22;
Таблица 10 Соотношение количества поступающего зерна по влажности и засоренности
Показатели состояния зерна
Количество поступающего зерна, %
Районы с сырым и влажным зерном (Восток)
Районы с зерном средней влажности (Центр)
Районы с сухим зерном (Юг)
1
2
3
4
Влажность, % : до 15
10
40
60
св. 15 до 17 вкл.
10
30
20
св. 17 до 22 вкл.
35
30
20
св. 22 до 26 вкл.
30
-
-
св. 26
15
-
-
Засоренность, %
до 1
-
20
50
св.1 до 3 вкл.
-
60
45
св.3 до 5 вкл.
40
10
5
св. 5
60
10
-
Необходимое количество сепараторов А1-БИС-100
Принимаем два сепаратора.
Количество зерна, подлежащего очистке от трудноотделимых примесей, при проектировании конкретных предприятий определяется технологическими изысканиями. При разработке типовых проектов предприятий предусматривают очистку зерна на триерах в течение расчетного периода заготовок в размере не менее 10 % годового поступления зерна от хлебосдатчиков
Необходимое количество триеров типа А9-УТК-6 и А9-УТО-6 определяют по формуле:
, (30)
где А – количество зерна, поступающее в проектируемое сооружение от хлебосдатчиков за период заготовок (т);
φ – количество зерна, подлежащего очистке на триерах ( принимать 10 %);
Qт – паспортная производительность триеров (т/ч).
1.2.5 Оборудование для сушки зерна
Расчет необходимого количества зерносушилок и их потребной производительности должен учитывать следующие требования:
- сушку зерна колосовых культур, кукурузы в зерне, семян бобовых культур необходимо обеспечить в объеме среднесуточного поступления;
- зерносушильное оборудование проектируемого предприятия должно обеспечивать своевременную сушку одновременно поступающих разнокачественных партий зерна;
- выбор типа и производительности зерносушилки должен быть основан на фактическом количестве зерна, которое может просушить зерносушилка за период заготовок;
- количество типоразмеров зерносушилок на предприятии следует принимать минимальным (не более трех);
- вместимость оперативных емкостей для сырого и сухого зерна принимать из расчета бесперебойной работы зерносушилки в течение восьми часов.
Годовой объем сушки поступающего от хлебосдатчиков зерна для предприятия в целом устанавливается по формуле:
Ас = 0,8Аа/тКвКнКкс , (31)
где Аа/т – количество зерна, которое необходимо просушить;
Кв – коэффициент перевода физических тонн в плановые тонны сушки. Для типовых проектов его принимают: для районов с сухим зерном – 0,6; для районов с зерном средней влажности – 0,8; для районов с сырым и влажным зерном – 1,2.
Кн – коэффициент, учитывающий изменение производительности зерносушилок в зависимости от назначения зерна. Для семенного зерна этот коэффициент следует принимать равным 2, для пивоваренного ячменя – 1,7, для остального зерна – 1;принимаем равным 1,41.
Ккс - коэффициент, учитывающий изменение производительности зерносушилок в зависимости от просушиваемой культуры. Его следует принимать:
Для пшеницы продовольственной, ячменя, овса продовольственного и кормового – 1,00; для пшеницы сильной, твердой и ценных сортов – 1,25; для ржи – 0,91; для проса – 1,25; для гороха – 2,00; для гречихи – 1,80;принимаем равным 1,25.
Число партий, требующих сушки и их относительная величина в объеме заготовок, в зависимости от климатической зоны, где расположено проектируемое предприятие устанавливаются по таблице 11
Таблица 11 Число подлежащих сушке партий зерна в зависимости от продолжительности периода заготовок
Объем заготовок за расчетный период, тыс.тонн
Число партий влажного и сырого зерна,
требующего сушки
Для районов с продолжительностью
периода заготовок , сут
15
20
30
До 25
4
6
4
От 25 до 50
6
9
7
От 50 до 75
7
12
11
От 75 до 100
8
15
14
Свыше 100
10
18
18
Ас = 0,8*19500*0,6*1,35*1,125=14215,5т/год.
Расчетное количество зерна, которое может просушить одна зерносушилка за период заготовок, определяют по формуле:
Азс = Пт · Пр · 20,5 · Кпер , (32)
где Пт - паспортная производительность зерносушилки, т /ч, принимаем зерносушилку ДСП-50;
Кпер - коэффициент, учитывающий снижение производительности зерносушилки в зависимости от числа направляемых на нее партий зерна. При числе партий 5 равен 0,73.
Азс = 50*15*· 20,5 · 0,73=11672,7Т/год.
Паспортную производительность зерносушилки следует подбирать по величине партии зерна, требующего сушки. Затем определяют необходимое число зерносушилок, которые обеспечат сушку заданного числа партий сырого и влажного зерна. При этом на каждую сушилку направляют не более пяти партий зерна, желательно одной культуры.
Необходимое количество зерносушилок
1,2
Принимаем 1 зерносушилку
1.2.6 Оборудование для обработки и транспортировки отходов
Обработку отходов на элеваторах и хлебоприемных предприятиях проводят на сепараторах марки А1- БЛС- 6 (12), А1- БИС-6 (12) и других марок.
Количество выделенных отходов и их фракционный состав зависят от схемы обработки зерна на проектируемом предприятии, оборудования принятого к установке, количества зерна подлежащего очистке, а так же исходного содержания примесей в зерне. Отходы выделяют на сепараторах для предварительной и основной очистки зерна, а так же на газорециркуляционных сушилках.
Количество отходов после обработки зерна находят по формуле:
, (32)
где G – количество отходов, т;
Асут – расчетный суточный объем очистки зерна;
С – количество выделенных отходов, принимается в размере 1,5% от массы обрабатываемого зерна;
Пр – период заготовок.
т
Далее определяют количественное деление отходов по фракциям:
Сход с сортировочных сит составляет 40 %,т.е. 0,104т;
Проход подсевных сит составляет 55 %,т.е.0,143т;
Аспирационные относы составляют 10%,т.е. 0,026т;
Необходимое количество сепараторов для контроля отходов рассчитывается по формуле:
,(33)
где G– количество отходов, получаемых после очистки зерна на сепараторах, т
Qс – паспортная производительность сепаратора, т/час;
К – коэффициент, равный 0,4.
Принимаем один контрольный сепаратор А1-БИС-12
Вместимость бункеров для отходов над контрольными сепараторами необходимо принимать из расчета их двухчасовой работы.
Накопление отходов предусматривается в отдельно стоящих металлических бункерах. Вместимость отдельно стоящих бункеров для хранения пыли и отходов, получаемых при предварительной очистке и сушке зерна, предусматривают из расчета накапливания их в течение суток, а для отходов, получаемых при основной очистке – в течение 3 суток. Бункера для отходов размещают вне здания у глухих стен с учетом требований взрыво,-пожаробезопасности.
Отходы транспортируют самотечным, механическим (нории, скребковые, винтовые конвейеры) и пневматическим транспортом.
1.2.7 Основное транспортирующее оборудование (нории и конвейеры)
К основному транспортному оборудованию относят нории, конвейеры и самотечный транспорт. В зависимости от назначения нории подразделяют на основные и специализированные. Основные нории устанавливают в рабочих зданиях элеватора, они предназначены для выполнения основных технологических операций по приемке, очистке, сушке, отгрузке зерна. Специализированные нории допускается устанавливать в приемно-отпускных устройствах, зданиях зерносушилок, в рабочих зданиях элеваторах для транспортировки отходов, подачи зерна на предварительную очистку, внутреннего учета. Потребное количество норий определяют по занятости нории в течении расчетного периода (24 часа) на внешних и внутренних операциях.
Необходимое число часов работы нории на каждой технологической операции определяют по формуле:
, (34)
где асi – суточный объем i-ой операции, т/сут;
Кп – количество подъемов зерна норией;
Qн- паспортная производительность нории, т/ч;
К- коэффициент использования нории;
Квз- коэффициент, зависящий от влажности и засоренности зерна;
Кк – коэффициент, зависящий от культуры .
Суточный объем каждой операции
1)прием с автотранспорта аа/т=373,3т/сут;
2)отгрузка с железнодорожного транспорта аж/д=1363,6т/сут;
3)прием и отгрузка с причала ар=17507т/сут;
4)суточный объем на хранение ахр=17507т/сут;
5)объем очистки аоч=373,3т/сут;
6)объем сушки асуш =373,3-0,26=373,04т/сут.
Необходимое число часов работы нории на каждой технологической операции
1) ч,
2)ч,
3)ч
4)ч принимаем 50%
5)ч
6)ч
Расчетное количество норий на внешних (внутренних) операциях определяют по отношению суммарного числа работы норий к возможному времени ее работы в течение суток (24 часа):
, (35)
Необходимое количество норий принимаем равным пяти.
Окончательный подбор количества норий производится после проверки возможности выполнения операций, совпадающих по времени, а также выполнения наиболее интенсивной операции. Производительность над – и подсилосных конвейеров выбирают по производительности нории. При установке автоматических весов производительность надсилосного конвейера равна производительности нории. Количество надсилосных конвейеров должно быть не менее количества потоков, одновременно выполняемых операции по загрузке зерна в силосы. Пропускная способность самотечного транспорта зависит от сечения самотека и угла наклона его к горизонту. Угол наклона зернопровода зависит от культуры, состояния зерна по влажности.
2 Характеристика строительной части и объемно-планировочных решений по конструкциям, компоновке основных производственных зданий и сооружений элеватора, установление их габаритных размеров
2.1 Выбор варианта компоновки рабочего здания с силосными корпусами и приемно-отпускными устройствами
Портовые элеваторы компонуют по однокрылой схеме, что обеспечивает хорошую связь рабочего здания с силосным корпусом и приемно-отпускными устройствами. Приемно-отпускные устройства увязывают с рабочим зданием так, чтобы надземные и подземные галереи имели минимальную протяженность и обеспечивались удобные и короткие подъезды и подходы. Для автомобильного и железнодорожного транспорта приемные и отпускные устройства располагают с разных сторон элеватора, а для водного транспорта –в зависимости от размещения элеватора относительно водного причала. Приемное устройство с автомобильного транспорта соединяют с рабочим зданием подземными и надземными конвейерами. Железнодорожные пути на предприятиях, связанных с водным транспортом, проходят , как правило, между элеватором и причалом. В данном случае они расположены за элеватором. При этом конвейерные галереи обычно располагают выше габарита приближения строений к железнодорожным путям.
Увязка приемно-отпускных устройств может иметь различные исполнения, и в каждом конкретном случае ее решают с учетом местных условий, и чтобы приемно-отпускные устройства обеспечивали выполнение необходимых операций в полном объеме, в установленные сроки без простоев и требовали минимальных капиталовложений и эксплуатационных затрат.
2.2 Размещение транспортного и технологического оборудования в рабочем здании и силосном корпусе
Нория- основная транспортная машина, определяет тип и мощность рабочего здания элеватора. На элеваторе нории в рабочем здании обеспечивают выполнение различных операций, что позволяет рассчитать их по суммарному суточному объему работ.В данном портовом элеваторе установлены нории производительностью 175и 350 т/ч. Нории производительностью 175 т/ч располагают вдоль рабочего здания с поворотом потока зерна на 90 градусов, а производительностью 350 т/ч- поперек рабочего здания в специальных шахтах. Весы в рабочем здании элеватора расположены в верхней части выше надсилосного этажа. Высота рабочего здания получается 55.8 м. Размещение зерноочистительного оборудования зависит от производительности транспортных механизмов.В рабочем здании оборудование размещено по схеме, когда над и под зерноочистительными машинами устраивают бункера. Зерноочистительные машины располагают в средней части рабочего здания так, чтобы над сепараторами был бункер, обеспечивающий непрерывную их работу в течение 4 ч, т. е. в течение времени, которое необходимо для одновременной очистки и отпуска зерна на железнодорожный транспорт. Контрольные сепараторы расположены этажом ниже после сепараторов и триеров. Одна зерносушилка марки А1-ДСП-50 открытого типа расположен рядом с силосным корпусом. При этом близлежащие силоса выполняют роль надсушильных и подсушильных бункеров. Связь осуществляется при помощи дополнительно установленных норий. При таком расположении зерносушилок открытого типа значительно сокращаются капиталовложения. На плане этажа, находящегося на высоте 55,8м расположены пять головок норий. Они находятся на расстояние 1,6м и 4,7м от противоположных стен. Расстояние между нориями составляет 2,6м. Расстояние от стены до нории 1.1 составляет 1м. На плане сепараторного этажа, расположены два сепаратора и один триерный блок. Расстояние между сепаратором и триерным блоком до стены составляет 2м и 4,4м. Между ними 1,6 и 1,8. От сепаратора до стены 1,5м. Все расстояния соответствуют требованиям техники безопасности, удобству обслуживания технологического оборудования. На плане сепараторного этажа, находящегося на высоте 15,6м, располагаются один сепаратор А1- БИС- 12.Растояние между стеной и сепаратором составляет 2,9 и 3,9м. Норийные трубы не мешают выемки сит из сепаратора.
На этаже башмаков норий расположены пять нории.
2.3 Определение размеров рабочего здания и силосного корпуса в плане
Размещение оборудования в плане и определение размеров рабочего здания выполняется с учетом обеспечения удобства обслуживание оборудования, освещенность рабочих мест естественным светом, соблюдения норм проходов в соответствии с правилами по технике безопасности, производственных санитарии и противопожарной безопасности. Соблюдая все выше перечисленные требования, размеры рабочего здания составили 9000×27000мм. Силосный корпус расположен рядом с рабочем зданием. В данном курсовом проекте силосный корпус состоит силосов круглой формы диаметром 6м, при рядном их расположении, сетка силосов 3×11.Определенные размеры силосного корпуса в плане, который составляет 1800×66000мм.
2.4 Определение высот этажей рабочего здания и силосного корпуса
Высоты этажей должны удовлетворять строительным нормам ,достаточным для размещения , монтажа и обслуживания оборудования , а также обеспечивать возможность подачи (уборки) зерна на машины или в бункера. Строительными нормами предусмотрена минимальная высота помещений в 3600 мм при высоте выступающих конструкций 2400 мм. Высота проходов допускается не ниже 1900 мм. Высоты этажей должны быть кратными 1,2 м. Высоты, необходимые для монтажа и обслуживания оборудования, определяются для каждого изделия индивидуально; при разработке проекта они могут быть приняты равными 500 — 600 мм.
При проектировании самотечного транспорта приходится определять две величины: его длину и угол наклона к горизонтальной поверхности. Измерить их непосредственно на чсртеже можно только в том случае, когда на одном из видов (продольном или поперечном) проекция самотека вертикальна, во всех других случаях истинные значения длины и угла наклона самотека могут определяться аналитически (расчетом), по таблицам или номограммам. Высоту этажей рабочего здания и силосного корпуса рассчитывают по диктующей для каждого этажа самотечной трубе . Величина этажа слагается из высоты оборудования, величины проекции диктующей самотечной трубы, подающей зерно в оборудование (или принимающей из-под оборудования), суммы высот на установку деталей трубы (секторы, перекидные клапаны, вводы и др.) и монтажной высоты. Угол наклона самотечной трубы для большинства культур принимают 36°, для сырого и засоренного зерна угол увеличивают до 45°. Высоты стен силосов, под- и надсилосных этажей должны быть кратными 0,6. Высоту этажа надвесовых бункеров определяют в зависимости от их вместимости, обеспечивающей нормальную работу весов, а высоту над- и подсепараторных бункеров определяют исходя из увязки рабочего здания элеватора с силосным корпусом. На элеваторе устанавливают много самотечных труб. Поэтому не представляется возможным рассчитывать их в отдельности. Все самотечные трубы типизируют в зависимости от их пропускной способности , что упрощает монтаж. Рассчитаем высоты этажей рабочего здания и силосного корпуса. Для этажа башмаков норий диктующей возьмем самотечную трубу с подсилосного конвейера,входящего в рабочее здание элеватора и подающего зерно в норию, наиболее от него отдаленную.
Как видно (рис. 1,) высота этажа башмаков норий слагается из следующих величин:
Рисунок 1 Основные элементы, определяющие высоты этажей
h1— высоты постамента, предназначенного для удобства опорожнения при завале;
h2 — расстояния от нижней кромки башмака| до приемного носика нории;
h3 — высоты, необходимой для установки входа самотечной трубы в башмак нории;
h4,,h6 — высот, необходимых для установки секторов;
h5 — величины проекции диктующей самотечной трубы на вертикальную плоскость,т.е.
h5=lc.тр*tgα,
где lс.тр.-длина самотечной трубы,
a-угол наклона трубы
h7, h8 — высот, связанных с конструкцией сбрасывающей коробки транспортера;
h9 — высоты, необходимой для монтажа и ремонта сбрасывающей коробки; h9 =500...600 мм.
Примем h1=150мм, h2=370мм, h4=100мм,
h5=5000*tg230=2225мм, h7+h8=430мм, h9=600мм
Высота этажа башмака норий будет ровна
Hб.н.=150+370+100+2225+100+730+600=6300мм.
При принятых значениях размеров рабочего здания длина,ширина и высота оперативных бункеров будет равна 9*24*9,9.В результате емкость их составит
Е=9*24*9,9*0,75*0,9=1443 т.
Для сепараторного этажа (рис. 2) диктующей является самотечная труба, подающая зерно в сепаратор из наиболее отдаленного от его приемной коробки отверстия бункера.
Высота сепараторного этажа слагается из следующих компонентов:
h1 — высоты расположения приемного отверстия сепаратора;
h2 — высоты, необходимой для ввода самотечной трубы в приемное отверстие сепаратора;
h3,h5 — высот, необходимых для установки секторов;
h4 — величины проекции диктующей самотечной трубы на вертикальную плоскость;
h6— высоты, необходимой для установки патрубка под бункером.
Примем h1=120мм, h2=150мм, h3=h5=100мм,
h4=5000*tg380=4906мм, h6=150мм
Высота сепараторного этажа составит
Hс=120+150+100+4906+100+150=5981мм
Принимаем высоту этажа 6000мм
Высота распределительного этажа при установке поворотного патрубка (рис. 3) слагается из следующих величин:
h1— высоты расположения верхней ленты надсилосного транспортера над полом;
h2 — высоты насыпного лотка;
h3,h5 — высот, необходимых для установки секторов;
h4 — величины проекции диктующей самотечной трубы на вертикальную плоскость;
h8 — высоты поворотного патрубка;
h7 — высоты переходного патрубка (или части бункера) под порционными весами.
Принимаем h1=700мм, h2=450мм, h3=h5=100мм
h4=5800*tg300=4745,2мм, h6=1000мм
Высота распределительного этажа составит
Hр=700+450+100+4745,2+100+1000=7589мм
Высота весового этажа (рис. 4) слагается из следующих величин:
Рисунок 4. Основные элементы, определяющие высоты этажей
h1— высоты части подвесового бункера, находящегося на весовом этаже;
h2 — высоты весов;
h3— высоты надвесового бункера.
На (рис 4)обозначено:
h4— высота части подвесного бункера, находящегося ниже весового этажа, и h5— полная высота подвесового бункера.
Примем h1=1500мм, h2=1670мм, h3=4100мм
Вычислим высоту этажа автоматических весов
Hв=1500+1670+4100=7270мм
Высота этажа головок норий (рис. 5) слагается из следующих величин:
h1—величины проекции самотечной трубы на вертикальную плоскость;
h3, h2— высот,обусловленных конструкцией нории;
h4— требуемая монтажная высота
Иногда вместо высот h3 + h4 дают высоту h5 — расстояние от оси головки нории до выступающей части перекрытия.
H1=1600мм (h1=l*tga=1500*tg44), h2+h3=1300мм, h4=700мм
Hг.н.=1600+1300+700=3600мм
Высоту над- и подсепараторных этажей определяют после увязки силосного корпуса с рабочим зданием элеватора. Практически над- и подеспараторные бункера делают одинаковыми по размерам.
Для подсилосного этажа (рис. 6,а) диктующей будет самотечная труба, подающая зерно на подсилосный конвейер из наиболее удаленного силоса. Высота подсилосного этажа включает:
Рисунок 6,а и 6,б. Основное элементы, определяющие высоту этажей
а —подсилосного; б — надсилоспого
h1— высоту расположения ленты подсилосного конвейера над полом; h1=500...600мм;
h2 — высоту, необходимую для установки насыпного лотка;
h3, h5 — высоту, необходимую для установки секторов;
h4 — величину проекции диктующей трубы на вертикальную плоскость;
h6 — высоту подвесной воронки, применяемой для уменьшения объема забутки в силосе.
Примем h1=600мм, h4=4600мм, h6=1100мм
Тогда высота подсилосного этажа составит
Hп.с.=600+4600+1100=6300мм
Высота надсилосного этажа (рис.7.8.4,б) слагается из следующих величин:
h1 — высоты подножки (или переходного мостика в зависимости от конструкции) разгрузочной тележки над полом;
h2 — высоты над подножкой (или переходным мостиком) до выступающих частей перекрытия согласно нормам техники безопасности;
h3 — высоты балок.
Принимая h1=600мм, h2=5800мм, h3=800мм, получим высоту надсилосного этажа
Нн.с.=600+5800+800=7200мм.
Таким образом, общая высота рабочего здания составит
Hобщ=55,81м,
а высота силосного корпуса
Hс.к.=43,5м.
3. Характеристика генерального плана
Отличие генерального плана портового элеватора от генеральных планов заготовительных и производственных элеваторов объясняется различным характером их работ. Портовый элеватор принимает зерно из железнодорожных вагонов и барж и отгружает на суда. Это отличие наряду с более компактным размещением сооружений вызвано ограниченными площадями портовых территорий , требует другой компоновки сооружений .При решении генерального плана портового элеватора предусматривают минимальную протяженность территории вдоль причальной линии, возможность одновременного швартования двух судов и минимальную общую площадь территории. Проектирование плана портового элеватора заключается в нахождении оптимального решения генплана как единого комплекса основных элементов порта , скомпонованных в одно рациональное целое. Этот комплекс должен удовлетворять требованиям безопасного приема, быстрейшей загрузки – выгрузки и комплексного обслуживания транспортных судов.
При компоновке плана портового элеватора необходимо выполнять требования санитарных норм проектирования, то есть исходить из наиболее целесообразного взаимного расположения отдельных районов, и учитывать естественные условия побережья.
Учитывая необходимость наиболее рационального расположения на плане отдельных участков порта различного технологического назначения, следует придерживаться следующих рекомендаций:
Районы по переработке генеральных грузов могут размещаться на любом участке порта при выполнении условия: районы с большими глубинами размещаются вблизи входа в порт.
Причалы, на которых расположены холодильники, зерновые элеваторы и другие специальные сооружения клиентуры выносятся за пределы расположения грузовых районов.
Район зерновых грузов целесообразно располагать на узких пирсах шириной 15-20м и с размещением на них оборудования для перегрузки зерна.
Под вспомогательные причалы отводятся места, непригодные для грузовых операций (торцы широких пирсов).
В общем процессе перегрузочных работ особое значение имеет внутриэлеваторный транспорт: железнодорожный, автомобильный, погрузочно-транспортирующий и водный.
От протяженности и расположения железных и автомобильных дорог зависит эксплуатационная деятельность элеватора, организация перегрузочных работ и их стоимость. Расположение железных и автомобильных дорог определяется топографическими условиями, размерами территории элеватора, интенсивностью грузоперевозок. В данном курсовом проекте водные приемно- отпускные устройства расположены вдоль береговой линии, так как в районе предполагаемого строительства не развивается инфраструктура. Экономичность генерального плана характеризуется показателями, основные из которых площадь участка и число отдельных сооружений. Рациональное использование территории предприятия и её благоустройство определяются коэффициентом застройки (К з), и озеленения (Коз), значение которых в (%) находятся следующим образом:
Кз = ∑f /F*100; (36)
где f – площадь каждого здания, м2;
F- площадь всей территории предприятия, F=15700м2.
Площадь каждого здания вычисляется:
f =а * b, (37)
где а – длинна здания ;b- ширина здания ;
Площадь рабочего здания элеватора равна;
f =9* 27=243м2;
Площадь силосного корпуса равна;
f =18*66=1188м2;
Площади приемного устройства с автомобильного транспорта равна;
f = 3*1,5=4,5м2;
Площадь отпускного устройства с железнодорожного транспорта равна;
f = 2,4*1,4=3,36м2;
Площадь автомобильных весов равна;
f = 1,5*1,7=2,55м2;
Площадь вагонных весов равна;
f = 1,4*2=2,8м2;
Площадь административно бытового корпуса равна;
f = 15*10=150м2;
Площадь бункеров для отходов № 1,2 равна;
f = 5*5=25м2;
Площадь зерносушильных агрегатов № 1,2,3 равна;
f = 7*11=77м2;
Площадь насосной станции равна;
f = 5*5=25м2;
Площадь резервуара для воды равна;
f = 0,5*0,5=0,25м2;
Площадь надземной галереи равна;
f = 47*1,5=70,5м2;
Площадь трансформаторной подстанции равна;
f = 1,1*0,9=0,99м2;
Сумма всех зданий равна;∑f=1792,95м2.
Кз =1792,95/15700* 100= 12,5%
Коз = Fоз /F*100; (38)
где- Fоз суммарная площадь озеленения м2;
Коз = 2900 /15700*100=18,5%;
4 ПРОЕКТИРОВАНИЕ ТЕХНОЛОГИЧЕСКОГО ПРОЦЕССА ЭЛЕВАТОРА КАК ПОТОЧНО- ПРОИЗВОДСТВЕННОЙ СИСТЕМЫ
4.1 Описание технологической схемы движения зерна и отходов
Поступающее зерно с автотранспорта разгружается автомобилеразгрузчиком У15-УРАГ и приемными конвейерами 2.1 и 2.2 подается на норию 1.1 производительностью 350т\ч.
Для выгрузки зерна с барж применен пневматический способ, в данном случае используется циклонразгрузитель, размещенный вдоль берега. Из них при помощи конвейера 2.3 передает в промежуточную башню, где осуществляется передача на другой конвейер 4.7 и далее на надсепараторный бункер рабочего здания. Нории 1.1-1.5 марки НЦ-11-350 подают зерно на автоматические весы 3.1-3.5 соответственно. После взвешивания распределительные круги 5.1-5.5 распределяют зерно по надсепораторным бункерам. Далее зерно из надсепараторных бункеров передается для очистки от примесей, отличающихся от него шириной и толщиной на ситовоздушных сепараторах 7.1 и 7.2 марки А1-БИС-100. Зерно также очищается в триерном блоке, состоящий из двух триеров У9-УТО-6 и У9-УТК-6. Очищенное зерно поступает в подсепараторный бункер. Также здесь осуществляется контроль отходов, выделившихся в процессе сепарирования и триерования. Эти отходы конвейерами 11.1 и 11.2 через норию 12.1 производительностью 20т\ч подаются в контрольный сепаратор 9.1 марки А1-БИС-12. После тщательной очистки отходы загружаются в бункера для отходов, а выделенное доброкачественное зерно загружают подсепараторные бункера. Из подсепараторных бункеров зерно распределяется по нориям 1.1-1.5, которые в свою очередь подают зерно на надсилосные конвейеры 4.1 и 4.2, загружающие силоса. Часть зерна, требующая сушки из силосов подается в зерносушилку 10.1, марки А1-ДСП-50. Они загружаются дополнительно установленными нориями 2.1 и 2.5 марки НЦ-11-175. Выделяемые в процессе сушки отходы отправляются в бункера для отходов. После сушки зерно из зерносушилок конвейерами 2.7,подается в нории 2.3, которые загружают заново силоса. На железнодорожный транспорт зерно отгружают из отсека, устроенного в силосном корпусе через самотечные трубы. Железнодорожные вагоны загружают при помощи отгрузочных труб через верхние люки в крыше вагона. Зерно на водный транспорт подают двумя последовательно расположенными перпендикулярно друг другу конвейерами 4.6 и 2.4. На отпускной конвейер 4.6 зерно подается из распределительного круга 5.4 в приемно- отпускную башню, где осуществляется передача зерна на следующий конвейер 2.4. Конвейер 2.4 оборудован разгрузочными тележками, которые позволяют подавать зерно в воронки отпускной трубы.
5 Проверка работоспособности технологической схемы элеватора и установление объёмов выполненных операций с зерном на основании сводного графика работы
Наиболее наглядную картину для анализа производственного процесса дают графики сводной (сменной или суточной) работы элеватора (ГСР). В них планируют объем и очередность операций, совершаемых в течение смены или суток. При проектировании сводные графики составляют для суток наиболее напряженной работы элеватора. Они позволяют определить правильность выбора основного технологического и транспортирующего оборудования и возможность выполнить заданный максимальный объем работы. Используя сводные графики, можно определить потребность в электроэнергии для выполнения объема операций. В процессе эксплуатации сводные графики составляют в целях научной организации труда. В этих графиках предусмотрены объемы и порядок выполнения всех операции. Для облегчения ежедневного оперативного планирования целесообразно разработать ряд графиков работы для суток с различным объемом операций при их различных возможных сочетаниях. При планировании работы на конкретные сутки используют наиболее подходящий для этих суток график.
Заключение
В данном курсовом проекте разработан портовый элеватор в соответствии с исходными данными и схемой побережья. Элеватор имеет грузооборот 118000т\год, складскую емкость на 1966тонн, коэффициент оборота равного 6. Элеватор имеет по одной точке выгрузки зерна с автотранспорта и из судов, а также по одной точке погрузки зерна в суда и на железнодорожный транспорт. Имеются одна зерносушилка марки А1-ДСП-50 производительностью 50 т\ч ,оборудование по подработке зерна.
Разработаны генеральный план элеватора в масштабе М 1:10, технологическая схема ,а также разрезы и планы этажей рабочего здания, силосного корпуса и приемно- отпускных устройств.
БИБЛИОГРАФИЧЕСКИЙ СПИСОК
1. Анисимова Л.В. Проектирование элеваторов с основами САПР. Учебное пособие. Барнаул, 1994. 112 с
2. Нормы технологического проектирования хлебоприемных предприятий и элеваторов. ВНТП-05-88 Минхлебопродуктов СССР / Утв. приказом № 133 от 03.07.1989 г.- М.: ЦНИИПРОМЗЕРНОПРОЕКТ, 1989.
3. Пунков С.П., Ким Л.В., Фейденгольд В.Б. Проектирование элеваторов и хлебоприемных предприятий с основами САПР: Учебник/ Под ред. С.П. Пункова. – Воронеж: Воронежский университет, 1996. – 284 с.
4. Пунков С.П., Фейденгольд В.Б., Изтаев А.И., Додин А.В. Определение эксплуатационной производительности технологических линий приема и обработки зерна.: Методическое пособие к проведению УИРС для студентов по специальности технология хранения и переработки зерна./МТИПП, ВНИИЗ,АФДТИЛПП:- Алма-Ата, 1988, -108 с.
5. Фейденгольд В.Б. Эксплуатационная производительность технологических линий хлебоприемных предприятий и элеваторов. – М.: ЦНИИТЭИ хлебопродуктов, 1993. – 64 с.
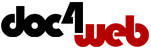
Нравится материал? Поддержи автора!
Ещё документы из категории строительство :
Чтобы скачать документ, порекомендуйте, пожалуйста, его своим друзьям в любой соц. сети.
После чего кнопка «СКАЧАТЬ» станет доступной!
Кнопочки находятся чуть ниже. Спасибо!
Кнопки:
Скачать документ