Технологический процесс ремонта маховика двигателя ЯМЗ-238ФЕ
Министерство образования и науки РФ
Федеральное агентство по образованию
Федеральное государственное образовательное
Учреждение среднего профессионального образования
Астраханский автомобильно-дорожный колледж
производственный ремонтируемый деталь прочность
Курсовой проект
По ремонту автомобилей
Тема проекта "Технологический процесс ремонта маховика двигателя ЯМЗ-238ФЕ"
Разработал
Студент группы 4251
Аадк 51СД 04 КП 055
Ветлугин Ф.С.
Проверил
Стукалов А.П.
Астрахань
2010г.
Содержание
1. Введение
2. Расчет размера производственной партии ремонтируемой детали
3. Разработка технического процесса ремонта детали
3.1 Характеристика ремонтируемой детали и условия ее работы
3.2 Выбор способа ремонта детали
3.3 Выбор установочных баз
3.4 Схема технических процессов восстановления
3.5 Составление планово-технических операций
4. Разработка технических операций ремонта деталей
5. Расчет норм времени технических операций ремонта деталей
6. Техническая документация на технический процесс ремонта деталей
7. Конституционная часть
7.1 Описание его конструкции приспособления и его техническая характеристика
7.2 Расчет на прочность наиболее ответственной части деталей приспособления
7.3 Порядок применения приспособления и меры безопасности при работе с ним
Заключение
Список литературы
1. Введение
Ремонт автомобилей является объективной необходимостью, которая обусловлена техническими и экономическими причинами.
Во-первых, потребности народного хозяйства в автомобилях частично удовлетворяются путем эксплуатации отремонтированных авто.
Во-вторых, ремонт обеспечивает дальнейшее использование некоторых элементов авто, которые не полностью изношены.
В-третьих, ремонт способствует экономии материалов, идущих на изготовление новых авто. При восстановлении деталей расход металла в 20….30 раз ниже, чем при их изготовлении. Увеличение масштабов производства авто приводит к росту абсолютного объема работ.
Техническое совершенство авто с точки зрения их долговечности и простоте ремонта должно оцениваться не с позиции возможности исправления и восстановления изношенных частей, а с позиции необходимости создания автомобилей, требующих при ремонте лишь мало трудоемких разборо-сборочных работ, связанных со сменой взаимозаменяемых быстро изнашиваемых деталей и узлов. В последние годы наметилась тенденция ограничения малоэффективного капитального ремонта (КР) и увеличения доли амортизационных отчислений, выделяемых на замену изношенного и морально устаревшего оборудования машин. Многочисленные исследования показывают, что первый КР , как правило, это все слагаемые экономических затрат общественного труда, выгоднее приобретения новой машины. Это объясняется двумя обстоятельствами:
-фактические затраты на первый КР большинства видов машин и оборудования обычно не превышает 30-40% балансовой стоимости, повторные же ремонты обходятся значительно дороже; большинство видов машин подвергаются первому КР, как правило, до наступления морального износа. Перспектива должна быть в том, чтобы автомашина подвергалась КР за весь срок службы, только один раз. Авторемонтные предприятия, получив значительное развитие, еще не в полной мере реализуют свои потенциальные возможности. По своей эффективности организационного и технического уровня оно все еще отстает от основного производства автомобилестроения. Качество ремонта остается низким, стоимость высокой, уровень механизации достигает лишь 25-40%, вследствие чего производительность труда в два раза ниже, чем в автомобилестроении. Авторемонтные предприятия (АРП) оснащены ,в основном, универсальным оборудованием большой степени изношенности.
Эти негативные стороны современного состояния авторемонтного производства и определены пути его развития. Огромные потенциальные возможности кроются в организации и внедрении агрегатного и узлового методов ремонта. Применение этих прогрессивных норм организации ремонтного обслуживания автомобилей позволяет полнее использовать ресурс агрегатов и деталей, сократить простои в работе, значительно повысить срок службы автомашин и агрегатов до КР и это, в свою очередь, ведет к сокращению общего количества КР. Важным элементом считается создание необходимой технической базы, которая предопределяла бы внедрение прогрессивных форм организации труда, повышения уровня механизации работ , оборудования, сокращение затрат труда и средств производства. Анализ практики показывает, что структура ремонтной базы автомобильного транспорта должна состоять из предприятий трех типов соответствующих уровню технической сложности выполняемых ремонтных работ:
-мастерские АТП, выполняющие мелкий ТР без разборки агрегатов;
- базы централизованного наиболее сложного текущего ремонта.
- заводы по КР агрегатов (автомобилей), организацией которых должен быть обязательный капитальный ремонт.
Целью данного курсового проекта является разработка технологического процесса ремонта маховика.
2. Расчет размеров производственной партии ремонтируемой детали
Количество деталей в партии определяется по формуле:
n = Ni * np /253
где n –количество деталей в партии;
Ni- количество деталей заданного наименования по годовой программе выпуска;
пp- коэффициент ремонта ( из задания);
253 – количество рабочих дней в году.
N′ =N * m,
где N – заданная программа ( из задания); N =4000.
M – количество деталей заданного наименования у одного автомобиля, m = 1.
N′ = N * m = 4000 * 1 = 4000 (деталей).
n = 4000 * 0,25 / 253 = 3,95 (дет.)
3. Разработка технологического процесса ремонта детали
3.1 Характеристика ремонтируемой детали и условия ее работы
Маховик служит для обеспечения равномерной работы двигателя, вывода поршней из мертвых точек, облегчая пуск двигателя и движения автомобиля с места. Для пуска двигателя стартером на маховик по окружности напрессован зубчатый венец. Маховик относится к деталям класса "диски с гладким периметром". Изготовлен маховик из чугуна марки С4 18-36.
При передачи крутящего момента на ведомые элементы присутствует сила трения.
Трущиеся поверхности изнашиваются, главным образом, при относительном их проскальзовании, сопровождающийся при этом вибрацией деталей. Разрушительным фактором при работе маховика является трение и вибрация.
3.2 Выбор способа ремонта детали
Изношенную или поврежденную резьбу ( более двух ниток) в отверстиях маховика заваривают и рассверливают. После зачистки наплавленного металла до уровня основного сверлят отверстие, зенкеруют фаску и зенкеруют отверстия на определенную глубину и нарезают резьбу в соответствии с размерами на рабочем чертеже.
Глубокие риски, задиры и выработку на рабочей поверхности маховика устраняют точением до размера не менее установленного техническими требованиями.
3.3 Выбор установочных баз
Установочными базами при механической обработке маховика служат, как правило, наружные или внутренние цилиндрические поверхности и торец.
3.4. Схема технологических процессов
Дефекты
Способ устранения
№ операции
Наименование и содержание операции
Установочная база
1-я схема: срыв резьбы в отверстии крепления сцепления
2-я схема: износ торцевых поверхностей, установка ведомого диска сцепления
Нарезание новой резьбы
Протачивание
1
2
3
4
5
6
1
Сверлильная
Сварочная
Токарная
Сверлильная
Сверлильная
Сверлильная
Токарная
Торец
Наружные цилиндрические поверхности, торец,
Наружные цилиндрические поверхности, торец.
Наружные цилиндрические поверхности, торец
3.5 Составление плана технологических операций восстановления деталей
4. Разработка технологических операций ремонта деталей
4.1 Составление развернутого операционного плана
4.1.05. Сверлильная 1.
(рассверлить отверстие крепления маховика )
1.Установить маховик на станок.
2. Рассверлить отверстие.
3. Снять деталь со станка.
4.1.10. Сварочная.
(заварить отверстие крепления маховика).
1.Подготовить поверхность под сварку.
2. Заварить отверстие.
1. 4.1.15. Токарная 1
(снять наплавленный металл отверстия до уровня основного).
1. Установить маховик на приспособление.
2. Установить приспособление с маховиком на станок.
3. Произвести расточку наплавленного металла отверстия крепления маховика.
4. Снять приспособление с маховика.
5. Снять маховик с приспособления.
4.1.20. Токарная 2
(расточить торцевую поверхность под установку маховика).
1. Установить маховик на приспособление.
2. Установить приспособление с маховиком на станок.
3. Расточить торцевую поверхность маховика под установку сцепления.
4. Снять приспособление с маховиком.
5. Снять маховик с приспособления.
4.1.25. Сверлильная 2
(рассверлить отверстие маховика под установку сцепления).
1. Установить маховик на станок.
2. Рассверлить отверстие.
3. Снять деталь со станка.
4.1.30. Сверлильная 3
(зенкерование фаску отверстия крепления маховика).
1. Установить маховик на станок.
2. Зенкерование фаски.
3. Снять маховик со станка.
4.1.35. Сверлильная 4
(нарезать резьбу в отверстии крепления маховика).
1. Установить маховик на приспособление.
2. Установить приспособление на тиски.
3. Нарезать резьбу.
4. Снять приспособление с маховиком.
5. Снять маховик с приспособления.
4.1.40.Заключительный контроль.
4.2 Определение принципов обработки деталей
4.2.05.Сверлильная 1
(рассверлить отверстие под установку маховика).
1.Рассверлить отверстие до диаметра Ø 10 мм.
4.2.10. Сварочная
(заварить отверстие крепления маховика).
1.Заварить отверстие диаметром Ø10мм длиной ℓ =40 мм.
4.2.15. Токарная 1
(снять слой наплавленного металла с отверстий крепления сцепления).
1. Произвести расточку наплавленного металла с отверстия крепления маховика до уровня основного.
4.2.20. Токарная 2
(расточить торцевую поверхность под установку маховика).
1. Расточить торцевую поверхность под установку маховика от диаметра d = 17,2мм до диаметра d =17,5 мм. £ = d d = 17,5 – 17,2 = 0,3 мм при ℓ = 150 мм.
4.2.25. Сверление 2
(рассверлить отверстие маховика под установку сцепления)
1.Рассверлить отверстие под установку маховика до диаметра Ø 6,8 мм.
4.2.30. Сверлильная 3
(зенкеровать фаску отверстия крепления маховика ) .
1.Зенкеровать фаску отверстия крепления маховика под углом 45о на глубину ℓ =2 мм.
4.2.35. Сверление 4
(нарезать резьбу в отверстии крепления маховика).
1. Нарезать резьбу в отверстии крепления маховика.
4.20.40. Заключительный контроль.
4.3 Составление развернутого операционного плана с промежуточными размерами
4.3.05. Сверлильная 1
(рассверлить отверстие крепления маховика).
1.Установить маховик на станок.
2. Рассверлить отверстия с резьбой диаметра Ø 10 мм.
3.Снять деталь со станка.
4.3.10. Сварочная
(заварить отверстие крепления маховика).
1. Подготовить поверхность под сварку.
2. Заварить отверстие диаметром Ø 10 мм длинной ℓ = 40 мм.
4.3.15. Токарная 1
(снять наплавленный металл отверстия до уровня основного).
1. Установить маховик на приспособление.
2. Установить приспособление с маховиком на станок.
3. Произвести расточку наплавленного металла отверстия крепления маховика до уровня основного.
4. Снять приспособление с маховиком.
5. Снять маховик с приспособления.
4.3.20. Токарная 2
(расточить торцевую поверхность под установку маховика).
1. Установить маховик на приспособление.
2. Установить приспособление с маховиком на станок.
3. Расточить торцевую поверхность под установку сцепления от диаметра d = 17,2 мм до диаметра 17,5 мм, £= d – d = 17,5 -17,2 = 0,3 мм при ℓ = 150 мм.
4. Снять приспособление с маховиком.
5. Снять маховик с приспособления.
4.3.25. Сверлильная 2
(рассверлить отверстие маховика под установку сцепления).
1. Установить маховик на станок.
2. Рассверлить отверстие под установку сцепления до диаметра Ø = 6,8мм.
3. Снять деталь со станка.
4.3.30. Сверлильная 3.
(зенкеровать фаску отверстия крепления маховика ).
1. Установить маховик на станок.
2. Зенкеровать фаску отверстия крепления сцепления под углом 450 на глубину ℓ =2мм.
4.3.35. Сверлильная 4
(нарезать резьбу в отверстие крепления маховика).
1.Установить маховик на приспособление.
2. Установить приспособление на тиски.
3. Нарезать резьбу .
4. Снять приспособление с маховиком.
5.Снять маховик с приспособления.
4.3.40. Заключительный контроль.
4.4 Выбор оборудования и технологической оснастки
4.4.05. Сверлильная 1
(рассверлить отверстие крепления маховика).
Оборудование:
Вертикально-сверлильный станок модели 2 А 135.
Техническая характеристика:
1. Наибольший диаметр сверления, мм -35.
2. Наибольший ход шпинделя, мм -225.
3. Вылет шпинделя, мм -300.
4. Ход салазок шпинделя, мм -200.
5. Число оборотов шпинделя в минуту : 68 ;100;140;195;275;400;530;750;1100.
6. Подачи шпинделя в мм/об : 0,115;0,15;0,2; 0,25;0,32;0,43;0,57;0,725;0,96;1,22.
7. Рабочая поверхность стола 450х500 мм.
8. Мощность электродвигателя, кВт =4,5.
9. Габаритные размеры станка, мм от 1240 х 810 х 2560.
10. Масса станка, кг - 1550.
4.4.10. Сварочная
(заварить отверстие крепления маховика).
Оборудование:
Полуавтомат А-547 У (проволока ПАНИ-11).
4.4.15. Токарная 1.
( снять наплавленный металл с отверстия до уровня основного).
Оборудование:
Токарно-винторезный станок модели 1М 63.
Техническая характеристика:
1.Наибольший диаметр обрабатываемой детали
над станиной , мм ,630
над суппортом, мм, 350
2. Наибольший диаметр круга, обрабатываемого в патроне, мм, -65.
3. Расстояние между центрами, мм,1400.
4. Шаг нарезаемой резьбы, мм, 192.
5. Диаметр отверстия шпинделя, мм 70.
6. Метрический конус отверстия шпинделя, мм, 80.
7. Наибольшее перемещение суппорта продольного, мм, 350.
8. Наибольшее перемещение суппорта поперечного, мм, 110.
9. Наибольшее перемещение верхних салазок, мм – 200.
10.Сечение державочной части резца , мм, 30 * 40.
11.Конус морзе отверстия, мм, - 5
12.Число оборотов шпинделя в минуту – 10;12,7;16,5;20,4;25,5;59,9;40,8;51,0;
63,7;79,7;102;128;163;206;255;319;408;510;635;816;1020;1250. 13 Продольная подача суппорта , в мм на один оборот шпинделя, - 0,070,074;0,084;0,097; 0,11;0,12;,013;0,14;0,15;0,17;0,195;0,21;0,23;0,26;0,28;0,3;0,34;0,39;0,43;0,47;0,52;0,57;0,61;
0,7;0,78;0,84;0,95;1,04;1,71;1,4;1,56;1,74;1,9;2,08;2,28; 2,42;2,8;3,12;5,48;3,8;4,16.
14.Поперечные подачи суппорта: -0,035;0,037;0,048;0,042;0,055;0,06;0,065;0,07;0,074;
0,084;0,097;0,11;0,12;0,13;0,14;0,15;0,17;0,195;0,21;0,23;0,26;0,28;0,30;0,34;0,39;0,43;0,47;
0,52;0,57;0,6;0,7;0,78;0,87;0,95;1,04;1,14;1,71;1,4;1,56;1,74;1,9;2,08.
15. Мощность электродвигателя , кВт= 19.
Приспособления:
Приспособление для закрепления маховика на станок.
Инструмент: рабочий- резец.
4.4.20. Токарная 2
(расточить торцевую поверхность под установку маховика).
Оборудование : смотреть п.4.4.15.
Приспособление6 смотреть п.4.4.15.
Инструмент: смотреть п.4.4.15.
4.4.25. Сверлильная 2
(рассверлить отверстие маховика под установку сцепления).
Оборудование: смотреть п.4.4.05.
Инструмент: сверло Ø 6,8 мм.
4.4.30. Сверлильная 3.
Оборудование : смотреть п.4.4.05.
Инструмент : зенкер.
4.4.35. Сверлильная 4. (нарезать резьбу в отверстие крепления маховика).
Оборудование: тиски слесарные.
Приспособление: приспособление для закрепления маховика на станок.
Инструмент: рабочий 6 метчик, вороток.
4.4.40. Заключительный контроль.
4.5 Разработка каждой технической операции
4.5.05.Сверлильная 1. (рассверлить отверстие крепления маховика).
1.Установить маховик на станок
__
__
__
__
__
2. Рассверлить отверстие
Торцевая поверхность
Ø 10
0,63
9
__
3. Снять маховик со станка
__
__
__
__
__
5. Расчет норм времени технических операций ремонта детали
Сверлильная работа 1.
1. t = Дов –d /2 = 12 -10 /2 = 1 (мин).
Подачу принимаем из данных станка 0,96.
1.2. Основное время.
То = Z /n * S = ℓ + ℓ1 + ℓ2 / n * S ; мин. [ 3 ]
где: ℓ - толщина маховика, ℓ =40 мм;
ℓ1 = 3 мм – толщина;
ℓ2 = 3 мм – толщина
n =140 об/мин.частота вращения шпинделя;
S = 0.96 мм/об подача инструмента.
То = (40 + 3+ 3) / (140 * 0,96) = 0,34 мин.
1.3.Вспомогательное время на установку и снятие детали.
Тв = Тв1 +Тв2 *12 , мин. [ 3 ]
12- количество отверстий маховика.
Тв1 = 2.1 – вспомогательное время на установку и снятие детали берется
по таблице №63 [3];
Тв2 =0,2 – вспомогательное время ( примечание к таблице №63).
Тв = 2,1 + 0,2 * 12 = 27,6 мин.
1.4. Оперативное время
Топ = То +Тв = 0,34 +2,76 = 27,94 мин. [3 ]
1.5.Дополнительное время
По таблице №65 берем Т доп. в % к оперативному времени и получаем его равным 3.9.мин.
1.6. Подготовительно-заключительное время берем по таблице №66 [ 3].
Т пз = 8 мин.
1.7. Штучное время
Тш = То =Т доп = 0,34 + 3,9 = 4,24 мин . [ 3]
Тш – штучное время.
1.8.Калькуляционное время.
ТК =( ТПЗ / q ) + ТШ ; мин. [ 3]
где , q – количество деталей в партии.
ТК = 8/4 + 4,24 = 6,24 мин.
1.9. Норма времени
ТН = ТО + ТВ + ТДОП + ТПЗ/ n ; мин. [ 3]
ТН = 0,34 + 27,6 + 3,9 + 8/140 = 31,9 мин.
2.Электродуговая сварка и наплавка.
2.1. Основное время.
ТО = (60 * Q * A * m)/ (L *Y) * n ; мин. [ 3]
где, Q – масса наплавленного металла Г;
А =1,2 – поправочный коэффициент на длину шва берется из табл .№ 182 [ 3];
т =1 –поправочный коэффициент на положение шва в пространстве,
берется из табл. № 183;
L – коэффициент наплавки (г/а*ч); берется их табл № 184 [ 3]; L = 6,5.
Y – величина сварочного тока , Y = 150;
Длина электрода равная 4.
Q = F *Z * γ [ 3]
определяем по формуле: F – площадь поперечного сечения шва, см2 , берем из табл. №185 [ 3];
F= П R2 = 3,14 * 0,05 =0,008;
Z –длина шва 40 см;
γ – плотность наплавленного металла, электрода, г/см2, берется из таблицы №186 [ 3],
γ =7,1.
Q = 0,008 * 40 * 7,1 = 2,3.
ТО = (60 * 2,3 * 1,2 *1) /(6,5*150) = 0,17 мин.
2.2.Вспомогательное время.
ТВ = ТВ1 + ТВ2 + ТВ3 ; [ 3] ;
где, ТВ1 – время связанное со свариванием шва, мин, 0,9- берется из таблицы №188 [ 3] ;
ТВ2 = 0,1 – повороты и снятие деталей вручную, мин., берется по табл. №189 [ 3] ;
Т В3 = 0,9 + 0,4 + 0,3 = 1,3 мин.
2.3. Оперативное время.
ТОП = ТО + ТВ = 0,17 + 1,3 = 1,47 мин. [ 3]
2.4. Дополнительное время.
Дополнительное время составляет в среднем 10% от оперативного времени и определяется по формуле 1.
Т ДОП = (ТО + ТВ) * 10 / 100 = (0,17+1,3)* 10/ 100 =0,147 мин.[3 ]
2.5. Подготовительно-заключительное время.
ТПЗ = 5 мин., берется по табл. №191.
2.6. Норма времени.
ТН = ТО + ТВ + ТДОП + ТПЗ / п;
3. Нормирование токарных работ 1.
3.1.Основное время.
ТО = Z *i / n * S , мин. [ 3]
где , Z – расчетная длина обработки, мм, - 30;
n - частота вращения шпинделя, 100 об/мин, берется из данных по станку;
S – подача инструмента, 0,2 мин/об, берется из данных по станку;
i – число проходов -1.
ТО = 30 * 1 / 100 * 0,2 = 1,5 мин.
3.2. Вспомогательное время.
ТВ = Т В1 + ТВ2 [3];
где, ТВ1 = 0,9 – вспомогательное время на установку и снятие изделия,
мин., по табл. №22 [3];
ТВ2 = 0,5 – вспомогательное время, связанное с проходом, мин., по табл. №24,[3 ].
ТВ = 0,9 + 0,5 = 1,4.
3.3. Оперативное время
ТВ = ТО + ТВ = 1,5 + 1,4 = 2,9 мин. [3]
3.4. Дополнительное время в % от оперативного времени:
ТДОП = ТОП * К / 100, мин. [3] ,
где К- коэффициент , берется из табл. № 25, К = 6,5.
Т ДОП = 2,9 * 6,5 / 100 = 0,2.
3.5. Подготовительно-заключительное время при токарной обработке, в мин.
ТПЗ =13 мин., берется по табл. №26 [3] .
3.6.Норма времени.
ТН = То + Тв + Тдоп + Тпз/ п; мин., [3].
Тн= 1,5 + 1,4 +0,2 + 13 /100 = 3,23 мин.
4.Токарная 2.
4.1. Основное время.
То = Z*i /n*S,
где, Z – расчетная длина обработки, мм, - 82;
i –число проходов, -1;
п – частота вращения шпинделя, 100 об/ мин., берется из данных к станку;
S – подача инструмента, 0,2 мм/об., берется из данных к станку.
То = 82,*1 / 100*,02 =4,1 мин.
4.2. Вспомогательное время.
Тв = Тв1 +Тв2 , мин., [3].
Тв1= 0,9 – на установку и снятие изделия, мин., берется по таблице №22;
Тв2 =0,5 – связанное с проходом, мин., берется по табл. №24.
Тв= 0,9 +0,5 = 1,4 мин.
4.3. Оперативное время.
Топ = 4,1 + 1,4 = 5,5 мин.,[3.]
4.4.Дополнительное время в % от оперативного времени.
Тдоп = Топ *К / 100, мин., [3];
К- коэффициент, берется по табл.№25; К=6,5;
Тдоп= 5,5 *6,5 /100= 0,36 мин.
4.5. Подготовительно-заключительное время при токарной обработке берется
по табл. №26 [3], Тпз= 13 мин.
5. Нормирование сверлильных работ 2.
5.1. t = Дов / 2= 10/2 =5; подача , принимается из данных станка – 1,22.
5.2. То = l+ l1+ l 2 / n * S; мин., [3];
где, l – толщина маховика, 40; l1 = 3 мм, толщина; l2= 3 мм, толщина.
п = 100 об/мин – частота вращения шпинделя берется из данных станка;
S = 1.22 – подача инструмента, мм/об, берется из данных станка.
То = 40 + 3 + 3 /100 *1,22 = 0,38 мин.
5.3. Вспомогательное время.
Тв = Тв1 + Тв2 *12;
12- отверстий маховика;
Тв1 = 2,1 – вспомогательное время ( примечание к табл.№63 [3]);
Тв = 2,1 +0,2 +*12 =27,6
5.4.Оперативное время.
Топ = То + Тв =0,38 + 27,6 = 28 мин.,[3]
5.5.Дополнительное время.
По таблице №65 берем Тдоп в % к оперативному времени и получаем : Тдоп = 3,9.
5.6. Подготовительно-заключительное время берется по табл. №66; Тпз =* мин.
5.7. Штучное время.
Тм =То + Т доп = 0,36+ 3,9=4,26 мин. [3]
5.8. Калькуляционное время
Тк = Тпз / q + Тш; мин., [3 ];
Тк = 8/4 +4,26 = 6,26.
5.9. Норма времени
Тн = То +Тв + Т доп + Тпз/п; мин. [3]
Тн = 0,8 + 27,6 + 3,9 + 8 / 100 = 31,96 мин.
6.0. Нормативно слесарные работы.
6.1. Неполное оперативное время определяется по табл. Т ноп =30 мин.
Время нарезания 4,7 мин., т.к. работаем двумя метчиками
Т ноп * 0,7 = 30 * 0,7 = 21 мин.
6.2. Оперативное время.
Топ = Тноп + Тв [3]
где, Тв – вспомогательное время на установку 0,9, берем по табл. №245 [3]
Топ = 21,+ 0,9 = 21,9 мин.
6.3. Подготовительно-заключительное время берется по табл. №246; Тпз = 3.
6.4. Штучное время.
Тш = Тосн + Твсп + Тдоп = Топ + Тдоп ;
Дополнительное время составляет 8% от оперативного и определяется по формуле 1.
Тдоп= 8%, от Тдоп = Топ * 8 /100 = 21,9 * 8 /100 = 1,76,
Тш = 22+1,8=23,8 мин.
6.5. Калькуляционное время.
Тк = Тпз / q + Тш мин, [3],
где q – количество деталей в партии ,4.
Тк = ¾ + 24 = 24,75 мин.
7. Конструкторская часть
По сравнению с ранее применявшейся в АТП приспособлениями разработанная мною конструкция приспособления обладает следующими преимуществами:
* простое изготовление не требует дефицитных материалов и дорогостоящего оборудования и специалистов второй квалификации для изготовления;
* надежно фиксируется;
* хорошо центруется;
* не требует больших физических усилий исполнителя при работе;
* не требует большого ухода при шлифовании.
Расчет.
G = N /A≤[g ]
дополнительное напряжение.
Отлив из серого чугуна марки С418-36
n = g пред / g ≥ [n] – коэффициент запаса прочности
∆l = Fl / (ЕН) = 1кГс /9,8Н /1Т = 103 кГс;
4ОТ = 40 * 103 кГс = 40 * 103 9,8Н = 392000кН.
Призма приспособления для правки маховика изготовлено из стали ГОСТ 380-71.
При проведении проверочного расчета необходимо определить наибольшее расчетное напряжение, которое необходимо сравнить с допустимым и определить, отвечает ли данное приспособление необходимым требованиям. Условие прочности при :
G = N / A ≤ l [g]
имеет вид
n = σпред / ≥ [n]
Маховик устанавливается на призме крайними опорными гайками. На маховик действует пресс с максимальной нагрузкой 40т. Нагрузка делится на две призмы поровну, поэтому в расчетах будет рассчитываться только одна призма.
Переведем нагрузку с 40 т в н.
40т = Р = 40 * 103 кГс = 40 * 103 * 9,8 н = 392000н = 392 кн
Так как нагрузка от пресса распределяется примерно поровну, то максимальную нагрузку на призму поделим на 2:
F / 2 = 392 кн/ 2 = 196 кн
При нагрузке 30 т правка будет проходить в оптимальном режиме.
Рабочая нагрузка будет:
30*103 кГс ≤ 30 * 103 * 9,8н ≤ 294000≤ 294 кн
Нагрузку на одну призму: 294 /2 = 147000н;
N≤F
Находим площадь поперечного сечения призмы:
А= а* b =80 * 16 = 12,8 см2
[g] - допустимое напряжение для ВТ 5 при вжатии равно 170 Мпа.
Находим расчетное напряжение в наиболее опасном сечении:
g = N / A =(147 * 103 ) / 12,8 *10 -4 = 115 Мпа.
g [g] – условие прочности.
Найдем расчетный коэффициент запаса прочности при сжатии и сравним его с нормативом.
n = gпред / ω ≥ [n];
gпред = (196 * 130 ) / (12,8 * 10-4)≤ 153 Мпа.
n = 153/115=1,4 – коэффициент прочности для пластичного материала составляет оптимальное значение.
7.3.Правила применения приспособления при выполнении работ.
Перед применением приспособления необходимо его тщательно осмотреть и убедиться в технической исправности.
После этого необходимо произвести регулировку. После окончания работ очистить приспособление и рабочую поверхность от загрязнений.
Проверить надежность крепления всех его частей, при необходимости подтянуть их крепления. Также необходимо найти укорочение призмы при сжатии пол формуле Гука.
∆lст = Fl / ЕА
Е – модуль продольной упругости;
Е = 2 * 105 МПа по табл. 2.1.
L – длина;
F – сила;
А – площадь поперечного сечения в наиболее опасном месте;
∆lст = 147 * 103 * 0,76 * 10-3 / 2 * 105 * 12,8 * 10-4 = 0,4 мм -
укорочение не существенно, им можно пренебречь.
Вывод: приспособление работает в оптимальных условиях.
Заключение
В данном проекте рассматривается вопрос разработки технологического процесса ремонта маховика двигателя ЯМЗ-236 в условиях авторемонтного предприятия с годовой производственной программой КР.
Во втором разделе проекта произведен расчет производственной партии ремонтируемых деталей за один день работы АРП.
В следующем разделе проекта произведена разработка технологических операций для восстановления детали в условиях АРП.
В четвертом разделе проекта произведена разработка технологических операций для восстановления детали в условиях АРП.
В пятом разделе произведен расчет норм времени на выполнение технологических операций по восстановлению детали с разными дефектами.
В следующем разделе мною выполнена технологическая документация на технологический процесс восстановления детали в виде марки двух операционных карт и двух карт эскизов.
В последнем разделе проекта мною разработана конструкция недорогого и надежного для ремонта маховика двигателя ЯМЗ-236, произведен расчет прочности наиболее нагруженных деталей приспособления, дано описание правил его применения и мер безопасности при его работе с ним.
Исходя из вышеизложенного считаю, что цель, поставленная в задании на курсовой проект, выполнены в целом на достаточно высоком техническом уровне.
Список литературы
1. Дюмин И.Е. "Ремонт автомобилей", М., транспорт, 1998г.
2. Мельников Т.Н. "Ремонт автомобилей и деталей", "Методика выполнения курсового
проекта" ,Н.Новгород, РЗАТТ, 1999 г.
3. Рурвич И.С. " Методика технического нормирования в ремонтном производстве",
Росто-Дон, 1986 г.
4. Кребатов Б.В. "Ремонт автомобилей" М.Транспорт,1974г.
5. Краткий автомобильный справочник ИИАТ,М.Транспорт,1984г.
6. Малышев А.Т. Справочник "Технология авторемонтного производства",
М.Транспорт, 1977г.
7. Суханов Б.Н. " ТО и ремонт автомобиля, пособие по курсу и дипломному
проектированию",М. Транспорт, 1985г.
8. Балабанов А.Н. "Краткий справочник технолога машиностроения".М.,
Издательство стандартов, 1992г.
9.ОРЛОА п.н. "Краткий справочник металлов" М., Машиностроение, 1987г.
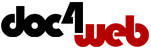
Нравится материал? Поддержи автора!
Ещё документы из категории транспорт :
Чтобы скачать документ, порекомендуйте, пожалуйста, его своим друзьям в любой соц. сети.
После чего кнопка «СКАЧАТЬ» станет доступной!
Кнопочки находятся чуть ниже. Спасибо!
Кнопки:
Скачать документ