Химические процессы в увлажняющем аппарате.
Химические процессы в увлажняющем аппарате печатной машины. Часть 2.
(Продолжение статьи "Химическая реакция в печатной машине")
На офсетных печатных машинах встречаются самые разные системы увлажнения. Строгой классификации их видов нет. Для определенности попробуем сами сгруппировать их по различным признакам. В зависимости от способа нанесения раствора на форму выделим три группы:
К первой отнесем увлажняющие аппараты прямого или независимого типа, в которых увлажняющие и красочные валики связаны между собой лишь формным цилиндром, и раствор подается через накатные увлажняющие валики.
Ко второй относятся аппараты, обеспечивающие подачу раствора бесконтактным способом. Например, набрызгиванием с помощью форсунок (системы Фуко), конденсацией пара на поверхности охлажденной печатной формы и др. Такие системы на современных машинах не используются.
К третьей можно отнести аппараты, передающие раствор косвенным путем через красочную систему машины. Их иногда называют интегрированными или смешанными. Недостаток этих систем в том, что при передозировках увлажняющего раствора краска на валиках быстро начинает эмульгировать, и для продолжения работы ее приходиться полностью заменять.
В зависимости от материала покрытия валиков их можно разделить на:
Моллетоновые системы увлажнения, где часть валиков покрыта влагоемким тряпичным покрытием.
Системы без использования тканевых валиков.
В зависимости от способа регулирования и поддержания уровня подачи раствора:
На системы прерывистого действия с передаточным качающимся валиком.
На системы непрерывного (пленочного) увлажнения.
Существует великое множество видов увлажняющих аппаратов. Некоторые из них давно устарели, а иные и вовсе применялись лишь на опытных образцах. Мы не будем рассматривать такие диковины, и остановимся лишь на некоторых, употребляемых сейчас на распространенных печатных машинах.
Заранее хочется оговорить, что в этом обзоре не ставиться целью сравнение различных видов печатного оборудования. Не существует единого критерия для оценки систем увлажнения, ошибкой является оценка по количеству валиков (можно привести факт, что у более современной машины Heidelberg Speedmaster их меньше, чем у GTO) или по покрытию валиков (более солидная серия Ryobi 500 имеет моллетоновую систему, в то время как в серии 3300 применяется Crestline). Практически у каждой системы есть свои преимущества и недостатки, и не стоит недооценивать конструкторские бюро каждого производителя.
Система увлажнения Molleton
Это наиболее традиционная, испытанная временем, можно сказать, классическая система имеет валики с тканевым покрытием. Иногда даже в названии этой системы звучит термин "обычная". Сегодня большинство машин офсетной печати снабжено этими системами увлажнения. Их преимуществами являются невысокие цены и широкая известность среди работающих в офсетной печати. Эта система неприхотлива в настройке и отличается высокой стабильностью подачи раствора при соблюдении необходимого состава увлажнения и правильных приемах работы. Применяется несколько вариантов данной системы, отличающихся количеством, расположением и материалом валиков. Для покрытия используют трикотажные или тканевые чехлы. В последнее время очень популярны чехлы из синтетического термоусадочного материала. Их главное преимущество в отсутствии швов, пыли и ворса. Такие чехлы имеют несколько больший диаметр и усаживаются до нужного размера после обработки горячей водой.
На рис. 1 показаны основные схемы с моллетоновым увлажнением
Наиболее простая схема (рис. А) состоит из четырех валиков и включает один накатной (находящийся в контакте с печатной формой). Такие увлажняющие аппараты установлены на машинах Multigraphics, Hamada, Ryobi 3200MCD.
Систему, содержащую пять валиков, из них два накатных (рис. Б), можно увидеть на машинах Dominant, Polly, Hamada серии С, В и А, Ryobi серии 500.
На машинах Ryobi 3300MR, 3302М и Itek 3985 применяется другая система (рис. 1В). Здесь также используется пять валиков, но всего один из них накатной. На ее примере рассмотрим более подробно строение моллетоновой системы. Дукторный вал R и раскатной вал О (совершающие возвратно-поступательное движение вдоль оси) имеют хромированное покрытие, а передаточный S, промежуточный D и накатной W обшиты трикотажными чехлами. Для стабильной подачи воды используется циклическое перемещение передаточного валика, который соприкасается то с дукторным валом, купающимся в специальном резервуаре, то с раскатным валиком. Зафиксировав этот валик в одном положении, можно прекратить подачу раствора. Дозирование раствора осуществляется либо изменением скорости вращения дукторного вала, если у него имеется отдельный привод, либо его разового угла поворота, если для привода используется храповой механизм.
Большое значение для устойчивой работы имеет взаимное расположение валиков увлажняющего аппарата. Для обеспечения равномерной и непрерывной подачи увлажняющего раствора необходимо, чтобы сила прижатия между валиками увеличивалась по мере продвижения от дуктора к формному цилиндру. Такую регулировку вполне может выполнить и сам печатник, хотя, конечно, желательна работа профессионального наладчика. Для проверки используется бумажный (плотностью 80 гр/кв.м.) щуп. Давление проверяется по силе, требуемой для того, чтобы вытащить эту полоску бумаги, зажатую между влажными валиками без его обрыва. Металлические или пластиковые щупы плохи тем, что у них усилие вытягивания зависит не только от давления между валиками, но и от других факторов (состояние поверхности щупа, его влажность и т.п.). Максимальное давление должно быть в месте контакта валиков с печатной формой. Конкретные механизмы регулировок на каждой модели печатной машины свои.
Основным недостатком моллетоновых систем является трудоемкость их обслуживания. Этот недостаток можно устранить применением современных синтетических чехлов и строгим соблюдением технологических правил.
Система Dahlgren
Фирма Dahlgren - один из основателей систем непрерывного действия.
Увлажняющий аппарат косвенного действия (рис. 2) содержит всего три валика: резиновый дукторный, формный хромированный цилиндр, промежуточный и резиновый накатной, являющийся общим для красочной и увлажняющих систем. Количество подаваемого увлажняющего раствора регулируется изменением скорости вращения дукторного и промежуточного валиков, которые имеют независимый привод.
Недостатки этой системы:
Малое количество валов, что допускает большую неравномерность подачи по ширине.
Нет режима предварительного смачивания формы. Это приводит к тому, что при включении машины печатная форма сразу же закатывается краской, и, чтобы это предотвратить, приходится перед включением вручную смачивать форму.
Система Aquamagic
В этой системе спиртового увлажнения (рис 3), разработанной фирмой Ryobi, в отличие от предыдущей схемы, используются четыре валика и прерывистая подача раствора. Все валики, кроме дукторного, вращаются со скоростью хода машины. Один из валиков совершает перемещения вдоль оси, и за счет этого выравнивается подача раствора по ширине. Подача увлажняющего раствора меняется изменением скорости вращения дукторного вала. Временно прекратить подачу увлажнения можно, зафиксировав передаточный валик.
Система Aquamatic
Эта система спиртового увлажнения (рис. 4} применяется на печатных машинах компании АВDick. Здесь контакт между аппаратом увлажнения и наката краски осуществляется не на уровне накатного валика, а раньше. Передаточный качающийся валик с одной стороны касается дукторного увлажняющего валика, а с другой - раскатного красочного. Таким образом, количество чисто увлажняющих валиков меньше, чем в предыдущей схеме, и уже два валика работают на обе системы одновременно. Водно-красочный баланс начинает устанавливаться еще раньше, что, несомненно, является положительным моментом. Минусом же, с другой стороны, является еще большая склонность к эмульгированию. Количество увлажняющего раствора, как и в предыдущем случае, регулируется изменением скорости вращения дукторного валика.
Несмотря на внешнюю простоту, эта система пленочного увлажнения {рис. 5) является последней разработкой фирмы Heidelberg. Здесь полностью автоматизированы процессы предварительного раската краски на увлажняющих валиках, режим смачивания формы и смывка увлажняющего аппарата. Чисто увлажняющими можно назвать четыре валика: дукторный (R), дозирующий (S), накатной (W) и раскатной (О). Причем накатной валик всегда находиться в контакте с красочным аппаратом. По информации производителей, при создании этой системы применялось компьютерное моделирование, и был выбран оптимальный вариант.
Система Crestline
Система пленочного увлажнения прямого действия {рис. 6). В ней увлажняющие валики не касаются валиков красочного аппарата, за счет чего можно подавать воду или краску независимо друг от друга. Отличительной особенностью этой системы является ее саморегулируемость. Так, при резком увеличении подачи краски автоматически увеличивается подача увлажняющего раствора, предотвращая тем самым закатывание пробельных элементов на форме. Тем самым освобождается время печатника, который может сконцентрироваться на более важных операциях. При необходимости остается возможность регулирования подачи воды вручную, за счет изменения зазоров между валиками. Эта оригинальная система применяется на печатных машинах Ryobi 3300CR, 3302С, Itek 3980, иногда устанавливаются на машины АВ Dick, Hamada, Multi, Toko и Heidelberg GTO.
Список всех систем увлажнения не исчерпывается рассмотренными в этой статье. Для примера, приведем просто перечень наименований некоторых систем:
Alcomatic, Aquafine, Eric, Rolandmatic, Ryobimatic, Ryobi SuperDampener, Komori-matik, Miehlermatic, Varn Kompac и многие другие, не имеющие специальных названий. Практически каждый крупный производитель печатного оборудования разрабатывает уникальные увлажняющие аппараты или вносит свои изменения в применявшиеся ранее системы.
Скажем несколько слов о регулировании положения валиков в системах без тканевых покрытий. Как правило, в таких машинах нет выведенной наружу ручки изменения давления накатного валика на форму, как на моллетоновых системах. Одно это говорит о том, что здесь предъявляются более жесткие требования к взаимному положению валиков, и лучше всего, если такие регулировки будет выполнять квалифицированный техник. Все же скажу несколько слов об этих настройках: для такой проверки обычного вытягивания щупов оказывается недостаточно. Давление проверяют по полосам контактов, которые оставляют друг на друге валики, покрытые краской. Необходимо, чтобы эти полосы были одинаковой ширины (не клинообразной формы) и чтобы у валиков, расположенных ближе к печатной форме, они были не меньше, чем у предыдущих валиков. Конкретные величины этих полос различны в разных моделях печатных машин (например, у системы Crestline они следующие: давление на форму 4,5 мм, между остальными по 4 мм).
Теперь поговорим об уходе за увлажняющими аппаратами. Для очистки валиков от засохшей краски не рекомендуется пользоваться химикатами сильного действия, предназначенными для красочных систем. Если в процессе печати на валиках скопилось много краски, для удаления лучше использовать салфетку с увлажняющим раствором или спиртовой добавкой вместо смывки на основе керосина. Вообще желательно отказаться от таких смывок и пользоваться водорастворимыми химикатами. Принцип действия таких жидкостей основан на разложении печатных красок, после чего валики легко смываются обычной водой.
После смывки увлажняющего аппарата следует дополнительно обработать валики специальными консервантами для смягчения и защиты валиков. Для обработки хромированных валиков также желательно обзавестись соответствующей химией. Более подробно об употреблении расходных материалов рассказано в статье Д. Ширенова "Скупой платит не дважды, а во много раз больше" (см. "Курсив" # 3-96). Большое значение имеет состояние поверхности валиков, их жесткость и эластичность. Бывали случаи, когда дефекты валиков невозможно было определить визуально, и лишь после их замены машина начинала работать нормально.
15 мая 1998 г.
В апрельском номере журнала "Курсив" была опубликована моя статья "Вспомогательные операции - это не те, которые помогают, а те, которые мешают", посвященная автоматизации вспомогательных операций в процессе офсетной печати. Статья, предлагаемая Вашему вниманию на этот раз, является логическим продолжением этой темы. В ней речь пойдет о системах управления качеством печати.
Начнем с систем, основным назначением которых является достижение и удержание высокого качества печатной продукции. Понятие качества многогранно, это удерживание необходимого цветового тона изображения по площади отпечатка и на протяжении тиража, отсутствие марашек, царапин, тенения и т.п., а также постоянное поддержание точного совмещения цветов на печатных оттисках. Рассмотрим по порядку эти параметры качества, а также системы, автоматизирующие контроль за ними.
Системы, действующие через увлажняющий аппарат
Ключевым моментом для получения хороших отпечатков является поддержание стабильного водно-красочного баланса на поверхности печатной формы. Для достижения этой цели важно постоянство подачи и состава увлажняющего раствора. Этой теме была посвящена одна из прошлых моих статей в журнале Курсив (#_, 1997г. "Химическая реакция в печатной машине"). Напомним основные требования: жесткость пропорций, минимально-возможное количество компонентов, особенно увлажняющего раствора, стабильность подачи и состав увлажняющего раствора и краски.
Для многих уже не новость, что высококачественную полноцветную продукцию невозможно получить без систем рециркуляции увлажняющего раствора. Ввиду широкого распространения таких аппаратов мы не будем подробно рассматривать их устройства. Скажем лишь, что увлажняющий раствор в таких машинах не пополняется из бутылок увлажнения, а циркулирует через специальные системы с баками большой емкости (не менее 20 л), постоянно фильтруется и охлаждается до оптимальной рабочей температуры.
Рис 1. Системы рециркуляции увлажняющего раствора
Наиболее развитые устройства, имеют в своем составе подсистемы автоматического поддержания концентрации спиртовых добавок, кислотности и электропроводности увлажняющего раствора. Перечисленные узлы приведены в порядке возрастания их стоимости и, соответственно, частоты практического использования.
Рециркуляционные аппараты не влияют прямым образом на поддержание необходимого водно-красочного балланса, но, обеспечивая постоянство состава увлажнения, его чистоту и температуру в рабочей зоне вносят свой вклад в стабильность печатного процесса. Автоматическое дозирование подачи увлажнения
Теперь рассмотрим системы, автоматически регулирующие подачу увлажнения на печатную форму. Такие системы обязательно должны иметь устройства обратной связи, и менять параметры своей работы в зависимости от текущей ситуации на печатной форме или печатном оттиске. Существуют схемы получающие информацию от формного цилиндра, они действуют быстрее и стоят дешевле, а также системы, имеющие датчики на ПВУ (приемно-выводном устройстве) и контролирующие выходящие оттиски. Эти механизмы работают точнее и учитывают все компоненты печатного процесса (в том числе качество офсетного полотна и бумаги).
Наиболее простые системы не имеют электронных компонентов и действуют за счет физико-химических процессов на поверхностях увлажняющих валиков. Для примера рассмотрим одну из таких систем увлажнения - Crestline, созданную американской фирмой Accel Graphics.
Рис 2. Система увлажнения Crestline
Система Crestline является системой пленочного увлажнения прямого действия (см. рис 2). В ней увлажняющие валики не касаются валиков красочного аппарата, за счет чего можно подавать воду или краску независимо друг от друга. Отличительной особенностью этой системы является ее саморегулируемость при одновременной подаче на форму краски и увлажняющего раствора. Валики увлажняющего аппарата сделаны из специальной резины, которая в сухом виде не смачивается водой и не способна передавать увлажняющий раствор от дуктора к форме. Но, офсетная краска, попадая на поверхность этих валиков, меняет их гидрофильность и способствует нормальной передаче влаги. Причем гидрофильная способность напрямую зависит от количества краски на этих валиках. Надеюсь, читатели уже догадались о схеме работы такой системы.
При резком увеличении подачи краски, на поверхности печатной формы скапливается много краски и нарушается водно-красочный баланс, что приводит к увеличению количества краски сначала на накатном, а затем и на других увлажняющих валиках. Гидрофильная способность этих валиков увеличивается, что ведет к увеличению подачи увлажняющего раствора. Таким образом предотвращается закатывание пробельных элементов на форме, и водно-красочный баланс автоматически приходит в норму. Аналогично система реагирует и на изменение подачи краски в меньшую сторону и так же самостоятельно уменьшает подачу увлажнения. Тем самым подача увлажняющего раствора автоматически регулируется, поддерживая стабильность работы.
За счет этого печатник может сконцентрироваться на более важных операциях, и меньше отвлекается на регулирование цветового тона на отпечатке. При необходимости, остается возможность регулирования подачи воды вручную, за счет изменения зазоров между валиками. Эта оригинальная система применяется на печатных машинах Ryobi 3300CR, 3302C. Разработаны модификации этой системы для установки на машины ABDick, Hamada, Multi, Toko и Heidelberg GTO.
Система ААС
Следующим рассмотрим наиболее современное устройство, ААС (Aqua Automatic System), созданное японской фирмой Ryobi. Это компьютеризированная система, предназначенная для автоматического поддержания толщины водной пленки на форме, была создана в 1996 году.
Рис 3. Система автоматического поддержания водно-красочного балланса Ryobi ААС
Система имеет электронный датчик, расположенные вблизи формного цилиндра печатной машины. С его помощью во время печати непрерывно контролируется количество влаги на алюминиевой поверхности печатной формы. Чувствительность этого датчика такова, что регистрируются изменения толщины водной пленки на сотые доли миллиметра. Значение этой толщина постоянно высвечивается на цифровом дисплее. Таким образом мы получаем инструмент, достоверно информирующий печатника об одном из параметров печатного процесса (напомним, что на традиционных печатных машинах довольствуются лишь показаниями скорости вращения дукторного или дозурующих увлажняющих валов). При запусках печатных машин с этой системой наблюдался устойчивый процесс печати с мизерной подачей увлажняющего раствора. Форма казалась абсолютно сухой, но в тоже время шла нормальная печать без тенения и марашек на оттисках.
Кроме точного измерения, система ААС может автоматически регулировать подачу увлажнения. В электронном блоке управления, в зависимости от показаний датчика толщины водной пленки, вырабатываются командные импульсы на изменение скорости вращения дозирующего валика увлажняющего аппарата. За счет этого, во время работы печатнику достаточно один раз выйти при приладке на необходимый цветовой тон и включить автоматику, как система запомнит необходимое для работы количество увлажнения и будет в дальнейшем самостоятельно его поддерживать. Причем заметьте, что система реагирует быстрее, чем формный цилиндр успевает сделать один оборот, за счет этого моментально устраняются изменения водно-красочного баланса.
Причины же возникновения дисбалланса окружают нас со всех сторон. Это может быть увеличение или уменьшение скорости работы машины, подача другой бумаги с иными свойствами поверхности, изменение температуры поверхности валиков и формы, влажности и температуры окружающей среды (возникающие даже при открывании дверей или форточек в производственном помещении), т.е. факторы, реально встречающие при печати тиражей в любых типографиях. Так как система основывается на измерениях в конечном звене подачи увлажнения, она корректирует даже неоднородность состава увлажняющего раствора, вызывающие изменение ее поверхностного натяжения и смачивающей способности.
Системы, действующие на красочный аппарат
В устройствах, действующих через увлажняющий аппарат, как правило, контролировался лишь один параметр - количество подаваемого увлажняющего раствора. Перед системами, влияющими на красочный аппарат, стоит более сложная задача. Это не только регулирование общей подачей краски, но и зональное изменение ее по ширине изображения. Многие, наверное, помнят традиционные винты на красочном ящике, положение которых приходиться устанавливать перед печатью каждого тиража.
Перед тем, как рассматривать подробные реализации различных систем, попробуем сформулировать задачу, стоящую перед нами, и вычленить отдельные функции, которые необходимо автоматизировать.
Удобство управления
Во-первых, необходимо обеспечить удобство зонной регулировки краски, ведь регулировка краски с помощью винтов, не имеющих даже примитивной шкалы, занимает много времени и потерь бумаги. Удобнее, если каждый регулировочный винт имеет круговую шкалу. Еще более приятно работать с ползунковыми регуляторами, тогда процесс выставления краски по этим линейкам занимает меньше времени.
Следующим этапом усовершенствования этого процесса можно назвать применение специальных выносных пультов управления. С их использованием, весь процесс регулирования сводиться лишь к нажатию нескольких клавиш, а исполнительные механизмы в виде отдельных серводвигателей на каждом сегменте красочных ножей сделают все сами. Такие пульты устанавливаются вблизи приемно-выводного устройства (ПВУ) машины, и печатник имеет возможность, не сходя с места, регулировать краску на всех секциях большой машины и в то же время наблюдать за выходящей продукцией. Картина с печатниками, бегающими вдоль длинной машины между секциями и приемкой, уходит в прошлое. Сейчас не только четырехкрасочные, но и двухкрасочные машины большого формата оснащаются таким устройством штатно. На сегодняшний день практически каждый производитель тяжелой техники имеет выносной пульт управления (Komori - PQS, Heidelberg - CPTronic, Rolland - PECOM, KBA - Ergotronic с встроенной Colortronic, Polly - INKFLOW). Для примера, рассмотрим устройство PCS (Printing Control System) от фирмы Ryobi.
Рис 4. Выносные пульты управления
Такие пульты, как правило, имеют подставку для расположения полученного с машины оттиска и цветопробы оригинала, специальное освещение в этой зоне, а также ряд клавиш для изменения подачи краски в каждом сегменте. Многие пульты позволяют изменять высоту рабочей поверхности, ее наклон и оснащены дополнительными предметами, такими как шкафы и полки для образцов, лампы и т.п. Для контроля изменений подачи краски над каждой парой клавиш расположены цифровые дисплеи или электронные шкалы контроля. Отдельными клавишами изменяется общая подача краски и выбирается регулируемая секция печатной машины. Положительными сторонами такого устройства, во-первых, является наглядность процесса, так как необходимые клавиши расположены прямо под оттиском с печатной машины, и, во-вторых, большая точность таких регулировок. Значение могут меняться от 0 до 99 для каждого сегмента, что невозможно достигнуть на шкалах ручных регуляторов красочных ящиков.
Дополнительными удобствами выносного пульта является также возможность записывать полученные настройки на дискету и использовать повторно при выполнении этого заказа. Также можно программировать и держать в электронной памяти устройства цветовые профили под заданные марки красок и используемых бумаг, и одним нажатием перестраиваться к необходимым материалам. В этом же режиме можно менять параметры светлых, темных или полутоновых участков изображения, пользуясь стандартными профилями. Например, бывают ситуации, когда надо осветлить темные участки изображения, не трогая полутонов и бликов. В этом случае электроника, делает более мягкие и правильные коррективы. Часто такой пульт позволяет дистанционно выполнять приводку изображений.
Зонная регулировка подачи краски
Во-вторых, рассмотрим устройства, которые автоматически выполняли бы работу печатника по настройки подачи краски. Рассмотренные выше примеры лишь механизировали труд печатника, и облегчали удобство зонной регулировки.
Попыток создать устройства облегчающие процесс начального выставления подачи краски по ширине изображения, было много. Есть чисто программные реализации, когда, обрабатывая Poscript-файл, получают ряд чисел, характеризующих необходимую зависимость. Ведь с математической точки зрения этот процесс прост: для этого необходимо поделить изображение на вертикальные полоски по числу красочных винтов (или сегментов) и проинтегрировать количество печатных элементов в каждой из получившихся полосок. Далее получившиеся значения необходимо нормализовать, т.е. привести их к требуемому диапазону, например от 0 до 100, (процесс, также не занимающий много вычислений) и вывести их на дисплей или принтер.
На самом деле, конечно, не все так просто, ведь при этом не учитываются особенности ФНА, формных процессов и т.п., их влияние на конечный результат. Также процесс получения данных со станции верстки невозможен при использовании составной фотоформы, когда оригиналом для печатной формы служат несколько смонтированных пленок. Сейчас мы не будем углубляться в возникающие сложности и способы их решения. На сегодняшний день находят применение другие, может быть дорогие, но и более надежные и отлаженные способы решения данной задачи. Оригиналом для считывающих устройств можно использовать готовые печатные формы. Главным компонентом таких систем (Komori - PSS, Heidelberg - CPC3, Rolland - EPS, КВА - Scantronic, Ryobi - DEMIA, и др.) является специальный сканер.
Рис 5. Сканеры печатных форм DEMIA, PSS
В такой прибор вставляется готовая печатная форма, затем задается количество сегментов красочных ножей на используемой печатной машине и нажимается клавиша "Старт". Сканирующая линейка проезжает над нашей пластиной, и полученные данные отображаются на дисплее или распечатываются с помощью встроенного в прибор принтера.
Дальнейшие действия оператора понятны, он либо выставляет необходимые регулировки вручную на красочном ящике, либо на дисплее выносного пульта управления. В случае же использования пульта и сканера одной фирмы-производителя, и вовсе процедура сводиться лишь к переноске дискеты от одного устройства к другому или соединения этих устройств кабелем.
В заключение же этого подраздела рассмотрим устройство, которое не только облегчает процесс начальной подготовки красочного аппарата к работе, но и автоматизирует процесс регулирования подачи краски во время печати тиража. Система PDC-S, разработанная японской фирмой Komori, представляет собой выносной пульт управления, имеющий встроенный спектроденситометр.
Рис 6. Система контроля подачи краски PDC-S (от Komori и Ryobi)
Сначала этой системе дают настроиться, прочитав данные со цветопробы или Poscript-файла. Далее весь процесс регулирования краски сводиться к размещению время от времени на выносной пульт управления печатного оттисков, полученного во время тиража, и нажатия клавиш. Над бумагой проезжает считывающая головка денситометра, которая снимает информацию со специальной шкалы, размещенной на кромке листа. По необходимости, электроника дает команды на сервоприводы красочных ножей и корректирует подачу краски. Шкалы, в электронном виде, поставляются вместе с машиной и могут размещаться как в "голове", так и в "хвосте" изображения.
Подобные системы есть почти у всех производителей печатных машин.
Совмещение изображений на печатном оттиске
Теперь заглянем на другой аспект качества продукции и рассмотрим устройства облегчающие получение точного совмещения цветоделенных изображений на печатном оттиске. В данном подразделе мы не будем обсуждать разницу между одно-, двух- и четырех красочными печатными машинами и говорить о различных системах равнения бумаги и схемах ее проводки. Считаем, что наша машина работает идеально и выдерживает все допуски по этому критерию. Взглянем на весь процесс получения и работы с печатными формами в целом.
Неотъемлемой частью машин для печати высококачественной продукции является системы штифтовой приводки. Основные составляющие таких систем и рабочие операции широко известны, но все же, пусть не обижаются на меня опытные полиграфисты, позволю себе повторить их и рассказать о технологии работы с формным оборудованием.
Исходным материалом для изготовления офсетных форм являются фотоформы, получаемые после компьютерной верстке на фотонаборных автоматах. Неотъемлемой частью процесса является монтаж пленок, который выполняется на специальном столе с нижней подсветкой. Контроль точности совмещения выполняется на этом этапе визуально с помощью лупы. При этом технология работы выглядит так:
Перфоратором пробивают монтажные отверстия в монтажной пленке (астролоне) и в офсетных пластинах.
На монтажном столе размещают штифты, соответствующие пробитым отверстиям, и помещают на них первый лист монтажной пленки.
Ориентируясь по координатной сетке, размещают диапозитивы одного из цветов и прикрепляют их скотчем к монтажной пленке.
Поверх первого смонтированного листа кладут следующий лист монтажной пленки и размещают на нем диапозитивы следующего цвета, добиваясь точного совмещения приводочных крестов первого и второго цветов.
Затем второй лист снимают и по очереди монтируют остальные цвета, накладывая их на первый лист монтажа.
Перфорируют комплект офсетных пластин.
Помещают в копировальную раму пробитую офсетную пластину чувствительным слоем вверх и вкладывают в ее отверстия специальные штифты уменьшенной высоты.
Накладывают на нее, надевая отверстия на штифты, один из смонтированных листов пленками вниз.<
Выполняют экспонирование в копировальной раме под ультрафиолетовой лампой.
Вручную в кюветах, либо в специальных процессорах проявляют пластину.
Затем аналогично изготавливают остальные формы.
Закрепляют пластины на формных цилиндрах печатной машины, устанавливая их точно по имеющимся штифтам.
В результате, при аккуратном выполнении всех этих операций, далее в процессе печати приладка занимает минимум времени.
Подробное перечисление этих операций даны не случайно, как видите, процесс выполнения этой работы далеко не быстротечен, трудоемок и оставляет возможность допущения ошибок. Поэтому в современных типографиях, при наличии большого количества работы на формном участке, рекомендуется использовать различные системы, облегчающие труд монтажиста. Идеальным вариантом исключения монтажных операций является применение, нашумевших в наши дни, аппаратов "Computer to Plate", когда готовые платины сразу выходят из фотовыводных аппаратов. В таком случае требуется только перфорация офсетных форм и установка их на печатную машину. Возможность допущения ошибок здесь минимальна и приладка перед печатью практически не требуется.
Но, в силу того, что устройства CtP пока не нашли широкого применения, ввиду дороговизны и некоторых других недостатков, используются и другие, промежуточные решения.
Использование ФНА с перфорированием
Одним из способов является использование встроенных перфорирующих систем обычных фотонаборных аппаратов. К сожалению, не всегда схема перфорации ФНА совпадает со схемами, применяемыми на печатных машинах (СНОСКА: Наиболее популярной является на сегодняшний день схема пробивки отверстий под названием Bacher, применяющаяся на фотонаборах фирм AGFA, ECRM и печатных машинах Ryobi, Heidelberg, Sacurai и др. Кроме этого известны некоторые другие системы: PROTOCOL, MONTALOCH.), поэтому этот путь требует дополнительных затрат и отладки. Хорошо, если имеется дополнительный механический перфоратор, способный пробить офсетные пластины также как и ФНА, в таком случае, из процесса полностью выпадает процесс монтажа (наиболее длительный по времени и сильно влияющий на количество ошибок). В таком варианте печатные формы готовятся с использованием этого перфоратора, для совмещения в копировальной раме используются штифты под него. Не беда, если применяемая в этом случае система перфорации не совпадает со штифтовой системой печатной машины, проблема легко решается с помощью второго, теперь уже машинного перфоратора.
Перфорирование, базируясь на метки совмещения
Другим, кардинально отличающимся, решением является использование перфораторов с пробивкой отверстий на готовых печатных формах, ориентируясь на имеющиеся на них метки совмещения. В таком варианте этап монтажа также полностью исключается. Для работы достаточно ручного наложения фотоформ на офсетные пластины в копировальной раме с допуском плюс-минус 2 мм. Основная работа по выполнению работы по совмещению выполняется на специальном оборудовании. В качестве примера рассмотрим прецизионный перфоратор RP730 (High Precision Register Punch), используемый с печатными машинами Ryobi.
Рис 7. Прецизионный перфоратор печатных форм, использующий в качестве базы кресты совмещения изображений
С его помощью достаточно навести с помощью клавиш специальные оптические прицелы на два противоположных креста совмещения изображения (для точного перемещения используются серводвигатели с шагом 0.01 мм) и нажать клавишу, как форма автоматически переместиться в горизонтальном, вертикальном и угловом направлении и перфорируется в необходимой точке.
Применяются и более дешевые механические перфораторы (например, RP220 у той же фирмы Ryobi или у других производителей), использующие тот же принцип.
Системы контроля печатных оттисков
Обзор различных автоматических систем печатной техники завершаем рассмотрением сложнейших систем контроля выходных оттисков.
Фирма Heidelberg производит специальные системы, основанные на стробоскопическом эффекте. Принцип их действия заключается в считывании заданных участков оттисков во время печати и дискретном выводе полученного изображения на телеэкран. В результате этого, на работающей с большой скоростью печатной машине, мы видим статическое изображение фрагментов изображения. Чаще всего, такому наблюдению подвергаются кресты совмещения и другие критические участки. За счет этого некоторые операции, такие как тонкая приводка или управление подачей краски и увлажнения можно производить без остановки машины.
Кроме этого, на последних модификациях машин SM-74 и SM-102 начала использоваться система Autoregister CPC-4. Считывающие датчики на передаточных цилиндрах машины настраиваются на две центральные метки совмещения и отслеживают совмещение разных красок на печатном оттиске. Если обнаруживается неприводка, то автоматически дается команда на радиальное или осевое смещение цилиндров и дисбалланс устраняется. Команда на корректировку вырабатывается после прохождения каждого листа бумаги. За счет этого, расположения цветов на изображении постоянно колеблется с мизерной амплитудой (сотые доли миллимитра) около точного значения. Таким образом эта система с обратной связью постоянно контролирует качество продукции.
Более развитая система PQA, установленная на печатных машинах Komori Lithrone, не только отслеживает фрагменты изображений, но и может анализировать содержимое всей картинки в целом. Эта система сканирует запечатанные листы и мгновенно сравнивает каждый лист с электронным отпечатком подписного оригинала, хранящимся в его памяти, определяя, например, марашки, капли воды на оттиске, тенение, отмарывание, царапины, несовмещение красок и дефекты бумаги. Такое устройство устанавливается на машины, имеющие два приемных стапеля (см. выше), и может производить сортировку печатных листов. В случае возможности устранения дефекта, например если идет рассовмещении красок, система автоматически исправляет дефект, если же идут трудно устранимые проблемы, то машина сигнализирует об этом печатнику, показывая на экране место их возникновения. Качественная продукция укладывается в основной стапель, а отбраковка во вспомогательный (рис 10, предыдущей статьи).
Рис 8. Камеры автоматического контроля качества
Упрощенная система контроля качества, Qualitronic, снабженная ССD-видеокамерами, и подающая звуковые сигналы при браке, есть также у фирмы KBA-Planeta. Она в случае брака останавливает печать тиража или отмечает испорченные листы.
Сейчас дело осталось лишь в создании системы, которая бы наряду с обнаружением неисправности, еще и устраняла бы причины самых разных проблем, например, регулировала бы приводку (о чем уже говорилось выше); подачу краски и увлажнения по зонам, подобно системам PDC-S, только на ходу; устраняла бы марашки и т.п. Учитывая, что прогресс остановить невозможно, даже такие фантастические системы вполне могут появиться в будущем.
Комплексная автоматизация
В статье об автоматизации отдельных печатных машин было бы неуместно говорить о комплексной автоматизации печатных цехов. Все рассмотренные выше автоматические устройства печатных машин значительно облегчают условия труда печатника и позволяют достигнуть наивысшего качества и производительности оборудования. Но в случае их комплексного применения эффект увеличивается многократно. Централизованные системы управления, основанные на новейших электронных технологиях, дают максимальную продуктивность и прибыльность производства. Сегодня у фирм Polland, KBA, и Komori существуют законченные решения создания автоматизированного производства печатной продукции. В этом случае всеми процессами, происходящими в производственных помещениях руководит одна центральная вычислительная машина. Система совместно предлагаемая фирмами Rolland и Scitex называется PEM-PECOM (Process Electronic Management), KBA - OPERA (OPen ERgonomic Automatic system), Komori - PAI (Print Automatic Integration System). Центральная ЭВМ в реальном времени руководит всеми процессами, локальная сеть доносит ее команды и возвращает данные о текущей ситуации на участках верстки, изготовления форм, печатном и финишном цеху.
Рассмотрим подобнее новейший комплекс от Komori - печатный цех будущего Printroom 2000 на базе машин Lithrone, презентация которой была 17 апреля 1997 г. в европейской штаб-квартире фирмы в г. Утрехте (Нидерланды).
Со станций верстки электронное изображение направляется на интегрированную систему вывода пленок, металлических печатных форм и цветопробы PTP. Паралельно с этим, данные об изображении поступают на пульт управления печатной машины и автоматически выставляется зональная подача краски, настраивается спектроденситометр PDC-S и система контроля качества продукции PQA. Печатная машина готовиться к предстоящей работе: смываются красочные валики и цилиндры, раскатывается необходимая краска, снимаются старые формы и т.п. По данным, из центральной ЭВМ на систему AMR (Automated Make-Ready) автоматически настраиваются механизмы проводки и равнения бумаги, выставляются необходимые зазоры между цилиндрами. Связующим звеном всех этих узлов является внутренняя закрытая локальная сеть K-LAN.
Оператору остается лишь вложить автоматически приготовленные печатные формы в приемные лотки и подкатить к самонакладу необходимую бумагу. Приладка выполняется в полуавтоматическом режиме, машина сама добивается необходимого совмещения и по оттискам, расположенным на пульте управления с системой PDC-S регулирует необходимую подачу краски и увлажнения. После печати тиража, машина снимает с себя формы, смывает офсетные и печатные цилиндры.
Постоянно ведется контроль за всеми процессами, происходящими в типографии. Отслеживается техническое состояние оборудования, качество печатной продукции, система оперативно решает или сигнализирует о возникающих нештатных ситуациях, предлагая методы решения проблемы. Информация дублируется на мониторах управления печатной машины и в центре управления производством.
Иногда эти системы интегрируют в сложные программные комплексы управлением производства. Так например система PAI (Komori) используется совместно с программой KEREN (AHD System). В этом варианте система кроме управления производством, ведет прием и размещение заказов, учет бумаги и других расходных материалов, занимается выписыванием бухгалтерских счетов и накладных актов. Программа контролирует загруженность каждой единицы оборудования, дает оперативные ответы на любые производственные вопросы и делает необходимые отчеты.
Цифровая передача данных позволяет освободить руководящий и рабочий персонал от административной деятельности, уменьшает горы бумаг на столах менеджеров. Вся электронная информация, заведенная один раз в систему, может использоваться для повторных заказов и для анализа работы типографии.
К сожалению, пока такие проекты для руководителей отечественных полиграфических предприятий лишь мечты: автоматизированных производств в нашей стране нет. Но учитывая растущие темпы перевооружения полиграфических производств, и насущную необходимость в таких комплексах, можно надеяться, что они рано или поздно появляться. По крайней мере, программные реализации систем автоматического управления полиграфическим предприятием уже используются в некоторых типографиях России.
Рис 9. Автоматизированный печатных цех
Заключение
В заключении, хочется сказать несколько общих слов о написанной статье. Источниками информации для меня служили опыт работы по обслуживанию печатной техники, общение с представителями фирм, производящих и поставляющих это оборудование, техническая документация, бюллетени и другие материалы. Если Вы заметите некоторые неточности, виной тому не моя тенденциозность, а недостаток информации об автоматических устройствах некоторых производителей. Целью публикации был обзор известных мне систем автоматизации печатного оборудования и желание познакомить наших полиграфистов с новыми веяниями в этой отрасли. Если у кого возникнет желание дополнить или исправить эту информацию, я жду Ваших откликов.
15 апреля 1998 г.
Новости
Оборудование Ryobi и Horizon выводит «Ви... [8 февраля 2005 г.]
RYOBI 750 – непревзойденное качество кар... [13 февраля 2004 г.]
Новинки Ryobi на выставке IGAS-2003 [22 октября 2003 г.]
АПОСТРОФ ПРИНТ на 7-ой выставке-семинаре... [15 сентября 2003 г.]
Новая международная награда печатных маш... [27 августа 2003 г.]
Автоматизация – европейский подход [1 августа 2003 г.]
Японский сертификат для российской типог... [28 июля 2003 г.]
Сакура зацвела для российских полиграфис... [9 апреля 2003 г.]
Ryobi 522HE - новая модель бестселлеров ... [10 июня 2002 г.]
Выставка 'Полиграфиздат-2002. Реклама. Д... [3 июня 2002 г.]
Статьи
Вспомогательные операции - это не те, которые помогают, а те, которые мешают.
Самые сильные ощущения при буксировке бечевой испытываешь, когда лодку тянут барышни:Для того, чтобы тянуть бечеву, необходимо не менее трех барышень: две тянут веревку, а третья прыгает вокруг них и заливается смехом.
Джером К. Джером "Трое в лодке, не считая собаки"
Введение
Не помню, кто именно сказал крылатую фразу, что лень является основным двигателем прогресса, но могу с этим согласиться. У многих ученых и конструкторов, часто первым толчком к изобретению служит желание упростить какую-либо работу или действие. Там где большинство, не задумываясь, выполняет рутинную работу, у этих людей возникает желание облегчить жизнь всем. Наверняка именно так были изобретены в свое время колесо, самолет, электричество, радио, посудомоющая машина и дистанционный пульт управления телевизора.
В данной статье мы не будем рассматривать все открытия, созданные за время существования человечества, акцентируем внимание лишь на тех изобретениях, которые облегчают физические действия человека, все то, что можно назвать одним словом - автоматизация рабочих процессов. Процесс автоматизации труда начался еще с первобытных времен, когда люди перекладывали тяжелые физические операции на плечи своих помощников. Сначала это были домашние животные и примитивные приспособления. Затем по мере появления более сложных задач, когда приручать было уже некого, начали появляться различные механизмы и машины. Прогресс шел ускоряющими темпами, и сейчас мы живем уже в то время, когда без участия человека работают автоматические производственные линии и роботоризированные цеха, выполняющие самостоятельно не только механические функции, но и умеющих принимать логические решения. Дело дошло до того, что некоторые фантасты уже пугают перспективами уничтожения человечества в борьбе с машинами, имеющими искуственный интеллект.
Конкретнее, речь пойдет о последних новинках и изобретениях в области печатного дела. Поговорим об автоматизации отдельных производственных операции и всего рабочего процесса в целом. Рассмотрим, чего же достигли на этом поприще создатели современного печатного оборудования и сделать прогнозы, какие изобретения можно ожидать в скором и отдаленном будущем. Скажем сразу, что пока разительных, революционных перемен в печатном оборудовании, в отличие, например, от издательского и допечатного секторов, не было. Цифровые печатные машины, о которых в последнее время выходит много публикаций, здесь рассматриваться не будут, ввиду ограниченности сферы их применения и малым распространением. Ограничим рамки статьи традиционным типографским оборудованием. В этой области, наверное, последним значительным открытием со времен появления гутенберговской машины стало появление и широкое распространение офсетного способа печати. Причем этот момент был уже полвека назад. Посмотрим, как далеко ушла сегодняшняя печатная индустрия и что может противопоставить современный печатный станок тому же старенькому Romayor-у, который до сих пор, вот уже несколько десятилетий верой и правдой служит многим нашим полиграфическим предприятиям.
Хочется сразу оговориться, что целью этой статьи не ставиться задача дискредитировать старую технику. Ведь по надежности и ресурсу выработки тем же Romayor, Dominant или, скажем, Heilelberg GTO, которые выпускаются уже четверть века нет и не будет равных. Но в современных условиях наряду с критериями надежности на десятилетия, от оборудования требуются и некоторые другие производственные параметры. Я имею в виду производительность, качество продукции, ее рентабельность и т.п. Действительно, ведь полиграфия, это не космонавтика, где до сих пор летают на королевских носителях, из-за того, что любое усовершенствование грозит снизить безопасность полетов. Это осознают все производители полиграфической техники и каждая вновь созданная единица несет в себе все больше автоматических систем, облегчающих жизнь печатникам и повышающих качество продукции и производительность машин.
Раньше, да и сейчас в некоторых типографиях, имеющих старое оборудованием, руководство буквально "молилось" на опытных печатников, от настроения которых зачастую зависело качество продукции и оперативность ее изготовления. Помню, как один директор хвалился своим работником: "Он творит чудеса взаимодействия с машиной, ему достаточно, взглянув на оригинал изображения, разок прикоснуться к винтам регулирования краски, как оттиски выходят один к одному, даже с помощью денситометра невозможно найти разницу с цветопробой. Другие печатники на той же машине по часу выходят на необходимый режим и переводят кучу бумаги в макулатуру".
Конечно хорошо, когда у фирмы есть такие работники, но что случиться, если этот печатник заболеет или вовсе уволиться? Положение дела, когда сотрудники работают на грани шаманства является скорее минусом, чем плюсом, т.к. это подрывает стабильность и плановость производства. Если процессы трудно измерить и запрограммировать, описав необходимые рабочие действия, то язык не поворачивается назвать это надежным производством. Время, когда качество продукции и производительность печатной машины целиком зависело от мастерства и настроения оператора постепенно уходит. Хотя требование в хороших печатниках будет всегда, на современных машинах, снабженных множеством автоматических устройств, процент выхода качественной продукции уже в меньшей мере зависит от стажа и опыта работников, обслуживающих это оборудование.
Мы рассмотрим по порядку дополнительные устройства и системы, устанавливаемые на печатные машины для облегчения труда персонала, автоматизации и ускорения рабочих операций, а также достижения максимального качества и повышения стабильности работы оборудования.
Автоматизация рабочих процессов
Управление печатной машиной
Сначала поговорим об органах управления печатными машинами. Именно они первыми бросаются в глаза при сравнении современного оборудования со старым. Например, маленькие клавиши и сенсоры управления, гладкие обтекаемые формы Heidelberg SM или Ryobi 520X разительно отличаются от GTO или Domiant. Причем на новых машинах автоматизированы не только процедуры включения натиска, но даже приводка осуществляется посредством клавиш. Поговорим об этом
Если формный участок не оснащен устройством CtP или прецизионным перфоратором печатных форм, использующий в качестве базы кресты совмещения изображений, то некоторые неточности в изготовлении офсетных форм останутся и не избежать приводочных операций перед печатью. Новейшие печатные печатной машине имеют, как правило, устройства дистанционного управления приладками. Органы управления выполнены в виде клавиш и цифровых дисплеев и, при работе с такими устройствами, процедура приладки сводиться лишь к замеру с помощью лупы со шкалой, величины расхождения между крестами разных цветов и вводу этих цифровых значений с клавиатуры. После этого серводвигатели автоматически смещают формный цилиндр и передние упоры равнения бумаги в заданное положение. Наиболее сложно реализуем процесс угловой приводки, но сейчас существуют устройства, решающие и эту задачу.
Рис 1. Пульты управления приводкой
Подобное устройство может быть расположено как на встроенном пульте управления печатной машины, так и иметь вид отдельно стоящего выносного пульта. Рисунок устройства управления печатной машины Ryobi 522HXX приводится, чтобы показать наглядность и интуитивность управления современной печатной машиной. Для достижения точного совмещения, необходимо задать растояние между двумя противоположными по ширине листа крестами совмещения на печатном оттиске и указать величину смещения цветов в сотых долях миллиметра. Практически уже вторая попытка заканчивается точным совмещением на оттиске.
Выносные пульты управления мы рассматривали раньше, обычно эти приборы объединяют как регулировку зонной подачи краски и возможностью стыковки со сканером форм, так и управление смещениями изображений.
Смена печатных форм
Существуют автоматизированные механизмы, предназначенные для облегчения и ускорения процессов установки печатных форм в машину и выброса отработанных пластин из нее. Как правило, такие устройства (Komori (APC), Heidelberg (Autoplate), Rolland (PPL), KBA, Ryobi и др.) выполняют цикл снятие-установку печатных форм в полуавтоматическом, либо полностью автоматическом режиме в течение всего 2-3 минут на всех секциях печатной машины. В первом случае автоматизируется лишь процесс зажатия и натяжения пластин на формном цилиндре, установку же в штифты выполняет печатник, во втором отрабатывается весь цикл, и работа печатника заключается лишь в укладке в приемный поддон новой формы и удаление снятой.
Точность установки формы лежит в пределах 0.05 мм, что вполне достаточно для того, чтобы начать печатание большинства работ без дополнительной приладки.
Рис 2. Система автоматической смены форм Full-APC
Сейчас в этой статье рассмотрим лишь одно из таких устройств: систему автоматической смены форм Full-APC от фирмы Komori (рис 2). Для активации работы этой системы от печатника требуется лишь вложить печатные формы в подающие лотки (рис А), это можно сделать во время печати предыдущего тиража, и нажать соотвтствующую клавишу. Машина проверит по специальным меткам правильность расположения форм, при помощи пневмоцилиндров откроет защитный кожух ограждения и подведет загрузчик в рабочую позицию (рис Б). Далее у формного цилиндра откроются клапана зажима формы (рис В), отработанная пластина выдвинется в приемный карман (рис. Г) и запрется там, новая форма из подающего отсека установиться по штифтам в передний захват (рис Д). За счет вращения цилиндра, пластина установиться по месту (рис Е), задняя ее кромка также прижмется к поверхности цилиндра и захватиться клапаном, форма натянется с требуемым усилием (рис Ж). В конце процесса загрузчик вернется в исходное состояние и защитные ограждения также закроются (рис З). Отработанные формы будут скапливаться в приемном кармане и их можно будет удалить как сразу, так и в конце смены.
Рис 3. Процедура автоматической смены форм
Скажем лишь, что сейчас такими автоматическими системами оснащаются не только машины, предназначенные для высококачественной печати, но и более простая техника, рассчитанная на работы бизнес класса. Таковыми можно назвать печатные машины Ryobi 3200, Heidelberg QM-46. Особняком стоит одна из разновидностей цифровых печатных машин Heidelberg QM-46DI, которая использует рулонный формный материал, закрепленный внутри формного цилиндра. Здесь формы меняются подобно пленке в фотоаппарате, каждый тираж печатается со своего "кадра", старая же печатная форма автоматически сматывается в приемный рулон.
Рис 4. Система смены печатных форм QM-46DI
Автоматическая смывка
Далее рассмотрим системы облегчающие уход за печатной машиной и смену красок перед печатью следующего тиража. Речь пойдет об устройствах автоматической смывки красочных и увлажняющих валиков, а также, формных, офсетных и печатных цилиндров.
Начнем с систем, предназначенных для смывки офсетных полотен в печатных машинах. Подобные схемы существуют практически у всех производителей печатной техники, самых разных реализаций. Наиболее простые устройства имеют лишь один щеточный валик, который купается в ванне со смывочным раствором и касается офсетного полотна (встречается на машинах Rolland), более сложные имеют по 3 валика и системы не только промывки, но и протирающие механизмы. Сейчас подробно рассмотрим устройство, устанавливаемое в оборудование фирмы Ryobi.
Устройство содержит систему трубопроводов для подвода или слива смывочного раствора, собственно сам смывочный аппарат и электронный пульт управления. Смывочный аппарат состоит из специального корыта, одного поролонового и двух резиновых валиков и рулонов для подачи и смотки протирочной х/б ткани.
Рис 5. Устройство автоматической смывки офсетного полотна. (А - от Roland, Б - от Heidelberg)
Процесс очистки офсетного полотна заключается в нанесении смывочного раствора на его поверхность, и протирки его х/б материалом. Работа печатника опять же сводиться лишь к нажатию необходимой клавиши на пульте управления. Для обеспечения эффективной работы можно задать необходимую продолжительность и другие параметры смывки.
Интересное устройство устанавливается на печатных машинах Heidelberg. Устройство и принцип действия его понятны из рис 5 Б. Специальная ткань проматывается из одного рулона в другой, касаясь при этом офсетного или печатного цилиндра. Смывочный раствор подается на ее внутреннюю поверхность посредством системы трубопроводов и распылителей.
Системы, предназначенные для автоматической смывки красочных аппаратов, встречаются реже, т.к. этот процесс и в обычном режиме достаточно удобен. Обычно смывка происходит в специальный ящик с ракельный ножом. Она заключается в подстыковке этого ракеля к валикам и поливе сверху смывочного раствора из бутылки. Преимущества автоматической смывки начинают сказываться лишь на многосекционных большеформатных машинах.
Рис 6. Автоматическая смывка красочного аппарата
На рисунке изображено подобное устройство, установленное на машинах Komori Lithrone. Оно содержит систему трубопроводов для подвода смывки к валикам и пневматическую систему включения ракеля.
Отдельно хочу коснуться процесса смывки увлажняющих валиков. Наиболее неудобными в этом плане являются системы типа Molleton, которые содержат валики с тканым покрытием. Разумеется, речь об их смывки на машинах не идет, но можно автоматизировать процесс их промывки в автономных устройствах. Таких устройств выпускается большое множество, некоторые из них используют метод мытья погружением, другие задействуют специальные движущиеся щетки или моют валики струями воды, подающейся под большим давлением. Отжим обычно выполняется вращением валиков с большой скоростью, при этом удаляется не только лишняя влага, но и частицы ворса и твердых включений в чехлы. Скажем лишь, что весь процесс мытья одного комплекта валиков занимает 3-5 минут и результат получается лучше, чем при получасовом мытье их вручную.
Рис 7. Аппарат промывки чехлов увлажняющих валиков
Наиболее совершенные системы увлажняющих аппаратов: Alcolor от Heidelberg, Komorimatic, Rollandmatic, RyobiSuperdampener и Ryobimatic от одноименных производителей, не имеют в своем составе валиков с тканым покрытием и содержат специальный подвижный валик-мостик между увлажняющим и красочными аппаратами. За счет этого увлажняющие валики смываются совместно с красочными в автоматическом или полуавтоматическом режимах.
Системы для автоматической очистке печатных цилиндров встречаются еще реже, чем устройства смывки валиков. Наверное это неправильно, т.к. обычно подобный процесс, хоть и используется редко, но является очень трудоемким на машинах с посекционной схемой расположения цилиндров из-за сложного доступа к этим узлам. На машинах с планетарным расположением, печатные цилиндры более доступны и необходимость в подобных аппаратах не так актуальна. Но важным преимуществом автоматики остается ускорение работы и чистота производственных процессов.
Системы автоматической очистки печатных цилиндров по своему устройству схожи с аппаратами смывки офсетных полотен, поэтому ограничимся лишь констатацией факта их существования и рисунком, не будем рассматривать подробные схемы.
Системы проводки бумаги
Процессы загрузки бумаги, подготовки узлов проводки бумаги печатной машины под необходимый формат и толщину листов, а также выемки отпечатанной продукции занимают достаточно много времени, чтобы конструкторы задумались об их автоматизации. Сейчас мы рассмотрим несколько действующих систем, посвященных этой тематике.
Подача бумаги
Процесс подачи бумаги начинается с загрузки подающего стола. Сам процесс укладки бумаги в стопу не автоматизирован, но существуют специальные системы, позволяющие вставлять загруженную в стороне стопу в стапель машины. Они состоят из специальных транспортеров и подъемных устройств.
Широко распространены так называемые двух стапельные самонаклады, суть этих устройств заключается в следующем: во время печати тиража, когда бумага на самонакладе подходит к концу и подающий стапель поднят высоко вверх, под ним можно установить второй стапельный стол и начать укладку второй порции бумаги. Когда же бумага в первом стапеле закончиться и печатная машина остановиться, весь процесс смены будет заключаться лишь в удалении пустого стола и подъема стопы бумаги на несколько сантиметров вверх. Таким образом, вместо десятков минут, остановка продлиться не более одной минуты.
На этом автоматизация загрузки не заканчивается, сейчас существуют печатные машины с системами безостановочной подачей бумаги. Одна из таких, применяемых на машинах Komori, показана на рисунке.
Рис 8. Система безостановочной загрузки бумагой стола самонаклада печатнной машины
Принцип ее работы схож с двухкаскадными машинами, но здесь вторая стопа загружается в стороне от основного самонаклада, и по рольгангам подается под первую стопу. Затем под рабочую стопу автоматически вводиться специальный вилочный механизм удержания и из-под нее вынимается пустой стол. Далее, как обычно, поднимается второй стол с загруженной бумагой и убирается удерживающий механизм. Во время всего этого процесса машина не перестает печатать.
Все печатные машины имеют датчики контроля двойных листов, на современном оборудовании их несколько разного принципа действия. Если электромеханические датчики хорошо работают с бумагой средней и большой толщины, то электронные имеют приоритет при диагностике тонких листов, т.к. они работают на просвет бумаги ИК-лучами. Одним из плюсов машин с полистной подачей является наличие в них устройств автоматического отсева двойных или отличающихся по толщине листов бумаги. Многие машины кроме датчиков двойных листов имеют еще ряд контрольных механизмов на механизмах равнения, проверяются такие параметры как недовод, перекос бумаги на передних и боковых упорах. Эти устройства также повышают качество печатной продукции и ускоряют время приладки.
Итак, стопу мы загрузили, теперь займется подстройкой машины под необходимый формат и толщину бумаги. Опять же наибольшего развития эти системы получили у печатных машины Komori. На серии Lithrone, например, для этого достаточно ввести на пульте управления численные значения размеров листа. После этого все боковые направляющие на самонакладе и ПВУ, ролики и щетки на столе равнения, а также упоры бокового равнения автоматически установятся в необходимые положения. Под толщину бумаги автоматически отрегулируется зазор между печатными и офсетными цилиндрами. Подобные схемы есть и у других производителей.
Переворот бумаги в процессе печати
Очень распространеным атрибутом современных машин разных производителей (Komori, Heidelberg, Rolland, KBA, Dominant, Polly) является наличие устройств автоматического переворота листов. На некоторых машинах ставиться несколько устройств между секциями многокрасочной печатной машины. Применение данного механизма позволяет расширить степень гибкости машины без увеличения ее производственных площадей. Переворотный цилиндр может применяться вместо передаточного цилиндра как для односторонней печати, так и для печати с переворотом. В таком случае переключение режимов работы требует некоторого времени на подстройку. Печатные цилиндры, расположенные после устройства переворота имеют специально обработанную поверхность или покрытие, которое препятствует прилипанию на него свежеотпечатанного листа. Кроме этого, под цилиндром переворота и при последующих передачах лист поддерживается воздушной подушкой, которая эффективно защищает его поверхность от царапин. Недостатками подобных устройств является некоторое замедление работы печатной машины с включенным переворотом и более жесткое требование к точной подрезки бумаги.
Сам процесс переворота можно разделить на четыре этапа (рис 9).
Рис 9. Цикл переворота листа
Сначала система присосов переворачивающего барабана захватывает на ходу заднюю кромку листа (рис. А). Во время поворота системы присосов и клапанов (рис. Б) задняя кромка листа прочно удерживается присосами и далее передается на зажимы барабана (рис В). После этого лист идет как и при обычном процессе, удерживаясь в зажимах барабана, с той лишь разницей, что он идет задом наперед и печатной стороной внутри (рис. Г). Процесс заканчивается передачей бумаги в клапана следующего печатного цилиндра (рис. Д).
Приемно-выводные устройства
Теперь скажем несколько слов об автоматизации приемно-выводных устройств (ПВУ) печатных машин. На современных моделях, предназначенных для высококачественных работ, ПВУ представляют собой сложнейшие устройства, содержащие вакуумные системы бесперебойной проводки бумаги, с зонально регулируемым поддувом сверху, тормозными барабанами, устройствами против скручивания листов, порошковой, ИК и УФ сушки и т.п. Сейчас мы не будем касаться всего этого, как не относящегося напрямую к теме нашей публикации, рассмотрим лишь те механизмы, которые можно отнести к автоматизации рабочих операций.
О датчиках высоты стопы и механизме автоматического опускания приемного стола можно и не говорить, т.к. сейчас он применяется повсеместно. Системы безостановочной разгрузки приемного стапеля также находят применение у всех крупных производителей печатного оборудования. Поэтому не будем сейчас конкретно рассматривать какие-либо реализации, скажем лишь об общих принципах их действия. Главной частью этих механизмов являются вилочные поддерживающие устройства, которые вставляются вручную или автоматически сверху приемного стапеля. Затем нагруженный бумагой стол опускается, и отводиться в сторону, а пустой устанавливается на его место, все это время машина работает, выводя продукцию на удерживающие механизмы. Удерживающий механизм удаляется, и машина продолжает работать дальше.
Более совершенный механизм безостановочной разгрузки печатной продукции состоит их двух последовательно расположенных приемных стапельных столов, см. рисунок. В этом случае переключение на необходимый стапель осуществляется автоматически по достижению определенной высоты стопы либо по желанию печатника.
Рис 10. Механизм безостановочной разгрузки продукции
Хочется также упомянуть экзотическую приставку для вкладывания ленточек-закладок в приемную стопу.
Данное устройство необходимо, если часто печатаются тиражи, нуждающие в разделение на равные части. Закладки могут вставляться также автоматически, через заданное количество, либо при нажатии клавиши на корпусе устройства.
Рис 11. Устройство вставки в стопу ленточек закладок
В конце обзора систем, автоматизирующих вспомогательные и подготовительные операции, дадим диаграмму затрат времени на эти них при традиционном подходе и с использованием автоматики, составленную специалистами фирмы Komori.
Рис 12. Затраты времени на подготовительные операции
15 февраля 1998 г.
Измеряйте!
Часами измеряется время,
а временем жизнь человеческая;
но чем, скажи, измеришь ты
глубину Восточного океана?
К. Прутков,
Мысли и афоризмы
Можно долго спорить о том, как правильно печатать: "на глаз" или "по приборам".
Но если Вы никогда не видели погружного влагомера, денситометра или спектрофотометра, а словосочетание "аспирационный психрометр" вызывает ассоциации с Фрейдом, тогда эта статья для Вас
О несовершенстве человеческих органов чувств говорили много и не только медики. Тем не менее мы продолжим эту тему применительно к области полиграфии. Поговорим о том, что надо измерять сотрудникам типографий в повседневной работе, зачем это нужно, какими контрольно-измерительными приборами приходится (и какими необходимо) пользоваться; как происходит процесс измерений и какие значения должны получаться. При этом постараемся удержаться от азбучных истин и излишней дотошности. Ясно, что пользоваться штангенциркулем в нашей "самой образованной" стране сможет практически любой (включая и тех, кто пока не знает, что это такое).
О том, что рассматривать эту тему не бесполезно, можно судить по тому факту, что половина печатников, с которыми автору приходилось сталкиваться, никогда не держали в руке обычного денситометра, не говоря уже о более экзотическом измерителе электропроводности увлажняющего раствора или твердомере резины. Причем не всегда это объясняется нехваткой средств. Есть случаи, когда имеющиеся в типографии дорогостоящие приборы не использовались из-за незнания, неумения или сложившихся традиций.
Конечно, мы понимаем, что сами по себе контрольно-измерительные инструменты еще ничего не значат. Используемый в качестве груза или прижима денситометр уступает в эффективности обычному куску металла. Важно, чтобы были соблюдены все требования: инструменты должны быть на своих местах, ими должны уметь пользоваться операторы и при этом правильно анализировать результаты измерений, чтобы делать правильные корректировки и так далее. Одним словом, все это можно назвать — отлаженная технология. Надо сказать, что при работе по современным технологиям измерительные приборы являются лишь вспомогательным средством, хотя и немаловажным. Практически, их главная задача — информировать человека о сути происходящих явлений, отслеживать и предупреждать появление брака или повреждение оборудования.
Однако несмотря на самые сложные инструменты и повальную автоматизацию процессов, главным творцом печатной продукции все же остается человек. Именно он выбирает методы решения тех или иных задач, способы работы и соответственно — электронных и механических помощников, которые будут ему нужны. Если печатник привык работать, полагаясь лишь на свои руки и зрение, то пользы от дополнительного инструмента ему не будет никакой. С другой стороны, человек тем и отличается от представителей животного мира, что способен обучаться. Поэтому автор надеется, что представленная здесь информация может оказаться полезной для читателей.
Прежде чем рассматривать контрольно-измерительные приборы и инструменты, мы условно разобьем их по областям применения. Отдельно выделим инструменты, предназначенные для контроля микроклимата в помещении типографии, проверки качества полуфабрикатов (печатных форм, бумаги, краски, увлажняющего раствора и т. п.), тестирования состояния печатной машины и проверки качества получаемой продукции.
Микроклимат в помещении типографии
Комбинированный измеритель температуры и влажности
Хотя понятие "микроклимат" включает десятки различных параметров, для печатного процесса достаточно знать и контролировать лишь влажность и температуру внутри и снаружи помещения. Очень удобным для этой цели может оказаться комбинированный электронный прибор, включающий в себя измеритель влажности и два термометра, один из которых снимает данные с внутреннего, а другой с вынесенного наружу (посредством электропровода) датчика.
Если такого интегрированного прибора нет, его могут заменить обычные спиртовые термометры и погружной влагомер. Для калибровки этих измерителей влажности раз в месяц желательно еще иметь и аспирационный психрометр.
Прибор для поддержания уровня влажности в помещении типографии
Наиболее благоприятная для печати температура — 18–22 °С, относительная влажность — 40–60 %. Причем зачастую главную роль играет не сама величина этих параметров, а их стабильность. Так, если летом в жару печать началась при температуре 19 °С, а затем была открыта форточка и воздух прогрелся до 22 °С, то это принесет существенно больший вред, нежели постоянная работа при 25 °С жаре. Изменится вязкость краски (а значит и характеристики ее растекания на бумаге и, как следстви,е показатели растискивания); изменятся размеры бумаги (и если печать велась на одно-двухкрасочных машинах, то осуществить приводку при последующих прогонах будет сложно), изменятся характеристики увлажняющего раствора (испарится спирт и изменятся параметры водно-красочного баланса) и т. д.
С этой точки зрения рекомендуется герметизировать производственный цех от улицы (говоря по-простому, заделать щели в окнах и дверях) и оборудовать его системами кондиционирования воздуха. Причем затраты даже на дорогостоящие импортные сплит-системы окупятся одним-двумя спасенными заказами. За границей, в южных странах, для поддержания постоянной влажности в помещениях типографии часто используют специальные промышленные увлажнители, которые постоянно испаряют большое количество влаги. У нас таких аппаратов в продаже нет, но при необходимости их можно заменить обычными чайниками. Не забывайте только контролировать получаемые показатели, иначе можно вместо желаемой стабилизации получить обратный эффект
Для того, чтобы исключить влияние перепада температур между улицей и помещением необходимо, чтобы закупленная бумага и химикаты проходили акклиматизацию в том помещении, где будет производится печать. В авторской справке приведена таблица времени акклиматизации бумаги, в которой указан рекомендуемый интервал времени, в течение которого бумага должна отлежаться, чтобы в процессе печати не происходила ее сильная усадка.
Авторская справка
Время акклиматизации бумаги
Для того, чтобы в процессе печати не возникали проблемы с изменениями размеров бумаги вследствие усадки из-за разницы температур при перевозке и в помещении, ее необходимо выдерживать в помещении с такими же климатическими условиями, как и в печатном цехе (или прямо в нем) Особенно это важно зимой. В таблице приведено необходимое время акклиматизации бумаги в зависимости от объема упаковки. Соответственно, следующий прибор для контроля микроклимата — часы. Шутка.
объем упаковки бумаги,
м3
разница t°
5
7,5
10
15
20
25
30
35
0,2
4 ч
7 ч
9 ч
15 ч
21 ч
28 ч
41 ч
62 ч
0,4
7 ч
12 ч
17 ч
26 ч
36 ч
41 ч
64 ч
92 ч
0,6
9 ч
15 ч
20 ч
31 ч
42 ч
55 ч
76 ч
106 ч
1
12 ч
18 ч
23 ч
33 ч
46 ч
63 ч
84 ч
115 ч
2
13 ч
19 ч
24 ч
35 ч
49 ч
66 ч
90 ч
123 ч
Шарифуллин Марсель,
октябрь 2000 г.
15 мая 2000 г.
Вводное обучение персонала при запусках печатного оборудования
Введение
В типовом контракте на поставку Полиграфического комплекса последним пунктом, после гарантийной поддержки и пусконаладки, идет скромная строчка "обучение персонала" (правда, нередко обозначенная в колонке "стоимость" отнюдь не скромной цифрой). Каждая из сторон вкладывает в нее свой смысл. Для продавца, конечно, первичный смысл заключен именно в колонке "стоимость". Кроме того, здесь и выполнение "обязательной программы" - без обучения теперь машину не продашь, и элемент успокоения клиента ("не забивайте себе голову деталями, вам все объяснят на месте, а сейчас поскорее платите"). При этом подразумевается, что наладчик покажет, куда класть бумагу, а куда - краску. Покупатель же, в свою очередь, надеется, что инструктор будет возиться с его хлопцами до тех пор, пока они не освоят в полном объеме программу полиграфической академии. При той простоте нравов, которая до сих пор существует в отечественном полиграфическом бизнесе, столь трагическая разница во взглядах на жизнь часто обнаруживается только на месте, когда дело доходит до подписания отчетных документов по контракту.
Можно посмотреть на эту проблему и по-другому. Хотя это и неочевидно на первый взгляд, но некачественное обучение невыгодно и продавцу. Полиграфический мир достаточно тесен, и слух о плохо работающей машине Х, проданной компанией У, быстро распространится по всей России. При этом никто не будет разбираться, в чем причина - плоха ли сама машина, или не было нормального обучения, или печатник - разгильдяй, но репутация оборудования и его продавца будет изрядно подмочена. Как минимум, типография не войдет в открытый список установленного компанией оборудования. Кстати, предоставление информации об ранее установленных машинах может служить некоторым индикатором профессионализма фирмы. Хорошему продавцу незачем скрывать своих клиентов.
С другой стороны, нередко сам покупатель отказывается от полноценного качественного обучения. Одна из причин - у него нет достаточного времени: как водится, оборудование еще не пришло, а заказов уже набрали на месяц вперед. Другая причина - жалко денег: хорошее обучение стоит дорого, да еще надо потратиться на бумагу, краску, расходники, которые будут угроблены во время обучения.
Работая несколько последних лет наладчиками полиграфического оборудования, мы успели установить больше сотни печатных машин и комплексов на их основе, приобщить человек двести к профессии печатника и попутно много раз наступить некоторые грабли. Этой статьей мы призываем и продавцов, и покупателей оборудования отнестись к проблемам вводного обучения максимально ответственно, и постараемся обозначить коварные моменты этого процесса.
Историческое отступление
Вводное обучение на современном оборудовании - дело достаточно новое; богатые методические разработки прошлых лет здесь подходят плохо, потому что они делались для традиционных технологий и машин большого формата. Курс подготовки печатника в техническом училище был рассчитан на 2-3 года. Во многих статьях мы уже проводили мысль, что с внедрением новых технологий полиграфия утрачивает черты клановости и превращается в ремесло, доступное каждому. Во всем мире этот процесс шел плавно в течение нескольких десятилетий, а у нас он приобрел черты революционного скачка. Может быть, кто-то из читателей этой статьи увлекался фотографией в доперестроечное время и помнит, какой эпопеей была самостоятельная обработка цветной пленки и печать. А теперь цветная фотография доступна любой домохозяйке. Нечто аналогичное происходит и в полиграфии. Современные печатные машины и материалы имеют большие технологические запасы, поэтому не требуется отточенного десятилетиями мастерства, что бы получать приемлемое качество. (СНОСКА. Об этом подробнее авторы уже писали в своей прошлой статье "Оперативная полиграфия" в журнале "Publish" #2 за 1999 г, www.publish.ru).
Как показывает наш опыт, при правильной постановке дела обучить ремеслу печатника можно любого смышленого человека практически с нуля за 2-3 дня. С другой стороны, печатная машина, конечно, не ксерокс и в работе печатника всегда присутствует элемент искусства (тем больший, чем менее данная машина приспособлена для данного вида печати).
Как не надо делать
Опора на собственные силы
Наш особый российский менталитет частенько толкает нас к проблемам на ровном месте. С детства мы знаем, что у нас самое лучшее в мире образование, и что никакие буржуи нам не указ. Зачем сдавать импортный телевизор в ремонт, если мы заканчивали технический вуз (например, по ракетостроению), и у нас дома есть паяльник? То же самое отношение наблюдается и у некоторых полиграфистов. Наладчику, несколько десятков лет обслуживавшему Ромайоры и Доминанты, трудно внушить, что эксплуатация современных машин требует иного подхода. Что, например, красочные валики современной машины могут выйти из строя лишь оттого, что их пару раз забудут смыть на ночь. Печатник, годами выполняющий эту процедуру раз в неделю, и то с большой неохотой (после нее только руки надо полчаса отмывать от краски), не сразу привыкнет к тому, чтобы выполнять ее ежедневно, по несколько раз за смену. Даже наглядная демонстрация того, что на новом оборудовании это совсем не требует залезания руками в краску, и выполняется в полуавтоматическом режиме за 2-3 минуты, действует только до отъезда инструктора.
Поэтому, на наш взгляд, даже многолетний стаж печатников не может заменить вводного обучения. Более того, часто обучить молодого новичка "с нуля" легче, чем седовласого мастера. Ну привык он тушить окурки в корыте увлажнения во время работы, и ничего с этим не поделаешь. При обучении печатников со стажем нередко приходится не только объяснять отличия современной машины от Ромайора, но и отучать их от приобретенного годами специфического отношения к работе и к технике.
Вводное обучение в подарок
Некоторые фирмы, в том числе очень крупные и известные, иногда вставляют в договора пункт о том, что вводное обучение персонала проводится бесплатно. Это, конечно, прекрасно, но это может считаться заботой о клиенте только в том случае, если речь идет о достаточно простой технике, которую он в противном случае способен освоить самостоятельно. Если же рассматривать такой подарок в отношении печатной машины или фотонаборного аппарата, это не только не достоинство сделки, а, напротив, ее минус. Как известно, в зубы дареному коню не смотрят, поэтому непонятно, как заказчик сможет требовать выполнения этого пункта договора.
Отсюда рекомендация покупателям - не поддавайтесь на эти уловки. Если Вам предлагают такой подарок, требуйте, чтобы в контракте была заложена позиция с явно указанной стоимостью вводного обучения, а в следующей строке - скидка на эту же сумму, но уже без конкретной привязки к обучению. Далее нужно оформить приложение, в котором будет раскрыто содержание этого пункта - объем и подробная программа обучения. Это позволит в дальнейшем потребовать от продавца полноценного и добросовестного выполнения всех пунктов контракта.
В погоне за сиюминутной выгодой
Часто мы сталкиваемся с давлением руководства типографии, когда нас просят совместить процесс обучения с производством тиражной продукции. Действительно, казалось бы, что же тут плохого? Эффективное использование материалов, экономия времени. Более ответственный подход к делу - печатаем не на макулатурной, а на дорогостоящей бумаге, не в мусорную корзину, а для заказчика. Это должно заставлять печатника серьезнее следить за своими действиями. Казалось бы одни преимущества для покупателя. Но на самом деле извлечь выгоду из этой ситуации скорее сможет продавец. Как всегда при погоне за двумя зайцами, приходится делать выбор между своевременной сдачей данного тиража и качеством обучения. И, естественно, выбор обычно бывает в пользу печати тиража. Инструктор со словами "смотри и запоминай" отодвигает печатника от машины, быстренько сам прогоняет тираж, показывает его руководству как результат обучения - и все, его обязательства выполнены. Ведь фактически уже началась коммерческая эксплуатация машины.
Как известно, в каждом тираже найдется своя "закавыка" - или плашка во весь лист, или выворотки по четырем цветам шестым кеглем, или пленки кривоватые, или бумага попадется капризная. Если на учебном тираже можно временно закрыть глаза на отдельные проблемы, чтобы не нарушать методичности обучения, то на коммерческом заказе эту проблему придется решать, хоть кровь из носу. В результате лимит времени, отведенный под обучение, может быть потрачен на борьбу с конкретным тиражом, а не на разбор всего перечня операций, которыми должен владеть печатник. Очень важные моменты могут быть объяснены мимолетом и не подтверждены практической работой обучаемого (некогда, идет тираж), поэтому они не зафиксируются в его памяти. К тому же на обычном тиражном оттиске (который может быть произвольным по сложности) иногда бывает трудно контролировать навыки и способности печатника. Например, если он хорошо напечатает самостоятельно простую двухцветную работу, это еще вовсе не означает, что в дальнейшем он также успешно справится с более сложной цветной печатью или сплошными плашками.
Правда, иногда покупатель оборудования решает проблему срочной печати заказов очень просто. Достоверно известен случай, когда наших коллег насильственно удерживали в течение трех месяцев, пока они не отпечатали большой заказ, под который и было, собственно, куплено оборудование. Дело было в одной из бывших братских республик, находившейся в состоянии войны с другой бывшей братской республикой. После того, как заказ был выполнен, нужда в типографии отпала, поэтому покупателю не требовалось обучать своих печатников и ставить технику на обслуживание.
Хотя это и крайний случай, но в принципе у покупателя всегда есть очень большой соблазн вместо обучения своих кадров просто использовать инструктора в качестве печатника. Об этой опасности необходимо постоянно помнить продавцу. Полбеды, если его сотрудник просто перейдет в типографию; хуже, если он будет втихую подхалтуривать там по ночам. Отстаивая свои личные интересы, он будет сваливать вину за брак на некачественное оборудование, и рано или поздно спровоцирует конфликт между продавцом и покупателем.
Предварительное обучение
Очень часто заказчик не имеет возможности уделить много времени на обучение своих сотрудников. Бывает, что пришедшая машина должна сразу впрягаться в рабочий процесс, и график ее работы расписан на ближайшее время почти по минутам. Конечно, неплохо бы покупателям нового оборудования перед составлением бизнес-плана почитать настольную книгу всех советских полиграфистов "Положение о техническом обслуживании и ремонте оборудования полиграфических предприятий" (Москва, Книжная палата, 1990), где приведены нормативы на пусконаладку и обучение. Например, монтаж и наладка однокрасочной листовой офсетной машины - 21 день, освоение машины печатником - 15 смен, а если печатник до этого не имел опыта на листовом офсете, эту цифру рекомендовано умножить на 3: Это, конечно, относится в первую очередь к большим машинам, но все равно ясно, что обучение требует немалого времени.
Напрашивающееся решение - провести обучение печатников заранее, чтобы они с первого дня после монтажа смогли начать работать.
Обучение может производиться либо на собственной базе поставщика (в том числе и с выездом за границу), либо в одной из ранее установленных типографий. И тот, и другой подходы имеют свои плюсы. Если обучение проводится "на базе", его можно четко организовать и провести строго по программе. А стажировка в действующей типографии позволяет печатникам увидеть весь процесс выпуска реальных тиражей целиком и позаимствовать всякие маленькие хитрости и приемы работы.
Если у покупателя есть возможность отправить своих печатников на стажировку заранее, это стоит сделать. Надо только спланировать ее срок так, чтобы печатники не растеряли эти знания до прихода оборудования, то есть чтобы перерыв между обучением и началом работы был не более одной-двух недель.
И все-таки мы считаем, что обойтись совсем без обучения на месте невозможно. Наверняка на месте будут другими состав оборудования, технологические цепочки, виды продукции, материалы. Поэтому наиболее рационально совместить обучение с пусконаладочными работами и проводить его на новом оборудовании, купленном вместе с комплектом расходных материалов. Это решает многие проблемы (например, привязку к местному климату, качеству воды, бумаги и т.п.), но только при условии, что комплекс составлен грамотно, расходные материалы подобраны грамотно, программа обучения продумана, а инструктор хорошо знает технологию и не растеряется в нештатной ситуации
Рис 3. Счастливый финал
Несколько слов об обучении за границей. Мы сами проходили обучение в США и Германии, и считаем, что оно целесообразно и эффективно лишь для сервисных инженеров, причем тех, которые уже накопили некоторый опыт и у которых накопились вопросы. Возможность задать их в непосредственном общении мастерам фирмы-производителя, имеющим 20-30-летний опыт работы с данными машинами, позволяет за одну-две недели сделать качественный скачок в квалификации. А вот вводное обучение печатника легче и эффективнее проводить в России. В первую очередь это связано с языковым барьером: обычно печатник может общаться за границей только через переводчика, а если переводчик сам не является хорошим специалистом в полиграфии, общение с инструктором вынужденно переходит на язык жестов. По нашему мнению, поездки печатников и технологов за рубеж стоит рассматривать в основном как рекламно-поощрительный момент сделки и не возлагать на них особых надежд в плане обучения. Хотя, конечно, наличие красивых сертификатов, полученных из рук ведущих специалистов производителя, может значительно поднять имидж фирмы в глазах заказчиков.
Как надо делать
Условия проведения обучения
Прежде, чем говорить о содержании и программе обучения, остановимся на подготовке этого процесса. Ниже мы просто дадим небольшую выдержку из положения о пусконаладке, которым мы руководствуемся в своей работе. Может быть, на первый взгляд это покажется маниакальным педантизмом, но, как каждая строчка армейского устава написана кровью, так и за каждым пунктом этого положения стоят реальные проблемы при обучении. Например, нам особо ярко запомнился один запуск в Сибири, который руководители типографии превратили в помпезное событие, с приглашением первых лиц республики. И в то же время на всю пусконаладку трехтонной офсетной печатной машины и десятидневное обучение было закуплено две пачки ксероксной бумаги.
Итак, к началу вводного обучения должны быть выполнены следующие условия:
в помещении должны быть закончены ремонтные и отделочные работы;
в помещении не должны проводиться никакие другие работы и не должны присутствовать лица, не участвующие в обучении;
температура в помещении должна быть в пределах +17...+25 ОС;
относительная влажность в пределах 40...80 %;
в помещении должно быть хорошее общее освещение (мощность верхних светильников дневного света не менее 15 Вт на 1 кв. м площади помещения);
машина должна быть полностью отрегулирована и проверена инструктором посредством печати такого же тиража, как и учебный;
претенденты на должность печатника должны быть полностью освобождены от других работ;
размер учебного тиража должен быть не менее 1000 листов.
В достаточном количестве должны быть заготовлены все необходимые расходные материалы и бумага требуемых сортов;
виды и количество расходных материалов и бумаги должны быть согласованы и одобрены инструктором.
Кто будет учить
На больших машинах практикуется выезд на ПНР наладчика-механика, электронщика и инструктора. Стоимость ПНР пропорциональна стоимости машины, и продавцы больших машин могут себе это позволить. Малые комплексы предполагают и малые средства на ПНР, поэтому идеальный для заказчика вариант, если наладчик выступает сразу в трех ипостасях. Но это, конечно, требует от него большого опыта и квалификации.
Недостаточно просто доверять заявлениям фирмы продавца (пусть даже очень крупной и известной), что она имеет профессиональных специалистов. Необходимо лично убедиться в наличии профессиональной технической службы, которая отвечает за обучение персонала и может грамотно выполнять гарантийное и сервисное обслуживание оборудования. Мы рекомендуем покупателю пообщаться непосредственно с теми инженерами, которые будут устанавливать оборудование и обучать печатников.
Для пущей достоверности свяжитесь с теми, кто уже прошел по этой дороге до вас и купил оборудование у вашего поставщика раньше. Получите отзывы о технической службе продавца. Не лишним будет узнать фамилии инженеров, чья работа понравилась покупателям. В последнее время по известным причинам во многих фирмах произошли большие кадровые изменения, и может оказаться, что эти специалисты уже давно работают в других местах.
Рис 4. Наладчик в роли лектора
Регламент обучения и контроль результата
Первый вопрос, на который должен ответить для себя покупатель - это за что он платит: за процесс или за результат?
На самом деле вводное обучение как процесс, когда оплачивается определенное количество рабочих часов инструктора, вполне имеет право на существование. У такого подхода очевидные преимущества: легко контролируется факт выполнения работы, легко обосновать стоимость. Инструктор, не связанный жесткой программой, может построить обучение, исходя из имеющейся квалификации обучаемого, и не рассказывать, например, опытному печатнику азы настройки самонаклада, а уделить больше времени особенностям машины. Но такой вариант возможен только при условии, что продавец и покупатель хорошо знают друг друга и полностью доверяют, что встречается крайне редко. Такой подход может привести к конфликтам, причем иногда самым неожиданным образом. Например, один из наших клиентов несколько лет назад приобрел цветоделитель-цветокорректор Crossfield и для подстраховки заложил в контракте 30 дней обучения. Приехавший из-за рубежа инструктор основательно взялся за дело, но уже через несколько дней перешел к методу "повторение - мать учения", причем объяснял в основном теорию цветовосприятия, потому что на практику было жалко пленки. Только тут в типографии поняли, в какую ловушку себя загнали. Закрывать контракт инструктор категорически отказывался, ему за пребывание в России шли командировочные с бешеными коэффициентами, а покупатель не мог начать эксплуатацию до окончания обучения, потому что он при этом лишался гарантии.
Другой подход состоит в том, что покупатель платит за результат, то есть за умение печатника работать самостоятельно. Здесь встает вопрос контроля обучения. По сути, обучение работе на печатной машине имеет много общего с обучением вождению автомобиля. В случае с вождением в качественном результате заинтересованы другие участники движения, а проверку от их имени выполняет автоинспекция. В типографии в результате обучения заинтересованы ее руководители, и лучшим вариантом будет, если при обучении или хотя бы при печати учебного тиража будет лично присутствовать кто-либо из технического руководства. Однако нередко нам приходилось сталкиваться с таким мнением руководителей, что обучающий инструктор должен сам в конце устроить нечто вроде экзамена для печатников. Очевидно, что инструктор не сможет объективно оценить результаты своего собственного труда и получает широкие возможности для халтуры. С другой стороны, такой подход чреват неприятностями и для продавца. Покупатель вполне может заявить: "Вы продали нам машину, обучили наш персонал и сами подтвердили, что он все усвоил; поэтому весь наш брак не оттого, что мы не умеем работать, а оттого, что вы нас не научили. Так что, будьте добры, приезжайте и все за нас перепечатывайте".
По нашему мнению, на этапе согласования контракта должны быть строго сформулированы все моменты, связанные с обучением: что считать результатом, в каком объеме проводится обучение и как принимается работа.
Обучение идеальное
Сначала абстрагируемся от действительности и попробуем нарисовать картину идеального обучения. Для покупателя идеальным будет такое обучение, после которого его персонал может обеспечить максимальное качество печати на всех видах продукции, для которых предназначена данная машина.
Даже сама постановка задачи уже представляет некоторую трудность. Во-первых, должно быть известно, какое максимальное качество может обеспечивать эта машина, причем это должно быть выражено в количественных критериях, поддающихся объективному контролю. Во-вторых, требует точного определения выражение "все виды продукции".
Продолжаем абстрагироваться и предполагаем, что эти проблемы так или иначе решены. Следующие трудности будут связаны с описанием критериев результата. Они также должны быть объективными и количественными. Нам представляется, что оценка результата обучения должна базироваться на печати учебного тиража. С точки зрения покупателя идеальными критериями приобретенного печатником мастерства могут служить следующие параметры:
время подготовки машины к печати из положения ночного простоя;
время закладки бумаги и настройки на формат;
время установки форм и приводки;
количество листов, использованных на приводку;
достигнутая точность приводки по полю листа;
время настройки насыщенности краски и количество использованных листов;
максимальное отклонение насыщенности краски по ширине листа после приладки;
максимальное отклонение насыщенности краски в пределах тиража;
количество остановок печати во время тиража;
время смены краски и подготовки второго прогона;
достигнутая точность приводки при двух прогонах;
относительная доля листов с несовмещением на двух прогонах, превышающим допустимое;
относительная доля забракованных листов после двух прогонов (слипшиеся, с отмарыванием, с замятиями, с марашками и т.п.).
Предположим, что продавец и покупатель нашли общий язык, договорились о критериях обучения и конкретных цифрах и записали их в договоре. Однако, как известно, бумага все терпит, а надо еще все это реализовать на практике. Здесь основные сложности состоят в том, что перечисленные выше параметры зависят не только от мастерства, старания и доброй воли всех участников.
Во-первых, они могут оказаться недостижимы потому, что машина находится не в лучшем состоянии (не отрегулирована должным образом, или, например, пришли в негодность валики или офсетное полотно).
Во-вторых, хотя и говорится, что битьем можно и зайца научить на гармошке играть, с печатниками дело обстоит гораздо хуже - многим людям просто не дано печатать цвет, и тут уж ничего не поделаешь.
Заранее избежать этих ситуаций, к сожалению, нельзя. Но, по крайней мере, есть простой способ показать, что с машиной все в порядке, а дело только в печатнике: прежде, чем начинать обучение, инструктор должен сам отпечатать такой же тираж, выдержав все критерии качества. (Считаем само собой разумеющимся, что инструктор - ас печати).
А что делать, если даже ас-инструктор на идеально отрегулированной новой машине не может достичь заданных параметров? Не исключено, что они были неправильно заданы и заведомо превышают возможности данной машины. А возможно, что причина в некачественной бумаге, плохой краске, плохих формах, резком изменении климата или еще в чем-то постороннем. Поэтому крайне желательно, чтобы процесс обучения контролировала третья сторона в роли независимого арбитра. Ее мнение будет решающим в спорных ситуациях. Естественно, в качестве такого арбитра может выступать только фирма или лицо, чьи компетентность и авторитет признаны и продавцом, и покупателем.
Итак, организовать идеальное обучение в принципе возможно. Для этого необходимы следующие условия:
продуманная программа обучения и система оценки результатов,
достаточно высокая квалификация инструктора,
готовность покупателя затратить достаточное количество времени и материалов,
наличие компетентного наблюдателя-арбитра.
Обучение реальное (наш подход)
Есть много причин, по которым обучение редко строится по такой идеальной схеме. Чаще всего продавец не готов взять на себя ответственность за результат печати, тем более, когда печать будет выполняться чужими руками, а покупатель не готов заплатить за достаточно продолжительное обучение и еще за бумагу, краску, формы, за услуги фирмы-консультанта. Поэтому на практике обучение проходит по упрощенной схеме, а конечная цель формулируется несколько иначе: печатник должен освоить органы управления машины, порядок ее эксплуатации и обслуживания. Подразумевается, что качественно и быстро печатать он научится сам по мере накопления практического опыта. Тем не менее и такое обучение надо стремиться приблизить к идеальной схеме.
В большинстве случаев в своей работе мы используем следующий подход. Программа обучения строится на руководстве оператора, которым в обязательном порядке снабжена любая печатная машина, то есть в том объеме, который сам производитель считает достаточным для работы на ней. В ходе обучения инструктор руководствуется так называемым "контрольным листом" - подробным перечнем вопросов, которые он обязан объяснить печатнику и разобрать на практике. Вопросы достаточно детализированы, например, отдельным пунктом может присутствовать "переключение автомата бокового равнения на другую сторону при работе с оборотом". Каждый отдельный пункт инструктор разбирает с печатником столько времени, сколько тому требуется для полного уяснения. Но, когда у печатника иссякли вопросы по данному пункту, он должен в соседней графе поставить свою подпись, означающую, что о н все понял. И так по всей программе обучения. Кроме того, этот контрольный лист подписывает начальник производства или мастер, подтверждая тем самым, что теперь он знает, чего можно требовать от печатника. Разумеется, для этого он должен быть свидетелем процесса обучения и лично видеть его результаты. Таким образом, результатом такого обучения становится понимание печатником способов и приемов управления данной конкретной машиной. Что немаловажно, этот результат документально зафиксирован в контрольном листе.
Рис 5. Разбор причины дефекта
Кроме ознакомления с устройством машины и органами управления печатник в очень сжатые сроки должен получить конкретные практические навыки, которые потом позволят ему самостоятельно решать новые проблемы, которые будут на других тиражах.
Программа должна включать:
Практикум по всем настройкам машины, как они описаны в руководстве.
Практикум печати на специально подготовленных формах, позволяющих отдельно потренироваться в совмещении, регулировке баланса, регулировке цвета, многократных прогонах и т.п. Для этого не годятся фотоформы реальных тиражей заказчика, потому что на них могут встретиться сразу все проблемы, или, наоборот, одна побочная, но которая оттянет на себя все время и внимание.
Разбор сложных ситуаций, которые могут возникнуть в процессе работы (броски бумаги, эмульгирование краски, тенение, марашки и т.п.) и рекомендации по их преодолению.
Для этих целей должно быть подготовлено достаточное количество бумаги и расходных материалов. Идеальный случай, когда на растущую гору макулатуры просто не обращают внимания. Это помогает раскрепостить печатника и выработать уверенность в своих действиях. В противном случае, если все вокруг будут трястись над каждым испорченным листом при печати пробных тиражей, печатник не сможет сосредоточиться на процессе печатания. Для экономии можно один и тот же лист гонять по несколько раз, по разному его ориентируя. И лишь в конце обучения можно отпечатать показательный тираж, который покажет способности печатника. Об этом поподробнее.
Печать учебного тиража
Очень важный этап, без которого нельзя обойтись. Но необходимо заранее договориться, для чего мы это делаем. Можно, конечно, рассматривать учебный тираж как генеральную проверку знаний и умений печатника, а его качество - как результат обучения. Но для этого, как мы писали выше, необходимо сначала разработать систему объективных критериев, по которым будет оцениваться качество печати и качество работы, а здесь одни сплошные подводные камни. Например, мы закладываем требование: "совмещение 0,1 мм по всему полю должно быть достигнуто печатником не более чем через 100 приладочных листов". Вроде бы ничего особенного, но ведь совмещение зависит не только от искусства печатника, но и от свойств бумаги. Значит, придется заодно оговаривать еще сорт и плотность бумаги, на которой будем печатать. А где и, главное, на что купить импортную меловку заданного сорта, например, в Якутске?
Итак, рассматривать учебный тираж как критерий достижения результата обучения можно, но осторожно: выполнение всех условий, которыми будет обставлен такой договор, может оказаться невозможным для обеих сторон, причем не из-за недостатка квалификации, а просто организационно. Делать это следует только в особо ответственных и сложных случаях, например, когда комплекс поставляется несколькими фирмами и трудно найти крайнего, виноватого в плохом качестве.
Обычно же учебный тираж печатается с двумя простыми целями: во-первых, дать возможность печатнику самому выполнить работу от начала до конца в присутствии инструктора и, во-вторых, зафиксировать факт, что после вводного обучения данный печатник на данной машине может самостоятельно печатать вот с таким качеством.
Что печатать
К подбору картинки для печати нужно подходить максимально чутко и в первую очередь с психологических позиций. Как правило, персонал типографии связывает с первым самостоятельным тиражом большие личные надежды - и имеет на это полное право: ведь они заплатили за все это большие деньги! Директор типографии спит и видит, как он со свежими оттисками полетит по городу утирать носы конкурентам, новоиспеченные печатники мечтают показать свое творение домашним, остальные сотрудники тоже щедро одарят всех знакомых и незнакомых, и в результате через день эти листки будут встречаться в городе на каждом углу. Но это будет всего лишь первый, учебный тираж, который наверняка будет далек от совершенства и по стабильности краски, и по приводкам. Поэтому, во-первых, надо выбрать такую картинку, которая не "упадет" из-за небольшого нарушения приладки или неравномерности краски. И, во-вторых, она должна органично смотреться везде - и в пафосно оформленном кабинете мэра, и на окошке кассы в магазине, и дома на стене сортира. Это очень непростая задача, из чего следует, что пленки для учебной печати инструктор должен возить с собой, а готовить их должны высококвалифицированные дизайнеры.
Не менее важны вопросы, чем печатать и на чем печатать. Какой бы хорошей ни была машина, и как бы ни старался печатник, красиво напечатать полноцветную картинку на бумаге "офсет #1" невозможно. И пусть даже с технической точки зрения все отпечатано идеально, общее впечатление от оттиска будет настолько тоскливым, что вместо радости от покупки новой современной техники у всех будет глубокое разочарование. А несколько листов обязательно попадут в конкурирующие типографии и станут в их руках грозным антирекламным оружием. Но руководство типографии, как правило, морально не готово перевести несколько тысяч листов хорошей импортной мелованной бумаги в заведомую макулатуру. Поэтому еще на этапе согласования условий обучения нужно записать, что покупатель обязуется предоставить 2000-3000 листов бумаги такого-то сорта, такой-то плотности, а также формы, краски, реактивы строго оговоренного типа для целей пусконаладки и печати учебного тиража.
Кстати, по нашему опыту, очень неплохой компромисс между качеством печати и затратами на бумагу достигается при использовании этикеточной бумаги плотностью 65-75 г/кв.м. Конечно, она несколько капризнее в печати, чем Galerie Art gloss 150 г/кв.м, но, с другой стороны, учиться надо в первую очередь на ней, потому что в нынешние времена именно этикетка и станет для типографии, вероятнее всего, основным хлебом.
Рис 6. Первый тираж глазами министра
Однако красивые оттиски - только побочная цель учебной печати. Главное - дать возможность печатнику приноровиться к машине и попрактиковаться в основных элементах процесса печати: настройка на формат, приладка, регулировка краски, поддержание баланса, печать в несколько прогонов, печать с оборотом. И лучше, если он сразу будет учиться делать это грамотно, по-современному, с использованием и визуальных, и аппаратных средств контроля. Поэтому кроме красивой картинки учебные формы обязательно должны содержать достаточное количество приводочных меток и полный набор технологических полей: для замера плотностей красок денситометром, для контроля растискивания, баланса серого, индикаторы двоения и скольжения, поля контроля формного процесса: Очень важно, чтобы инструктор на практике показал и объяснил, для чего служит каждое поле, как оно работает и как пользоваться шкалами. Практика показывает, что печатники очень консервативны, и, если при вводном обучении им показали, что контролировать плотность краски можно по смазыванию ее пальцем, они так и будут годами ее смазывать, несмотря на то, что у технолога в столе ржавеет денситометр.
Обучение сервисному обслуживанию машины
Этому следует обучать, не скрывая технической информации. Опасность не заработать в будущем на сервисных услугах - мнимая. Хорошая сервисная служба должна зарабатывать не на элементарных рутинных операциях, которые запрещается делать заказчику под страхом снятия с гарантии, а на решении нестандартных проблем. Если сервисная служба умеет делать это, она без работы не останется, потому что полиграфия изобилует такими проблемами на каждом шагу.
Как правило, хорошая печатная машина сопровождается и хорошим руководством, в котором описаны все регламентные и регулировочные операции, которые должен делать персонал типографии. Руководство по сервису может быть как отдельной книгой, так и разделом общего руководства по эксплуатации.
Рис 7. Даже работа масленкой требует знаний
Знание внутреннего устройства машины и умение самостоятельно ее регулировать особенно важно в типографиях, удаленных от сервисных центров. В нашей стране есть города, до которых из Москвы порой нельзя добраться быстрее, чем за 3-4 дня, а решать проблемы обычно необходимо сразу, не останавливая производство. Поэтому во время обучения нужно обязательно отвести по крайней мере один-два дня на ознакомление с узлами машины, их устройством, приемами разборки, проверки и регулировки. Не обязательно этот мини-курс по обслуживанию должен проходить печатник. Лучше, если это будет механик. Однако в маленьких типографиях зачастую весь штат состоит из печатника да директора. Если директор - технически подкованный человек, тогда именно он должен изучать машину. Печатники имеют свойство увольняться, и лучше, чтобы с ними не уходили секреты обслуживания и ремонта.
Отдельная печальная тема - это ремонт электроники. Парадокс, но в нашей стране, где каждый второй закончил физтех и строил "Буран", некому починить сломавшийся тумблер на печатной машине. Специалистов по электронике полно, и оборудования хватает, но они почему-то друг друга не находят. И блок микропроцессорного управления ремонтирует дядя Вася из ОГМ, который в 52-м году закончил двухнедельный курс монтеров-электриков. Одному из нас недавно довелось налаживать б/у машину с нумератором. Долго не удавалось понять, почему не включается нумерация - все датчики работают, соленоиды исправны, реле срабатывают: У прежнего владельца нумератор не использовался, зато была установлена дополнительная лампочка подсветки на приемке. Для нее понадобился выключатель. Тамошние кулибины не стали мудрить, просто оторвали весь жгут кабелей от панели управления нумерацией и кинули провода от лампочки на ее выключатель. Таких примеров варварского вмешательства в машину у нас накопилось много. Поэтому мы пришли к выводу, что лучше, когда электронные узлы являются заповедной зоной, доступной только сервис-инженерам.
Рис 8. Электрика современной печатной машины
Самообразование
Хотя вводное обучение занимает несколько дней, высокая квалификация приобретается годами. Причем не сама собой: печатник должен иметь пытливый ум, а руководство должно создать ему необходимые условия для роста: снабдить книгами, обеспечить подписку на полиграфическую периодику, доступ в Интернет, связь с сервисной службой.
Из книг мы можем рекомендовать, во-первых, классику: "Офсетная печать: проблемы практической работы" Петера Мюллера, вышедшую в 1987 году в издательстве "Книга". Правда, нужно правильно относиться к тому, что в ней написано. Это отнюдь не Священное Писание; многое относится только к большим машинам типа Планеты или вообще устарело. Например, если плохо держат захваты выводного устройства, не надо сразу бросаться подклеивать на них картонные накладки - лучше их просто отрегулировать. Тем не менее эта книга дает очень много для понимания сложных взаимосвязей между состоянием оборудования, свойствами материалов и качеством печати. Довольно много полезного есть и в книге В.Валенски "Бумага плюс печать", выпущенной "Дубль-В" в 1996 году. К сожалению, нам не известны другие книги, посвященные современной технологии офсетной печати. Много статей, посвященных практике офсетной печати, можно найти в периодических журналах: Курсив, Пол играфия, Паблиш, Компьюарт.
15 июля 1999 г
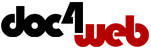
Нравится материал? Поддержи автора!
Ещё документы из категории журналистика :
Чтобы скачать документ, порекомендуйте, пожалуйста, его своим друзьям в любой соц. сети.
После чего кнопка «СКАЧАТЬ» станет доступной!
Кнопочки находятся чуть ниже. Спасибо!
Кнопки:
Скачать документ