Технология строительного производства
Технология строительного производства
1. Механизация бетонных и железобетонных работ
Оптимальный вариант механизации определяют по трем основным показателям: продолжительность работы; трудоемкость работ; стоимость работ на 1 м3 уложенного бетона.
Транспортировка бетонной смеси. Бетонная смесь доставляется до потребителя, т. е. в зону бетонных работ, автобетоновозами или автобетоносмесителями. Автобетоновозы — открытые самосвалы с объемом кузова 3...5 м3 используют обычно при расположении бетонного завода в пределах 10 мин пути до строительной площадки. Автобетоносмесители представляют собой бетонный смеситель объемом 5...8 м3, устанавливаемый на автомобилях типа МАЗ, КамАЗ (для меньших объемов) и «Рено», «Мерседес» (для больших объемов). Отечественные автобетоносмесители выпускают с двумя режимами работы: принудительным перемешиванием бетонной смеси по команде водителя из кабины и с перемешиванием бетонной смеси только при движении автомобиля. Недостатком смесителей второго типа является ограниченная область их применения только на строительстве объектов, где бетонирование осуществляется строго по графику, в случае непредвиденного ожидания разгрузка значительно усложняется.
Уклада бетонной смеси. Бетонная смесь подается в конструкцию различными способами: по лотку, грузоподъемными механизмами, бетононасосами. Первые два способа используют при укладке до 50 м3 бетона в смену, третий — при любых объемах, но экономически целесообразно его применение при укладке не менее 45 м3 бетонной смеси в смену. По лотку бетонная смесь подается при возможности установки автобетоносмесителя выше уровня бетонируемой конструкции, например, при заливке фундаментной плиты и возможности заезда автомобиля на дно котлована. Лотки изготавливают из влагостойкой фанеры или металлических листов длиной до 6 м. Для подачи бетонной смеси в бадьях или бункерах используют имеющиеся и задействованные для других погрузочно-разгру-зочных работ грузоподъемные механизмы. В основном это самоходные и башенные краны, иногда используют приставные краны. Бадьи имеют объем 0,3... 1 м3 и для удобства подачи бетонной смеси выполнены в виде «рюмки», на которую для полного ее опорожнения устанавливают вибратор.
Наибольшее распространение при укладке бетонной смеси имеют бетононасосы. При объеме укладки до 80 м3 бетона в смену используют отечественные или импортные автобетононасосы на базе автомобилей КамАЗ, МАЗ, «Мерседес». Автобетононасосы оснащены загрузочным бункером, насосом и раздаточной стрелой. Бетонную смесь подают в вертикальном (до 80 м) и горизонтальном (до 360 м) направлениях. При строительстве объектов с потребностью более 60 м3 бетона в смену, а также зданий повышенной этажности (более 20 этажей) применяют стационарные бетононасосы в комплекте с раздаточными бетоноукладчиками. Бетоноукладчики, имеющие вылет стрелы до 60 м, устанавливают на смонтированные конструкции здания или вспомогательные опоры. Бункер бетононасоса соединяется с бетоноукладчиком с помощью вертикального трубопровода, по которому и поступает смесь. С одной стоянки бетоноукладчика осуществляется укладка бетона на нескольких ярусах. На следующую стоянку бетоноукладчик, масса которого составляет 1...6 т, переставляют установленным на объекте монтажным краном, бетоновод удлиняют и бетонная смесь подается на вновь возводимые ярусы здания. Для уплотнения бетонной смеси, в случае если это требуется по технологии производства работ, используют вибраторы различного назначения: для вертикальных конструкций — глубинные вибраторы, для горизонтальных — виброрейки.
2. Разработка грунта скреперами. Способы набора схемы резанья грунта. Скреперы
Эксплуатационные возможности скреперов позволяют использовать их при отрывке котлованов и планировке поверхностей, при устройстве различных выемок и насыпей. Скреперы классифицируются:
по геометрическому объему ковша — малый (до 3 м3), средний (от 3 до 10 м3) и большой (свыше 10 м3);
по роду агрегатирования с тягачом — прицепные и самоходные (в том числе полуприцепные и седельные);
по способу загрузки ковша — загружаемые за счет силы тяги тягача и с механической (элеваторной) загрузкой;
по способу разгрузки ковша — со свободной, полупринудительной и принудительной разгрузкой;
по способу привода рабочих органов — гидравлические и канатные.
Скреперами ведут разработку, транспортирование (дальность транспортирования грунта колеблется от 50 м до 3 км) и укладку песчаных, супесчаных, лессовых, суглинистых, глинистых и других грунтов, не имеющих валунов, а примесь гальки и щебня не должна превышать 10%. В зависимости от категории грунтов резать их наиболее эффективно на прямолинейном участке пути при движении под уклон 3-7 градусов. Толщина разрабатываемого слоя в зависимости от мощности скрепера колеблется от 0,15 до 0,3 м. Разгружают скрепер на прямолинейном участке, при этом поверхность грунта разравнивают днищем скрепера.
Рис. 9. Способы срезания стружки при работе скрепера: а — с наполнением ковша стружкой постоянной толщины; б — с наполнением ковша стружкой переменного сечения; в — гребенчатый способ наполнения ковша стружкой; г — наполнение ковша способом клевков
Различают несколько способов срезания стружки при работе скрепера (рис. 9):
стружкой постоянной толщины. Способ применяют при планировочных работах;
стружкой переменного сечения. При этом грунт срезается с постепенным уменьшением толщины стружки по мере наполнения ковша, т. е. с постепенным выглублением ножа скрепера к концу набора;
гребенчатым способом. При этом грунт срезается с попеременным заглублением и постепенным подъемом ковша скрепера: на разных стадиях толщина стружки меняется от 0,2-0,3 м до 0,08-0,12 м;
клевками. Наполнение ковша осуществляется путем многократного заглубления ножей скрепера на возможно большую глубину. Способ применяют при работе в рыхлых сыпучих грунтах.
В зависимости от размеров земляного сооружения, взаимного расположения выемок и насыпей применяют различные схемы работы скреперов. Наиболее распространенной является схема работы по эллипсу. При этом скрепер каждый раз поворачивается в одну сторону.
Рис. 10. Способы разработки забоя: а — траншейно-гребенчатый; б — ребристо-шахматный.
При работе в широких и длинных забоях наполнение ковша скрепера осуществляется траншейно-гребенчатым и ребристо-шахматным способами. При траншейно-гребенчатом способе (рис. 10) разработка забоя ведется от края резерва или выемки параллельными полосами постоянной глубины 0,1-0,2 м, одинаковыми по длине. Между полосами первого ряда оставляют полосы не срезанного грунта — гребни, по ширине равные половине ширины ковша. Во втором ряду проходов забирают грунт на полную ширину ковша, срезая гребень и образовывая под ним траншею. Толщина стружки в этом случае в середине ковша 0,2-0,4 м, а по краям 0,1-0,2 м.
При ребристо-шахматном способе (рис. 10) разработка забоя производится от края выемки или резерва параллельными полосами так, чтобы между проходками скрепера оставались полосы не срезанного грунта, равные по ширине половине ширины ковша.
Второй ряд проходок разрабатывают, отступая от начала первого ряда на половину длины проходки первого ряда. Работу скрепера следует сочетать с работой бульдозера, используя их для разработки повышенных участков и перемещения грунта на небольшие расстояния в пониженные места.
3. Способы укрепления грунтов
Совокупность воздействий, в результате которых повышается прочность грунта, он становится неразрываемым, а в некоторых случаях и водонепроницаемым, представляет собой искусственное закрепление грунтов.
Закрепляют грунты для создания вокруг разрабатываемых выемок водонепроницаемых завес и повышения несущей способности грунтовых оснований. В зависимости от физико-механических свойств грунта, его состояния, требуемой степени и назначения закрепления существуют следующие способы искусственного за крепления грунтов: замораживание, цементация, битумизация, химический, электрохимический и др.
Замораживание грунтов применяют в сильно водонасыщенных грунтах (плывунах) при разработке глубоких выемок. для этого по периметру котлована погружают замораживающие колонки из труб, соединенные между собой трубопроводом, по которому нагнетают специальную жидкость— рассол (растворы солей с низкой температурой замерзания), охлажденный холодильной установкой до —20...—25°С (рис. ‚1.8).
Охлаждающие иглы состоят из наружных труб, закрытых и заостренных снизу, и внутренних, вставленных в них коаксиально и открытых снизу. Рассол поступает во внутреннюю трубу, а в нижней части колонки переходит в наружную трубу, по которой поднимается вверх, после чего направляется к следующей колонке. Окружающий грунт замерзает концентрическими цилиндрами с постепенно увеличивающимися диаметрами. Эти цилиндры смерзаются в сплошную стенку мерзлого грунта, которая выполняет функцию ограждения временной выемки. Способ замораживания имеет следующие недостатки: временное сохранение эффекта (на период действия замораживающей установки), длительный процесс естественного оттаивания, повышение влажности грунта за счет миграции воды из теплых слоев грунта к охлажденным (под действием градиента температур) и др. Однако технология замораживания и технические средства для ее выполнения достаточно отработаны, и поэтому, несмотря на указанные недостатки, этот способ широко используют.
Цементация и битумизация заключаются в инекцировании соответственно цементного раствора или разогретых битумов в пористые грунты с высоким коэффициентом фильтрации, а также в трещиноватые скальные породы.
Химическим способом закрепляют песчаные и лессовые грунты нагнетанием в них через инъекторы химических растворов.
Химический способ может быть двух- и одно растворный. Двух растворное закрепление состоит в последовательном нагнетании в грунт сначала водного раствора силиката натрия (Та28iОз а затем хлористого кальция (СаСI2). Растворы вступают в реакцию и образуют гель кремниевой кислоты (пiО2тН2О), который обволакивает зерна грунта и, твердея, связывает их в •монолит. Этот способ применяют в достаточно хорошо дренирующих грунтах (коэффициент фильтрации 2...80 м/сут). При этом прочность грунта достигает 1,5...3 МПа.
Однорастворное закрепление (Смесь силиката натрия и отвердителя) используют для слабодренирующих грунтов с коэффициентом фильтрации менее 0.3 м/сут. Прочность закрепленного грунта 0,3...0,6 МПа.
Раствор при химическом закреплении нагнетают специальными трубами-инъекторами (рис. У.9), погружаемыми раздельно или пакетами по 5 шт. Расстояния между инъекторами принимают в зависимости от вязкости раствора и типа грунта, уточняют экспериментально.
Электрическим способом закрепляют влажные глинистые грунты. Заключается он в пропуске через грунт постоянного электрического тока с напряженностью поля 0,5... 1 В/СМИ и плотностью тока 1...5 А1м2. При этом глина осушается, сильно уплотняется и теряет способность к пучению.
Электрохимический способ отличается от предыдущего тем, что одновременно с электрическим током в грунт вводят через трубу, являющуюся катодом и служащую инъектором, растворы химических добавок, увеличивающие проводимость тока (силикат натрия, хлористый кальций, хлористое железо и др.). Благодаря этому интенсивность процесса закрепления грунта возрастает.
4. Приготовление и транспортирование бетонной смеси
Основной технологической задачей при приготовлении бетонных смесей является обеспечение точного соответствия готовой смеси заданным составам. Эту задачу решают благодаря использованию кондиционных компонентов бетонной смеси. ТОЧНОСТИ ИХ дозирования, включая и учет влажности инертных заполнителей.
Приготовление бетонной смеси производится на районных и центральных заводах товарного бетона или на бетоносмесительных установках, располагаемых вблизи от места потребления бетона.
Районные заводы имеют годовую мощность 100...200 тыс. м3 к обслуживают стройки, находящиеся в радиусе ДО 25...З0 км. Завод состоит из одной, двух или трех секций, каждая из которых рассчитана на самостоятельную работу в автоматизированном режиме. Себестоимость товарного бетона на таких заводах сравнительно низка, однако они экономически оправданны, если в районе их действия гарантировано потребление всей продукции в течение 1О...15 лет.
Районные бетонные заводы могут готовить и сухие товарные смеси, т. е. дозированные компоненты смеси без воды. В этом случае бетонные смеси в специальной таре доставляют обычными автомобилями к месту потребления и перерабатывают на построечных бетоноприготовительных установках или в процессе транспортирования в автобетоносмесителях.
Применение сухих смесей требует решения ряда вопросов, связанных с их надежным тарированием, транспортированием и хранением.
Центральные бетонные или бетонорастворные заводы обычно обслуживают одну крупную строительную площадку, их рассчитывают на срок службы блочной конструкции до 5...б лет. Такие заводы выполняют сборно-разборными блочной конструкции (рИс. Х.21), что делает возможным их перебазировку за 20...30 сут на трайлерах грузоподъемностью 20 т.
Себестоимость приготовления бетонной смеси на таких заводах выше, чем на районных бетонных заводах, и составляет около 0,5 руб/м3 при трудоемкости приготовления около 0,1...0,2чел.-дн/м. Однако их технологическим преимуществом является приближенность к мету потребления бетонных смесей.
Для обслуживания рассредоточенных объектов с незначительными объемами бетонных работ могут использоваться передвижные бетоносмесительные установки (рис. Х.22) производительностью 15...ЗО м3/ч. Их монтируют на специальных трэйлерных прицепах и перевозят с объекта на объект на буксире. Разновидностью передвижных установок являются установки, монтируемые на плавучих средствах. Передвижные установки могут работать автономно, а будучи приданы районному бетонному заводу, существенно увеличивают радиус его действия.
На рассмотренных выше бетоносмесительных заводах и в установках все рабочие операции, связанные с приготовлением смеси, как правило, частично или полностью автоматизированы.
При месячной потребности в бетоне до 1,5 тыс. м и отсутствии я районе строительства бетонных заводов используют инвентарные бетоносмесительные установки (рис. Х.23). При этом действия эффективны при больших объемах работ и непрерывной укладке смеси, например при бетонировании гидротехнических Сооружений.
По способу подачи компонентов в смесительные машины различают одно- и двухступенчатые технологические схемы (рис. Х.24).
При одноступенчатой схеме материалы подают в накопительные бункера, и затем через систему дозаторов под действием собственной массы (гравитационный гирющип) они опускаются в бетоносмесительные машины. Это облегчает возможность автоматизации приготовления смеси. При двухступенчатой схеме получается двукратный подъем материалов.
Заводы с одноступенчатой схемой более компактны (рис. Х.25),. но имеют значительную высоту (20...ЗО м), что усложняет их моптаж. В этой связи их рекомендуется применять при расходе бетона свыше 25...35 М3/Ч.
Все компоненты бетонной смеси дозируют по массе. При этом допускаемые отклонения на замес не должны превышать для воды и цемента 1% и для заполнителей 2%. Исследованиями установлено, что при приготовлении бетонных смесей отсутствие контроля влажности заполнителей приводит к колебаниям значений прочности бетона до 15%, а подвижности смеси—до З раз. Поэтому на современных бетонных заводах и установках начали применять стандартные станции управления бетонным заводом (СУБЗ), которые обеспечивают автоматизированное управление дозированием смеси, включая автоматическую корректировку воды затворения методом контроля влажности заполнителей, в том числе, например, путем комплексного использования нейтровных влагомеров и гамма-плотномеров в системах, учитывающих погрешности, вызываемые колебаниями объемной массы заполнителей.
Для приготовления бетонной смеси применяют бетоносмесительные машины, в которых составляющие перемешиваются по принципу свободного падения (гравитационного действия), и машины, работающие по принципу принудительного перемешивания (лопастные или шнековые). Бетоносмесители принудительного перемешивания при меньших габаритах обеспечивают более высокую однородность бетонной смеси. Они особо эффективны для приготовления жестких бетонных смесей и бетонов на пористых заполнителях.
Транспортирование бетонных смесей. При перевозке бетонной смеси основным технологическим условием является сохранение ее однородности и обеспечение требуемой для укладки подвижности. При этом надо иметь в виду, что при интенсивных сотрясениях во время перевозки, разгрузки или перегрузки крупный заполнитель оседает вниз, а цементное молоко и раствор всплывают вверх и бетонная смесь теряет однородность.
На практике пользуются тремя технологическими схемами доставки бетонных смесей к месту их укладки:
от места приготовления до места их разгрузки у строящегося объекта;
от места приготовления до места разгрузки непосредственно в -бетонируемую конструкцию;
от места разгрузки до места укладки в конструкцию.
По первой и второй схемам для перевозки бетонной смеси в зависимости от расстояний, состояния дорог и других условий могут быть использованы автомобили-самосвалы, автобетоновозы и автобетоносмесители.
По третьей схеме бетонную смесь можно транспортировать кранами (в бадьях), бетононасосами, пневмонагнетателями, а при бетонировании конструкций на уровне или ниже уровня земли — ленточными конвейерами, вибропитателями, бетононасосами и пневмонагнетателями.
При схеме, предусматривающей перегрузку бетонной смеси на объекте, производительность механизмов по приему, подаче Н распределению бетонной смеси должна быть на 1О...15% выше Вопрос о технологически допустимой дальности перевозки бетонной смеси в самосвалах и бетоновозах должен решаться в каждом отдельном случае с учетом состава смеси, температурных условий, состояния покрытия дорог, типа транспортных средств. Так, например, при перевозках бетонных смесей на расстояние более 20...30 км повышается адгезия к кузову самосвала. При перевозке в самосвалах на расстояние более 15 км и в бетоновозах более 20 км бетонная смесь расслаивается и, как следствие этого, снижается конечная прочность бетона.
Автобетоносмеситель представляет собой бетоносмесительный барабан, смонтированный на шасси автомобиля или на полуприцепе, буксируемом седельным тягачом, и приводимый в движение от двигателя автомобиля через коробку отбора мощности.
Автобетоносмеситель загружают сухой смесью (отдозированные компоненты). Вода поступает в барабан в пути следования машины из водяного бачка. Начало перемешивания назначается в зависимости от расстояния перевозки, обычно не ранее чем за 5...10 мин до доставки на пункт назначения. При этом дальность транспортирования ограничивается в основном экономическими соображениями. На более короткие расстояния экономичнее перевозить в автобетоносмесителях готовую бетонную смесь с ее побуждением в пути. дальность транспортирования бетонной смеси при этом может доходить до 60...70 км.
Существенным технологическим преимуществом автобетоносмесителей является возможность порционной выгрузки бетонной смеси.
В зарубежной практике в автобетоносмесителях перевозят также компоненты бетонной смеси, перемешанные с небольшим количеством воды. Полученную таким образом влажную массу можно перевозить на большие расстояния, чем готовую смесь. При приближении к месту разгрузки в барабан добавляют воду до нормы. Этот метод по сравнению с перевозкой сухой смеси позволяет увеличить заполнение барабана (К3=0,7), однако сравнительно сложен и поэтому не получил широкого распространения
В СССР выпуск автобетоносмесителей увеличивается. При этом наряду с изготовлением машин с ограниченной вместимостью смесительного барабана начат выпуск более мощных бетоносмесителей с полезной вместимостью барабана 9 м3, монтируемых на специальных полуприцепах, буксируемых автомобильными тягачами.
При выборе способов перевозки бетонных смесей следует учитывать, что Автобетоносмеситель является тяжелой машиной массой 20 т и более, рассчитанной на дороги с достаточно прочным покрытием. Кроме того, учитывая холостые пробеги этих мобильных бетоноприготовительных установок, необходимы специальные экономические обоснования их применения.
Разгрузка автосамосвалов, автобетоновозов или автобетоносмесителей может производиться: непосредственно в опалубку бетонируемой конструкции; в переносные бункера, бадьи или в другую тару с последующей их переноской краном в зону бетонирования: приемные бункера бетононасосов или пневмотранспортных установок.
При бетонировании фундаментов смесь можно разгружать из самосвала в вибропитатель и затем по вибролотку (рис. Х.27) или виброхоботу транспортировать непосредственно в опалубку.
При бетонировании сооружений на отметках выше уровня земли смесь можно разгружать в бункера или поворотные бадьи (рис. Х.28). Бункера загружают с эстакад или устанавливают в специальные приямки. Вместимость бункера или нескольких установленных вплотную друг к другу поворотных бадей должна быть несколько больше вместимости кузова самосвала, автобетоновоза или барабана автобетоносмесителя.
В ряде случаев смесь доставляют на автомобилях в контейнерах. К месту укладки бетонную смесь в бадьях подают краном.
В промышленном строительстве применяют бадьи вместимостью 0,3, 0,6 и 0,8 м3.
Транспортирования бетонной смеси и потерь ее в пути скорость движения конвейерной ленты не должна превышать 1 м/с. Уклон ее зависит от консистенции бетонной смеси и не должен превышать 18... 15° при подъеме смеси с осадкой конуса до 4...5 см, а при спуске — I2...IОе.
Во избежание влияния атмосферных осадков на водоцементное отношение смеси над конвейерами устанавливают козырьки.
Трубопроводы для перемещения бетонных смесей — это внутри. площадочный транспорт. Этот вид транспорта при определенных условиях имеет ряд технологических преимуществ перед другими способа ми горизонтального и вертикального транспортирования бетонных смесей. К их числу относятся возможность осуществления одним механизмом горизонтального и вертикального перемещения смесей непосредственно от бетонорастворного узла на строительной площадке или от мест их разгрузки на объекте к месту укладки, возможность доставки бетонных смесей в труднодоступные участки возводимого сооружения.
Главным технологическим условием.для транспортирования бетонных смесей по трубам является их достаточная степень транспортабельности (удобоперекачиваемости).
Бетононасосы по способу действия подразделяют на периодического (циклического) и непрерывного действия, по виду привода — с механическим и гидравлическим приводом. Они обеспе1 iявают более высокие давления, более равномерное движение бетонной смеси и высоту подачи до 100...120 м.
На рис. Х.29 показана принципиальная схема одной из распространенных конструкций бетононасосов с гидравлическим приводом. Бетононасос состоит из рамы, двигателя, приемного бункера с колосниковой решеткой и мешалкой, двух управляющих и двух рабочих гидроцилиндров, маятникового патрубка в виде изогнутой трубы, один конец которой шар нирно соединен с бетоноводом, а второй поочередно соединяется с отверстиями рабочих цилиндров насосной станции, подающей рабочую жидкость в управляющие гидроцилиндры, и системы привода остальных механизмов и золотникового распределительного устройства.
Каждая пара цилиндров (управляющего и рабочего) расположена на одной оси, а штоки цилиндров соединены между собой муфтами. Поршни каждой пары цилиндров движутся одновременно во взаимно противоположных направлениях.. Когда бетонная смесь всасывается в один из рабочих цилиндров, поршень второго выталкивает ее через маятниковый патрубок в бетоновод.
5. Виды конструкций каменных кладок. Системы перевязки
Виды кирпичной кладки и системы ее перевязки. По конструктивным и технологическим особенностям кирпичную кладку разделяют на сплошную, облегченную, армированную, декоративную, кладку с облицовкой.
Сплошная кладка. Так называют кладку, выполненную в виде монолитного массива толщиной, кратной 0,5 кирпича. Ряды сплошной кладки состоят из кирпичей, уложенных вдоль наружных граней стены, называемых верстами, и заполнения между ними — забутки. В ряду кирпич укладывают вдоль стены длинной или короткой стороной и в зависимости от этого называют ложком или тычком. От того как уложены кирпичи в стену, весь ряд называют ложковым или тычковым. Забутку выкладывают тычками или используют половинки. При сплошной кладке стен применяют однорядную (цепную) или многорядную системы перевязки; для узких простенков (шириной до 1 м) и столбов — трехрядную.
Облегченная кладка. В малоэтажном сельском строительстве распространены облегченные ограждающие конструкции, состоящие из двух параллельных стенок толщиной в полкирпича каждая, между которыми размещают теплоизоляцию в виде засыпки, легкого бетона, блоков-вкладышей, плитного утеплителя. Для связи стенок между собой применяют горизонтальные вутообразные армированные растворные и кирпичные диафрагмы, тычковые ряды, заходящие в термоизоляционный слой на полкирпича и кирпичные вертикальные стенки.
Армированная кладка. Для повышения несущей способности сильнонагруженных стен, столбов и узких простенков применяют поперечное и продольное армирование кладки, размещая арматуру в горизонтальных и вертикальных швах. При этом толщина швов в кладке должна превышать сумму диаметров пересекающейся арматуры на 4 мм, при соблюдении нормативной средней толщины шва. Поперечное армирование осуществляют сетками прямоугольной формы или типа «зигзаг» с диаметром стержней 3...8 мм, которые укладывают не реже чем через пять рядов кладки. Сетки «зигзаг» располагают в смежных рядах так, чтобы направление прутков в них было взаимно перпендикулярно. Отдельные (контрольные) концы стержней должны выступать на 2...3 мм. При продольном армировании стержни размещают в вертикальных швах или снаружи конструкции и связывают хомутами.
Декоративная кладка. В последнее время широкое распространение получили две разновидности декоративной кладки: вертикальные швы по высоте здания в наружной версте совпадают во всех рядах. С наружной стороны стены кладка состоит из чередующихся трех ложковых и одного тычкового рядов. Вертикальные и горизонтальные швы выполняют одинаковой толщины, придерживаясь одного профиля при расшивке швов. В декоративных целях применяют также сочетание силикатного и глиняного кирпичей.
Кладка с облицовкой. При такой кладке наружную отделку стен выполняют одновременно с их возведением. Для облицовки возведением. Для облицовки используют лицевой кирпич, укладывая его в наружный верстовой ряд одновременно с кладкой обычных кирпичей, применяя многорядную систему перевязки. Лицевой слой кладки связывают при этом с массивом стены тычковыми рядами. Одновременно с кладкой стен выполняют также облицовку закладными или прислонными керамическими плитами.
При однорядной (цепной) системе перевязки тычковые и ложковые ряды чередуются. Каждый вертикальный шов нижнего ряда перекрывается кирпичами верхнего ряда. При этом в каждом ряду вертикальные поперечные швы перекрываются на 1/4, а вертикальные продольные — на 1/2 кирпича. Для перекрытия вертикальных поперечных швов на '/2 кирпича начинают кладку ряда с трехчетверок (3/4 кирпича). С фасадной стороны связанные между собой кирпичи по вертикали образуют рисунок в виде цепочки, чем объясняется сохранившееся до сих пор название — цепная перевязка. Кладка с однорядной системой перевязки отличается высокой прочностью; в ней полностью соблюдаются все три правила разрезки. Однако она требует значительных затрат труда на укладку большого объема верстовых рядов (составляющих 75% общего объема кладки при толщине стен в два кирпича) и заготовку трехчетверок.
Многорядная система перевязки основана на чередовании одного тычкового ряда с пятью ложковыми. При этом вертикальные поперечные швы перекрывают вышележащими кирпичами в каждом ряду, а продольные швы — только через пять рядов. В такой кладке несущая способность составляет 94% по отношению к этому показателю кладки с однорядной системой перевязки. Однако она менее трудоемка благодаря уменьшению объема верстовых рядов (58% общего объема кладки при толщине стен в два кирпича) за счет увеличения забутки и сокращения заготовки трехчетверок.
Трехрядная система перевязки (предложена Л.Н. Онищиком) допускает совпадение вертикальных продольных и поперечных швов в трех смежных рядах, перевязывая их четвертым рядом кладки. Несущая способность такой кладки составляет 97% однорядной кладки.
Независимо от принятой системы перевязки требуется ряды кладки — первый и последний, а также на уровне обрезов стен и столбов, в выступающих элементах (карнизах, поясах и т.п.), под опорными частями балок, плит и других конструкций — выкладывать тычками из целых кирпичей. Вынужденные разрывы в кладке допускается выполнять в виде наклонной или вертикальной штрабы. Для связи с примыкающей кладкой в швы вертикальной штрабы закладывают конструктивную арматуру — не менее трех стержней диаметром до 8 мм через 2 м по высоте и на уровне перекрытия. Разница в высоте возводимой кладки на смежных участках не должна превышать высоты этажа.
6. Организация работ при возведении кирпичных стен
Приведенный технологический процесс кирпичной кладки может быть организован поточно-расчлененным или поточно-кольцевым (конвейерным) методом.
При поточно-расчлененном методе для работы каменщиков выделяют захватку, которую разбивают соответственно числу звеньев на делянки. Размеры делянки должны обеспечить достаточный фронт работ для звена соответствующего состава в течение смены.
Состав звеньев каменщиков зависит от сложности кладки, толщины стены, системы перевязки швов. Он приводится в технологических картах, картах трудовых процессов для кирпичной кладки и составляет 2...6 чел.
В звене обязанности распределяются таким образом, чтобы все каменщики были равномерно загружены в течение смены и выполняли рабочие операции, по сложности соответствующие их разряду.
Звено «двойка» рекомендуется при кладке стен с большим числом проемов или архитектурных деталей толщиной до полутора кирпичей и перегородок. В таком звене каменщик IV (V) разряда устанавливает порядовку, натягивает причалку, ведет кладку верстовых рядов, а каменщик II разряда подает и расстилает раствор, раскладывает кирпич, выполняет периодически совместно с ведущим каменщиком кладку забутки, помогает устанавливать контрольные приспособления.
Звено «тройка» целесообразно применять при толщине стен в два кирпича с менее сложным архитектурным оформлением. В нем каменщик IV (V) разряда устанавливает порядовку, натягивает причалку, кладет версты; каменщик II разряда подает и расстилает раствор, раскладывает кирпич, а каменщик III разряда выполняет забутку, помогает устанавливать контрольные приспособления.
Звено «пятерка» наиболее эффективно при кладке стен толщиной в два и более кирпичей с небольшим числом проемов и простым архитектурным оформлением. При этом каменщики IV (V) и III разрядов кладут наружную версту, каменщики IV и II разрядов — внутреннюю, а второй каменщик II разряда — забутку.
При выполнении кладки поточно-кольцевым (конвейерным) методом выделенную для бригады захватку на делянки не разбивают. Кладку в пределах захватки ведут непрерывным потоком укрупненными звеньями («шестерками» или «пятерками»)у которые перемещаются вдоль возводимой стены по кольцу одно за другим на расстоянии 6...8 м, выкладывая один ряд кладки. При работе «шестеркой» звено разделяют на три «двойки», выполняющие соответственно кладку наружной версты, внутренней и забутку. В звене «пятерка» два каменщика выкладывают наружную версту, а остальные три члена звена — внутреннюю версту и забутку. Поточно-кольцевой метод целесообразно применять при возведении зданий простого очертания в плане со стенами толщиной два и более кирпича, с малым числом проемов и простым архитектурным оформлением. При этом значительно повышается производительность труда.
Существенное влияние на производительность труда оказывает организация рабочего места каменщиков. Оно должно находиться в сфере обслуживания подъемного крана и включать три зоны: рабочую зону шириной 0,6...0,7 м, зону материалов— 1 м и зону прохода рабочих — 0,8...0,9 м. Общая ширина рабочего места каменщиков- достигает 2,5 м. Кирпич располагают вдоль фронта работ, чередуя с раствором. При кладке стен с проемами кирпич размещают напротив простенков, а раствор — напротив проемов. В пределах рабочего места кладку ведут ярусом высотой до 1,2 м. В процессе кладки яруса производительность труда каменщика изменяется, достигая наибольшего значения на высоте 0,6 м от уровня рабочего места. Это указывает на наличие резерва повышения производительности труда за счет улучшения организации рабочего места.
7. Технология возведения зданий из бруса
Особенность Брусовых зданий заключается в том, что возникающая вертикальная нагрузка воспринимается наружными и внутренними стенами, смонтированными из бруса. После возведения фундамента или стен подвала и выполнения вертикальной и горизонтальной гидроизоляции по ним устраивают обвязку и укладывают порядно брус наружных и внутренних стен. Для наружных стен используют антисептированный и антипирированный (пропитанный раствором, понижающим горючесть древесины) брус 150 х 150...200 х 200 мм, для внутренних — брус 100 х 100 мм. Между рядами прокладывают слой гидро- и теплоизоляции, позволяющий осуществлять лучшее сопряжение брусьев и препятствующий задуванию и проникновению влаги внутрь здания. Между собой брусья соединяют крепежными элементами — нагелями, представляющими собой металлические штыри диаметром 25 мм и длиной, равной двукратной высоте брусьев плюс 30 мм. Такая длина нагелей обеспечивает прошивание двух рядов брусьев и вхождение на 25...30 мм в третий брус. Нагели устанавливают в шахматном порядке через 1,5 м один от другого, но не менее чем два нагеля на один брус.
На возведенные стены первого этажа укладывают балки перекрытия, монтируют конструкции второго этажа, чердачное перекрытие, несущие пространственные конструкции кровли и кровлю.
На следующем этапе наружные стены утепляют- изнутри или снаружи и обшивают декоративными материалами — деревянными элементами или отделочным камнем. После этого приступают к санитарно-технической и электротехнической разводкам, внутренним отделочным работам и благоустройству прилегающей территории.
К недостаткам брусовых зданий относятся повышенные требования специальной подготовки к используемым при их возведении материалам. До начала строительства брус должен пройти пропитку антисептирующими и водоотталкивающими растворами, после чего их укладывают в сушильную камеру и доводят уровень влажности до значений, не превышающих 8%. На протяжении строительства брусья должны храниться в сухом отапливаемом помещении. Если эти условия не соблюдаются, повышение влажности приводит к тому, что после возведения здания происходит усыхание древесины, обжатие теплоизоляционной прокладки и, как следствие, усадка здания до 5% по высоте.
8. Состав комплексного процесса бетонных и железобетонных работ
Для изготовления бетонной и железобетонной конструкции определенных размеров и конфигурации необходимо бетонную смесь и арматуру уложить в заранее приготовленную форму, которая называется опалубкой.
Опалубка на высоте поддерживается в проектном положении при помощи лесов. Опалубка и леса должны быть жесткими, прочными и неизменяемыми, простыми в изготовлении, сборке и разборке. Сторона опалубки, примыкающая к бетону, должна быть гладкой, стыки досок и щитов не должны при бетонировании пропускать цементного молока.
Для удешевления бетонных и железобетонных конструкций щиты и другие элементы опалубки делают с учетом их много кратного использования. Стоимость опалубки составляет 20-30% общей стоимости бетонных и железобетонных конструкций
Производство опалубочных работ.
Деревянную и фанерную опалубки и элементы поддерживающих их деревянных лесов рационально изготовлять в опалубочных цехах деревообделочных комбинатов. При малых объемах работ и отдаленности объектов от центральных мастерских деревянная опалубка может быть изготовлена в приобъектных опалубочных мастерских.
Для правильной сборки и разборки опалубки последняя маркируется. Опалубщики работают по маркировочному или установочному чертежу, состоящему из плана сооружения с нанесенными элементами железобетонной конструкции и присвоенными им марками. Сборка опалубки производится с применением шаблонов, кондукторов и других приспособлений, обеспечивающих точность работ при минимальных затратах труда.
При наличии на строительной площадке кранов достаточной грузоподъемности опалубку следует собирать в укрупненные блоки и устанавливать этими кранами.
АРМАТУРНЫЕ РАБОТЫ
В железобетоне арматурой называются стальные стержни различного сечения и формы, стальные канаты и пряди, воспринимающие растягивающие и скалывающие напряжения, возникающие в железобетонных элементах от внешних нагрузок и собственного веса конструкций. Арматура может быть постоянного сечения (гладкие стержни) и периодического профиля.
БЕТОННЫЕ РАБОТЫ
Подготовка объектов бетонирования.
До начала бетонирования необходимо проверить правильность установки арматуры и закладных частей, наличие бетонных подкладок для соблюдения защитного слоя. Если арматура, анкерные болты, опорные плиты и т. п. были установлены задолго до укладки бетонной смеси и коррозировали, они должны быть очищены от ржавчины, которая снижает сцепление бетона с металлом и отрицательно влияет на качество конструкции. Качество и положение арматуры и закладных частей фиксируется актом.
Работы по бетонированию массивных конструкций должны быть организованы на основе типовых технологических карт, составленных с учетом опыта передовых строек и в каждом отдельном случае уточненных и привязанных к местным условиям строительства данного объекта.
Технологические карты, разработанные по определенной методике, содержат в своем составе следующие разделы: область применения; основные указания по выполнению комплексного процесса бетонирования; суточный график выполнения работ; схема организации работ; потребность в материально-технических ресурсах; технико-экономические показатели. К технологической карте должна быть приложена производственная калькуляция трудовых затрат, которая служит для составления наряда на производство работ.
Приготовление бетонной смеси, транспортировка, укладка и уплотнение.
Бетонная смесь должна обладать свойствами, обеспечивающими заданную прочность бетона. Бетонная смесь должна удовлетворять следующим требованиям: сохранять при транспортировании, перегрузке и укладке в опалубку свою однородность, достигнутую при перемешивании; обладать соответствующей консистенцией, способностью хорошо формоваться и уплотняться; обладать удобоукладываемостью для быстрого и плотного заполнения опалубки, всех промежутков между арматурными стержнями.
Различают подвижные (пластичные) смеси, способные укладываться в опалубку и уплотняться под действием собственного веса, и жесткие, требующие для своего уплотнения приложение внешних сил (вибрирование, виброштампование, вибропрокат). Жесткие смеси содержат ограниченное количество воды; смесь при этом отличается большой насыщенностью крупного заполнителя (щебнем или гравием). Применение жестких бетонных смесей способствует повышению прочности бетона, более экономному расходованию цемента и ускорению оборачиваемости опалубки. В процессе приготовления жестких смесей требуется точная дозировка воды, так как даже незначительные отклонения содержание ее в смеси резко изменяют ее свойства.
При осуществлении бетонных и железобетонных работ широкие применение нашли малоподвижные смеси, которые по структуре и повышенному содержанию цементного теста приближаются к пластичным смесям, а из-за уменьшенного содержания воды обладают положительными свойствами жесткой бетонной смеси.
Степень подвижности пластичных бетонных смесей оценивают мри помощи стандартного конуса, в который укладывают бетонную смесь. После снятия формы бетон под собственным весом оседает; величина осадки в мм характеризует подвижность бетонной смеси.
Бетонная смесь, как правило, приготовляется на бетонных заводах и доставляется на строительство специализированными автомашинами. В необходимых случаях приготовление бетона может быть организовано в бетонорастворных узлах непосредственно на строительной площадке. Бетонные заводы или бетонные узлы на строительной площадке состоят из складов цемента, песка и гравия (или щебня), дозировочных устройств, бетоносмесительных машин и бункеров для готового бетона. Бетонные заводы и установки оборудуются водоснабжением и средствами автоматизации производства и механизации подъемно-транспортных работ.
Дозирование составляющих материалов при приготовлении бетонной смеси механизированным способом производится по весу.
Дозирование воды не по весу, а по объему допускается только на бетонных заводах непрерывного действия.
Бетонная смесь, доставляемая к месту укладки, должна быть однородной и удобоукладываемой. Расслоившуюся при перевозке бетонную смесь, потерявшую прочность перед укладкой, необходимо вновь хорошо перемешать до полного восстановления однородности.
Укладка бетонной смеси производится слоями с тщательным их уплотнением, от качества уплотнения зависят плотность, прочность и долговечность бетона. Для уплотнения бетона применяются электромеханические, электромагнитные и пневматические вибраторы.
Уплотнение бетона и ускорение его твердения возможно при помощи вакуумирования, т.е. искусственное удаление лишней влаги, которая замедляет процесс схватывания и не позволяет достичь более полного уплотнения.
Зимой же укладку бетонной смеси следует производить после отогрева промороженного основания. Допускается укладывать смесь на не отогретое непучинистое основание или старый бетон при выдержании бетона в конструкции способом термоса, при предварительном разогреве бетонной смеси, а также пре применении бетона с противоморозными добавками.
РАСПАЛУБЛИВАНИЕ КОНСТРУКЦИЙ
Нарастание прочности бетона в определенные сроки контролируется лабораторией путем испытания серий образцов. С учетом прочности бетона назначаются сроки распалубливания бетонных и железобетонных конструкций.
Перед началом распалубливания открытые бетонные поверхности осматривают и обстукивают. При распалубливания необходимо сохранять опалубку от повреждений, чтобы снизить расходы на ее ремонт.
Процесс распалубливания всегда начинают с удаления боковых элементов опалубки, не несущих нагрузки от собственною веса конструкций. Летом при температуре наружного воздуха 15—20° боковые поверхности распалубливают через 2—3 дня.
Несущая опалубка железобетонных конструкций небольших пролетов снимается примерно через 10—12 дней в зависимости от вида конструкции, температуры наружного воздуха, марки и вида цемента, величины и характера нагрузок и т. д. Эти сроки определяют применительно к виду конструкций, исходя из требуемой прочности бетона к моменту распалубки.
9. Специальные методы бетонирования
При невозможности или неэффективности применения традиционной технологии бетонирования применяют специальные методы, к которым относятся вакуумирование и торкретирование бетона, подводное бетонирование.
Вакуумирование бетона является технологическим методом, позволяющим извлечь из уложенной бетонной смеси около 10... 25% воды затворения с сопутствующим или дополнительным уплотнением. Метод дает возможность применять бетонные смеси с подвижностью до 10 см, что упрощает и удешевляет их распределение и уплотнение, достигая при этом существенного улучшения физико-механических характеристик затвердевшего бетона, соответствующих пониженному остаточному водоцементному отношению.
В зависимости от типа конструкции вакуумирование производят либо сверху, либо со стороны боковых поверхностей возводимой конструкции.
Горизонтальные и пространственные конструкции, например междуэтажные перекрытия, своды-оболочки, полы, вакуумируют сверху, применяя переносные жесткие вакуум-щиты или вакуумматы, а стены, колонны и другие развитые по высоте конструкции - со стороны боковых поверхностей, используя для этого вакуум-опалубку.
Конструктивно вакуум-щит представляет собой короб (обычно размером в плане 100x125 см) с герметизирующим замком по контуру. Герметизированная коробка верхнего покрытия щита выполняется из стали, водостойкой фанеры или стеклопластика. Снизу щит оборудован вакуум-полостью, непосредственно соприкасающейся с бетоном. Такая полость создается путем прокладки двух слоев металлической тканой и плетеной сеток, прикрепляемых на внутренней поверхности щита. Благодаря изогнутости проволок сетка в своем сечении образует сообщающиеся между собой мелкие (тонкие) воздушные каналы, которые в сумме и составляют тонкую воздушную прослойку (вакуум-полость).
В настоящее время вместо металлических переходят на использование некорродирующих, легких, штампованных из пластмасс сеток. Во избежание уноса из свежеуложенного бетона цементных частиц вся поверхность сетки, обращенная к бетону, покрывается фильтрующей тканью из нейлона или капрона. Для создания в вакуумполости разрежения, а следовательно, и удаления части воды затворения и воздуха в центре вакуум-щита установлен штуцер, подсоединяемый через трехходовой кран к источнику вакуума. По периметрувакуумщит имеет резиновый фартук для герметизации.
Вакуум-мат состоит из двух самостоятельных элементов: нижнего и верхнего. Нижний, укладываемый на бетон, представляет фильтрующую ткань, прошитую с распределительной сеткой из лавсана. Верхний элемент - герметизирующий. Его выполняют из плотной газонепроницаемой синтетической ткани и раскатывают поверх фильтрующего элемента. По продольной оси верхнего элемента расположен отсасывающий перфорированный шланг, подсоединяемый через штуцер к источнику вакуума.
Вакуум-опалубку изготовляют на основе обычной сборно-разборной опалубки. Для этого опалубочные щиты со стороны палубы оборудуют по высоте горизонтальными изолированными друг от друга вакуумполостями, которые по мере укладки бетонной смеси подключают к источнику вакуума. Вакуум-опалубку можно также собирать из вакуум-щитов, обеспечивая при этом неизменяемость их положения элементами жесткости и крепежными деталями.
В зависимости от условий вакуумирования бетона - с помощью вакуум-щитов (вакуумматов) или вакуумопалубок - физические процессы протекают по-разному.
При вакуумировании бетона вакуум-щитами (вакуумматами), имеющими возможность перемещения в сторону бетона, одновременно с отсосом воды и воздуха происходит дополнительное статическое уплотнение вследствие разности атмосферного давления и давления в вакуумполости. При этом величина действующего усилия достигает 70...75 кН/м2. С удалением от поверхности вакуумирования передаваемое на бетон давление снижается, так как часть нагрузки расходуется на преодоление сил внутреннего трения и развития контактных напряжений в твердой фазе.
Торкретирование бетона - технологический процесс нанесения в струе сжатого воздуха на поверхность конструкции или опалубки одного или нескольких слоев цементно-песчаного раствора (торкрет) или бетонной смеси (набрызгбетон) (в зарубежной практике носит наименование «шприцбетон»). Благодаря большой кинетической энергии, развиваемой частицами смеси, нанесенный на поверхности раствор (бетон) приобретает повышенные характеристики по прочности, водонепроницаемости, морозостойкости, сцеплению с поверхностями нанесения.
В состав торкрета входят цемент и песок, в состав набрызгбетона помимо цемента и песка входит крупный заполнитель размером до 30 мм. Растворы или бетонные смеси приготовляют на портлан-цементах не ниже М400.
Процесс нанесения слоя торкрета (набрызгбетона) включает две стадии: на первой стадии на поверхности нанесения происходит отложение пластичного слоя, состоящего из раствора с самыми мелкими фракциями заполнителя. Толщина слоя цементного молока и тонких фракций, способного поглотить энергию удара крупных частиц заполнителя и способного удержать крупные частицы, составляет 5... 10 мм; на второй стадии происходит частичное проникновение в растворный слой зерен более крупного заполнителя и таким образом образование слоя торкрета или набрызгбетона.
Торкретирование обычно сопровождается потерей некоторого количества материала, отскакивающего от поверхности нанесения - так называемый «отскок». Величина отскока частиц зависит от условий производства работ, состава смеси, размера крупных частиц заполнителя и кинетической энергии частиц при ударе. В начальной стадии нанесения почти все частицы крупного заполнителя отскакивают от поверхности и только цемент и зерна мелких фракций заполнителя удерживаются на ней. Поэтому первоначально наносимый слой толщиной до 2 мм состоит в основном из цементного теста. По мере увеличения толщины наносимого слоя более крупные частицы заполнителя начинают задерживаться в нем, после чего устанавливается постоянный процент отскока. Количественно величина отскока при торкретировании вертикальных поверхностей составляет 10... 20%, а при торкретировании потолочных поверхностей - 20... 30%. Уменьшение объема отскока достигается выбором оптимальных скоростей выхода смеси из сопла и расстояния от сопла до поверхности нанесения торкрета или набрызгбетона.
Торкретирование бетона осуществляют двумя способами: «сухим» и «мокрым».
При сухом способе исходная сухая смесь во взвешенном состоянии подается в насадку (сопло), в которую в нужном количестве поступает вода затворения. В сопле происходит перемешивание смеси с последующей подачей ее под давлением сжатого воздуха на бетонируемые поверхности.
При мокром способе в сопло под давлением сжатого воздуха поступает готовая смесь. В сопле смесь переводится во взвешенное состояние и под давлением наносится на бетонируемые поверхности («пневмобетонирование»).
Сухой способ применяют для нанесения торкрета, а мокрый - для торкрета и набрызгбетона. Каждый из способов характеризуется своими техническими средствами и особенностями выполнения операций.
Основные технические средства для торкретирования сухими смесями включают агрегат для нанесения смеси, компрессор, сопло, шланги для подачи к соплу сухой смеси, воздуха и воды. В отечественной практике в качестве агрегата для нанесения смеси преимущественно применяют двухкамерные цемент-пушки (СБ-117 и СБ-67А производительностью по сухой смеси соответственно 2 и 4 м3/ч). Колокольные затворы верхней и нижней камер обеспечивают шлюзование. В то время как сухая смесь из нижней камеры подается питателем к разгрузочному отверстию и сжатым воздухом выносится в материальный шланг, верхняя камера заполняется новой порцией сухой смеси. Таким образом обеспечивается непрерывность торкретирования.
Технологическая последовательность выполнения операций при данном способе такова: загрузка приготовленной сухой смеси в цемент-пушку; дозированная подача сухой смеси к разгрузочному устройству цемент-пушки для пневмотранспорта ее по шлангам; транспортирование сухой смеси в струе сжатого воздуха и по шлангам к соплу; дозированная подача в сопло воды под давлением и перемешивание раствора в сопле; нанесение на торкретируемую поверхность готовой смеси, выходящей факелом из сопла с высокой скоростью.
Для торкретирования сухим способом используют чистый песок влажностью не более 6%, модулем крупности 2,5...3 при максимальной крупности отдельных зерен 5 мм (допускается гравий предельной крупностью 8 мм). Диапазон соотношения между массой цемента и песком 1:3... 1:4,5. Содержание цемента в торкрете составляет 600...800 кг/м3 при фактическом водоцементном отношении при выходе из сопла 0,32...0,37. При меньшем В/Ц имеют место пыление и недостаточное смачивание сухих составляющих, при больших - оплывание уложенного слоя.
Избыточное давление воздуха в цемент-пушке принимают обычно 0,2...0,3 МПа, что обеспечивает выход из сопла увлажненной смеси со скоростью 100 м/с. Для получения плотного слоя торкрета равномерной толщины сопло при нанесении держат на расстоянии 0,7... 1 м от поверхности нанесения, перемещают его круговыми движениями, а струю смеси направляют перпендикулярно ей. Чтобы не допускать всплывания, толщина слоев, одновременно наносимых торкретированием, должна быть не более 15 мм при нанесении на горизонтальные (снизу вверх) или вертикальные неармированные поверхности и 25 мм при нанесении на вертикальные армированные поверхности. При наличии нескольких слоев последующий слой наносят с интервалом, определяемым из условия, чтобы под действием струи свежей смеси не разрушался предыдущий слой (определяется опытным путем).
Основными техническими средствами при мокром способе торкретирования являются нагнетатели (пневмоустановки и различные насосы).
В отечественной практике при мокром способе торкретирования преимущественно применяют растворные смеси на мелких песках с добавкой каменной мелочи фракции 3... 10 мм в количестве до 50% от общей массы заполнителя. Для нанесения смеси на поверхности используют установки «Пневмобетон» различных модификаций, в состав которых входят: приемно-перемешивающее устройство со смесителем принудительного действия; вибросито с ячейками 10 х 10 мм; питатель; материальный трубопровод; воздушный трубопровод; сопло для нанесения смесей. В качестве питателя установки «Пневмобетон» используют серийные растворонасосы С-683, С-684 и С-317Б номинальной подачей соответственно 2, 4 и 6 м3/ч, переоборудованные на прямоточную схему и дополнительно оборудованные смесительной камерой. Воздух к смесительной камере подают под давлением 0,4...0,6 МПа, что обеспечивает выход струи смеси из сопла со скоростью 70...90 м/с и образование распыленного факела.
Технологическая последовательность выполнения операций при данном способе такова: загрузка в нагнетатель заранее приготовленной растворной или бетонной смеси; нагнетание готовой смеси по шлангам к соплу; подача к соплу сжатого воздуха, эжектирующего поступающую по шлангам готовую смесь для увеличения скорости ее выхода из сопла; нанесение на торкретируемую поверхность факела готовой смеси.
Для качественного нанесения слоев бетона (раствора) установкой «Пневмобетон» руководствуются следующим: сопло при нанесении смеси располагают перпендикулярно поверхности (допускается отклонение сопла на небольшой угол при заполнении пространства за арматурными стержнями диаметром более 16 мм); сопло должно находиться на расстоянии 0,7... 1,2 м от рабочей поверхности, чтобы максимально уменьшить «отскок»; на вертикальные поверхности смесь наносят снизу вверх; толщина единовременно наносимого слоя не должна превышать 15 мм при нанесении на горизонтальные (снизу вверх) поверхности, 25 мм при нанесении на вертикальные поверхности и 50 мм при нанесении на горизонтальные (сверху вниз) поверхности. При появлении признаков сползания смеси необходимо уменьшить толщину наносимого слоя; при нанесении первого слоя на опалубку или затвердевший бетон используют мелкозернистую смесь, что уменьшает потери материалов на «отскок»; толщина этого слоя не должна превышать 10 мм; для получения ровной поверхности после схватывания последнего нанесенного слоя цемента поверхность дополнительно отделывают раствором на мелком песке, который тут же заглаживают.
Торкретирование бетона в общем случае не конкурентоспособно традиционной технологии бетонных работ. Этот процесс сравнительно дорогой, трудоемкий и малопроизводительный. Применяют его при невозможности возвести традиционными методами бетонирования конструктивные элементы толщиной в несколько сантиментров (особенно при применении пневмоопалубок), когда требуется получение материала повышенных свойств, для нанесения туннельных обделок, при устройстве защитных слоев на поверхности предварительно напряженных резервуаров, для ремонта и усиления железобетонных конструкций, для замоноличивания стыков и др.
Подводное бетонирование - укладка бетонной смеси под водой без производства водоотлива. Применяют следующие методы подводного бетонирования: метод вертикально перемещаемой трубы, метод восходящего раствора, укладку бетонной смеси бункерами, метод втрамбовывания бетонной смеси.
Метод вертикально перемещаемой трубы (ВПТ) применяют при бетонировании элементов конструкций на глубине до 50 м, защищенных от проточной воды, высокой прочности и монолитности возводимой конструкции.
В качестве ограждения используют шпунтовые стенки, специально изготовленную опалубку в виде пространственных блоков (ящиков) из дерева, железобетона, металла либо конструкции (плиты-оболочки, опускные колодцы и др.). Конструкция ограждения должна быть непроницаемой для цементного раствора. Для производства работ над ограждением устраивают рабочую площадку, на которой устанавливают траверсу. К траверсе подвешивают стальной бетоновод, собираемый из отдельных бесшовных труб длиной 1... 1,2 м и диаметром 200... 300 мм на легкоразъемных водонепроницаемых соединениях. Сверху бетоновод оборудован воронкой для приема бетонной смеси, снизу - металлическим клапаном, который открывается в момент подачи бетонной смеси. Радиус действия бетонолитной трубы не более 6 м. Число труб, устанавливаемых в заопалубленном пространстве, определяют с учетом обязательного перекрытия всей площади бетонирования круговыми зонами действия труб.
В начале бетонирования трубы опускают до дна с минимальным зазором, допускающим свободный выход смеси. В полость трубы вводят пакет из мешковины, а через загрузочную воронку подают бетонную смесь, под тяжестью которой пыж опускается к основанию трубы и вытесняет из нее воду. Бетонирование без подъема трубы продолжают до тех пор, пока бетонная смесь, заполнив все пространство бетонируемого блока, не поднимется выше конца трубы на 0,8 при глубине бетонирования до 10 м и не менее чем на 1,5 м при глубине до 20 м. Затем, не прекращая подачи бетонной смеси, трубу поднимают с таким расчетом, чтобы нижний ее конец постоянно располагался не менее чем на 0,8... 1,5 м ниже поверхности бетона.
По окончании подъема трубы на высоту звена бетонирование приостанавливают, демонтируют верхнее звено трубы, переставляют воронку, после чего подачу бетонной смеси возобновляют. Блок бетонируют до уровня, превышающего проектную отметку на величину, равную 2% его высоты, но не менее чем на 100 мм, с последующим удалением слабого верхнего слоя.
По достижении бетоном прочности 2... 2,5 МПа верхний слабый слой бетона, непрерывно соприкасающийся с водой во время производства работ, удаляют.
При методе ВПТ применяют бетон класса не ниже В25, бетонную смесь, укладываемую с вибрацией, подвижностью 6... 10 см и укладываемую без вибрации подвижностью 16...20 см. Приготовляют смесь на гравии или смеси гравия с 20... 30% щебня, обязательно вводя пластифицирующие добавки.
Метод восходящего раствора (ВР) бывает безнапорным и напорным. При безнапорном методе в бетонируемый блок устанавливают шахту с решетчатыми стенками (рис. 7.55, б), на всю глубину которой опускают стальную трубу 038... 100 мм, собранную из звеньев длиной до 1 м с водонепроницаемыми легкоразъемными соединениями. В заопалубленное пространство отсыпают каменную наброску (крупностью 150...400 мм для бутобетонной кладки и крупностью 40... 150 мм для бетонной кладки), пустоты которой заполняют раствором, подаваемым через трубу. Заливку каменной наброски при бутобетонной кладке производят цементным раствором состава 1:1... 1:2, а при бетонной - цементным тестом. Цементный раствор и цементное тесто, подаваемое в шахту через трубу, должны свободно растекаться и обволакивать заполнитель. Поэтому для приготовления раствора применяют мелкие пески крупностью зерен не более 2,5 мм и с содержанием не менее 50% частиц не более 0,6 мм. Подвижность раствора должна быть 12... 15 см по конусу СтройЦНИЛа. Радиус действия каждой трубы 2...3 м. Заглублять трубы в укладываемый раствор необходимо на глубину не менее 0,8 м. По мере повышения уровня укладываемого раствора трубы поднимают, демонтируя их верхние звенья. Уровень раствора доводят на 100... 200 мм выше проектной отметки. Когда кладка достигнет прочности 2...2,5 МПа, излишек раствора удаляют.
При напорном методе заливочные трубы устанавливают без шахт в каменный или щебеночный заполнитель и через них нагнетают (инъецируют) под давлением цементный раствор (тесто).
Метод ВР применяют при укладке бетонной смеси на глубине до 20 м.
При методе укладки бункерами бетонную смесь опускают под воду на основание (или ранее уложенный слой) бетонируемого элемента в раскрывающихся ящиках, бадьях или грейферах и разгружают через раскрытое отверстие. Закрытые сверху бункера имеют уплотнение по контуру закрывания, которое препятствует вытеканию цементного теста и прониканию воды внутрь бункера. Бетонную смесь выпускают при минимальном отрыве дна бункера от поверхности уложенного бетона, исключая тем самым возможность свободного сбрасывания бетонной смеси через толщу воды. Метод технологически прост, не требует устройства подмостей и допускает укладку бетонной смеси на неровное основание с большими углублениями и возвышениями. Однако бетонная кладка характеризуется слоистостью. Метод применяют при глубине до 20 м и если класс укладываемого бетона не выше В20.
Втрамбовывание бетонной смеси начинают с создания бетонного островка в одном из углов бетонируемой конструкции при подаче смеси по трубе или бадьей с открывающимся дном. Островок должен возвышаться над поверхностью воды не менее чем на 30 см. Для втрамбовывания применяют бетонную смесь подвижностью 5...7 см. Подводный откос островка, с которого начинают втрамбовывание, должен образовывать под водой угол 35...45° к горизонтали. Новые порции бетонной смеси втрамбовывают в островок равномерно с интенсивностью, не нарушающей процесс твердения уложенного бетона, и не ближе 20...30 см от кромки воды. Этим приемом обеспечивается защита от соприкосновения с водой новых порций бетонной смеси.
Метод применяют при глубине воды до 1,5 м для конструкций больших площадей при классе бетона до В25.
10. Основные, подготовительные и транспортные работы при монтаже строительных конструкций
Транспортные процессы состоят из транспортирования конструкций на центральные и приобъектные склады, погрузки и разгрузки конструкций. сортировки и укладки их на складах, подачи конструкций с укрупнительной сборки или складов на монтаж, транспортирование материалов, полуфабрикатов, деталей и приспособлений в зону монтажа. При складировании конструкций особо контролируют их качество, размеры, маркировку и комплектность. При монтаже зданий транспортных средств исключаются процессы разгрузки и сортировки, так как конструкции сразу подаются на монтаж.
IIодготовительные процессы включают: проверку состояния конструкций, укрупнительную сборку, временное (монтажное) усиление конструкций, подготовку к монтажу и обустройство, подачу конструкций в виде монтажной единицы непосредственно к месту установки. дополнительно входят процессы по оснастке конструкций приспособлениями для временного их закрепления и безопасного выполнения работ, нанесение установочных рисок на монтируемые элементы, навеска подмостей и лестниц, если это требуется выполнить до подъема конструкций.
Транспортирование сборных строительных Конструкций, В зависимости от места расположения монтируемого объекта и принятой организации монтажных работ могут быть следующие варианты доставки сборных конструкций:
железнодорожным транспортом от завода-изготовителя к месту укрупнительной сборки или непосредственно в зону монтажа. Этим вариантом в основном пользуются для перевозки металлических конструкций, доставляемых с заводов-изготовителей отправочными марками;
автомобильным транспортом от завода-изготовителя к месту складирования или в зону монтажа. Так доставляют сборные железобетонные конструкции, изготовляемые, как правило, на близ расположенных предприятиях;
водным транспортом от завода-изготовителя к месту промежуточной разгрузки. Этот вариант может оказаться выгодным при расположении завода-изготовителя конструкций и строящегося объекта в непосредственной близости от водной магистрали;
воздушным транспортом от завода-изготовителя к строящемуся объекту. Этот вариант применяют, когда доставка конструкций другим видом транспорта невозможна.
Основными технологическими условиями при перевозке сборных конструкций является обеспечение их сохранности, а также доставка в последовательности и сроки, обусловленные графиком производства монтажных работ. Сохранность конструкций гарантирована при перевозке их на специализированных транспортных средствах. В качестве специализированных транспортных средств используют автомобили грузоподъемностью 4... 16 т, автомобили с прицепами, автопоезда в составе тягача с полуприцепом в выше панелевоза, фермовоза, блоковоза, специально оборудованные железнодорожные платформы грузоподъемностью 20...60 т и др.
Конструкции, рассчитанные на работу в вертикальном положении, н изделия из легких бетонов толщиной менее 200 мм, как правило, транспортируют в вертикальном положении. Так, в вертикальном или наклонном положении перевозят стальные и железобетонные фермы, стеновые панели, железобетонные балки, прогоны и др. При этом опирают их в двух точках, обозначенных в рабочих чертежах. Стальные элементы решетчатых конструкций при перевозке в горизонтальном положении опирают в местах узлов, сплошные — в местах расположения ребер жесткости. В отдельных случаях при перевозке длинномерных гибких элементов временно усиливают, что обеспечивает необходимую жесткость. При перевозке не должны быть превышены установленные дорожные габариты. Так, автомобильным транспортом без специального разрешения ГАП можно перевозить Конструкции, если Высотный габарит груженого транспортного средства не превышает 3,8 м, ширина 2,5 м и свесы не более 2 м. длина автопоезда, используемого для перевозки, не должна превышать 20 м при наличии одного прицепа и 24 м — при двух прицепах.
При монтаже с транспортных средств конструкции доставляют в соответствии с почасовым графиком монтажа, в котором указывают рабочую смену, номер и продолжительность рейса, марку и число конструкций, перевозимых за один рейс, время прибытия машины.
Складирование сборных строительных конструкций. В зависимости от принятой организации монтажных работ складирование сборных конструкций может осуществляться на промежуточной площадке или непосредственно у монтируемого объекта в зоне действия монтажного крана. В последнем случае учитывают последовательность монтажа, массу монтажных элементов и грузоподъемность монтажного крана на соответствующем вылете крюка. I-1 промежуточный склад обычно доставляют металлоконструкции, когда площадку этого склада используют для укрупнительной сборки конструкций.
Приобъектвые склады устраивают, когда невозможно вести монтаж непосредственно с транспортных средств.
Площадь складов строительных конструкций состоит из грузовой площадки, занятой конструкциями, и оперативной, занятой проходами, проездами, местами стоянки транспортных средств под разгрузкой и т. д.
Необходимую площадь складов строительных конструкций определяют во формуле
Г=РК0, (клв м8)
Где Р— масса (или объем) конструкции, подлежащей хранению на складе, т
(клв м8); — удельная загрузка грузовой площади складов, т/м2 (или м3/м2);
К0 коэффициент, учитывающий величину оперативной площади, принимаемый
11. Разработка грунта одноковшовым экскаватором
Одноковшовые строительные экскаваторы (ЭО) относятся к машинам циклического действия.
Главный параметр ЭО - вместимость ковша, м3.
Основные технологические параметры:
- глубина (высота) копания,
- максимальный радиус копания,
- высота погрузки.
В строительстве работают экскаваторы восьми размерных групп, имеющие вместимость ковша 0,15...4,0 м3. Наибольшее распространение находят экскаваторы 4-й и 5-й групп (вместимость ковша 0,65 и 1 м3). На ряде моделей устанавливаются устройства, автоматизирующие отдельные операции рабочего процесса экскаватора. При помощи традиционного оборудования (прямая лопата, обратная лопата, драглайн, грейфер) одноковшовый экскаватор может быть использован на механизации следующих процессов переработки грунта, входящих в состав комплексного технологического процесса: разработка и укладка грунта в земляных сооружениях различных типов; погрузка грунта; перемещение грунта в пределах земляного сооружения.
Большинство одноковшовых строительных экскаваторов - это универсальные машины, которые могут быть оснащены различными видами сменного рабочего оборудования. Использование сменного рабочего оборудования дает возможность механизировать такие процессы, как: зачистка дна выемок; дробление и удаление негабаритов и валунов; отделка поверхности откосов земляного сооружения, дна выемок; послойное уплотнение грунта в стесненных условиях, при устройстве обратных засыпок; рыхление мерзлого и трудноразрабатываемого грунта.
Для погрузки ранее разработанного грунта, снятия верхнего слоя и для планировочных работ применяют погрузочное оборудование. Проведение земляных работ, например, при разработке траншей под инженерные коммуникации, часто сопровождается сопутствующими работами, связанными с подачей оборудования, материалов, грузов. В этом случае используется крановое оборудование.
Одноковшовый экскаватор - машина цикличного действия, процесс разработки грунта при любом виде рабочего оборудования складывается из чередующихся в определенной последовательности операций отдельного цикла:
- резание грунта и заполнение ковша;
- подъем ковша с грунтом;
- поворот экскаватора вокруг оси к месту выгрузки;
- выгрузка грунта из ковша;
- обратный поворот экскаватора;
- опускание ковша на грунт и подача его для резания грунта.
Основное назначение экскаваторов - разработка выемок, резервов, карьеров, траншей, котлованов с разгрузкой грунта в отвал или погрузкой в транспортные средства.
Предельные размеры выемок, которые могут быть разработаны одноковшовым экскаватором с одной стоянки, зависят от его рабочих параметров.
Разработку грунта одноковшовыми экскаваторами ведут позиционно. Рабочая площадка экскаватора называется забоем.
Забой - рабочая зона экскаватора, включающая площадку, где расположен экскаватор; часть разрабатываемого массива грунта; места установки транспортных средств; площадку для укладки разрабатываемого грунта (при работе в отвал).
По окончании разработки грунта в данном забое экскаватор перемещается на новую позицию экскаватор и транспортные средства должны быть расположены в забое таким образом, чтобы среднее значение угла поворота экскаватора от места заполнения ковша до места его выгрузки было минимальным, так как поворот стрелы осуществляется дважды - с грузом до транспортного средства и после выгрузки, то время поворота в среднем составляет до 70% рабочего времени одного цикла экскаватора.
В зависимости от условий строительной площадки выбор экскаватора начинают с определения наиболее целесообразных вместимости ковша и типа экскаватора, а также требуемых параметров - длины стрелы, радиуса резания, выгрузки и др. Выбор сменного оборудования экскаватора зависит от уровня грунтовых вод и характера разрабатываемой выемки (траншея, узкий или широкий котлован).
Экскаватор «прямая лопата» используют для разработки грунтов, расположенных выше уровня стоянки экскаватора, преимущественно с погрузкой на транспорт. Его широко применяют в карьерах, в строительстве используют для погрузки в транспортные средства ранее собранного в кучи (сплоченного) фунта или для отрывки котлованов, при этом устраивается самим экскаватором пандус - съезд в котлован с уклоном 10...15% для экскаватора и транспортных средств.
Прямая лопата представляет собой открытый сверху ковш с режущим передним краем. Ковш шарнирно соединен с рукоятью, которая, в свою очередь, шарнирно соединена со стрелой машины и выдвигается вперед при помощи напорного механизма. Конструкция экскаватора позволяет ему копать ниже уровня своей стоянки не более чем на 10...20 см, нормативная производительность может быть достигнута при высоте забоя не менее 1,5 м. Опорожняется ковш путем открытия его днища. Такая конструкция прямой лопаты обеспечивает ей наибольшую производительность за счет наполнения ковша «с шапкой».
При разработке грунтов 1-й и 2-й групп экскаватор может быть снабжен ковшом увеличенного объема. Экскаватор применяется в основном при необходимости погрузки грунта в транспортные средства. Нецелесообразно использование экскаватора, если уровень грунтовых вод выше подошвы выемки, так как движение экскаватора и транспортных средств по мокрому грунту затруднено.
Разработку фунта экскаватором «прямая лопата» производят лобовым и боковым забоями.
Лобовой забой применяют при разработке экскаватором грунта впереди себя и отгрузке его на транспортные средства, которые подаются к экскаватору по дну забоя или сбоку по естественной поверхности земли. В первом случае автомобили подходят задним ходом попеременно то с одной, то с другой стороны забоя, размер которого понизу не должен быть менее 7 м. При таких условиях работы угол поворота экскаватора достигает 140...1800, что значительно снижает его производительность. По этим причинам лобовой забой принимают крайне редко, в основном при устройстве въездного пандуса в котлован или при разработке первой (пионерской) проходки.
При узких забоях самосвалы подают под загрузку с одной стороны сзади экскаватора, а при нормальных — с обеих сторон от экскаватора попеременно, что исключает простои экскаватора при смене под загрузкой транспортных средств. При данных забоях экскаватор перемещается в котловане прямолинейно по оси забоя.
В некоторых случаях разработку грунта предпочтительнее вести уширенным забоем с перемещением экскаватора по зигзагу. В таких забоях сокращаются холостые проходки экскаватора и облегчаются условия для маневрирования и установки под погрузку самосвалов.
Разработка выемок способом лобового забоя затруднительна для перемещения и установки под погрузку самосвалов. Средний угол поворота экскаватора для погрузки грунта в транспортные средства, особенно при работе в узких забоях может достигать 180°, что значительно увеличивает время рабочего цикла экскаватора и снижает его производительность. Кроме этого для спуска экскаватора в забой с дневной поверхности ему необходимо выкопать пандус - наклонную аппарель со значительным объемом грунта, который также необходимо переместить от котлована. По этим причинам применение лобового забоя ограничено.
Более эффективным является разработка грунта боковым забоем, когда заполнение ковша грунтом осуществляется преимущественно с одной стороны движения экскаватора и частично впереди себя. По этой схеме транспорт подается под загрузку сбоку выработки, чем достигается значительное уменьшение угла поворота стрелы экскаватора (в пределах 70...900) при погрузке грунта в транспортные средства. В боковых забоях транспортные пути проходят параллельно оси перемещения экскаватора и, как правило, на уровне его стоянки.
Продолжительность загрузки автосамосвала колеблется в широких пределах в зависимости от числа ковшей с грунтом, загружаемых в кузов, рода грунта и его плотности, среднего угла поворота машины при загрузке и типа экскаватора.
Строительные экскаваторы «прямая лопата» применяют с ковшом вместимостью 0,15...2,5 м.
Экскаватор «драглайн» используют для разработки грунтов, расположенных ниже уровня стоянки экскаватора: для отрывки глубоких котлованов, широких траншей, возведения насыпей, разработки грунта из-под воды и т. п. Драглайн применяют также при планировке площадей и зачистке откосов. Достоинство экскаватора - радиус действия до 10 м и глубина копания до 12 м. Глубина копания у экскаватора практически неограничена, конструкция машины позволяет располагать транспортные средства на дневной поверхности и на дне котлована, т. е. уровень грунтовых вод не оказывает влияния на работу экскаватора. Эффективно разрабатывать экскаватором мягкие и плотные грунты, в том числе обводненные.
Ковш экскаватора навешивается на канатах на удлиненную стрелу кранового типа. Забрасывая ковш в выемку на расстояние, несколько превышающее длину стрелы, ковш заполняют грунтом путем подтягивания по поверхности земли к стреле. Затем ковш поднимают в горизонтальное положение и поворотом машины перемещают к месту разгрузки. Опорожняется ковш при ослаблении натяжения тягового каната.
Применимы разработки грунта лобовой и боковой проходками с отгрузкой грунта в транспорт и отвал. В зависимости от ширины выемки, способа разгрузки грунта (в отвал или в транспортные средства) и особенностей земляного сооружения, в практике нашли применение челночные способы разработки грунта, так как конструктивное решение экскаватора позволяет применять такие схемы.
Поперечно-челночная схема дает возможность набирать грунт поочередно с каждой боковой стороны самосвала, подаваемого под погрузку по дну выемки, не прекращая поворота стрелы в момент выгрузки грунта. При продольно-челночной схеме грунт набирают перед задней стенкой кузова и, подняв ковш, разгружают его над кузовом. В цикле работы экскаватора повороты занимают основное время, в этом плане челночные схемы с минимальным углом поворота для погрузки и выгрузки являются оптимальными. Благодаря уменьшению высоты подъема ковша и сокращению угла поворота экскаватора (при продольно-челночной схеме около 0°, а при поперечно-челночной 9...200) производительность экскаватора увеличивается в 1,5...2 раза. Строительные экскаваторы «драглайн» применяют с ковшом вместимостью 0,25...2,5 м3
Грейфер используют в сугубо специфических случаях для отрывки узких глубоких котлованов, траншей, колодцев, при разработке грунта ниже уровня грунтовых вод. Он представляет собой ковш с двумя или более лопастями и канатным или в последнее время стоечным приводом, принудительно смыкающим лопасти. Грейфер навешивается на стрелу и разрабатывает выемки с вертикальными стенками. При повороте стрелы ковш перемещается к месту разгрузки и опорожняется при принудительном раскрытии лопастей. Погружение в грунт осуществляется только за счет собственной массы и принудительного опускания стойки, поэтому можно разрабатывать грунты малой и высокой плотности, в том числе и находящиеся под водой. Строительные экскаваторы «грейфер» применяют с ковшом вместимостью 0,35...2,5 м3.
Экскаватор «обратная лопата» применяют при разработке фунтов ниже уровня стоянки экскаватора, в основном при отрывке котлованов глубиной до 6 м и траншей при глубине до 7,6 м. Затраты времени на один цикл экскаватора с обратной лопатой на 10... 15% больше, чем у прямой лопаты. Поярусная разработка выемок при этом виде оборудования не практикуется.
Обратная лопата - это открытый снизу ковш с режущим передним краем, шарнирно соединенный с рукоятью, которая, в свою очередь, шарнирно соединена со стрелой. По мере протягивания назад ковш заполняется грунтом. Затем при вертикальном положении рукояти ковш переводят к месту выгрузки и разгружают путем подъема с одновременным опрокидыванием.
Разработку грунта экскаватором «обратная лопата» производят боковым и лобовым забоями с погрузкой грунта в транспорт или в отвал (рис. 5.14). При боковом забое экскаватор разрабатывает выемки сбоку, ширина выемки ограничена радиусом резания, разработка грунта осуществляется поперек гусеничной ленты, т. е. при наименее устойчивом положении экскаватора. При лобовом забое черпание грунта производят при постепенном движении экскаватора задним ходом, разгрузку выполняют в транспортные средства, которые подаются к экскаватору по дну забоя или сбоку по естественной поверхности земли. Ширина забоя ограничивается только требованием нормальной производительности механизма. При лобовом забое экскаватор опускает стрелу с рукоятью в самое нижнее положение между гусеницами, поэтому глубина разработки узких траншей больше, чем широких.
Отрывку котлованов шириной до 14 м обычно осуществляют лобовой проходкой при перемещении экскаватора по зигзагу, а при большей ширине - поперечно-торцевой или продольно-торцевой.
12. Организация рабочего места и труда каменщика. Рабочее место каменщика
Рабочее место каменщика или звена включает участок возводимой стены, пространство, где размещаются рабочие, необходимые материалы, инструмент и приспособления. Рабочее место может находиться на земле, на межэтажных перекрытиях, на рабочих подмостях и на лесах.
При выполнении каменной кладки производительность труда каменщиков зависит от организации рабочего места (рис. 7.9), исключающей не относящиеся к процессу движения рабочих, и обеспечивающей минимальные расстояния перемещения кирпича и раствора от места складирования к месту укладки.
Рабочее место должно находиться в зоне действия монтажного крана. Практика подсказала, что общая ширина рабочего места должна быть 2,5...2,6 м, в том числе:
рабочая зона — шириной 0,6...0,7 м между стеной и материалами;
зона складирования материалов — полоса шириной 1,0...1,6 м дня размещения поддонов с кирпичом и ящиков с раствором;
транспортная зона при подаче материалов краном — 0,6...0,75 м, может доходить до 1,25 м дня передвижения рабочих, занятых доставкой и размещением материалов в пределах рабочей зоны.
Поддоны с кирпичом и ящики для раствора устанавливают длинной стороной перпендикулярно к оси возводимой стены, что сокращает затраты труда при наборе материалов. Число поддонов с кирпичом и ящиков с раствором и чередование их зависит от толщины возводи- мой стены, наличия проемов на данном участке кладки, сложности архитектурного оформления.
При кладке глухих стен расстояние между ящиками с раствором
Принимают 3,6 м, между ними устанавливают четыре поддона с кирпичом, керамическими блоками или камнями, расстояние между поддонами принимают 0,25...0,4 м. При кладке стен с проемами кирпич размещают против простенков на двух поддонах, а раствор — напротив проемов. Раствор на рабочее место подают в ящиках вместимостью до 0,27 м3, ящики устанавливают обычно напротив проемов, среднее расстояние между ними в пределах 2,0...2,5 м.
13. Технология возведения каркасных деревянных зданий
Строительство каркасных зданий начинают с возведения фундамента, выполняемого из железобетона или, в силу незначительного веса деревянных конструкций и здания в целом, из бетонных блоков. После проведения мероприятий по вертикальной и горизонтальной гидроизоляции по периметру здания устанавливают непрерывные балки пола первого этажа. Балки выполняют из толстых досок, устанавливаемых на кромки и сращиваемых по длине накладками из деревянных досок, расположенных внутри контура здания. Удлинение осуществляют с помощью гвоздей или болтов. Продольные периметральные балки связывают между собой промежуточными балками, устанавливаемыми через 50...70 см. Соединение продольных и поперечных балок осуществляют с помощью гвоздевых пластин.
Поверх смонтированной конструкции укладывают пол первого этажа. На следующем этапе монтируют стены и перегородки первого этажа, начиная с наружных. Для этого сначала на поверхности пола, в местах установки стен и перегородок, монтируют нижний пояс первого этажа в виде досок, устанавливаемых на их широкие стороны — пласты. Затем на горизонтальной поверхности собирают каркасы наружных и внутренних стен.
Каркас стены представляет собой прямоугольный фрагмент по длине, как правило, равный длине стены, но не превышающий 12 м, а по высоте равный высоте этажа. По периметру каркаса монтируют пластами толстые доски, а на расстоянии 70...90 см устанавливают дополнительные стойки, равные высоте этажа. В наружных стенах, в зонах установки окон и дверей монтируют проемообразователи для этих столярных изделий. Непосредственно над окнами или дверями устанавливают перемычку — усиленный деревянный элемент из бруса или из сплоченных досок, соединенных по ширине.
Под оконными проемообразователями устанавливают вертикальные стойки, соединяющие проемы с нижними балками каркаса.
Соединения всех элементов осуществляют на гвоздях или гвоздевых пластинах. Для придания пространственной жесткости и устойчивости фрагмент с внешней стороны обшивают листами влагостойкого гипсокартона. Гипсокартон соединяют с элементами каркаса шурупами. Собранный фрагмент каркаса устанавливают в проектное положение, поднимая его краном или вручную. Соединение с нижним поясом первого этажа осуществляют гвоздями, а для придания дополнительной пространственной жесткости и устойчивости фрагменты раскрепляют временными подкосами. Затем устанавливают каркасы внутренних стен перегородок. Их отличие от наружных заключается в отсутствии проемообразователей под окна и монтаже в проектное положение без обшивки гипсокартоном. Заканчивается возведение конструкций первого этажа монтажом балок перекрытия. К ним снизу прибивают конструкции обрешетки, являющиеся направляющими, к которым крепится потолок первого этажа. Поверх обрешетки укладывают звукоизоляцию, монтируют электротехническую и, если требуется, горизонтальную санитарно-техническую разводку.
После выполнения этих процессов укладывают подготовку пола второго этажа. Возведение конструкций второго этажа осуществляют в той же последовательности. Поверх верхнего пояса второго этажа монтируют несущие конструкции кровли. Как правило, их выполняют в виде ферм, изготавливаемых в заводских или построечных условиях, полностью подготовленных для монтажа в проектное положение. Для двухскатных крыш фермы устанавливают в поперечном направлении с шагом до 3 м. Для образования дополнительных скатов в трех- и четырехскатных крышах к крайним фермам в продольном направлении достраивают полуфермы изменяемой высоты. По верхним поясам ферм укладывают настил и покрытие в соответствии с описываемыми ранее решениями.
На следующем этапе в наружных и внутренних стенах монтируют электротехническую разводку и вертикальные санитар-но-технические стояки. Затем укладывают теплоизоляцию в наружные стены и звукоизоляцию во внутренние стены и перегородки, после чего их обшивают листами гипсокартона.
На последнем этапе осуществляют окончательную отделку помещений изнутри, а после облицовки фасада деревянными изделиями или декоративным камнем — его покраску снаружи. Прилегающую территорию благоустраивают.
Возведение каркасного здания площадью 250 м2 с установкой санитарно-технического и кухонного оборудования, с полной отделкой внутри дома и снаружи и благоустройство прилегающей территории комплексная бригада, состоящая из 6 рабочих, выполняет в течение 2,5...3мес.
14. Конструктивные особенности кирпичных стен
Кирпичные стены.
Самый распространенный кирпич — это обыкновенный глиняный красный. Годится и белый силикатный. Правда, его нельзя применять для кладки фундаментов, печей и каминов. Для облицовки стен используют лицевой (желтый) кирпич. Все кирпичи выпускаются либо полнотелыми, либо пустотелыми (эффективными), то есть с круглыми или прямоугольными сквозными отверстиями. Кстати, такие кирпичи обладают лучшими теплотехническими показателями. 250x120x65 мм или 250x120x88 мм. Широкие его грани называются соответственно верхней и нижней постелью, длинная боковая грань — ложком, короткая — тычком. Ряд кирпичей, уложенных длинной стороной вдоль стены, называется ложковым, а поперек стены — тычковым. Наружные ряды кладки называются верстой, внутренние (скрытые) — забуткой. На забутку используют кирпичи со сколами и далее бой (половняк). В магазине вам могут предложить и керамический камень. Это, по сути, тот же кирпич, но большего размера — 250x120x138 мм. Его выпускают только пустотелым. Прочность стены достигается перевязкой швов кладки — однорядной или многорядной. При однорядной системе, как правило, последовательно чередуются ложковые и тычковые ряды кладки либо комбинации из них (рис.1). Правда, такой способ требует более высокой квалификации каменщика, и к тому же на углы дома нужно заготовить много трехчетвертных кирпичей. Многорядная перевязка значительно проще. Здесь на один тычковый ряд приходится три-пять ложковых (рис.2), класть которые легче и быстрее. К тому же рисунок швов выглядит как дополнительный элемент украшения. Декоративность можно еще более усилить, если кладку лицевых поверхностей стен делать по трех-пятирядной системе и со сквозными вертикальными швами (рис.3). Тогда на наружную версту лучше брать лицевой (желтый) или отборный красный кирпич. Если для ложковых и тычковых рядов использовать кирпичи разного цвета, получится полосатая стена. Впрочем, об узорах мы поговорим позже. А сейчас вернемся к технологии строительных работ.
Толщина швов при любой системе перевязки должна быть около 10 мм. Через каждые 2 — 3 ряда проверяют горизонтальность кладки и при необходимости корректируют ее, уменьшая или увеличивая толщину шва, но не резко, а равномерно распределяя раствор на несколько рядов. Швы надо заполнять полностью и, пока раствор не высох, расшивать их, придав им выпуклую, вогнутую или треугольную форму. Если стену предполагается штукатурить, то швы оставляют пустыми примерно на глубину 1 см (у строителеи это называется вести кладку впус-тошовку). Начинают работу всегда от угла дома с тычкового ряда лицевой версты.
На (рис.4) показаны порядовки кладки толщиной в 1,5 кирпича простенков, углов, а также устройство четвертей проемов при многорядной системе перевязки. По краям оконных и дверных проемов для установки коробок закладывают с каждой стороны по две деревянные пробки размером в полкирпича. Их нужно обернуть одним слоем рубероида. Коробки перед установкой в проем также изолируют рубероидом. Разрез готовой кирпичной стены показан на (рис.5). Однако стены сплошной кладки из полнотелого кирпича толщиной более 38 см (то есть в 1,5 кирпича) экономически невыгодны. Во-первых, из-за того, что получается слишком большой расход строительных материалов, а во-вторых, тяжелые стены требуют соответственно и массивных фундаментов, что еще более увеличивает расход кирпича, цемента и т. д. Что в таком случае надо делать? Есть два варианта.
Первый — использовать эффективный (пустотный) кирпич.
Второй — строить из обыкновенного полнотелого кирпича, применяя облегченную кладку. Какие же конструкции ее можно предложить?
1. Стены, в толще которых сделаны воздушные промежутки шириной 4—6 см.
2. Стены, облицованные изнутри плитным утеплителем.
3. Стены с теплоизоляционной засыпкой между наружным и внутренним рядами кирпича и поперечными стенками (так называемая колодцевая кладка).
4. Стены с засыпкой и горизонтальными диафрагмами.
Все перечисленные конструкции существенно экономят кирпич и, несмотря на меньшую толщину кладки, сохраняют хорошие теплотехнические показатели. Судите сами. При температуре наружного воздуха —30° толщина стены с воздушным промежутком будет 54—56 см, стены с внутренним утеплением —25—38 см, а стены колодцевой кладки с различными засыпками — 51—58 см. Толщина стены сплошной кладки из эффективного кирпича при той же температуре равна 51 см. Как видите, наибольший выигрыш дает колодцевая кладка и кладка с внутренним утеплением. Если же учесть еще и то, что меньший вес стен позволяет делать более легкие фундаменты, экономия становится довольно существенной. Однако имейте в виду: подобные конструкции требуют очень аккуратного исполнения работ и особенно тщательной перевязки швов. В некоторых случаях горизонтальные швы нужно будет армировать стальной сеткой из тонкой проволоки. В кладке с воздушным промежутком, а также с внутренним утеплением можно использовать эффективный кирпич — он не только улучшит теплоизоляционные свойства стены, но и облегчит ее. Давайте подробнее разберем эти экономичные конструкции.
Стена с воздушным промежутком состоит из наружного ряда толщиной в полкирпича, воздушного промежутка и основного массива толщиной в один или полтора кирпича. (рис.6)
Такая стена рассчитана на температуру наружного воздуха от —20° до —30° (при использовании эффективного кирпича допустимые температуры будут —30—40°). Через каждые 4— 6 рядов обе кладки перевязывают тычковым рядом кирпичей по всей длине стены. Кирпичные связи можно заменить на армирование стальными прутками диаметром 6—8 мм с шагом 50 см.Для лучшего сцепления с раствором концы прутков нужно согнуть. И еще. Они не должны доходить до наружных граней стены на 4—6 см.
Стены с плитным утеплителем делают так.(рис.7).К обычной сплошной кладке с помощью растворных маяков (при этом образуется воздушный зазор в 2—4 см) крепят теплоизоляционные плиты. Возможен и другой способ деревянные рейки прибивают к пробкам, установленным в швах кладки, затем на них набивают утеплитель (арболит, фибролит, жесткие минерало-ватные плиты или плиты из легкого бетона, а также других материалов неорганического происхождения). Для районов, где зимняя температура —30°, стену кладут в полтора кирпича и утепляют фибролитовыми плитами толщиной 50 мм, а при использовании эффективного кирпича толщина кладки может быть 25 см (то есть в один кирпич).
Стены колодцевой кладки с засыпкой или заполнением легким бетоном имеют следующую конструкцию (рис.8).Поперечные стенки устраивают через три кирпича по длине. Наружные углы выложены тычковым рядом. Засыпку мелким шлаком, керамзитом или другими легкими заполнителями делают по мере возведения стены слоями по 10—15 см (тщательно трамбуя каждый слой). Через 2—3 слоя засыпку поливают известковым раствором сметанообразной консистенции. Вместо перечисленных заполнителей можно использовать песок, смешанный с опилками и известью-пушонкой в пропорции примерно 1:4:1. Завершать колодцевую кладку нужно 3—4 рядами сплошной кладки, предварительно армировав металлической сеткой последний ряд с засыпкой.
Наконец, последняя конструкция — облегченная кирпичная кладка с горизонтальными диафрагмами (рис.9). Она состоит из двух стенок, выложенных в полкирпича, и с утеплителем между ними. Стенки связывают тычковыми рядами (диафрагмами) через каждые 3—5 рядов. Утеплитель используют тот же, что и в колодцевой кладке. Толщину кирпичных стен различной конструкции (в зависимости от температуры наружного воздуха) вы узнаете из Таблицы 2 Внутренние несущие стены должны быть толщиной не менее 25 см. Перегородки обычно делают в полкирпича (120 мм) или даже в четверть (65 мм — то есть «на ребро»). Если перегородка или простенок толщиной 65 мм имеет длину более 1,5 м, то кладку следует армировать стальной проволокой через 2—3 ряда. Обычно подобные перегородки ставят в санузлах и ванных комнатах, а потом их штукатурят с обеих сторон цементно-песчаным раствором состава 1:2 по металлической сетке или проволоке, натянутой по мелким гвоздям, забитым в швы кладки. Сплошные наружные и внутренние стены толщиной в один кирпич и облегченные стены любой конструкции возводят на растворе марки М25. Для перегородок и наружных стен сплошной кладки толщиной 38 см и более применяют раствор марки М10.
15. Устройство кровель из штучных материалов
Асбестоцементные кровли из волнистых листов обыкновенного профиля ВО (ГОСТ 378—76) устраивают на кровлях с уклоном более 27% по деревянной обрешетке на жилых, гражданских, производственных зданиях, а также на объектах сельскохозяйственного назначения. Обрешетку устраивают из брусков сечением 60х60 мм. На определенном расстоянии друг от друга (с шагом 530 мм) раскладывают и крепят обрешетки от карниза к коньку.
Последовательность укладки листов в покрытие. Первый лист укладывают по шнуру вдоль ската, начиная от карниза, без обрезки углов. Затем на гребне второй волны с правой стороны листа ручной дрелью (с диаметром сверла на 1...2 мм больше диаметра гвоздя) сверлят отверстие на расстояние 80...100 мм от нижней кромки. Лист через отверстие прибивают к карнизному свесу шиферным гвоздем с прокладкой из резины, толя, рубероида, не добивая гвоздь до отказа на 2...3 мм. Далее кровельщик кладет на место второй лист продольного ряда (от первого ряда к концу), точно прилаживает лист с отрезанным ножницами углом по месту, сверлит отверстие на второй волне справа на середине нахлестки второго листа на первый (на расстоянии 60 м от нижней грани второго листа) и прибивает его к обрешетке шиферным гвоздем с рубероидной прокладкой, не добивая гвоздь до отказа на 3...4 мм. Таким же образом обрабатывают следующие листы первого продольного ряда и прибивают их к обрешетке. В покрытие волнистые листы укладывают в определенной последовательности: в поперечном направлении — справа налево (обращаясь лицом к коньку) с перекрытием одного листа другим на одну волну; в продольном направлении — снизу вверх с перекрытием нижеуложенного ряда вышеукладываемым на 140 мм при уклоне до 33%. Листы в ряду удобнее укладывать справа налево, причем учитывают направление господствующих в данном районе ветров, чтобы открытые кромки продольных стыков были обращены на подветренную сторону. Покрывать крышу с нахлесткой волнистых листов можно двумя способами: со смешением продольных кромок листов на одну волну по отношению к таким же кромкам листов ранее уложенного ряда; с совмещением продольных кромок листов во всех вышеукладываемых рядах. Для укладки по первому способу заготовляют необходимое количество листов, обрезанных на одну, две, три и четыре волны. В этом случае линия стыков листов на скате в продольном направлении будет ступенчатой. При укладке вторым способом в листах обрезают лишь углы (рис. 101), тогда линия стыковки листов на скате по продольным кромкам будет прямой.
Рис. 101. Подкотовка листов ВО к укладке: а - последовательность обрезки листов при укладке справа налево; б - соединение четырех листов продольно-поперечной нахлесткой; 1 - угловой лист; 2 - сливной и фронтонный листы; 3 - фронтонный и коньковый листы; 4 - рядовой лист
Листами ВО с долевой обрезкой волн рекомендуется покрывать относительно узкие по уклону, но длинные в поперечном направлении скаты. Широкие по уклону, но короткие в поперечном направлении скаты покрывают листами ВО со срезанными углами. Основанием под кровлю служит обрешетка из брусков сечением 60х60 мм. Высота карнизного бруска — 66 мм, нечетных — 60 мм, четных — 63 мм. Если для однотипности берут бруски 60х60 мм, их надо нарастить, например, уложив на стропила планки 1 (рис. 102, а) толщиной 3 мм. На таком основании продольная нахлестка листов будет плотной и листы ВО будут прочно лежать на брусках обрешетки.
Рис. 102. Укладка и крепление листов ВО: а - продольный разрез ската; б - крепление листов; в - дополнительное крепление листов на карнизе; 1 - уравнительная планка; 2 - лист ВО; 3 - обрешеточный брусок; 4 - гвоздь; 5 - резиновая шайба; 6 - шуруп; 7 - карнизный брусок; 8 - гвоздь; 9 - противоветровая скоба (цифры в скобках относятся к укладке обрешетки при уклоне ската менее 58%); В - вылет свеса
Крепят листы на обрешетке гвоздями, шурупами (рис. 102, 6) и частично противоветровыми скобами (рис. 102, в). В районах, где сила ветра превышает восемь баллов, листы устанавливают на шурупах и скобах. В карнизном ряду скобы ставят по шнуру из расчета по две на лист. Обрешетку крыши выполняют с таким расчетом, чтобы на нее можно было уложить целое число листов как в продольном, так и в поперечном направлениях (рис. 103). Если это невозможно, в кровлю вводят обрезанные листы, которые в поперечных рядах укладывают предпоследними у фронтонного свеса, а в продольных — у конька. Чтобы не обрезать листы, можно увеличить или уменьшить свесы кровли на фронтонах, а также изменить величину выноса карнизного свеса.
Рис. 103. Покрытие ската листами ВО: а - начальная стадия укладки листов ВО с совмещением продольных кромок; б - поперечный разрез фронтонного свеса; 1, 2 - карнизный и обрешеточный бруски, листы; 3 - сливной; 4 - рядовой; 5 - фронтонный; 6 - угловой; 7 - гвоздь; 8 - резиновая шайба (цифры в скобках относятся к укладке обрешетки при уклоне ската менее 58%)
Подготовляя листы, проверяют их внешнее состояние, длину и ширину, затем обрезают их углы или продольные полосы. Отверстия, как правило, сверлят по месту ручной или электрической сверлильной машиной. Диаметр сверла должен быть на 2 мм больше диаметра гвоздя или шурупа. Размечают углы на листах ВО следующим образом. Кровельщики из досок сами делают стусло и в нем по рекомендуемым размерам делают прорези. Лист ВО укладывают так, чтобы отрезаемый угол упирался в бортики стусла, а затем ножовкой с мелкими зубьями отрезают угол. Более производительно эта операция выполняется с помощью дисковой электропилы ИЭ-5102В. Листы в пакете плотно прижимают один к другому с помощью струбцины или тяжелого предмета, укладываемого на пакет сверху, а затем обрезают. Углы в листах ВО можно срезать также ножницами электрическими ножевыми или вырубными. Делают это так. На листе ВО карандашом чертят линию среза и ножницами отрезают угол, следя за тем, чтобы разметочная линия отреза оставалась нетронутой. Прорезь в листе делается за счет отрезаемого угла. Длина и ширина листов ВО могут отличаться от номинальных размеров в пределах допусков, поэтому взаимное расположение листов с обрезанными углами может быть различным. Чтобы угловые срезы плотно прилегали один к другому, их при необходимости подгоняют шерхебелем или рашпилем в процессе укладки.
Покрытие волнистыми листами полагается неплотное, так как листы в местах сопряжений криволинейных поверхностей образуют серповидные зазоры, через которые в чердачное помещение проникает снег или дождевая вода. Чтобы этого не было, зазоры, превышающие 7 мм, в местах соединений промазывают мастикой УМС-50 или холодной сметано-образной мастикой Михайлевского. Состав мастики Михайлевского, % по массе: вяжущее вещество (битум марки БН-90/10) — 4; растворитель (соляровое масло) — 28; наполнитель (известь-пушонка) — 12; волокнистый наполнитель — 13. Мастику наносят на перекрываемые полосы деревянным шпателем. Толщина слоя мастики 5...6 мм, ширина в поперечных соединениях — 30...40, в продольных — 60...70 мм.
Очередной лист, укладываемый в ряд, своей продольной кромкой должен накрывать волну ранее уложенного листа. Его нижняя волнистая сторона должна вплотную подойти к натянутому шнуру, а угловой срез — сомкнуться с таким же срезом на смежном листе. После этого на гребне второй волны у нижнего края листа, над бруском обрешетки, сверлят отверстие. Гвоздь с надвинутой на него резиновой шайбой, обмазанной с обеих сторон густым окрасочным составом на натуральной олифе, вставляют в отверстие на гребне волны и ударами молотка забивают в брусок. Гвоздь перестают забивать, когда из-под шайбы выступит излишек окрасочного состава. Этим составом пришпатлевывают головку гвоздя и шайбу, которые после высыхания окрашивают масляным окрасочным составом под цвет уложенных листов. Качество покрытия и быстрота его устройства во многом зависят от организации кровельных работ (рис. 104).
Рис. 104. Рабочее место звена укладчиков кровли: 1 - уравнительная планка; 2 - возок с запасом волнистых листов; 3 - коньковый брусок; 4 - укладываемый волнистый лист; 5 - ходовой мостик; 6 - приконьковый брусок обрешетки; 7 - электрическая сверлильная машина; 8 - брусок обрешетки; 9 - стропильная нога
На крышу материалы с помощью различных подъемников доставляют в контейнерах, поддонах (рис. 105, а) или на инвентарных сборно-разборных площадках (рис. 105, б).
Рис. 105. Поддон (а) и инвентарная сборно-разборная площадка (б) для подачи и приема волнистых листов
Началом устройства кровель из металлочерепицы является замер скатов с установлением перпендикулярности торцов крыши по отношению к линиям конька и карнизов. Обрешетку под листы металлочерепицы выполняют из досок сечением 32х100 мм с расстоянием между ребрами 350 мм, т.е равными размерами между ребрами металлочерепицы. Если размер поперечных ребер металлочерепицы иной, например 400 мм, то и обрешетку устраивают соответственно. На карнизах расстояние от наружного края карнизной доски — 300 мм (рис. 144).
Рис. 144. Разметка укладки листов металлочерепицы: а - места нахлестов; б - установка самонарезающихся винтов
Доски на торцевых участках и доски ребристой обшивки, выходящие на карнизы, должны быть расположены выше других досок. Края листов металлочерепицы должны быть закрыты сплошной обшивкой досками для их прочного закрепления. Монтаж листов металлочерепицы начинают с торцевых участков. Сначала у края карниза следует закрепить направляющую доску. От нее будет направляющая линия. Целесообразно вначале 3—4 листа закрепить одним шурупом на коньке, выровнять по карнизу, затем закрепить окончательно: сначала первый лист прикрепить у конька, затем второй лист. Скрепить нахлест шурупом по верху волны. Канавка на крае каждого листа должна быть закрыта соседним листом. Край с канавкой каждого следующего листа укладывают под ранее уложенный, предыдущий закрепленный лист, который удерживает монтируемый лист (если монтаж начать с левого торца). Для закрепления листов металлочерепицы к обрешетке можно использовать самозавинчивающиеся болты А4 9х27 с уплотнениями или самонарезающиеся шурупы с уплотнительной шайбой (6 шурупов на 1 м2). Отверстия для болтов просверлить дрелью. Болты следует устанавливать перпендикулярно к листам на каждую вторую гофрированную складку, на дно канавки и на нижнюю сторону поперечной складки
Все дальнейшие нахлестки выполняют у поперечной границы листа. Длина нахлестки составляет примерно 250 мм. Места нахлеста закрепляют на болтах или шурупах. Конек закрывают специальными коньковыми элементами с уплотнением. Они имеют полуцилиндрическую форму и хорошо укладываются на верхние концы профильных листов металлочерепицы (рис. 145). Торцевые элементы закрывают кровлю от попадания дождя и ветра.
Рис. 145. Схема расположения конькового элемента
Карнизные элементы защищают карниз и обрешетку от отекания с крыши воды (рис. 146).
Рис. 146. Схема расположения карнизного элемента
Для исключения образования конденсата на холодной внутренней поверхности металлочерепицы следует создать условия для вентиляции под кровлей от карниза до конька, а под обрешеткой разместить рулонный материал (рис. 147).
Рис. 147. Конструкция крыши с кровлей из металлочерепицы: 1 - обрешетка; 2 - гидроизоляционный материал; 3 - металлочерепица; 4 - направление движения воздуха
Ендову кровли из металлочерепицы выполняют с помощью специального разжелобочного элемента. На обшивку, находящуюся внизу, монтируют промежуточную конструкцию. На эту конструкцию прикрепляют на болтах разжелобочный элемент (рис. 148).
Рис. 148. Монтаж разжелобка: 1 - промежуточная конструкция; 2 - разжелобочный элемент
Зазоры между металлочерепицей и разжелобочным элементом, а также под коньком во всех местах, где есть неплотности и зазоры, герметизируют с использованием любого силиконового и другого отверждающегося герметика, или с применением специальных уплотнительных лент, прибиваемых к профилю небольшими гвоздями. При обрезке листа или при сверлении образовавшуюся металлическую крошку необходимо смести, чтобы не испортить покрытие. Во время монтажа следует ходить в обуви с мягкой подошвой и наступать только в местах обрешетки и в прогиб волны.
Крепления листов болтами или шурупами выполняют в соответствии со схемами. Для выхода на крышу в листах металлочерепицы имеется элемент с отверстием, выполненный из стеклопластика, внешний вид и рисунок которого такой же, как и у листа металлочерепицы. Для устройства кровли из металлочерепицы требуется 30 различных комплектующих изделий. Кроме того, необходима лестница для подъема на крышу, переходные мостки, лестница на крыше, водосточные трубы, крюки под желоба. Листы металлочерепицы поставляют по размерам. Длина листа каждого типа должна быть равной длине ската плюс карниз (рис 149). Для обеспечения полного монтажа и надежности кровли заводы поставляют на объект большое разнообразие комплектующих элементов, таких как конек прямоугольный; конек полуцилиндрический, торцевой элемент конька, торцевые элементы карнизов, наружных и внутренних углов, конструкции листов для выхода на крышу и др. (рис. 150).
Рис. 149. Укладка листа металлочерепицы
Рис. 150. Основные конструктивные доборные элементы для кровли из метеллочерепицы: а - коньковый элемент; б - коньковый элемент с полукруглым профилем; в - торцевой элемент конька; г - торцевой элемент к рядовым листам; д - карнизный элемент; е - элемент ендовы
Устройство кровли из листовой стали.
Лежачие и стоячие фальцы. Для рядового покрытия скатов крыши, карнизных свесов, настенных желобов, разжелобков и т. д. изготовляют картины. Картина — это элемент кровельного покрытия, у которого кромки подготовлены для фальцевого соединения. Обычно их делают составными из двух листов (85...90%), реже одинарными (10...15%) для добавок в рядовых полосах. Кровельная листовая сталь для заготовки картин должна иметь ровные плоскости; все углы должны быть прямыми. Заготовку фальцевых соединений кровельщик выполняет на верстаке, щит которого окантован с одной или двух сторон угловой сталью. Фальцевые соединения по внешнему виду делят на лежачие (рис. 167, а...г) и стоячие (рис. 167, д...и), а по степени уплотнения — на одинарные и двойные. (Размеры фальцев даны для листов толщиной 0,45...0,7 мм. Для более толстых листов отгибы увеличивают на 20%.)
Рис. 167. Последовательность формирования фальцевых соединений: а - отгиб кромки для одинарного лежачего фальца; б - соединение листов одинарным лежачим фальцем (пунктиром показан лист с подсечкой); в - отгиб кромки для двойного лежачего фальца; г - соединение листов двойным лежачим фальцем; д - отгибы в листах кромок для одинарного стоячего фальца; е - соединения листов одинарным стоячим фальцем (гребнем); ж - отгибы в листах кромок для двойного стоячего фальца; з - промежуточный отгиб для двойного стоячего фальца; и - законченное соединение листов двойным стоячим фальцем (гребнем)
Картины для рядового покрытия. Скаты кровель покрывают полосами, которые составляют из последовательно соединенных картин. Для покрытия крыши требуется 85...90% двойных картин и 10...15% одинарных, необходимых для дополнений в полосах. Заготавливают картины на верстаке. На короткой стороне листа отгибают кромку шириной 10 мм (рис. 181) для лежачего фальца, затем лист переворачивают и отгибают вторую кромку. После этого на коротких сторонах листа кромки окажутся отогнутыми в разные стороны. Обработанные таким образом листы соединяют попарно в картины. Фальцы уплотняют деревянным молотком.
Рис. 181. Двойная картина для рядового покрытия
Далее у соединенных таким образом листов отгибают кромки для образования стоячих фальцев (гребней) сначала по одной (длинной) стороне картины, затем по другой (противоположной). В картине отгибают продольные кромки под углом 90°. Сначала отгибают малый гребень (левый) высотой 20...25 мм, затем на противоположной стороне картины в том же направлении делают большой (правый) отгиб для стоячего фальца высотой 40...45 мм. В углах картины на длине около 70 мм кромки обоих стоячих фальцев не отгибают, чтобы не смять загнутые на коротких сторонах лежачие фальцы.
Элементы карнизного свеса. При заготовке элементов для карнизных свесов исходят из уклона настенных желобов. Для средних и северных районов России наилучшим является уклон настенных желобов 1:20, а для южных районов, где часто выпадают обильные дожди — 1:10. Рассмотрим последовательность заготовки картин карнизного свеса (рис. 182) для наиболее часто встречающегося случая, когда расстояние между водоприемными воронками равно 12 м, а уклон — 1:20.
Рис. 182. Раскрой заготовок (1...5) для покрытия карнизного свеса
На дощатом настиле вдоль натянутого шнура раскладывают семь листов кровельной стали. Листы должны перекрывать друг друга на припуск для последующего отгиба кромок лежачего фальца. Для образования свеса кровли с карниза (с вылетом 120 мм) и капельника с отворотной губкой от нижней продольной кромки уложенных листов откладывают отрезок ав, равный 200 мм, а затем отрезок бв = Ai, где А — расстояние между воронкой и водоразделом, равное 6 м (или 6000 мм); i — уклон с соотношением 1:20, т. е. бв = 6*1000*1/20 = 600*1/2 = 300 мм.
Для перекрытия верхней кромки карнизного свеса водосточными желобами откладывают отрезок в, г равный 150 мм. Вдоль нижней кромки листов из точки а откладывают отрезок ад, равный половине пролета между водоприемными воронками. Затем на вертикальном отрезке, восстановленном из точки д, откладывают отрезки д и еж, равные соответственно 200 и 150 мм. После этого с помощью шнура отбивают линию ве. Тем же шнуром отбивают вторую линию, пересекающую все листы по диагонали (через точки г, ж). Наконец, из точки л откладывают отрезок кл, равный дж. Как и в предыдущем случае, из точки к откладывают половину пролета км, равную 6000 мм, и припуски на поперечные фальцы.
Заготовки картин размечают, проставляя на них масляной краской цифры 1...5. После этого уложенную полосу листов разрезают в продольном (по линии ги) и в трех поперечных направлениях: слева от прямой кл и справа от прямых жд и ми. Заштрихованные на рисунке участки обрезают и используют для изготовления деталей водоприемных воронок и кляммер.
Рис. 183. Одинарная картина покрытия карнизного свеса: а - готовая картина (штрихпунктиром показан контур заготовки); б - последовательность гибки капельника; 1...5 - последовательность операций.
Затем при ручной заготовке картин их укладывают на верстак и выполняют киянкой гибку. Обрезав нижние углы всех заготовок на 35...45° для уменьшения толщины фальцев в местах стыкования, приступают к гибке капельников с отворотными губками (рис. 183, а, узел II). Последовательность гибки капельника показана на рис. 183, б. В картине отгибают губку на длинной стороне заготовки с угловыми вырезами, а затем боковые отвороты на коротких сторонах картины для соединения со смежными картинами двойными лежачими фальцами. Стрелки на рис. 183, б показывают направления ударов киянки при гибке. Отвороты в картинах для их соединения на карнизе в общую полосу отгибают, как показано на рис. 183, а. Таким образом, все фальцевые соединения на участке карниза между воронками будут направлены от водораздела в разные стороны (по стоку воды).
Скаты крыш (сначала противоположные фасадным, затем фасадные) покрывают после устройства карнизных свесов и настенных желобов. В зависимости от формы крыши рядовое покрытие (рис. 202, а, б) укладывают в разной последовательности: на фронтонных крышах первую полосу располагают вдоль фронтона или брандмауэра; при вальмовых, полувальмовых и многощипцовых — от начала коньков. Как правило, картины в рядах раскладывают в направлении от желоба к коньку. Кромки в стоячих фальцах 3 в пределах одного ската кровли загибают в одну сторону. К первой картине первой рядовой полосы 1 укладывают вторую, которую зацепляют отгибом предыдущей, и т. д. Картины соединяют между собой лежачими 2 фальцами, при уплотнении которых в качестве подкладки используют стальную полосу размером 5х60 мм. В готовой полосе в местах стыкования картин выпрямляют кромки для стоячих фальцев 3. Все рядовые полосы покрываемого ската перепускают через конек с таким расчетом, чтобы после обрезки можно было отогнуть коньковую кромку на одном скате высотой 30 мм, на другом — 50 мм. Стоячие фальцы 3 рядового покрытия, выходящие на конек крыши и к ребрам, сваливают в сторону малого отгиба на длину 80...100 мм. Для реберного соединения делают припуски, как и для конькового стоячего фальца 4 (рис. 202, в).
Рис. 202. Рядовое покрытие ската: а - укладка рядовых полос; б - поперечное примыкание ската к стене; в - коньковый стоячий фальц; г - крепление фронтонного края рядовой полосы; 1 - картина в рядовой полосе; 2, 3 - одинарные лежачий и стоячий фальцы; 4 - коньковый стоячий фальц; 5 - доска; 6 - брусок; 7 - фартук; 8 - закладной брусок; 9 - толевый гвоздь; 10 - цементно-песчаный раствор; 11 - фронтонная кляммера; 12 - кровельный гвоздь
Укрепив полосу гвоздем за малый отгиб, у досок 5 конька с помощью шнура выверяют ее положение. Затем укрепляют рядовую полосу вдоль малого отгиба, плотно подтягивая ее к обрешетке кляммерами. Кляммеры ставят из расчета не менее двух на каждую сторону листа (примерно через 600 мм), прибивают гвоздями 12 (3,5х45 мм) к боковым граням брусков 6 обрешетки и загибают их на кромку малого отгиба. Если кляммера совпадает с лежачим фальцем в рядовой полосе, ее перемещают на другую сторону бруска. Смежные рядовые полосы на скате располагают так, чтобы взаимное смещение лежачих фальцев в картинах в пределах одного ската кровли и взаимное смещение стоячих фальцев на противоположном скате кровли были не менее 50 мм (рис. 202, а). Достигается это подрезкой на 50 мм каждой четной полосы у конька и обрезкой первой рядовой полосы смежного ската в продольном направлении. При обрезке четных полос следят за тем, чтобы лежачие фальцы в полосе не попадали в отгибаемые кромки конькового стоячего фальца.
Вторую рядовую полосу собирают, как первую, затем ее пододвигают стороной с большим отгибом к малому отгибу первой полосы. Малый отгиб второй полосы крепят к обрешетке кляммерами, после чего приступают к соединению полос стоячим фальцем. Иногда рядовые полосы соединяют только у кляммер, а к окончательному их соединению возвращаются после того, как полосами будет покрыт весь скат. Рядовые полосы соединяют одинарным стоячим фальцем с помощью гребнегиба и киянки (см. рис. 169). Для этого кровельщик становится так, чтобы видеть весь загибаемый фальц, и движется в направлении от карниза к коньку. Гибочный скребок гребнегиба подводят вплотную к большому отгибу; в это время малый отгиб должен быть на одном уровне со скребком. Затем кровельщик сваливает киянкой кромку большого отгиба на плоскость скребка при одновременной и плавной перестановке гребнегиба вдоль фальца и, продвигаясь вперед, ударами киянки наклоняют кромку большого отворота из горизонтального положения книзу. После этого переставляет гребнегиб на смежную рядовую полосу так, чтобы брусок гребнегиба упирался в тыльную грань фальца. Потом начинает уплотнять его, двигаясь снова вдоль фальца и нанося киянкой равномерные удары по уплотняемой кромке, одновременно переставляя гребнегиб. При каждой выполняемой операции гребнегиб передвигают рукой вдоль фальца. Иногда по описанной технологии одинарный лежачий фальц формируют за один проход. Кроме приведенного способа при отсутствии гребнегиба и киянки картины соединяют другими простыми способами: двумя кровельными молотками и с помощью молотка и бруса-отворотки (рис. 203).
Рис. 203. Соединение картин стоячим фальцем с помощью кровельных молотков (а) или молотка и бруса-отворотки (б)
В первом случае (рис. 203, а) один молоток используют сначала как скребок гребнегиба, а вторым молотком-ручником сваливают фальц. Затем ручник используется как брусок гребнегиба (упор), а вторым молотком уплотняют фальц. Во втором случае (рис. 203, б) брус-отворотку подставляют к фальцу, молотком сваливают его на скребковую часть. Затем брус-отворотку переставляют так, чтобы брусок упирался в тыльную часть фальца. Молотком кровельщик уплотняет фальц, равномерно ударяя по отогнутой кромке фальца. В последнее время начали применять гребнегибочные машины и приспособления-гребнегибы новых конструкций, позволяющие выполнять эту работу без кровельных молотков.
16. Конструкция современных опалубочных систем
Основные типы опалубок
Опалубку классифицируют по функциональному назначению в зависимости от типа бетонируемых конструкций:
• для вертикальных поверхностей, в том числе стен; • для горизонтальных и наклонных поверхностей, в том числе перекрытий; • для одновременного бетонирования стен и перекрытий; • для бетонирования комнат и отдельных квартир; • для криволинейных поверхностей (используется в основном пневматическая опалубка).
Для бетонирования стен применяют опалубку следующих видов: мелкощитовую, крупнощитовую, блок-формы, блочную и скользящую.
Для бетонирования перекрытий используют мелкощитовую опалубку с поддерживающими элементами и крупнощитовую, в которой опалубочные поверхности составляют единый опалубочный блок, целиком переставляемый краном.
Для одновременного бетонирования стен и перекрытий или части здания используют объемно-переставную опалубку. Для этих же целей применяют горизонтально перемещаемую, в том числе катучую, опалубку, которая может быть использована для бетонирования вертикальных, горизонтальных и наклонных поверхностей.
Разборно-переставная мелкощитовая опалубка состоит из набора элементов небольшого размера площадью до 3 м2 и массой до 50 кг, что позволяет устанавливать и разбирать их вручную. Из элементов опалубки можно собирать крупные панели и блоки, монтируемые и демонтируемые краном без разборки на составляющие элементы. Опалубка унифицирована, применима для самых разнообразных монолитных конструкций с постоянными, переменными и повторяющимися размерами. Наиболее целесообразно использовать опалубку для бетонирования неунифицированных конструкций небольшого объема.
Крупнощитовая опалубка состоит из крупноразмерных щитов и элементов соединения. Щиты опалубки воспринимают все технологические нагрузки без установки дополнительных несущих и поддерживающих элементов. Опалубку применяют для бетонирования протяженных стен, перекрытий и туннелей. Размер щитов равен размеру бетонируемой конструкции: для стен — ширина и высота помещения, для перекрытия — ширина и длина этого перекрытия. В случае бетонирования перекрытий большой площади, когда не представляется возможности уложить и уплотнить бетон конструкции в течение одной смены, перекрытие разбивают на карты. Размеры карты задают технологическим регламентом, на их границах устанавливают металлическую сетку толщиной 2...4 мм с ячейками 10 х 10 мм для обеспечения достаточного сцепления с последующими картами. Крупнощитовая опалубка рекомендуется для зданий с монолитными стенами и перегородками, сборными перекрытиями. Разборно-переставная крупнощитовая опалубка применяется также для бетонирования конструкций переменного поперечного сечения (силосы, дымовые трубы, градирни).
Блочная опалубка — это объемно-переставная опалубка, предназначенная для возведения одновременно трех или четырех стен по контуру ячейки здания без устройства перекрытия. Опалубку монтируют из отдельных блоков с зазорами, равными толщине возводимых стен. Для зданий с монолитными наружными и внутренними несущими стенами и сборными перекрытиями рекомендуется комбинированный вариант: для наружных поверхностей стен — крупнощитовая опалубка, а для внутренних поверхностей и стен — блочная, вертикально перемещаемая и извлекаемая опалубка.
Блок-формы представляют собой пространственные замкнутые блоки: неразъемные и жесткие, выполненные на конус, разъемные или раздвижные (переналаживаемые). Блок-формы применяют для бетонирования замкнутых конструкций относительно небольшого объема не только для вертикальных, но и для горизонтальных поверхностей. Кроме этого они используются для объемных элементов стен, лифтовых шахт, отдельно стоящих фундаментов, колонн и т. д.
Объемно-переставная опалубка состоит из секций П-образной формы и представляет собой горизонтально извлекаемый крупноразмерный блок, предназначенный для одновременного бетонирования стен и перекрытий. При распалубке секции сдвигают (сжимают) внутрь и выкатывают к проему для последующего извлечения краном. Эту опалубку используют для бетонирования поперечных несущих стен и монолитных перекрытий жилых и гражданских зданий. Данный тип продольно перемещаемой опалубки нашел применение в зданиях с монолитными продольными несущими стенами и перекрытиями из монолитного железобетона. Для зданий с простой конфигурацией в плане, большой площадью этажа, плоскими поверхностями фасадов рекомендуются объемно-переставные опалубки — туннельная, вертикально и горизонтально перемещаемые опалубки.
Туннельная опалубка — объемно-переставная опалубка, предназначенная для одновременного возведения двух поперечных и одной продольной стены здания и перекрытия над этими стенами. Туннель может быть образован из двух противостоящих полутуннелей путем соединения их горизонтальных и вертикальных щитов с помощью быстроразъемных замков. Опалубка туннельного типа наиболее часто применяется для зданий с монолитными внутренними стенами, монолитными перекрытиями и навесными фасадными панелями.
Горизонтально перемещаемая опалубка предназначена для бетонирования горизонтально протяженных конструкций и сооружений, а также конструкций замкнутого сечения с большим периметром.
Скользящая опалубка применяется для бетонирования стен высоких зданий и сооружений. Она представляет собой пространственную опалубочную форму, установленную по периметру стен и поднимаемую гидродомкратами по мере бетонирования. Для зданий точечного (башенного) типа большой этажности и с простой внутренней планировкой рекомендуется вертикально извлекаемая опалубка блочного типа или скользящая опалубка.
Пневматическая опалубка — гибкая, воздухонепроницаемая оболочка, раскроенная по габаритам сооружения. Устанавливают опалубку в рабочее положение, создают внутри избыточное давление воздуха или другого газа и бетонируют. Применима такая опалубка для бетонирования сооружений относительно небольшого объема и криволинейных очертаний.
Несъемная опалубка используется для возведения конструкций без распалубливания, создания облицовки, а также тепло- и гидроизоляции. При бетонных работах применяют следующие вспомогательные элементы опалубочных систем. Навесные подмости — специальные подмости, навешиваемые на стены со стороны фасадов с помощью кронштейнов, закрепленных в отверстиях, оставленных при бетонировании стен. Выкатные подмости — подмости, предназначенные для выкатывания по ним туннельной опалубки или опалубки перекрытий при их демонтаже. Проемообразователи — специальная опалубка, предназначенная для формирования в монолитных конструкциях оконных, дверных и прочих проемов. Основные направления повышения технологичности монолитных конструкций и снижения трудозатрат на выполнение комплекса бетонных работ:
• переход на высокоподвижные и литые бетонные смеси с химическими добавками, что снижает до минимума трудозатраты на транспортирование, укладку и уплотнение бетона — снижение ручного труда с 35 до 8%, и одновременно с повышением интенсивности бетонирования значительно снижается относительная себестоимость укладки бетонной смеси; • использование армокаркасов полной готовности, переход от сварных соединений к механическим стыкам — снижение трудоемкости в 1,5...2 раза; • применение инвентарной, быстроразъемной опалубки модульных систем со специальным полимерным антиадгезионным покрытием, исключающим затраты по очистке и смазке палубы; • использование опалубочных систем непрерывного бетонирования, применение несъемных опалубок, снижающих или исключающих трудозатраты на их демонтаж.
Если принять общую трудоемкость возведения монолитных железобетонных конструкций за 100%, то трудозатраты на выполнение опалубочных работ составляют примерно 45...65%, арматурных—15...25% и бетонных —20...30%.
17. Технология погружения готовых свай
Сваи погружают ударом, вибрацией, вдавливанием, завинчиванием, с использованием подмыва и злектроосмоса, а также комбинациями этих методов. Эффективность применения того или иного метода зависит в основном от грунтовых условий.
Ударный метод. Метод основан на использовании энергии удара (ударной нагрузки), под действием которой сваи нижней заостренной частью внедряется в грунт. По мере погружения она смещает частицы грунта в стороны, частично вниз, частично вверх. Ударную нагрузку на оголовок сваи создают специальными механизмами - молотами самых разных типов, основными из которых явл-ся дизельные.
Вибрационный метод. Метод основан на значительном уменьшении при вибрации коэф. Внутреннего трения в грунте и сил трения по боковой поверхности сваи. Благодаря этому при вибрировании для погружения свай требуется усилий в десятки и сотни раз меньше, чем при забивке. При вибрационном методе сваю погружают с помощью специальных механизмов-вибропогружателей. Вибропогружатель, представляющий собой электромеханическую машину вибрационного действия, подвешивают к мачте сваепогружающей установки и соединяют со сваей наголовником. Вибрационный метод наиболее эффективен при несвязных водоносных грунтах. Более универсальным является виброударный способ погружения свай с помощью вибромолота. Они могут самонастраиваться, т.е. увеличивать энергию удара с повышением сопротивления грунта погружению свай.
Погружение свай завинчиванием. Метод основан на завинчивании стальных и ж\б свай со стальными наконечниками с помощью установок, смонтированных на базе автомобилей. Рабочие операции при погружении свай методом завинчивания аналогичные операциям, выполняемым при погружении свай методом забивки или вибропогружением. Только вместо установки и снятии наголовника здесь надевают и снимают оболочки.
С использованием подмыва. Подмывом грунт разрыхляют и частично вымывают струями воды, вытекающими под давлением из нескольких трубок диаметром 38.... 62мм, укрепленных на свае. При этом сопротивление грунта у острия сваи снижается, а поднимающаяся вдоль ствола вода размывает грунт, уменьшая тем самым трение по боковым поверхностям сваи. Применение подмыва не допускается, если имеется угроза просадки близлежащих сооружений, а также при наличии просадочных грунтов.
С использованием электроосмоса. Применяют при наличии водонасыщенных плотных глинистых грунтов, моренных суглинков и глин. Для практической реализации метода погруженную сваю присоединяют к положительному полюсу(аноду) источника тока, а соседнюю с ней погружаемую- отрицательному полюс(катоду) того же источника тока.При включении тока вокруг сваи(анод) снижается влажность грунта, а у погружаемой сваи(катод), наоборот, повышается. После прекращения подачи тока происходит восстановление первонач. сост.грунт-х вод и несущ, способ. свай явл-ся катодами. возрастает. Этот метод позволяет на 25-40% ускорить процесс погружения свай, а также уменьшить нагрузки, необход-ые для погруж-я сваи.
железобетонные монтажные каменные бетонный
18. Разработка грунта экскаваторами непрерывного действия
Экскаваторы непрерывного действия предназначены для отрывки траншей и каналов в грунтах I—IV групп как в городских, так и в полевых условиях. Это землеройные машины на гусеничном или пневмоколесном ходу самоходного, полуприцепного и прицепного типов, которые при своем поступательном движении во время работы разрушают грунт с помощью группы непрерывно движущихся по замкнутому контуру ковшей, скребков или резцов, отрывают позади себя продольную выемку определенных размеров и одновременно эвакуируют грунт в сторону от нее (в отвал или транспортные средства) с помощью конвейера, ротора или шнека. Различают два типа экскаваторов непрерывного действия: цепные и роторные. Рабочим органом цепных экскаваторов является одно- или двухрядная бесконечная цепь, огибающая наклонную раму и несущая на себе ковши, скребки или резцы. У роторных экскаваторов рабочий орган — жесткий ротор, или колесо с ковшами или скребками, вращающееся на роликах. Толщина разрушаемого грунта цепным органом практически постоянна по высоте забоя, роторным — переменной толщины, достигающей максимального значения на уровне оси вращения ротора. В зависимости от условий работы и трудоемкости разработки грунтов скорости передвижения экскаватора и движения рабочего органа подбираются такими, чтобы независимо от глубины траншеи обеспечивалось расчетное наполнение ковшей.
Рис. 4.9. Экскаваторы непрерывного действия а — скребковый одноцепной: 1 — отпал; 2 — трактор; 3 — цепной рабочий орган; 4 — механизм подъема—опускания рабочего органа; 5 — шнек; 6— резцы; 7— скребок;8 — зачистной башмак; б — скребковый двухцепной: 1 — силовая установка; 2 — управление; 3 — гидропривод; 4 — трансмиссия; 5 — механизм подъема и опускания рабочего органа; 6 — конвейер; 7 — лоток; 8 — рабочий орган; в — роторный: 1 — тягач; 2 — рама для монтажа рабочего оборудования; 3,4 — механизмы подъема и привода; 5 — конвейер; 6 — ковш; 7 — ковшовый ротор.
По типу рабочего органа цепные экскаваторы делятся на одноцепные, снабженные резцами и скребками, и двухцепные, между ветвями которых укреплены ковши или скребки с резцами. Скребковые одноцепные экскаваторы (рис. 4.9, а) предназначены для отрывки траншей прямоугольного профиля шириной 0,14...0,4 м, глубиной до 1,7 м в однородных (без каменистых включений) грунтах I — III групп. Производительность таких экскаваторов составляет 60...80 м3/ч. Скребковые двухцепные экскаваторы (рис. 4.9, б) используют для рытья траншей прямоугольного и трапецеидального сечений глубиной до 3,5 м, шириной по дну до 1,1 м и поверху до 2,8 м в талых грунтах I — III групп с включением камней диаметром до 0,2 м и в мерзлых грунтах с глубиной промерзания до 1,2 м. Разработка грунта ведется режущими элементами скребкового типа и транспортирующими заслонками. Для отрывки траншей трапецеидального профиля на рабочем органе экскаватора устанавливают активные цепные откосообразователи. Грунт, отделяемый цепями от целика, обрушивается на дно траншеи, откуда выносится на поверхность транспортирующими заслонками. Для разработки мерзлых грунтов устанавливается сменное рабочее оборудование — ковшовая цепь с зубьями-клыками. Поднятый наверх скребками (ковшами) грунт выгружается на поперечный ленточный конвейер и отводится им в сторону от траншеи (до 3 м). Производительность двухцепных экскаваторов до 220 м3/ч. Роторные траншейные экскаваторы (рис. 4.9, в) разрабатывают траншеи различного сечения в грунтах I — IV групп с включением камней диаметром до 0,3 м, а также в мерзлых грунтах при глубине промерзания до 1,5 м. Ширина траншей поверху до 3,2 м, понизу до 2,1 м, глубина до 2,5 м. Во время поступательного движения трактора и вращательного движения ротора ковши с зубьями непрерывно разрабатывают, поднимают на поверхность и выгружают грунт на ленту поперечного конвейера. Размеры траншей определяются шириной ковшей и степенью заглубления в грунт ротора. Для образования откосов с крутизной до 1 : 0,25 в талых грунтах экскаваторы оборудуются пассивными ножевыми откосниками, в мерзлых грунтах — активными фрезерными уширителями. Производительность роторных экскаваторов до 1200 м3/ч. Экскаваторы-каналокопатели работают по тому же принципу, что и роторные. В отличие от роторных они способны отрывать каналы с пологими откосами (до 1 : 1,5) при ширине понизу до 2,5 м, глубине до 3 м. До установки экскаватора непрерывного действия на трассу необходимо выполнить планировочные работы. Ширина спланированной полосы должна быть не меньше ширины гусеничного хода экскаватора, предназначенного для рытья траншеи. После планировочных работ и разбивки оси траншеи рытье траншеи, как правило, начинают со стороны низких отметок продольного профиля (для удобства водоотлива) и ведут навстречу уклону, при этом отвалы грунта, вынутого из траншеи, следует размещать с одной стороны выемки (преимущественно с нагорной) для защиты вырытой траншеи от стока поверхностных вод и возможности выполнения последующих монтажных работ с другой стороны.
Производство работ экскаваторами непрерывного действия. Разработка грунта экскаваторами непрерывного действия осуществляется по следующей технологии. До начала разработки грунта поверхность земли по трассе траншеи выравнивается бульдозером. Ширина этой полосы должна быть не менее ширины гусеничного хода экскаватора. После планировочных работ и разбивки осей отрывка грунта в траншее, как правило, ведется в сторону повышения рельефа. При этом отвал грунта размещается с одной стороны (преимущественно с нагорной) для защиты траншеи от поверхностных вод. Заданный продольный уклон траншеи и глубину разработки грунта регулируют подъемом или опусканием рабочего органа (ротора или ковшовой цепи) экскаватора (рис.4).
Рис.4. Разработка траншей многоковшовыми экскаваторами черпания а - цепным экскаватором; б - роторным экскаватором; в - поперечный профиль траншеи и временного отвала.
19. Монтаж строительных конструкций. Схема технологического процесса монтажа строительных конструкций
Монтаж строительных конструкций — это комплексно-механизированный процесс поточной сборки зданий и сооружений из элементов и конструктивных узлов заводского изготовления. До начала монтажных работ должны быть выполнены все работы подъемной части зданий. Монтаж конструкций, как правило, следует вести непосредственно с транспортных средств.
При монтаже должна быть обеспечена неизменяемость и устойчивость каждой смонтированной конструкции или ячейки сооружения. Последовательность монтажа должна предусматривать возможность сдачи в заданные сроки отдельных участков сооружения под отделку или монтаж оборудования.
Монтаж строительных конструкций состоит из подготовительных и основных процессов.
В подготовительные процессы входят транспортирование, складирование и укрупнительная сборка.
Основные процессы—это подготовка к подъему и подъем конструкций, выверка и временное закрепление, замоноличивание стыков и швов, а также противокоррозионная защита конструкций.
В зависимости от степени укрупнения собираемых элементов различают следующие методы зданий и сооружений:
мелкоэлементный монтаж из отдельных конструктивных деталей. Ввиду значительной трудоемкости применение этого метода ограничено. Примером мелкоэлементного монтажа может служить полистовая сборка резервуаров;
- поэлементный монтаж — монтаж конструктивными крупными элементами (панели, колонны, плиты и т. д.). Этот метод имеет наиболее широкое распространение;
блочный монтаж из геометрически не изменяемых блоков, предварительно собранных из отдельных конструкций. Монтажные блоки могут быть в следующем конструктивном исполнении:
плоские — например, блоки элементов фахверка металлических конструкций зданий, блоки оболочек;
пространственные — например, блоки покрытий промышленных зданий, блоки объемно-элементных зданий и т. д.
В ряде случаев блоки могут иметь полную степень готовности, включая наличие коммуникаций и комплектующего их легкого оборудования. Примером могут служить строительно-технологические блоки покрытий одноэтажных промышленных зданий. Их выполняют в виде статически устойчивого блока, состоящего из ферм, связей, конструкций покрытия, кровли и подвешенных к блоку вентиляционных или других коммуникаций.
Принцип блочного монтажа принят за основу при комплектно блочном методе строительства, разработанном в нашей стране. Сущность метода в том, что в стадии проектирования объект разделяют на крупногабаритные, но транспортабельные, конструктивно законченные и укомплектованные оборудованием монтажные блоки. Их изготовляют в обжитых районах в заводских условиях и затем в специальных контейнерах (боксах) доставляют на тяжелых самолетах, вертолетах, вездеходах или других транспортных средствах, к месту назначения, где из них собирают здания и сооружения.
Контейнер для транспортирования таких блоков, масса которых может доходить до 100 т и более, выполняют в виде легкого металлического каркаса с листовым (при необходимости — утепленным) покрытием.
Комплектно-блочный метод широко используют в стране при строительстве в необжитых районах, отдаленных от производственных баз нефтегазовых комплексов, насосных станций, технологических трубопроводов, подстанций и ряда других объектов.
Комплектно-блочный метод существенно улучшает технико-экономические показатели строительства; Так, по данным Миннефтегазстроя СССР, применение этого метода позволяет переместить до 40 % работающих со строительной площадки на сборочно-комплектовочные предприятия, расположенные в обжитых районах, и сократить продолжительность строительства в 2...2,5 раза. Развитию комлектно-блочного метода будут способствовать выпуск технологического оборудования, приспособленного для блочной компоновки, увеличение массы блоков и создание специальной техники для их транспортирования и монтажа.
При организации монтажных работ (рис. ХТ.1) необходимо предусматривать наличие и развитие фронта монтажных и послемонтажных работ, нужную последовательность монтажа, порядок
укрупнения конструкций, мероприятия по доставке монтажных элементов в рабочую зону и т. д.
Могут иметь место следующие варианты организации монтажных работ: доставка конструкций с завода или площадки укрупнительной сборки и предварительное складирование их на объекте в зоне действия монтажного крана этот вариант является следствием особых условий или недостаточно четкой организации монтажных работ (рис. ХI. 1,а);
доставка укрупненных конструкций непосредственно с заводов и их монтаж с транспортных средств (рис. ХТ.1,б);
разгрузка и складирование отправочных элементов конструкций на площадке укрепительной сборки, укрупнение и транспортирование укрупненных конструкций в зону действия монтажного крана (рис. ХI.1,в);
доставка к объекту линейных и плоских конструкций, наземная сборка из них пространственных блоков в зоне действия монтажного механизма или на конвейерной линии (рис. ХТ, г);
изготовление конструкций непосредственно в зоне действия монтажного крана. Такой вариант иногда применяют при монтаже тяжелых нетранспортабельных железобетонных конструкций, которые экономичнее изготовлять непосредственно у места их монтажа. Эти варианты можно комбинировать. Возможности повышения эффективности организации монтажных работ на крупных объектах расширяет использование поузлового метода строительства. При этом методе в общем комплексе строительства в стадии проектирования выделяют общеплощадочные, строительные и технологические узлы. Каждый узел — это локальный строительно-технологический комплекс, который может быть завершен, включая строительные работы, монтаж оборудования и пусконаладочные работы, независимо от монтажа других узлов. Так как каждый узел по отношению ко всему строительству автономен и имеет четкие границы, то те или иные сбои в ходе производства работ не затрагивают всего комплекса и не вызывают необходимости корректировки общего плана и графика работ.
Технологическая структура монтажных процессов
Важным фактором для строителей является технологичность возводимого здания в целом, включая технологичность используемых монтажных элементов, которые подразумевают:
- минимальное количество типоразмеров монтируемых элементов, т. е. степень типизации конструкций;
- максимальная строительная готовность поставляемых конструкций - степень точности геометрических размеров и положения закладных деталей;
- удобство строповки, подъема, установки и выверки всех элементов;
- простота и удобство заделки всех стыков и заливки швов;
- близкий к 1 показатель монтажной массы, выражающий отношение среднего веса конструкций к максимальному, т. е. их укрупненность и равновесность.
Комплексный технологический процесс монтажа сборных строительных конструкций - совокупность процессов и операций, в результате выполнения которых получают каркас, часть здания или сооружения, полностью возведенное сооружение. Вся совокупность процессов, позволяющая получить готовую смонтированную продукцию, состоит из транспортных, подготовительных, основных и вспомогательных процессов.
Транспортные процессы состоят из транспортирования конструкций на центральные и приобъектные склады, погрузки и разгрузки конструкций, сортировки и укладки их на складах, подачи конструкций с укрупнительной сборки или складов на монтаж, транспортирование материалов, полуфабрикатов, деталей и приспособлений в зону монтажа. При складировании конструкций особо контролируют их качество, размеры, маркировку и комплектность. При монтаже зданий с транспортных средств исключаются процессы разгрузки и сортировки, так как конструкции сразу подаются на монтаж.
Подготовительные процессы включают: проверку состояния конструкций, укрупнительную сборку, временное (монтажное) усиление конструкций, подготовку к монтажу и обустройство, подачу конструкций в виде монтажной единицы непосредственно к месту установки. Дополнительно входят процессы по оснастке конструкций приспособлениями для временного их закрепления и безопасного выполнения Работ, нанесение установочных рисок на монтируемые элементы, намека подмостей и лестниц, если это требуется выполнить до подъема конструкций.
Вспомогательные процессы включают подготовку опорных поверхностей фундаментов, выверку конструкций, если ее выполняют после их установки, устройство подмостей, переходных площадок, лестниц и ограждений, выполняемых в период установки конструкций.
Основные или монтажные процессы - установка конструкций в проектное положение, т. е. собственно монтаж. В состав монтажных процессов входят:
- подготовка мест установки сборных конструкций;
- строповка и подъем с необходимым перемещением в пространстве, ориентировании и установке с временным закреплением;
- расстроповка;
- окончательная выверка и закрепление;
- снятие временных креплений;
- заделка стыков и швов.
В зависимости от вида конструкций, монтажной оснастки, стыков и условий обеспечения устойчивости, выверку можно осуществлять в процессе установки, когда конструкция удерживается монтажным краном, или после установки при временном ее закреплении.
Приведенная структура процесса монтажа строительных конструкций является обобщающей и в каждом конкретном случае может быть уточнена в сторону увеличения или уменьшения подлежащих выполнению отдельных операций и процессов.
Монтаж строительных конструкций (с точки зрения его организации) может быть осуществлен по двум схемам:
- монтаж со склада
- монтаж с транспортных средств.
При осуществлении монтажа со склада все технологические операции, рассмотренные ранее, выполняют непосредственно на строительной площадке.
Монтаж «с колес» предполагает выполнение на строительной площадке в основном только собственно монтажных процессов. Полностью изготовленные и подготовленные к монтажу конструкции поставляют на строительную площадку с заводов-изготовителей в точно назначенное время и эти конструкции непосредственно с транспортных средств подают к месту их установки в проектное положение. Такая организация строительного процесса должна обеспечивать комплектную и ритмичную доставку только тех конструкций, которые должны быть смонтированы в данный конкретный момент. Этот метод прогрессивен, при нем практически отпадает потребность в приобъектном складе, исключается промежуточная перегрузка сборных элементов, создаются благоприятные условия для производства работ на стесненных строительных площадках, организация труда на строительной площадке начинает напоминать заводскую технологию сборочного процесса, обеспечивается ритмичность, непрерывность строительного процесса
20. Каменная кладка в условиях низкой и высокой температур
Отрицательная температура отражается на процессе ведения каменных работ. Каменщик в теплой одежде и рукавицах под воздействием холода ведет кладку менее аккуратно. Изменяются свойства материалов, главным образом раствора, который при замерзании, в отличие от других материалов, увеличивается в объеме до 9%, а до замерзания быстро теряет подвижность и плохо заполняет узкие щели в кладке. В результате раствор не только теряет прочность, но также не обеспечивает должной монолитности кладки и способствует ее повышенной неравномерной деформативности. Рассмотрим физические процессы, протекающие в зимней кладке. При укладке теплого раствора на охлажденный кирпич из-за гравитации (тяготения к земле) и градиента (разности) температур вода при укладке раствора уходит в нижние кирпичи. Раствор обезвоживается, теряет подвижность и не обжимается верхним кирпичом. При дальнейшем охлаждении оставшаяся вода превращается в лед. увеличивается в объеме, разрыхляя шов и препятствуя его сцеплению с кирпичами. После оттаивания твердение раствора возобновляется, но из-за отсутствия должного количества воды процессы гидролиза и гидратации цемента протекают вяло, не обжатый при укладке раствор дает большую и неравномерную усадку. В результате зимняя кладка отличается от летней большей деформативностью и меньшей прочностью. При этом тем больше, чем раньше она была заморожена. С учетом этого разработан ряд методов выполнения каменных работ в зимнее время. Метод замораживания заключается в том, что кладка ведется так же, как летом, но на подогретом растворе. В этом случае при отрицательных температурах можно возводить не более четырех этажей (15 м); запрещено выполнять кладку из рваного бута. Раствор при укладке в среднем должен быть подогрет до абсолютной температурь наружного воздуха. Кирпич и камень должны. Укладываться по однорядной системе перевязки, с полным заполнением швов. Раствор при кладке расстилается не более, чем на 2 кирпича при выполнении версты; не более, чем на 6…8 кирпичей при кладке забутки. На период оттаивания должен осуществляться контроль за деформацией кладки и, при необходимости, осуществляться мероприятия по ее разгрузке и временному усилению. Практика строительства показала, что если раствор в кладке до замерзания приобретает 20% своей проектной прочности (критическая прочность), то этого достаточно для дальнейшей безопасной эксплуатации каменной конструкции. На этом явлении основан ряд методов каменных работ с применением любой системы перевязки кладки. Кладка на растворах с противоморозными добавками может применяться при температуре окружающей среды до —35 °С. Это основано на свойстве растворов ряда солей замерзать при отрицательной температуре, что обеспечивает условия твердения строительных растворов в определенных пределах при отрицательных температурах. При температуре до —15 °С в строительстве применяют нитрит натрия (NaN02), при более низкой температуре — смесь из нитритов, нитратов и хлоридов, а также поташ (К2С03). Однако, за исключением нитрита натрия, перечисленные соли обладают рядом свойств (быстрое схватывание раствора, коррозия арматуры, высолы и гигроскопичность стен и т.д.), которые затрудняют их широкое использование, особенно при строительстве жилых зданий Прогрев кладки нагревательными устройствами (ТЭНамП-калориферами и пр.) можно осуществлять только изнутри закрытого помещения. При этом желательно, чтобы в это время кладка снаружи нагревалась солнечными лучами, поскольку в противном случае она может потерять равновесие в результате одностороннего отогревания. Рекомендовавшиеся ранее паропрогревание и электропрогревание кладки, а также применение быстротвердеющих растворов широкого распространения не получили. Применяющаяся в некоторых странах (Канада, ФРГ) кладка в тепляках под пленочным покрытием создает условия работ, аналогичные летним. В нашей стране этот метод пока распространения не получил. Для кладки в условиях жаркого климата характерны раннее начало работы, перерыв с 12 до 17 ч, затем продолжение работы. При перерывах в работе кладку укрывают подсобными солнцезащитными покрытиями. Применяется сложный раствор литой консистенции состава 1:1:6…1:1:8 (цемент: известь или глина: песок). Кирпич перед укладкой погружают в воду и удерживают до полного водонасыщения; перед укладкой раствора производится смачивание ранее выложенного ряда. Затеняются места хранения материалов и рабочие места; емкости для воды, бункеры с вяжущим компонентом и заполнителем окрашивают белой краской.
21. Возведение каменных конструкций в зимних условиях
Влияние отрицательных температур на прочность кладки.
В зимних условиях для каменной кладки применяют раствор на цементном вяжущем. Однако при понижении температуры ниже 0°С нарушается влагообмен из раствора в камни и необходимого уплотнения швов не происходит, что существенно влияет на прочность кладки. Свободная вода в растворе превращается в лед, и, расширяясь при замерзании, частично нарушает структуру цементного теста. При замерзании прочность раствора увеличивается, но с наступлением оттепели он из твердого состояния переходит в пластичное, и прочность кладки резко снижается, достигая критической величины. Прочность раствора в кладке может оказаться близкой к нулю. При положительной температуре после оттаивания кладки цементное тесто продолжает твердеть, однако нарушенная структура восстанавливается не полностью и конечная прочность раствора несколько нижелетней (рис. VIII.а). Чем раньше раствор замерзает, тем больше потери прочности.
Способы выполнения кладки в зимних условиях. Для обеспечения проектной прочности конструкции из кирпича и камней правильной формы в зимних условиях возводят одним из следующих способов: замораживанием раствора, на растворах с противоморозными химическими добавками и прогревом кладки.
Кладка способом замораживания. Согласно СНиП 3.03.01 — 87 допускается замораживание раствора в швах кладки при ограничении высоты возведения конструкции до 15 м (четыре этажа) с последующим оттаиванием и твердением при потеплении или искусственном отогреве кладки нижних этажей. Не допускается применять этот способ при кладке конструкций внецентренно сжатых со значительным эксцентриситетом; конструкций, подвергающихся вибрации и динамическим нагрузкам во время оттаивания; при выполнении бутовой кладки из камней неправильной формы, а также в районах с повышенной сейсмичностью.
Кладку способом замораживания выполняют на растворах марки не ниже М10, с запасом тепла, достаточным на время его укладки и обжатия камнями кладки до требуемой толщины шва, а также для частичного влагообмена между раствором и кладкой, чтобы достичь определенной прочности его до замерзания. Если раствор холодный, он быстро замерзает, его нельзя расстелить тонким слоем, швы получаются толстыми и неодинаковой толщины, что приводит к большой и неравномерной осадке кладки при оттаивании и может быть причиной аварии. Поэтому нормами регламентируется температура раствора в момент укладки не ниже 5, 10 и 15°С, при температуре наружного воздуха соответственно до минус 10, 20 и ниже минус 20°С. Для снижения теплопотерь при доставке раствора растворовозы и автосамосвалы утепляют, а раствор подогревают в пути отработанными газами автомобиля. Также утепляют раздаточные бункеры и растворные ящики на объекте. При необходимости в них подогревают раствор с помощью трубчатых электронагревателей. Кирпич и камни при укладке должны быть очищены от снега и льда. Снижение конечной прочности кладки, выполняемой способом замораживания, следует компенсировать повышением марки раствора: на одну ступень при среднесуточной температуре наружного воздуха До минус 20 °С, на две ступени — при температуре ниже минус.
Для обеспечения устойчивости каменных конструкций в процессе оттаивания предусматривают конструктивные мероприятия: укладывают в процессе кладки в углах и пересечениях стен стальные связи (рис. VIII. 11,6), заанкеривают элементы перекрытий после возведения каждого этажа; над оконными и дверными коробками оставляют зазоры на осадку при кирпичной кладке не менее 5 мм и при мелкоблочной кладке — 3 мм. За кладкой в период оттаивания устанавливают постоянное наблюдение и, когда потребуется, ставят временное крепление в виде стоек в проемах, обжимных обойм стен, подкосов, оттяжек и др.
Кладка на растворе с противоморозными добавками. Химические добавки вводят при приготовлении раствора. Они снижают температуру его замерзания и обеспечивают тем самым обжатие и частичное твердение при отрицательных температурах. В качестве противоморозных добавок применяют хлористый кальций (СаСО), хлористый натрий (МаС1), нитрит натрия (МаМО2), поташ (К2С03), нитрит кальция с мочевиной (НКМ). Первые две добавки повышают гигроскопичность кладки и вызывают появление высолов, в связи с чем их рекомендуют использовать в растворах только для подземной части зданий в количестве 1,5...7,5% от массы цемента в растворе при температуре воздуха от 0 до минус 15°С. С добавкой нитрита натрия, поташа или НКМ применяют растворы для возведения наземных каменных конструкций. Растворы с добавкой нитрита натрия 2...10% от массы цемента могут твердеть на морозе от О до минус 15°С, а при добавке поташа 5...15% —от минус 5 до минус 30 °С. Однако при большой концентрации этих добавок раствор быстро схватывается, загустевает и теряет подвижность, что затрудняет его расстилание. Для замедления схватывания при приготовлении растворов вводят сульфитно-дрожжевую бражку (1...2,5% от массы цемента) или другие замедлители. Марка раствора с противоморозными добавками должна быть не ниже М50.
Кладка с прогревом. Прогрев кладки применяют в том случае, когда нельзя осуществить способ замораживания, а применение противоморозных добавок не обеспечивает заданной проектом прочности конструкций, воспринимающих большие нагрузки (столбы, простенки и др.). Для прогрева кладки применяют электроэнергию (электропрогрев), пар (паропрогрев), подогретый воздух (воздухообогрев). При прогреве в кладке поддерживается положительная температура до приобретения раствором заданной прочности. Кладку выполняют на растворе марки не ниже М10.
Электропрогрев кладки осуществляют, закладывая в горизонтальные швы пластинчатые или стержневые электроды, которые отпайками подключают к питающим электропроводам переменного тока напряжением 220...380 В. В кирпичных столбах в качестве электродов используют уложенные при кладке арматурные сетки «зигзаг» (рис. VIII. 11,в).
Паропрогрев проводят в паровой рубашке — опалубке, укрывающей поверхность каменной конструкции, куда подают пар от разводящей сети.
Воздухообогрев осуществляют подогретым воздухом от калорифера также с применением ограждающей рубашки в виде плоского или секционного тепляка, охватывающего часть каменной конструкции. Объемные тепляки применяют при возведении фундаментов в траншеях или котлованах, поддерживая там температуру калориферами не ниже 10°С на уровне 0,5 м от подошвы кладки.
22. Устройство набивных свай
Набивные сваи устраивают на месте их проектного положения путем укладки (набивания) в полости (скважины), образуемые в грунте, бетонной смеси или песка (грунта). Сваи часто делают с уширенной нижней частью пятой. Уширение получают путем разбуривания грунта специальными бурами, распирания грунта усиленным трамбованием бетонной смеси в нижней части скважины или путем взрывания заряда взрывчатого вещества.
В зависимости от способов создания в грунте полости и методов укладки в уплотнения материала забивки сван подразделяют на буронабивные, пневмонабивные, вибротрамбованные и частотрамбоваяные.
Устройство буронабивных бетонных и железобетонных свай. Характерной особенностью технологии устройства буронабивных свай являются предварительное бурение скважин до заданной отметки и последующее формирование ствола сваи.
В зависимости от грунтовых условий буронабивные сваи устраивают одним из следующих трех способов: без крепления стенок скважин (сухой способ), с применением глинистого раствора для предотвращения обрушения стенок скважины, с креплением скважин обсадными трубами.
Сухой способ (рис. УIII. 16) применим в устойчивых грунтах, которые могут держать стенки скважины (просадочные и глинистые твердой, полутвердой и тугопластичной консистенции) - Технология устройства таких свай состоит в следующем. Методами вращательного бурения (шнековая колонна или ковшовый бур) в грунте разбуривают скважину необходимого диаметра и на заданную глубину. После достижения забоем скважины проектной отметки в необходимых случаях нижнюю часть скважины расширяют с помощью специальных расширителей, закрепленных на буровой штанге я входящих в комплект бурового станка. Принцип работы расширителя следующий: давление, передаваемое через штангу, раскрывает шарнирную систему ножей расширителя; при вращении штанги ножи срезают грунт, попадающий в бадью, расположенную под расширителем. За 4—5 операций срезывания и извлечения грунта образуется уширенная полость диаметром до 1,6 м. После приемки скважины в установленном порядке при необходимости в ней монтируют арматурный каркас и бетонируют методом вертикально перемещающейся трубы (ВПТ). Применяемые в строительстве бетонолитные трубы, как правило, состоят из отдельных секций я имеют стыки, позволяющие быстро и надежно соединять трубы. В приемную воронку бетонную смесь подают непосредственно из автобетоносмесителя или с помощью специального загрузочного бункера. По мере укладки бетонной смеси бетоволитную трубу извлекают из скважины. Уплотняют бетонную смесь в скважине с помощью вибраторов, укрепленных на приемной воронке бетонолитной трубы. По окончании бетонирования скважины голову сваи формуют в специальном инвентарном кондукторе и в зимнее время защищают утеплителем. Чаще всего этой технологии изготовляют буронабывные сван диаметром 400, 500, 600, 1000 и 1200 мм и длиной до 30 м.
Глинистый раствор для удержания стенок скважин от обрушения применяют при устройстве буронабивных свай (рис. УIII. 17) в неустойчивых обводненных грунтах. В этом случае скважины бурят вращательным способом. Однако при проходке по скальным включениям и прослойкам используют сменные рабочие органы ударного типа (грейферы, долота). Глинистый раствор поступает в скважину по пустотелой буровой штанге. За счет гидростатического давления, оказываемого ЭТИМ раствором, плотность которого 1,2...1,3г/сма, устраивают сван без обсадных труб. Глинистый раствор готовят па месте производства работ преимущественно из бентонитовых глин, и ПО мере бурения его нагнетают в скважину. Поднимаясь по скважине вдоль ее стенок, глиняный раствор попадает в зумпф откуда возвращается насосом в буровую штангу для дальнейшей циркуляции. Затем в скважину устанавливают арматурпый каркас. Бетонную смесь подают с помощью вибробункера с бетонолитной трубой, которую опускают в скважину. Вибрируемая бетонная смесь, поступая в скважину, вытесняет глинистый раствор. По мере заполнения скважины бетонной смесью бетоновод извлекают.
Рассмотренный метод крепления стенок скважин является наиболее простым. Однако он недостаточно надежен и весьма трудоемок при производстве работ зимой.
Устройство буронабивных свай с креплением стенок скважин обсадными трубами (рис. УIII. 18) возможно в любых геологических и гидрогеологических условиях. Обсадные трубы можно оставлять в грунте или извлекать из скважин в процессе изготовления свай (инвентарные трубы). Секции обсадных труб, как правило, соединяют стыками специальной конструкции или с помощью сварки. Погружают обсадные трубы в процессе бурения скважины гидродомкратами, а также посредством забивки трубы в грунт или вибропогружением. Бурят скважины вращательным или ударным способом специальными установками.
При ударном бурении осадная труба погружается в грунт по мере разработки скважины. При этом отдельные секции обсадных труб наращивают по мере необходимости.
Затем бурят следующий участок скважины, после чего наращивают и погружают в скважину очередную секцию обсадной трубы. Эти операции повторяют до окончания бурения скважины на проектную отметку.
После зачистки забоя и установки в скважине арматурного каркаса скважину бетонируют методом ВПТ. По мере заполнения скважины бетонной смесью инвентарную обсадную трубу извлекают. При этом специальная система домкратов, смонтированных на установке, сообщает обсадной трубе возвратно-поступательное и полувращательное движение, дополнительно уплотняя бетонную смесь. По окончании бетонирования скважины голову сваи формуют в специальном инвентарном кондукторе.
Для устройства уширения в основаниях свай, как правило, применяют взрывной способ. для этого (рис. УIII. 19) в пробуренной скважине устанавливают обсадную трубу так, чтобы ее нижний конец не доходил до дна скважины на 1,2...1,5 м, т. е был за пределами действия камуфлетного взрыва. В обсадную трубу опускают на дно скважины заряд взрывчатки расчетной массы и выводят проводники от детонатора к подрывной машине. Трубу заполняют бетонной смесью и производят взрыв. Энергия взрыва уплотняет грунт и создает сферическую полость, которая немедленно заполняется бетонной смесью из обсадной трубы.
Окончательно заполняют скважину описанным выше способом.
В СССР буронабивные сван изготовляют диаметром 880...1200мм, длиной до 35 м. для устройства буронабивнмх свай используют литую бетонную смесь с осадкой конуса 1б...20 см.
Пневмонабивные сваи применяют при устройстве свайных фундаментов в грунтах с большим притоком воды, затрудняющим сооружение буронабивных свай. В этом случае бетонную смесь укладывают в полость обсадной трубы при постоянном повышенном давлении воздуха (0,25...0,3 МПа), который подается от компрессора через ресивер. Бетонную смесь подают небольшими порциями через специальное устройство — шлюзовую камеру, действующую по принципу пневмонагнетательных установок, применяемых для транспортирования бетонной смеси. Шлюзовые камеры состоят из двух отрезков труб, соединенных фланцами, которые имеют верхние и нижние отверстия, закрываемые клапанами. При подаче смеси через воронку в верхнюю камеру закрыт ее нижний клапан; после подачи порции верхний клапан верхней камеры закрывается, а нижний открывается и т. д. В целях экономии сжатого воздуха применяют герметизированные бетоносмесителя.
Армируют пневмонабивные сваи путем погружения стержней арматуры в свежий бетон.
Вибротрамбованные сваи (рис. УIII. 20) используют в сухих связных грунтах, в которых можно укладывать бетонную смесь в открытую скважину глубиной 4...6 м.
Такие сваи устраивают следующим образом. В грунт с помощью вибропогружателя, подвешенного к экскаватору погружают стальную обсадную трубу, имеющую на конце съемный железобетонный башмак.
После погружения трубы вибропогружатель снимают и внутреннюю полость трубы заполняют на 0,8... 1 м бетонкой смесью. С помощью трамбующей штанги, подведенной к вибропогружателю, смесь трамбуют, в результате чего она вместе с башмаком вдавливается в грунт, образуя при этом уширенную пяту. Заполнив бетонной смесью обсадную трубу, ее извлекают из грунта с помощью
— экскаватора при работающем вибропогружателе. После извлечения трубы устанавливают арматурный каркас для связи головы сваи с железобетонным ростверком.
Частотрамбованные сваи устраивают путем забивки обсадных труб, опирающихся на металлический (обычно чугунный) наконечник. Затем в полости, образованной обсадной трубой, устраивают армированную (или неармированную) сваю, уплотняя бетонную смесь с помощью ударов паровоздушного молота двойного действия, передающихся через трубу.
Частотрамбованные сваи (рис. У11121) устраивают с помощью специально оборудованного копра в такой последовательности. На копер лебедкой поднимают паровоздушный молот двойного действия и обсадную трубу, которая в верхней части имеет оголовок. На нижний конец обсадной трубы насаживают металлический башмак со смоляным канатом, чтобы исключить проникание в трубу воды. Под действием ударов молота обсадная труба погружается до проектной отметки. Погружаясь, труба раздвигает частицы грунта и уплотняет его. Затем молот поднимают и в полость трубы опускают арматурный каркас (если сваи армируются). Из вибробадьи с помощью каната через воронку подают в полость обсадной трубы бетонную смесь с осадкой конуса 8...10 см.
Параллельно с укладкой смеси извлекают (вытягивают) обсадную трубу из грунта, причем металлический башмак остается у основания сваи. В это время молот двойного действия соединенный с обсадной трубой, уплотняет бетонную смесь. При этом сила его погружающего удара в 2 раза меньше выдергивающих усилий, передаваемых на обсадную трубу. При ударах молота, направленных вверх, труба должна извлекаться на 4...5 см из грунта, а при ударах, направленных вниз,— погружаться на 2...3 см. Удары, направленные вниз, наряду с вибрационным воздействием трубы значительно уплотняют бетонную смесь, впрессовывая ее в стенки скважины, что в свою очередь дополнительно уплотняет грунт.
Песчаные (грунтовые) набивные и грунтобетонные сваи применяют для уплотнения слабых грунтов. В этих случаях используют самоходные стреловые краны со специальными приспособлениями в виде стальной обсадной трубы с киническим четырехлопастным раскрывающимся наконечником. Трубу заполняют песком (грунтом) и с Помощью вибропогружателя погружают на проектную глубину (рис. У1!1.22). Когда труба движется вверх, кольцо, открывающее лепестки наконечника, спадает и остается в грунте, а песок (сухой грунт) заполняет скважину. Песок уплотняют за счет вибрации от погружателя или трамбовками с помощью легкого копра. Таким способом выполняют набивку скважин на глубину до 7м.
В последние годы стали устраивать грунтобетонные сваи, для чего применяют бурильно-крановые машины с пустотелой буровой штангой, имеющей на конце смесительный бур с режущими и перемешивающими лопастями. Через штанги нагнетают растворонасосом водоцементную суспензию, изготовляемую в растворосмесителе. Смесительный бур при обратном вращении и извлечении послойно уплотняет грунт, насыщенный водоцементной эмульсией в результате образуется грунтобетонная свая, изготовленная на месте без выемки грунта.
23. Организация поточного производства монтажных и каменных работ
Основная особенность возведения многоэтажных зданий с кирпичными стенами состоит в сочетании выполнения монтажных и каменных работ. Оба этих процесса неразрывно связаны между собой и могут выполняться параллельно либо с некоторым интервалом во времени.
Специфика этих работ в том, что их выполнение связано с соблюдением необходимых технологических перерывов. Монтаж очередного этажа каркасного здания разрешается производить только после достижения бетоном, используемым для омоноличивания стыков, узлов и швов перекрытий, не менее 70% проектной прочности, а для кирпичной кладки — 50%.
Возведение кирпичных зданий следует осуществлять только поточным методом, предусматривающим деление здания на несколько одинаковых по трудоемкости захваток: по одно-, двух- и трехзахватной системам.
Однозахватная система организации работ применяется преимущественно при строительстве небольших в плане односекционных домов, при одноэтажном строительстве, когда кладку ведут на всю высоту этажа при трехъярусном членении. Каменную кладку и монтаж ведут каменщики, освоившие профессию монтажника. Кирпичная кладка по периметру здания на высоту яруса должна быть закончена к концу первой смены. В этот же день во вторую смену выполняют вспомогательные работы: установку подмостей, доставку кирпича на подмости и т. д. Через три дня, завершив кладку третьего яруса, бригада разделяется на монтажные звенья по 4...5 человек, в зависимости от числа звеньев сборные элементы монтируют в две или три смены. На захватке (рабочем участке), где выполняют монтажные работы, по условиям техники безопасности не могут одновременно работать каменщики и наоборот.
В сельскохозяйственном строительстве при возведении небольших рассредоточенных объектов, при строительстве кирпичных коттеджей целесообразно, чтобы весь комплекс работ вела одна комплексная бригада с внутри звеньевой специализацией. В состав такой бригады должны входить звенья каменщиков, монтажников и такелажников, плотников и транспортных рабочих. Ведущим в бригаде является звено каменщиков, остальные звенья комплектуют с учетом обеспечения ими работы каменщиков и монтажников. При такой организации и кооперировании труда можно сократить внутрибригадные простои, уменьшить объем вспомогательных работ. Для ряда объектов, в том числе животноводческих комплексов, ведущим может оказаться звено монтажников, при значительных объемах монтажных работ — самостоятельная бригада.
При поточной организации работ целесообразно наличие четырех бригад (звеньев), выполняющих возведение нулевого цикла, кирпичную кладку, монтаж сборных конструкций, кровельщиков и отделочников, выполняющих свои работы в определенном, общем для всех ритме и последовательно переходящих с одного объекта на другой.
Двухзахватная система является наиболее распространенной и ее применяют при строительстве двух-, трех- и четырехсекционных зданий. Здание в плане разбивают на две примерно равные по трудоемкости захватки: на первой ведут кладку, на второй — монтаж конструкций каркаса этажа, монтаж перегородок и других встроенных конструкций, устанавливают подмости. Состав рабочих звеньев должен обеспечить завершение работ на обеих захватках одновременно, после чего звенья меняются захватками. Такая последовательность сохраняется при возведении всех этажей здания. Работа может быть организована в одну, две и три смены.
24. Каменные работы. Правила резки каменной кладки
Назначение каменных работ и виды каменной кладки. Каменные работы выполняют при возведении различных каменных конструкций зданий и сооружений; фундаментов, стен, столбов, перегородок и др.
В зависимости от применяемых материалов различают следующие виды каменной кладки: кирпичную, мелкоблочную, бутовую, бутобетонную, тесовую.
Кирпичная кладка — наиболее распространенная. Выполняют ее из полнотелого и пустотелого глиняного кирпича для всех конструкций марок 75...300 (ГОСТ 530—80) и силикатного полнотелого, пустотного и пористого кирпича для наземных конструкций марок 75...300 (ГОСТ 379—79). Для строительства промышленных печей, обмуровки котлов, футеровки топок печей и т. д. применяют огнеупорный кирпич.
Мелкоблочную кладку выполняют из искусственных и природных камней правильной формы с размерами и массой, допускающими ручную кладку. К искусственным материалам относят: керамические (ГОСТ 530—80) и силикатные (ГОСТ 379—79) камни, бетонные камни, грунтобетонные блоки и саман. Последние два вида мелких блоков применяют в сельскохозяйственном строительстве. В качестве природных материалов используют камни правильной формы, выпиленные из известняка, ракушечника, туфа и др. (ГОСТ 4001—84).
Бутовая кладка — это кладка из природных камней неправильной формы, называемых бутовым камнем (ГОСТ 22132—76). Ее применяют главным образом для устройства фундаментов и стен подвалов.
Бутобетонная кладка состоит из бутового камня, втапливаемого в бетонную смесь, и применяют ее для тех же целей, что и бутовую.
Тесовую кладку выполняют из природных предварительно обработанных камней. Применяют ее для облицовки монументальных зданий и сооружений.
Каменную кладку создают поштучной укладкой камней на раствор, связывающий камни между собой. В результате благодаря выравниванию поверхностей соприкосновения обеспечивается более равномерная передача усилий на камни, а также предохраняется кладка от продувания и проникания воды. Вид и состав раствора зависят от назначения каменной кладки, условий ее работы и указываются проектом.
Цементные растворы, обладающие высокой прочностью, используют для кладки конструкций, несущих большие нагрузки, а также конструкций, расположенных в насыщенных водой грунтах.
Сложные растворы (цементно-известковые или цементно-глиняные) применяют при нормальных нагрузках на кладку в сухих и влажных местах.
Известковые растворы, имеющие невысокую прочность, но обладающие пластичностью, применяют только для кладки в сухих местах.
Глиняные растворы предназначены для кладки из самана наземной части стен одноэтажных сельскохозяйственных зданий и для печных работ.
Для улучшения теплотехнических показателей кладки пользуются легкими растворами, которые в отличие от обычных тяжелых имеют вместо кварцевого песка шлаковый или пемзовый. В зависимости от прочности на сжатие установлены марки растворов 4...300. Существенное значение имеет подвижность раствора, выражаемая величиной погружения стандартного конуса в сантиметрах. Растворы с большой подвижностью обеспечивают более высокую производительность труда при кладке. Для повышения подвижности и водоудерживающей способности к жестким цементным растворам добавляют пластификаторы — сульфитно-спиртовую барду, мылонафт и др. Подвижность раствора для кирпича и мелких блоков должна быть в пределах 9...13 см, при наличии в них пустот — 7...8 см, для бутовой кладки — 4...6 см; для заливки швов этой кладки — 13...15 см.
В зависимости от принятой отделки поверхности стен швы между отдельными камнями полностью заполняют раствором, придавая им определенную форму расшивкой, или оставляют незаполненными на глубину 1...1.5 см. Соответственно кладка носит название под расшивку и впустошовку. Кладку, выполненную впустошовку, впоследствии оштукатуривают или облицовывают. Согласно нормативным требованиям, для кирпича и камней правильной формы толщина горизонтальных швов должна быть не менее 10 и не более 15 мм (средняя 12), вертикальных в пределах 8...15 мм (средняя 10).
Развитие каменных работ происходит в тесной связи науки с производством.
Наряду с совершенствованием технологии и организации каменных работ развиваются индустриальные методы возведения каменных конструкций с использованием для кладки стен вместо мелкоштучных камней крупных кирпичных блоков и виброкирпичных панелей.
Правила разрезки каменной кладки. Для обеспечения работы кладки как монолитного массива и предотвращения перемещения камней под действием нагрузок в процессе эксплуатации конструкции необходимо располагать их, соблюдая определенные условия, которые принято называть правилами разрезки.
Первое правило — кладку необходимо вести рядами, ограниченными плоскостями, перпендикулярными направлению действующих сил. Руководствуясь этим правилом, каменную кладку, воспринимающую вертикальные нагрузки, ведут горизонтальными рядами. В арках и сводах плоскости, ограничивающие ряды кладки, должны быть перпендикулярными к кривой давления. При этом обеспечивается работа камней на сжатие и исключаются сдвигающие усилия. Допустимое отклонение перпендикуляра к плоскостям, ограничивающим ряды кладки, с направлением действующих сил, выражаемое углом не должно превышать 15...17°. Величину этого угла определяют из условия уравновешивания сдвигающего усилия от действия наклонной силы и противодействующей ему силы трения.
Второе правило — внутри каждого ряда боковые грани камней должны образовывать две системы взаимно перпендикулярных плоскостей. При этом одна система плоскостей должна быть перпендикулярна постели и лицевой поверхности кладки, а вторая — параллельна лицевой поверхности и перпендикулярна постели. Эти плоскости образуют в кладке вертикальные поперечные и продольные швы. Если боковые грани камней в нарушение этого правила будут расположены наклонно, то они, уподобляясь клину, под действием нагрузок могут раздвинуть соседние камни, а кромки камней с острыми углами отколоть.
Третье правило — вертикальные поперечные и продольные швы в смежных рядах не должны совпадать, то есть иметь перевязку.
При использовании в кладке прочных растворов, на цементном вяжущем допускается оставлять без перевязки вертикальные продольные швы в пяти рядах или вертикальные поперечные швы в трех рядах кирпича. Если массив кладки разрезать по всей высоте вертикальными швами, то образуются отдельные неустойчивые столбы, которые под действием нагрузки могут деформироваться.
25. Материалы. Приспособления и инструменты для каменной кладки
Кирпичная кладка — наиболее распространенная. Выполняют ее из полнотелого и пустотелого глиняного кирпича для всех конструкций марок 75...300 (ГОСТ 530—80) и силикатного полнотелого, пустотного и пористого кирпича для наземных конструкций марок 75...300 (ГОСТ 379—79). Для строительства промышленных печей, обмуровки котлов, футеровки топок печей и т. д. применяют огнеупорный кирпич.
Мелкоблочную кладку выполняют из искусственных и природных камней правильной формы с размерами и массой, допускающими ручную кладку. К искусственным материалам относят: керамические (ГОСТ 530—80) и силикатные (ГОСТ 379—79) камни, бетонные камни, грунтобетонные блоки и саман. Последние два вида мелких блоков применяют в сельскохозяйственном строительстве. В качестве природных материалов используют камни правильной формы, выпиленные из известняка, ракушечника, туфа и др. (ГОСТ 4001—84).
Бутовая кладка — это кладка из природных камней неправильной формы, называемых бутовым камнем (ГОСТ 22132—76). Ее применяют главным образом для устройства фундаментов и стен подвалов.
Бутобетонная кладка состоит из бутового камня, втапливаемого в бетонную смесь, и применяют ее для тех же целей, что и бутовую.
Тесовую кладку выполняют из природных предварительно обработанных камней. Применяют ее для облицовки монументальных зданий и сооружений.
Каменную кладку создают поштучной укладкой камней на раствор, связывающий камни между собой. В результате благодаря выравниванию поверхностей соприкосновения обеспечивается более равномерная передача усилий на камни, а также предохраняется кладка от продувания и проникания воды. Вид и состав раствора зависят от назначения каменной кладки, условий ее работы и указываются проектом.
Цементные растворы, обладающие высокой прочностью, используют для кладки конструкций, несущих большие нагрузки, а также конструкций, расположенных в насыщенных водой грунтах.
Сложные растворы (цементно-известковые или цементно-глиняные) применяют при нормальных нагрузках на кладку в сухих и влажных местах.
Известковые растворы, имеющие невысокую прочность, но обладающие пластичностью, применяют только для кладки в сухих местах.
Глиняные растворы предназначены для кладки из самана наземной части стен одноэтажных сельскохозяйственных зданий и для печных работ.
Материалы для каменной кладки. Каменные и кирпичные работы — это наиболее распространенный вид кладки. Камень — это один из наиболее распространенных долговечных материалов. Впервые камень использовался в качестве защиты от природной стихии, а также от нападения животных. В каменных работах для строительства современного жилья используется два основных материала: каменный материал и раствор. Все каменные материалы подразделяются на две основные группы: Естественные (природные), которые можно найти в природе. Гранит — кристаллическая горная порода. В состав ее входят: кварц, слюда, полевой шпат, прекрасно обтесывается и полируется. Известняк — в его состав входят углекислый кальций и различные примеси. Также к естественным каменным материалам относятся: песчаник, туф, мрамор (рис. 29).
Рис. 29. Природные камни
Искусственные камни, получаемые искусственным путем, делятся на: обжиговые — кирпичные керамические блоки; безобжиговый — силикатный кирпич (из смеси извести и песка), мелкие блоки из шлака и пемзы (см. табл. 3).
Таблица 3. Размеры кирпича
Наименование
Марка
Размеры
Кирпич глиняный обыкновенный пластического прессования (ГОСТ 530-80)
300
250х120х65
250
200
150
125
100
75
Кирпич глиняный модульный
-
250х120х88
Кирпич керамический пустотелый пластического прессования (ГОСТ 530-90), одинарный
250
250х120х65
Кирпич керамический пустотелый пластического прессования (ГОСТ 530-90), утолщенный
100
250х120х88
Кирпич керамический пустотелый пластического прессования (ГОСТ 530-90), модульный
75
288х138х63
Камни керамические пустотелые пластического прессования (ГОСТ 530-80), камень
250
250х120х138
Камни керамические пустотелые пластического прессования (ГОСТ 530-80), камень модульных размеров
200
288х138х138
Камни керамические пустотелые пластического прессования (ГОСТ 530-80), камень укрупненный
150
250х250х138
Кирпич силикатный (ГОСТ 379-79), одинарный
250
250х120х65
200
150
Кирпич силикатный (ГОСТ 379-79), модульный
125
250х120х88
100
75
Наиболее распространенные искусственные камни — это кирпич глиняный обыкновенный, силикатный, легкий пустотелый и лицевой, камни — шлакобетонные, бетонные, ячеистые, керамические и др. По величине камни бывают крупными и малыми. Кирпич глиняный обыкновенный (рис. 30, а) — имеет красный цвет и формуется из глины, обжиг происходит при температуре 1000° С. Формование такого кирпича выполняется двумя способами — пластическим и полусухим. Кирпич глиняный обыкновенный используется для кладки внутренних и наружных стен, а также для фундаментной кладки зданий и кладки столбов. Силикатный кирпич (рис. 30, б), подобен по размеру глиняному обыкновенному, однако имеет светло-серый цвет, и не применим для возведения конструкций, подвергающихся частому увлажнению или сильному нагреванию — более 200°С. Силикатный кирпич применяют для возведения наружных стен, так как он обладает морозостойкостью. Кирпич глиняный пустотелый (рис. 30, в), имеет красный цвет, из-за своих теплотехнических свойств применяется для кладки наружных и внутренних стен. Наружные стены из этого кирпича выполняются тоньше, чем из обыкновенного глиняного. Лицевой кирпич (рис. 30, г), бывает профильный и рядовой. Лицевой кирпич укладывается вместе с основной кладкой, его применяют для облицовки как фасадов, так и внутренних стен в нежилых помещениях. Поверхность лицевого кирпича может быть рифленой, гладкой, офактуренной, а цветовая гамма — от кремового до темно-красного. Бетонные и шлакобетонные камни (рис. 30, д) — в состав смеси входят вяжущие материалы — это цемент, известь, вода; заполнители — щебень, песок, гравий, шлак. По заполнителям можно определить вид бетонного камня — тяжелый и легкий. Шлакобетонные камни производят как сплошными, так и пустотелыми. Стеклянные пустотелые блоки (рис. 30, е) выполняют с помощью сварки полублоков. Улучшение теплоизоляционных свойств блоков происходит благодаря созданию вакуума внутри блока, когда охлаждается горячий воздух. Форма блоков может быть различной: прямоугольной, угловой, радиальной, квадратной. Самыми распространенными являются квадратные блоки. Гипсовые и гипсобетонные блоки (рис. 30, ж), применяются в строительстве для перегородок и производятся полнотелыми и со сквозными пустотами.
Рис. 30. Искусственные камни
Инструменты, инвентарь и приспособления
Материалы, инструменты, приспособления, используемые для каменной и кирпичной кладки
При производстве кладки выполняется множество операций, и все они выполняются индивидуальным инструментом. Кельма (рис. 31, а) — главный инструмент каменщика. Лопатка, выполненная из стали с ручкой из дерева, предназначена для разравнивания раствора, качественного заполнения вертикальных швов и подрезки излишков раствора на швах. Вес кельмы составляет около 300 грамм. Ковш-лопата (рис. 31, б) применяется для подачи, для перелопачивания раствора и его расстилания. В некоторых случаях для расстилания раствора применяют специальный совок. Расшивки (рис. 31, в) используются для отделки швов кладки, ими придается различная форма. Расшиваются горизонтальные швы, только по линейке. Молоток-кирочка односторонняя (рис. 31, г), используется для тески и рубки кирпича. Двухсторонняя кирочка применяется для оформления кладки. Околку бутовых камней можно выполнять любыми молотками, даже кувалдой и специальными топориками.
Рис. 31. Инструменты для кирпичной кладки: а - комбинированная кельма; б - растворная лопатка; в - расшивки для выпуклых и вогнутых швов; г - молоток-кирочка; д - швабровка; е - пневматический отбойный молоток; ж - шлямбур; з – скарпель
Контрольно-измерительные инструменты для определения качества кладки: отвес, метр, угольник, уровень, правило. Набор инструмента каменщика см. табл. 4.
Таблица 4. Набор инструмента каменщика
Инструмент
Ед. изм.
Двойка
Тройка
Четверка
Пятерка
Кельма
шт.
2
2
4
4
Растворная лопата
шт.
1
2
2
3
Молоток-кирочка
шт.
2
2
2
3
Отвесы 400 и 600 г
комп.
1
1
2
2
Уровень
шт.
1
1
2
2
Расшивка
шт.
2
2
4
4
Метр складной
шт.
1
1
2
2
Правило
шт.
1
1
2
2
Деревянный угольник
шт.
1
1
2
2
Причальный крученый шнур
м
30
45
60
60
Рулетка
1
1
1
1
Отвес, или весок (рис. 32, а) — для проверки вертикальности кладки. Масса отвеса 200—400 г, с его помощью провешивают кладку внутренних стен, столбов в пределах этажа, а более тяжелым весом — от 600 до 1000 г — проверяют наружные углы и конструкции. Метр, или рулетка (рис. 32, б, в) — ими проверяются все размеры, необходимые при выполнении кладки, и производят разбивку. Для измерения больших расстояний используют рулетки следующих размеров 1, 2, 5, 10, 15м. Угольник (рис. 32, г) — с его помощью проверяют правильность закладки углов. Правило (рис. 32, д) используется для определения прямолинейности на наружной стороне кладки. Правило — это идеально выровненная деревянная рейка длиной 1,5 м.
Рис. 32. Контрольно-измерительные инструменты для каменной кладки: а - отвес; б - складной метр; в - рулетка; г - угольник; д - деревянное правило
Использование в полном объеме инструмента каменщика значительно повышает качество его работы и сокращает срок ее исполнения. Швабровку используют для чистки вентиляционных каналов от выступившего из швов раствора или для полного заполнения швов раствором (рис. 31, д). Уровень (рис. 33, а) применяется для проверки горизонтальности кладки, бывает деревянным и металлическим. В уровне находится незамерзающая жидкость, и по положению пузырька проверяются горизонтальные и вертикальные плоскости. Длина уровня около 50 см. При работе с таким уровнем необходимо установить его на брусок, длина которого составляет 1—1,5 м. В советские времена набор инструментов с самыми необходимыми для каменщика приспособлениями выпускался в специальной сумке (рис. 33, б). )
Рис. 33. Приспособления для возведения каменной кладки: а - уровень; б - сумка каменщика; в - порядовка и крепление порядовки к кладке (1 - рейка; 2 - держатель; 3 - клин); г - поддон для кирпича
Каменная кладка — дело не простое, поэтому чтобы сохранить постоянную толщину, правильность кладки по рядам, выдержать точное направление требуется ряд приспособлений: шнур-причалка, порядовка и многое другое. Порядовка — это обычная рейка длиной 3 м (рис. 33, в). На порядовке стоят метки через каждые 77 см (почему именно 77-см — сюда входит высота кирпичного ряда 65 мм и толщина горизонтального шва раствора 12 мм). Кроме деревянных реек-порядовок, применяются и металлические порядовки. Причалка натягивается между порядовками и отстоит от стены с учетом подкладки под нее кирпича (рис. 34, а). Причалка выполняется из крученого шнура толщиной 3 мм и назначение ее обеспечить прямолинейность рядов кладки. Иногда возникает необходимость разборки каменных стен, пробивки борозд под требуемые коммуникации. Для этих целей используют пневматические отбойные молотки, скарпели, шлямбуры, пробойники с наконечниками из твердых металлов (рис. 31, е, ж, з).
Рис. 34. Установка причалки: а - переустановка скобы со шнуром; б - причальная скоба
При выполнении кладки арок, столбов, сводов используют шаблоны (рис. 35). Для подачи раствора на рабочее место каменщика удобнее пользоваться тачками, можно ящиками, которые бывают как деревянными, так и металлическими. Подавать кирпичи можно на небольшом поддоне (рис. 33, г).
Рис. 35. Шаблон для кладки арок, сводов: 1 - шнур; 2 - шаблон-угольник; 3 – клинья.
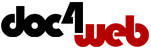
Нравится материал? Поддержи автора!
Ещё документы из категории строительство :
Чтобы скачать документ, порекомендуйте, пожалуйста, его своим друзьям в любой соц. сети.
После чего кнопка «СКАЧАТЬ» станет доступной!
Кнопочки находятся чуть ниже. Спасибо!
Кнопки:
Скачать документ