Расчет привода ленточного конвейера
Федеральное агентство по образованию (Рособразование)
Архангельский государственный технический университет
Кафедра прикладной механики и конструирования
КУРСОВОЙ ПРОЕКТ
По дисциплине: Детали машин и основы конструирования
На тему: Расчет привода ленточного конвейера
Пояснительная записка
2006г.
СОДЕРЖАНИЕ
Реферат
Подбор электродвигателя
Расчет ременной передачи
Расчет закрытой конической прямозубой передачи
Расчет валов
Подбор муфт
Расчет шпонок
Подбор подшипников
Подбор редуктора
Список литературы
РЕФЕРАТ
Курсовой проект состоит из расчетно-пояснительной записки и графической части. Графическая часть включает в себя сборочный чертеж привода на формате A1, спецификацию к этому чертежу и рабочие чертежи деталей на формате A3 в количестве двух штук. Расчетно-пояснительная записка изложена на 26 страницах печатного текста, включает одну таблицу, 13 рисунков и перечень литературы из пяти источников.
В записке приведены следующие расчеты:
1. Кинематический расчет.
Выбрали асинхронный электродвигатель серии 4A100L4. Определили параметры на валах привода: угловые скорости, расчетные мощности, вращающие моменты.
2. Расчет и конструирование клиноременной передачи. Определили основные параметры шкива.
3. Расчет закрытой конической прямозубой передачи. Выбрали материал шестерни и колеса: марка стали 45. Определили допускаемые и контактные напряжения шестерни и колеса, и по исходным данным:
рассчитали основные параметры коническое передачи.
4. Расчет валов. Выполнили расчет вала одноступенчатого редуктора. Определили диаметры валов в сечениях.
5. Подбор подшипников.
Выбрали радиально шариковый подшипник 306.
6. Расчет шпонок.
Подобрали и проверили призматическую шпонку с двумя скругленными торцами на прочность.
7. Подбор муфт.
Выбрали муфту, компенсирующую кулачково-дисковую 400-28-3 УЗ ГОСТ 20720-93
8. Подбор редуктора.
Выбрали редуктор конический одноступенчатый К-200
1. ЭНЕРГЕТИЧЕСКИЙ И КИНЕМАТИЧЕСКИЙ РАСЧЕТЫ ПРИВОДА
1.1. Подбор электродвигателя привода
1.1.1. Потребляемая мощность на рабочем валу
1.1.2 Определяем КПД привода
1.1.3 Потребляемая мощность привода
Принимаем кВт
1.2 Рациональная разбивка передаточных чисел
1.2.1 Частота вращения рабочего вала
-конвейера
1.2.2 Определяем передаточное число привода
Электродвигатель серии 4A100L4 n=1430 мин-1
1.2.3 Уточнение передаточного числа
Рисунок 1 Эскиз асинхронного электродвигателя серии 4A100L4
1.3 Определение частот вращения и угловых скоростей на валах привода
1.4 Мощности на валах
1.5 Вращающий момент
Таблица 1
-
1430
433,3
109,3
109,3
149,7
45,4
11,4
11,4
4,00
3,88
3,76
3,65
26,7
85,5
329,8
320,2
2. КЛИНОРЕМЕННАЯ ПЕРЕДАЧА
Ременные передачи осуществляют передачу вращающего момента непосредственно от вала двигателя трением и используется на быстроходных ступенях приводов.
Рисунок 2. Кинематическая схема клиноременной передачи.
Расчет клиноременной передачи.
y=4,2; b=17; δ=11;bp=14
-
Определяемый параметр
Размерность
Расчет
Коэффициент динамичности Ср, учитывающий характер нагрузки и режим работы
-
Ср=1
Расчетная передаваемая мощность N
кВт
N=N1∙ Ср
N=4∙1=4
Сечение ремня
-
В
Диаметр ведущего шкива dp1
мм
dр1=140
Диаметр ведомого шкива dp2
мм
dp2=140∙3,3∙0,99=457,4
Фактическое передаточное число uф
-
uф=450/(140∙(1-0,01))=3,25
Разность фактического и заданного передаточных чисел ∆u
%
∆u=((u-uф)/u)∙100%
Предельные значения межосевого расстояния аmin и amax
мм
аmin=0,7(dp1+dp2)
аmax=2(dp1+dp2)
аmin=0,7(140+450)=413
аmax=2(140+450)=1180
Предварительное межосевое расстояние а’
мм
а’=500
Длина ремня L
мм
L=2a’+0,5π(dp1+dp2)+((dp2-dp1)2/(4a’))
L=2∙500+0,5π(140+450)+((450-
-150)2/(4∙500))=2000
Уточненное межосевое расстояние а
мм
Угол обхвата ведущего шкива ремнем α1
град
α1=1800-57,30((dp1-dp2)/a)
α1=145,40
Скорость ремня V
м/с
V=(π∙dp1∙n1)/(60∙103)
V=(π∙140∙1430)/(60∙103)=10,5
Номинальная мощность N0, передаваемая одним ремнем
кВт
N0=2,7
Коэффициент Сu, учитывающий влияние передаточного числа
-
Сu=1+0,02∙uф=1,065
Коэффициент Сα, учитывающий угол обхвата шкива
-
Сα=1-0,0025∙(1800-α1)=0,9135
Коэффициент СL, учитывающий влияния длины ремня
-
СL=0,97
Предварительное число ремней Z’
шт.
Коэффициент Сz, учитывающий число ремней
-
Сz=0,80
Уточненное число ремней z
шт.
Z=Z’/Cz=1,57/0,80=2
Предварительное натяжение ремня F0
Н
Нагрузка на валы Fв
Н
Fв=2F0sin(α1/2)z
Fв=2∙176,2sin(145,4/2)2=672,9
Окружная сила Ft
Н
Ft=N1/(V∙z)
Ft=4∙103/(10,5∙2)=190,5
Натяжение ведущей ветви F1
Н
F1=F0+Ft/2
F1=672,9+190,5/2=271,5
Натяжение ведомой ветви F2
Н
F2=F0-Ft/2
F2=672,9+190,5/2=81,2
Напряжение в ведущей ветви σ1
Н
σ1=F1/S
σ1=271,5/138=1,97
Напряжение от изгиба на ведущем шкиве σu
МПа
σu=2Ey/dp1
σu=2∙90∙4,2/140=5,4
Напряжение от центробежной силы σv
МПа
σv=MV2/S
σv=0,18∙10,52/138=0,14
Максимальное напряжение в ремне σmax
МПа
σmax=σv+σu+σ1
σmax=1,97+5,4+0,14=7,51
Число пробегов ремня i
с-1
i=V∙103/L
i=10,5∙103/2000=5,25
Коэффициент СD, учитывающий снижение изгибных напряжений на ведомом шкиве
-
Предел выносливости материала ремня σ-1
МПа
σ-1≈9
Долговечность ремня Т
ч
Рисунок 3. Эскиз шкива для клиноременной передачи
3. ЗУБЧАТЫЕ ПЕРЕДАЧИ
Виды разрушения зубьев.
Решающее значение на работоспособность зубьев оказывают 2 вида напряжений, контактные и изгибные напряжения.
Поломка звеньев. Чаще носит усталостный характер и возникает под действием подменных изгибных напряжений. Она является особо опасным видом напряжений. Напряжения при изгибе превысившие предел выносливости вызывают микротрещины, которые возникают в зоне максимальной концентрации напряжений.
Выкрашивание. Возникает под действием переменных контактных напряжений. Большое значение имеет смазка.
Амброзивный износ зубьев. Происходит в передачах недостаточно защищенных от загрязнения амброзивными веществами.
Отслаивание поверхностных слоев наблюдается в тех случаях, когда под упрочненным поверхностным слоем контактные напряжения максимально велики.
Заедания зубьев высокоскоростных передач.
Расчет конической прямозубой передачи
3.1 Выбор материала
Шестерня Сталь 45 У
Колесо Сталь 45 H
3.2 Выбор допускаемых напряжений
Допускаемое напряжение при расчете зубьев на усталостную контактную прочность:
Для шестерни
МПа
=1.1 - коэффициент запаса прочности
Для колеса
МПа
МПа
МПа
Берем меньшее значение МПа
Допускаемое напряжение при расчете зубьев на усталостную изгибную прочность:
Для шестерни
МПа
=
=1.5,
МПа
Для колеса
МПа
=1.5
МПа
Берем меньшее значение МПа
4. РАСЧЕТ КОНИЧЕСКОЙ ПЕРЕДАЧИ
электродвигатель вал привод редуктор
4.1 Исходные данные:
4.2 Углы делительных конусов
4.3 Внешний делительный диаметр колеса
мм
4.4 Внешнее конусное расстояние
мм
4.5 Среднее конусное расстояние в=45 (по таблице 1.8)
мм
4.6 Внешний окружной модуль
мм
Принимаем ;
4.7 Средний модуль
мм
4.8 Делительный диаметр шестерни
Средний: мм
Внешний: мм
4.9 Внешний диаметр окружности вершин зубьев
Шестерни: мм
Колеса: мм
4.10 Внешний диаметр окружности впадин зубьев
Шестерни: мм
Колеса: мм
4.11 Окружная скорость зубчатых колес
м/c
4.12 Угол головки зуба
4.13 Угол ножки зуба
4.14 Углы конусов вершин зубьев (углы обточки)
Шестерни:
Колеса:
4.15 Окружная сила на шестерне и колесе
кH
4.16 Осевая сила на шестерне, радиальная сила на колесе
H
4.17 Радиальная сила на шестерне, осевая сила на колесе
H
4.18 Расчетное контактное напряжение (проверочный расчет), МПа
МПа
4.19 Расчет напряжения изгиба (проверочный расчет), МПа
Для шестерни:
определяем по табл.1.6 для шестерни и колеса по эквивалентному числу их зубьев
Для колеса:
Выбор стандартного редуктора
Конический редуктор
Тип редуктора k-200
Рисунок 4. Эскиз конического одноступенчатого редуктора типа К-200
5. ВАЛЫ
На валах устанавливают вращающие детали: зубчатые колеса, шкивы, звездочки и т.д. Вал передает вращающий момент и поддерживает сидящие на нем детали, поэтому работает на кручение и изгиб. Валы должны быть прочными, жесткими, упругими и хорошо обрабатываться. Их изготовляют из углеродистых и легированных сталей. Валы при работе испытывают циклически изменяющиеся напряжения. Основными критериями работоспособности валов является усталостная прочность, жесткость и виброустойчивость. Прочность – способность детали сопротивляться разрушению (при хрупких материалах, например чугун) или возникновению пластичных деформаций (при пластичных материалах, например сталь) под действием приложенных к ней нагрузок. Жесткость – способность детали сопротивляться изменению ее размеров и формы под действием нагрузки.
Недостаточная изгибная жесткость валов нарушает надежную работу передач и приводит к снижению работоспособности механизма. Виброустойчивость - способность детали или конструкции работать в заданном диапазоне режимов без недопускаемых колебаний. Вибрация валов снижает качество работы механизма, создает шум, уменьшает долговечность подшипников и передач.
Расчет валов
5.1 Компоновка валов.
Рисунок 5. Предварительная компоновка валов.
мм
мм
мм
мм
мм
мм
в=45 мм
шкив
муфта
Рисунок 6. Пространственная система сил.
Рисунок 7. Схема вала, с указанием приложенных нагрузок.
Fb=673 H
Ft1=4100 H
Fa1=362 H
Fr1=1451 H
Вертикальная плоскость. Определяем реакции опор:
H
H
Проверка:
0 = 0 - проверка сошлась
M3=Ra*l2=2740*33=90.4 Н*м
M2=0
M4=0
Горизонтальная плоскость. Определяем реакции опор:
H
H
Проверка:
0=0- проверка сошлась
М1=0 Нм
M2=-Fв*l1=-47.1 Нм
M3=-Fb*(l1+l2)+Ral2=22.5 Нм
M4=-Fa1*d/2=-9.5 Нм
Суммарные реакции опор определяем:
H
H
Строим эпюру суммарных изгибающих моментов:
M1=0 Нм
M2=47.1 Нм
M3=93,2 Нм
M4=9,5 Нм
Строим эпюру крутящих моментов:
H*м
Строим эпюру эквивалентных моментов:
H*м
H*м
H*м
Определяем диаметры вала в сечениях:
Сталь 45 МПа
МПа
мм; мм
мм; мм
мм; мм
мм мм
Рисунок 8. Конструкция быстроходного вала.
6. МУФТЫ
Муфты – это устройства, служащие для соединения соостных деталей, например труб, валов, стержней и т.д. В курсе деталей машин рассматриваются муфты, соединяющие концы валов и служащие для передачи вращающего момента от одного вала к другому без изменения его величины и направления. Наряду с основным назначением муфт – передавать вращающий момент – муфты отдельных типов могут выполнять и другие функции (компенсировать погрешности изготовления и монтажа валов, обеспечить соединение и разъединение валов во время работы механизма, передавать вращающий момент только в одном направлении и т.д.
6.1 Выбор муфты по расчетному вращаемому моменту.
Т - действующий момент, K –коэффициент режима работы
При спокойной нагрузке k=1…1.2
При вибрационной нагрузке k=1.5…2
При сильных толчках k=2…2.5
- номинальный крутящий момент для муфты
H*м
H∙м < Tн
d2ред= 30 мм, Тн=400 Н∙м
Муфта, компенсирующая кулачково-дисковая 400-40-3 УЗ ГОСТ 20720-93
Рисунок 9. Эскиз муфты, компенсирующей кулачково-дисковой.
7. ШПОНКИ
Шпоночные соединения представляют собой шпонку, входящую в продольные пазы вала и ступицы, вращающейся детали (шкива, звездочки, зубчатого или червячного колеса полумуфты). Она служит для передачи вращающего момента от вала к ступице, вращающейся детали или наоборот.
Достоинства: простота конструкции и низкая стоимость, легкость монтажа и демонтажа.
Недостаток: шпоночные пазы ослабляют вал и ступицу детали, насаживаемой на вал.
Шпоночные соединения бывают: ненапряженные и напряженные. Ненапряженные с помощью призматических и сегментных шпонок. Напряженные с помощью клиновых и тангенциальных шпонок. Выбираем призматические шпонки, так как они представляют собой стержни прямоугольного сечения.
7.1 Проверяем шпонку на смятие.
- глубина паза на валу;
- высота шпонки;
- толщина.
МПа
; Н*м; мм;
МПа
lшп=26 мм
Рисунок 10. Конструкция призматической шпонки с двумя скругленными торцами.
Рисунок 11. Соединение вала и ступицы детали с помощью призматической шпонки
ПОДШИПНИКИ
Опоры валов и вращающихся осей называют подшипниками. Они воспринимают нагрузки, приложенные к валу или оси, и передают их на корпус машины. В зависимости от направления воспринимаемой нагрузки подшипники бывают:
радиальные, воспринимающие в основном радиальные нагрузки, перпендикулярные оси цапфы;
радиально-упорные, воспринимающие радиальные и осевые нагрузки;
упорные, воспринимающие осевые нагрузки.
В зависимости от вида трения подшипники делятся на подшипники скольжения и подшипники качения.
8.1 Выбор подшипника
- принимается радиально шариковый подшипник 306
8.1 Выписываем динамическую грузоподъемность
H
H
8.2 По условиям эксплуатации подшипников принимаем:
коэффициент вращения
коэффициент безопасности
температурный коэффициент(при )
коэффициент надежности
8.3 Определяем соотношение
и находим путем линейной интерполяции значение e
8.4 Принимаем
8.5 Вычисляем эквивалентную динамическую нагрузку:
H
8.6 Определяем долговечность наиболее нагруженного подшипника:
ч
Рисунок 12. Эскиз шарикового радиального однорядного подшипника
Шариковые однорядные подшипники не требуют высокой точности в установке, обладают наименьшим коэффициентом трения и наиболее приспособлены для высоких частот вращения. Они самые дешевые и просты в эксплуатации.
9. РЕДУКТОР
Выбираем редуктор конический одноступенчатый типа K-200
Рисунок 13. Редуктор конический одноступенчатый типа К-200
СПИСОК ЛИТЕРАТУРЫ
A.C.Сметанин, Н.И.Дундин, Н.Н.Костылева. Энергетические и кинематические расчеты привода: Задания и методические указания к курсовому проектированию. Архангельск: РИО АЛТИ,1990.-32c.
Е.А.Богданов, Е.О.Орленко, А.С.Сметанин. Расчет и конструирование механических передач с гибкой связью: Методические указания и справочные материалы к курсовому и дипломному проектированию.-2-е изд.,перер. и доп.-Архангельск:Изд-во Арханг.гос.техн.ун-та,2004.-73c.
Г.Ф.Прокофьев, Н.И.Дундин, Н.Ю.Микловцик. Зубчатые и червячные передачи: Учебное пособие. Архангельск:Изд-во Арханг.гос.техн.ун-та,2002.-116c.
Г.Ф.Прокофьев, Н.И.Дундин, Н.Ю.Микловцик. Валы и оси. Муфты. Шпоночные и шлицевые соединения: Учебное пособие. Архангельск:Изд-во Арханг.гос.техн.ун-та,2003.-104c.
Г.Ф.Прокофьев, Н.И.Дундин, Н.Ю.Микловцик. Подшипники. Смазка и смазочные соединения.Уплотнения: Учебное пособие. Архангельск:Изд-во Арханг.гос.техн.ун-та,2004.-140c.
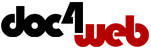
Нравится материал? Поддержи автора!
Ещё документы из категории транспорт :
Чтобы скачать документ, порекомендуйте, пожалуйста, его своим друзьям в любой соц. сети.
После чего кнопка «СКАЧАТЬ» станет доступной!
Кнопочки находятся чуть ниже. Спасибо!
Кнопки:
Скачать документ