Розробка проекту ремонту чотирьохвісних критих вагонів
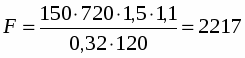
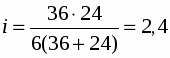



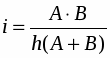













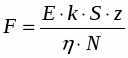
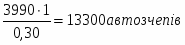
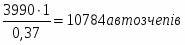
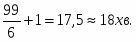
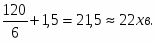


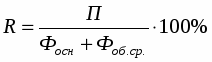







































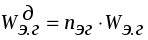


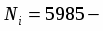
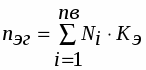

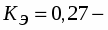
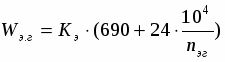






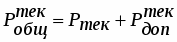

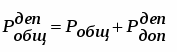









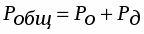










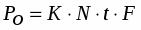
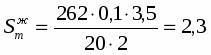
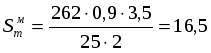

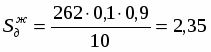

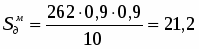

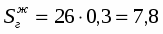










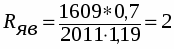

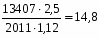
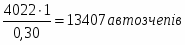

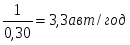

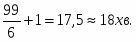




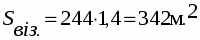

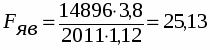
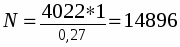
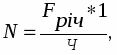

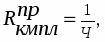
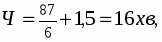
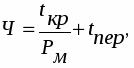
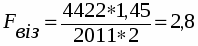
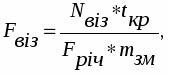



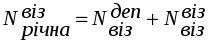

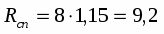
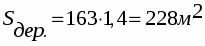




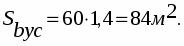

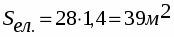

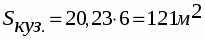




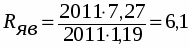


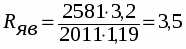



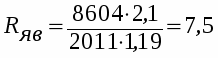












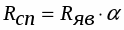
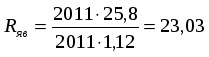
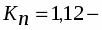




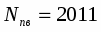

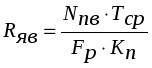

















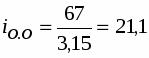


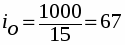
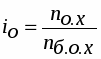
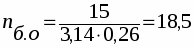
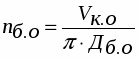
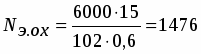


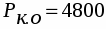

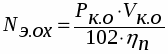



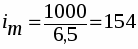

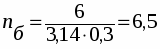
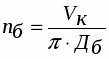
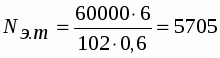









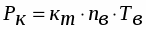

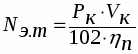


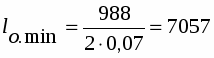
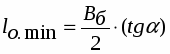
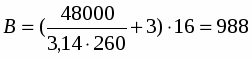
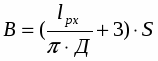





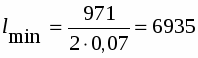
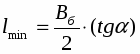
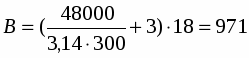



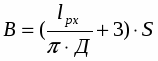


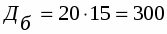

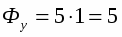
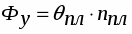
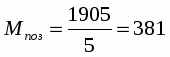
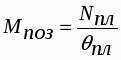
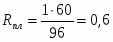
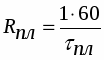
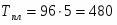
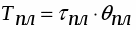
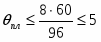


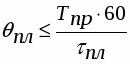
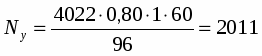

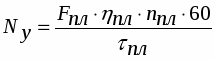




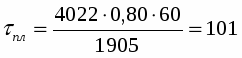
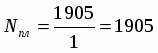



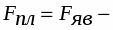
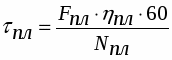
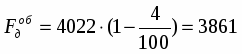

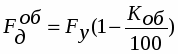


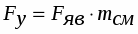




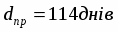




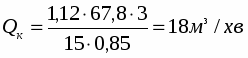




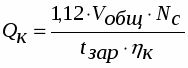

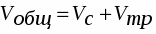
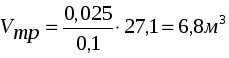
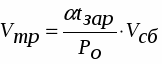
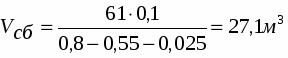
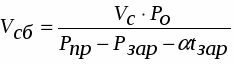
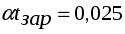












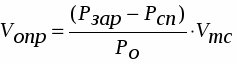
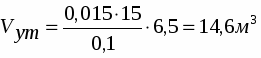


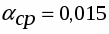

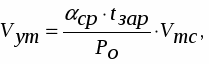
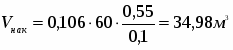








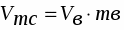

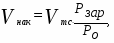
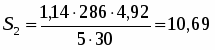
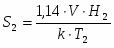
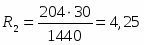
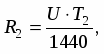
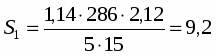
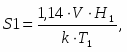
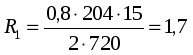

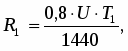
















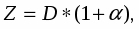

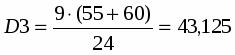
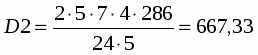
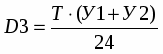



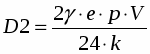
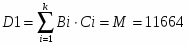


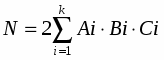
Вступ
Залізничний транспорт є однією з важливіших складових частин, яка забезпечує життєдіяльність багатогалузевої економіки України. Загальна протяжність залізничної мережі України становить 22,5 тис. км. Кількість працівників основної діяльності залізниць - понад 370 тис. чол.
Характерною рисою управління галуззю сьогодні є визначення пріоритетів на кожному й розвитку залізничного транспорту України.
Майбутнє галузі її докорінною реструктуризацією. Нині успішно реалізуються завдання першого етапу реструктуризації, які забезпечать істотне зменшення собівартості перевезень, підвищення продуктивності праці персоналу. Цією роботою займаються і працівники Південної-Західної залізниці.
Вагоноремонтне виробництво є складовою частиною залізничного транспорту, а організація та технологія ремонту вагонів тісно пов’язана з експлуатацією вагонного парку.
процес ремонту вагонів дуже складний та різноманітний. Для його забезпечення необхідні значні витрати праці і часу, необхідне різноманітне технологічне обладнання та інструменти. Вагоноремонтне підприємство являє собою організацію, яка складається з основних та допоміжних дільниць і обслуговуючих господарств, в яких одночасно виконується велика кількість різнорідних, але в той же час тісно пов'язаних процесів виробництва.
Вагоноремонтне депо, що проектується, призначене для деповського ремонту вагонів. З метою виробництва створення більш сприятливих умов виконавцям робіт передбачено впровадження прогресивних технологічних процесів ремонту вагонів і його частин, впровадження в експлуатацію нових високопродуктивних машин і механізмів, впровадження потокового методу ремонту.
Організація ремонту вагонів, їх вузлів та деталей на автоматизованих та механізованих потокових лініях є одним з головних напрямків прискорення науково-технічного прогресу у вагоноремонтному виробництві.
Вагонне господарство залізниць, розвиваючи сучасну матеріально-технічну базу та ремонту вагонів, здобуває міцну індустріальну основу для забезпечення високого рівня працездатності вагонного парку в сучасних умовах його експлуатації.
В даному дипломному проекті розглянуте питання реструктуризації контрольного пункту автозчепу, на базі вагонного депо «Дарниця». В даному депо впроваджуються установки які дозволяють відновляти корпуси автозчепів з зношеним більш норми перемичками.
Розрахований поточний метод ремонту корпусу автозчепу, розрахунок проведений за допомогою ЕОМ.
Також розрахований техніко економічний ефект прийнятих рішень, даний розрахунок приведений в розділі 7.
Уділено увагу питанням охорони праці в контрольному пункті автозчепу.
1. Проектування пункту технічного огляду вагонів на сортувальній станції
Призначення і структура системи технічного обслуговування та ремонту вагонів
Система технічного обслуговування і ремонту вагонів має тісний взаємозв'язок у часі й у просторі з експлуатаційною роботою станції.
Тому розробка питань організації вагонного господарства починається з аналізу вагонопотоків станції.
При цьому приділяється велика увага розміщенню всіх пристроїв на території станції.
Пункти технічного обслуговування вагонів призначені для перевірки справності, що тече ремонту вагонів і підготовки їх до перевезень. Відповідно до встановленого технологічного процесу і графіка руху поїздів на ПТО контролюють технічний стан вагонів, виконують поточний ремонт і випробування автоматичних гальм.
Для відновлення працездатності вагонного парку в процесі експлуатації в пунктах масового навантаження, вивантаження і формування порожніх поїздів створюються механізовані пункти поточного відчіпного ремонту вантажних вагонів.
Створення і розвиток механізованих пунктів підготовки вагонів (ППВ) до перевезень розглядаються як важливий крок у формуванні технічної бази для обслуговування вагонів. Вагонні депо призначені для забезпечення технічного обслуговування вантажних вагонів на заданих дільницях і виконання деповського ремонту.
1.2 Розробка прогресивного технологічного процесу ПТО
Унаслідок збільшення швидкості руху вантажних поїздів до 120 км/год, водіння здвоєних поїздів, підвищення вантажопідйомності вагонів, упровадження засобів механізації вантажно-розвантажувальних операцій значно зросли навантаження на вузли і деталі вагонів.
Аналіз роботи ПТО мережі залізниць показав, що в парку відправлення, при існуючій типовій технології, затрачається близько 10 – 15 хвилин на повторний пошук несправностей вагонів і безпосередньо на ремонт і випробування гальмів тільки 15 – 20 хвилин. При діючому порядку технічного обслуговування вагонів на сортувальних станціях має місце дублювання огляду, що знижує продуктивність праці працівників ПТО, не забезпечує виконання повного обсягу ремонтних робіт. Тому виконання більш трудомістких робіт з ремонту рухомого складу передбачається не в парку відправлення, а на спеціалізованих коліях сортувального парку, виділених для цієї мети й обладнаних відповідним технологічним оснащенням.
Комплекс задач автоматизованої системи управління ПТО (АСУ ПТО) як складова частина автоматизованої системи управління роботою сортувальної станції (АСУ СС) у єдиному технологічному процесі її роботи. Технологія АСУ ПТО розроблена з урахуванням виділення додатково двох шляхів (тупиків) для нагромадження і ремонту вагонів поточним відчіпним ремонтом.
Пропонована технологія дозволяє організувати безвідчіпний ремонт вагонів у парку відправлення і поточний відчіпний – на спеціалізованих коліях сортувального парку по нарядах. Ця система створює умови для повного і якісного усунення несправностей вагонів, забезпечення контролю за наявністю запасу деталей і матеріалів і використанням робочої сили в змінах. Впровадження АСУ дозволить робити аналіз зупинок поїздів за показниками приладів КТСМ-01Д.
На основі збору первинних даних ПТО представляється можливим формувати інформаційний масив, що є базою для рішення задач по контролю за якістю підготовки поїздів у рейс і надалі за технічним станом вагонів усієї мережі залізниць.
Технологія АСУ ПТО повинна впроваджуватися при оснащенні існуючих сортувальних станцій засобами обчислювальної техніки, а також при розробці документації на будівництво нових і реконструкцію діючих сортувальних станцій. Упровадження комплексної автоматизації і механізації виробничих процесів на ПТО забезпечує підвищення якості технічного обслуговування вагонів, подальше подовження гарантійних дільниць невпинного руху поїздів, а також підвищення продуктивності і поліпшення умов праці.
До засобів автоматичного контролю технічного стану рухомого складу на ходу поїзда відноситься апаратура виявлення перегрітих букс та система комплексного контролю КТСМ-01Д.
Основне призначення засобів контролю полягає в підвищенні безпеки руху поїздів завдяки своєчасному виявленню несправностей рухомого складу. Поїзда, у яких за допомогою засобів контролю будуть виявлені несправні вагони, зупиняються на станції, перед якою розташовані ці засоби, для огляду, усунення чи несправностей відчеплення вагона.
Система КТСМ-01Д включає у свій поїзд базову підсистему для виявлення перегрітих букс, підсистему для виявлення дефектів коліс по колу катання, підсистему –для виявлення деталей, що волочаться.
Апаратура КТСМ-01Д призначається для безконтактного виявлення на ходу поїзда перегрітих букс рухомого складу і видачі обслуговуючому персоналу на станції інформації про наявність і розташування в поїзді вагонів з такого виду несправностями.
Принцип дії апаратури КТСМ-01Д заснований на сприйнятті чуттєвими елементами імпульсів інфрачервоного випромінювання від задніх, по ходу руху поїзда, стінок корпусів букс, і додатково від маточини колеса з наступним перетворенням цих імпульсів в електричні сигнали, виділенні сигналів від перегрітих букс, реєстрації і передачі отриманої інформації.
Принцип дії системи КТСМ-01Д заснований на вимірі за допомогою п'єзоелектричних датчиків прискорень рейки при ударі по ньому колеса з дефектом по колу катання (повзун, навар, вищерблини, нерівномірний прокат) і виділенні за визначеними критеріями сигналу інформації у випадках, коли динамічний вплив колеса на рейку перевищує задане граничне значення. Система виробляє сигнал наявності у вагоні деталі, що волочиться, при механічному зіткненні вузлів і деталей вагона, що виходять за межі нижнього обрису габариту рухомого складу, з елементами напільного електромеханічного датчика підсистеми.
Апаратура КТСМ-01Д включає у свій поїзд перегінне і станційне устаткування, зв'язані між собою кабельною лінією зв'язку. Перегінне устаткування у свою чергу підрозділяється на напільне і постове, а станційне - на, що реєструє і сигналізує.
Напільне устаткування встановлюється безпосередньо на шляху і призначено для зчитування інформації з рухомого складу. Сигнали від напільного устаткування надходять по кабелю до постового устаткування.
Після обробки сигналів пристроями постового устаткування інформація про стан букс вагонів передається до станційного устаткування і реєструється цифродрукуючими пристроями. При цьому для апаратури КТСМ-01Д установлюються порядкові номери вагонів (починаючи з голови поїзда) з перегрітими буксами, сторона поїзду, загальна кількість вагонів у поїзді, загальна кількість вагонів з перегрітими буксами, справність.
Система КТСМ-01Д забезпечує додатково вказівку порядкового номера осі з перегрітою буксою у вагоні, ступені перегріву букси, часу контролю поїзда, його порядкового номера.
У момент виявлення засобами контролю перегрітих букс, дефектів чи коліс деталей, що волочаться, зі станційного устаткування відповідні сигнали про це передаються на сигнальний світловий покажчик, встановлюваний між перегінним устаткуванням і вхідним сигналом станції, а також на устаткування, що сигналізує. Устаткування засобів, що сигналізує, контролю видає звукові і світлові сигнали тривоги. При цьому в системі КТСМ-01Д передбачений видача сигналу «Тривога1», виявленні перегрітих букс середнього ступеня аварійності (температура букси незначно перевищує рівень настроювання) чи несправних коліс по колу катання, і сигнал «Тривога2», при виявленні перегрітих букс із високою температурою шийки чи осі деталі, що волочиться.
Особи, що знімають показання пристроїв засобів контролю, повідомляють черговому по станції про наявність у поїзді несправних вагонів, що прибуває, про вид несправностей, а оглядачам-ремонтникам – додатково про кількість, розташування в поїзді таких вагонів.
1.3 Розрахунок вагонопотоку на сортувальній станції
Обсяг роботи сортувальної станції характеризується добовим вагонопотоком, що проходить через станцію. Він визначається по формулі [2,c.5]
,(1.1)
де k – число дільниць полігона, k=5;
Bi – розміри руху на i-тій дільниці;
Ci – середня кількість вагонів у поїздах на i-тій дільниці.
5
1
11664
)
56
43
55
41
57
39
58
41
60
40
(
i
M
вагонів.
Схема сортувальної станції – двостороння [дивись графічну частину аркуш ВЧДГ – 05985.02.00.00.]
Загальний пробіг вагонів на полігоні [2,c.5]
, (1.2)
де Ai – довжина дільниці даного полігона.
вагонів. км.
1.4 Розрахунок робочого і наявного парків вагонів
Робочий парк вагонів підраховується за формулою [2,c.5]
D=D1+D2+D3, (1.3)
де D1 – кількість вагонів у русі [2,c.5];
D2 – кількість вагонів, які знаходяться на переробці на технічних станціях [2,c.6];
D3 – кількість вагонів, які знаходяться під вантажними операціями [2,c.6]
вагонів.(1.4)
,(1.5)
де - число призначень поїздів за планом формування, =5 [2,c.6];
e – параметр нагромадження, е=7 [2,c.6];
р – число технічних станцій, р=К-1=5-1=4 [2,c.6];
V – сумарне число вагонів у поїздах усіх дільниць.
[2,c.6], V=286(1.6)
,(1.7)
де Т – норма простою вагонів під однією вантажною операцією, Т=9ч. [2,c.6];
У1 – середньодобове вивантаження, У1=55вагонів. [2,c.6];
У2 – середньодобове навантаження, У2=60вагонів. [2,c.6]
вагонів.
вагонів.
вагонів.
Загальний інвентарний парк вагонів розраховується за формулою [2,c.6]
(1.8)
де - коефіцієнт, що враховує вагони, що знаходяться в неробочому парку.
[2,c.7]
вагонів.
Інвентарний парк визначених вагонів розраховуємо за формулою [2,c.7]
(1.9)
де - коефіцієнт, що враховує наявність у загальному парку вагонів
визначеного типу (критих вагонів), =0,18
вагонів.
Всі значення для розрахунку ПТО на ЕОМ відобразимо в таблиці 1.1
Таблиця 1.1- значення для розрахунку ПТО на ЕОМ
Фізичний параметр
Ім’я
Фізичний параметр
Ім’я
А
A
P
0,2
В
B
Z1
Z1
2784
С
C
Z2
Z2
20
K
K
Z3
Z3
180
Y1
Y1
55
F1
F1
0,1
Y2
Y2
60
F2
F2
0,4
N
N
L1
L1
M
M
L2
L2
2146
V
V
286
R1
R1
2
U
U
204
R2
R2
4
Д
Д
T1
T1
15
Q
5
T2
T2
30
e
E
7
S1
S1
10
T
T
9
S2
S2
11
Z
Z
13922
H1
H1
2,12
W
0,125
H2
H2
4,92
1.5 Потреба вагонів у ремонті
Кількість вагонів, що підлягають капітальному ремонту розраховується по формулі [2,c.7]
(1.10)
деF1 – коефіцієнт циклічності ремонту, зворотний міжремонтному періоду в літах, F1=0,1;
Z2 – кількість нових вагонів, включених в інвентарний парк за міжремонтний період, Z2=20;
Z3 – кількість вагонів, уперше підметів капітальному ремонту в планованому році, Z3=180.
вагонів.
Кількість вагонів, що підлягають деповському ремонту розраховуємо по формулі [2,c.7]
(1.11)
де F2 – коефіцієнт враховуючий постачання нових вагонів, а також наявність вагонів, що пройшли капітальний ремонт у попередні роки, F2=0,4 [2,c.7]
вагонів.
1.6 Робота сортувальної станції
Утримування вагонів у технічно справному стані є основою всією експлуатаційною роботою вагонного господарства. Для цього на великих сортувальних станціях організуються ПТО вагонів, на яких проводиться робота з виявлення й усунення всіх несправностей на вагонах для забезпечення схоронності вантажів і проходження вагонів без відчеплення до місця призначення.
Сортувальна станція складається з парку прибуття, сортувального парку і парку відправлення.
На коліях парку прибуття проводиться технічний огляд вагонів у поїздах, що прибувають для розформування. Пред'явлення поїздів до огляду здійснюється оператором ПТО парку прибуття по парковому двосторонньому радіозв'язку. Оглядачі, що оглядають поїзд сходу, при виявленні несправностей чи їхніх ознак, за допомогою переносної радіостанції повідомляють про них оператору парку, називаючи номер вагона. Оператор, по двосторонньому зв'язку, повідомляє дані про отримані несправності оглядачам інших бригад для більш уважного огляду несправних вагонів.
У процесі огляду (із пролазом) оглядачі наносять на вагони у встановлених місцях чіткі крейдові розмітки, відповідно до класифікатора несправностей, і по переносній радіостанції повідомляють оператору дані відповідно до коду – номер шляху, інвентарний номер вагона, сторону складу (права чи ліва), найменування робіт і їхня кількість. Оператор одержав дані, готує дефектну відомість на вагони, у яких виявлені несправності, і до розпуску складу з гірки по телетайпу передає їх у вузловий обчислювальний центр.
На вагони потребуючі поточного відчіпного ремонту, наноситься крейдова розмітка з указівкою номера шляху сортувального парку, куди повинні надходити такі вагони. На вагони повинні виписуватися повідомлення форми ВУ – 23. На кінцевому брусі, першого з групи, вагона крейдою наноситься позначка про дату часу початку огляду, а на брусі останнього вагона – дата і час закінчення огляду. На ушкоджені вагони, що прибули з інших станцій і вимагають поточного відчіпного ремонту, оглядачі виписують повідомлення форми ВУ – 23 і оформляють акти довільної форми. Ці документи відправляються оператору ПТО.
При формуванні потягу, ЕОМ в автоматичному режимі вибирає з інформаційної пам'яті вагони несправності, що мають, і по закінченню формування складу, за 15 - 20 хвилин до його виставляння в парк відправлення, по телетайпу видає наряд, на обсяг ремонтних робіт у робоче приміщення ремонтних груп парку відправлення, а також оператору парку відправлення для планування роботи і контролю за обробкою складу. В наряді вказується порядковий номер вагона в складі, його інвентарний номер, код ремонтної групи, сторона вагона, з яким знаходиться ця несправність. Час простою складу під технічним обслуговуванням – 15 хвилин.
У сортувальному парку оглядач проводить огляд вагонів і оформлення ушкоджень у випадках їхнього виникнення в процесі розпуску із сортувальної гірки. При виявленні несправностей, що вимагають відчеплення вагона, і які усуваються без відчеплення від складу, оглядач за допомогою переносної радіостанції повідомляє оператору парку відправлення, називаючи номер шляху сортувального парку, інвентарний номер вагона, код ремонтної роботи, сторону складу, обсяг виконуваних робіт і орієнтоване місце розташування вагона в складі (хвіст, голова, середина).
У парку, суміжно зі шляхами механізованого парку поточного відчіпного ремонту, виділяються два шляхи для усунення несправностей вагонів, зазначених у додатку Б, з оформленням і видачею на них повідомлення ВУ – 23. При розпуску складу з гірки, вагони з розміткою несправностей, що вимагають відчіпного ремонту направляються на один зі спеціалізованих шляхів ремонту вагонів, на другому шляху в цей час виробляється ремонт раніше накопичених вагонів. Ремонт виконується ремонтною бригадою за допомогою ремонтних установок і інших засобів технічного оснащення.
Порядок заїзду гіркового локомотива на спеціалізований шлях, і подачі на гірку для повторного розпуску відремонтованих вагонів, визначається комплексним робочим технологічним процесом ПТО і ТРА станції.
Контроль технічного стану і ремонту вагонів у парку відправлення здійснюється комплексними бригадами відповідно до типового технологічного процесу. Ремонтні роботи в парку оправлення виконуються на підставі наряду (дефектної відомості) станції, що надходить з обчислювального центра, на телетайп, що знаходиться в робочому приміщенні ремонтних груп і оператора цього парку.
При наявності інформації про ушкодження вагонів і про несправності виявлених оглядачами при перебуванні складу в сортувальному парку, оператор коректує наряд. Після одержання наряду, оператор переконується в прийнятті його до виконання оглядачами. Бригада ремонтників приступає до усунення зазначених в наряді несправностей заздалегідь підготувавши запасні частини, механізми й інструменти. При наявності в складі чи його окремих групах великого обсягу ремонту оператор, одержавши розпорядження старшого оглядача (майстра), дає вказівку по двосторонньому радіозв'язку іншим ремонтним групам про надання допомоги в ремонті цього складу.
Вагони, включені до складу без огляду в парку прибуття, відчіплюються від складу по окремій вказівці чи оглядаються і ремонтуються у встановленому порядку.
У парку відправлення проводиться контрольний огляд і повний іспит гальм відповідно до вимог типового технологічного процесу технічного обслуговування вантажних вагонів. Така технологія дозволяє скоротити час перебування складів у сортувальному парку і парку відправлення.
1.6.1 Розрахунок робочої сили для парку прибуття
Кількість бригад парку прибуття розраховується по формулі [2,c.8]
R=п, (1.12)
де, п- коефіцієнт, що враховує переробку (розбирання) вагонів, приймаємо п=0,8;
U= Bi -середньодобова кількість прибуваючих на станцію поїздів;
Тобр - тривалість обробки складу в парку прибуття, Тобрпр =15 хв і в парку відправлення Тобротп=30 хв;
Т -тривалість робочих змін на ПТО, Т=12*60=720 хв.
Тоді:
(1.13)
вагонів.
.
Приймаємо дві бригади.
Явочна кількість працівників однієї бригади парку прибуття розраховується по формулі [2,c.8]
(1.14)
де 1,14 – коефіцієнт, що враховує непродуктивні переходи бригад [2,c.9];
Н1 – трудомісткість технічного обслуговування одного вагона в парку прибуття, Н1=2,12 чол-хв.
чоловік.
Приймаємо 10 чоловік.
1.6.2 Розрахунок робочої сили для парку відправлення
Число комплексних бригад парку відправлення визначається за формулою [2,c.8]
(1.15)
де Т2 – тривалість обробки потягу в парку відправлення, Т2=30 хв [2,с.9];
U – середньодобова кількість прибуваючих на станцію поїздів U=204.
.
Приймаємо 4 бригади.
Явочна кількість працівників однієї бригади парку відправлення розраховується по формулі [2,c.8]
,(1.16)
де Н2 – трудомісткість технічного обслуговування одного вагона в парку відправлення, Н2=4,92 чол-хв [2,с.9];
чоловік. Приймаємо 11 чоловік.
1.7 Розрахунок потреби в стиснутому повітрі і розрахунок повітропроводу
Продуктивність компресорної установки для забезпечення стисненим повітрям поїзду при одночасному іспиті гальм, визначаємо в такій послідовності [3.с.9 – 11]
Розраховується витрата повітря, м3, на нагромадження гальмової мережі усіх вагонів одного випробовуваного складу за формулою [2,с.10]:
(1.17)
де загальний обсяг гальмової мережі вантажного поїзду, м3,
;
– середній обсяг гальмової мережі чотиривісного вантажного вагона,
=0,106м3;
– найбільша кількість вагонів у поїзді, =60 вагонів;
– зарядний тиск, =0,55 МПа;
– атмосферний тиск, =0,1 МПа.
.
Визначаємо витрати повітря, м3, на нагромадження в гальмовій магістралі вантажного поїзду в період зарядки й іспиту гальм за формулою [2,с.10]:
(1.18)
де - середній темп падіння тиску повітря в магістралі потягу через витоки, МПа/хв;
- час зарядки й іспиту гальм, =15 хв.
.
Обчислюємо обсяг повітря, м3, на випробування гальмів складу:
,(1.19)
де – тиск у гальмовій магістралі загальмованого рухомого складу,
=0,37МПа.
.
Установлюємо витрату повітря, м3, на один випробовуваний склад по формулі:
,(1.20)
.
Визначаємо обсяг додаткових повітрозбірників для випробування гальм одного рухомого складу з умови, що при виключеному компресорі можна зробити зарядку й випробування гальм складу за рахунок зниження тиску в повітрозбірниках із МПа до = 0,55 МПа.
Цю умову можна виразити рівнянням [2,с.10]:
,(1.21)
деобсяг додаткових повітрозбірників, м3;
– граничний тиск у мережі і повітрозбірників, МПа;
зниження тиску в стаціонарному трубопроводі в результаті витоків через його не щільності, МПа.
З рівності обсяг додаткових повітрозбірників буде дорівнює:
,(1.22)
.
Визначаємо витрати повітря на наповнення витоків у стаціонарному трубопроводі в період іспиту гальм одного складу по формулі:
,(1.23)
.
Загальна витрата повітря на випробування гальм одного рухомого складу з урахуванням витоків у стаціонарному трубопроводі визначається по формулі:
,(1.24)
.
Продуктивність компресорної установки для забезпечення стисненим повітрям одночасного іспиту гальм заданої кількості поїздів визначається по формулі:
,(1.25)
де 1,12 – коефіцієнт, що враховує витрата повітря на нестатки контрольного пункту автогальм;
кількість одночасна випробовуваних складів, ;
об'ємний коефіцієнт корисної дії компресора, .
.
1.8 Зведений розрахунок робочої сили для ПТО
Зводимо загальну кількість робітників ПТО в таблицю 1.2
Таблиця 1.2 – Загальна кількість робітників ПТО.
Професія
Парк прибуття
Парк відправлення
Усього
1 Начальник ПТО
-
-
1
2 Оператор
1
2
3
3 Старший оглядач
1
4
5
4 Оглядач ремонтник
16
14
30
5 Слюсар по ремонту рухомого складу
-
16
16
6 Слюсар по ремонту автогальм
-
8
9
РАЗОМ
18
44
62
1.9 Заходи щодо охорони праці на ПТО
Для прискорення процесу обробки і підвищення якості підготовки поїздів у рейс повинні строго дотримуватися технологічні процеси, правила техніки безпеки і виробничої санітарії, за виконання яких несуть відповідальність начальники і головні інженери депо, начальники ПТО, майстри і старші оглядачі.
Місцеві інструкції з охорони праці затверджує начальник відділу залізниці, і вони вивішуються на робочих місцях.
Колії на яких ремонтуються вагони повинні бути обгороджені сигналами зупинки, що виключають заїзд локомотивів. Розташовані на міжпуттях парку стелажі, воздухорозбірні, змазкорозбірні і водорозбірні колонки не повинні заважати проїзду ремонтних установок і транспортних засобів. Стовпчика монтують у приямках із кришками, що закриваються, нижче рівня асфальтної доріжки. Стелажі обладнаються дверцятами, що розсовуються, і встановлюються на міжпуттях.
Забороняється оглядати і ремонтувати вагони на шляхах де проводяться маневри, а також перенесення деталей і інших предметів через шляхи під вагонами. Колії, на яких знаходяться вагони, пред'явлені до огляду, відгороджуються оператором пункту при наявності пристроїв централізованого огородження поїздів чи переносними червоними сигналами, що встановлюються на осі шляху на відстані 50 метрів від крайнього вагона.
Постановка і зняття переносних сигналів огородження чи повідомлення оператора про зняття сигналу централізованого огородження можуть бути зроблені тільки особами, на яких ці обов'язки покладені керівником зміни.
У процесі огляду і ремонту не можна пересувати вагони, а також причіпляти до них інші вагони і локомотиви.
2. Вагонне депо
2.1 Призначення та спеціалізація запроектованого депо
Проектоване вагонне депо призначено для забезпечення технічного обслуговування вантажних вагонів на заданих ділянках і виконання деповського ремонту 4-х вісних критих вагонів.
Вагонне депо є основним госпрозрахунковим підприємством вагонного господарства воно повинне забезпечувати випуск відремонтованих вагонів високої якості, відповідності з вимогами стандартів, правил, посібника з ремонту, інструктажів, технічних указівок, чи креслень нормативів.
Передбачаємо, що проектоване депо буде спеціалізуватися на ремонті 4-х вісних критих вагонів і буде розташовано на сортувальній станції.
2.2 Основи організаційно-технологічного задуму підприємства
В основу організаційно-технічного задуму закладений потоковий метод виробництва. При цьому методі враховані сучасні вимоги до організації поточно-конвеєрної лінії ПКЛ і технології виконання робіт, а також до застосовуваного устаткування. При потоковому методі виробництва виключається простій вагонів. Під кожну операцію виділяється визначена кількість часу. Визначається такт і ритм потокової лінії. Після закінчення часу роботи на одній позиції, вагони переміщаються на наступну ремонтну позицію.
Таблиця 2.1 – Організаційно-технологічний задум
Найменування етапів послідовності ремонтів
Існуюча технологія на базовому підприємстві
Утримування нового технологічного задуму
Примітка
1 Добірка груп вагонів як добове
завдання по обсягу
ремонту.
Подача вагонів зі станція примикання на шляху нагромадження маневровим локомотивом станції. Щодобова добірка старшим майстром із усього масиву вагонів добової норми і видача завдання старшому-складачу на маневрові роботи.
Маневри провадяться локомотивом депо з постановкою
вагонів на ремонтні стійла. Групування вагонів по трудомісткості не потрібно.
Подача вагонів зі станції примикання на спеціально виділені шляхи нагромадження маневровим локомотивом станції. Вагони з підвищеним обсягом ремонту подаються на зрівняльну позицію. Маневри роблять локомотивом депо. Проводиться підбір
вагонів по однаковій трудомісткості попарно.
Підбор вагонів попарно по однаковій трудомісткості проводиться за допомогою ЕОМ.
2 Очищення вагонів від залишків вантажів.
Провадиться засобами станції.
Очищення провадиться вакуумною установкою ПКБ – ЦВ.
3 Обмивка вагонів
Провадиться вручну теплою водою. Регенерація миючого засобу (розчину) не провадиться.
Робити обмивку вагонів за допомогою спеціальної мийної машини з застосуванням миючих засобів (розчинів) і їхньої регенерації. Видалення продуктів обмивки механізовано. Подача вагонів на обмивку провадиться за допомогою конвеєра.
Тип установки ММД.
4 Попередній (зрівняльний) ремонт особливо ушкоджених вагонів до середньої трудомісткості.
На базовому підприємстві не провадиться.
Зрівняльний ремонт передбачається здійснювати на окремій позиції поза головним конвеєром. Приймання виконаних робіт робить старший майстер.
На окремому стійлі в цеху поточного ремонту вагонів.
5 Розбирання вагона. Перевірка і приймання якості виконаних робіт.
Розбирання вагонів провадиться на кожнім ремонтному стійлі в наступному порядку: а)зйомка автозчеплення і фрикційного апарата; б)розбирання автогальмового устаткування. Піднімання вагона і викочування візків виконується вручну за допомогою стаціонарних домкратів вантажопідйомністю – 10т.
Транспортування деталей і вузлів у заготівельному відділенні здійснюються за допомогою електрокарів, із застосуванням ручного завантаження і вивантаження.
Передбачає розбирання вагона на окремій позиції вагоноскладальної дільниці. Для виконання робіт з розбирання передбачається вагоноремонтна машина. Транспортування знятих з вагона деталей буде провадиться транспортером. Перевірка і контроль якості розбирання вагонів у
проектованому депо передбачається впровадженням у системи управління якістю продукції, що випускається.
Тип машини УСПМ – 2.
6 Основний ремонт і зборка вагонів.
Стаціонарний метод. Транспортування знятих з вагона вузлів і деталей провадяться краном і електрокарами.
Передбачаємо потоковий метод ремонту з заміною несправних деталей і вузлів заздалегідь відремонтованими чи новими.
7 Ремонт відповідальних і спеціальних вузлів.
Зняття з вагона автозчеплення, деталей автогальмового устаткування ремонтується в цехах. Ремонт автозчеплень у відділенні ремонту автозчеплень, ремонт візків у візковому відділенні.
Передбачаємо поточно-конвеєрну лінію для ремонту візків
8 Фарбування і сушіння, нанесення трафаретів.
Фарбування вагонів провадиться за допомогою ОКУ – 3; сушіння не провадиться, нанесення трафаретів вручну – пульверизатором.
Передбачаємо для повного фарбування кузова машину ОКУ – 3. Сушіння провадиться довільно, на відкритому повітрі.
9 Приймання вагонів.
Приймає приймальник
2.3 Структура та система управління депо
Очолює вагонне депо начальник депо. Він керує всією роботою підприємства як безпосередньо, так і через своїх заступників. Начальник депо несе відповідальність за виконання задач передбачених “Положенням про вагонні депо”, законодавства, наказів і розпоряджень Укрзалізниці, керує виробничо-господарською діяльністю підприємства.
Головний інженер депо є першим заступником начальника. Він забезпечує, організовує розробку і впровадження нової техніки і прогресивної технології, механізації й автоматизації виробничих процесів, забезпечує виконання правил техніки безпеки і промислової санітарії на усіх виробничих ділянках депо.
Заступник начальника з ремонту здійснює через начальників і майстрів цехів і відділень керівництво роботою підрозділів, що виконують ремонт вагонів, ремонт і виготовлення вузлів і деталей.
Заступник начальника з експлуатації керує роботами, зв'язаними з експлуатаційною діяльністю вагонного депо. Він керує роботою ПТО, і іншими підрозділами. Виробничо-технічний відділ депо здійснює технічне керівництво ділянками і відділеннями депо, погоджує і координує роботу, розробляє технічні й організаційні заходи щодо впровадження нової техніки.
Відділ кадрів завідує підбором, оформленням прийому і звільнення працівників, організує контроль за веденням табельного обліку в цехах депо.
Бухгалтерія організує і веде бухгалтерський облік в депо, здійснює контроль за витратою матеріальних ресурсів і дотриманням фінансової дисципліни, складає бухгалтерські звіти і баланси, робить інвентаризацію основних і оборотних коштів депо і веде їхній облік.
Диспетчерський апарат депо здійснює оперативний контроль за виконанням змінних і добових завдань з ремонту вагонів, з ремонту і виготовленню запасних частин, ремонту устаткування, постачанню цехів і ділянок матеріалами і запасними частинами.
Структура керування депо зображена схематично [див. рисунок 2.1].
2.4 Генеральний план депо
На підставі розробленого технологічного задуму і структури сортувальної станції розробляємо генеральний план вагонного депо [дивись графічну частину аркуш ВЧДГ – 02011.01.00.00.СК]. Основні ремонтні заготівельні дільниці і відділення розташовані в одному корпусі. Окремо від основного корпуса розташовані котельня, трансформаторна підстанція, компресорна, склад газових балонів, адміністративний корпус, склад паливно-мастильних матеріалів (ПММ), гараж для автомобілів і мотовоза, матеріальний склад, медпункт і їдальня. Передбачено площадку очищення й обмивки вагонів.
Основні показники генплану (на основі базового депо):
площа території, виділена огородженням;
сумарна площа забудови;
коефіцієнт забудови;
довжина залізничних колій, м;
площа, зайнята залізничними коліями, м2;
довжина доріг для безрейкового транспорту;
площа зайнята дорогами для безрейкового транспорту, м2;
сумарна площа, займана площадками з навісами, площадками, які мають тверде покриття, і площадки обладнаними кранами, м2;
загальна площа зайнята під забудовою і під іншими спорудженнями, м2;
10) коефіцієнт використання території.
2.5 Режим роботи депо та фонди робочого часу
Режим роботи і фонди робочого часу відділень, устаткування і робітників визначається по наступним формулах.
Річний фонд часу явочного робітника з нормальною тривалістю робочого дня, ч,
, (2.26)
де число календарних днів у році, (2008 рік).
число неробочих днів у році,;
8,0 годин – нормована тривалість робочого дня (відповідно до
базового підприємства);
кількість днів у році зі скороченим на 1ч робочим днем, ;
година– величина скорочення часу робочого дня.
2011 годин
1
5
0
,
8
)
114
366
(
яв
F
Річний фонд робочого часу одного робітника в 2008 році Fяв=2011 годин (згідно статті в газеті „Робоче слово”).
Річний фонд часу роботи дільниці визначається по формулі.
, (2.27)
де змінність роботи дільниці.
годин
Дійсний річний фонд часу роботи устаткування:
, (2.28)
де % - коефіцієнт, що враховує втрати часу на ремонт
устаткування.
годин
2.6 Вагоноскладальна дільниця
Вагоноскладальна дільниця є головною ділянкою вагонного депо [дивись графічну частину аркуш ВЧДГ – 02011.01.00.00.СБ]. У вагоноскладальній дільниці виконуються розбірні, ремонтні, складальні і малярські роботи на вагонах. Усі роботи виконуються на відповідних позиціях головного конвеєра. Вагоноскладальна дільниця проектованого депо спеціалізується на ремонті чотиривісних критих вагонів.
Піднімання кузова ремонтуємих вагонів провадяться за допомогою стаціонарних електродомкратів. Викочування з під кузовів і підкочування під них візків провадяться за допомогою спеціальних відкаточних станцій з наступним перекочуванням їх у візкову дільницю. Для пересування вагона по позиціях застосовується конвеєр з автоматичним керуванням. Ремонтні позиції оснащені машинами портального типу УСПМ – 2 для виправлення деформованих металевих елементів рами і каркаса кузова, фарбувальною установкою ОКУ – 3 для фарбування вагонів. Робітники позначка обладнаються розподільними колонками стиснутого повітря, електролінією для живлення зварювальних апаратів.
У даному проекті, виходячи з трудоємкості слюсарних робіт по ремонту візків, використовуємо потоково-конвеєрну форму ремонту візків, тому що кількість працюючих в зміні (чотири і більше) дозволяє організувати дві або більше позицій потокової лінії і забезпечити повне завантаження обладнання.
Для переміщення піввагонів з позиції на позицію в проектованій вагоноскладальній дільниці передбачається впровадити головний конвеєр транспортуючого типу з тяговою станцією, станцією зворотного ходу і з автоматичними штовхальниками, що при переміщенні вагонів будуть взаємодіяти із середніми частинами осей колісних пар.
Усі позиції головного конвеєра обладнані спеціальними пристроями сповіщаючими оператора про закінчення роботи на даній позиції.
Графічний головний конвеєр виконаний [дивись графічну частину аркуш ВЧДГ – 02011.05.00.00.СК].
Конвеєр є головним засобом переміщення ремонтуємих вагонів по позиціям. Конвеєр обладнаний приводною станцією, лебідкою з тяговим зусиллям, приводною станцією зворотного ходу. Приводна станція змонтована в бетонованих котлованах і розміщені біля залізничних колій конвеєра.
Приводна станція робочої частини конвеєра забезпечую переміщення вагонів по позиціям потоку.
Приводна станція зворотного ходу призначена для повернення тягової конструкції конвеєра в початкове положення. Тяговий пристрій конвеєра розташований в направляючих швелерах, які утворюють напівзакритий короб, та закріплений на опорах між рейковими нитями залізничного шляху. Він призначений для захвату та переміщення вагонів конвеєра. Система управління головним конвеєром автоматична. Вся апаратура та управління конвеєром розміщується в зоні гарного огляду механізованих ліній.
2.6.1 Поточно-конвеєрна лінія ремонту 4-х вісних критих вагонів
Для переміщення вагонів з позиції на позицію на проектує мій вагоноскладальній дільниці передбачається впровадити головний конвеєр транспортуючого типу з тяговою станцією, станцією зворотного ходу і з автоматичними штовхальниками які при переміщенні вагонів будуть взаємодіяти із середніми частинами осей колісних пар.
За головним конвеєром буде спостерігати оператор, усі позиції головного конвеєра обладнані спеціальними пристроями які доповідають оператору про закінчення роботи на даній позиції. Після прийнятої всієї інформації про готовність позиції до руху конвеєра, останній буде виконувати пересування автоматично.
2.6.2 Мережовий графік технології та організації ремонту критих вагонів на потоці
Мережовий графік являє собою графічне зображення послідовності виконання комплексу робіт на потоковій лінії головного конвеєра. Він показує взаємозв'язок усіх процесів і операцій у їхній технологічній послідовності і дає можливість визначити оптимальну тривалість ремонту вагона.
Мережовий графік розроблений на весь процес ремонту вагонів від початку і до кінця з ув'язуванням усіх ділянок і відділень. Середня тривалість деповського ремонту одного критого вагона: tкр=12 годин [див. додаток В].
2.6.3 Розрахунок параметрів потокових ліній
Розрахунок проводимо згідно [3,с.18-20]. Приймаємо 1 поточно-конвеєрну лінію (ПКЛ). Потім визначаємо такт потокової лінії, хв., за формулою [3,с.10]:
,(2.29)
де річний фонд часу роботи потокової лінії, ч;
коефіцієнт, що враховує втрати робочого часу на
обслуговування робочих місць і ремонт устаткування,;
річна програма потокової лінії, ваг.
хв.
Такт потокової лінії повинний бути залежний від тривалості робочої зміни таким чином, щоб тривалість робочої зміни була величиною кратною такту, тобто дотримувалася умова:
,(2.30)
де тривалість робочої зміни;
знак цілого числа.
У тому випадку, якщо отримана величина такту не задовольняє вимогам кратності, вона коректується і приймається найбільш близької до розрахункового, але задовольняючої вимогам кратності. Після вибору величини такту коректується і план ремонту дільниці, що визначається по формулі:
,(2.31)
де кількість потокових ліній на дільниці.
ваг.
Число позицій потокової лінії визначається за формулою:
,(2.32)
де норма перебування виробу в ремонті, годин. (відповідно до мережного графіка). [див. Додаток В]
.
Приймаємо 5 – позицій.
Далі визначаються інші параметри потокових ліній по формулах:
цикл потокової лінії, хв,
,(2.33)
мін.
Ритм потокової лінії, виробів/рік,
,(2.34)
виробу/год.
Продуктивність однієї позиції в рік,
,(2.35)
ваг.
Фронт роботи дільниці,
,(2.36)
ваг.
2.6.4 Конструкторська компоновка ПКЛ
На підставі технологічного планування розробляємо конструкторське компонування головного конвеєра. Конструкторське компонування розробляється на підставі наступних розмірів: довжина вагона складає 14,7 метрів; відстань від внутрішньої стіни будинку до першого вагона – 2 метри; відстань між вагонами на позиції для викочування візків – 6 метрів; транспортний проїзд – 6 метрів; відстань від вагонів до стінок малярського відділення – 3,8 метри; відстань від осей конвеєра до стін ділянки – 5 метрів; відстань від вагона до переїзду приймаємо 3 метри.
У зв'язку з різними інтервалами між позиціями і різними довжинами позицій, розробляємо спеціальну конструкцію тягового конвеєра, штовхальники якого розташовані на різних відстанях друг від друга. Тягову станцію конвеєра розміщають поза приміщенням ділянки. Тягова станція обладнана кулачковою муфтою, що керується електрощитом. При переміщенні вагонів з позиції на позицію ця муфта забезпечує з'єднання вала редуктора з валом барабана. При зворотному ході конвеєра вона повинна відключатися. Керування муфтою забезпечується кінцевими вимикачами, на які впливає тягова конструкція конвеєра. Барабан тягової станції обладнаний стрічковим гальмом, що утримує барабан від довільного обертання під час зворотного ходу тягового конвеєра. На підставі конструкторського компонування визначаємо:
А) довжина тягової конструкції – 150000 мм.
Б) довжина робочого ходу конвеєра – 48000 мм.
На підставі ГОСТ 3241 – 80 діаметр троса для тягової станції,
мм.
Визначаємо діаметр барабана тягової станції.
Діаметр барабана повинний бути рівним не менш 20 діаметрів троса:
мм.
Кількість витків тертя приймаємо рівне, .
Відстань на барабані для закріплення троса приймаємо, мм.
Довжину барабана визначаємо по формулі:
, (2.37)
декрок намотування троса. Приймаємо ;
мм.
мм.
Визначаємо відстань між торцем тягової конструкції і віссю приводної станції:
, (2.38)
мм.
Для станції зворотного ходу приймаємо трос діаметром 13 мм. Визначаємо діаметр барабана станції зворотного ходу:
мм.
Кількість витків тертя приймаємо, витка.
Відстань на барабані для закріплення троса приймаємо, мм.
Крок намотування троса приймаємо:
, (2.39)
мм.
Визначаємо довжину барабана станції зворотного ходу по формулі:
, (2.40)
мм.
Визначаємо мінімальну відстань між торцем тягової конструкції і віссю барабана станції зворотного ходу:
, (2.41)
мм.
Визначаємо загальну довжину конвеєра:
, (2.42)
мм.
Визначаємо потужність електродвигуна тягової станції конвеєра по формулі:
, (2.43)
дестискальне зусилля: ,
дестискальне зусилля на один вагон, Н;
кількість переміщуваних конвеєром вагонів, ваг.
Н,
швидкість пересування конвеєра, м/хв;
ККД передачі, .
Вт=5,7 кВт.
Відповідно з ГОСТ-3062-80 приймаємо електродвигун типу 4А – 180М12/8/6/4У3 із частотою обертання 1000 об./хв.
Визначаємо швидкість обертання барабана тягової станції:
, (2.44)
об./хв.
Визначаємо загальне передаточне число приводу тягової станції:
, (2.45)
.
Вибираємо редуктор типу Ц2У – 160, ГОСТ – 20758 – 88 з передаточним числом .
Тоді передаточне число відкритої передачі буде дорівнює:
, (2.46)
Визначаємо потужність електродвигуна станції зворотного ходу по формулі :
, (2.47)
дестискальне зусилля, приймаємо для станції зворотного ходу в десять разів менше, ніж для тягової станції, Н;
швидкість руху конвеєра при зворотному ході, приймаємо м/хв.
Вт=14,7кВт.
Приймаємо електродвигун для станції зворотного ходу типу 4А112МВ8/6/4У3 з частотою обертання 1000 об./хв.
Визначаємо швидкість обертання барабана станції зворотного ходу по
формулі :
, (2.48)
об./хв.
Визначаємо загальне передаточне число приводу станції зворотного ходу по формулі (2.17)
, (2.49)
.
Приймаємо редуктор типу Ц3У – 200 за ГОСТ – 20758 – 88 з передаточним числом , тоді передаточне число відкритої передачі буде дорівнює по формулі :
,
.
2.6.5 Розрахунок основних розмірних параметрів вагоноскладальної дільниці
Для більшості дільниць і відділень депо основні розміри (довжина, ширина, висота) є уніфікованими і приймаються по нормах технологічного проектування вагонних депо. Основні розміри вагоноскладальної дільниці залежать від обсягу й організації виробництва, тому їх розраховують окремо для кожного конкретного випадку.
Довжина вагоноскладальної дільниці, м, при потоковому методі ремонту вагонів визначається по формулі [3,c.24]
,(2.50)
де відстань від крайньої позиції до торцевої стіни дільниці,м;
довжина ремонтної позиції, м;
ширина транспортного проїзду усередині дільниці, м;
відстань між ремонтними позиціями для викочування чи підкочування візків, м.
м.
При проектуванні вагоноскладальної дільниці повинні дотримуватися будівельні вимоги, тому отриману довжину необхідно скорегувати, з метою дотримання кратності будівельному кроку, тобто 12. Тому довжину дільниці
приймаємо 96м.
Ширина вагоноскладальної дільниці визначається по формулі [3,c.24]
,(2.51)
де відстань від осей крайніх шляхів до подовжніх стін будинку,
м;
кількість шляхів усередині вагоноскладальної дільниці;
відстань між осями суміжних шляхів на вагоноскладальній дільниці, м.
м.
Ширина вагоноскладальної дільниці з урахуванням будівельного кроку повинна бути кратна 12, тому довжину дільниці приймаємо 12 м.
Висота вагоноскладальної дільниці приймається рівної: до верха підкранової рейки – 8,6 м; до низу конструкції перекриття – 10,8 м.
2.6.6 Розрахунок робочої сили вагоноскладальної дільниці
Розрахунок робочої сили основних виробничих робітників будемо робити виходячи з програми деповського ремонту.
Явочна кількість робітників визначаємо по формулі:
, (2.52)
депрограма ремонту критих вагонів, ваг;
середня трудомісткість ремонту критого вагону чол-год;
річний фонд часу, год;
коефіцієнт росту продуктивності праці.
чол. Приймаємо 23 чоловіка.
Облікова кількість основних виробничих робітників визначаємо по формулі:
, (2.53)
де коефіцієнт примари явочної чисельності робітників до облікового,
враховуючи невиходи на роботу з поважної причини, приймаємо за даними базового депо,
чол.
Приймаємо 27 чоловік.
Таблиця 2.2– Штатна відомість ВСД
ПРОФЕСІЯ
КІЛЬКІСТЬ
1 Старший майстер
1
2 Майстер
1
3 Бригадир
1
4 Оператор
1
5 Машиніст крана
1
6 Столяр
4
7 Електрозварювач
4
8 Газорізчик
2
9 Слюсар
8
10 Маляр
2
11 Підсобний робітник
1
12 Прибиральниця
1
РАЗОМ
27
Технічна оснащеність вагоноскладальної дільниці містить у собі устаткування, необхідне для подачі вагонів у дільницю, переміщення вагонів у процесі ремонту, викочування візків, піднімання вагона, зняття і постановку автозчеплення, транспортування устаткування і запасних частин.
Таблиця 2.3 – Перелік устаткування ВСД
НАЙМЕНУВАННЯ УСТАТКУВАННЯ
КІЛЬКІСТЬ
1 Мостовий кран
2
2 Конвеєр для переміщення вагонів по позиціях
1
3 Стаціонарний домкрат, Q=10тс
12
4 Пристрій для викочування візків
1
5 Пристрій для зняття автозчеплень
1
6 Вагоноремонтна машина
1
7 Напівавтомат для зварювання
3
8 Трансформатор для ручного зварювання
2
9 Фарбувальна машина ОКУ-3
1
РАЗОМ
24
2.7 Колісно-роликова дільниця
Колісно-роликова дільниця призначена для ремонту колісних пар без зміни елементів. У колісному відділенні виконується очищення, обмивка, комплексна дефектоскопія колісних пар та деталей роликового буксового вузла. А також звичайне і повне обстеження колісних пар та проміжна і повна ревізія роликового буксового вузла..
Програма колісно-роликової дільниці визначається з умови, що на ділянку надходять усі колісні пари ремонтуємих візків, і 14% з поточного ремонту. Тоді програма визначається:
кол. пар
Згідно базового підприємства, колісні пари, що вимагають ремонту, розподіляються по видах робіт у наступному співвідношенні;
очищення від старого фарбування – 100%
обточування по колу катання – 50%
фарбування і сушіння колісних пар – 100%
Виходячи з цього програма ремонту по видах робіт складе:
кол. пар
Повній ревізії підлягають 30% від усіх колісних пар (згідно даним базового підприємства). Програма ремонту складе: кол. пар
При виконанні повної ревізії, виконується шліфування шийок осі 30% колісних пар, що надходять у ремонт (згідно з даними базового підприємства):
кол. пар
Кількість робочої сили колісно-роликової дільниці виконується в наступній послідовності:
Визначаємо явочну кількість робітників по формулі (2.38),
декількість колісних пар які підлягають ремонту за рік;
трудомісткість ремонту однієї колісної пари, чол. -год. (по даним базового підприємства);
коефіцієнт росту продуктивності праці, .
чол.
Приймаємо 8 чоловік.
Облікова кількість робітників визначається по формулі (2.53)
чол.
Приймаємо 9 чоловік.
Річна програма ремонту роликового відділення складе 2581 колісних пар, тобто 30% від колісних пар поступаючих в ремонт.
Визначаємо явочну кількість робітників необхідних для ремонту роликових букс по формулі (2.52)
де трудомісткість ремонту роликових букс, чол.год.
(по даним базового підприємства).
чол.
Приймаємо 4 чоловіка.
Облікова кількість робітників дорівнює:
чол.
Приймаємо 5 чоловік.
Таблиця 2.4- Штатна відомість колісно-роликової дільниці
Професія
Кількість чоловік
1 Майстер
1
2 Технік дефектоскопист
1
3 Токарі: а)колісно-токарський верстат
2
б)шеєчно-накатний
1
4 Слюсар по монтажу і демонтажу роликових букс
2
5Машиніст мийної машини
1
6 Прибиральниця
1
РАЗОМ
9
Застосовані устаткування і пристосування при ремонті колісних пар і їхніх вузлів заносимо в таблицю (2.5).
Таблиця 2.5– Перелік устаткування колісно-роликової дільниці
Найменування
Кіл-ть
Займаєма
площа, м²
1
2
3
1 Стенд демонтажу букс
1
104
2 Машина для обмивки й очищення колісних пар
1
10
3 Стенд для перевірки колісних пар ультразвуком
1
6
4 Стен для перевірки колісних пар магнітним контролем
1
6
5 Стенд для оптичного обмірювання колісних пар
1
6
6 Колісно-токарський верстат
2
80
7 Шеєчно-накатний верстат
1
40
8 Місткість з миючим розчином
2
2
9 Мийна машина для підшипників
1
10
10 Пристосування для зачищення зовнішніх кілець
1
3
11 Камера для нагрівання кілець
1
3
12 Стенд для комплектовки підшипників
1
5
13 Стенд для шліфування зовнішніх кілець
1
3
14 Стелаж для нагромадження підшипників
1
5
15 Мийна машина обмивки корпусів букс
1
14
16 Стелаж для інструмента
2
12
17 Пристосування для зачищення роликів підшипника
1
2
18 Стенд для монтажу роликових букс
1
65
19 Стенд проміжної ревізії роликових букс
1
40
20 Установка по наплавленню гребенів колісних пар КТ-068
1
18
21 Установка для нагрівання гребенів колісних пар КТ-066
1
6
22 Термос для остигання колісних пар після наплавлення
2
5
23 Шафа для прокалювання флюсу
1
2
24 Пристрій для перемотування дроту Св-08ХМ, Св-08Г2С
1
2
25 Пристрій для відновлення корпусів букс
1
10
26 Стелажі для ремонту
3
15
27 Пристрій для покраски колісних пар
1
3
28 Установка для очищення колісних пар
1
3
РАЗОМ
20
480
Визначаємо площу колісно-роликового відділення з урахуванням проходів і проїздів:
S =Sоб·k, ( 2.54 )
де Sоб. –загальна площа;
k-коефіцієнт враховуючий проходи і проїзди, k=2,6.
S=480·2,6=1248 м2.
В тому числі площа роликового відділення складе 235 м2.
2.8 Автогальмівне відділення
Відділення призначене для ремонту гальмового обладнання вагонів, повітророзподільників, авторежимів, авторегуляторів, ремонту і комплектовки сполучних рукавів.
Визначаємо явочну кількість робітників по формулі (2.52)
де чол-год. – трудомісткість ремонту одного комплекту автогальмового устаткування (за даними базового депо).
чол.
Приймаємо 7 чоловік.
Облікову кількість робітників розраховуємо по формулі (2.53)
чол.
Приймаємо 9 чоловік.
Таблиця 2.6 – Штатна відомість робітників автогальмового відділення
Професія
Кіл-ть чоловік
1
2
1 Бригадир АКП
1
2 Слюсар по ремонту:
а)повітророзподілювачів
3
б)авторегуляторів
2
в)сполучної арматури
1
3. Робітник відділення
2
РАЗОМ
9
Устаткування автогальмового відділення приймаємо згідно типового технологічного процесу і зводимо в таблицю 2.7.
Таблиця 2.7– Найменування устаткування автогальмового відділення
Найменування устаткування
Кіл -ть
Займаємо площа,
м²
1
2
3
1 Мийна машина
1
5
2 Стенд для ремонту й іспиту автогальм
1
8
3 Стенд для ремонту й іспиту повітророзподілювачів
1
8
4 Стенд для ремонту й іспиту гальмівних рукавів
1
4
5 Стелаж для повітророзподілювачів
2
4
6 Верстат слюсарний
2
8
7 Стелаж для деталей
2
4
8 Шафа для інструментів
2
6
9 Стенд для ремонту гальмівних циліндрів
1
6
10 Верстат для притирання деталей
1
8
РАЗОМ
14
77
Визначаємо площу автогальмового відділення з обліком проходів і проїздів по формулі (2.54)
2.9 Слюсарно-механічне відділення
Слюсарно-механічне відділення призначене для обробки продукції ковальського і електрогазозварювального відділення, а також для виготовлення нових деталей для виробничих і господарських нестатків депо.
Устаткування слюсарно-механічного відділення приймаємо згідно типового технологічного процесу і зводимо в таблицю 2.8.
Таблиця 2.8– Перелік устаткування в слюсарно-механічному відділенні
Найменування устаткування
Кіл-ть
Займаєма
площа, м²
1
2
3
1 Токарно-гвинторізний верстат
3
5
2 Верстат револьверний
1
6
3 Верстат свердлильний
2
5
4 Верстат фрезерний
2
4
5 Верстат болторізний і гайконарізний
1
2
6 Стілаж для деталей
2
2
РАЗОМ
11
45
Визначаємо площу слюсарно-механічного відділення з урахуванням проходів і проїздів по формулі (2.54)
де k-коефіцієнт урахування проходів і проїздів для слюсарно-механічного відділення,k=3,5.
Приймаємо 158 м²
Кількість робочих відділень визначаємо по кількості верстатного устаткування і зводимо в таблицю (2.9).
Таблиця 2.9– Штатна відомість слюсарно-механічного відділення
-
Професія
Кіл-ть чоловік
1 Майстер
1
2 Токар
3
3 Свердлувальник
2
4 Фрезерувальник
2
5 Слюсар
5
6 Болторізчик-гайкорізчик
1
РАЗОМ
14
Облікова кількість робітників визначаємо по формулі (2.53)
чол.
Приймаємо 16 чоловік.
2.10 Ковальсько-ресорне відділення
Ковальсько-ресорне відділення призначене для виготовлення кувань, штампів, пристосувань, а також для ремонту й іспиту пружин ресор.
Кількість устаткування ковальсько-ресорного відділення залежить від планованої річної програми ремонтного кування і вартовий продуктивності ковальських агрегатів.
Програма відділення визначається потребою у відремонтованих ресорах депо і ПТО. Нормами передбачено, що на один вантажний вагон деповського ремонту потрібно ремонт 1,2 ресор, а на поточний відчіпний ремонт 0,4 і безвідчіпний – 0,0015 ресори на 1000 вагоно-вісі.км [21].
Перелік устаткування зводимо в таблицю (2.10).
Таблиця 2.10– Перелік устаткування в ковальсько-ресорному відділенні
Найменування устаткування
Кіл-ть
Займаємо площа,
м²
1 Молот
1
2,23
2 Піч нагрівальна
1
8
3 Горн
1
1
5 Стелаж для деталей
2
2
6 Шафа для інструмента
1
3
7 Верстат слюсарний
1
2
РАЗОМ
7
20,23
Визначаємо площу ковальсько-ресорного відділення з урахуванням проходів і проїздів по формулі (2.54)
де k- коефіцієнт урахування проходів і проїздів ковальсько-ресорного відділення, k=6.
Штат робітників ковальсько-ресорного відділення [згідно типового технологічного процесу] зводимо в таблицю (2.11).
Таблиця 2.11 – Штатна відомість робітників ковальсько-ресорного відділення
Професія
Кіл-ть чоловік
1 Ковалі
2
2 Молотобійці
2
3 Машиніст молота
1
4 Підсобний робітник
1
РАЗОМ
6
Облікова кількість робітників визначається по формулі (2.53):
чол.Приймаємо 7 чоловік.
2.11 Електрогазозварювальне відділення
Відділення призначене для виготовлення нескладних конструкцій і відновлення деталей вагонів.
Устаткування електрогазозварювального відділення приймаємо згідно типового технологічного процесу і зводимо в таблицю 2.14
Апарати розподілимо по наступним дільницям та відділенням депо і ПТО у складальному-5; у візковому-3; у електрогазозварювальному-1; в інших ділянках і відділеннях депо-1.
Перелік устаткування електрогазозварювального відділення зводимо в таблицю (2.12).
Таблиця 2.12 – Перелік устаткування електрогазозварювального відділення
Найменування устаткування
Кіл-ть
Займаємо площа, м²
1 Зварювальні кабіни
1
4
2 Газозварювальні кабіни
1
8
3 Стелаж
3
8
РАЗОМ
5
28
Визначаємо площу електрогазозварювального відділення з урахуванням проходів і проїздів по формулі (2.54)
Штат робітників електрогазозварювального відділення передбачає кількість устаткування, яку зводимо в таблицю (2.13).
Таблиця 2.13– Штатна відомість електрогазозварювального відділення
Професія
Кіл-ть чоловік
1 Електрозварювач
1
2 Газозварювач
1
РАЗОМ
2
Облікова кількість працівників визначаємо по формулі (2.53)
чол. Приймаємо 3 чоловіка.
2.12 Інструментальне відділення
Відділення призначене для ремонту устаткування і пристроїв депо, для часткового виготовлення, термічної обробки, заточення, ремонту, роздачі інструменту, шаблонів і спеціальних пристосувань.
Відділення має приміщення для збереження і видачі інструменту і для його ремонту, термічної обробки і централізованого заточення.
Перше приміщення обладнується полично-клітинними стелажами, шафами, столом і пірамідами для інструменту. В другому встановлюють токарно-гвинторізний, вертикально-свердлильний, і універсально-заточувальні верстати, а також верстат для заточення різців, електропіч, слюсарний верстат, правильну плиту та ін. Перелік устаткування відділення зводимо в таблицю 2.16
Таблиця 2.14– Перелік устаткування інструментального відділення
Найменування устаткування
Кіл-ть
Займаєма
площа,
м²
1 Верстат токарно-гвинторізний
2
5
2 Верстат вертикально-свердлильний
1
6
3 Верстат для заточення різців
1
4
4 Верстат слюсарний
2
4
5 Правильна плита
1
4
6 Шафа для інструментів
2
4
7 Електропіч
1
2
8 Стелаж для інструментів
2
8
9 Стіл для інструментів
1
2
РАЗОМ
15
60
Визначаємо площу інструментального відділення з урахуванням проходів і проїздів по формулі (2.54):
Визначаємо явочну кількість робітників інструментального відділення по формулі (2.52):
чол.
Приймаємо 8 чоловік.
Облікову кількість робітників визначаємо по формулі (2.53):
чол.
Приймаємо 10 чоловік.
Штат робітників інструментального відділення зводимо в таблицю (2.15):
Таблиця 2.15 – Штатна відомість робітників інструментального відділення
Професія
Кіл-ть чоловік
1 Майстер
1
2 Бригадир
1
3 Слюсар-інструментальник
2
4 Електромонтер
2
5 Слюсар по ремонту устаткування
2
6 Інструментальник роздавальної
1
7 Електрогазозварювач
1
8 Слюсар водопровідник
1
РАЗОМ
10
Малярне відділення
Малярне відділення призначене для фарбування і сушіння зовнішніх і внутрішніх поверхонь вагона.
Розміри малярного відділення згідно з нормами технологічного проектування дорівнюють: довжина-22м; ширина-24м.
Так як для фарбування торців вагонів необхідна участь фарбувальної установки, то вона повинна ставати по торцях вагона з двох сторін. Добавляємо ще 6 м. до довжини цеха. Товщина тамбур-шлюзу дорівнює 6м. Тоді загальна довжина малярного відділення дорівнює 34 м.
Складаємо перелік устаткування малярного відділення і зводимо в таблицю (2.16).
Таблиця 2.16 – Перелік устаткування малярного відділення
Найменування устаткування
Кіл-ть
Займаємо площа, м²
1 Машина для готування фарб
1
1
2 Стелаж для фарб
2
8
3 Стіл для фарб
2
4
4 Шафа для інструмента
1
4
5 Компресор для пістолета розпилювача
1
1
6 Фарбувальна установка
3
3
РАЗОМ
10
21
Визначаємо площу малярського відділення з урахуванням проходів по формулі (2.54):
де k-коефіцієнт урахування проходів малярного відділення, k=3
Штат малярного відділення зводимо в таблицю (2.17)
Таблиця 2.17 – Штатна відомість робітників малярного відділення.
Професія
Кіл-ть чоловік
1 Маляр
6
РАЗОМ
6
Облікова кількість робітників визначаємо по формулі (2.39)
чол. Приймаємо 7 чоловік.
Деревообробна дільниця
Дільниця призначена для обробки деревини для потреб депо.
Сушіння і готування деревини проводиться в сушильних камерах. Після цього матеріали подаються для подальшої обробки.
Устаткування деревообробної дільниці приймаємо згідно типового
технологічного процесу і зводимо в таблицю 2.18.
Таблиця 2.18 – Перелік устаткування деревообробної дільниці
Найменування устаткування
Кіл-ть
Займаємо площа, м²
1 Строгальний чотирибічний верстат
1
36
2 Фрезерний верстат
1
34
3 Кругопильний верстат
1
30
4 Рейсмусовий верстат
1
34
5 Лентопильний верстат
1
25
6 Шафа для інструментів
1
4
РАЗОМ
6
163
Визначаємо площу деревообробної дільниці з урахуванням проходів і проїздів по формулі (2.54):
Штат деревообробної дільниці зводимо в таблицю (2.19).
Таблиця 2.19 – Штат робітників дільниці
Професія
Кіл-ть чоловік
1 Бригадир
1
2 Верстатник
6
3 Підсобний робітник
1
РАЗОМ
8
Облікову кількість робітників визначаємо по формулі (2.53):
чол.
Приймаємо 9 чоловік.
2.15 Комора депо
Комора депо забезпечує видачу і прийом деталей вагонів відремонтованих у депо, постачання дільниць і відділень новими запасними частинами і матеріалами.
Приміщення комори обладнано стелажами для збереження запасних частин і матеріалів.
Штат робітників комори зводимо в таблицю (2.20):
Таблиця 2.20– Штатна відомість робітників комори
Професія
Кіл-ть чоловік
1 Комірник
2
2 Підсобний робітник
6
РАЗОМ
8
Площу комори приймаємо 56м2.
Транспортне відділення
Транспортне відділення виконує операції по переміщенню ремонтуємих вагонів, навантаженню, розвантаженню сировини, матеріалів, напівфабрикатів, палива, готової продукції та ін.
Для виконання цих операцій приймаємо наступні транспортні засоби, і зводимо в таблицю (2.21).
Таблиця 2.21- Перелік транспортних засобів
Транспортний засіб
Кількість
1 Маневровий тепловоз
1
2 Автомобіль
2
3 Електрокар
2
4 Автонавантажувач
1
5 Трактор
1
РАЗОМ
7
Штат працівників транспортного відділення зводимо в таблицю (2.22).
Таблиця 2.22– Штатна відомість робітників транспортного відділення
Професія
Кількість
чоловік
1 Машиніст тепловоза
2
2 Укладач
2
3 Шофер
2
4 Водій автонавантажувача
1
5 Водій автокара
2
6 Тракторист
1
РАЗОМ
10
Облікову кількість працівників визначаємо по формулі (2.53)
чол.
Приймаємо 12 чоловік.
Візкова дільниця
Візкова дільниця призначена для ремонту візків вагонів. На дільниці виконується їхнє повне розбирання, ремонт, збірка, перевірка і фарбування.
Річна програма візкової дільниці знаходиться в повній залежності від річної програми деповського ремонту вагонів, а також вагонів поточного
відчіпного ремонту.
Річна програма ремонту візкової дільниці складе:
,
де кількість візків, що надходять в ремонт з під вагонів деповського ремонту;
кількість візків які поступають в ремонт із поточного відчіпного ремонту, 20%.
візків.
Перш ніж надійти в ремонт, візки проходять через мийну машину. Для ремонту візків передбачають поточно-конвеєрну лінію. Керує роботою цеху майстер.
Визначимо фронт роботи потокової лінії візкової дільниці за формулою [16,с.19]:
(2.55)
де tкр –час у ремонті одного візка, tкр=1,45 год.[21];
Fріч – річний фонд часу, Fріч=2011 год.;
тзм – 2 число змін.
Тоді:
≈ 3 візка
Такт роботи конвеєра визначається за формулою [16,с.15]:
(2.56)
де tпер – час пересування, tпер=1,5 хв.; Рм – кількість технологічних позицій, Рм = 6. 16 хв=0,27 год.
Визначимо проектний ритм за формулою [16,с.19]:
(2.57)
Визначимо проектну потужність КМПЛ за формулою [16,с.25]:
(2.58)
візків
Приймаємо потокову лінію з 6 технологічними позиціями
Ширина дільниці приймається 18 м, а довжина 40 м [7,с.242]:
Площа вікової дільниці 720 м2 [7,с.242]:
Визначаємо явочну кількість робітників по формулі (2.52).
чол. Приймаємо 29 чоловік.
Кількість робітників по професіях візкової дільниці зводимо в таблицю (2.23).
Таблиця 2.23– Штатна відомість робітників візкової дільниці
-
Професія
Кіл-ть
1 Майстер
1
2 Бригадир
2
3 Слюсар по ремонту візків
8
4 Слюсар по ремонту тріангелів
4
5 Електрозварювач
4
6 Оператор
2
7 Мийник візків
2
8 Токар-фрезерувальник
2
РАЗОМ
25
Устаткування візкової дільниці приймаємо відповідно до типового технологічного процесу і зводимо в таблицю (2.24).
Таблиця 2.24– Перелік устаткування візкової дільниці
Найменування устаткування
Кіл-ть
займаємо площа, м²
1 Конвеєр для ремонту візків
1
127
2 Потокова лінія по ремонту тріангелів
1
24
3 Електрозварювальне відділення з установкою для наплавлення деталей
1
10
4 Токарно-гвинторізний верстат
1
12
5 Фрезерний верстат
2
10
6 Стелаж для деталей
3
10
7 Шафа для інструментів
2
4
8 Верстат для розсверлування
1
2
9 Кран-балка
1
2
10 Камера фарбування і сушіння
1
5
11 Установка для наплавлення похилих площин КТ-008
1
6
12 Установка для фрезерування похилих площин КТ-031
1
4
13 Установка для наплавлення підп’ятникового місця над ресорної балки
1
6
14 Установка для фрезерування підп’ятникового місця над ресорної балки
1
6
15 Установка для наплавлення фрикційних клинів ВІН-1
1
4
16 Установка для відновлення бокових рам наплавленням
1
6
17 Установка для фрезерування бокових рам наплавленням
1
6
РАЗОМ
21
244
Визначаємо площу візкової дільниці з урахуванням проходів і проїздів по формулі (2.54):
2.18 Відділення по ремонту автозчеплень
Основним призначенням відділення є ремонт і комплектовка автозчеплень і поглинальних апаратів.
Програма ремонту відділення визначається проектною програмою ремонту депо і 14% від загальної кількості вагонів відчіпного поточного ремонту по одному автозчепленню.
Звідси
Nдеп = 2011*2+0,14*1000*2 =4302 автозчеплень.
З огляду на 5% негідних автозчеплень, що поступають в ремонт, маємо:
N = 4302 -(0,05*4302) = 4087 автозчеплень.
Перш ніж надійти в ремонт автозчіпний пристрій очищається від бруду та старої фарби. Для ремонту автозчеплень передбачають потоково-конвеєрну лінію. Керує роботою дільниці майстер.
Визначимо фронт роботи потокової лінії дільниці по ремонту автозчеплень за формулою [7,с.19]:
Fавт = (2.59)
Де tкр – час у ремонті одного авто зчіпного пристрою, tкр=1,65 год (за даними базового депо);
Fріч – річний фонд часу, Fріч = 2011 год;
тзм – число змін, тзм = 2.
Тоді:
Fавт = автозчепа
Такт роботи конвеэра визначаэться за формулою [7,с.15]:
Ч = (2.60)
tпер – час пересування, tпер=1 хв.;
Рт – кількість технологічних позицій, Рт=6.
Ч = 18 хв=0,3 год.
Визначимо проектний ритм за формулою [7,с.19]:
Rпркмпл = (2.61)
Rпркмпл =
Визначимо проектну потужність КМПЛ за формулою [7,с.25]:
Ν = (2.62)
Ν =
Приймаємо потокову лінію з 6 технологічними позиціями.
Ширина дільниці 24 м довжина 36 м.
Площа дільниці з ремонту автозчепу 864 м2.
Явочна кількість робітників, що необхідна для виконання програми ремонту, визначається по формулі (2.33), з огляду на те, що Н=2,7 люд-год (на основі даних базового депо):
Rяв=чол. Облікову кількість робітників визначаємо по формулі (2.34):
Rсп = 15*1,15 = 17,25 чол.
Остаточно приймаємо 17 чоловік.
Розподіляємо робітників по професіях і складаємо таблицю 2.24, устаткування відділення автозчеплення подано в таблиці 2.25.
Таблиця 2.25– Штатна відомість робочих відділення автозчеплення
Професія
Кіл-ть
чоловік
1 Майстер
1
2 Бригадир
1
3 Слюсар
4
4 Електрозварювач
4
5 Стругальник
2
6 Дефектоскопіст
1
7 Підсобний робітник
2
РАЗОМ
15
Таблиця 2.26 - Устаткування відділення автозчеплення
Найменування устаткування
Кількість
Площа, м3
Кран-балка Q = 1т
1
-
Конвейєр з ремонту автозчеплень
1
95
Фрезерний верстат
1
6
Стругальний верстат
1
5
Стенд ремонту поглинаючих апаратів
1
8
Стелаж для деталей автозчеплень
1
6
Верстат слюсарний
1
6
Стелаж для пристосувань
1
4
Настільний свердлильний верстат
1
4
Стелаж для інструмента
1
3,5
Пресс для зняття поглинаючих апаратів
1
3,5
Нагрівальна піч
1
3,5
Гідропрес для правки хвостовика
1
3,5
Установка для наплавлення
2
8
Верстат заточувальний
1
4
Разом:
161
160
Визначаємо площу відділення по ремонту автозчіплювального устрою з урахуванням проїздів і проходів по формулі (2.37)
Sавт = 160*5,4 = 864 м2.
2.18.1 Проектування дільниці по ремонту автозчеплень в об’ємі технічного проекту
На дільниці по ремонту проводиться розбирання, ремонт та складання автозчепів. Робота дільниці організовується на принципах заміни автозчепів раніше відремонтованими, чого створюється оборотний їх запас, що забезпечує своєчасну подачу справних автозчепів на позицію вагоноскладальної дільниці.
Деталі автозчіпного пристрою, які поступають в ремонт для повного огляду, очищаються від бруду та старої краски.
Після очищення деталей автозчепного пристрою піддають на конвеєрну лінію для розбирання, ремонту та складання. Всі ці операції виконують автоматично по заданій програмі.
Конверна дільниця проектуючої дільниці має вигляд металевої рами зварювальної конструкції, яка обладнана ланцюжним транспортером з електричним приводом. Лінія приводиться в робочій стан з автоматичного пульту. Всі операції виконуються на шести позиціях, на яких встановлено відповідне обладнання.
На першій позиції проводиться розбирання автозчепного пристрою потім деталі подаються на позиції де їх ремонтують, обстежують контролюють та проводять неруйнівний контроль та розробка дефектних місць.
На другій позиції проводяться зварювальні роботи. Заварювання вертикальних тріщин в зіву зверху та знизу. Заварювання тріщин в кутах вікон для замка та замкоутримувача. Заварювання тріщин перемичок між отворами для сигнального відростка замка та отвором для направляючого зуба замка. Заварювання тріщин в місцях переходу від голови до хвостовика. Постановка та приварювання нової полочки для верхнього плеча запобіжника. Приварювання нового шипа. Приварювання шайби в кармані корпусу зі сторони меншого отвору для валика підйомника. Поставнока та приварювання серповидного прилива.
На третій позиції проводиться наплавлення зношених стінок двох отворів для валика підйомника. Наплавлення опори шийки замкоутримувача на корпусі з внутрішньої сторони. Наплавлення нижньої перемички в вікні для замка та задньої похилої частини дна карману в місці опори замка. Наплавлення зношених поверхонь хвостовика, які соприкасаються з тяговим хомутом, центруючої балочки та стінами ударної розетки. Наплавлення зношених торцевих поверхонь хвостовика. Наплавлення зношених стінок овального отвору хвостовика по ширині та довжині. Наплавлення перемичок хвостовика. Наплавлення зношених тягових поверхонь малого та більшого зуба корпуса, ударної поверхні зіву. Наплавлення зношених поверхонь центруючої балочоки, маятникової підвіски, тягового хомута, упорної плити.
На четвертій позиції проводиться механічне оброблення наплавлених поверхонь деталей автозчипного пристрою. Оброблення ударних та тягових поверхонь малого та більшого зуба. Оброблення овального отвору перемичок хвостовика, стінок отвору для валика підйомника. Зачищення корпуса автозчепу після станочного оброблення, зварних швів в зіві, напливи на торці швостовика. Перевірка всіх контролюємих параметрів. Постановка клейм.
На п’ятій позиції проводиться підігрів та виправлення корпусу автозчепу та подача в камеру для подальшого остигання.
На шостій позиції проводиться неруйнівний контоль наплавлених поверхонь та складання відремонтованих частин автозчіпного пристрою.
При проектуванні дільниці по ремонту автозчіпного обладнання необхідно знати фронт роботи дільниці, такт роботи конвеєра, кількість технологічних позицій, ритм і потужність потокової лінії. В проектуючій дільниці приймаємо потокову лінію з шістьма позиціями, фронт роботи дільниці 6 автозчепів, такт роботи конвеєра 0,3 години, ритм лінії 3,3 авт/години, потужність потокової лінії 13407 автозчепів.
Згідно переліку обладнання, яке необхідне для ремонту автозчіпного обладнання визначаєио площу дільниці яка дорівнює 864 м2.
Явочна чисельність робітників дільниці 15 чоловік, а облікова 17 чоловіка, згідно розрахунку.
Робота на дільниці в 2 зміни. Згідно розрахунку крім майстра та двох бригадирів, будуть працювати 2 слюсарів по ремонту автозчепу, 2 токарів які мають право працювати на заточних, фрезерних, строгальних та токарних верстатах, 4 електрозварників,1 дефектоскопіст та 2 підсобних робітника.
Дільниця з ремонту автозчіпного обладнання, згідно норм типового технологічного процесу забезпечена слідуючим обладнанням:
Кран-балка Q = 1т
Конвейєр з ремонту автозчеплень
Фрезерний верстат
Стругальний верстат
Стенд ремонту поглинаючих апаратів
Стелаж для деталей автозчеплень
Верстат слюсарний
Стелаж для пристосувань
Настільний свердлильний верстат
Стелаж для інструмента
Пресс для зняття поглинаючих апаратів
Нагрівальна піч
Гідропрес для правки хвостовика
Установка для наплавлення
Верстат заточувальний
2.18.2 Опис роботи нестандартного устаткування
Півавтомат А-1197 для наплавлення деталей автозчіпного пристрою
Півавтомат А-1197 призначений для наплавлення постійним током в середовищі захисних газів та порошковій проволоці.
Півавтомат А-1197 складається з механізму подачи електродного дроту та шафи керування. Комплектується для зварювання:
в вуглекисломі газі – утримувачем та газовою апаратурою;
відкритою дугою – утримувачем;
під флюсом – утримувачем та бункером для флюсу.
Півавтомат комплектується візком та фігуркою для більшої кількості дроту (стаціонарний варіант), кронштейном та катушкою для меншої кількості електродного дроту (переносний варіант).
Швидкість подачи змінюється ступінчато.
Комплектується перетворювачем ПСГ-500 або випрямлечем ВС-600.
Технічна характеристика
Напруга живлячої мережі380 В
Номінальний зварювальний струм500 А
Номінальна тривалість включень (ПВ)60 %
Швидкість подачі електродного дроту580-582м/год
Діаметр електродного дроту:
Суцільної1,6-2,0 мм
Порошкової1,6-3,0 мм
Габаритні розміри:
Візка з механізмом подачи та фігуркою для
Електродного дроту:
Довжина 960 мм
Ширина 660 мм
Висота 560 мм
Кронштейна з механізмом подачі та катушкою для
Електродного дроту:
Довжина550 мм
Ширина360 мм
Висота 200 мм
Маса візка з механізмом подачі та фігуркою для
Електродного дроду35 кг
Маса кронштейна з механізмом подачі та
катушкою для електродного дроту23 кг.
Всі зварювальні і наплавлювальні роботи при ремонті автозчіпного пристрою виконуються відповідно до вимог „Інструкції по зварюванню і наплавленні при ремонті вантажних вагонів і контейнерів” ЦВ-0019.
Прес для виправлення корпусу ватозчепу
Для правлення корпусів застосовуються гідравличні преси. Прес складається з рами на якому закріплені гідравличні цілиндри, які створюють сусилля 500 кН, та горизонтальний зусиллям 250 кН. На штоках вказаних циліндрів шарнірно закріплені натисні елементи, які мають окреслення, які відповідають конструкції корпуса автозчепу в зоні виправляємих місць. Подача робочої жидкості в циліндри та виконується насосом. Резервуар служить як компенсатор для розміщення жидкості.
При правленні вигнутого корпусу автозчепу його встановлюють на профільну опору та включають насос гідропривода. Жидкость подається в вертикальний циліндр, який призначений для виправлення вигинів хвостовика в горизонтальній площині і для стискання розшириного зіву або в циліндр, який призначений для вигинів хвостовика в вертикальній площині корпусу автозчепу. Прес дозволяє проводити правлення корпусу одночасно в двох площинах в залежності від характера деформації. Після виправлення натисні елементи гідравличних циліндрів встановлюються в первинне положення, і корпус з допомогою маніпулятора виймається з пресу. При стисканні розшириного зіву між малим та великим зубом корпусу встановлюється спеціальний обмежувач.
Вигнуті деталі автозчепного пристрою перед правкою попередньо підігрівають а потім правять до розмірів, які передбачені відповідними кресленнями або шадлонами. Підігрівають корпуса автозчепу до температури 800-850 0С в газових або нафтових печах, обладнаних приборами для контролю температури. Щоби оберегти поверхню корпусу автозчепу від окислення (виникнення окалини), атмосферу в пічі підтримують відновлювальної та нейтральної. В момент закінчення робіт температура корпусу повинна бути не менше 650 0С, що визначається з допомогою оптичного прибору.
Стенд для зварювальних робіт на корпусі автозчепу
Стенд для ручної, автоматичної та півавтоматичної наплавки корпусу атозчепу складається з нерухомої рами, яка виповнена у вигляді двох вертикальних зв’язаних між собою стойок, та рухомої рами, яка складається з двох кронштейнів, які мають з однієї сторони поворотну обойму, а з другої-гайку ходового гвинта. Обертання на гвинт передається від електродвигуна через зубчату та червячну передачу. Корпус автозчепу встановлюється хвостовиком в прямокутний отвір диску поворотної рамки та закріпляються. На такому стенді можливо встановлювати корпус на необхідній висоті за допомогою електродвигуна, обертати його в вертикальній площині та навколо власної продольної осі, а також обертати на деякий кут в площині, яка приходиться через вісь кріплення поворотної рамки. Це позволяє встановлювати корпуса автозчепу в любому потрібному положенні для удобного виконання робіт. Особливо це важно при автоматичній або півавтоматичній наплавці, коли необхідно точно дотримуватися передбачених технологією кути нахилу наплавлюємих поверхонь.
Розглядуємий стенд дозволяє встановлювати корпус в поворотному диску при відсутності в кабіні зварювальника підйомноо пристрою. Корпус встановлюють вертикально хвостовиком вверх, на нього опускають рамку так, щоб хвостовик ввійшов в отвір диска та закріпляють в цьому положенні, після чого піднімають на потрібну висоту.
2.19 Відділення по ремонту дверей та завантажувальних люків 4-х вісного критого вагону
Програма відділення визначається з умови надходження в ремонт 30% дверей та 20 % завантажувальних люків. Розрахунок проводимо за умови надходження в ремонт 50% критих вагонів з 2 дверми та 50% з 4 дверми.
Nд шт.
Nд=2011*4*0,2=1609 шт.
Визначимо явочну кількість робітників за формулою, де Нт=0,7 чол-год- середня трудомісткість ремонту дверей та люків на основі базового депо.
, приймаємо 2 чоловіка.
Облікова кількість робітників визначаємо по формулі:
Rоб=2*1,15=2,3приймаємо 3 чоловіка.
Таблиця 2.27– Штатна відомість відділення по ремонту дверей та завантажувальних люків 4-х вісного критого вагону
Професія
Кіл-ть чоловік
1 Слюсар
1
2 Електрозварювач
1
3 Газорізчик
1
РАЗОМ
3
Таблиця 2.28 – Перелік устаткування відділення
Найменування устаткування
Кількість
Займаємо площа, м2
1. Прес для виправлення деталей
1
15
2. Прес-ножиці
1
10
3. Апарат зварювальний
1
4
4. Верстат слюсарний
1
10
5. Прес для виправлення люків
1
5
6. Прес для правлення дверей
1
10
Разом:
6
54
2.20 Зведений розрахунок загальної чисельності працівників депо
Загальну чисельність працівників депо зводимо в таблицю 2.29.
Таблиця 2.29 – Загальна чисельність робітників депо.
Найменування дільниці
Явочна кількість робітників
Списочна кількість робітників
1
2
3
1 Вагонозбиральна дільниця
69
79
2 Візкове відділення
25
29
3 Колісно-роликове відділення
24
28
4 Ресорно-ковальське відділення
6
7
5 Електрогазозварювальне відділення
2
3
6 Відділення ремонту автозчеплень
15
17
7 Автогальмове відділення
18
21
8 Інструментальне відділення
22
25
9 Деревообробна дільниця
8
9
10 Малярське відділення
6
7
11 Слюсарно-механічне відділення
14
16
12 Кладова депо
8
8
РАЗОМ
227
262
Чисельність адміністративно-управлінських працівників не повинна перевищувати 4% від загальної чисельності основних виробничих робітників.
чол.
Чисельність інженерно-технічних працівників, включаючи майстрів, повинна бути 6% від основних виробничих робітників.
чол.
Чисельність робітників, що обслуговують устаткування, приймаємо 6% від кількості основних робітників.
чол.
Чисельність лічильно-конторського персоналу приймаємо в розмірі 2% від основних виробничих робітників [4.ст. 266.ваг.]
чол.
Чисельність молодшого обслуговуючого персоналу визначаємо з розрахунку 2% від основних робітників.
чол.
2.21 Розрахунок санітарно-побутових і службових приміщень
Розрахунок приміщень робимо по сумарній кількості працюючих з обліком 0,3 м2 на одну людину. Гардеробні визначаємо з розрахунку кількості жінок і чоловіків. Чоловіки складають 90% від загальної кількості робітників. Звідси маємо: чол.
Жінки складають 10% від загальної кількості робітників. Звідси маємо: чол. Визначаємо площу гардеробних для чоловіків: м2.
З урахуванням проходів і місць для перевдягання площу чоловічої гардеробної приймаємо рівної, м2,
м2.
Визначаємо площу гардеробної для жінок:
м2
З урахуванням проходів і місць перевдягання приймаємо,м2,
м2.
Загальна площа гардеробної складе 90 м2.
Душові розміщені в приміщеннях суміжних з гардеробними. Розрахунок душових робимо з розрахунку установки в душових одній лейки на 10 чоловік, розмірами 0,9 м2 з урахуванням проходу через душові однієї зміни.
Чоловічі душові:
Число кабін приймаємо з розрахунку працюючих в одну зміну;
м2.
З урахуванням проходів площа чоловічих душових приймаємо, м2,
м2.
Жіночі душові:
м2.
З урахуванням проходів площа жіночих душових приймаємо, м2,
м2.
Площу туалетних приймаємо з розрахунку 1 кабіна на 25 чоловік для чоловіків і 20 для жінок. Площа однієї кабіни складає 3,5 м2.
Для чоловіків: м2.
Для жінок:
м2.
З обліком 2-х умивальників загальна площа туалетних складе 24 м2.
Площа службових приміщень приймаємо відповідно до санітарних норм проектування будівельних підприємств.
Площа службових приміщень зводимо в таблицю 2.30
Таблиця 2.30 – Площа службових приміщень
НАЙМЕНУВАННЯ ПРИМІЩЕННЯ
ПЛОЩА, М2
1
2
1 Кабінет начальника депо
30
2 Кабінет головного інженера
15
3 Кабінет заступника начальника депо
20
4 Приймальня
10
5 Кабінет голови профкому
15
6 Кабінет головного механіка
15
7 Технічний відділ
45
8 Бухгалтерія
30
9 Кабінет приймальника вагонів
15
10 Відділ кадрів
35
11 Актовий зал
160
12 Кабінет охорони праці
50
13 Медичний пункт
25
РАЗОМ
465
3. Розрахунок собівартості деповського ремонту критого вагонУ
Прямі витрати
Річний фонд заробітної плати деповського ремонту визначаємо по формулі:
, (3.1)
де середній тарифний коефіцієнт,;
річна програма ремонту вагонів;
трудомісткість ремонту одного критого вагона, чол-ч;
-годинна тарифна ставка робітника 4-го розряду, (за даними базового депо).
грн.
Додаткова заробітна плата виробничих робітників приймається в розмірі 16% від основної:
грн.
Загальна заробітна плата виробничих робітників складе:
,(3.2)
грн.
Річний фонд заробітної плати поточного ремонту складе:
грн.
Додаткову заробітну плату робітників поточного ремонту приймаємо в розмірі 20 % від основної. Вона складе:
грн.
Загальна заробітна плата робітників поточного ремонту складе:
грн.
Оплата чергових відпусток і додаткова оплата за роботу у святкові дні приймається в розмірі 7% від основної заробітної плати. Звідси маємо:
грн.
грн.
грн.
Нарахування на зарплату по соцстраху ─ 2,1%, в пенсійний фонд ─ 32,3 %, у фонд зайнятості ─1,6 %, від нещасних випадків ─ 1,7%, від загального фонду заробітної плати відчислення складуть 37,7% (за даними базового депо)
грн.
грн.
Загальний фонд заробітної плати складе:
,(3.3)
грн.
,(3.4)
грн.
Звідси основна заробітна плата всіх робітників складе:
грн.
Вартість матеріалів, напівфабрикатів і запасних частин приймаємо згідно з даними базового депо.
Таблиця 3.1 - Норми витрат і вартість матеріалів, запасних частин і напівфабрикатів
Назва
Одиниця виміру
Вартість за одиницю, грн
Норма витрат на одиницю
Витрата на рік, шт
Вартість річна, грн
1
2
3
4
5
6
1. Кільце лабіринтне
1 шт
95,6
0,03
176
16825
2. Гайка торцева
1 шт
39,2
0,05
294
11525
3. Корпус букси
1 шт
678
0,007
41
27798
4. Кришка оглядова
1 шт
141,3
0,04
235
33205
5. Кришка скріплювальна
1 шт
417
0,03
176
73395
6. Прокладка гумова
1 шт
5,76
1
5878
33857
7. Кільце гумове
1 шт
3,06
2
11756
35973
8. Автозчепка в зборі
1 шт
2787
0,03
176
490512
9. Клинок візка
1 шт
107,34
0,015
88
9446
10. Клин тягового хомута
1 шт
159,6
0,02
118
18833
11. Колодка гальмівна
1 шт
36
10
58780
2116080
12. Кран роз'єднувальний
1 шт
153,3
0,07
411
63006
13. З'єднувальний рукав
1 шт
99,6
0,5
2939
292724
14. Башмак гальмовий
1 шт
77,1
0,13
764
58904
15. Повітророзподілювач
1 шт
3897
0,06
353
1375641
16. Підвіска башмака
1 шт
86,1
0,2
1176
101512
17.Тяговий хомут
1 шт
55,5
0,05
294
163170
18. Підвіска маятникова
1 шт
36,3
0,4
2351
85341
19. Накречник триангеля
1 шт
15,78
0,08
470
7417
20. Кран кінцевий
1 шт
130,5
0,02
118
15399
21. Чека гальм. колодки
1 шт
4,61
4
14695
55547
Разом:
5086107
Матеріали
22. Сталь середньосортова
К2
2,79
10
58780
163996
23. Сталь дрібносортова
К2
3,3
6
35268
116384
24. Сталь крупносортова
К2
3,6
10
58780
211608
25. Сталь товстолистова
К2
3,82
12
70536
269448
26. Труба газова
К2
4,1
0,8
4702
19278
27. Електрод зварювальний
К2
5,2
5,2
30566
158943
28. Оліфа
К2
4,4
2,5
14695
64658
29. Фарба коричнева
К2
7,5
0,7
4115
30863
30. Фарба чорна
К2
8,33
5
29390
244819
31. Білина
К2
7,87
0,4
2351
18502
32. Балка і швелер
К2
5,25
1,9
11168
58632
Разом:
1357131
Всього:
6443238
Річна вартість основних запасних частин і матеріалів складе 6443238 грн., вартість допоміжних запчастин і матеріалів, напівфабрикатів, необхідних для потокового ремонту й облаштування підприємства, приймаємо рівним 3,5% від вартості основних [8].
Тоді:
грн.
Загальна вартість матеріалів складе:
грн.
Загально-виробничі витрати
Заробітна плата робочих, обслуговуючих устаткування.
Згідно з даними базового підприємства приймаємо, що більшість робітників, що обслуговують устаткування складає 6% від облікового складу основних виробничих робітників. Звідси маємо:
чол.
Складаємо облікову відомість робітників по обслуговуванню устаткування в депо і зводимо в таблицю.
Таблиця 3.2 – Штатна відомість робітників по обслуговуванню устаткування
Професія
Кількість робітників
Розряд робітника
Годинна тарифна ставка
Зарплата по Тарифах
Розмір доплати
Загальна зарплата
1 Слюсар по ремонту механічного устаткування
8
4
4,76
75970
11395
87365
2 Електромонтер
4
5
5,45
43491
6524
50015
3 Електрозварювач
4
4
4,76
37985
5698
43683
РАЗОМ
16
-
-
157446
23617
181063
Фонд робочого часу одного робітника в 2006 році FH =1995 годин (згідно статі в газеті “Робоче слово”).
Нарахування на зарплату по соцстраху - 2,1%, в пенсійний фонд - 32,3%, в фонд зайнятості - 1,6%, від нещасних випадків - 1,7%.
грн.
Розрахунок амортизаційних відрахувань на устаткування, пристосувань і інструмента робимо вартістю понад 500 грн. за одиницю.
Розрахунок витрат на створення амортизаційного фонду проводиться по нормах, встановлених і затверджених постановою Ради Міністрів України. Загальна вартість обладнання складе 7036000 грн. (за даними базового депо).
Сума амортизаційних відрахувань за даними базового депо складає: 7036000*0,096= 675456 (грн.)
Витрати на матеріали для утримання приймаємо в розмірі 0,5% від вартості (за даними базового депо). 7036000*0,005=35180 (грн.)
Витрати на утримання обладнання складуть 5% від вартості обладнання (за даними базового депо). 7036000*0,05= 351800(грн.)
Витрати на інструменти складатимуть 5% від вартості обладнання (за даними базового депо). 7036000*0,05= 351800(грн.)
Вартість енергоносіїв
Середня річна витрата електроенергії, що доводиться на один критий вагон деповського ремонту, визначаємо по формулі:
,(3.5)
декоефіцієнт енергоємності ремонту вагонів;
число ремонтуємих вагонів у приведених одиницях, визначаємо по формулі:
,(3.6)
де число ремонтуємих вагонів за рік.
ваг.
Звідси маємо:
квт-год/ваг.
Витрата електроенергії для деповського ремонту 5985 вагонів у рік визначаємо по формулі:
,(3.7)
квт-год/рік.
При вартості електроенергії 0,37 грн. за 1 квт-год. вартість електроенергії на ремонт вагонів складе:
грн.
Витрата електроенергії на освітлення визначаємо по нормі споживання 0,011 кВт, на 1 м2 будівлі депо, річній кількості годин освітлювального навантаження (при двозмінній роботі 2400 годин) і коефіцієнту попиту 0,8.
,(3.8)
де норма споживання електроенергії на 1 м2 площі, квт/м2;
площа приміщень, м2, м2;
освітлювальне навантаження, годин;
вартість електроенергії;
коефіцієнт попиту, .
квт/год.
Загальна вартість електроенергії по депо складе:
грн.
Витрати і вартість кисню
При деповському ремонті на один критий вагон витрачається в середньому 1,1 м3 кисню. Загальні витрати кисню складають: м3.
При вартості кисню 2,45 грн., сума на виконання програми ремонту складе: грн.
Витрати та вартість води на виробничі нестатки на підставі даних базового підприємства складе:
для обмивки вагонів – 6200 м3;
для обмивки візків – 3000 м3;
для обмивки колісних пар – 1900 м3;
Загальна витрата води складе 11100 м3.
Вартість води складає 3 грн. за 1 м3, тоді вартість води на виробничі нестатки складе:
грн.
Витрати та вартість пари на виробничі потреби, згідно даним базового підприємства, складе:
для обмивки одного вагона – 7 кг;
для обмивки одного візка – 5 кг;
для обмивки однієї колісної пари – 1,2 кг;
для обмивки букс – 1,3 кг.
Тоді витрата пари складе:
для обмивки вагонів
кг.
для обмивки візків
кг.
для обмивки колісних пар
кг.
для обмивки букс
кг.
Витрата пару для інших потреб приймаємо 48800 кг (за даними базового депо). Тоді загальна витрата пару на виробничі потреби складе:
кг.
Витрати та вартість мазуту
Для виробітку однієї тонни пару необхідно спалити 1 кг толочного мазуту. Звідси загальна витрата толочного мазуту складе:
кг.
Вартість однієї тонни толочного мазуту за даними базового підприємства 1068,1 грн. Тоді загальна вартість толочного мазуту, яка витрачається на виробничі потреби, складе:
грн./т.
Витрати та вартість газу
При деповському ремонті на один критий вагон витрачається в середньому 1 м3 газу. Звідси загальна витрата газу складе:
м3.
При вартості газу 3,1 грн. за 1 м3, вартість газу на виконання програми ремонту складе:
грн.
Витрата і вартість енергоресурсів на виробничі потреби заносимо в таблицю 3.3
Таблиця 3.3 – Витрата і вартість енергоресурсів
Найменування енергоресурсів
Витрата, кг
Вартість, грн.
1 Електроенергія, квт-г.
365216
185142
2 Вода, м3
11100
33300
3 Кисень, м3
6584
14663
4 Мазут толочний, т
241517
257964
5 Газ, м3
5985
18554
РАЗОМ
509623
Амортизаційні відрахування на виробничі будівлі і споруди
За даними базового підприємства вартість виробничих та допоміжних будівель складає 5000510 грн. (на 1.01.2006)
Амортизаційні відрахування на будівлі складає 6,25% від вартості будівлі. Звідси маємо: грн.
Витрати по охороні праці і промислової санітарії
Приймаємо з розрахунку 100 грн. на одного працюючого. Звідси маємо: грн.
Витрати на поточний ремонт будівель
Витрати на поточний ремонт будівель складають 5% від їхньої вартості. Звідси маємо: грн.
Розрахунок заробітної плати ІТП, АУР, ЛКП, допоміжних робітників
Річний фонд заробітної плати ІТП беремо за даними базового підприємства. Дані зводимо в таблицю 3.4
Таблиця 3.4 – Заробітна плата інженерно-технічних працівників
Посада
Кількість чоловік
Місячний оклад, грн
Річний фонд зарплати, грн
1 Старший майстер
1
1426
17112
2 Майстер
5
1300
15600
3 Інженер 1 категорії
2
1282
15384
4 Інженер 2 категорії
4
1185
14220
5 Інженер по нормуванню праці
1
1397
16764
6 Економіст провідний
1
1397
16764
7 Начальник сектора охорони праці
1
1397
16764
8 Інженер по охороні праці
1
1282
15384
РАЗОМ
16
-
127992
Нарахування на зарплату по соцстраху - 2,1%, в пенсійний фонд - 32,3%, в фонд зайнятості - 1,6%, від нещасних випадків - 1,7%.
Звідси маємо:
грн.
Річний фонд заробітної плати адміністративно-управлінського персоналу приймаємо за даними базового депо і зводимо в таблицю 3.5.
Таблиця 3.5 – Заробітна плата адміністративно-управлінських робітників
Посада
Кількість чоловік.
Місячний оклад, грн.
Річний фонд зарплати, грн.
1 Начальник депо
1
1961
23532
2 Головний інженер
1
1760
21120
3 Заступник начальника по ремонту
1
1754
21048
4 Заступник начальника з експлуатації
1
1754
21048
5 Начальник технічного відділу
1
1478
17736
6 Начальник відділу кадрів
1
1564
18768
7 Головний механік
1
1449
17388
8 Головний технолог
1
1478
17736
9 Помічник начальника по безпеці руху
1
1369
16428
10 Начальник гальмівно-випробувального вагону
1
1305
15660
11 Секретар
1
799
9588
РАЗОМ
11
-
200052
Аналогічно проводимо розрахунок фонду заробітної плати бухгалтерії персона. Дані зводимо в таблицю 3.6.
Таблиця 3.6 – Заробітна плата лічильно-конторського персоналу
Посада.
Кількість чоловік.
Місячний оклад, грн.
Річний фонд зарплати, грн.
1 Головний бухгалтер
1
1754
21048
2 Заступник головного бухгалтера
1
1495
17940
3 Бухгалтер 1 категорії
1
1282
15384
4 Бухгалтер 2 категорії
1
1185
14220
5 Касир старший
1
926
11112
РАЗОМ
5
-
79704
Проводимо розрахунок річного фонду заробітної плати допоміжних робітників (за даними базового депо). Дані зводимо в таблицю 3.7.
Таблиця 3.7– Заробітна плата допоміжних робітників
Професія
Кількість Чоловік
Розряд
Годинна тарифна ставка, грн.
Місячна ставка, грн.
Річний фонд зарплати, грн.
1 Слюсар інструментальник
2
6
6,40
2128
25536
2 Слюсар сантехник
2
3
4,40
1463
17556
3 Комірник
2
-
-
620
14880
4 Машиніст тепловоза
1
6
6,4
1064
12768
5 Шофер
1
-
-
780
9360
6 Машиніст крана
2
4
4,80
1596
19152
7 Водій електрокара
2
2
3,60
1197
14364
8 Електрозварювач
2
4
4,80
1596
19152
9 Столяр
2
4
4,80
1596
19152
РАЗОМ
16
-
-
12040
151920
Розраховуємо річний фонд заробітної плати для молодшого обслуговуючого персоналу. Дані зводимо в таблицю 3.8
Таблиця 3.8– Заробітна плата молодшого обслуговуючого персоналу
Професія
Кількість чоловік
Місячна ставка, грн.
Річний фонд зарплати, грн.
1 Сторож
2
650
15600
2 Прибиральниця
3
650
23400
РАЗОМ
5
39000
Нарахування на зарплату по соцстраху - 2,1%, в пенсійний фонд - 32,3%, в фонд зайнятості - 1,6%, від нещасних випадків - 1,7%.
Звідси маємо: грн.
Звідси загальний річний фонд заробітної плати ЛКП складе: грн.
Нарахування на зарплату по соцстраху - 2,1%, в пенсійний фонд - 32,3%, в фонд зайнятості - 1,6%, від нещасних випадків - 1,7%.
Звідси маємо: грн.
Загальний фонд заробітної плати АУР складе:
грн.
Розраховуємо суму відрахувань на соціальне страхування для допоміжних робітників. Нарахування на зарплату по соцстраху - 2,1%, в пенсійний фонд - 32,3%, в фонд зайнятості - 1,6%, від нещасних випадків - 1,7%.
Звідси маємо:
грн.
Загальний річний фонд заробітної плати допоміжних робітників складе:
грн.
Розраховуємо суму відрахувань на соціальне страхування для МОП. Нарахування на зарплату по соцстраху ─ 2,1%, в пенсійний фонд ─ 32,3%, в фонд зайнятості ─ 1,6%, від нещасних випадків ─ 1,7%.
Звідси маємо:
грн.
Загальної річної заробітної плати МОП складе:
грн.
Складаємо кошторис виробничих витрат і зводимо в таблицю 3.9.
Таблиця 3.9 – Кошторис виробничих витрат
Найменування витрат
Сума витрат, грн.
1
2
1 Заробітна плата виробничих робітників
1909352
2 Відрахування на соціальні потреби
719826
3 Вартість матеріалів і запасних частин
6443238
Всього:
9072416
Загально-виробничі витрати
1 Заробітна плата робочих обслуговуючих устаткування
68261
2 Амортизаційні відрахування
675456
3 Витрати матеріалу для утримування устаткування
35180
4 Витрати на ремонт виробничого устаткування
351800
5 Витрати на матеріали
351800
6 Вартість енергоносіїв
509623
Всього:
1992120
Загально-виробничі витрати не залежні від виробництва
1 Заробітна плата ІТП; АУР; СКП; МОП; допоміжних робітників
615172
2 Нарахування на соціальне страхування
231920
3 Амортизаційні відрахування на будівлі
312532
4 Вартість виробничих допоміжних будівель
5000510
5 Витрати по охороні праці
31500
6 Витрати на поточний ремонт будівель
250026
Всього:
6441660
Разом:
17506196
Собівартість ремонту вагонів
По знайдених вище даних розраховуємо собівартість ремонту вагонів. Дані заносимо в таблицю 3.10.
Таблиця 3.10 – Собівартість деповського ремонту вагонів
Найменування продукції
Річна програма ремонту вагонів
Эксплуатаційні витрати
Собівартість ремонту, грн.
Фонд Зарплати, грн.
Матеріали і запчастини, грн.
Критий вагон
5985
2524524
14981672
17506196
Найменування продукції
Річна програма ремонту вагонів
Эксплуатаційні витрати
Собівартість ремонту, грн.
Фонд Зарплати, грн.
Матеріали і запчастини, грн.
Критий вагон
5985
422
2503
2925
Далі розраховуємо прибуток, що одержить наше підприємство від ремонту вагонів. Відділення дороги планує прибуток вагонному депо в розмірі 15,5 % від експлуатаційних витрат. Звідси маємо: грн.
Далі розраховуємо вартість основних фондів і оборотних коштів, що рівні вартості устаткування і будівель: грн.
Вартість оборотних коштів складає 20% від вартості основних фондів. Звідси маємо:
грн.
Далі розраховуємо рентабельність проектованого депо. Рівень загальної рентабельності розраховуємо по формулі:
,(3.9)
.
Усі приведені вище розрахунки дозволяють говорити про те, що проектоване вагонне депо є прибутковим і рентабельним підприємством на залізниці.
4. Розрахунок економічної ефективності впровадження розроблених пропозицій
Розрахуємо економічний ефект від впровадження стенду для зварювальних робіт на корпусі автозчепу.
До впровадження стенду для зварювальних робіт на корпусі автозчепу зварювальні роботи проводили на стенді, який мав гірші технічні показники в зв’язку з цим витрачувалося набагато більше часу на виконання зварювальних робіт.
Розрахуємо економічний ефект від впровадження стенду для зварювальних робіт на корпусі автозчепу по формулі (2.41-2.43).
Такт роботи конвеєра визначається за формулою [7,с.15]:
Ч =
Де tкрі – час у ремонті одного авто зчіпного пристрою,
tкр=1,65 год після впровадження стенду,
tкр=2,0 год до впровадження стенду, (за даними базового депо); tпері – час пересування ковеєра, tпер=1 хв. після впровадженні стенду;
tпер=1,5 хв. при до впровадження стенду
Рт – кількість технологічних позицій, Рт=6.
До впровадження стенду: Ч = 22 хв=0,37 год.
Після впровадження стенду: Ч = 18 хв=0,3 год.
Визначимо проектну потужність ПКЛ за формулою (2.43), [7,с.25]:
До впровадження стенду: Ν до =
Після впровадження стенду: Ν після =
Визначимо економічний ефект за формулою:
Є=Nпісля*С-Nдо*С, (4.1)
де С-прибуток від ремонту одного автозчепу, С=360 грн.
Тоді:
Є=13300*100-10784*100=251600 грн.
Виходячи з розрахунку бачимо, що економічний ефект від впровадження стенду для зварювальних робіт на корпусі автозчепу складає 251600 грн.
5. Методи та обладнання неруйнівного контролю автозчіпного прИстрою
Деталі автозчіпного пристрою в процесі експлуатації сприймають різні навантаження. Тому при плановому виді ремонту крім перевірки геометричних розмірів деталей автозчіпного пристрою необхідно проводити неруйнівний контроль деталей автозчіпного пристрою а саме:
корпусу автозчепу;
клину тягового хомута;
тягового хомута;
стяжного болта поглинального апарату;
маятникової підвіски.
Неруйнівний контроль виконується магнітним та вихрострумовим методом.
При магнітному неруйнівному контролі корпусу автозчепу, клина тягового хомута, тягового хомута, стяжного болта поглинального апарату та маятникової підвіски застосовується магнітний дефектоскоп МД-12ПШ, МД-12ПС при вихрострумовому ВД-12НФ або ВД-30НК.
6. Пошкодження та несправності автозчіпних пристроїв в експлуатації
Огляд та перевірка авто зчіпного пристрою при перемичному ремонті рухомого складу гарантує надійний роботу в міжремонтні строки. Отже в експлуатації можливі випадки пошкодження. Крізь мірного зносу деталей, проявлення дефектів виготовлення, які можуть визвати порушення нормальної дії авто зчіпного пристрою, а при визначних несприятливих умовах привести до саморозчепу автозчепу або злому окремих деталей. Саморозчеп на шляху слідування інколи приводить до набігання відчепленої частини рухомого складу, а злом-до падіння на колії, в слідстві чого можливий сход рухомого складу з рельс.
Найбільш частіше зустрічається несправність це недіючий запобіжник від саморозчепу. Надійність дій запобіжника від саморозчепу визначається розміром вертикального зачеплення противовісом верхнього плеча запобіжника в зчепленому стані.
Велику роль для надійної дії автозчепу має зазор між торцями верхнього плеча запобіжника та прововісами замкоутримувача, визначаючий вільне переміщення замка при включеному запобіжнику. Цей зазор характеризує роботу механізма автозчепу при зчепленні. Зноси торця верхнього плеча запобіжника та торця противовіса, отвору запобіжника та шипа замка, а також вигини замкоутримувача та запобіжника приводить до збільшення зазору. Це може визвати опереження включення запобіжника. В такому випадку відбудеться вигин або злом деталей запобіжника пристрою і, як слідство, саморозчеп в результаті часткової або повної втрати вертикального зачеплення.
В експлуатації також зустрічаються випадки зносу шипа (на конус) для навішування замкоутримувача. Тоді замкоутримувач, спада з шипа, притискається до замка, останній втрачає рухомість і замкоутримувач приймає положення, при якому противовага буде піднятий вище полочки для запобіжника. В процесі зчеплення відбудеться опереження включення запобіжника.
Саморозчепи автозчепів можуть виникати не тільки в наслідок несправності деталей, та і по іншим причинам. Так коротка ціп розчіпного приводу при стисканні поглинального апарату, а також при значному боковому відхиленні автозчепу на кривій повертає валик підйомника. Підйомник який знаходиться на квадратній частині валика, широким пальцем піднімає нижне плече запобіжника в результаті чого верхне плече вище противоваги замкоутримувача, тобто запобіжник від саморозчепу виключиться.
7. Вентиляція і освітлення виробничих об’єктів
Розглянемо види вентиляції і освітлення які використовують на залізничному транспорті і які ми можемо застосувати у відділенні по ремонту візків для даного дипломного проекту.
Призначення і класифікація промислової вентиляції
Промислову вентиляцію застосовують для технічних цілей у різних технологічних процесах і для забезпечення встановлених санітарними нормами метеорологічних параметрів і чистоти повітря в приміщеннях.
Вентиляція забезпечує повітрообмін у приміщенні, видаляє забруднене і подає свіже повітря. По способу переміщення повітря розрізняють природну і штучну вентиляцію. Обидва цих виду вентиляції можуть застосовуватися в сполученні (змішана вентиляція).
Вентиляцію називають природною, якщо повітрообмін у приміщенні здійснюється за рахунок теплового і вітрового напорів. При механічній вентиляції повітрообмін здійснюється вентиляторами.
Вентиляція буває приточною, витяжною і приточно-витяжною. Приточна призначена для організованої подачі чистого повітря в приміщення, витяжна – для видалення з нього забрудненого повітря. По місцеві дії вентиляцію підрозділяють на загальну обмінну і місцеву. Загальна обмінна вентиляція призначена для забезпечення в робочій зоні приміщення умов, що відповідають санітарним нормам. Дуже важливо не дати шкідливим домішкам поширитися по всьому приміщенню і видалити їхній безпосередньо від місця виділення. Цій меті служить місцева витяжна вентиляція, що локалізує. У ряді випадків застосовують подачу чистого повітря в робочу зону – місцеву приточну вентиляцію. Прикладом служать повітряні душі, що влаштовуються на робочих місцях при значних тепловиділеннях.
Місцеву вентиляцію застосовують у сполученні з загально обмінною як штучною, так і природною.
Змішані системи місцевої механічної і природній загально обмінної вентиляції знаходять широке застосування у великих цехах з локальними виділеннями шкодливостей.
Місцевий отсоси для видалення вибухонебезпечних і пожаронебезпечних газів і парів проектують індивідуальними для кожного приміщення і кожної одиниці устаткування.
При загально обмінній штучній вентиляції забруднене повітря необхідно видаляти з тих місць, де спостерігаються найбільші концентрації шкідливих речовин. У випадку застосування приточної вентиляції повітря подають у робочу зону при наявності теплонадлишків чи будь-яких шкідливих виділень і у верхню зону – при їхній відсутності.
Системи штучної вентиляції складаються з вентиляторів, воздуховоду, воздухозабірних і повітророзподільних пристроїв. Для підігріву повітря застосовують калорифери, а для його очищення – фільтри.
Вентилятори служать для переміщення повітря. Збудником руху повітря у вентиляторах служить робоче колесо, що укладене в кожух, що визначає напрямок руху.
Воздухозабірні пристрої являють собою прості конструкції в зовнішніх стінах, що закриваються жалюзійними ґратами, чи шахти виведені на дах будинку і прикриваються зверху ковпаком від атмосферних опадів.
Воздухозабірні пристрої усередині виробничих приміщень вибирають з урахуванням ефективного видалення ними шкідливих речовин у місцях їхнього найбільшого скупчення. Вони виконуються у виді розтрубів-відводів із сітками, витяжних тумбочок, вікон із сітками у воздуховодах.
Повітророзподільні пристрої повинні забезпечувати рівномірну роздачу свіжого повітря в робочу зону приміщення. До цих пристроїв відносяться різні конусні, сітчасті, жалюзійні насадки, тумбочки пристінного типу.
Повітря, подаваний у приміщення, у холодний час року підігрівають у калориферах. Їх застосовують у системах вентиляції і кондиціонування повітря, а також у системах повітряного опалення й у сушильних установках.
Калорифер складається з трубок гладких чи з тонкими сталевими пластинами. Трубки розташовують у шаховому порядку і пропускають по них теплоносій – воду чи пару. Повітря, проходячи між трубками нагрівається.
Види і системи освітлення
У залежності від природи джерела світлової енергії розрізняють природне, штучне і сполучене освітлення.
Природне освітлення підрозділяють на бічне (одне чи двох стороннє), коли світло проникає в приміщення через світлові прорізи в зовнішніх стінах; верхнє, здійснюване через ліхтарі і світлові прорізи в покрівлі; верхнє і бічне, що сполучить верхнє і бічне освітлення.
Сполучене освітлення застосовують у приміщеннях з недостатнім природним світлом, що доповнюється електричними джерелами світла, що працюють не тільки в темний але й у світлий час доби.
Штучне (електричне) освітлення по характері виконуваних задач поділяють на робоче, аварійне, евакуаційне, охоронне і чергове.
Робоче освітлення влаштовують у всіх приміщеннях, а також на відкритих територіях, призначених для роботи, проходу людей і рухи транспорту.
Аварійне освітлення передбачають на випадок, коли припинення чи порушення нормального обслуговування устаткування в слідстві виходу з ладу робочого освітлення може викликати пожежу, чи зривши отруєння людей, тривале порушення технологічного процесу, відмовлення в роботі зв'язку, тепло – чи електропостачання, каналізації, небезпека травмування.
Евакуаційне освітлення виконують у місцях, небезпечних для пересування людей, в основних проходах і на сходових клітках будинків, у яких працює більш 50 чоловік, а також у приміщеннях, вихід людей з який при аварії висвітлення зв'язаний з небезпекою травмування.
Охоронне освітлення влаштовують уздовж границі площадок підприємств, охоронюваних у нічний час.
По конструктивному виконанню розрізняють дві системи електричного освітлення – загальне і комбіноване.
При загальному освітленні всі робочі місця в приміщенні освітлюються від загальної освітлювальної установки. Якщо до загального освітлення додають місцевий зосереджений світловий потік безпосередньо на робочих місцях, то таке освітлення називають комбінованим. Одне місцеве освітлення до застосування не допускається, тому що викликає необхідність частої періадаптації зору, створює глибокі і різкі тіні, небезпеку травмування.
При визначенні вимог, пропонованих до освітлення, виходять з основних властивостей зору, що припускає створення умов, що виключають стомлення зору і виникнення причин виробничого травматизму, що сприяють підвищенню продуктивності праці.
Освітлювальні установки повинні забезпечувати:
достатню яскравість робочої поверхні чи при визначеному коефіцієнті відображення її достатню освітленість;
достатню рівномірність розподілу яскравості (чи освітленості) на робочій поверхні;
відсутність глибоких і різких тіней на робочих поверхнях, а також на підлоги, у проходах, міжколійях, міжвагонних просторах;
відсутність у поле зору спостерігача великих яскравостей;
сталість освітленості робочої поверхні в часі.
Розрахунок освітлення горизонтальних поверхонь при відсутності великих предметів, що затемнюють, провадиться різними методами:
1)методом коефіцієнта використання світлового потоку;
2)метод питомої потужності;
3)крапковим методом.
Найбільш розповсюдженим у проектній практиці є розрахунок освітлення по методу коефіцієнта використання світлового потоку.
Цей метод дає можливість визначити світловий потік ламп, необхідний для створення заданої чи освітленості при заданому потоці знайти освітленість. Метод застосовується для розрахунку повного освітлення при горизонтальній робочій поверхні з урахуванням світла, відбитого стінами і стелею.
Світловий потік лампи розраховується по формулі [6,c.1]
, (7.1)
дезадана мінімальна освітленість, лк;
коефіцієнт запасу, уводять для компенсації зниження освітленості від напилювання перекриттів приміщень і світильників і від старіння ламп у міру експлуатації освітлювальної установки, ;
освітлювана площа, м2 (відділення по ремонту автозчеплень);
відношення середньої освітленості до мінімального. Для ламп накалювання , для ламп люмінесцентних - ;
число світильників;
коефіцієнт використання світлового потоку в частках одиниці, тобто відношення світлового потоку, що подає на розрахункову поверхню, до сумарного потоку.
Для визначення коефіцієнта знаходиться індекс приміщення і приблизно оцінюються коефіцієнти відображення поверхонь приміщень, стелі, стін, розрахункової чи поверхні підлоги. Коефіцієнти відображення приймаємо рівними 0 [6,додаток 9]
Індекс знаходиться по формулі [6,c.2]
, (7.2)
дедовжина приміщення;
розрахункова висота;
ширина приміщення.
.
лк.
Приймаємо лампу типу ЛД40 – 4 ДСТ 6825 – 70 потужністю 40 Вт, напругою на лампі 103 В, струм лампи 0,43 А, діаметр 40 мм, довжина зі штирками 1213,6мм без штирків – 1199,4мм, світловий потік, лк, після 100 годин горіння – 2225 [6,додаток 10].
8. Охорона навколишнього середовища на залізничному транспорті
Охорона навколишнього середовища, раціональне використання природних ресурсів, забезпечення екологічної безпеки життєдіяльності людини – невід'ємна умова постійного економічного і соціального розвитку України.
З цією метою Україна здійснює на своїй території екологічну політику, спрямовану на збереження безпечного для існування живої і неживої природи навколишнього середовища, захисту життя і здоров'я населення від негативного впливу, обумовленого забрудненням навколишнього середовища, досягнення гармонійної взаємодії суспільства і природи, охорону, раціональне використання, і відтворення природних ресурсів.
За екологічні правопорушення, тобто за порушення природоохоронного законодавства України, недотримання правил і норм, заподіяння шкоди навколишньому середовищу і здоров'ю людей, особи несуть дисциплінарну, адміністративну, карну, матеріальну відповідальність, а підприємства й організації – адміністративну і цивільно-правову відповідальність відповідно до природоохоронних законів.
Вплив об'єктів залізничного транспорту на природу обумовлено будівництвом доріг, виробничо-господарською діяльністю підприємств, експлуатацією залізниць і рухомого складу, спалювання великої кількості палива й ін.
Забруднення від об'єктів залізничного транспорту накладаються на фонові забруднення від господарсько-побутової, культурної виробничої діяльності суспільства, від об'єктів теплоенергетики, промисловості й інших видів діяльності. Часто в районах станцій і вузлів залізниць фонові забруднення рівні чи перевищують припустимі норми.
Будівництво і функціонування залізниць вимагає вилучення з природного середовища землі, ґрунтів, флори, фауни, ландшафту. Об'єкти залізничного транспорту споживають воду, паливно-енергетичні і мінеральні ресурси.
Також навколишнє середовище забруднюється викидами, стоками, відходами.
Фактори впливу об'єктів залізничного транспорту на навколишнє середовище класифікуються по наступним ознаках:
механічні (тверді відходи, механічний вплив на ґрунти будівельних, дорожніх, шляхових і інших машин);
фізичні (теплові випромінювання, електричні полючи, шум, вібрація);
хімічні речовини (кислоти, солі, лугу, фарби і розчинники, антисептики для шпал), що підрозділяються на надзвичайно небезпечні, високо небезпечні, небезпечні і малонебезпечні;
біологічні (макро і мікроорганізми, бактерії, віруси).
Ці фактори можуть діяти на природне середовище довгочасно, порівняно недовго, короткочасно і миттєво.
На залізничному транспорті використовуються виробничі, перевізні й інші процеси, що по своєму призначенню можна об'єднати в наступні групи:
використовувані при будівництві і ремонті залізничних колій, станційних споруджень, інженерних комунікацій і інших пристроїв;
застосовувані при ремонті і технічному обслуговуванні рухомого складу, виробничого устаткування, технічних систем автоматики, зв'язку і сигналізації, а також при виробництві нових виробів;
використовувані при переробці, навантаженні, транспортуванні і вивантаженні вантажів.
Основними напрямками зниження екологічної небезпеки виробничих процесів варто вважати застосування раціональних видів сировини і матеріалів, зниження витрати природних ресурсів, упровадження замкнутих, безвідхідних і маловідходних технологій, зниження витрати матеріалів, води, енергії, палива на одиницю готової продукції. Обсяг водоспоживання не повинний порушувати природних процесів у водоймах. Скидання стічних вод у водойми допускається тільки після їхнього очищення до рівня не робить вплив на стан живих організмів у воді.
Технологічні процеси по можливості повинні забезпечувати високий коефіцієнт використання сировини, мінімальна безповоротна витрата води і повітря, споживати раціональна кількість енергії, передбачати заміну природної сировини на синтетичне. Також треба домагатися скорочення викидів, стоків і шкідливих випромінювань.
Виробниче устаткування повинне мати екологічну безпеку, витрачати раціональна кількість енергії, води, повітря, палива, мати пристрою аварійної зупинки при виході на аварійний режим роботи.
Найбільш забруднююче навколишнє середовище процесом є мийка ремонтуємих виробів, при якій у стічні води потрапляють нафтопродукти, поверхово активні речовини, різні солі і кислоти. Миючі розчини забруднюють ґрунт і повітря. Для забезпечення екологічності процесу мийки необхідні замкнуті системи використання миючих розчинів, і ефективна вентиляція з пристроями уловлювання аерозолей. Не допускається влучення їх у ґрунт.
При розбиранні рухомого складу найбільше важливо забезпечити схоронність і повторне використання деталей після їхнього відновлення різними ресурсосберігаючими методами. При одержанні заготівель деталей куванням і штампуванням необхідно виключити вплив вібрації на конструкції будинків, щоб не викликати руйнувань, захистити навколишніх від шуму, викидів пилу, газів; забезпечити охолодження устаткування водою по замкнутому циклі; не допустити контакту нагрітих виробів з пальними речовинами; передбачити засоби очищення викидів в атмосферу і стоків у водойми.
При термічній обробці деталей варто виключити утворення вибухонебезпечних концентрацій газів і пар, зменшити теплові й іонізаційні випромінювання, очистити стоки від хімічних і механічних забруднень.
У виробничих процесах зварювання і наплавлення варто передбачити засоби захисту навколишнього середовища від світлових, теплових, іонізаційних випромінювань, створити замкнуті системи водокористування і системи рекуперації повітря, використовуваного в зварювальних установках.
Механічна обробка деталей супроводжується утворенням великої кількості стружки, яку необхідно брикетувати і використовувати для переплавляння. Мастильно-охолодні рідини варто використовувати по замкнутому циклі з періодичною їх очищенням і регенерацією.
При фарбуванні виробів варто використовувати методи, що знижують витрату лакофарбових матеріалів, не допускати в приміщеннях і у вентиляційних системах утворення вибухонебезпечних концентрацій пар розчинників, очищати викиди в атмосферу від лакофарбових матеріалів, використовуючи різні типи гідрофільтрів, передбачати допалювачі пальних складових лакофарбових матеріалов.
Екологічність виробничих процесів забезпечується обґрунтованим вибором виробничих площадок; вибором виробничого устаткування; раціональним розміщення будинків, споруджень, енергетичних установок, інженерних комунікацій і доріг; створенням пристроїв очищення викидів в атмосферу і стоків у водойми; скороченням витрати природних і енергетичних ресурсів; створенням засобів захисту від шуму, вібрації, теплових, електромагнітних, радіоактивних і інших видів випромінювань.
Одним з напрямків рішення задачі заощадження природних ресурсів є заміна диференційованої системи і споживання на інтегровану ерготехнічну схему, що дозволяє вести виробництво більш ощадливо, безпечно і безвідходно з використанням енергетичних ефектів. Змінюються і принципи створення нових виробничих систем завдяки використанню багатоцільових виробництв, що володіють меншою громіздкістю, більшою екологічною безпекою, меншим споживанням сировини й енергії. У багатоцільових виробництвах легше здійснювати синхронізацію процесів, їхнє рівномірне завантаження, кооперацію і взаємодію, зменшувати вплив на природу за рахунок розробки і впровадження безвідхідних і маловідхідних технологій.
Список використаних джерел
1. Технологічний процес технічного обслуговування вагонів на сортувальній станції з використанням спеціалізованих колій для поточного отцепочного ремонту та АСУ ПТО.
2. Горбенко А.П. Розрахунок пункту технічного обслуговування вантажних вагонів на ЭОМ “Іскра – 266”. – Харьків.: ХІІЗТ, 1987.
3. Вагонне господарство. Методичні вказівки для студентів спеціальності “Вагонобудівництво та вагонне господарство”. - М.: ВЗІІЗТ – 1989.
4. Гридюшко В.Н., Бугаєв В.П., Криворучко Н.З. Вагонне господарство. – М.: Транспорт, 1988.
5. Руденко Н.Ф. Курсове проектування грузових машин. – М.: Машинобудівництво, 1976.
6. Ножевников А.М. Поточно-конвейерні лінії ремонту вагонів. – М.: Транспорт, 1980.
7. Норми технологиічного проектування депо для ремонту вантажних та пасажирських вагонів. – М.: Транспорт, 1987.
8. Сібарова Ю.Г. Охорона праці на залізничному транспорті. – М.: Транспорт, 1981.
9. Гуревич М.Л., Каленіченко Л.Н. Дипломне проектування. Методичні вказівки (инженерні методи расррахунку штучного освітлення ). – Харьків.: ХІІЗТ, 1972.
10. Конструювання та розрахунок вагонів: Підручник для вузів залізничного транспорту/ Під. ред. В.В Лукіна. – М.: УМК РФ, 2000
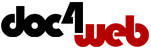
Нравится материал? Поддержи автора!
Ещё документы из категории транспорт :
Чтобы скачать документ, порекомендуйте, пожалуйста, его своим друзьям в любой соц. сети.
После чего кнопка «СКАЧАТЬ» станет доступной!
Кнопочки находятся чуть ниже. Спасибо!
Кнопки:
Скачать документ