Устройство автомобиля
1. Структура автомобильного парка РФ
Структура автомобильного парка РФ в зависимости от типа автомобиля выглядит следующим образом: в целом по России, на долю легковых автомобилей приходится не менее 80% от общей численности автомобильного парка Доля грузовых автомобилей составляет примерно 13%. Автобусов в России значительно меньше - около 2% от общей численности авт-го парка. Москва и Московская область лидируют по количеству автомобилей среди регионов РФ. В структуре автомобильного парка г. Москва несколько больший удельный вес имеет доля легкового автотранспорта – 87 % и в тоже время, меньше доля грузового автотранспорта - 8%, а также доля прочих автотранспортных средств - только 3% (РФ - 5%). Примерно такая же диспропорция характера для парка автомобилей Санкт-Петербурга и других городов с населением более миллиона человек.
Первенство столицы России обусловлено большой концентрацией легковых автомобилей, доля которых превышает в общей численности автопарка страны. Ежегодно численность автомобилей в столице увеличивается, как минимум на 10%, и, по-видимому, эта тенденция сохранится на ближайшие годы. Некоторые эксперты прогнозируют снижение темпов прироста парка автомобилей - как в Москве, так и в России в целом (до 4-6% в год).
2. Основные тенденции развития конструкций автомобилей
Конструкции автомобилей непрерывно совершенствуются. Тенденции развития конструкций автомобилей обусловлены как экономическими так, так и социальными причинами. Экономические причины определяют тенденцию повышения топливной экономичности как легковых, таки и грузовых автомобилей, что в настоящее время стало одним из ведущих направлений современного автостроения. Социальными причинами обусловлена тенденция повышения безопасности автомобилей. Автомобиль – объект повышенной опасности. Поэтому необходимо совершенствование активной и пассивной безопасности автомобиля. Автомобиль является источником загрязнения окружающей среды отработавшими газами(окись углерода, окислы азота). Это определяет непрерывное повышение требований экологической безопасности автомобиля. Следует также отметить тенденцию автоматизации управления автомобилем, которая обеспечивается современными средствами электронной, микропроцессорной техники и направлена на повышение топливной экономичности и динамики автомобиля (управление двигателем и трансмиссией), активной безопасности (управление тормозной системой), комфортабельности (управление подвеской и др.) Автомобильный транспорт явл-ся одним из основных потребителей нефтяного топлива, поэтому в результате энергет-го кризиса, вызвавшего резкое повышение стоимости нефти, возникла необходимость во всех странах принять экстренные меры по экономии нефтяного топлива. Первоначально было введено ограничение максимальной скорости движения, что позволило снизить расход топлива, привело к сокращению числа ДТП.
Конструктивные мероприятия, направленные на снижение расхода топлива:
Двигатель. Расширение применения дизелей, позволяющих снизить расход топлива на 25…30%.
Работа по совершенствованию рабочего процесса бензиновых двигателей проводится в след. направлениях: организация послойного распределения заряда в камере сгорания, позволяющего использовать обедненные смеси; впрыскивание топлива во всасывающий тракт; использование электронного управления дозированием подачи топлива и зажиганием; применение турбонаддува. (снижение расхода топлива до 20%).
В РФ перспективно широкое применение природных газов. Более дальней перспективой является использование в качестве топлива для двигателей внутреннего сгорания водорода, запасы которого практически неограниченны. При работе на водородном топливе может быть решена проблема токсичности отработавших газов, так как в результате сгорания водорода образуется вода. Однако получение водорода сопряжено с большими энергетическими затратами, затруднены хранение и транспортирование водорода.
Некоторое развитие получает электромобили, главным образом для городских условий эксплуатации. Они бесшумны и не загрязняют окружающую среду.
Препятствием к их широкому применению является малая энергоемкость аккумуляторных батарей, их громоздкость, что снижает грузоподъемность автомобиля и запас хода.
В недалеком будущем получат развитие двигатели новых типов. Создание адиабатного керамического двигателя, обеспечивающего высокий термический КПД благодаря высокой температуре рабочего процесса из-за малого излучения теплоты в окружающую среду. В таких двигателях система охлаждения отсутствует.
Газотурбинные двигатели (ГТД) в настоящее время не используют, так как их топливная экономичность ниже, чем у дизелей, однако в перспективе при применении керамических материалов может быть налажено производство автомобильных ГТД (при повышении температуры сгорания расход топлива уменьшается).
Шасси. При снижении массы легкового автомобиля на 50…70 кг может быть получена экономия топлива 2…3%. Для снижения массы автомобиля проводят работы в трех направлениях:
1 поиск рациональных компоновочных решений (Компоновка легковых авт-ей с передними ведущими и управляемыми колесами.
Для грузовых авт-ей оптимальным компоновочным решением, позволяющим значительно снизить массу, является размещение кабины над двигателем);
2 поиск рациональных форм деталей (применение листовых рессор. При установке листов Т-образного сечения, малолистовых и однолистовых рессор их масса может быть снижена.);
3 применение конструкционных материалов, обладающих малой плотностью при обеспечении достаточной плотности. В наибольшей степени масса зависит от плотности материалов. Использование легированных и низколегированных сталей, а также алюминия позволяет значительно снизить массу автомобилей. Существенно уменьшается масса автомобиля при использовании пластмасс. Помимо снижения массы автомобиля, это обеспечивает уменьшение трудоемкости изготовления деталей, повышение их коррозионной стойкости, уменьшение теплопроводности и др. пластмассы могут быть как декоративными, так и конструкционными материалами для деталей, воспринимающих различные нагрузки.
Особое внимание уделяется композиционным материалам, которые представляют собой пластмассы, армированные волокнами различного вида (стеклопластики, углепластики, боропластики).
Кузов. Топливная экономичность автомобиля в большой степени зависит от аэродинамического сопротивления кузова и автомобиля в целом. Затраты мощности на преодоление аэродинамического сопротивления пропорциональны фактору обтекаемости и третьей степени скорости автомобиля.
Масса кузова составляет значительную часть массы автомобиля, поэтому снижение массы кузова важно для улучшения топливной экономичности. Наибольший эффект дает применение пластмассовых кузовов и отдельных пластмассовых деталей. В среднем масса деталей, изготовленных из пластмасс, в 2 раза меньше массы деталей, изготовленных из стали.
3. Требования, предъявляемые к конструкции автомобилей
К конструкции автомобиля предъявляют производственные, эксплуатационные, потребительские требования и требования безопасности.
1 Производственные требования – соответствие конструкции технологическим возможностям завода или передовым тенденциям перспективной технологии:
- минимальный расход материалов; - минимальная трудоемкость; - минимальная себестоимость.
2 Эксплуатационные требования:
- Топливная экономичность; - Курсовая устойчивость;
- управляемость; - маневренность; - Плавность хода; - проходимость; - надежность; - технологичность обслуживания и ремонта; - минимальная себестоимость транспортных работ.
3 Потребительские требования:
- Малая стоимость автомобиля и его эксплуатации; - безотказность и ремонтопригодность; - безопасность;
- комфортабельность; - легкость управления.
Требования безопасности распространяются на активную, пассивную, послеаварийную и экологическую безопасность автомобиля.
Аварийная безопасность автомобиля – свойство снижать вероятность возникновения дорожно-транспортных происшествий. Это свойство заложено в конструкцию автомобиля (отсюда термин – конструктивная безопасность) и проявляется постоянно при движении и в аварийной ситуации. Этот вид безопасности характеризуется обзорностью, сигнализацией, освещенностью, эргономическими условиями рабочего места водителя, маневренностью, управляемостью, устойчивостью, скоростными и тормозными свойствами и др.
Пассивная безопасность автомобиля – свойство снижать тяжесть последствий дорожно-транспортных происшествий. Внутреннюю пассивную безопасность характеризуют мероприятия, направленные на снижение травматизма водителя и пассажиров, обеспечение сохранности грузов, а внешнюю пассивную безопасность – снижение травматизма людей, находящихся вне автомобиля в процессе дорожно-транспортного происшествия.
Послеаварийная безопасность зависит от возможностей снизить тяжесть последствий аварии (аптечка, огнетушитель), эвакуации пострадавших и др.
Экологическая безопасность автомобиля – свойство автомобиля уменьшать вредное влияние на окружающую среду (загазовывание атмосферы, запыление, осадки вредных веществ на придорожную полосу, нарушение травяного покрова, порча деревьев и кустарников, загрязнение почвы и водоемов, шум и вибрации и др.)
Назначение, классификация и требования к сцеплению. Выбор и расчет основ.пар-ов сцепления. Расчет хар-к износостойкости сцепления.
Назначение сцепления – надежная передача крутящего момента от двигателя к трансмиссии.
Классификационные признаки
I. По характеру работы:
1. постоянно замкнутые;
2. постоянно разомкнутые.
II. По типу привода:
1. с механическим;
2. с гидравлическим;
3. с комбинированным:
3.1 пневмомеханическим;
3.2 пневмогидравлическим;
3.3 электромеханическим;
3.4 электровакуумным.
III. По способу управления:
1. автоматическое;
2. неавтоматическое (ножное, ручное):
2.1 с усилителем;
2.2 без усилителя.
IV. По характеру связи между ведущим и ведомыми элементами:
1. гидравлическое (гидромуфта);
2. электромагнитное (порошковое);
3. фрикционное:
3.1 по форме элементов трения:
3.1.1. специальное (конусное, барабанное и др.);
3.1.2. дисковое:
3.1.2.1. с дисками в масле;
3.1.2.2. с сухими дисками:
3.1.2.2.1. однодисковое;
3.1.2.2.2. двухдисковое;
3.1.2.1.3. многодисковое.
3.2. по способу создания нажимного усилия:
3.2.1. центробежное;
3.2.2. полуцентробежное;
3.2.3. электромагнитное;
3.2.4. пружинное:
3.2.4.1. с периферийной пружиной;
3.2.4.2. с центральной пружиной:
3.2.4.2.1. цилиндрической;
3.2.4.2.2. конической;
3.2.4.2.3. диафрагменной.
Требования, предъявляемые к конструкции:
Надежная передача крутящего момента от двигателя к трансмиссии;
Плавность и полнота включения;
Чистота выключения;
Минимальный момент инерции ведомых элементов;
Хороший отвод теплоты от поверхностей трения;
Предохранение трансмиссии от динамических нагрузок;
Поддержание нажимного усилия в заданных пределах в процессе эксплуатации;
Минимальные затраты физических усилий на управление;
Хорошая уравновешенность;
Общие требования: обеспечение минимальных размеров и массы, простота устройства и обслуживания, технологичность, ремонтопригодность, низкий уровень шума.
Характеристики симметричного и ассиметричного циклов
Ассиметричный цикл, в котором среднее напряжение цикла будет
Амплитуда цикла
Коэффициент асимметрии
Буквой Т обозначен период, соответствующий полному циклу изменения напряжения.
Симметричный цикл, у которого = - , а среднее напряжение цикла
,
амплитуда цикла
А коэффициент асимметрии цикла
В качестве примера можно указать, что в автомобиле изменение напряжений по ассиметричной схеме имеет место у некоторых деталей ходовой части и подвески рессор, балок мостов поворотных шкворней. По симметричной схеме - у валов КП, у полуразгруженных полуосей (напряжения изгиба).
Характеристика пульсирующего цикла
Пульсирующий цикл, являющийся частным случаем несимметричного цикла, когда , а среднее напряжение и амплитуда цикла
По пульсирующей схеме – у зубьев шестерен.
Определение перед.числа привода сцепления и выбор пар-ов отдельных его звеньев
Схемы приводов сцепления: а) механического, б) гидравлического
Общее передаточное число привода сцепления
uп.с. = u1u2
где u1 – передаточное число педального привода; u2 – передаточное число
рычагов выключения сцепления.
Передаточное число механического привода:
гидравлического:
Ход педали зависит от величины s, на которую отводится нажимной диск при выключении сцепления, и зазора Д2 между рычагами выключения и выжимным подшипником.
Sпед = suп.с. + Д2u1
Общее передаточное число привода сцепления включает передаточное число рычагов выключения и передаточное число педального привода, а в случае гидравлического привода и передаточное число гидравлической части привода. Общее передаточное число привода сцепления определяется из условия, что усилие на педали при отсутствии усилителя не должно превосходить для легковых автомобилей 150 Н, для грузовых 250 Н. Полный ход педали должен лежать при этом в пределах 120...190 мм, включая свободный ход педали.
Расчет крестовины шарнира карданной передачи
В карданном шарнире угловых скоростей определяют нагрузки в крестовине и в вилке. Шипы крестовины испытывают напряжения изгиба и смятия, а крестовина – напряжение разрыва. Вилка подвергается изгибу и скручиванию. Примем, что шарниром передается максимальный динамический момент, который ограничивается коэффициентом запаса сцепления. При малом угле наклона г вала шарнир передает момент (передаточное число трансмиссии до карданной передачи), а динамическое нагружение можно учитывать запасом прочности.
Напряжение изгиба шипа крестовины (см.рис.):
Напряжения среза шипа крестовины:
Напряжения крестовины на разрыв в сечении А-А площадью F:
Материал крестовин: стали 18ХГТ, 20Х.
Назначение, классификация и требования к конструкции ведущих мостов. Расчет балки ведущего моста на прочность (нагрузочный режим- разгон автомобиля). Расчет балки ведущего моста на прочность (нагрузочный режим - торможение)
Мосты обеспечивают поддержание несущей части, передают силы и моменты от колес на несущую часть, являясь элементом рулевого управления, обеспечивают поворот автомобиля, является частью автомобиля.
К автомобильным мостам предъявляются следующие основные требования: минимальная масса, наименьшие габаритные размеры и оптимальная жесткость.
Ведущие мосты одновременно являются корпусной деталью для элементов трансмиссии и включают в себя: главную передачу, дифференциал, полуоси и применяются в качестве заднего и промежуточного моста.
Классификация мостов.
1 По назначению (ведущий, управляемый(с поворотными колесами, с поворотной балкой), комбинированный, ведомый)
2 По числу колес (с одинарными, со сдвоенными)
3 По виду применяемой подвески (неразрезной, разрезной)
4 По конструктивной схеме (с поперечиной, с балкой )
5 По составу (одиночный, в составе тележки)
Расчет балки моста (прямолинейное движение автомобиля)
Мосты автомобиля рассчитывают на прочность по сцеплению колес автомобиля с дорогой при максимальном значении коэффициента сцепления. Расчет выполняют для различных режимов движения автомобиля. При расчете значения сил и моментов, действующих на мосты при движении автомобиля, принимаются максимальными.
Ведущий мост. Балку ведущего моста рассчитывают для трех нагрузочных режимов: прямолинейное движение автомобиля, занос автомобиля и переезд автомобиля через препятствие.
При прямолинейном движении автомобиля балка ведущего моста (см.рис.) изгибается в вертикальной плоскости под воздействием нормальных реакций дороги и на ведущие колеса.
Изгибающий момент в вертикальной плоскости где – плечо изгиба.
Нормальные реакции дороги от нагрузки на ведущий мост равны:
где – коэффициент перераспределения нагрузки на задний мост.
Кроме того, под действием тяговой силы балка ведущего моста испытывает статическую нагрузку и изгибается также в горизонтальной плоскости. Изгибающий момент в горизонтальной плоскости Тяговые силы на ведущих колесах равны: - коэф сцепл колес с дорогой.
Кроме изгибающих моментов на балку ведущего моста действует крутящий момент
где – радиус ведущих колес.
В балке ведущего моста наиболее опасными местами являются обычно сечения под площадками для крепления пружин (рессор).
Суммарный результ-й момент от изгиба и круч-я в опасном сеч-и балки моста
Результ-е напряжения от изгиба и кручения для трубчатого круглого сечения
где – момент сопротивления трубчатого сечения.
Расчет балки ведущего моста на прочность (режим – динамические нагрузки)
При динамическом нагружении изгибающий момент в вертикальной плоскости:
Mи = Rz1Кдl,
где Кд= 1,5...3 — коэффициент динамичности.
Напряжение изгиба уи= Mи /W.
Для балок мостов, литых из стали и чугуна, [фи]= 300 МПа, для штампованных из стального листа [фи]= 500 МПа.
Определение нагрузок и расчет переднего моста производят так же, как и заднего моста. При торможении коэффициент перераспределения нагрузки на передний мост m1=1,1...1,2. Необходимо учитывать переменное сечение балки: двутавровое в средней части и после рессорной площадки постепенно переходящее в круглое. Вертикальные реакции Rz1=Rz2= m1G1/2, где G1— нагрузка на передние колеса.
Для балки управляемого моста жесткость важна для сохранения углов установки колес. Жесткость ведущего моста влияет на условия зацепления зубчатых передач, на нагрузку подшипников и на нагруженность полуосей.
Прогиб балки равен силе в заданном сечении, отнесенной к жесткости сечения i=Ри/(ЕJx). Балка нагружена в местах крепления рессор.
Переменное сечение балки затрудняет расчет. В таких случаях или упрощают схему и ведут расчет по наиболее опасному сечению, или усложняют расчет, применяя метод конечных элементов.
Прогиб балки грузовых автомобилей достигает 2...3 мм
Расчет балки ведущего моста на прочность (нагрузочный режим – боковой занос автомобиля)
При заносе балку моста рассчитывают на изгиб в вертикальной плоскости, считая при этом Pт1=Pт2=0.
Изгибающие моменты в вертикальной плоскости
, — боковые реакции при заносе;
,
где и — нормальные реакции опорной поверхности при заносе. Условно принимается .
Эпюры моментов от и строят раздельно, а затем складывают. Опасное сечение картера находится в месте крепления рессоры: здесь напряжение изгиба:
,
Назначение, классификация и требования к конструкции главных передач. Выбор основных параметров и расчет на прочность конических зубчатых пар главной передачи.
Главная передача обеспечивает постоянное увеличение крутящего момента и передачу его к ведущим колёсам, выбирается из условий получения заданной максимальной скорости автомобиля на высшей передаче в коробке передач и оптимальной топливной экономичности.
К главным передачам предъявляют следующие требования: -оптимальное значение передаточного числа; - высокий КПД; -низкий уровень шума; - небольшие вертикальные размеры.
Классификация главных передач.
1 Одинарные (червячная, цилиндрическая(прямозубая ,косозубая, шевронная)коническая, гипоидная)
2 двойная (центральная, разнесенная)
При расчете шестерен на прочность) определяют напряжения в зубьях от изгиба:
где окружная сила;
коэффициент, учитывающий форму и число зубьев;
ширина шестерни;
нормальный шаг в среднем сечении начального конуса шестерни.
Допускаемые напряжения изгиба в зубьях .
Расчет главной передачи на износостойкость зубьев по контактным напряжениям
При расчете главной передачи на износ определяют контактные напряжения в зубьях:
где модуль упругости;
средние радиусы начального конуса соответственно ведущей и ведомой шестерен.
Допускаемые контактные напряжения (большие значения – для гипоидных главных передач).
Шестерни главных передач изготавливают из стали следующих марок: 15ХН3А, 20ХН3А, 20ХНМА, 30ХГТ.
Расчет шкворня и втулок поворотных цапф на прочность (режим - торможение)
Углами наклона шкворня в поперечной и продольной плоскостях пренебрегают вследствие их небольших значений, которые не влияют на результаты расчета.
При торможении силы и , нагружающие соответственно верхний и нижний концы шкворня, возникают под действием:
нормальной реакции :
тормозной силы :
реактивной силы :
тормозного момента
Суммарная сила, действующая на верхний конец шкворня
Суммарная сила, действующая на нижний конец шкворня
Расчет шкворня и втулок поворотных цапф на прочность (режим - боковой занос автомобиля)
При заносе на верхний и нижний конец шкворня действуют только поперечные силы:от нормальной реакции :
от поперечной реакции :
на левом шкворне
на правом шкворне
Суммарные силы:
на левом шкворне
на правом шкворне
Расчет шкворня и втулок поворотных цапф на прочность (режим - динамические нагрузки)
на шкворень действуют силы:
Шкворень на всех нагрузочных режимах рассчитывают на изгиб и на срез, а втулки шкворня рассчитывают на смятие:
Напряжения изгиба шкворня
Напряжения среза шкворня
Напряжения смятия втулок шкворня
Где диаметр шкворня, высота втулки шкворня.При определении напряжений в шкворне и втулках шкворня принимают наибольшие из значений суммарных сил, действующих на шкворень для рассматриваемых режимов движения автомобиля. Шкворни изготавливают из стали марок 40, 50, 18ХГТ. [] = 500 МПа, [] = 100 МПа, [] = 50 МПа.
Назначение, классификация и требования к конструкции подвески. Последовательность расчета листовой рессоры.
Подвеска обеспечивает упругое соединение несущей системы с колесами автомобиля.
К подвескам автомобилей предъявляют следующие требования: 1 Обеспечение плавности хода; 2Обеспечение движения по неровным дорогам без ударов в ограничитель; 3 Ограничение поперечного крена автомобиля; 4 Кинематическое согласование перемещений управляемых колес, исключающее их колебание относительно шкворней; 5 Обеспечение затухания колебаний кузова и колес; 6 Постоянство колеи, углов наклона колес, постоянство углов наклона шкворней; 7 Надежная передача от колес к кузову продольных и поперечных сил; 8 Обеспечение затухания колебаний кузова и колес; 9 Снижение неподрессоренной массы. Классификация подвесок. 1 По типу характеристики (постоянной, переменной жесткости, прогрессивная) 2 По типу направляющих устройств (зависимые (автономная, балансирная), независимая) 3 По способу передачи сил и моментов от колес (рессорная, шланговая, рычажная) 4 По типу упругого элемента (металлическая (рессорная, пружинная, торсионная, комбинированная), неметаллическая(пневматическая, гидропневмат., комбинир., резиновая)) 5 По способу гашения колебания (гидравлич амортизаторы (рычажные, телескопические), механическое трение(трение в упругом эл-те и направл. Уст-ве ))
Основными расчетными характеристиками листовой рессоры являются напряжение изгиба и , прогиб f P и жесткость C P.
Материалом для изготовления рессор служат стали 55ГС, 50С2, 60С2, для которых допускаемые напряжения при максимальном прогибе [уH ] =800. ..1000 МПа.
Расчет упругого элемента в независимой подвеске
В зависимости от схемы подвески нагрузка на упругий элемент меняется. Для однорычажной подвески (б)
нагрузка на упругий элемент
где l, a - параметры подвески автомобиля;
- вес колеса и направляющего устройства.
Прогиб упругого элемента однорычажной, двухрычажной подвески:
Для двухрычажной подвески (а) нагрузка на упругий элемент:
а прогиб
Для двухрычажной подвески с торсионным упругим элементом нагрузка на упругий элемент определяется моментом закручивания торсиона
Расчет основных параметров амортизатора
Коэфициент апериодичности в подвеске при колебаниях автомобиля Ша;
-Максимальное усилие при сжатии и отбое;
-Критические скорости движения поршня, при которых открываются клапана:
-Энергоёмкость и степень её уменьшения при нагреве.
Сила сопротивления выражается Pн=kрvпm , где Vп- скорость поршня; Лн- коэффициент сопротивления на начальном участке до открытия клапана; ь- показатель степени(м=1..3)
На клапанном участке Pk=
Назначение, классификация и требования к конструкции рулевого управления. Выбор основ.размеров и расчет рул.мех-ма (глобоидальный “червяк-ролик”)
Рулевое управление — это совокупность устройств, обеспечивающих поворот управляемых колес автомобиля при воздействии водителя на рулевое колесо. Оно состоит из рулевого механизма и рулевого привода. Для облегчения поворота колес в рулевой механизм или привод может встраиваться усилитель.
Конструкция рулевого управления должна обеспечивать:
- легкость управления, оцениваемую усилием на рулевом колесе. Для лег без усилителя при движении это усилие составляет 50...100 Н, а с усилителем— 10...20 Н.
- качение управляемых колес с минимальными боковым уводом и скольжением при повороте автомобиля. Несоблюдение этого требования приводит к ускорению изнашивания шин и снижению устойчивости автомобиля при движении;
- стабилизацию повернутых управляемых колес, обеспечивающую их возвращение в положение, соответствующее прямолинейному движению, при отпущенном рулевом колесе;
- предотвращение передачи ударов на рулевое колесо при наезде управляемых колес на препятствия;
- минимальные зазоры в соединениях. Оцениваются углом свободного поворота рулевого колеса автомобиля, стоящего на сухой, твердой и ровной поверхности в положении, соответствующем прямолинейному движению. По ГОСТ этот зазор не должен превышать 15° при наличии усилителя и и 5° — без усилителя рулевого управления;
- отсутствие автоколебаний управляемых колес при работе автомобиля в любых условиях и на любых режимах движения;
- повышенная надежность, так как выход из строя рулевого управления приводит к аварии;
- возможно меньшее значение минимального радиуса поворота для обеспечения хорошей маневренности автомобиля;
- силовое и кинематическое следящее действие, т.е. пропорциональность между усилием на рулевом колесе и моментом сопротивления повороту управляемых колес и заданное соответствие между углом поворота рулевого колеса и углом поворота управляемых колес;
- кинематическая согласованность элементов рулевого управления с подвеской для исключения самопроизвольного поворота управляемых колес при деформации упругих элементов.
Классификация рулевых управлений
1 По способу поворота автомобиля
- Поворотом управляемых колес
- Торможением колеса одного борта
- Вращением колес одного борта в сторону, обратную движению
- Складыванием элементов (одноосный тягач и одноосный прицеп)
2 По расположению рулевого колеса
- правое - левое
3 По расположению управляемых колес на…
3.1 Двухосных автомобилях (Первой оси
Второй оси, Первой и второй осей)
3.2 Трехосных автомобилях (Первой оси,
Первой и третьей осей)
3.3 Четырехосных автомобилях (Первой и второй осей, Первой и третьей осей, Всех осей)
Рулевой механизм включает в себя рулевую пару (иногда называют рулевой передачей), размещенную в картере, рулевой вал, рулевую колонку и рулевое колесо.
К конструкции рулевых механизмов предъявляется ряд специальных требований:
а) высокий КПД в прямом направлении (при передаче усилия от рулевого колеса) для облегчения управления автомобилем и несколько пониженный КПД в обратном направлении для снижения силы толчков, передаваемых на рулевое колесо от управляемых колес при наезде на неровности;
б) обратимость рулевой пары, чтобы рулевой механизм не препятствовал стабилизации управляемых колес;
в) минимальный зазор в зацеплении элементов рулевой пары в нейтральном положении управляемых колес и в некотором диапазоне углов поворота (беззазорное зацепление) при обязательной возможности регулирования зазора в процессе эксплуатации;
г) заданный характер изменения передаточного числа рулевого механизма;
д) травмобезопасность рулевого механизма, с тем чтобы при лобовом столкновении он не был причиной травмы водителя.
Расчет рул.мех-ма (глобоидальный “червяк-ролик”)
Для механизма, включающего глобоидный червяк и ролик, определяется контактное напряжение в зацеплении
у = Px/(Fn),
где Рх — осевое усилие, воспринимаемое червяком; F — площадь контакта одного гребня ролика с червяком (сумма площадей двух сегментов, рис);
n — число гребней ролика.
Схема для определения контактной площадки в червячном рулевом механизме
Осевая сила
Px=Mp.k/(rщotgв)
где rщo — начальный радиус червяка в горловом сечении; в — угол подъема винтовой линии в том же сечении.
Площадь контакта одного гребня ролика с червяком (рис)
F = 0,5[(ц1 — sin ц1)r²1+( ц2 — sin ц2) r²2]
Материал червяка—цианируемая сталь 30Х, 35Х, 40Х, 30ХН; материал ролика - цеменуемая сталь 12ХНЗА, 15ХН; [у] = 7...8 МПа.
Оценка и расчет основных размеров деталей рулевого привода
К рулевому приводу предъявляют следующие требования: правильное соотношение углов поворота колес, отсутствие автоколебаний управляемых колес, а также самопроизвольного поворота колес при колебаниях автомобиля на подвеске.
Рулевой привод включает рулевую трапецию, рычаги и тяги, связывающие рулевой механизм с рулевой трапецией, а также рулевой усилитель, устанавливаемый на ряде автомобилей.
Расчет рулевой сошки на изгиб и кручение
Изгиб и кручение - основные виды напряжения. Расчет ведут на сложное сопротивление; шлицы рассчитывают на срез. Усилие на шаровом пальце сошки, вызывающее изгиб и кручение (при наличии встроенного усилителя): Напряжение изгиба в опасном сечении А—А:
.
Напряжение кручения:
,
где и — соответственно осевой и полярный моменты сопротивления опасного сечения.
Эквивалентное напряжение рассчитывается по одной из теорий прочности. [ф] = 300...400 МПа
Напряжение кручения вала сошки при наличии усилителя
где d — диаметр вала сошки. Материал вала сошки — сталь 30, 18ХГТ, 20ХНЗА.; [т] = 300...350 МПа.
Расчет продольной тяги в рулевом управлении. Расчет поперечной тяги в рулевом управлении
Сила Рсош вызывает напряжения сжатия-растяжения и продольного
изгиба тяги
Напряжение сжатия
где F — площадь сечения продольной тяги.
Критическое напряжение при продольном изгибе
где I — экваториальный момент инерции сечения тяги;
LT—длина продольной тяги (по центрам шарниров).
Запас устойчивости
Материал тяги: сталь 20, сталь 35; [д] = ,5...2,5.
Поперечная тяга трапеции.
Нагруженная силой РПТ=РсошS/l тяга рассчитывается по той же методике, что и продольная тяга, т. е. на сжатие и продольную устойчивость (|д|= 1,5...2,5). Для изготовления поперечной тяги используют те же материалы, что и для продольной.
Назначение, классификация и требования к конструкции тормозных систем. Расчет сил и моментов, действующих в колесном тормозе барабанного типа (с одной активной колодкой)
К тормозному управлению автомобиля, служащему для замедления его движения вплоть до полной остановки и удержания на месте на стоянке, предъявляются повышенные требования, так как тормозное управление является важнейшим средством обеспечения активной безопасности автомобиля.
Требования к тормозным системам следующие: - минимальный тормозной путь или максимальное установившееся замедление в соответствии с требованиями ГОСТ
- сохранение устойчивости при торможении (критериями устойчивости служат линейное отклонение, угловое отклонение, угол складывания автопоезда);
- стабильность тормозных свойств при неоднократных торможениях;
- минимальное время срабатывания тормозного привода;
- силовое следящее действие тормозного привода, т. е. пропорциональность между усилием на педали и приводным моментом;
- малая работа управления тормозными системами — усилие на тормозной педали в зависимости от назначения автотранспортного средства должно лежать в пределах 500...700 Н (низший предел для легковых автомобилей); ход тормозной педали 80...180 мм;
- отсутствие органолептических явлений (слуховых, обонятельных);
- надежность всех элементов тормозных систем; основные элементы (тормозная педаль и ее крепление, главный тормозной цилиндр, тормозной кран и др.) должны иметь гарантированную прочность, не должны выходить из строя на протяжении гарантированного ресурса; должна быть также предусмотрена сигнализация, оповещающая водителя о неисправности тормозной системы;
В соответствии с ГОСТ тормозное управление должно включать следующие тормозные системы: - рабочую; - запасную; - стояночную;
- вспомогательную (тормоз — замедлитель), предназначенную для торможения на длительных спусках и поддерживающую скорость 30 км/ч на спуске с уклоном 7% протяженностью 6 км.
Классификация тормозных механизмов
Тормозной механизм: гидравлический,
механический (фрикционный), электрический
Механический (фрикционный):
По форме поверхности трения
дисковые барабанные (колодочные ленточные)
По расположению
колесный трансмиссионный
Тормозной привод: механический, гидравлический, пневматический
электрический, комбинированный
Схема (а) и статическая характеристика (б) барабанного тормозного механизма с гидравлическим приводом с равными приводными силами и односторонним расположением опор:
1-первичная колодка; 2-вторичная колодка; 3-тормозной цилиндр.
Для этого тормозного механизма характерным является следующее. Приводные силы P1 и P2, прижимающие колодки 1 и 2 к барабану равны (P1=P2), так как площади поршней тормозного цилиндра 3 одинаковы. Нормальные реакции барабана N1 b N2 на колодки не равны между собой (N1>N2). Момент, создаваемый силой трения F1 и действующий на колодку 1, совпадает по направлению с моментом приводной силы P1, вследствие чего колодка захватывается барабаном, а сила трения F1 способствует прижатию колодки к барабану. Момент силы трения F2, действующий на колодку 2, противоположен по направлению моменту приводной силы P2, и поэтому сила трения F2 препятствует прижатию колодки 2 к тормозному барабану.
Колодка 1 называется первичной (активной, самоприжимной), а колодка 2 – вторичной (пассивной, самоотжимной). Первичная колодка нагружается больше, чем вторичная. При вращении колеса в противоположную сторону функции колодок изменяются и колодка 2 работает кА первичная, а колодка 1 – как вторичная.
Тормозной момент, создаваемый тормозным механизмом:
Мтор=(F1+F2)rб
или с учётом значения сил трения F1=µN1; F2=µN2
Mтор=µ(N1+N2)rб,
где µ=0,3 – коэффициент трения
Из условия равновесия тормозящего колеса имеем:
P1(a+c)+ F1rб-N1a=0 – для первичной колодки;
P2(a+c)+ F2rб-N2a=0 – для вторичной колодки.
Подставив в эти уравнения значения сил трения F1 и F2, получим соответственно для первичной и вторичной колодок:
P1=N1; P2=N2;
Расчет диаметра цилиндра колесного тормоза с гидроприводом
При служебных торможениях давление жидкости в тормозном приводе лежит в пределах 4...10 МПа. В случае экстренного торможения давление жидкости
может до 15 МПа и выше. Усилие на педали можно вычислить исходя из максимального давления в
приводе:
где p´ж - давление жидкости в приводе при экстренном торможении; dг.ц -диаметр главного цилиндра; uп.п - передаточное число педального привода (uп.п =а/b); зп.п - коэффициент полезного действия привода (зп.п = 0,92...0,95).
При этом усилие, создаваемое рабочим цилиндром на тормозные колодки
где dр.ц - диаметр рабочего цилиндра, (dр.ц = 0,9...1,2) dг.ц.
С какой целью проводят стендовые испыт.агрегатов, мех-ов, и ав-ей в целом
Стендовые испытания агрегатов, механизмов и автомобилей в целом проводятся с целью получения данных для расчёта каких-либо характеристик (мощностных, экологических и др.) или с целью проверки соответствия тому, что указано в паспорте агрегата, автомобиля.
С какой целью проводят дорож.,эксплуат, заводские и госуд.испыт.ав-ей.
Заводские и государственные испытания (государственный контроль) автомобилей, как и техосмотр, проводятся с целью проверки соответствия ГОСТам и стандартам. Проверяется экологичность и техническое состояние.
Расчетные режимы и обоснование их выбора
Для расчёта отдельных узлов и агрегатов автомобиля могут быть использованы разные расчётные режимы. Важно правильно оценить эти режимы для обоснованного выбора применительно к поставленной задаче. Трансмиссия. На основании анализа нагрузочных режимов трансмиссии могут быть установлены расчётные режимы.
Первый расчётный режим – по максимальному моменту двигателя
M=(Mт)max*I,
где M – момент на валу трансмиссии, соответствующий максимальному моменту двигателя;
(Mт)max – максимальный момент двигателя;
I – передаточное число, считая от вала двигателя до соответствующего вала трансмиссии.
Второй расчётный режим – по максимальному сцеплению ведущих колёс с грунтом цmax.
Третий расчётный режим – по максимальной динамической нагрузке, имеющей место при резком включении сцепления.
Четвёртый расчётный режим – принимается по действительным эксплуатационным нагрузкам (расчёт на выносливость).
Тормоза. Выбор расчётного режима для тормозов должен предусматривать возможность торможения автомобиля с наибольшей эффективностью, что может быть достигнуто в случае полного использования силы сцепления заторможенных колёс с дорогой до юза или состояния близкого к юзу.
В качестве расчётного режима для расчёта на прочность деталей тормозов и тормозных приводов (барабаны, колодки и их опоры, привод к разжимным кулакам и другие) принимаются максимальные силы, приложенные к соответствующим деталям.
Подвески и мосты. Расчёт на прочность деталей подвесок и мостов производится по максимальной нагрузке Pmax, имеющей место при движении автомобиля. Рулевое управление. Расчёт на прочность деталей рулевого механизма может производиться на следующие режимы нагрузки:
- Максимальный момент Mш, приложенный к рулевому колесу,
Mш=(Pш)max*Rш,
где (Pш)max – максимальное усилие, приложенное водителем к рулевому колесу;
Rш – радиус рулевого колеса.
- Максимальную тормозную силу, приложенную к одному или обоим управляемым колёсам на дороге с ц=0,8÷1,0.
- Удар управляемых колёс при переезде через пороговые препятствия разной высоты или вертикальную стенку.
Виды прочности дет. При их раасчетах
Прочность детали может быть статическая (в неподвижном состоянии) и динамическая (в движении).
Опред-ие вел-ны расчет.момента при расчете дет.трансмиссии на долговечность
Величина расчётного момента при расчёте деталей трансмиссии на долговечность определяется по формуле.
Как учитываются динам.нагрузки при расчете дет. Ходов.части,подвески и рамы на долговечность
Динамические нагрузки при расчёте деталей ходовой части, подвески и рамы на долговечность учитываются использованием их значений в формулах расчёта.
Назначение, классификация и требования к конструкции КП. Какие исход.данные принимаются для расчета КП.Определение сил, действ.на зуб косозубой шестерни КП
Требования, классификация К коробке передач предъявляются следующие требования: а) обеспечение оптимальных тягово-скоростных и топливно-экономических свойств автомобиля при заданной внешней характеристике двигателя; б) бесшумность при работе и переключении передач; в) легкость управления; г) высокий КПД; д) общие требования.
По характеру изменения передаточного числа
а) бесступенчатая -Механическая
фрикционная импульсная
-Гидравлическая
гидрообъемная гидродинамическая
-Электрическая
б)комбинированная
-Гидромеханическая -Электромеханическая
в)ступенчатая
-По конструктивной схеме с неподвижными осями
с подвижными осями комбинированная
-По числу ступеней
Трехступенчатые четырехступенчатые
Пятиступенчатые многоступенчатые
-По типу зубчатого зацепления
Прямозубая косозубая
Шевронная смешанная
-По способу переключения
с подвижными зубчатыми колесами
с муфтами легкого включения
с синхронизаторами
-По способу управления
с непосредственным
с дистанционным
полуавтоматическая
автоматическая
Исходные данные для расчета
Определение сил, действующих на зуб косозубой шестерни КП. На зубья пары постоянного зацепления привода промежуточного вала действуют следующие силы:
Здесь бщ - угол профиля зуба; в — угол наклона зубьев; rщП.З. – радиус делительной.
На зубья пары при включении i-й передачи действуют силы:
Здесь ui — передаточное число включенной передачи; ri— радиус делительной окружности зубчатого колеса ведомого вала.
Расчет валов КП на прочность
Валы коробок передач воспринимают скручивающие и изгибающие нагрузки. Кроме того, они должны быть достаточно жесткими, чтобы их прогиб не вызывал перекоса зубчатых колес, находящихся в зацеплении. Последовательность определения напряжений в валах: в трехвальных коробках передач — ведомый, промежуточный вал, ведущий вал; в двухвальных коробках передач расчет можно начинать с любого из валов. Пользуясь схемой (например, приведенной на рис.70), определяют силы, действующие на зубчатые колеса на всех передачах, по формулам, приведенным выше. Затем для каждой передачи находят реакции в опорах. После этого строят эпюры моментов и определяют наибольший изгибающий и крутящий моменты.
Результирующее напряжение
где d в о . - диаметр вала в опасном сечении.
Шлицованный вал рассчитывают по внутреннему диаметру.
16 Жесткость валов КП и опред стрелы прогиба
Жесткость валов определяется по их прогибу. Силы Рх1 и PR1 дают прогиб fв валов в плоскости, в которой лежат оси валов, сила Pi, дает прогиб в перпендикулярной плоскости. Прогиб вала в каждой плоскости должен лежать в пределах 0,05...0,1 мм. Полный прогиб
Валы должны обладать достаточной жесткостью, поэтому напряжения в них невысокие (200...400 МПа).
Шлицы валов проверяют на смятие см =200 МПа.
Для изготовления валов применяют обычно те же материалы, что и для зубчатых колес.
Расчёт подшипников валов коробок передач
Критерием оценки эксплуатационных свойств подшипников является базовая долговечность, соответствующая 90 %-ной надежности.
Для определения долговечности подшипника необходимо иметь следующие данные: радиальные и осевые силы, действующие на подшипник на каждой передаче; ресурс коробки передач до капитального ремонта (в километрах пробега автомобиля или часах); среднюю техническую скорость движения; распределение пробега на передачах.
Радиальные и осевые силы, действующие на подшипник на каждой передаче,
представляющие собой реакции опор валов коробки передач, рассчитывают,
пользуясь формулами:
окружная Pi= MKmaxui/rщi
осевая Pxi= Pitgв
радиальная PRi= Pitgбщ/cosв
нормальная Pni=
Здесь ui— передаточное число включенной передачи; rщi -радиус делительной окружности зубчатого колеса ведомого вала.
Однако при расчете подшипника на долговечность в этих формулах вместо
максимального значения крутящего момента двигателя МКмах следует принимать расчетную величину крутящего момента аМКмах, (где а — коэффициент использования крутящего момента). Этот коэффициент зависит от отношения мощности двигателя к весу автомобиля.
Базовая долговечность подшипника определяется в соответствии с ГОСТ по ресурсу (в млн. оборотов)
L10=(C/P)p, где С — динамическая грузоподъемность подшипника (опреде-ляют по каталогу), Р — эквивалентная динамическая нагрузка, р — показатель степени (шариковые подшипники - р=3, роликовые р=3,33).
Эквивалентная динамическая нагрузка на подшипник определяется для условий работы на каждой передаче:
Радиальные Pr=(XVFr+YFa)KbKt
радиально-упорные Pa=(XFr+YFa)KbKt
где Fr,Fa - соответственно радиальная и осевая нагрузки; X, Y—коэффициенты радиальной и осевой нагрузок (по каталогу); V—коэффициент вращения (при вращении внутреннего кольца V=1, при вращении наружного кольца V=1,2); Kb -коэффициент безопасности (для коробок передач Kb=1); Kt -температурный коэффициент (Kt=1,10 при 150 °С).
Следует иметь в виду, что коэффициенты Х и Y различны в зависимости от типа подшипника и соотношения осевой и радиальной нагрузок.
Для вычисления эквивалентной динамической нагрузки на подшипник коробки передач необходимо вначале определить долю работы подшипника на каждой передаче, учитывая нагрузку и соответствующее число оборотов за время работы на данной передаче. Суммируя по всем передачам, можно вычислить эквивалентную динамическую нагрузку по формуле
P=
где P1,P2,P3,…Pn - эквивалентные нагрузки на подшипник на каждой передаче
при долговечности соответственно L1,L2,L3,..Ln;
L=, Li=Si/(2рrk*uTPi*106),
(Si - пробег автомобиля на каждой передаче, uTPi - передаточное число части трансмиссии от вала, на котором установлен подшипник, до вала ведущего колеса автомобиля).
Динамическая грузоподъемность подшипника C = P .
Назначение, классификация и требования к карданным передачам. Кинематические харак-ки карданных передач неравных и равных угловых скоростей. Расчет карданного вала на прочность и жесткость.
Силовые приводы, силовые передачи и валы трансмиссии
Назначение, требования, классификация
Силовые приводы и силовые передачи трансмиссии (валы, карданные передачи, полуоси) применяются в трансмиссиях автомобилей для силовой связи механизмов, в том числе, валы которых несоосные или расположены под углом, причем взаимное положение их может меняться в процессе движения. Силовые приводы могут иметь один или несколько шарниров, соединенных валами, и промежуточные опоры. Передачи применяют также для привода вспомогательных механизмов, например, лебедки.
К силовым передачам предъявляют следующие требования:
а) передача крутящего момента без создания дополнительных нагрузок в трансмиссии (изгибающих, скручивающих, вибрационных, осевых);
б) возможность передачи крутящего момента с обеспечением равенства угловых скоростей ведущего и ведомого валов независимо от угла между соединяемыми валами;
в) высокий КПД;
г) бесшумность;
д) общие требования.
На рисунке 6.1 приведены классификации шарниров силовых передач.
Шарнир неравных угловых скоростей
В этом шарнире определяют нагрузки в крестовине и в вилке. Шипы крестовины испытывают напряжения изгиба и смятия, а крестовина напряжение разрыва. Вилка подвергается изгибу и скручиванию. Как указывалось выше, момент, передаваемый шарниром при наклоне вала, не является постоянным в течение одного оборота, а следовательно, и силы, действующие на детали шарнира, также переменны. Для определения нагрузок будем считать, что шарниром передается максимальный динамический момент, который ограничивается коэффициентом запаса сцепления. При малом угле наклона г вала шарнир передает момент МкmaxuґТРmax (uґТРmax – передаточное число трансмиссии до карданной передачи), а динамическое нагружение можно учитывать запасом прочности.
Валы
Во время работы вал силовой передачи испытывает изгибающие, скручивающие и осевые нагрузки.
Изгибающие нагрузки возникают в результате не уравновешенности вала, и в некоторой степени пары осевых сил, нагружающих шарнир. В эксплуатации неуравновешенность может появиться не только в результате механических повреждений вала, но также при износе шлицевого соединения или подшипников шарниров. Неуравновешенность приводит к вибрациям в силовой передаче и возникновению шума. Вал подвергается тщательной динамической балансировке на специальных балансировочных станках. Допустимый дисбаланс зависит от максимального значения эксплуатационной угловой скорости вала и находился в пределах. (15...100) г·см. Для балансировки к валу приваривают пластины в местах, которые автоматически определяются балансировочным станком. Помимо этого проверяется биение вала в сборе с шарнирами. Допустимое биение устанавливается заводом изготовителем.
Следует иметь в виду, что даже хорошо уравновешенный вал в результате естественною прогиба, вызванного собственным весом, при некоторой угловой скорости, называемой критической, теряет устойчивость; его прогиб возрастает настолько, что возможно разрушение вала.
Пусть в статическом положении ось вала смешена на расстояние е от оси вращения, а при угловой скорости щ получает прогиб f . Тогда при вращении вала возникает центробежная сила
где mв – масса вала.
Центробежная сила уравновешивается силой упругости вала
где И с – изгибная жесткость.
Поэтому
Прогиб вала определяется в зависимости от принятой схемы его нагружения.
Будем считать вал нагруженной равномерно балкой на двух опорах со свободными концами. Прогиб балки
где Е = 2·105 МПа – модуль упругости первого рода;
– момент инерции поперечного сечения вала (dн и dвн – соответственно наружный и внутренний диаметры вала).
Если считать вал балкой с защемленными опорами, то числовой коэффициент в формуле следует принимать большим в 1,5...2,25 раза.
Расчет критич. Частоты вращения карданного вала и осевой нагрузки
Критическая частота вращения вала должна быть в 1,5...2 раза больше максимальной эксплуатационной. Для повышения критической частоты вращения следует уменьшать длину вала, что особенно эффективно, и увеличивать как наружный, так и внутренний диаметры. Внутренний диаметр трубчатого вала можно увеличивать до определенного предела (лимитирует прочность вала).
Скручивающие нагрузки, которые воспринимает вал, зависят от крутящего момента, передаваемого валом. Кроме того, являясь элементом многомассовой упругой системы трансмиссии, вал силового привода участвует в крутильных колебаниях и воспринимает дополнительно скручивающие нагрузки, которые в случае резонанса могут быть значительными, а иногда и разрушающими. Правильный подбор элементов трансмиссии должен исключать возникновение резонансных крутильных колебаний или предусматривать возможность гашения возникающих колебаний. Крутильные колебания трансмиссии, как известно, гасятся демпфером, расположенным в механизме сцепления.
Трубчатый вал изготовляют из малоуглеродистой стали (сталь 15, сталь 20), не подвергая ее закалке. Толщина стенок обычно не превышает 3,5 мм.
Напряжение кручения трубчатого вала
Осевые нагрузки в силовых приводах возникают в шлицевом соединении при перемещениях, связанных с изменением расстояния между шарнирами, например при колебаниях кузова. Исследования показали, что даже при наличии большого количества смазочного материала последний не удерживается на поверхности трения и перемещение в шлицевом соединении происходит в условиях граничного трения. При этом коэффициент трения м = 0,2, а иногда (при появлении задиров) м = 0,4. При передаче большого крутящего момента в шлицевом соединении происходит защемление, и вал, по существу, передает тяговое усилие. При этом двигатель, установленный на упругих подушках, продольно смещается в некоторых автомобилях на 10 мм, а иногда и больше.
Осевые силы являются одной из главных причин того, что долговечность передач в 2....3 раза ниже долговечности основных агрегатов автомобиля. Осевая сила
Дифференциалы трансмиссии автомобиля. Назначение, требования, классификация, расчет деталей на прочность
Дифференциалы - дифференциал механизм трансмиссии, выполняющий функции распределения подводимого к нему крутящего момента между колесами или мостами (в некоторых автомобилях между бортами) и позволяющий ведомым валам вращаться с неодинаковыми угловыми скоростями.
К конструкции дифференциала предъявляют следующие требования:
а) распределение крутящих моментов между колесами и мостами в пропорции, обеспечивающей наилучшие эксплуатационные свойства (максимальную тяговую силу, хорошие устойчивость и управляёмость);
б) общие требования.
Нагрузки в дифференциалах:
В коническом дифференциале определяя нагрузки на зубья сателлитов, полуосевых шестерен, крестовину и нагрузки со стороны сателлитов на корпус дифференциала. Нагрузку на зуб сателлита и полуосевых шестерен определяют из условия, что окружная сила распределена поровну между всеми сателлитами и каждый передает усилие двумя зубьями. Окружная сила, действующая на один сателлит:
где r1 — радиус приложения;
nс — число сателлитов.
Шин крестовины (18ХГТ, 20ХН3А и др.) под сателлитом испытывает:
напряжение смятия : хсм =Рс/(dl1), [хсм] =50...60 МПа,
напряжение среза : ф ср = 4Рс/(рdІ), [ф ср] = 100…120 МПа,
напряжение смятия в месте крепления в корпусе дифференциала под действием окружной силы
у см = Рд/ (dl2), [у cм] =50...60 МПа,
Давление торца сателлита на корпус дифференциала определяется напряжением смятия
у см = Рxc/F, [у cм] = 10...20 МПа,
где Рxc=Рctgбщ sinдc, sin5С (бщ— угол зацепления; дc— половина угла конуса саттелита).
Назначение, классификация и требования к конструкции полуосей. Расчет ведущих полуосей полностью разгруженных от действия изгибающих сил и моментов.
В зависимости от испытываемых полуосью нагрузок принято их условное деление на полуразгруженные (рисунок 6.4, а), - три четверти разгруженные (рисунок 6.4, б) полностью разгруженные (рисунок 6.4, в). Полуразгруженная полуось воспринимающие все усилия и моменты, действующие - дороги. На три четверти разгружена; полуось имеет внешнюю опору меж; ступицей колеса и балкой моста, поэтому изгибающие моменты от реакций Rz, Рт (Ртор) и Рy, воспринимают одновременно и полуось, и балка моста через подшипник.
а- полуразгруженная; б - на три четверти груженая; в – полностью разгруженная
Полностью разгруженная полуось теоретически передает только крутящий момент от дифферециала к ведущим колесам, однако для нее возможны деформации изгиба, обусловленные деформацией балки моста, несоосностью ступицы колеса с полуосевой шестерней, перекосом и смещением шлицевых концов полуосей относительно шестерни и фланца при наличии зазоров в шлицевом соединении.
30. 31. 32 Расчет ведущей полуоси нагруженной на ½ от действия изгибающих сил и моментов (режим разгона, бокового заноса, динамических нагрузок.)
При прямолинейном движении – результирующий изгибающий момент полуоси в вертикальной и горизонтальной плоскостях:
;
момент кручения полуоси
;
сложное напряжение
.
При заносе изгибающие моменты на правом и левом колёсах
; , где
При динамическом нагружении:
вертикальная нагрузка-, где =1,5…3 – коэффициент динамичности.
горизонтальная нагрузка- (при прямолинейном движении принимается: при прямолинейном движении 0,8…0,9, при заносе - 1);
скручивающая нагрузка- ;
При расчёте полуразгруженной полуоси плечо изгиба определяется как расстояние между плоскостями, проходящими через центр опорной площадки колеса и через центр опорного подшипника.
Полуразгруженная полуось разрушается в опасном сечении под подшипником. Здесь полуось должна быть утолщена.
Полуоси изготавливают из легированных сталей – 30ХГС, 40Х, 40ХНМА и др; допускаемые напряжения МПа, МПа.
Назначение и требования к конструкции управляемого моста, расчетные режимы. Расчет балки управляемого моста на прочность (режим – торможение).
К автомобильным мостам предъявляются следующие основные требования: минимальная масса, наименьшие габаритные размеры и оптимальная жесткость. Управляемые мосты, как правило, передние: включают в себя поворотные цапфы и соединяющие детали. Применяются и задние управляемые мосты.
При прямолинейном движении автомобиля балка ведущего моста (см.рис.) изгибается в вертикальной плоскости под воздействием нормальных реакций дороги и на ведущие колеса.
Изгибающий момент в вертикальной плоскости где – плечо изгиба.
Нормальные реакции дороги от нагрузки на ведущий мост равны:
где – коэффициент перераспределения нагрузки на задний мост.
Кроме того, под действием тяговой силы балка ведущего моста испытывает статическую нагрузку и изгибается также в горизонтальной плоскости.
Изгибающий момент в горизонтальной плоскости
Тяговые силы на ведущих колесах равны: - коэф сцепл колес с дорогой.
Кроме изгибающих моментов на балку ведущего моста действует крутящий момент
где – радиус ведущих колес.
В балке ведущего моста наиболее опасными местами являются обычно сечения под площадками для крепления пружин (рессор).
Суммарный результ-й момент от изгиба и круч-я в опасном сеч-и балки моста
Результ-е напряжения от изгиба и кручения для трубчатого круглого сечения
где – момент сопротивления трубчатого сечения.
Расчет оси колеса (шипа поворотной цапфы) на прочность (режим – торможение, динамическая нагрузка)
При торможении суммарный момент изгиба в вертикальной плоскости
,
где ; - тормозная сила на колесе, нагружающая цапфу.
Напряжение изгиба
При заносе напряжение изгиба на цапфе при
; .
При динамической нагрузке напряжение изгиба
.
Расчет сил и моментов, действующих в колесном тормозе барабанного типа (с 2мя активными колодками). Расчет сил и моментов, действующих в колесном тормозе дискового типа.
Схема (а) и статическая характеристика (б) барабанного тормозного механизма с гидравлическим приводом с равными приводными силами и разнесёнными опорами:
1,2 тормозные колодки; 3 – тормозной цилиндр
Каждая из колодок приводится в действие своим тормозным цилиндром. Одинаковые размеры тормозных цилиндров обеспечивают равенство приводных сил P1 и P2, нормальных реакций барабана на колодки N1 и N2, сил трения F1 и F2, а так же углов охвата колодок в1 и в2.
Тормозной момент, создаваемый тормозным механизмом:
Мтор=µ(N1+N2)rб=2 µNrб
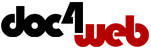
Нравится материал? Поддержи автора!
Ещё документы из категории транспорт :
Чтобы скачать документ, порекомендуйте, пожалуйста, его своим друзьям в любой соц. сети.
После чего кнопка «СКАЧАТЬ» станет доступной!
Кнопочки находятся чуть ниже. Спасибо!
Кнопки:
Скачать документ