Завод по изготовления ригелей
1 Технико-экономическое обоснование проекта.
1.1 Оценка состояния отрасли и предприятия как объекта инвестирования.
1.1.1 Характеристика отрасли.
Развитие отрасли промышленного строительства в недостаточной мере отвечает как количеству, так и качеству железобетонных изделий, выпускаемых в настоящее время. Производство сборного железобетона для промышленного строительства необходимо поднимать на новый, более высокий качественный уровень - переход к высокоэффективным технологиям, технологиям XXI века, к использованию качественного материала, применению комплекса химических добавок.
Для работы нового завода имеется сырьевая база: песок доставляться будет с местного карьера, щебень - с Павловского карьера, цемент со Старооскольского цементного завода.
На данный момент в г. Воронеж действует только один завод ЖБК, который выпускает продукцию для промышленного строительства. Уровень качества продукции - средний, при стоимости 4241 - 5557 р/м .
Необходимость строительства нового завода обосновывается дефицитом строительных изделий. Проектируемый завод будет выпускать 40 тыс. м3 железобетонных изделий в год, при этом предполагается, что реализация продукта будет 100 %.
1.1.2 Общая характеристика выпускаемой продукции
Ригели выполняют из стали класса Ат-V ø 10…25 мм, А-I, А-II, А-III ø 10…40, Вр-I ø 3 мм.
Арматурная сталь принята в соответствии с ГОСТ I30I5.0-83 . Для плоских каркасов, сеток и отдельных стержней принята сталь класса А-II, А-III по ГОСТ 5781-82, класса Вр-I по ГОСТ 6727-00, для подъемных (строповочных) петель, анкерных петель принята сталь класса А-I по ГОСТ 5731-82 * марки ВСт Зпс2 ГОСТ 380-71* ,для закладных деталей принята сталь по ГОСТ 103-76*марки ВСт Зкп.2 по ГОСТ 38С-"71*.
Диаметры подъемных (строповочных) петель приняты в соответствия с «Руководством по проектированию бетонных и железобетонных конструкций из тяжелого бетона (без предварительного натяжения)» M.I978 г.
Арматурные стали должны обладать достаточной пластичностью, что важно по условиям работы конструкций под нагрузкой, а также при заготовке арматуры. Арматурная сталь не должна снижать механических свойств при сварке.
1.1.3 Источники материальных, энергетических и трудовых ресурсов.
Для строительства завода выбран один из районных центров Воронежской области город Острогожск. Это обусловлено наличием близко расположенных источников материальных ресурсов и наличием трудовых ресурсов, а также хорошо развитой сетью автомобильных дорог и железнодорожной станции.
Доставка мелкого заполнителя – песка может осуществляться с любого из трех расположенных по близости песчаных месторождений: Лискинского (30 км.), Коротоянского (15 км.), Петропавловского (17 км.).
Крупный заполнитель – гранитный щебень доставляется из Павловска железнодорожным транспортом на станцию Острогожск, а оттуда по отдельной железнодорожной ветке на предприятие, которое будет расположено на правом берегу реки Тихая Сосна в промышленной зоне города.
Цемент поставляется на завод со Старооскольского цементного завода железнодорожным транспортом аналогично крупному заполнителю.
Пар на тепловую обработку изделий поступает от собственной котельной, расположенной на территории предприятия.
Вода на предприятие поступает из собственной скважины. Химические добавки привозятся на предприятие с Россошанского химического комбината автомобильным транспортом. Эмульсон поставляется на завод острогоржской нефтебазой.
Поставщиком электроэнергии на предприятие является МУП «Острогожскэлектросеть».
Источником трудовых ресурсов являются Воронежский Государственный Архитектурно-Строительный Университет и ПТУ-19 города Острогожск.
1.1.4 Определение потенциальных потребителей продукции, мощности и места размещения проектируемого предприятия.
Основными потребителями выпускаемой продукции завода ЖБК являются строительные фирмы, строительные организации, занимающиеся строительством промышленных одноэтажных зданий.
Продукция будет реализовываться посредством оптовой торговли за безналичный расчет. Предполагаются только прямые поставки.
Место строительства проектируемого завода должно удовлетворять следующим основным требованиям:
- завод должен находиться как можно ближе к поставщику сырьевых
материалов (чтобы расход на доставку был минимальным).
наличие подъездных путей, а также энергетических ресурсов.
наличие трудовых ресурсов.
Оптимальным местом строительства нового завода является территория на Воронежской области, г Острогоржск. Выполняются все требования по размещению завода - имеются в наличии подъездные железнодорожные пути и большая сеть автодорог.
Предполагается, что поставки сырьевых материалов и сбыт готовой продукции будет осуществляться в полной мере.
Мощность проектируемого предприятия 40000 м3.
2 Технологические решения.
2.1 Выбор и обоснование способа и технологии производства продукции.
2.1.1 Выбор способа организации производства.
Проектируя ж/б элементы, предусматривают возможность высокопроизводительного труда при их изготовлении на специальных заводах монтажа на строительных площадках путем выбора оптимальных габаритов, экономичных форм сечения, рациональных способов армирования. Конструктивные решение элементов и технология заводского изготовления находятся в тесной взаимосвязи. Элементы, конструкция которых допускает их массовое изготовление на заводе или полигоне с использованием высокопроизводительных машин и механизмов без трудоемких ручных работ, является технологичными. Производство сборных ж/б элементов ведут по нескольким технологическим схемам. Существует несколько видов технологий :
Конвейерная технология .
Элементы изготавливают в формах, установленных на вагонетках и перемещаемых по рельсам конвейера от одного агрегата к другому. По мере продвижения вагонетки последовательно выполняют необходимые технологические операции : установку арматурных каркасов, натяжение арматуры предварительно напряженных элементов, установку вкладышей – пустотообразователей для элементов с пустотами, укладку бетонной смеси и ее уплотнение, извлечение вкладышей, термовлажностную обработку изделия для ускорения процесса твердения. Все формы вагонетки перемещаются в установленном ритме. Высокопроизводительную конвейерную технологию применяют на крупных заводах при массовом выпуске элементов относительно малой массы.
Поточно-агрегатная технология.
Технологические операции выполняются в соответствующих цехах завода. При этом агрегаты, выполняющие необходимые технологические операции, неподвижны, а форма с изделием перемещается от одного агрегата к другому краном. Технологический ритм перемещения заранее не установлен и не является принудительным.
Стендовая технология.
Ее особенность состоит в том, что изделия в процессе изготовления и тепловой обработки остаются неподвижными, а агрегаты, выполняющие операции, перемещаются вдоль форм.
Такие стенды оборудованы передвижными кранами, подвижными бетоноукладчиками, а также вибраторами для уплотнения бетонной смеси. Элементы изготавливают в гладких или профилированных формах. По стендовой технологии изготовляют крупноразмерные и предварительно напряженные элементы промышленных зданий.
Вибропрокатная технология.
Плиты перекрытия и панели формуют на движущейся ленте, гладкая или рифленая поверхность которой образует форму изделия. После укладки арматурного каркаса бетонную смесь, поданную на ленту, вибрируют и уплотняют с помощью расположенных сверху валков. Последовательно прокатанные изделия, укрытые сверху и подогреваемые снизу, за время перемещения по ленте набирают необходимую прочность и после охлаждения на стеллажах транспортируются на склад готовой продукции. Технологические операции подчинены одному ритму – скорости движения формующей ленты.
С учетом видов выпускаемой продукции и объемов производства рационально будет выбрать агрегатно-поточный способ организации производства.
2.1.2 Характеристика сырья и полуфабрикатов, обоснование технологии подготовки и складирования.
Вяжущее.
В качестве вяжущих веществ для производства бетонных и железобетонных изделий из цементных тяжелых бетонов применяется портландцемент марки 400.
Применение цементов марки 400 для бетонов разных класов допустимо при применении технологических мероприятий (введение суперпластификаторов, воздухововлекающих добавок), что позволяет достичь требуемого класса без значительного (более 10 %) увеличения расхода цемента.
Крупный заполнитель.
В качестве крупных заполнителей применяется щебень из изверженных метаморфических и осадочных пород по ГОСТ 8267 - 93. Щебень не будет содержать дробленые зерна в количестве более 80 % по массе.
Наибольшая крупность заполнителя используемого для изготовления всех железобетонных изделий будет не более 20 мм. Заполнители будут складироваться и дозироваться вместе обе фракции. Зерновой состав крупных заполнителей регламентируется ГОСТ 10268-93
Содержание пылевидных и глинистых частиц в щебне из изверженных и метаморфических пород не будет превышать 1 % по массе. Содержание зерен пластинчатой (лещадной) и игловатой формы в крупном заполнителе не будет превышать 35 % по массе. Морозостойкость крупных заполнителей должна быть не ниже нормируемой марки бетона по морозостойкости.
Содержание в щебне слабых и выветренных пород не будет превышать 10 %. Разрешается применять щебень из карбонатных пород марки 400, если содержание в нем зерен слабых пород менее 5 %/(к слабым породам относятся породы с прочностью при сжатии в водонасыщенном состоянии менее 20 МПа).
Мелкий заполнитель.
В качестве мелкого заполнителя используется песок (ГОСТ 8736-93), применяемый для тяжелого бетона. В качестве такового используются природные пески (в естественном состоянии). Допускается использование смеси песков природного и из отсеков дробления.
Использование в качестве мелких заполнителей смеси песка из отсевов дробления с природным мелким песком допускается при условии обеспечения заданной удобоукладываемости бетонной смеси без перерасхода цемента.
Вода.
Вода, используемая для приготовления бетонных смесей, будет соответствовать требованиям ГОСТ 23732-79. Для затворения бетонной смеси могут быть использованы природные воды (питьевая), не содержащие солей кислот и органических примесей выше допустимых норм, а также не загрязненные сточными, бытовыми и промышленными водами и маслами. При приготовлении бетонных изделий в соответствии с ГОСТ 23732-79 считается непригодной вода, в которой общее содержание солей выше 5000 мг/л или сульфатов (сернокислый кальций, натрий, магний) в расчете на ион SO4 свыше 2700 мг/л, а также при водородном показателе рН < 4, что свидетельствует о кислотном характере воды.
Окисляемость воды не будет более 15 мг/л. Водородный показатель воды (рН) не будет менее 4.
Вода не будет содержать также примесей в количествах, нарушающих сроки схватывания и твердения цементного теста и бетона, снижающих прочность и морозостойкость бетона.
На заводе будет применяться суперпластификатор С-3 (ТУ 6-14-625-80) на основе натриевых солей продукта конденсации нафталинсульфокислоты и формальдегида. Жидкость темно-коричневого цвета, плотность 1,15 - 1,20 г/см2 или не слеживающийся темно-коричневый порошок, легко растворимый в воде. Выпускается в виде водного раствора 40% концентрации и не имеет ограничений в области применения для различных бетонов. Водные растворы С-3 не изменяют своих свойств при нагревании до 85 °С и замораживании до - 40 °С.
Используемая арматурная сталь в производстве ж/б изделий поступает ж/д транспортом непосредственно на склад. Разгружается с помощью мостового крана. Складирование производится по видам и маркам. Склад для хранения арматурной стали размещается в составе арматурного цеха. Сталь со склада на дальнейшую переработку поступает на специализированных вывозных тележках.
2.1.4 Обоснование технологии приготовления формовочных смесей.
Приготовление бетонной смеси осуществляется в бетоносмесительной установке и состоит из операций загрузки расходных бункеров, дозирования, перемешивания сырьевых компонентов и выдачи бетонной готовой смеси на транспортные средства.
В зависимости от вертикальной компоновки различают бетоносмесительные цехи с одноступенчатой (вертикальной) схемой, когда производится однократный подъём компонентов смеси в расходные бункера и гравитационное их перемещение технологической линии, и с двухступенчатой (партерной) схемой -двукратный подъём материалов. Эффективнее одноступенчатая схема, позволяющая сократить число операций транспортировки. В данном проекте принята одноступенчатая схема.
Дозирование компонентов бетонной смеси осуществляется по массе. Точность дозирования соответствует требованиям нормативных документов. Для дозирования сырьевых компонентов используются автоматические весовые дозаторы. Для приготовления малоподвижных бетонных смесей применяются бетоносмесители принудительного перемешивания. В этих смесителях компоненты перемешиваются в чаше или барабане принудительно, под воздействием вращающихся лопастей частицы многократно перемещаются по сложным траекториям. Так же при перемешивании целесообразно использовать явление вибрации с целью тиксотропного разжижения густого цементного теста, уменьшая таким образом предельное сопротивление сдвигу и внутреннее трение при перемешивании компонентов смеси. При этом вода и цементное тесто более равномерно распределяется в объёме смеси, достигается более высокая однородность, происходит активация цемента, что приводит к дополнительному повышению прочности бетона, ускоряет процесс его твердения в раннем возрасте.
2.1.5.1. Технология подготовки форм.
Формование изделий происходит в металлических формах, они обладают большой жесткостью, чтобы не деформировались при транспортировании. Применяются унифицированные формы с откидными бортами.
После распалубки изделия на форме остаются мельчайшие остатки бетона, смазочного материала, что значительно ухудшает качество изделий. Поэтому форму подвергают тщательной очистке после каждого цикла формования. Очистка может быть как механической, так и ручной. Применим ручной способ очистки рабочими с помощью скребков. Химическую очистку поддонов необходимо применять не более 2 раз в год.
На качество железобетонных изделий существенно влияет сцепление бетона с поверхностью форм. Одним из способов уменьшения сцепления является применение различных смазок. Правильно подобранная и хорошо нанесенная смазка обеспечивает легкое освобождение изделия из формы.
Наиболее широкое распространение получили смазки типа эмульсия. Она имеет повышенную адгезию к металлу и поэтому хорошо удерживается на металлической поверхности формы.
Смазка форм осуществляется с помощью пульверизатора, что обеспечивает равномерное нанесение смазки, тщательное смазывание углов и ребер.
2.1.5.2.Технология армирования изделий.
Ригель армируется предварительно напряженной и не напряженной арматурой.
Сборка арматурного каркаса ригеля происходит в следующей последовательности: устанавливаются закладные детали , укладывается U-образная сетка . После этого на упоры формы закрепляется напрягаемая арматура, укладываются конструктивные сетки и устанавливаются каркасы. Сверху укладывается сетка .
2.1.5.3. Технология формования изделий.
На посту формования подготовленная форма устанавливается на виброплощадку. Бетоноукладчиком бетонная смесь подвижностью подается в форму. После этого форма крепится к виброплощадке электромагнитом и уплотняется бетонная смесь с амплитудой колебаний 0,2 - 0,5 мм. Одновременно с этим вручную заглаживаются неровности, и при необходимости добавляется бетонная смесь. Уплотнение бетонной смеси происходит в течении 3 мин.
2.2.5.4. Технология распалубки готовых изделий.
Изделия в форме прошедшие ТВО поступают на пост подготовки, где последовательно производят открытие продольных бортов. Очищают от затвердевшего бетона концы напрягаемой арматуры и механическим станком с вращающимся диском их обрезают таким образом, чтобы концы арматуры не выступали за пределы плиты более 10 мм. Оголенные концы арматуры покрываются битумным лаком. Далее мостовым краном перемещают готовое изделие на пост промежуточного складирования, затем на склад готовой продукции.
2.1.6. Обоснование способов и режимов тепловой обработки, расходов тепловой энергии.
Выбор рациональных способов и режимов тепловой обработки основывается на полной увязке технологических и теплотехнических факторов.
Вид и режим тепловой обработки следует выбирать с учетом влияния вяжущего. Для бетонов на высокоактивных вяжущих М400 рекомендуется паропрогрев при температуре 68 - 85 °С и относительной влажностью среды 80 - 100 %. Жесткие бетонные смеси по сравнению с подвижными обеспечивают сокращение сроков теплового воздействия.
На продолжительность тепловой обработки влияет также массивность изделий: с её увеличением растет температурный перепад, вероятность возникновения температурных деформаций.
Цикл тепловой обработки состоит из трех основных стадий: подъема температуры среды, изотермического выдерживания при постоянной температуре и охлаждения изделий.
Скорость прогрева зависит от начальной прочности бетона, пластичности бетонной смеси, модуля открытой поверхности. На основании многочисленных исследований оптимальной скоростью подъема температуры при прогреве изделий с умеренной жесткостью и толщиной до 20 мм составляет 30 °С/ч. Прогрев при максимальной температуре должен составлять не менее 4 ч. Скорость снижения температуры в пределах 25 - 50 °С/ч не должна приводить к перепаду температур поверхности изделия и окружающей среды.
Для бетона используемого для изготовления железобетонных изделий в курсовом проекте принимаем режим тепловой обработки 9,5 часов.
Способы тепловой обработки:
Прогрев бетона при атмосферном давлении - основной способ ускорения твердения изделий на заводах сборного железобетона.
Ямные камеры используются для поточно-агрегатного способа производства. Они просты в изготовлении, имеют большое распространение. Недостатки: большая продолжительность обработки, завышенные удельные расходы тепла.
Стендовая технология тепловой обработки для изготовления крупноразмерных изделий не позволяет применять передвижные формы, поэтому тепловая обработка происходит в самой форме.
Щелевые камеры тепловой обработки применяются при конвейерном способе производства. Значительно механизирована и автоматизирована, на трудна в переналадке на новую номенклатуру изделий.
Из всех способов наиболее оптимальна тепловая обработка в ямной камере изделий изготовляемых агрегатно-поточным способом.
2.1.7. Обоснование технологии складирования готовой продукции.
Склад готовой продукции проектируемого завода предназначен для хранения прошедших контроль изделий до отгрузки их потребителю. Компоновка склада тесно увязывается с главными производственными корпусами завода.
Изделия на складе хранят в штабелях или стеллажах, в каждом из которых находятся изделия одного типоразмера или марки. Каждое изделие при хранении должно опираться на деревянные подкладки и прокладки. Нижний ряд изделий укладывается на подкладки. Укладка одних изделий на другие без прокладок не допускается. Подкладки и прокладки должны быть одинаковой длинны, следует располагать их по вертикали строго одну под другой. Особое внимание должно быть уделено устойчивому и правильному положению подкладок под нижним рядом штабеля, которые располагают на выровненном и очищенном основании.
Склад готовой продукции представляет собой открытую прямоугольную площадку, оборудованную подъемно-транспортными оборудованием и механизмами. Складская площадка должна иметь бетонное основание, водоотводные канавы и кюветы для стока воды.
Для выполнения погрузочно-разгрузочных работ применяют мостовые краны, обладающие высокой маневренностью и удобными в управлении.
Вместимость склада готовой продукции определяют по формуле:
V= q*n, где
q - суточное поступление изделий на склад;
n - нормативный срок хранения изделий.
V= 172,48*10 = 1724,8 м3
Площадь склада, необходимую для складирования изделий, вычисляют по формуле:
S,=V/nb
где nb — норма хранения изделий на 1 м2 площади, принимается равной 1,8 м /м для хранения изделий в горизонтальном положении.
S1= 1724,8 /1,8 =958,22 м2
Площадь склада с учетом условий его обслуживания, составляет:
S2= S1*k1*k2,
где kj - коэффициент, учитывающий проходы на складах;
к2 - коэффициент учитывающий увеличение площади в зависимости от типа склада.
S2 = 958,22* 1,5 * 1,3 =1868,53 м2
На основании расчетов принимаем следующие параметры склада: число пролетов - 1; длина 108 м; ширина 18 м; площадь 1944 м2.
2.2. Режим работы и производственные программы предприятия.
Режим работы предприятия назначается в соответствии с нормами технологического проектирования ОНТП 07-85 исходя из способа производства.
Таблица 7 – Режим работы предприятия.
Наименование
подразделений
Показатели
Количество
рабочих дней в году
Количество рабочих смен в сутки
Продол-
житель-
ность смены, ч рабочего времени
Годовой фонд рабочего времени F, ч
номи
наль-
ное
расчет-
ное
номи-
наль-ный
расчет-
ный
Смесительный
цех
253
246
2
8
4048
3936
По приему сырья и
материалов
365
350
3
8
8760
8400
По выдаче сырья в производство
253
246
2
8
4048
3936
Арматурный цех
253
246
2
8
4048
3936
Формовочный цех
253
246
2
8
4048
3936
Тепловая обработка
365
350
3
8
8760
8400
Складирование и отправка готовой продукци
253
246
2
8
4048
3936
Таблица 9 – Производственная программа по сырью и материалам.
Наименование материалов
Ед. измерения
Потребность
Годовая
Суточная
Часовая
Ригели
Цемент
Т
7456,36
30,31
1,89
Песок
М3
10485,5
42,62
2,66
Щебень
М3
20971,01
85,25
5,33
Вода
М3
4660,22
18,94
1,18
Добавка С-3
Л
37281,79
151,55
9,47
Арматура
Т
1758,61
7,15
0,45
Таблица 10 - Расчетные вместимости складов.
Наименование склада
Ед. изм.
Суточный объем хранения
Норма запаса, сутки
Общий запас
Коэффициент использования
Вместимость склада
Склад заполнителей
м3
232,84
7
1629,88
0,76
2144,58
Склад цемента
т
54,52
7
381,64
0,82
465,41
Склад химических добавок
м3
0,26
60
15,6
0,57
27,37
Склад арматурной стали,
м3
23,41
20
468,2
0,98
477,76
Склад смазочных материалов
м3
0,006
60
0,36
0,006
60
Таблица 11 - Технико-экономические характеристики складов предприятия.
Наименование
показателей
Склад
цемента
заполнителей
арматурной
стали
химической
добавкиС-3
смазочных
материалов
Шифр типового проекта
409-29-63
708-13.84
-
-
70999-5
Способ доставки грузов
ж/д
ж/д и авто.
ж/д
авто
ж/д
Вместимость
720 т
3000 м3
120 т
20 т
100 м3
Годовой грузооборот
35,7 тыс.т
100 тыс.м3
1200 т
150 т
Установленная мощность электродвигателей, кВт
212
300
37
25
22
Расход сжатого воздуха, м3/год
2370
33
-
-
-
Расход пара, т/год
200
2000
-
900
1300
Численность рабочих по приёмке грузов
3
3
4
2
1
Численность рабочих по обслуживанию технологического процесса
3
3
2
2
1
Сметная стоимость млн.р. в т.ч. зданий и сооружений
оборудовония
2,368
0,943
14,985
5,125
0,360
0,38
0,637
0,120
0,844
0,152
2.3. Организация производства, определение численности рабочих (на производстве ребристых плит покрытия 1ПГ12).
Разработка пооперационной схемы технологического процесса.
Очистка формы Доставка арматурных
изделий к посту
Смазка формы
Укладка и закрепление закладных деталей Электронагрев стержней
Укладка и закрепление ненапрягаемой
арматуры
Укладка электронагретых стержней
на упоры формы
Сборка формы Доставка и загрузка бетонной
смеси бетоукладчиком к посту
Укладка и закрепление
ненапрягаемой арматуры
Укладка, закрепление монтажных петель
Укладка бетонной смеси
Уплотнение бетонной смеси
Комплектование пакета форм с изделиями для ямной камеры
Закрывание ямной камеры крышкой и ТВО
Открывание ямной камеры
Выгрузка пакетов форм
Распалубка
Механическая обрезка преднапреженных
стержней обрезным станком с вращающимся
диском
Маркировка изделий Отправка изделий на склад
Таблица 12 – Нормы времени при изготовлении ригеля агрегатно-потчным способом производства
Наименование операций
Норма времени на операцию, чел.-мин.
Очистка формы пневмоскребком
16,3
Смазка формы
6,66
Укладка арматуры в формы
11,5
Электронагрев стержней и укладка их в форму
24,8
Сборка формы
7,5
Установка и закрепление монтажных петель
3,0
Выемка фиксаторов
0,52
Установка закладных деталей
0,65
Доставка и загрузка бетонной смеси бетоукладчиком к посту
3,7
Установка форм на вибростол
1,3
Укладка бетонной смеси
6,8
Уплотнение и разравнивание бетонной смеси
20,3
Загрузка форм с изделиями в ямную камеру
2,1
Открывание и закрывание ямной камеры
2,88
Выгрузка форм
2,1
Распалубка
11,3
Установка формы с изделием на пост распалубки
1,8
Механическая обрезка преднапреженных
стержней обрезным станком с вращающимся диском
8,2
Итого
131,41
Определение ритма работы предприятия.
rрасч п=60*Fрасч д/Nвып,
где Fрасч д – расчетный годовой фонд времени работы предприятия,ч
Nвып – годовой выпуск изделий на предприятии, шт.
rрасч п=60*3936/7872=30мин.
Предполагается, что в форме одно изделие, необходимо выбрать такой ритм, который был бы кратен длительности смены и который бы не превышал расчетный ритм. Уточним ритм:
Nсмрасч=480/ rрасч п,
где 480 – длительность смены при 8 часах рабочего времени, мин.
Nсмрасч=480/30=16
Принятый ритм определяем по формуле
rприн п =480/ Nсмприн,
rприн п =480/16=30 мин.
Число рабочих определяют по формуле
N=Т/ rприн п,
где Т – сумма норм времени, мин
N=131,41/30=4,38
Принимаем количество рабочих 5 человека.
Рациональная расстановка рабочих по постам обеспечивает синхронность работы этих постов, то есть устойчивую и равномерную загрузку как оборудования, так и рабочих. Результаты синхронизации представлены в виде таблицы на отдельном листе
Работа мостового крана
0-1 Подготовка крана к работе 1,5
1-2 Опускание, строповка и подъем арматуры 1,3
2-3 Перемещение арматуры на промежуточное складирование 0,17
3-4 Опускание и растроповка арматуры 1,1
4-5 Строповка и подъем арматурной сетки 0,5
5-6 Перемещение крана к форме №6 0,81
6-7 Опускание и растроповка сетки 1,1
7-8 Перемещение крана к ЯК 0,28
8-9 Опускание и строповка крышки ЯК 0,7
9-10 Перемещение крышки ЯК 0,1
10-11 Опускание и растроповка крышки ЯК 0,7
11-12 Перемещение крана к форме №6 0,28
12-13 Строповка и подъем формы №6 1,1
13-14 Перемещение формы 6 к вибростолу 0,79
14-15 Опускание и растроповка формы 6, подъем крюка 1,1
15-16 Строповка и подъем формы №6 1,1
16-17 Перемещение формы №6 к ЯК 1,06
17-18 Опускание и растроповка формы 6, подъем крюка 1,1
18-19 Перемещение крана к ЯК 0,1
19-20 Опускание и строповка крышки ЯК 0,7
20-21 Перемещение крышки ЯК 0,1
21-22 Опускание и растроповка крышки ЯК 0,7
22-23 Опускание, строповка и подъем крышки ЯК 0,7
23-24 Перемещение крышки ЯК 0,1
24-25 Опускание и растроповка крышки ЯК, подъем крюка 0,7
25-26 Перемещение крюка к ЯК 0,1
26-27 Опускание, строповка и подъем формы 1,1
27-28 Перемещение формы №6 на пост распалубки 0,28
28-29 Перемещение крюка к крышке ЯК 0,28
29-30 Опускание и строповка крышки ЯК 0,7
30-31 Перемещение крышки ЯК 0,1
31-32 Опускание и растроповка крышки ЯК, подъем крюка 0,7
32-33 Перемещение крана к форме №6 0,28
33-34 Опускание, строповка и подъем готового изделия 1,1
34-35 Перемещение изделия на промежуточное складирование 0,67
35-36 Опускание и растроповка изделия 1,1
36-37 Строповка и подъем готового изделия 1,1
37-38 Перемещение готового изделия на самоходную тележку 0,13
38-39 Опускание и растроповка изделия 1,1
39-40 Возвращение на начальное место положения 1,58
Итого 28,21
Определение численности рабочих.
Таблица 14 – Явочный состав рабочих.
Наименование рабочих профессий
Тарифный разряд рабочих
Количество рабочих в смену
Количество смен в сутки
Количество рабочих в сутки
Количество рабочих смен в году
Годовой фонд времени рабочих, чел·ч
1
2
3
4
5
6
7
1. Основные рабочие
1. Бетоносмесительный цех
дозировщик
моторист
III
III
1
2
2
2
2
4
253
253
8096
16192
2. Арматурный цех
крановщик
арматурщик по заготовке арматурных петель
электросварщик на одноточечной машине
арматурщик на прессножницах
арматурщик на клещах
арматурщик по высадке анкерных головок
IV
III
IV
III
III
III
1
1
3
2
4
2
2
2
2
2
2
2
2
2
6
4
8
4
253
253
253
253
253
253
8096
8096
24288
16192
32384
16192
3. Формовочный цех
формовщик
крановщик
стропальщик
IV
III
III
10
2
2
2
2
2
20
4
4
253
253
253
80960
16192
16192
4.Склад готовой продукции
крановщик
стропальщик
IV
III
2
4
3
2
6
8
365
365
52560
70080
5. Склад цемента
- моторист
III
2
3
6
365
52560
6. Склад заполнителей
- моторист
III
2
3
6
365
52560
Итого основных рабочих
86
454448
2. Вспомогательные рабочие
1. Бетоносмесительный и арматурный цеха
слесарь-ремонтник
электрик
IV
IV
1
1
2
2
2
2
253
253
8096
8096
Таблица 15 – Продолжение.
1
2
3
4
5
6
7
2. Формовочный цех
слесарь по ремонту форм
механик-электрик
IV
IV
1
1
2
2
2
2
253
253
8096
8096
3. Материально технический склад
II
2
2
4
253
16192
4. Охрана
4
3
12
365
105120
5. Компрессорная
II
1
3
3
365
26280
6. Склад ГСМ
III
1
2
2
253
8096
7. Вахтёры
1
3
3
365
26280
Итого вспомогательные рабочие
32
214352
Всего
120
266644
Органы управления предприятием
Таблица 16.– Численность административно управленческого персонала.
Наименование штатных должностей
Категория работающих
Количество штатных единиц
Директор
Главный инженер
Секретарь
Главный энергетик
Главный механик
Инженеры отдела
Бухгалтеры
Главный бухгалтер
Инженеры ППО
Начальник ППО
Главный технолог
Начальник отдела сбыта и снабжения
Сотрудники отдела сбыта
Начальник ОТК
Инженер ОТК
Контролёры ОТК
Отдел кадров*
Инженер по ТБ
ИТР
ИТР
Служащие
ИТР
ИТР
ИТР
Служащие
Служащие
ИТР
ИТР
ИТР
ИТР
Служащие
ИТР
ИТР
Служащие
Служащие
ИТР
1
1
2
1
1
1
3
1
3
1
1
1
2
1
1
2
1
1
Итого
26
Таблица 17.– Численность цехового персонала.
Наименование штатных должностей
Категория работающих
Количество штатных единиц
Начальник формовочного цеха
ИТР
1
Мастер формовочного цеха
ИТР
3
Начальник БСЦ
ИТР
1
Мастер БСЦ
ИТР
1
Начальник РМЦ
ИТР
1
Мастер РМЦ
ИТР
1
Начальник лаборатории
ИТР
1
Лаборант
Служащий
2
Итого:
11
Явочную численность рабочих переведём в списочную с учётом коэффициента перехода, рассчитываемого по формуле:
где N – количество рабочих дней в году;
n1 – количество выходных и праздничных дней в году;
n2 – количество отпускных дней в году;
n3 – прочие невыходы на работу.
Количество основных рабочих, работающих 365 дней:
Р=181,706=31чел.
Количество основных рабочих, работающих 253 суток:
Р=681,18=81 чел.
Количество вспомогательных рабочих, работающих 365 дней:
Р=181,706=31 чел.
Количество вспомогательных рабочих, работающих 253 суток:
Р=161,18=19 чел.
Общий списочный состав – 199 человек.
2.4. Выбор и расчёт технологического оборудования.
Расчёты оборудования выполняются в соответствии с технологическим обоснованием и решениями по организации производства.
Расчёт необходимого количества оборудования каждого вида выполняют по единой схеме как отношение расчётной потребности производительности данного вида оборудования к паспортной производительности единицы принятого оборудования с учётом понижающих коэффициентов на неполное использование мощности и рабочего времени.
Окончательно выбор технологического оборудования представлен в виде таблицы .
Таблица 18 – Спецификация оборудования завода ЖБК.
Наименование оборудования
Тип или марка
Краткая техническая характеристика
Количе-ство еди-ниц обо-рудова-ния, шт.
Стоимость, тыс. руб.
Габаритные размеры, мм
Масса, кг
Установлен-ная мощ-ность, кВт
Еди-ницы
Всего
1
2
3
4
5
6
7
8
Бетоноукладчик
СМЖ-69А
3175 х 4000 х 2785
12000
22,2
2
360
720
Виброплощадка f=50 Гц
К-494
12800 х 3400 х 1450
7900
53,5
2
558
1116
Тележка самоходная
СМЖ-151
7490 х 2573 х 1450
3700
7,5
4
111
444
Прицеп тележки
СМЖ-154
7800 х 2500 х 800
2700
—
4
81
324
Бетонораздаточный бункер
СМЖ-2А
1600 х 2080 х 1497
2000
8
2
60
120
Кран мостовой гр. 10т
—
6800 х 16000 х 2500
30000
75
3
900
2700
Насосная станция
НСП-400
900 х 500 х 2000
305
2,2
1
9,15
9,15
2.5. Расчёт общего расхода электроэнергии.
Установленная мощность оборудования основных производственных цехов принимается на основании показателей, принятых в спецификации оборудования (таблица 19). Установленную мощность оборудования вспомогательных подразделений завода (ремонтно-механического цеха, компрессорной и т.д.) можно принимать условно как 5-10 % от мощности оборудования основного производства.
Расчётной нагрузкой называют произведение установленной мощности на коэффициенты, учитывающие КПД токоприёмников, потери в сети, долю использования оборудования во времени и по мощности, которые отличаются для различных групп оборудования.
При выполнении курсового проекта расчётная нагрузка не указывается, а расход электроэнергии на технологические цели (Эт) рассчитывается по упрощённой формуле:
Эт = Р·Fдрасч·к,
где Р – установленная мощность электродвигателей проектируемого предприятия, кВт;
Fдрасч – расчётный годовой фонд времени работы, принятый при обосновании режима работы предприятия, ч;
к – коэффициент, учитывающий КПД токоприёмников, потери в сети, долю использования оборудования во времени и по мощности; принимается равным 0,35 – 0,45.
Окончательно все расчёты расхода электроэнергии представлены в форме таблицы 19.
Таблица 19 – Установленная мощность и расход электроэнергии на предприятии.
Наименование цеха, участка, технологи-ческой линии
Электросиловое оборудование
Годовой расход электроэнергии на электроосвещение, кВт·ч
установленная мощность, кВт
расчётная нагрузка, кВт
годовой расход электроэнергии, кВт·ч
БСЦ
90,064
36,03
141796,8
14179,68
Склады сырья
59,3
23,72
93361,92
9336,192
Арматурный цех
588,35
235,34
926298,2
92629,82
Формовочный цех
93,4
37,36
147049
14704,9
Ремонтно-механический цех
83,11
33,24
130848,4
13084,84
Лаборатория
2,92
1,17
4597,25
459,72
Итого
914,22
365,69
1439354
143935,4
Примечание: в курсовом проекте допускается расходы электроэнергии на освещение принимать без расчёта в пределах 10-15 % от расходов электроэнергии на электросиловое оборудование.
2.6. Система контроля производственного процесса и качества продукции.
В состав разработки входят: карта контроля производственного процесса, спецификация лабораторного оборудования, численность контролирующего персонала и решения по размещению лаборатории и отдела технического контроля.
Таблица 20 – Карта контроля производства ребристых плит.
Форма конт-роля
Наимено-вание передела или операции
Объект контро-ля
Перечень конт-ролируемых опе-раций, парамет-ров с численны-ми значениями
Стан-дарты, ТУ
Перио-дич-ность конт-роля
Метод и средс-тва
Конт-роли-рую-щее лицо
Учёт-ная доку-мента-ция
1
2
3
4
5
6
7
8
9
Входной
Приём сырья и материалов
Цемент
Вид, марка, тон-кость помола, сроки схватыва-ния, нормальная густота
ГОСТ 3101-76, ГОСТ 10178-85
Каждая партия
прибор ПСХ-2, прибор Вика
Лабо-рант
Лабо-ратор-ный журнал
Щебень
Вид, средняя плотность, насы-пная плотность, зерновой состав, межзерновая пустотность
ГОСТ 8287-82, ГОСТ 8736-93
Каждая партия
Пресс, сита
Лабо-рант
Лабо-ратор-ный журнал
Песок
Вид, истинная и насыпная плот-ность, модуль крупности, нали-чие примесей
ГОСТ 8736-93
Каждая партия
Сита
Лабо-рант
Лабо-ратор-ный журнал
Армату-рная сталь
Вид, класс, мар-ка, наличие сер-тификата, пре-дел прочности, предел текучести
ГОСТ 9781-82, ГОСТ 7509-89*
Каждая партия
Пресс, штан-генцир-куль
Лабо-рант
Журнал испыта-ний
Пооперационный
Приготов-ление бетонной смеси
Бетонная смесь
Точность дозирования, продолжительность перемешивания, удобоукладываемость
ГОСТ 10181-81
1 раз в неделю
Секун-домер, дозатор
Рабочий БСЦ, лабо-рант
Лабо-ратор-ный журнал
Производс-ство арма-турных из-делий
Арматур-ные изделия
Режим сварки, при-менение стали за-данного класса, раз-меры и конструкция изделий, прочность на разрыв
ГОСТ 23858-79
1 раз в неделю
Штан-генцир-куль, измери-тельная линейка
Рабо-чий, мастер
Журнал испыта-ний
Формова-ние изделий
Форма
Чистота поверхнос-ти, равномерность смазывания поверх-ности
—
1 раз в смену
Визуа-льно
Мастер, контро-лёр ОТК
Лабо-ратор-ный журнал
Укладка и уплот-нение бе-тонной смеси
Продолжительность уплотнения
ГОСТ 10181-81
1 раз в неделю
Секун-домер
Конт-ролёр ОТК
Лабо-ратор-ный журнал
1
2
3
4
5
6
7
8
9
Выходной
Приём из-делий ОТК на складе готовой продукции
Железо-бетонные изделия
Определение проч-ности бетона, моро-зостойкости, водо-непроницаемости, трещиностойкости, толщины защитного слоя
ГОСТ 10060-95
ГОСТ 12730-78
ГОСТ 10180-90
Каждая партия
Моло-ток, пресс
Конт-ролёр ОТК, лабо-рант
Журнал ОТК, паспорт продук-ции
2.7. Характеристика компоновочных решений.
Формовочный цех завода железобетонных изделий для промышленного строительства занимает два пролёта размером 18 х 120 м. Шаг наружных колонн – 6 м, шаг внутренних колонн составляет 12 м. Выбор высоты цеха осуществляется исходя из возможности извлечения изделий из пропарочных камер. В каждом из пролётов размещена технологическая линия. Длина пролёта позволяет разместить необходимое оборудование и площадки для промежуточного складирования изделий и ремонта форм.
При принятии компоновочных решений были соблюдены поточность производства изделий, последовательность выполнения рабочих операций, исключены встречные и пересекающиеся потоки.
Арматурный цех расположен с перпендикулярно формовочному цеху и отделён от него стеной. Размеры арматурного цеха 24 х 108 м, в торце арматурного цеха расположен склад арматурной стали размером 24 х 24 м.
Сообщение между формовочным и арматурным цехом осуществляется посредством двух ворот и самоходных тележек.
Склад готовой продукции расположен перпендикулярно формовочному цеху и расположен на расстоянии 11,5 м от него. Сообщение между складом готовой продукции и формовочным цехом осуществляется посредством самоходных тележек.
3. Решения по охране труда, окружающей среды.
Современное промышленное производство загрязняет окружающую среду не только газообразными и твердыми отходами, но и тепловыми выбросами, электромагнитными полями, ультрафиолетовыми, инфракрасными, световыми и другими ионизирующими излучениями, радиоактивными веществами, шумовыми и другими физическими и химическими факторами.
Труд, как основная форма жизнедеятельности человека, представляет систему, которая должна характеризоваться способностью, а следовательно, и безопасностью труда. На безопасность труда влияет очень многие разнородные факторы: внешняя среда, организация производственного процесса в целом и на рабочем месте, состояние оборудование и др.
При принятии решений по обеспечению безопасности труда и охраны окружающей среды необходимо учитывать все эти разнородные факторы.
Решения по охране труда представлены в форме таблицы .
Таблица 21 – Решения по охране труда.
Технологический передел, процесс, операция
Возможные опасности и производственные вредности
Принятые решения
1
2
3
Виброуплотнение
Развитие виброболезни, по-теря слуха, расстройство нервной системы, нарушение функционирования внутрен-них органов
Устройство звуковой вибрационной изоляции помещения, рабочих мест, снабжение рабо-чих наушниками
Формование
Получение травм
При запуске формовоч-ных машин включать звуковую сигнализацию
Подъёмно-транспортные операции
Получение травм
Перед проведением опе-раций извещать рабочий персонал звуковым сиг-налом
Для предотвращения загрязнения воздуха рабочих помещений вредными выделениями и их распространения следует выполнить следующие операции:
источники выделения тепла должны быть теплоизолированы;
выбросы в виде пыли, паров и вредных газов перед выпуском в атмосферу должны быть подвержены очистке;
необходимо предусмотреть естественную или принудительную вентиляцию;
устройства и системы, при эксплуатации которых происходит влаговыделение, надежно укрываются.
Вода, используемая для промывки технологического оборудования, должна подвергаться очистке на локальных очистных сооружениях до концентрации, при которой она снова сможет поступать на технологические нужды для вторичного использования.
На стадии проектирования предусматриваются нормы безопасной работы и эксплуатации тепловых установок. Каждая тепловая установка разрабатывается с таким расчетом, чтобы она создавала оптимальные условия ведения технологического процесса и безопасные условия труда. Для этого необходимо, чтобы поверхности установок были теплоизолированы и имели температуру не выше 40 градусов.
Электрооборудование и электроприборы, размещённые в цехах, где производят тепловлажностную обработку, должны быть рассчитаны на работу во влажной среде. Электродвигатели должны иметь обязательное заземление. В цехах, где расположены установки для тепловлажностной обработки, вывешивают инструкции по охране груда при обслуживании данных установок.
Во всех производственных, бытовых и административных помещениях на случай возникновения пожара должна быть обеспечена возможность безопасной эвакуации людей через эвакуационные выходы.
4. Архитекрурно-строительные решения, генеральный план и транспорт.
4.1. Генеральный план и транспорт.
Генеральный план проектируемого предприятия разработан в соответствии со СНиП II-89-90 “Генеральный план промышленных зданий”.
Проектируемое предприятие по выпуску железобетонных изделий размещено на землях мало пригодных для сельского хозяйства. Предприятие находится в промышленном узле города Воронежа.
При формировании генерального плана предприятия ориентировались на зонирование территории. Выделили следующие зоны:
- предзаводская – эта зона расположена со стороны основных магистралей города и предназначена для осуществления кратчайшей связи с жилой зоной района и наиболее короткого пути следования рабочих на предприятие. В этой зоне располагается административно-бытовой корпус.
- промышленная – где располагаются цеха основного производства.
- складская – где располагаются склады сырья и полуфабрикатов.
Генеральный план разработан, исходя из условий размещения предприятий в едином промышленном узле, где решены вопросы энерго- и теплоснабжения, водопровода, канализации, подъездных путей автомобильных дорог. Ширина автомобильных дорог 6 м.
Размещение производственных зданий, а также административных и вспомогательных помещений производим с учетом господствующей розы ветров. Это является эффективным средством защиты города от вредных технологических выделений в атмосферу, проветриванием территории завода от снегозаносов.
Предприятие размещено в городе Воронеже. Господствующие ветра: в зимний период – западный, в летний период – северный. Предприятие размещено под углом 45° к северному ветру.
5. Технико-экономические расчёты.
5.1. Стоимость строительства.
Составление сметно-финансовых расчётов производится по общепринятой методике, состоящей из 12-ти глав:
часть 1:
глава 1 – подготовка территории строительства;
глава 2 – объекты основного производственного назначения;
глава 3 – объекты подсобного производственного и обслуживающего назначения;
глава 4 – объекты энергетического хозяйства;
глава 5 – объекты транспортного хозяйства и связи;
глава 6 – инженерные сети и сооружения;
глава 7 – благоустройство территории;
глава 8 – временные здания и сооружения;
глава 9 – прочие затраты и работы.
часть 2:
глава 10 – содержание дирекции строящегося предприятия;
глава 11 – расход на подготовку эксплуатационных кадров;
глава 12 – затраты на проектно-изыскательские работы. /12/
Таблица 24 – Стоимость зданий и сооружений основного производственного назначения.
Наименование зданий и сооружений
Единицы
измерения
Количество
Стоимость за
единицу, р.
Общая стоимость, тыс.р.
Главный производственный корпус
м3
63122,4
292,3
18450,68
Другие здания основного производственного назначения (подготовительные, смесительные)
м3
-
-
5106
Агрегаты тепловой обработки
м3
1313,28
995,3
1307,1
Особостроительные работы
м2
5004
451,4
2258,8
Склады сырья
м2
-
-
18196,6
Склад готовой продукции
м2
1944
1739
3380,6
Сооружения охраны окружающей среды
м2
-
-
4691,7
Итого стоимость:
53391,48
Таблица 25 – Стоимость оборудования основного производственного назначения.
Наименование цехов и участков
Стоимость, тыс. руб.
Примечание
Склады сырья
6219,7
—
Смесительный цех
2870
—
Арматурный цех
3941,4
—
Формовочный цех
9917,42
—
Участки тепловой обработки
1448,4
—
Склад готовой продукции
476,4
—
Оборудование лаборатории и ОТК
1492,4
6 % от стоимости основного оборудования
Инструменты и приспособления
248,73
1 % от стоимости основного оборудования
Объекты охраны окружающей среды
2984,79
12 % от стоимости основного оборудования
Неучтённое оборудование
3730,99
15 % от стоимости основного оборудования
Итого
33330,23
—
Таблица 26 – Сводный расчёт сметной стоимости по главе 2.
Наименование затрат
Стоимость,
тыс. руб.
Структура,
%
Здания и сооружения
53391,48
61,3
Оборудование
33330,23
38,7
Всего
86721,71
100
Таблица 27 – Сводный сметно-финансовый расчёт проектной стоимости основных фондов.
Наименование частей и глав сводного сметно-финансового баланса
Сметная стоимость, тыс. руб.
Способ определения
Зданий и сооружений
Технологического оборудования
Общая
Часть 1
глава 1 – подготовка тер-ритории строительства
669,7
-
669,7
148 тыс. руб. за 1 га
глава 2 – объекты основного производственного назначения;
53391,48
33330,23
86721,71
Табл. 31
Итого по главам 1 и 2:
54061,18
33330,23
87391,41
—
глава 3 – объекты подсобного производственного и обслуживающего назначения
16017,45
9999,06
26016,51
30 % от главы 2
глава 4 – объекты энергетического хозяйства;
5339,15
3333,02
8672,17
10 % от главы 2
глава 5 – объекты транспортного хозяйства и связи;
10678,3
6666,04
17344,34
20 % от главы 2
глава 6 – инженерные сети и сооружения;
13347,88
8332,55
21680,43
25 % от главы 2
глава 7 – благоустройство территории;
5339,15
3333,02
8672,17
10 % от главы 2
глава 8 – временные здания и сооружения;
1334,79
833,33
2168,04
2,5 % от главы 2
глава 9 – прочие затраты и работы
1067,83
666,61
1734,43
2 % от главы 2
Итого по 1 части:
107185,73
66493,86
173679,5
—
глава 10 – содержание дирекции строящегося предприятия
2669,58
1666,51
4336,09
5 % от главы 2
глава 11 – расход на подготовку эксплуатационных кадров
2669,58
1666,51
4336,09
5 % от главы 2
глава 12 – затраты на проектно-изыскательские работы
1067,83
666,61
1734,43
2 % от главы 2
Итого по 2 части:
6406,99
3999,63
10406,61
—
Проектная стоимость основных фондов
113592,72
70496,49
184086,11
—
Таблица 28. Амортизационные отчисления.
Группа основных фондов
Стоимость, тыс.р.
Норма амортизационных отчислений, %
Сумма амортизационных отчислений, тыс.р.
Здания и сооружения
113592,72
2-2,5%
2271,85
оборудование
70496,49
15%
10574,47
Всего:
-
12846,32
5.2. Затраты на производство. Стоимость единицы продукции.
Таблица 29 – Затраты на сырьё, материалы и полуфабрикаты.
Наименование сырья, материалов и полуфабрикатов
Ед. изм.
Заготови-тельная цена, руб./ед.
Норма рас-хода на 1 м3
Годовой объём выпуска продук-ции, м3
Расход на годовую программу
нат. ед.
тыс. руб.
Ребристая плита
Цемент
т
2330
0,32
23301,12
7456,36
17373,32
Песок
м3
110
0,45
10485,5
1153,41
Щебень
м3
330
0,9
20971,01
6920,43
Арматурная сталь
т
25200
0,07547
1758,61
44316,97
Добавка С-3
кг
22
0,08
1864,09
41,01
Итого
69805,14
Таблица 30 – Затраты на воду.
Назначение расходов воды
Заготовительная цена, руб./м3
Норма расхода на 1 м3
Годовой объём выпуска продукции, м3
Расход на годовую программу
м3
тыс. руб.
На технологические нужды
18,68
0,2
42430,08
8486,02
158,52
На общехозяйственные нужды
18,68
0,1
42430,08
4243,01
79,26
Всего
237,78
Таблица 31 – Затраты на топливо и теплоносители.
Назначение затрат
Вид теплоносителя
Заготовительная цена, тыс. руб./т
Норма расхода на 1 м3
Годовой объём выпуска продукции, м3
Расход на годовую программу
т
тыс. руб.
На технологические нужды
Пар
250
0,17
42430,08
7213,11
1803,28
На внепроизводственные нужды
Пар
250
0,1
42430,08
4243,01
1060,75
Всего
11456,12
2864,03
Таблица 32 - Затраты на электроэнергию и установленную мощность.
Назначение затрат
За установленную мощность
За электроэнергию
Сумма затрат тыс. р.
установленная мощность, кВт
годовой тариф, р./кВт
годовые затраты, тыс. р.
годовой расход, кВтчас
установленный тариф, р./кВтчас
годовые затраты, тыс. р
на технологические цели
-
-
-
1437736,2
0,76
1092,68
1092,68
плата за установленную мощность
828,19
3127
2589,75
-
-
-
2589,75
на другие цели
86,03
3127
269,02
148990,21
0,76
113,23
382,25
Всего
914,22
-
2858,77
1586726,4
-
1205,91
4064,68
6. ОРГАНИЗАЦИЯ КОНТРОЛЯ ТЕХНОЛОГИЧЕСКОГО ПРОЦЕССА И КАЧЕСТВА ГОТОВОЙ ПРОДУКЦИИ
При производстве сборных железобетонных изделий технический контроль осуществляют на различных стадиях технологического процесса. В зависимости от этого контроль различают входной, операционный и приемочный.
Контроль производства осуществляет цеховой технический персонал, он отвечает за соблюдение технологических требований к изделиям. Отдел технического контроля предприятия (ОТК) контролирует качество и производит прием готовой продукции, проверяет соответствие технологии техническим условиям производства изделий.
В задачи производственного контроля входят: контроль качества поступивших на предприятие материалов и полуфабрикатов — входной контроль; контроль выполнения технологических процессов, осуществляе-мый во время выполнения определенных операций в соответствии с установленными режимами, инструкциями и технологическими картами — операционный контроль; контроль качества и комплектности продукции, соответствие ее стандартам и техническим условиям — приемочный контроль.
Приемочный контроль — это контроль готовой продукции, по результатам которого принимается решение о ее пригодности к поставке потребителю. Его результаты используются для выявления недостатков технологического процесса и внесения необходимых изменении. Он устанавливает соответствие качественных показателей ригелей требованиям ГОСТа 13015 и проекта изделия. Он предусматривает испытания и измерения готовых железобетонных изделий и обобщение данных входного и операционного контроля.
Контроль может, быть сплошным, т. е. каждой единицы продукции, и выборочный, т. е. контроль части продукции, по результатам которого оценивают всю партию. В производстве железобетонных изделий находит применение статический приемочный контроль качества — выборочный контроль с использованием статистических методов для обоснования плана контроля или корректировка этого плана по накопленной информации.
При соответствующем качестве материалов и правильно организованном операционном контроле создаются условия выполнения технологического процесса, гарантирующие выход продукции высокого качества. Исходные материалы, поступающие на завод, подвергаются систематическому контролю. Действенность контроля обеспечивается правильным хранением материалов по видам, маркам и партиям, паспортизацией материалов и их использованием.
Автоматизация контроля и регулирования производственного процесса находит наиболее широкое применение на заводах железобетона, где уже практически решена задача создания заводов-автоматов.
7.РЕШЕНИЯ ПО ТЕХНИКЕ БЕЗОПАСНОСТИ
Техникой безопасности называется система организационных и технических мероприятий и средств, предотвращающих воздействие на работающих опасных производственных факторов.
Охране труда рабочих в нашей стране уделяется огромное внимание. Российское государство постоянно заботится о создании здоровых и безопасных условий труда, об устранении причин травматизма и заболеваний трудящихся на производстве. На выполнение мероприятий по охране труда ежегодно тратятся огромные средства.
Выполнение правил по технике безопасности является основным условием снижения производственного травматизма и полной его ликвидации. Все работающие должны хорошо знать правила и инструкции по технике безопасности и производственной санитарии.
Ответственность за выполнение мероприятий по охране труда и технике безопасности несут руководители данного предприятия.
Для повседневного контроля за выполнением мероприятий по охране труда и улучшением условий эксплуатации машин и оборудования назначается инженер по технике безопасности, в обязанности которого входит также организация обучения рабочих и инженерно-технического персонала безопасным приемам работы и правилам техники безопасности.
Поступающие на предприятия рабочие допускаются к работе только после прохождения вводного инструктажа по технике безопасности и инструктажа непосредственно на рабочем месте. Инструктаж на рабочем месте обязателен также для всех рабочих, переводимых в пределах предприятия с одной работы на другую.
При вводном инструктаже вновь принятый рабочий знакомится с характером работ на предприятии, основным положением по охране труда, технике безопасности и промышленной санитарии, правилами внутреннего трудового распорядка, индивидуальными средствами защиты, порядком регистрации несчастных случаев и др.
Производственный инструктаж на рабочем месте проводит начальник или мастер цеха. Рабочий должен ознакомиться с технологией производства на участке, где ему предстоит работать, с требованиями охраны труда, правильной организацией рабочего места, устройством машин и оборудования, безопасными приемами работы при их обслуживании и др.
Содержание инструктажа и оценка знаний рабочих заносится в журнал, которых хранится в каждом цехе и ведется по установленной форме.
Все вновь принятые на работу, а также переведенные с другой работы должны сдать экзамен по технике безопасности. Лица, не выдержавшие экзамена, не допускаются к обслуживанию агрегатов, машин и механизмов.
На рабочих местах должны быть инструкции по технике безопасности.
В цехах, кроме инструкций, вывешиваются на видных местах плакаты, иллюстрирующие методы безопасного выполнения работ.
Для оказания первой помощи пострадавшим и заболевшим на предприятиях с числом рабочих более 300 организуются здравпункты или амбулатории. В каждом цехе должна быть аптечка с перевязочными и лечебными средствами для оказания немедленной помощи при ранениях, порезах, ушибах.
Все производственные и вспомогательные помещения независимо от загрязненности воздуха должны иметь естественную или искусственную вентиляцию.
Въездные и выездные ворота в формовочном цехе необходимо оборудовать тепловыми завесами. В помещениях, где производится сварка, устраивают местные вытяжки.
Все отопительно-вентиляционные устройства должны быть исправны. При повреждении их нужно немедленно ремонтировать.
Во всех производственных и подсобных помещениях необходимо максимально использовать естественное освещение. Окна и световые фонари, а также осветительные установки при искусственном освещении надо содержать с исправности и чистоте. Местное освещение и переносные лампы должны работать при напряжении тока в сети от 12 до 36 В.
Армирование. Готовые арматурные изделия (стержни, петли, сетки) должны храниться на специально отведенных местах, на специализированных стеллажах или в контейнерах.
При установке сеток для ходьбы по форме не перегородку формы необходимо укладывать деревянные подмости-трапы.
Сварщики, арматурщики, обслуживающий персонал электротермических установок могут допускаться к самостоятельной работе по наладке и обслуживанию электрического оборудования после сдачи ими дополнительных экзаменов по технике безопасности по эксплуатации закрепленного за ними электрического оборудования.
При перерыве в работе установки следует отключать от сети электропитания.
Запрещается переносить краном арматурные изделия над работающими рабочими.
В темный период суток освещенность на уровне рабочей поверхности при проведении арматурных работ, а также при складировании и погрузки изделий, должна быть не менее 30 люкс (ГОСТ 12.1.046-85).
При производстве электросварочных работ должны соблюдаться правила пожарной безопасности согласно ГОСТ 12.1.004-91.
Список используемой литературы.
1. Баженов Ю.М., Комар А.Т. Технология бетонных и железобетонных изделий. М.: Стройиздат, 1984 – 672с.
2. Производство сборных железобетонных изделий : Справочник./ под редакцией К.В.Михайлова и К.М.Королёва. – М.: Стройиздат. 1989 – 447с.
3.ОНТП 07-85 Обжесоюзные нормы технологического проектирования предприятий сборного железобетона. – М.:ЦНТП Госстроя СССР, 1986 – 40с.
4. А.Д.Никулин, Е.И.Шмитько, Б.М.зуев. Проектирование предприятии по производству строительных материалов, изделий и конструкций: Учебное пособие – Воронеж 2004 – 334с.
5. И.А.Шеришевский. Конструирование промышленных зданий и сооружений. Учебное пособие. М.: Архитектура – С, 2005 – 168с.
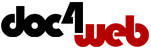
Нравится материал? Поддержи автора!
Ещё документы из категории строительство :
Чтобы скачать документ, порекомендуйте, пожалуйста, его своим друзьям в любой соц. сети.
После чего кнопка «СКАЧАТЬ» станет доступной!
Кнопочки находятся чуть ниже. Спасибо!
Кнопки:
Скачать документ