Установки погружных центробежных насосов (УЭЦН)
СОДЕРЖАНИЕ
лист
Аннотация (русский язык)
Аннотация (английский язык)
ВВЕДЕНИЕ
1.АНАЛИЗ СУЩЕСТВУЮЩИХ СХЕМ И КОНСТРУКЦИЙ.
1.1.Назначение и технические данные ЭЦН.
1.1.1.Историческая справка о развитии способа добычи.
1.1.2.Состав и комплектность УЭЦН.
1.1.3.Технические характеристики ПЭД.
1.1.4.Основные технические данные кабеля.
1.2. Краткий обзор отечественных схем и установок.
1.2.1.Общие сведения.
1.2.2.Погружной центробежный насос.
1.2.3.Погружные электродвигатели.
1.2.4.Гидрозащита электродвигателя.
1.3.Краткий обзор зарубежных схем и установок.
1.4. Анализ работы УЭЦН.
1.4.1.Анализ фонда скважин.
1.4.2.Анализ фонда ЭЦН.
1.4.3.По подаче.
1.4.4.По напору.
1.5.Краткая характеристика скважин.
1.6.Анализ неисправностей ЭЦН.
1.7.Анализ аварийности фонда УЭЦН.
2.ПАТЕНТНАЯ ПРОРАБОТКА.
2.1.Патентная проработка.
2.2.Обоснование выбранного прототипа.
2.3.Суть модернизации.
3. РАСЧЕТНАЯ ЧАСТЬ.
3.1. Расчет ступени ЭЦН.
3.1.1. Расчет рабочего колеса.
3.1.2. Расчет направляющего аппарата.
3.2.Проверочный расчет шпоночного соединения.
3.3.Проверочный расчет шлицевого соединения.
3.4.Расчет вала ЭЦН.
3.5.Прочностной расчет
3.5.1.Прочностной расчет корпуса насоса.
3.5.2.Прочностной расчет винтов страховочной муфты.
3.5.3.Прочностной расчет корпуса полумуфты.
4.ЭКОНОМИЧЕСКИЙ ЭФФЕКТ ОТ
5.БЕЗОПАСНОСТЬ И ЭКОЛОГИЧНОСТЬ ПРОЕКТА.
6.Литература.
7. Приложение 1
8.Приложение 2
9.Приложение 3
10.Приложение 4
11. Приложение 5.
5
6
7
8
8
8
9
14
15
16
16
17
18
18
19
22
22
22
22
23
24
24
26
28
28
30
31
32
32
32
35
36
38
39
44
44
45
45
47
53
63
64
65
66
67
68
ВВЕДЕНИЕ
УЭЦН предназначены для откачки пластовой жидкости из нефтяных скважин и используется для форсирования отбора жидкости. Установки относятся к группе изделий II, виду I по ГОСТ 27.003-83.
Климатические исполнение погружного оборудования – 5, наземного электрооборудования – I ГОСТ 15150-69.
Для надежной работы насоса требуется его правильный подбор к данной скважине. При работе скважины постоянно меняются параметры плата, призабойной зоны пласта, свойства отбираемой жидкости: содержание воды, количество попутного газа, количество механических примесей, и как следствие, отсюда идет не доотбор жидкости или работа насоса вхолостую, что сокращает межремонтный период работы насоса. На данный момент делается упор на более надежное оборудование, для увеличения межремонтного периода, и как следствие из этого снижение затрат на подъем жидкости. Этого можно добиться, применяя центробежные УЭЦН вместо ШСН, так как центробежные насосы имеют большой межремонтный период.
Установку УЭЦН можно применять при откачке жидкости, содержащих газ, песок, и коррозионо-активные элементы.
1.АНАЛИЗ СУЩЕСТВУЮЩИХ СХЕМ И КОНСТРУКЦИЙ.
1.1.Назначение и технические данные УЭЦН.
Установки погружных центробежных насосов предназначены для откачки из нефтяных скважин, в том числе и наклонных пластовой жидкости, содержащей нефть, воду и газ, и механические примеси. В зависимости от количества различных компонентов, содержащихся в откачиваемой жидкости, насосы установок имеют исполнение обычное и повышенной корозионно-износостойкости. При работе УЭЦН, где в откачиваемой жидкости концентрация мехпримесей превышает допустимую 0,1 грамм\литр происходит засорение насосов, интенсивной износ рабочих агрегатов. Как следствие, усиливается вибрация, попадание воды в ПЭД по торцевым уплотнениям, происходит перегрев двигателя, что приводит к отказу работы УЭЦН.
Условное обозначение установок:
УЭЦН К 5-180-1200, У 2 ЭЦН И 6-350-1100,
Где У – установка, 2 –вторая модификация, Э – с приводом от погружного электродвигателя, Ц – центробежный, Н – насос, К – повышенный коррозионостойкости, И – повышенной износостойкости, М – модульного исполнения, 6 – группы насосов, 180, 350 – подача м\сут, 1200, 1100 – напор, м.в.ст.
В зависимости от диаметра эксплуатационной колонны, максимального поперечного габарита погружного агрегата, применяют ЭЦН различных групп – 5,5, а 6. Установка группы 5 с поперечным диаметром не менее 121,7 мм. Установки группы 5 а с поперечным габаритом 124 мм – в скважинах внутренним диаметром не менее 148,3 мм. Насосы также подразделяют на три условные группы – 5,5 а, 6. Диаметры корпусов группы 5 – 92 мм, группы 5 а – 103 мм, группы 6 – 114 мм. Технические характеристики насосов типа ЭЦНМ и ЭЦНМК приведены в приложении 1.
1.1.1.Историческая справка о развитии способа добычи.
Разработка бесштанговых насосов в нашей стране началась еще до революции. Когда А.С. Артюнов вместе с В.К. Домовым разработали скважинный агрегат, в котором центробежный насос приводился в действие погружным электродвигателем. Советские инженеры, начиная с 20-х годов, предлагали разработку поршневых насосов с поршневым пневматическим двигателем. Одним из первых такие насосы разработал М.И. Марцишевский.
Разработка скважинного насоса с пневмодвигателем была продолжена в Азинмаше В.И.Документовым. скважинные центробежные насосы с электроприводом разрабатывались в предвоенный период А.А.Богдановым, А.В. Крыловым, Л.И. Штурман. Промышленные образцы центробежных насосов с электроприводом были разработаны в особом конструкторском бюро по бесштанговым насосам. Эта организация ведет все работы по скважинным бесштанговым насосам, в том числе и по винтовым, диафрагменным и др.
Нефтегазодобывающая промышленность с открытием новых месторождений нуждалась в насосах для отбора из скважины большого количества жидкости. Естественно, что наиболее рационален лопастной насос, приспособленный для больших подач. Из лопастных насосов получили распространение насосы с рабочими колесами центробежного типа, поскольку они давали большой напор при заданных подачах жидкости и габаритах насоса. Широкое применение скважинных центробежных насосов с электроприводом обусловлено многими факторами. При больших отборах жидкости из скважины установки ЭЦН наиболее экономичные и наименее трудоемки при обслуживании, по сравнению с компрессорной добычей и подъемом жидкости насосами других типов. При больших подачах энергетические затраты на установку относительно невелики. Обслуживание установок ЭЦН просто, так ака на поверхности размещаются только станция управления и трансформатор, не требующие постоянного ухода.
Монтаж оборудования ЭЦН прост, так как станция управления и трансформатор не нуждаются в устройстве фундаментов. Эти два узла установки ЭЦН размещают обычно в легкой будке.
1.1.2.Состав и комплектность УЭЦН
Установка УЭЦН состоит из погружного насосного агрегата (электродвигателя с гидрозащитой и насоса), кабельной линии (круглого плоского кабеля с муфтой кабельного ввода), колонны НКТ, оборудования устья скважины и наземного электрооборудования: трансформатора и станции управления (комплектного устройства) (см. рисунок 1.1.). Трансформаторная подстанция преобразует напряжение промысловой сети дооптимальной величины на зажимах электродвигателя с учетом потерь напряжения в кабеле. Станция управления обеспечивает управление работой насосных агрегатов и его защиту при оптимальных режимах.
Погружной насосный агрегат, состоящий из насоса и электродвигателя с гидрозащитой и компенсатора, опускается в скважину по НКТ. Кабельная линия обеспечивает подвод электроэнергии к электродвигателю. Кабель крепится к НКТ, металлическими колесами. На длине насоса и протектора кабель плоский, прикреплен к ним металлическим колесами и защищен от повреждений кожухами и хомутами. Над секциями насоса устанавливаются обратный и сливной клапаны. Насос откачивает жидкость из скважины и подает ее на поверхность по колонне НКТ (см. рисунок 1.2.)
Оборудование устья скважины обеспечивает подвеску на фланце обсадной колонны НКТ с электронасосом и кабелем, герметизацию труб и кабеля, а также отвод добываемой жидкости в выходной трубопровод.
Насос погружной, центробежный, секционный, многоступенчатый не отличается по принципу действия от обычных центробежный насосов.
Отличие его в том, что он секционный, многоступенчатый, с малым диаметром рабочих ступеней – рабочих колес и направляющих аппаратов. Выпускаемые для нефтяной промышленности погружные насосы содержат от 1300 до 415 ступеней.
Секции насоса, связанные фланцевыми соединениями, представляют собой металлический корпус. Изготовленный из стальной трубы длиной 5500 мм. Длина насоса определяется числом рабочих ступеней, число которых, в свою очередь, определяется основными параметрами насоса. – подачей и напором. Подача и напор ступеней зависят от поперечного сечения и конструкции проточной части (лопаток), а также от частоты вращения. В корпусе секций насоса вставляется пакет ступеней представляющих собой собрание на валу рабочих колес и направляющих аппаратов.
Рабочие колеса устанавливаются на валу на призматической шпонке по ходовой посадке и могут перемещаться в осевом направлении. Направляющие аппараты закреплены от поворота в корпусе ниппеля, расположенным в верхней части насоса. Снизу в корпус ввинчивают основание насоса с приемными отверстиями и фильтром, через которые жидкость из скважины поступает к первой ступени насоса.
Верхний конец вала насоса вращается в подшипниках сальника и заканчивается специальной пяткой, воспринимающей нагрузку на вал и его вес через пружинное кольцо. Радиальные усилия в насосе воспринимаются подшипниками скольжения, устанавливаемыми в основании ниппеля и на валу насоса.
В верхней части насоса находится ловильная головка, в которой устанавливается обратный клапан и к которой крепится НКТ.
Электродвигатель погружной, трехфазовый, асинхронный, маслозаполненный с короткозамкнутым ротором в обычном исполнении и коррозионностойком исполнениях ПЭДУ (ТУ 16-652-029-86). Климатическое исполнение – В, категория размещения – 5 по ГОСТ 15150 – 69. В основании электродвигателя предусмотрены клапан для закачки масла и его слива, а также фильтр для очистки масла от механических примесей.
Гидрозащита ПЭД состоит из протектора и компенсатора. Она предназначена для предохранения внутренней полости электродвигателя от попадания пластовой жидкости, а также компенсации температурных изменений объемов масла и его расхода. (см. рисунок 1.3.)
Протектор двухкамерный, с резиновой диафрагмой и торцевыми уплотнениями вала, компенсатор с резиновой диафрагмой.
Кабель трехжильный с полиэтиленовой изоляцией, бронированный. Кабельная линия, т.е. кабель намотанный на барабан, к основанию которого присоединен удлинитель – плоский кабель с муфтой кабельного ввода. Каждая жила кабеля имеет слой изоляции и оболочку, подушки из прорезиненной ткани и брони. Три изолированные жилы плоского кабеля уложены параллельно в ряд, а круглового скручены по винтовой линии. Кабель в сборе имеет унифицированную муфту кабельного ввода К 38, К 46 круглого типа. В металлическом корпусе муфты герметично заделаны с помощью резинового уплотнения, к токопроводящим жилам прикреплены наконечники.
Конструкция установок УЭЦНК, УЭЦНМ с насосом имеющим вал и ступени, выполненные из коррозионностойких материалов, и УЭЦНИ с насосом, имеющим пластмассовые рабочие колеса и резинометаллические подшипники аналогична конструкция установок УЭЦН.
При большом газовом факторе применяют насосные модули – газосепараторы, предназначенные для уменьшения объемного содержания свободного газа на приеме насоса. Газосепараторы соответствуют группе изделий 5, виду 1 (восстанавливаемые) по РД 50-650-87, климатическое исполнение - В, категория размещения – 5 по ГОСТ 15150-69.
Модули могут быть поставлены в двух исполнениях:
Газосепараторы: 1 МНГ 5, 1 МНГ5а, 1МНГ6 – обычного исполнения;
Газосепараторы 1 МНГК5, МНГ5а – повышенной коррозионной стойкости.
Модули насосные устанавливаются между входным модулем и модулем-секцией погружного насоса.
Погружной насос, электродвигатель, и гидрозащита соединяются между собой фланцами и шпильками. Валы насоса, двигателя и протектора имеют на концах шлицы и соединяются шлицевыми муфтами.
Комплектующие подъемы и оборудование установок ЭЦН приведены в приложении 2.
1.1.3.Технические характеристика ПЭД
Приводом погружных центробежных насосов служит специальный маслозаполненный погружной ассинхронный электродвигатель трехфазного переменного тока с короткозамкнутым ротором вертикального исполнения типа ПЭД. Электродвигатели имеют диаметры корпусов 103, 117, 123, 130, 138 мм. Поскольку диаметр электродвигателя ограничен, при больших мощностях двигатель имеет большую длину, а в некоторых случаях выполнения секционным. Так как электродвигатель работает погруженным в жидкость и часто под большим гидростатическим давлением, основное условие надежной работы – его герметичность (см. рисунок 1.3).
ПЭД заполняется специальным маловязким, высокой диэлектрической прочности маслом, служащим как для охлаждения, так и для смазки деталей.
Погружной электродвигатель состоит из статора, ротора, головки, основания. Корпус статора изготавливается из стальной трубы, на концах которой предусмотрена резьба для подсоединения головки и основания двигателя. Магнитопровод статора собирается из активных и немагнитных шихтованных жестей, имеющих пазы, в которых располагаются обмотка. Обмотка статора может быть однослойной, протяжной, катушечной или двухслойной, стержневой, петлевой. Фазы обмотки соединены.
Активная часть магнитопровода совместно с обмоткой создает в электродвигателей вращающееся магнитное поле, а немагнитная часть служит опорами для промежуточных подшипников ротора. К концам обмотки статора припаивают выводные концы, изготовленные из многожильной медного провода с изоляцией, имеющий высокую электрическую и механическую прочность. К концам припаивают штежельные гильзы, в которые входят наконечники кабеля. Выводные концы обмотки соединяют с кабелем через специальную штежельную колодку (муфту) кабельного ввода. Токоввод двигателя может быть и ножевого типа. Ротор двигателя короткозамкнутый, многосекционный. В его состав входят вал, сердечники (пакеты ротора), радиальные опоры (подшипники скольжения). Вал ротора выполнен из пустотелой калиброванной стали, сердечники из листовой электротехнической стали. Сердечники набираются на вал, чередуясь с радиальными подшипниками, и соединены с валом шпонками. Набор сердечников на валу затянуть в осевом направлении гайками или турбинкой. Турбинка служит для принудительной циркуляции масла для выравнивания температуры двигателя на длине статора. Для обеспечения циркуляции масла на погружной поверхности магнитопровода имеются продольные пазы. Масло циркуляцией через эти пазы, фильтра в нижней части двигателя, где оно очищается, и через отверстие в валу. В головке двигателя расположены пята и подшипник. Переводник в нижней части двигателя служит для размещения фильтра, перепускного клапана и клапана для закачки масла в двигатель. Электродвигатель секционного исполнения состоит из верхней и нижней секций. Каждая секция имеет такие же основные узлы. Технические характеристики ПЭД приведены в приложении 3.
1.1.4.Основные технические данные кабеля
Подвод электроэнергии к электродвигателю установки погружного насоса осуществляется через кабельную линию, состоящую из питающего кабеля и муфты кабельного ввода для сочленения с электродвигателем.
В зависимости от назначения в кабельную линию могут входить:
Кабель марок КПБК или КППБПС – в качестве основного кабеля.
Кабель марки КПБП (плоский)
Муфта кабельного ввода круглая или плоская.
Кабель КПБК состоит из медных однопроволочных или многопроволочных жил, изолированных в два слоя полиэтиленом высокой прочности и скрученных между собой, а также подушки и брони.
Кабели марок КПБП и КППБПС в общей шланговой оболочке состоят из медных однопроволочных и многопроволочных жил, изолированных полиэтиленом высокой плотности и уложенных в одной плоскости, а так же из общей шланговой оболочке, подушки и брони.
Кабели марки КППБПС с отдельно отшлангованными жилами состоят из медных одно-,многопроволочных жил, изолированных в два слоя полиэтилена высокого давления и уложенных в одной плоскости.
Кабель марки КПБК имеет:
Рабочее напряжение В – 3300
Допустимое давление пластовой жидкости, МПа – 19,6
Допустимый газовый фактор, м/т – 180
Кабель марки КПБП имеет:
Рабочее напряжение, В - 2500
Допустимое давление пластовой жидкости, МПа – 19,6
Допустимый газовый фактор, м/т – 180
Кабель марки КПБК и КПБП имеет допустимые температуры окружающей среды от 60 до 45 С воздуха, 90 С – пластовой жидкости.
Температуры кабельных линий приведены в приложении 4.
1.2.Краткий обзор отечественных схем и установок.
1.2.1.Общие сведения
Установки погружных центробежных насосов предназначены для откачивания нефтяных скважин, в том числе наклонных, пластовой жидкости, содержащей нефть и газ, и механической примеси.
Установки выпускаются двух видов – модульные и немодульные; трех исполнений: обычное, коррозионостойкое и повышенной износостойкости. Перекачиваемая среда отечественных насосов должна иметь следующие показатели:
пластовая дикость – смесь нефти, попутной воды и нефтяного газа;
максимальная кинематическая вязкость пластовой жидкости 1 мм\с;
водородный показатель попутной воды рН 6,0-8.3;
содержание мехпримесей для обычного и коррозионостойкого не более 0,1 г\л, износостойкого не более 0.5 г\л;
содержание сероводорода для обычного и износостойкого не более 0,01 г\л; корозионостойкого до 1.25 г\л;
максимальное содержание полученной воды 99%;
свободного газа на приеме до 25%, для установок с модулями – сепараторами до 55%;
максимальная температура добываемой продукции до 90С.
В зависимости от поперечных размеров применяемых в комплекте установок погружных центробежных электронасосов, элетродвигателей и кабельных линий установки условно делятся на 2 группы 5 и 5 а. С диаметрами обсадных колонн 121.7 мм; 130 мм; 144,3 мм соответственно.
Установка УЭЦ состоит из погружного насосного агрегата, кабеля в сборе, наземного электрооборудования – трансформаторной комилентной подстанции. Насосный агрегат состоит из погружного центробежного насоса и двигателя с гидрозащитой, спускается в скважину на колонне НКТ. Насос погружной, трехфазный, асинхронный, маслозаполненный с ротором.
Гидрозащита состоит из протектора и компенсатора. Кабель трехжильный с полиэтиленовой изоляцией, бронированный.
Погружной насос, электродвигатель и гидрозащита соединяются между собой фланцами и шпильками. Валы насоса, двигателя и протектора имеют на концах шлицы и соединяются шлицевыми муфтами.
1.2.2. Погружной центробежный насос.
Погружной центробежный насос по принципу действия не отличается от обычных центробежных насосов, применяемых для перекачки жидкости. Отличие в том, что он многосекционный с малым диаметром рабочих ступеней – рабочих колес и направляющих аппаратов. Рабочие колеса и направляющие аппараты насосов обычного исполнения изготавливают из модифицированного серого чугуна, насосов коррозионностойких – чугуна типа «нирезист», износостойких колес – их полиамидных смол.
Насос состоит из секций, число которых зависит от основных параметров насоса – напора, но не более четырех. Длина секции до 5500 метров. У модульных насосов состоит из входного модуля, модуля – секции. Модуль – головки, обратного и спускного клапанов. Соединение модулей между собой и входного модуля с двигателем – фланцевое соединение (кроме входного модуля, двигателем или сепаратором) уплотняются резиновыми манжетами. Соединение валов модулей-секций между собой, модуля-секции с валом входного модуля, вала входного модуля с валом гидрозащиты двигателя осуществляется шлицевыми муфтами. Валы модулей-секций всех групп насосов имеющих одинаковые длины корпусов унифицированы по длине.
Модуль-секция состоит из корпуса, вала, пакета ступеней (рабочих колес и направляющих аппаратов), верхнего и нижнего подшипников, верхней осевой опоры, головки, основания, двух ребер и резиновых колец. Ребра предназначены для защиты плоского кабеля с муфтой от механических повреждений.
Входной модуль состоит из основания с отверстиями для прохода пластовой жидкости, подшипниковых втулок и сетки, вала с защитными втулками и шлицевой муфтой, предназначенной для соединения вала модуля с валом гидрозащиты.
Модуль-головка состоит из корпуса, с одной стороны которого имеется внутренняя коническая резьба для подсоединения обратного клапана, с другой стороны – фланец для подсоединения к модулю-секции, двух ребер и резинового кольца.
В верхней части насоса имеется ловильная головка.
Отечественной промышленностью выпускаются насосы с подачей (м/сут):
Модульные – 50,80,125,200.160,250,400,500,320,800,1000.1250.
Немодульные – 40.80,130.160,100,200,250,360,350,500,700,1000.
Следующих напоров (м) - 700, 800, 900, 1000, 1400, 1700, 1800, 950, 1250, 1050, 1600, 1100, 750, 1150, 1450, 1750, 1800, 1700, 1550, 1300.
1.2.3. Погружные электродвигатели
Погружные электродвигатели состоят из электродвигателя и гидрозащиты.
Двигатели трехфазные, ассинхронные, короткозамкнутые, двухполюсные, погружные, унифицированной серии. ПЭД в нормальном и коррозионном исполнениях, климатического исполнения В, категории размещения 5, работают от сети переменного тока частотой 50 Гц и используются в качестве привода погружных центробежных насосов.
Двигатели предназначены для работы в среде пластовой жидкости (смесь нефти и попутной воды в любых пропорциях) с температурой до 110 С содержащей:
мехпримесей не более 0.5 г/л;
свободного газа не более 50%;
сероводорода для нормальных, не более 0.01 г/л, коррозионностойких до 1,25 г/л;
Гидрозащитное давление в зоне работы двигателя не более 20 МПа. Электродвигатели заполняются маслом с пробивным напряжением не менее 30 КВ. Предельная длительно допускаемая температура обмотки статора электродвигателя (для двигателя с диаметром корпуса 103 мм) равна 170 С, остальных электродвигателей 160 С.
Двигатель состоит из одного или нескольких электродвигателей (верхнего, среднего и нижнего, мощностью от 63 до 630 КВт) и протектора. Электродвигатель состоит из статора, ротора, головки с токовводом, корпуса.
1.2.4. Гидрозащита электродвигателя.
Гидрозащита предназначена для предотвращения проникновения пластовой жидкости во внутреннюю полость электродвигателя, компенсации объема масла во внутренней полости от температуры электродвигателя и передачи крутящего момента от вала электродвигателя к валу насоса. Существует несколько вариантов гидрозащиты: П, ПД, Г.
Гидрозащиту выпускают обычного и коррозионностойкого исполнений. Основным типом гидрозащиты для комплектации ПЭД принята гидрозащита открытого типа. Гидрозащита открытого типа требует применения специальной барьерной жидкости плотностью до 21 г/см, обладающий физико-химическими свойствами с пластовой жидкостью и маслом.
Гидрозащита состоит из двух камер сообщенных трубкой. Изменение объемов жидкого диэлектрика в двигателе компенсируется перетоком барьерной жидкости из одной камеры в другую. В гидрозащите закрытого
типа применяются резиновые диафрагмы. Их эластичность компенсирует изменение объема масла.
1.3. Краткий обзор зарубежных схем и установок.
Наиболее крупными фирмами, выпускающими погружные центробежные насосные установки являются «Реда ламп», «Оил дайнемикс».
Погружные центробежные насосы применяются для добычи нефтепродуктов в ряден стран.
Насосы имеют по 2 верхние и 2 нижние секции.
Рассчитаны на работу в скважинах:
с температурой до 95С;
содержание мехпримесей не более 0,5г\л;
сероводорода до 1,25 г\л;
свободного газа на приеме насоса до 35%.
После определения производительности скважины выбирается насос соответствующего размера. Характеристиками рабочего колеса центробежного насоса являются большое давление сверху вниз при низком уровне дебита. Чтобы продлить срок службы насоса, фирма ОДИ рекомендует использовать специальное оборудование, если предполагается значительное содержание песка – гофрированный резиновый подшипник – используется для осевой поддержки насоса. Резина обеспечивает прочную упругую поверхность осевого подшипника. Такая поверхность позволяет частица песка перекатывается по поверхности подшипника, не царапая ее. Канавки обеспечивают отвод для частиц песка, которые затем вымываются из подшипника. Если насос теряет осевую стабильность, вал начинает вращаться эксцентрично, что приводит к увеличению боковой нагрузки и эксцентричному вращению опорных шайб и сокращает срок службы насоса до нескольких часов.
Опорные модули с заполненными опорными колесами и подшипниками обеспечивают осевую и радиальную поддержку насоса благодаря износостойким материалам, намного тверже песка, устойчивым к воздействию агрессивных газовых и химических сред.
Насосы фирмы ОДИ отличаются от других зарубежных образцов:
две опорные ступени насоса;
валы секций не имеют своей пяты и, упираясь, друг в друга образуют вал, который передает осевую нагрузку на пяту расположенную в протекторе;
валы соединяются между собой с помощью зацепления;
вал, общей длиной более 24 метров имеет только одну осевую опору в нижней части и подвергается продольному изгибу;
в каждой двенадцатой ступени размещены бронированные втулки.
Фирма выпускает насос двух габаритов: 139.7 мм и 177.8 мм (диаметры обсадных колонн) следующих типов ( таблица 1.1)
Таблица 1.1.
Тип
насоса
Наружный
Диаметр,
(мм)
Максимальная мощность на валу насоса, КВт
Номинальная подача,
м/сут
Допустимое давление на пяту,
м.в.ст.
R 3
30-50
3862
RC 5
50-73
RA 7
90-125
R 9
109-133
RC 12
101,6
200
133-186
R 14
150-212
RA 16
186-239
RA 22
239-311
R 32
311-437
2652
R 38
437-570
1676
Двигатель фирмы отличается конструкцией – число пазов ротора и статора 18 и 23 соответственно, у других соответственно 18 и 16. Двигатели очень чувствительны к температуре, имеют малый температурный запас. Очень важна скорость обливающей их жидкости, фирма специально оговаривает диаметры скважин, в которые ставят ее двигатели. Фирма ODI предусматривает регуляторы частоты вращения двигателя и считается, что плавный пуск защитит двигатель, хотя есть вероятность того, что высокий ток на отдельных фазах может выбить пробки. В общем. Технические характеристики у двигателей фирмы ODI ниже, чем у отечественных двигателей.
Фирма ODI скопировала советские протекторы ГД и 1Г51. Она использует к гидрозащите вихревые газосепараторы KGV и RGV, если объем свободного газа на приеме достигает 10%. Используются для определения влияния повышенного содержания газа на работу насоса (рабочие характеристики вихревых газосепараторов).
Фирма ODI не является лучшей фирмой, представляющей на мировом рынке погружные центробежные насосы, но и не является плохой фирмой.
Более конкретно о технических данных насосов фирмы ODI представлено в приложении.
При разработке конструкции ступеней насосов фирма уделяет особое внимание проблеме защиты от абразии.
1.В ODI используется особая конструкция диффузора во всех ступенях насосов 55 и 70 серий для того, чтобы исключить попадание песка в область опорной втулки.
Конструкция ступени фирмы ODI представлена на рис.1.4.
1 – балансная гидравлическая конструкция устраняет необходимость балансных отверстий;
2 - пьедестальная конструкция позволяет плавный проток жидкости в рабочее колесо;
3 – поскольку в нормальном режиме рабочее колесо давит на опору сверху, такая конструкция препятствует попаданию песка в область между втулкой рабочего о поры диффузора;
4 – две опоры с феноловыми шайбами уменьшают радиальную нагрузку и увеличивают продолжительность службы шайб.
1.4.Аанализ работы ЭЦН..
1.4.1.Анализ фонда ЭЦН по АО “Сургутнефтегаз”
Таблица 1.1.
состояние
всего
Т И П О Б О Р У Д О В А Н И Я
ЭЦН5-20
ЭЦН5-30
ЭЦН5-80
ЭЦН5-125
ЭЦН5М-50
ЭЦН5-250
ЭЦН5А-250
ЭЦН5А-400
ЭЦН5А-500
ЭЦН5А-16
ЭЦН5А-25
Центрилифт
ODI
ВНН
ЦУНАР
прочие
Спущено в скважину
7769
302
27
1535
843
3891
360
148
73
33
17
6
105
387
42
0
0
В работе
6857
221
25
1372
768
3372
333
139
65
31
8
2
105
375
41
0
0
В простое
912
81
2
163
75
519
27
9
8
2
9
4
0
12
1
0
0
1.4.2 Анализ фонда скважин.
1.4.3. По подаче.
За последние годы было выпущено около 1042 насосов типа ЭЦН, из них :
2,5% - ЭЦН 20
38,9% - ЭЦН 50
15,0% - ЭЦН 80
12,1% - ЭЦН 125
1,7% - ЭЦН 160
7,6% - ЭЦН 200
7,3% - ЭЦН 250
2,5% - ЭЦН 360
11,3% - ЭЦН 500
Таблица 1.2.
Типоразмер
Фонд
на 1.01.97
Типоразмер
Фонд
на 1.01.97
ЭЦН 30
25
ЭЦН 200
76
ЭЦН 50
389
ЭЦН 250
73
ЭЦН 80
150
ЭЦН 360
25
ЭЦН 125
121
ЭЦН 500
113
ЭЦН 160
17
Всего
989
Импортного производства:
Таблица 1.3.
Типоразмер
Фонд
на 1.01.97
Типоразмер
Фонд
на 1.01.97
R – 3
6
RA – 16
1
RC – 5
9
RA – 22
1
RA – 7
5
R – 32
2
R – 9
6
R – 32
10
RC – 12
7
Всего ODI
53
R - 14
6
1.4.4.По напору.
По напору насосы распределились следующим образом:
35,7% - напор 1300 метров
17,8 – напор 1200 метров
напор 1400 метров
напор 1700 метров
напор 900 метров
напор 750 метров
напор 100 метров
В настоящее время растет необходимость в напоре 1300, 1700, 1800 метров с подачей 30.50 кубических метров.
1.5. Краткая характеристика скважин
Скважины бурились на месторождениях кустовым способом, все наклонно-направленные. Средняя глубина до 3000 метров. Угол наклона скважины до 45. Глубина спуска насоса колеблется в пределах от 1200 до 1700 метров.
Динамический уровень:
-самый малый – устье;
-самый большой – > 1000 метров.
Динамический уровень в основном колеблется в пределах от 0 до 800 метров. В настоящее время наблюдается все большее снижение уровня нефти в скважинах месторождений, увеличение числа скважин с динамическим уровнем больше одного километра.
Распределение фонда УЭЦН по динамическим уровням за 1996 год представлено в таблице 1.4.
Таблица 1.4.
0-200
201-400
401-800
801-1000
>1000
всего
действ.
фонд.
193
152
389
166
115
1015
1115
17,3%
13,6%
34,9%
14,9%
10,3%
91,0%
100%
1.6.Анализ неисправностей ЭЦН.
На предприятиях используются как модульные, так и немодульные насосные установки.
К неисправностям насосных установок можно отнести следующие неисправности:
- реже всего выходит из строя гидрозащита, основной поломкой является прорыв резиновой диафрагмы;
- двигатели выходят из строя из-за пробоя статора нижнего или верхнего оснований, а также коррозии корпуса;
- насос выходит из строя чаще всего из-за засорения мехпримесями, быстро изнашивается вал насоса.
Распределение отказов УЭЦН по укрупненным причинам за 1997 год представлен в таблице 1.5.
Таблица 1.5.
-
причины
НГДП
Нет подачи
200
R - 0
1020
Клин
15
Негерметичность НКТ
32
прочие
48
ВСЕГО
1315
Причины отказа погружных насосов выглядят следующим образом:
Таблица 1.6.
№
Причины отказа
1996 г.
1995 г
1
Мехповреждение кабеля
71
69
2
Засорение мехпримесями
162
118
3
Агрессивная среда
1
7
4
Негерметичность НКТ
14
7
5
Несоответствие кривизны
6
27
6
Некачественное глушение
2
2
7
Электроснабжение
3
6
8
Нарушение э/колонны
1
2
9
Некачественный монтаж
29
65
10
Полет ЭЦН
7
1
11
Комплектация несоотв. заявке
26
18
12
Бесконтрольная эксплуатация
39
35
13
ГТМ
17
4
14
Причина не выявлена НГДП
59
53
15
Прочие
91
-
Итого по вине НГДП
528
414
16
Брак ремонта кабеля
7
12
17
Брак ремонта ПЭД
9
8
18
Брак ремонта гидрозащиты
1
4
19
Брак ремонта насоса
1
-
20
Скрытый дефект оборудования
31
13
21
Причина не установлена ЭПУ
3
1
Итого по вине ЭПУ
52
38
НДП + ЭПУ
Спорные
Заводской брак
5
14
Итого отказов
585
466
Из таблицы видно, что самым значительным техническим фактором, влияющим на работу установок ЭЦН. И являющимися причинами выхода из строя можно назвать мехповреждения кабеля, засорение примесями, некачественный монтаж, а также несоответствие кривизны ствола скважины, и бесконтрольное эксплуатация. Отсюда следует, что забивание мехпримесями является важным фактором влияющим на срок службы насоса, а борьба с ними должна привести к увеличению межремонтного периода установки. За 1997 год межремонтный период и наработки на отказ имеют следующие значения:
Таблица 1.7.
Эксплуат.
фонд
Действ.
фонд
Отказы
Наработка
на отказ
Кол-во
ремонтов
МРП
Средний дебет
Обводненность
1995
1996
1995
1996
1995
1996
1995
1996
1995
1996
1995
1996
1995
1996
1995
1996
1576
1431
1168
1115
1172
1315
264
266
1226
1224
310
310
114.5
122.6
89,0
90,4
1.7.Анализ аварийного фонда по НГДУ «Лянторнефть»
В 1997 году произошло 60 полетов на 60 скважинах оборудованных установками электроцентрированных насосов. За прошедшие 5 лет наметилась тенденция увеличения количества аварий по фонду УЭЦН. В отчетном году аварийность повысилась на 16 скважин, по сравнению с аналогичным периодом 1996 года. Большая часть полетов произошли в результате расчленения фланцевых соединениях УЭЦН – 48%. Здесь следует выделить обрывы по шпилькам между секциями насоса – 25% и метод ПЭД и протектором гидрозащиты – 10%. Следующая группа обрывов – обрывы по НКТ. Основная доля обрывов приходится на нижнюю и верхнюю часть колонны НКТ, соответственно – 44% и 38%. Все остальные аварии относятся к категории частных случаев. Последняя большая группа аварий – это аварии по причине слома по телу узлов УЭЦН. По данной причине 4 полета получено в результате слома по телу корпуса секций насосов, 3 – по корпусу гидрозащиты, 1 – по телу ловильной головки. Сломы по «шейки насосов» возросли с 1 полета в 1996 г до 5 в 1997 году. Проводя анализ эксплуатации аварийного фонда скважин УЭЦН достаточно четко просматривается влияние осложняющих факторов на работу УЭЦН ставших причиной полета на этих скважинах. В первую очередь, львиная доля полетов получена на таких пластах, как А 4-5 и А 2-3, где наблюдается интенсивный вынос мехпримесей и высока степень коррозии. Высокое содержание мехпримесей в добываемой жидкости наблюдается практически по всем скважинам аварийного фонда, особенно на момент запуска и первых дней эксплуатации. Более того по ряду скважин в период работы содержание мехпримесей не только остается на одном уровне, но и увеличивается. Снижение выноса мехпримесей говорит о том, что установка начала снижать свою производительность из-за износа рабочих органов насоса.
Основными причинами аварий являются следующие факторы:
1.Повышенное содержание мехпримесей в добываемой жидкости как после ремонта, так и в процессе эксплуатации, что вызывает интенсивный износ оборудования, что в свою очередь повышает вибрационные нагрузки.
2.Некачественные крепежные материалы, применяемые при монтаже УЭЦН, которые не выдерживают вибрационные нагрузки в процессе работы. Монтаж зачастую проводится крепежными материалами не соответствующими ГОСТ.
3.Увеличение полетов 1997 году связано также низким уровнем обеспечения нефтепромысловым оборудованием, в результате чего не обновляется парк подземного оборудования.
4.Недостаточным контролем со стороны технических служб ДАОЗТ за режимом работы скважин.
5.«Спутник».
Предлагаемые меры по сокращению аварийности:
1.Повышать контроль за работой скважин, особенно по пластам А 4-5 и А
2-3. Здесь необходимо 1 раз в месяц отбирать пробу добываемой местности на анализ содержания мехпримесей (по пластам А 4-5 и А 2-3 2 раза в месяц), 2 раза в месяц (в начале и в конце) контролировать УЭЦН по динамическому уровню.
2.Производить спуск УЭЦН на заданную глубину (7-10 метров) только с замером НКТ, что исключит попадание установки в зону повышенной кривизны.
3.Рассмотреть вопрос о приобретении НКТ с антикоррозийным покрытием для спуска в скважину коррозийного фонда.
4.Увеличить процент обновляемости парка подземного ремонта.
5.При ПДС производить зачистку резьбы труб и муфт перед свинчиванием, более качественно проводить отбраковку НКТ по износу резьбовых соединений.
6.Возбновить работу ПДК по авариям, более детально подойти к расследованию причин полетов.
Подробное распределение отказов представлено в приложении 5.
2. ПАТЕНТНАЯ ПРОРАБОТКА
2.1. Патентная проработка
М.М. Трусов, В.Я. Райт, и др. Авторское свидетельство № 597785, №
21, 1976 г. с.4. «Скважинная насосная установка».
Изобретение относится к гидромашиностроению и может быть использовано в конструкциях скважинных насосных установок, предназначенных для откачивания сред, содержащих механические примеси.
Цель изобретения - уменьшение габаритов и металлоемкости установки, а также повышение степени очистки перекачиваемой среды.
Поставленная цель достигается тем, что в скважинной насосной установке, содержащей центробежный насос, размещенный под ним электродвигатель, установленный на выходе насоса гидроэлеватор с наружным кожухом и камерой смещения и деформируемый пакер, последний расположен выше гидроэлеватора, в наружном кожухе гидроэлеватора выполнены отверстия и его камера смешения сообщена с областью всасывания насоса посредством упомянутых отверстий, а электродвигатель снабжен спиральной направляющей на его наружной поверхности.
2.О.М. Юсупов, М.Д. Валеев и др. Авторское свидетельство № 1019111,
№ 19, 1982 г., с 4. «Способ запуска центробежного насоса».
Изобретение относится к гидромашиностроению и может быть использовано при эксплуатации центробежных насосов для подъема жидкости из скважины.
Цель изобретения - упрощение технологии запуска.
Указанная цель достигается тем, что согласно способу запуска центробежного насоса, откачивающего газированную жидкость и установленного в скважине на колонне подъемных труб, подключенной в верхней части к выкидной линии и затрубному пространству скважины, включающему создание положительной разности давлений на выходе и выходе насоса, раскрутку ротора последнего в турбинном режиме жидкостью, перетекающей из затрубного пространства в колонну подъемных труб под действием созданной разности давлений, и включение электродвигателя насоса, предварительно отключают колонну труб от выкидной линии и затрубного пространства, а создание положительной разности давлений осуществляют путем выпуска газа на верхней части колонны труб.
Ю.Г.Вагапов, А.А.Ланкин и др. Авторское свидетельство № 808698,
№ 8, 1981 г., с.4. «Погружной электроцентробежный агрегат».
Изобретение относится к насосостроению и может найти применение в погружных электроцентробежных насосах, предназначенных, например, для добычи нефти из скважин.
Цель изобретения – обеспечение возможности обратной прокачки жидкости через насос и измерения давления на приеме насоса.
Указанная цель достигается тем, что насос дополнительно содержит муфту, закрепленную над обратным клапаном, в которой размещен специальный груз со штоком в нижней части, проходящим через отверстие седла клапана, причем груз имеет сквозное отверстие.
Л.А.Чернобай, А.М. Романов и др. Авторское свидетельство №
1028893, № 26, 1981 г., с 4. «Погружной центробежный насосный агрегат».
Изобретение относится к гидромашиностроению, более конкретно к конструкциям насосных установок для подъема минерализованных жидкостей, например обводненной нефти, из скважины.
Цель изобретения – повышение долговечности при использовании агрегата для перекачивания обводненной нефти.
Поставленная цель достигается тем, что в погружном центробежным агрегате излучатель снабжен расположенным по обе стороны от него кольцевыми камерами, сообщенными с отверстиями.
5. С.А. Войтко, А.А. Гунин и др. Авторское свидетельство № 1083696,
1981 г., с.3. «Скважинная насосная установка».
Изобретение относится к области гидромашиностроения и может быть использовано в конструкциях насосных установок, предназначенных для откачивания жидкости с механическими примесями из скважин.
Цель изобретения – в повышении надежности и уменьшения габаритов установки.
Поставленная цель достигается тем, что в скважинной насосной установке, содержащей установленный на колонне подъемных труб насос, размещенный на выходе последнего пескоотстойник, снабженный в нижней части нормально открытым клапаном, и обводную трубу, нижний конец которой непосредственно сообщен с выходом насоса, а верхний через обратный клапан – с полостью колонны труб, обводная труба расположена внутри пескоотстойника, а нормально открытый клапан выполнен подпружиненным и имеет внутреннюю
полость, уплотненную относительно полости колонны труб и гидравлически связанную с выходом.
2.2.Обоснование выбранного прототипа.
Большое значение имеют погружные центробежные насосы для нефтедобывающей промышленности. Скважины, оборудованные установками погружных центробежных электронасосов, выгодно отличаются от скважин, оборудованных глубинонасосными установками. Применение такого оборудования позволяет вводить скважины в эксплуатацию сразу же после бурения в любой период года, без больших затрат времени и средств на сооружение фундаментов и монтаж тяжелого оборудования. Спуск электронасоса в скважину отличается от обычного для промыслов спуска НКТ лишь наличием кабеля и необходимостью его крепления к трубам, сборка же самого электронасоса на устье скважины очень проста и занимает по нормам не более 2-3 часов.
Характерной особенностью погружных центробежных насоса является простота обслуживания, экономичность, относительно большой межремонтный период их работы.
Насосный агрегат, состоящий из погружного центробежного насоса, двигателя и гидрозащиты спущен на колонне НКТ в скважину. Насосный агрегат откачивает пластовую жидкость из скважины и подает ее на поверхность по колонне НКТ. Кабель в сборе, обеспечивает подвод электроэнергии к электродвигателю, крепится к гидрозащите, насосу и колоне НКТ хомутами. Насос погружной, центробежный, модульный, многоступенчатый, вертикального исполнения.
Базовой моделью для моего усовершенствования является УЭЦН 5 50-1300, так как на основании проведенного анализа полетов УЭЦНМ в АО «Сургутнефтегаз» видно, что влияние вибрации в модульных насоса ЭЦН приводит к обрыву болтов во фланцевых соединениях, не только самого верхнего, но и ниже. На основании этого предлагается конструкция противополетного устройства, устанавливаемого на каждое фланцевое соединение насосного агрегата, описанное далее.
2.3.Суть модернизации.
Страховочные муфты предназначены для предотвращения падения установок в скважину при ее расчленении по фланцевому соединению.
Устанавливаются страховочные муфты между модуль-секциями насоса (кроме соединения входной модуль – модель-секция) и между модуль-головкой и модуль секцией. Если применяется противополетная головка.
Монтаж-демонтаж установок производится согласно «Инструкции по монтажу-демонтажу на устье скважин погружных электроцентробежных насосов для добычи нефти» со следующими дополнениями.
После соединения верхней и нижней секций, приподнять агрегат и установить на фланцевом соединении страховочную муфту в следующей последовательности:
1.Вывинтить стягивающие винты из корпуса муфты для рассоединения двух частей.
2.Установить обе части муфты на фланцевое соединение винтами вниз так, чтобы срезанная плоскими часть муфты находилась под кабелем.
3.Соединить часть муфты винтами при помощи шестигранного ключа, и расклинить винты со стороны разрезанной части, для предотвращения самопроизвольного развинчивания.
Аналогично установить муфту при наличии многосекционного насоса между всеми модулями.
Демонтаж муфты осуществить следующим образом:
1.Сжать плоскогубцами расклиненные концы винтов.
2.Вывинтить винты из корпуса страховочные муфты, разъединить части муфты и снять их.
3. РАСЧЕТНАЯ ЧАСТЬ
3.1.Расчет ступени ЭЦН
3.1.1.Расчет рабочего колеса.
При расчете ступени погружного центробежного насоса всегда известны подача и напор насоса, скорость вращения вала и диаметр обсадной колонны скважины для работы в которой предназначен насос. (1)
Подача, Q – 30 м\сут.
Напор, H – 1300 м.
Частота вращения вала, n – 3000 об\мин.
Внутренний диаметр корпуса насоса, d – 82 мм.
Внутренний диаметр корпуса ступени, d – 76,5 мм.
После того, как установлен внутренний диаметр ступени, можно приступать непосредственно к расчету проточной части рабочего колеса и других размеров.
Для этого необходимо выполнить следующее:
а) Определить наибольший внешний диаметр рабочего колеса D max
D2max=Dвн.–25, (3.1.)
где, S – радиальный зазор между внутренней стеной корпуса ступени
D вн. и наибольшим диаметром рабочего колеса D max.
Этот зазор выбираем в пределах S=2-3 мм
б) Определим приведенную подачу рассчитываемой ступени:
Qприв.=2800( 90 )3 Q, (3.2)
n D2max
где, 2800 – приведенная скорость вращения единичного насоса в об\мин.
90 – наибольший внешний диаметр рабочего колеса единичного
насоса в мм.
n – число оборотов вала, об\мин.
Q – рассчитываемая подача, л\с.
в) Определяем диаметр втулки при входе в рабочее колесо:
Dвт.=Кdвт*D2max, (3.3)
где, K d вт – коэффициент, соответствующий полученному значению
Q прив, 0,31.
После определения диаметра втулки необходимо проверить возможность размещения вала насоса.
При этом должно быть соблюдено условие:
D = d + 2 δ вт.,
где, D вт – диаметр втулки, мм;
D в – диаметр вала насоса, мм;
δвт. – толщина ступени втулки (для погружных центробежных насосов с диаметром корпуса 92-150, можно принять Sвт=2-4 мм);
г) Определяем наибольший диаметр входных кромок лопастей D1 max по уравнению:
D1max=D2max
KD1max (3.4)
где, КD1 max – коэффициент, определенный для Q прив, 2,3;
в) Определяем диаметр входа D в рабочее колесо:
D0=КD0*D1max, (3.5)
К – коэффициент диаметра входа в рабочее колесо для данного
Qприв, 0,96;
е) Определяем наименьший диаметр входных кромок лопастей рабочего колеса D2 min:
D2min=√D2вн.ст.–1*(D2max)2*Fприв
0,78590 (3.6)
где, Fприв – приведенная площадь без лопаточного кольца между стенкой
корпуса ступени Dвн.ст. и ободом верхнего диска рабочего колеса
D2 min. Находят для Q Fприв = 1600 мм.
ж) Определяем наименьший диаметр входных кромок лопастей D1min:
D1min= D2max
KD1min (3.7.)
где, KDmin – коэффициент определяемый для Qприв.
з) Определяем высоту канала b на выходе из рабочего колеса.
в=Кb2*D2max, (3.8)
где, Кb2 – коэффициент, определяемый для Q, 0,016;
и) Определяем высоту канала b1 на входе в рабочее колесо.
b1=Kb1*D2max, (3.9)
Кb1 – коэффициент, определяемый для Q, 0,036;
к) Напор ступени определяют по коэффициенту окружной скорости
Кv2окр., пользуясь уравнением:
Kv2окр.=V2окр.max (3.10)
60√2gH
где, V2окр. – окружная скорость на диаметре D2max рабочего колеса;
Кv2окр.= πD2ср.*n
60√2gH (3.11)
где, K v2окр. – коэффициент окружной скорости, Кv2окр. = 1,33;
D2ср. – внешний диаметр рабочего колеса, мм;
п – число оборотов вала, об/мин;
g – ускорение свободного падения, м/с;
л) Определяем коэффициент быстроходности ступени;
м) Определяем конструктивные углы β1 и β2 от быстроходности ступени.
Расчет колеса:
а) D2max=Dвн.ст. – 2S
В2max=76,5-2*2
D=72,5 мм;
б)Qприв = 2800 (90 )3 *Q;
n D2max
Qприв = 2800 ( 90 )3 * 0,347;
3000 72,5
Qприв=0,6196 л\с;
в) d вт.=Кdвт*D2max
dвт=0,31*72,5
dвт=22,475 мм;
dвт=dв + 2δвт.
dвт=17+2*2/5
dвт= 22 мм;
г)D1max= D2max
KD1max
D1max=72,5
2,3
D=31,52 мм;
д) D0=К0*D1max;
D0=0,96*31,52;
D0=30,26 мм;
е) D2min=√D2 вн.ст. - 1 (D2max)2 *Fприв.
0,785 90
D2min=√76,52 – 1 (72,5)2 *1600
0,785 90
D2min=67,3 мм;
ж) D1min= D2max
KD1min
D1min= 72,5
2,2
D1min=32,95 мм;
з) b2=Кb2 * D2max;
b2=0,016*72,5
b2=1,16 мм;
и) b1=Кb1*D2max
b1=0,036*7,25=2,61 мм;
к) Н=(πDср.* Н)2 * 1
60*КН2 2g
Н=(3,14*0,0725*3000) * 1
60*1,33 2*9,81
Н=3,73 м;
л) Hs=60;
м) β1=27;
β2=53;
3.1.2. Расчет направляющего аппарата.
Осевой направляющий аппарат ступени погружного центробежного насоса рассчитывают следующим образом:
а) Определяем приведенную подачу и по ней определим приведенную, а затем действительную высоту рассчитываемой ступени:
lприв=22;
l=lприв.*D2max (3.12)
90
б) Определяем высоту междулопаточных каналов:
b3пр.=90*b3 (3.13)
D2max
где, b3пр.- приведенная высота от приведенной подачи, 3.3;
b3пр.= b3прив.* D2max
90
в) Находим диаметр диафрагмы D направляющего аппарата:
F”прив.=0,7859(D2вн.ст.-D2)*(90)2 (3.14)
D2max
где, F”прив-приведенная площадь кольца внутренней стенкой корпуса
ступени и диаметром ступени, 800;
D3=√D2 вн.ст. – F’’прив. * (D2max)2
0,785 90
Расчет направляющего аппарата:
а) l=l прив. * D2max
90
l=22*72,5
90
l=17,7 мм;
б) b3=b3прив.*D2max
90
b3=3,3 * 72,5
90
b3=2,66 мм;
в) D3=√D2 вн.ст. – F’’ (D2max)2
0,785 90
D3=√76,52 – 800 (72,5)2
0,785 90
D3=72,04 мм;
КПД ступени 0,38
3.2.Проверочный расчет шпоночного соединения.
Шпоночное соединение проверяется по боковым граням шпонки под действием окружного усилия, передаваемого рабочему колесу:
σ=2Mр.к.D(h-t)*l (3.15)
где, Мр.к. – момент передаваемый рабочему колесу.
D – диаметр вала;
t - глубина паза по валу;
l - длина посадочной части рабочего колеса;
h – высота шпонки.
Момент, передаваемый рабочему колесу определяется из мощности передаваемой двигателем насосу. Мощность двигателя выбирают по основным параметрам насоса. К основным параметрам относятся подача, напор, КПД. Для определения напора необходимо определить количество ступеней находящихся в насосе. Количество ступеней можно определить следующим образом. Существует 5 видов секций отличающихся длиной, в зависимости от длины в каждой секции располагаются различное число ступеней. Для расчета возьмем следующий насоса: ЭЦН М-5-50-1300 состоящий из 2-х секций № 2 и № 5, в некоторых расположено 264 ступени, в секции № 2 расположено 73 ступени, а в секции № 5 расположено 192 ступени. Длина одной ступени ЭЦН 50 - 24 мм. Ступени насоса в секциях располагаются в пределах:
L=n*l (3.16)
где, n – число ступеней;
l - длина одной ступени;
L = (72*24) + (192*24)
L = 1728 + 4608
L = 6336 мм
Длина одной ступени ЭЦН – 30 равна 17,5 мм, в секциях расположится:
nр=L (3.17)
lp
где, np – число ступеней, рассчитываемого насоса в двух секциях;
lp – длина одной ступени ЭЦН – 30.
np=6336
17,5
np=362 ступени
Значит в секции № 2 расположится 99 ступеней, а в секции № 5 расположится 263 ступени. Напор одной ступени равен 3,73 м. Общий напор равен произведению количества ступеней на напор одной ступени:
H=N*h (3.18)
где, h-напор одной ступени
H=362*3,73
H=1350,26 м
H=1350 м.
Гидравлическая мощность насоса равна:
Nг=Q*H*j (3.19)
102 *η
где, Q – подача насосной установки;
H – напор насоса
j-относительный удельный вес жидкости
η-КПД насоса;
Q = 30 м3 /сут =3,5*10-4 м3 /с
Н = 1350 м
j=1900 кг/м3
η=0,43
Nг=3,5*10-4 *1350*1300
102*0,43
Nг =15 КВт
Мощность двигателя должна быть:
Nд ≥ 1,05 Nг, (3.20)
где Nд – мощность двигателя;
Nг – гидравлическая мощность насоса;
Nд = 1,05*15
Nд=15,8 КВт
По (1) подбираем двигатель, соответствующий условию отраженному в формуле (3.20):
Двигатель ЭД 20-103
Мощность двигателя Nд=20 КВт.
Момент, передаваемый на рабочее колесо:
Мр.к.=Nдв. (3.21)
Nz*n
где, Nдв. – мощность подобранного двигателя;
Nz – число рабочих колес, установленных в насосе;
n – число оборотов вала насоса;
Nz =362 ступени
n=2840 об/мин=47,33 об/сек
Мр.к. = 20*103
362*47,33
Мр.к.=1,17 Вт.
Расчет шпонки на смятие производится по формуле (3.15):
σсм.= 2Мр.к.
D (h-t)*l
Мр.к.=1,17 Вт.
D=17мм=0,017 м
l=10мм=0,01 м
h=1,6мм=0,0016 м
t=0,8мм=0,0008 м
σсм= 2*1,17
0,017(0,0016-0,0008)*0,01
σсм.=17205881 Н/м2
σсм.=17,2 Мпа
Шпонка представляет собой кружок твердый, вытянутый, изготовленный из латуни марки П63. Сопротивление латуни этой марки разрыву:
σв=75-95 кгс/мм2
σв=750-950 МПа
Сопротивление смятию находится в пределах ½ σв, запас прочности на смятие нас удовлетворяет.
3.3.Проверочный расчет шлицевого соединения.
Шлицевое соединение проверяется на смятие по формуле:
σсм.=Т (3.22)
0,75z Асм*Rср.
где, Т – передаваемый вращаемый момент;
z - число шлицев;
Ам – расчетная поверхность смятия;
Rср. – средний радиус шлицевого соединения.
Средний радиус шлицевого соединения определяется как:
Rср.=0,25 (D+d) (3.23)
где, d-диаметр впадин шлицев, ;
D-максимальный диаметр шлицев;
D=0,017 м
d=0,0137 м
Rср.=0,25 (0,017+0,137)
Rср.=0,007675 м
Расчетная поверхность смятия равна:
Асм.=(D-d-2ƒ)*l (3.24)
2
где, ƒ-фаска на шлицах;
l-длина контактирующей поверхности шлицевого соединения;
ƒ=0,003 м
l=0,04 м
Асм.= (0,017-0,0137 – 2*0,0003)*0,04
2
Асм.=0,000042 м2
Т=Nдв (3.25)
n
где, Nдв.- мощность двигателя;
n - число оборотов вала;
Nдв.=20 КВт=20000Вт
n=2840 об/мин=47,33 об/сек
Т=20000
47,33
Т=422,6 Н*м
σсм.= 422,6
0,75*6*0,000042**0,007675
σсм=291308000 Н/м
σсм=291,308 Мпа.
Вал насоса изготовлен из высоколегированной стали.
[σсм]вала=500-1100 МПа.
Следовательно, шлицевое соединение, рассчитанное нами и проверенное на смятие удовлетворяет нашему насосу.
3.4.Расчет вала ЭЦН
Различают валы прямые, коленчатые и гибкие. Наибольшее распространение имеют прямые валы. Коленчатые валы применяют в поршневых машинах. Гибкие валы допускают передачу вращения при больших перегибах. По конструкции различают валы и оси гладкие, фанонные или ступенчатые, а так же сплошные и полые. Образование ступеней на валу связано с закреплением деталей или самого вала в осевом направлении, а также с возможностью монтажа детали при подсадках с натягом. Полые валы изготавливают для уменьшения массы или в тех случаях, когда через вал пропускают другую деталь, подводят масло и пр. Прямые валы изготавливают преимущественно из углеродных и легированных сталей.
Валы рассчитывают на прочность.
Расчет вала на прочность.
Во время работы вал насоса подвергается воздействию крутящего момента, осевой сжимающей нагрузки на верхний торец вала и радиальной нагрузки. Радиальная нагрузка на вал вызывается насосным расположением валов секций насоса и протектора и возможность неточного изготовления шлицевого соединения.
Предварительно оценивают средний диаметр вала по внутреннему диаметру шлицев d концентрационных напряжений и изгиба вала:
τкр=Mкр.max=Mкр.max (3.26)
Wр=0,2*d3 вн.
где, dвн.=Мкр.max (3.27)
0,2*τкр
Максимальный крутящий момент:
Мкрmax=Nmax (3.28)
w
где, N max– приводная мощность двигателя, 13 т;
w= π*n - угловая скорость, сек;
30
п-частота вращения электродвигателя, об/мин.
Напряжение на кручение определяем по пределу текучести материала σт.
Допустимое касательное напряжение при кручении принимаем с коэффициентом запаса прочности η=1,5;
τ=[τ]= τт = σт (3.18)
η 2η
Для вала насоса ЭЦН берем сталь 40ХН с пределом текучести τ=750 Мпа.
Насосное соединение валов и некомпенсированные зазоры создают радиальную нагрузку в 60-130 кг.с, действующую на шлицевой конец вала насоса.
Радиальная нагрузка Р, находится по формуле:
Р1=K[3E*J*∆у] (3.29)
C3
где, К – коэффициент, учитывающий компенсирующее влияние зазоров
и равный 0,45-0,85;
Е – модуль упругости материала вала, Па.
J – момент инерции вала, принимаемый с учетом тела втулки. М;
∆у – стрела прогиба шлицевого конца вала, вызванная неспособнос-
тью в сочленении насоса и протектора, принимается равным 25*10 м;
С – расстояние от центра подшипника до середины муфты, м;
Момент инерции вала:
J=π*d4вн.*а*(D-dвн.)*(D+dвн.)*z (3.30)
64
где, а – ширина шлицы, м;
D – наружный диаметр шлицев, м;
z – число шлицев.
Радиальная нагрузка на вал Р2, зависящая от неравномерной передачи крутящего момента шлицами малы и ею можно пренебречь.
Пять работающих шлицев дают нагрузку, равную 0,2*Р, где
Рокр.=2*Мкр.max (3.31)
dср.
где, D – средний диаметр шлицев.
Р2=0,2*Рокр. (3.32)
Изгибающий момент на шлицевом конце вала:
Мизгб.max=(Р1+Р2)*b (3.33)
где, b-расстояние от середины муфты или от точки приложения силы Р
до проточки под стопорное кольцо, м.
Мизг.max.=(Р1-Р2)*b.
Зная момент изгиба и момент кручения, можно определить напряжение изгиба и кручения в опасном сечении вала (под проточку на стопорное кольцо).
σизг.max=Мизг.max (3.34)
Wx
Wх=π*d4кр. (3.35)
32*D
где, Wх- момент сопротивления в месте проточки под стопорное кольцо,
м;
dкр.-диаметр вала в месте проточки под стопорное кольцо, м;
σизгб.min=Мизг.min (3.36)
Wx
Напряжение кручения
τкр.=Мкр.max (3.37)
Wp
Wр=2*Wx – полярный момент сопротивления вала в месте проточки под стопорное кольцо;
Эквивалентное напряжение находим по четвертной прочности:
σэкв.=√σ2изг.max+3τ2 (3.38)
По этой величине и пределу текучести материала вала устанавливается запас прочности с учетом статистических нагрузок:
п=σт≥1,3 (3.39)
σэкв
Исходные данные:
Приводная мощность двигателя N = 2000Вт. Частота оборотов двигателя п=2840 об/мин. Предел текучести материала вала σ=750 МПа. Модуль упругости материала вала У=20*10 МПа. По данной методике произведем расчет с цифровыми значениями:
Момент инерции вала:
J= π*d4вн.+ а (D-dвн) * (D +dвн)2*z
64
J= 3,14*0,0124 + 0,0035 (0,017 – 0,012)*(0,017+0,012) 2*6
64
J=2,3*10-10 м;
Нагрузка создаваемая работающими шлицами:
Р2=0,2*Рокр.
Р2=0,2* Mкр.max
dср
Р2=0,2 * 2*67,28
0,0155
Р2= 1736,2584.
Максимальный изгибающий момент в месте проточки под стопорное кольцо:
Мизг.max= (Р1+Р2)*b
Мизг.max=(258,957+1736,258)*0,035
Мизг.max=69,83 Н*м.
Минимальный изгибающий момент в этом сечении:
Мизг.min=(Р1-Р2)*b
Мизг.min=(258,957-1736,258)*0,035
Мизг.min=51,74 Н*м;
Напряжение изгиба в опасном сечении:
σизг.max=Мизг.max
Wx
где, W= π*d4кр
32*D
W=3,14*0,01574
32*0,017
W=3,51*10-7 м3;
Это мы нашли осевой момент сопротивления вала:
σизг.max.= 69,83
3,51*10-7
σизг.max =198,945Мпа
Минимальное напряжение изгиба
σизг.min.= 51,71
3,51*10-7
σизг.min.= 147,321 МПа
Напряжение кручения:
τкр=Мкр.max
Wp
где, Wр=2*Wх
Wр=2*3,51*10-7
Wр=7,02*10-7 м
Это мы нашли полярный момент сопротивления вала
τкр.= 67,28
7,02*10-7
τкр.=96,114 Мпа;
Эквивалентное напряжение:
σэкв=√σ2 изг.max + τкр2
σэкв=√198,9452+3*96,1142
σэкв.=259,409 Мпа;
Запас прочности по пределу текучести:
п= σт ≥ 1,3
σэкв
п= 750
259,409
п=2,8;
Из результатов расчетов видно, что вал из стали 40 ХН диаметром 17 мм со шлицем и с проточкой под стопорное кольцо выдерживает заданные нагрузки с коэффициентом запаса прочности п=2,8, который удовлетворяет условию 2,8>[1,4].
3.5.Прочностной расчет
3.5.1.Прочностной расчет корпуса насоса
Корпусы погружных центробежных насосов изготавливают из трубных заготовок точением или из холодных комбинированных труб повышенной точности длиной 2100, 3600 и 5000 мм.
Корпус насоса будет рассчитываться в следующей последовательности.
1.Выбираем наружный диаметр и внутренний корпуса насоса.
Dвн.=0,092 м, Dвн=0,08 м
2.Определяем предварительную затяжку пакета ступеней с учетом коэффициента запаса плотности верхнего стыка по формуле:
T=πКρgНrвн.[1-Eк-Fк/2 (ЕкFк+Ена Fна)] (3.40)
где К – коэффициент запаса плотности стыка;
К=1,4
ρ - плотность воды;
ρ=1000м/кг
g – ускорение свободного падения;
g = 9,8 м/с
H- максимальный напор насоса;
Н =1300 м
r - внутренний радиус расточки корпуса насоса;
r=0,04 м
Ек- модуль упругости материала корпуса насоса;
Ек=0,1х10 6Мпа
Fк – площадь поперечного сечения корпуса насоса;
Fк=1,62х10 -3 м 2
Ена- модуль упругости материала направляющего аппарата;
Ена=1,45х10 5МПа
Fна – площадь поперечного сечения направляяющего аппарата;
Fна=6,08х10-4 м2
Т=3,14х1,4х1000х9,81х1160х0,042 [1-2,1х106 х1,62[10-3 /2(2,1х106 х1,62х10-3 +1,45х105 х6,08х10-4 ) ]=48256Н
3.Находим общее усилие, действующее вдоль оси корпуса по выражению:
Q=Т+ρgНrвн 2 EкFк/2(ЕкFк+ЕнаFна)+G + πКρgНrвн (3.41)
где Т – предварительная затяжка пакета ступеней, определенная по формуле
(3.40)
Т=48256Н
G – масса погружного агрегата;
G =20505 Н;
Hmax - максимальный напор насоса;
Нmax =3500 м
Q = 268519Н
4.Вычисляем осевое напряжение в опасных сечениях корпуса по формуле
σ=Q/Fк (3.42)
где Q – общее усилие, действующее вдоль корпуса насоса, определенное по
выражению (3.41)
Q=268591 Н
Fк – площадь ослабленного сечения корпуса по наружному диаметру
трубы;
Fк =1,24х10-3 м2
σz=268519/1,24х10-3=220МПа
5.Определяем тангенциальное напряжение в опасных сечения, по выражению:
σ=pgHmaxrвн/S-MT/F’ (3.43)
где S – толщина корпуса в опасном сечении;
S=0,009 м
M – коэффициент Пуассона;
M=0,28
σт=142 МПа
3.5.2.Прочностной расчет винтов страховочной муфты.
Расчет винтов на срез произведем по формуле:
τ≤[τ] (3.44)
где τ – напряжение среза действующее на винты страховочной муфты;
[τ] – допускаемое напряжение среза.
Допускаемое напряжение среза определяется по формуле:
[τ]=0,4σт
где σт – предел текучести материала винта, для стали 35 из которой
изготовлены винты
σт=360МПА.
[τ]=0,4х360=144МПа
Напряжение среза действующее на винты определяем по формуле
τ=4S/пdхz (3.45)
где S – сила среза действующая на винты;
d – внутренний диаметр резьбы;
d=0,0085 м;
z –количество винтов, z=2;
Находим силу среза по выражению
S=mхg (3.46)
где m – масса насосного агрегата
m=709 кг
g – ускорение свободного падения;
g =9,8 м/с
S=709х9,81=6955,29 кгм/с2 =6955,29 Н
Определяем напряжение среза, действующее на винты страховочной муфты по формуле (3.45)
τ=6955,29х4/3,14х0,00855 х2=61285468 Па=61,29 МПа.
Прочностной рачсет винтов на срез является допустимой, так как 61,29<144
Коэффициент запаса прочности винтов определяем из выражения
n=[τ]/ τ (3.47)
где [τ] – допускаемое напряжение среза, [τ]=144 МПА
τ – напряжение среза действующее на винты страховочной муфьы,
τ=61,29 МПа
П=144/61,29=2,35
Полученный коэффициент заппса прочности является достаточным.
3.5.3.Прочностной расчет корпуса полумуфты
Расчет корпуса полумуфты будет рассчитываться на растяжение в опасном сечении. Расчет полумуфты в опасном сечении произведем по формуле:
σ≤[σ] (3.48)
где σ – сопротивление при растяжении действующее в опасном сечении
полумуфты;
[σ] – допустимое сопротивление при растяжении.
Допустимое сопротивление при растяжении определяется из выражения
σ=0,3σт (3.49)
где σт – предел текучести материала для материала сталь 30 Л, из которого отлита полумуфта σт=240 МПа
[σ]=0.3х240=72 МПа
Определяем напряжение, получамемое давлением максимальной нагрузки на площадь по формуле:
σ=S/F (3.50)
где S – максимальная нагрузка действующая на полумуфту, определенная
по формуле (3.46)
S=6955,29Н
F – площадь полумуфты в опасном сечении;
F=5,68х10-4 м 2
σ=6955,29/5,68х10-4=12245228Па=12,25МПА
Прочность полумуфты в опасном сечении является допустимой, так как 12,25 МПа<72 Мпа
Коэффициент запаса прочности определяем из выражения
П= [σ] /σ (3.51)
где [σ] – допускаемое сопротивление при растяжении;
[σ]=72 МПА
σ- сопротивление при растяжении действующее в опасном сечении
муфты;
σ=12,25 МПА
П=72/12,25=5,87
Полученный коэффициент запаса прочности является допустимым.
4. ЭКОНОМИЧЕСКИЙ ЭФФЕКТ
На месторождениях, разрабатываемых и эксплуатируемых НГДУ “Сургутнефтегаз” дебет скважин по сравнению с прошлыми годами падает, что дает основанием использовать на скважинах электроцентробежные насосы с меньшей подачей.
При эксплуатации скважин УЭЦН М-30-1300 повышается межремонтный период и наработка на отказ.
Совершенствование электроцентробежного насоса с подачей 50 м/сут состоит в том, что в корпус электроцентробежного насоса с подачей на 50 м/сут мы ставим рабочие колеса и направляющие аппараты, рассчитанные на подачу 30 м/сут. Этим мы получаем насос с подачей 30 м/сутки для использования на малодебетных скважинах. За счет этого мы получаем экономию денежных средств, так, как не приходится запускать с заводов электроцентробежные насосы для малодебетных скважин.
Экономический эффект ожидается за счет:
-увеличение наработки на отказ;
-уменьшение числа текущих ремонтов;
-предотвращение затрат, связанных с закупкой УЭЦН-30 на заводах.
Методика расчета экономического эффекта
Экономический эффект определяется по формуле
Эт=Рг-Зг (4.1.)
Кр+Ен
где, Рг – стоимостная оценка годовых результатов
Зг – неизменные по годам годовые затраты;
Кр – норма амортизации с учетом фактора времени
Ен – норматив для приведения к расчетному году
Стоимостная оценка годовых результатов:
от количества ремонтов
Рг1=(365 – 365 ) *Срем. (4.2.)
МРПб МРПсов.
где, МРПб – базовый межремонтный период;
МРПсов.–межремонтный период усовершенствованного
оборудования
Срем. – стоимость текущего ремонта
Неизменные по годам годовые затраты:
Зг=Иг+(Кр+Ен)*К (4.3)
где, Иг – годовые текущие затраты
К – капитальные затраты
Годовые текущие затраты:
К1=1,2 ( Зср. *L + 0,395 * Зср. * L) (4.4)
166 166
где, К1 – капитальные затраты, связанные с изготовлением рабочей
ступени;
Зср – средняя затрата
L – длительность изготовления
Капитальные затраты на материалы, примененные при изготовлении рабочей ступени:
К2=m*c*Kи (4.5)
где, m – масса материалов;
c – стоимость материалов;
Ки- коэффициент, учитывающий, что часть материалов расходуется
при изготовлении.
К=К1+К2 (4.6)
К=n*(К1+К2) (4.7)
где, -n - количество рабочих ступеней.
Годовая прибыль, остающаяся в распоряжении предприятия:
Пt=Bt – Ct – Ht (4.8)
где, Bt – выручка от реализации продукции, полученной с применением
мероприятий НТП, без акцизов и налогов на добавочную стоимость;
Ct – себестоимость продукции;
Ht – налоги, общая сумма.
Срок возврата затрат:
Т= К (4.9)
П+А
где, П – прибыль чистая, получаемая за счет реализации мероприятия за
год;
А – сумма амортизации за год.
Исходные данные:
Стоимость ЭЦН – 50-1300 – 1320400 руб
Стоимость ЭЦН - 30-1300 – 18900000 руб
m1 – масса рабочего колеса, изготовляемого из полиамида.
m1=0,158 г
С – стоимость полиамида
С=1500000 руб за тонну
m2 – масса направляющего аппарата, изготовляемого из полиамида.
m2=320 г.
Средняя заработная плата:
Зср.=1800 руб
Длительность изготовления рабочей ступени
L=1 час
Межремонтный период базовый:
МРПб=316 суток
Межремонтный период совершенствованного оборудования:
МРПсов.=358 суток
Стоимость текущего ремонта (одного):
Т = 72 часа
Среднесуточный дебит :
Q=35 м/сут
Стоимость нефти на внутреннем рынке:
С = 500000 резв./тонну
Себестоимость нефти:
Ct=287274 руб/т
Расчет экономического эффекта
Стоимостная оценка годовых результатов:
от количества ремонтов:
Рг1= ( 365 – 365 ) *Срем.
МРПб МРПсов.
МРПб=316 суток
МРПсов.=358 суток
Ср=1150000 резб.
Рг1= (365 – 365) *1150000
358
Рг1=156400 руб
Рг2 берем из 40% от стоимости ЭЦН – 50-1300 и стоимости ЭЦн – 30-1300.
Рг2=0,4*13204000+18900000=2418600 руб
Рг=Рг1+Рг2
Рг=156400+24181600=24338000 руб
Расчет затрат:
Зг=Иг + (Кр+Ен)*К
Иг=ΔР*Т*Q*Сп
Сп3=55% от себестоимости 287274 руб/т
Иг=0,136*3,0830,0*0,55*287274
Иг=1933928,5 руб
Затраты на изготовление рабочей ступени
К1=1,2 *(1,395 * Зср. *L)
166
Зср.=1800000 руб
L=1 час
К1=1,2 * 1,395 * 1800000*1
166
К1=18151,719 руб
Затраты на материалы, примененные при изготовлении рабочей ступени:
К2=m*С*Ки
m=m1+m2
m=0,320+0,158
m=0,478
К2=0,478*10-3 *1500000*1,5=1075,5 руб
К=112*19227,219
К=2153449 руб
Зг=Иг + (Кр+Ен)*К
Зг=1933928,5 + (1+0,1)*2153449
Зг=4292722,4 руб.
Эффект рассчитывается для срока в 5 лет, срока амортизации оборудования типа УЭЦН
Кр=0,1638
Ен=0,1
Эт=24338000 - 4292722,4
0,1638 + 0,1
Эт=7598647 руб
Прибыль, остающаяся в распоряжении предприятия:
Пt=Bt – Ct – Ht
Формула (4.8) общая для расчета, ее можно разложить:
Пт=Рг2Иг (4.10)
где, Пт – прибыль без налогов
Текущая чистая прибыль:
Пч=0,65 * Пт
Рг2=24181600 руб
Иг=1933928,5 руб
Пt=24181600 – 1933928,5
Пt=22247671 руб
Пч=0,65* Пт
Пч=0,65 * 22247671
Пч=14460986 руб.
Срок возврата затрат
Т = К
П+А
К=2153449 руб
Пч=14460986 руб
А=20% от К
А=430689,8 руб
Т= 2153449
14460986+430689,8
Т = 2153449
14891675
Т=0,15 года
Т=1,8 месяца
Сводная таблица экономических показателей
Таблица 4.1.
Показатели
Значение
Капитальные затраты, руб
2153449
Текущие годовые затраты, руб
1933928,5
Межремонтный период до совершенствования, сутки
316
Межремонтный период после усовершенствования, сутки
358
Экономический эффект, руб
75986647
Чистая прибыль, руб
14460986
Срок окупаемости, год
0,15
4. ЭКОНОМИЧЕСКИЙ ЭФФЕКТ ОТ УСОВЕРШЕНСТВОВАНИЯ КОНСТРУКЦИИ ЭЦН
На месторождениях, разрабатываемых и эксплуатируемых НГДУ «Лянторнефть» дебет скважин по сравнению с прошлыми годами падает, что дает основанием использовать на скважинах электроцентробежные насосы с меньшей подачей.
При эксплуатации скважин УЭЦН М-30-1300 повышается межремонтный период и наработка на отказ.
Переводим подачу на 30 м/сут. Этим мы получаем насос с подачей 30 м/сутки для использования на малодебетных скважинах. За счет этого мы получаем экономию денежных средств, так, как не приходится запускать с заводов электроцентробежные насосы для малодебетных скважин.
Экономический эффект ожидается за счет:
-увеличение наработки на отказ;
-уменьшение числа текущих ремонтов;
-предотвращение затрат, связанных с закупкой УЭЦН-30 на заводах.
Методика расчета экономического эффекта
Экономический эффект определяется по формуле
Эт=Рг-Зг (4.1.)
Кр+Ен
где, Рг – стоимостная оценка годовых результатов
Зг – неизменные по годам годовые затраты;
Кр – норма амортизации с учетом фактора времени
Ен – норматив для приведения к расчетному году
Стоимостная оценка годовых результатов:
от количества ремонтов
Рг1=(365 – 365 ) *Срем. (4.2.)
МРПб МРПсов.
где, МРПб – базовый межремонтный период;
МРПсов.–межремонтный период усовершенствованного
оборудования
Срем. – стоимость текущего ремонта
Неизменные по годам годовые затраты:
Зг=Иг+(Кр+Ен)*К (4.3)
где, Иг – годовые текущие затраты
К – капитальные затраты
Годовые текущие затраты:
К1=1,2 ( Зср. *L + 0,395 * Зср. * L) (4.4)
166 166
где, К1 – капитальные затраты, связанные с изготовлением рабочей
ступени;
Зср – средняя затрата
L – длительность изготовления
Капитальные затраты на материалы, примененные при изготовлении рабочей ступени:
К2=m*c*Kи (4.5)
где, m – масса материалов;
c – стоимость материалов;
Ки- коэффициент, учитывающий, что часть материалов расходуется
при изготовлении.
К=К1+К2 (4.6)
К=n*(К1+К2) (4.7)
где, -n - количество рабочих ступеней.
Годовая прибыль, остающаяся в распоряжении предприятия:
Пt=Bt – Ct – Ht (4.8)
где, Bt – выручка от реализации продукции, полученной с применением
мероприятий НТП, без акцизов и налогов на добавочную стоимость;
Ct – себестоимость продукции;
Ht – налоги, общая сумма.
Срок возврата затрат:
Т= К (4.9)
П+А
где, П – прибыль чистая, получаемая за счет реализации мероприятия за
год;
А – сумма амортизации за год.
Исходные данные:
Стоимость ЭЦН – 50-1300 – 1320400 руб
Стоимость ЭЦН - 30-1300 – 18900000 руб
m1 – масса рабочего колеса, изготовляемого из полиамида.
m1=0,158 г
С – стоимость полиамида
С=1500000 руб за тонну
m2 – масса направляющего аппарата, изготовляемого из полиамида.
m2=320 г.
Средняя заработная плата:
Зср.=1800 руб
Длительность изготовления рабочей ступени
L=1 час
Межремонтный период базовый:
МРПб=316 суток
Межремонтный период совершенствованного оборудования:
МРПсов.=358 суток
Стоимость текущего ремонта (одного):
Т = 72 часа
Среднесуточный дебит :
Q=35 м/сут
Стоимость нефти на внутреннем рынке:
С = 500000 резв./тонну
Себестоимость нефти:
Ct=287274 руб/т
Расчет экономического эффекта
Стоимостная оценка годовых результатов:
от количества ремонтов:
Рг1= ( 365 – 365 ) *Срем.
МРПб МРПсов.
МРПб=316 суток
МРПсов.=358 суток
Ср=1150000 резб.
Рг1= (365 – 365) *1150000
358
Рг1=156400 руб
Рг2 берем из 40% от стоимости ЭЦН – 50-1300 и стоимости ЭЦн – 30-1300.
Рг2=0,4*13204000+18900000=2418600 руб
Рг=Рг1+Рг2
Рг=156400+24181600=24338000 руб
Расчет затрат:
Зг=Иг + (Кр+Ен)*К
Иг=ΔР*Т*Q*Сп
Сп3=55% от себестоимости 287274 руб/т
Иг=0,136*3,0830,0*0,55*287274
Иг=1933928,5 руб
Затраты на изготовление рабочей ступени
К1=1,2 *(1,395 * Зср. *L)
166
Зср.=1800000 руб
L=1 час
К1=1,2 * 1,395 * 1800000*1
166
К1=18151,719 руб
Затраты на материалы, примененные при изготовлении рабочей ступени:
К2=m*С*Ки
m=m1+m2
m=0,320+0,158
m=0,478
К2=0,478*10-3 *1500000*1,5=1075,5 руб
К=112*19227,219
К=2153449 руб
Зг=Иг + (Кр+Ен)*К
Зг=1933928,5 + (1+0,1)*2153449
Зг=4292722,4 руб.
Эффект рассчитывается для срока в 5 лет, срока амортизации оборудования типа УЭЦН
Кр=0,1638
Ен=0,1
Эт=24338000 - 4292722,4
0,1638 + 0,1
Эт=7598647 руб
Прибыль, остающаяся в распоряжении предприятия:
Пt=Bt – Ct – Ht
Формула (4.8) общая для расчета, ее можно разложить:
Пт=Рг2Иг (4.10)
где, Пт – прибыль без налогов
Текущая чистая прибыль:
Пч=0,65 * Пт
Рг2=24181600 руб
Иг=1933928,5 руб
Пt=24181600 – 1933928,5
Пt=22247671 руб
Пч=0,65* Пт
Пч=0,65 * 22247671
Пч=14460986 руб.
Срок возврата затрат
Т = К
П+А
К=2153449 руб
Пч=14460986 руб
А=20% от К
А=430689,8 руб
Т= 2153449
14460986+430689,8
Т = 2153449
14891675
Т=0,15 года
Т=1,8 месяца
Сводная таблица экономических показателей
Таблица 4.1.
Показатели
Значение
Капитальные затраты, руб
2153449
Текущие годовые затраты, руб
1933928,5
Межремонтный период до совершенствования, сутки
316
Межремонтный период после усовершенствования, сутки
358
Экономический эффект, руб
75986647
Чистая прибыль, руб
14460986
Срок окупаемости, год
0,15
5. БЕЗОПАСНОСТЬ и ЭКОЛОГИЧНОСТЬ ПРОЕКТА
Введение.
Основными законодательными актами по охране труда в нашей стране являются Конституция России, Основы законодательства и др. в этих документах отражены правовые вопросы охраны труда и здоровья трудящихся. На основании вышеперечисленных источников, а также исходя из соответствующих правил безопасности и норм производственной санитарии в данном проекте нами разрабатываются основные мероприятия по созданию безопасных условий работы операторов при обслуживании скважин, оборудованных УЭЦН.
Всякая деятельность протекает из определенных мотивов и направлена на достижение конкретных целей. Жизнедеятельность – активное отношение человека к окружающему миру для целесообразного его преобразования. Абсолютно безопасной деятельности не существует. По данным Госкомстата, по различным причинам в Российской Федерации на производстве ежегодно травмируется 650-700 тысяч человек, 15-16 тысяч человек с летальным исходом, 6 млн. человек работают во вредных условиях, более 700 тысяч единиц оборудования и 61 тысяча зданий и сооружений не отвечает требованиям безопасности. В среднем, ежегодно происходит около 500 тысяч пожаров, основными причинами этих негативных явлений являются:
недостаточный уровень обучения и квалификации персонала;
несоответствие технологических процессов современным требованиям безопасности;
недостаточное оснащение производства системами очистки выбросов;
устаревшее оборудование;
В данном случае, описывается несколько мероприятий по улучшению охраны и условий труда, охраны окружающей среды, предложены возможные чрезвычайные ситуации и их предотвращение.
5.1. Анализ и оценка опасностей при выполнении работ,
связанных с обслуживанием скважин, оборудованных УЭЦН.
Одна из главных особенностей условий труда операторов по добыче нефти – это работа, в основном, на открытом воздухе (на кустах скважин), а также работа связанная с перемещениями на территории объекта и между объектами (кустами), частыми подъемами на специальные площадки, находящиеся на высоте. Поэтому в условиях сурового климата Западной Сибири и Крайнего Севера с низкими температурами (зимой до –500С) и высокой влажностью (летом до 100%) играет метеорологические факторы. При низкой (сверхдопустимых норм) температуре окружающей среды тепловой баланс нарушается, что вызывает переохлаждение организма, ведущее к заболеванию. В случае низкой температуры воздушной среды уменьшается подвижность конечностей в следствии интенсивной теплоотдачи организм, что сковывает движения. Это может послужить причиной несчастных случаев и аварий.
При длительном пребывании работающего в условиях низкой температуры и, следовательно, переохлаждении организма возможно возникновение различных острых и хронических заболеваний: воспаление верхних дыхательных путей, ревматизм и другие. Результатами многократного воздействия низких температур являются пояснично-крестцовый радикулит и хроническое повреждение холодом (ознобление).
При высокой температуре снижаются внимание и скорость реакции работающего, что может послужить причиной несчастного случая и аварии. При работе в летнее время при высокой температуре (до +50 С) возможны перегревания организма, солнечные и тепловые удары.
Кусты, как правило, засыпаются песком, поэтому при сильных ветрах случается поднятие частиц песка и пыли, которые могут попасть в глаза и верхние дыхательные пути. Нормирование метеорологических параметров устанавливает ГОСТ 12.1.005-76.
В ходе производственных операций рабочие могут подвергаться вредных газов и паров нефти, источником которых являются нарушения герметичности фланцевых соединений, механической прочности фонтанной арматуры (свище, щели по шву) вследствие внутренней коррозии или износа, превышения максимально допустимого давления, отказы или выходы из строя регулирующих и предохранительных клапанов. Пары нефти и газа при определенном содержании их в воздухе могут вызвать отравления и заболевания. При постоянном вдыхании нефтяного газа и паров нефти поражается центральная нервная система, снижается артериальное давление, становится реже пульс и дыхание, понижается температура тела. Особенно опасен сероводород – сильный яд, действующий на нервную систему. Он нарушает доставку тканям кислорода, раздражающе действует на слизистую оболочку глаз и дыхательных путей,
вызывает острые и хронические заболевания, ПДК Н2S – 0,1 мг/м3 (ГОСТ 12.1.005-76.)
Специфическая особенность условий эксплуатации нефтяных скважин – высокое давление на устье, которое доходит до 30 МПа. В связи с этим любое ошибочное действие оператора при выполнении работ на устье скважины может привести к опасной аварии.
Высокое давление и загазованность указывают на повышенную пожаро-и взрывоопасность объекта.
Эксплуатация скважин с УЭЦН характеризуется с наличием высокого напряжения в силовом кабеле. Причем станция управления и скважина оборудования ЭЦН обычно не находятся в непосредственной близости друг от друга и часть кабеля проходит по поверхности, что увеличивает зону поражения электротоком, а следовательно и вероятность несчастного случая.
Причиной несчастного случая может быть также неудовлетворительное состояние объекта с позиции санитарии, его чрезмерная захламленность и замазученность, плохая подготовка скважин к замерам пластового давления.
Таким образом, мы выяснили основные факторы производственной среды, влияющие на здоровье и работоспособность операторов в процессе труда:
метеорологический фактор.
Вредное влияние паров нефти и газа.
Высокое давление.
Повышенная пожаро-и взрывоопасность.
Наличие высокого напряжения.
Причины организационного характера.
5.2. Расчет заземления электрооборудования.
Для предохранения рабочих от поражения электрическим током электрооборудование УЭЦН должно быть надежно заземлено. В соответствии с ГОСТом 12.1.006-84 выполнен расчет заземляющего устройства станции управления ЭЦН.
Заземление КТПН осуществляется электродами из круглой стали d=12 мм, l=5 м, забиваемых в землю на глубину 5,7 м и соединенных стальной полосой 40х4 мм. Сопротивление заземляющего устройства должно быть не более 4 Ом в любое время года. все соединения выполняются сваркой согласно ПЭУ. После устройства контура заземления необходимо замерить сопротивление и, если оно окажется больше допустимого, забить дополнительные электроды.
Расчет производится в соответствии «Типовых расчетов по электрооборудованию».
Сопротивление растеканию тока одиночных стержневых заземлителей определяется по формуле:
Rо.с.=ρ*Кс (ln 2l + 1 ln 4t+l (5.1.)
2πl d 2 4t-l
где ρ – удельное сопротивление грунта, 1*10-4ом*см;
Кс-коэффициент сезонности, для I климатической зоны Кс =1,65;
l – длина стержня, 500 см;
d - диаметр стержня, 1,2 см;
t – глубина залегания, 570 см;
Rс=1*104*1,65 (ln 2*500 +1/2 ln 4*570 +500) = 37,5 Ом
2*3,148500 1,2 4*570-500
Необходимое количество стержней:
n=
ηсR3 (5.2.)
где, η – коэффициент использования стержневых заземлителей, 0,61;
R3- сопротивление, оказываемое заземляющим устройством расте-
канию тока, 4 Ом;
=16 n=
0,61*4
Сопротивление всех стержней:
Rс=Rо.с./n* ηc=37,5/16*0,61=3,8 Ом
Сопротивление растекания горизонтального (протяжного) заземлителя определяется по формуле:
Rn= 0,366 * ρрасч./ln * lg lg2/dt1 (5.3.)
где, ln – общая длина горизонтального заземлителя (полосы 40х4 мм),
100000 см;
ρрасч = ρ* Кс=104*5 ом*см, Кс=5 - для I климатической зоны;
t1 – глубина залегания протяжного заземлителя;, 70 см;
Rn= 0,366* 5*10-4/100000 * 1000002/1,2*70=14.3 Ом.
Действительное сопротивление растеканию протяжного заземлителя с учетом коэффициента использования ηn=0,32
Rnд=Rn/ ηn=14,3/0,32=44,7 Ом (5.4.)
Общее сопротивление заземляющего устройства:
R32=Rc*Rпд/ Rc+Rпд= 3.8* 44,7/3,8+44,7=3,5 Ом (5.5.)
Из расчета следует, что полученное значение сопротивления не превышает допустимого, а следовательно будет обеспечено полноценное заземление объекта, соответствующее ГОСТу 12.1.006-84.
5.3. Основные мероприятия по обеспечению безопасности
условий труда операторов.
Основное условие безопасности при обслуживании нефтяных скважин – соблюдение трудовой и производственной дисциплины всеми работающими на них.
Все работы связанные с эксплуатацией УЭЦН (обслуживание, перевозка, монтаж, демонтаж) должны выполняться в соответствии с правилами безопасности и инструкциям по охране труда для рабочих цехов добычи нефти и ППД, а также следующими документами:
Правило безопасности в нефтяной и газовой промышленности, утверждение Госгортехнадзором.
Правила технической эксплуатации электроустановок, утвержденные Госэнергонадзором.
Правила техники безопасности при эксплуатации электроустановок, утвержденные Госэнергодзором.
Правила устройства электроустановок, утвержденные Госэнергонадзором.
Руководство по эксплуатации УЭЦН РЭ, утвержденное ОКБ БН.
На работу следует принимать лиц не моложе 18 лет, годных по состоянию здоровья, соответственным образом обученных и прошедших инструктаж по технике безопасности.
Перевозка рабочих на место и обратно должна осуществляться на бортовых автобусах или специально оборудованных грузовых бортовых автомобилях, а в труднодоступных местностях – на вездеходах. Продолжительность рабочего времени установлена трудовым законодательством и не должна превышать 41 час в неделю.
Рабочие должны обеспечиваться необходимой спецодеждой, соответствующей времени года (лето – роба х/б, сапоги, головной убор, рукавицы, а также средства защиты от кровососущих насекомых; зимой – шапка-ушанка, валенки, ватные штаны, шуба, ватные рукавицы).
На каждом кусте должна быть оборудована пульт-будка с имеющимися в наличии аптечкой, бачком с питьевой водой, носилками, а также мебелью для отдыха.
При работе в темное время суток объект должен быть освещен, во избежании травматизма. В качестве осветительных приборов применяются фонари и прожектора. Норма освещенности не ниже 10 лк (СНиП I – 4-79).
Особое внимание следует обратить на санитарное состояние территории куста, не допускать его захламления и замазученности, зимой необходимо регулярно расчищать снежные заносы на подходах к скважины.
Содержание нефтяных паров и газов в воздухе рабочей зоны не должно превышать ПДК (углеводороды предельно С-С10 в пересчете на С – 300 мг/м3, ГОСТ 12.1.005-76). Во время ремонта скважин при наличии в воздухе рабочей зоны нефтяных паров и газов, превышающих ПДК, необходимо заглушить скважину жидкостью соответствующих параметров и качества. Работы в загазованной зоны должны проводиться в соответствующих противогазах.
К монтажу (демонтажу) погружного агрегата УЭЦН и его обслуживанию допускается электротехнический персонал, знающий схемы применяемые станций управления, трансформаторов, подстанций погружных насосов (КТПН), конструкции по их эксплуатации, прошедший производственное обучение и стажировку на рабочем место, а также проверку знаний с присвоением квалификационной группы по электробезопасности.
Для измерения буферного давления и давления в затрубном пространстве на скважинах оборудованных УЭЦН должны быть установлены стационарные манометры с трехходовыми кранами.
Конструкция устьевого оборудования должна обеспечить возможность снижения давления в затрубном пространстве, а так же закачку жидкости для глушения скважины.
Наземное оборудование УЭЦН должно быть установлено в специальной будке или на открытой местности на расстоянии не менее 20 м от устья скважины.
При установке наземного оборудования в будке станция управления должна быть расположена так, чтобы при открытых дверцах обеспечивался свободный выход из будки.
При установке электрооборудования на открытой местности оно должно иметь ограждение и предупреждающий знак «Осторожно! Электрическое напряжение!».
Намотка и размотка кабеля на барабан кабеленаматывателя должна быть механизирована. Производить намотку (размотку) кабеля вручную, а также тормозить барабан руками, доской или трубой запрещается.
Все открытые движущиеся части механизмов кабеленаматывателя могущие служить причиной травмирования должны иметь ограждения.
Прокладка, перекладка кабелей УЭЦН по эстакаде рядом с действующими кабелями, находящимися под напряжением, а также перекладка кабелей допускается в случае необходимости при выполнении следующих условий:
Работу должны выполнять рабочие, имеющие опыт прокладки кабелей, по наряду-допуску (распоряжению электротехнического персонала ЦБПО НПО под руководством лица с группой по электробезопасности не ниже V при напряжении выше 1000 В.
Работать следует в диэликтрических перчатках, поверх которых для защиты от механияческих поверждений одеваются брезентовые рукавицы. Санитраные нормы действия тока на организм, устанавливает ГОСТ 12.1.000-76.
Таким образом в данном разделе разработаны основные мероприятия , которые обеспечат безопасные условия работы операторов при обслуживании скважин, оборудованных УЭЦН.
5.4. Общие требования к безопасности к рабочим цеха в подготовке
и перекачке нефти (ППН)
К самостоятельной работе в цехе ППН допускаются лица:
достигшие 18-летнего возраста.
Прошедшие медицинское освидетельствование согласно приказа Минздрава ССР № 700 от 19.06.84;
прошедшие производственное обучение, обучение безопасным методам в проведении работ, стажировку (при необходимости) на рабочем месте и проверку знаний по технике безопасности;
имеющие удостоверение о проверке знаний по технике безопасности.
Через каждые 3 месяца рабочие должны проходить инструктаж по безопасному ведению работ и не реже 1 раза в год – проверку знаний.
При внедрении новых видов оборудования и механизмов, новых технологических процессов, а также при введении в действие новых правил и инструкций по охране труда рабочие должны пройти дополнительное обучение и инструктаж.
Внеочередную проверку знаний по технике безопасности рабочие должны пройти:
после обучения, вызванного изменением технологического процесса, внедрением новых видов оборудования и механизмов, введением в действие новых правил и инструкций;
по требованию или распоряжению руководителей предприятий и представителей службы надзора.
Приступая к работе, рабочие должны иметь при себе удостоверение о проверке знаний по технике безопасности.
При приеме смены рабочие обязаны ознакомится с заданиями и распоряжениями руководителей работ, с записями в вахтовом журнале и уяснить себе обстановку на объекте и на рабочем месте.
При обнаружении какой-либо неисправности, не записанной в журнале, принимающий смену должен указать на нее сменяющемуся и вместе с ним сделать соответствующую запись в вахтовом журнале.
Не разрешается:
принимать или сдавать смену во время аварии и при ее ликвидации;
передавать смену рабочему, явившемуся в нетрезвом состоянии или больному.
Находясь на территории цеха ППН работающие должны соблюдать общие для всех правила поведения:
места открытого выделения газа надо обходить с наветренной стороны;
переходить через траншею, трубопроводы надо только в специально указанных местах, оборудованных переходами.
Рабочие цеха ППН перед началом работы обязаны: проверить состояние и исправность работающего и резервного оборудования (насосов, запорной арматуры, КИПиА и т.п.), чистоту рабочего места, производственных помещений и территории наличие инструмента и вспомогательного инвентаря, исправность действия вентиляционных установок, наличие и состояние средств индивидуальной защиты; привести в порядок спецодежду и др.средства индивидуальной защиты; проверить наличие и исправность пожаротушения и инструментов, их соответствие характеру работы, наличие и укомплектованность аптечки.
Рабочие обязаны следить за чистотой рабочих мест и всего оборудования. Рабочие площадки, лестницы и переходы необходимо очищать от грязи, снега и льда.
загромождение лестниц и площадок, проходов между трубопроводами и др. оборудованием, мешающие нормальному обслуживанию и ремонту не допускается.
Освещение объектов ППН должно быть выполнено во взрывобезопасном исполнении. Осветительная проводка должна прокладываться в герметичных газовых трубах, выключатели должны быть во взрывоопасном исполнении и установлены вне помещения.
В качестве аварийного освещения могут применятся только
аккумуляторные фонари во взрывобезопасном исполнении напряжением
12 Вт.
Рабочие должны иметь полагающиеся по нормам спецодежду, спецобувь, рукавицы и другие средства индивидуальной защиты, обеспечивающие безопасность. Спецодежду следует носить в застегнутом виде, она не должна меть свисающих концов.
При опасности попадания инородных тел, вредных жидкостей, паров, газа, раздражения глаз сильным световым излучением необходимо пользоваться соответствующими защитными очками.
При работе в колодцах, аппаратах, емкостях и других плохо проветриваемых местах необходимо применять шланговые противогазы.
Лица, допущенные к работам на объектах с возможным выделением сероводорода, должны иметь при себе исправные средства индивидуальной защиты (противогазы марки КД). Промышленные фильтрующие противогазы применяют в том случае, если в воздухе содержится не менее 18%
объемных кислорода, а концентрация вредных газов не превышает 0,5%
объемных.
Рабочие должны следить за состоянием предохранительной арматуры, наличием и исправностью манометром, обращать внимание на наличие и целостность пломб.
Не допускается эксплуатация аппаратов, емкостей и оборудования при неисправных предохранительных клапанах, отключающих и предохранительных устройствах, при отсутствии или неисправности контрольно-измерительных приборов и средств автоматики, а также работа с неисправным инструментом.
Все движущиеся части механизмов должны быть ограждены. Выступающие и вращающиеся детали должны быть закрыты по всей окружности вращения сплошными кожухами.
Запрещается эксплуатация неисправного оборудования отключающих и предохранительных устройств, неисправных контрольно-измерительных приборов и средств автоматики, а также работа неисправным инструментом.
Корпуса электрооборудования и пусковой аппаратуры должны быть заземлены.
Перед пуском механизмов в работу необходимо проверить их исправность. Пускать в работу механизмы следует, только убедившись, что у движущихся частей нет людей. И только после подачи предупредительного знака (сигнала).
Во время работы механизма запрещается:
производить ремонт их или крепление каких-либо частей;
чистить и смазывать движущиеся части вручную;
снимать ограждения или отдельные их части и проникать за ограждения;
тормозить движущиеся части механизмов подкладыванием труб, ваг и других предметов;
переходить через приводные ремни, цепей или под ними;
направлять, надевать, сбрасывать, натягивать или ослаблять ременные передачи;
находится в опасной зоне.
Ремонтные работы должны проводится в дневное время. При необходимости ремонтов в ночное время место работы должно быть освещено.
Работы по ремонту оборудования, связанные с применением открытого огня и возможностью образования открытого искрения, должны осуществляться по наряду-допуску на производство газоопасных работ или письменному разрешению главного инженера, согласованного с главным энергетиком предприятия и местной пожарной охраной.
Ремонтные работы в котловане, а также в нефтяных и газовых колодцах разрешается выполнять при соблюдении следующих условий:
бригада рабочих должна состоять не менее чем из двух человек (работающий и наблюдающий), обеспеченных соответствующими средствами индивидуальной защиты;
перед началом работ ответственный за их проведение должен спросить исполнителя о его самочувствии;
перед работой котлован или колодец проветрить, а перед сварочной работой – провести анализ воздушной среды;
проверить исправность шлангового противогаза, спасательного пояса и сигнально-спасательной веревки;
сроки единовременного пребывания работающего в шланговом противогазе должен превышать 20 минут.
В случае гидратообразования или замораживания участка трубопровода, обвязки насосов, запорной арматуры отогревать их следует водой или паром. Перед отогревом участок должен быть отключен от работающей системы.
При пропарке емкостей, аппаратов запрещается поднимать давление в них: пар должен иметь свободный выход. При пропарке труб запрещается стоять с противоположного конца, тем более, устранять закупорку пропариваемых труб разрыхлением различными предметами.
Пропуск газа и нефтепродуктов через фланцевые соединения, сальники, задвижки и другие неплотности необходимо своевременно устранять.
При необходимости проведения ремонтных работ на трубопроводах находящихся под давлением, подлежащий ремонту участок необходимо отключить задвижками с установкой маркированных заглушек после снижения в нем давления до атмосферного.
Закрывать (открывать) запорную арматуру следует плавно, без рывков, пользуясь при необходимости специальным (штурвальным) ключом.
В случае возникновения аварийной ситуации, связанной с повышением содержания сероводорода в воздухе, необходимо:
немедленно одеть противогаз;
прекратить все работы в опасной зоне;
сообщать об этом ответственному руководителю работ;
обозначить опасную зону предупреждающими знаками;
дальнейшие работы производить по плану ликвидации возможных аварий.
При аварии рабочие обязаны действовать в соответствии с планом ликвидации аварий; сообщить о происшедшей аварии диспетчеру, вывести людей из помещения или опасной зоны и при необходимости, в целях предупреждения осложнений, отключить технологическое оборудование.
При возникновении пожара необходимо немедленно вызвать пожарную охрану и приступить к тушению огня имеющимися на объекте противопожарными средствами.
При несчастном случае необходимо оказать пострадавшему доврачебную помощь, вызвать, если необходимо скорую медицинскую помощь, сообщать о происшедшем руководителю работ или начальнику цеха и по возможности сохранить обстановку на рабочем месте такой, какой она была в момент несчастного случая.
В случае возникновения аварийной ситуации смена, в которой возникла авария, не сдает смену до ликвидации аварии. Принимающая смена включается в работу по ликвидации аварии.
5.5.Характеристика условий труда.
Характеристика выбросов вредных веществ в атмосферу
Таблица 5.1.
Вредные вещества
Кол-во вредных
веществ отходящих от всех источников
В том числе: выделяются без очистки
Всего выброшено в атмосферу
Лимит выброса
Наименование
Окислы азота
9,355
9,355
9,355
9,355
Сернистый ангидрид
73,985
73,985
73,985
73,985
Окись углерода
53,62
53,62
53,62
53,62
Пятиокись ванадия
0,296
0,296
0,296
0,296
Окись железа
0,616
0,616
0,616
0,616
Стирол
0,222
0,222
0,222
0,222
По формуле можно рассчитать степень риска производства, определяемого за год:
R=Сn/Np= 1/104500=9,57х10-6
где Cn – число смертельных случаев за год;
где Np - число работающих.
5.6.Пожарная профилактика
Пожарная профилактика достигается правильным проектированием, эксплуатацией и обеспечением средствами пожаротушения.
В зависимости от пожаро- и взрывоопасных свойств применяемых, производимых или хранимых веществ, все производство по степени пожарной опасности подразделяется на пять категорий: А, Б, В, Г, Д.
Категория А. Производство, связанное с получением, применением или хранением: жидкостей, имеющих температуру вспышки паров (280С) и ниже; паров или газов с нижним пределом взрываемости 10% и менее в количествах, которые могут образовать с воздухом взрывоопасные смеси; горючих жидкостей при температуре нагрева их до 2500С.
Категория Б. Производства, связанные с применением, получением, хранением или переработкой: жидкостей с температурой паров от 290 до 1200С; горючих газов, нижний предел взрываемости которых более 10% к объему воздуха, при применении этих газов в количествах, которые могут образовать с воздухом взрывоопасные смеси; производства, в которых выделяются горючие волокна или пыль в таком количестве, что они могут образовать с воздухом взрывоопасные смеси.
Категория В. Производства, связанные с обработкой или применением твердых сгораемых веществ и материалов, а также жидкостей с температурой вспышки паров выше 1200С.
Категория Г. Производства, связанные с применением или обработкой несгораемых веществ и материалов в горячем, раскаленном или расплавленном состоянии и сопровождающиеся выделением лучистой теплоты, искр и пламени, а также производства, связанные с ожиганием твердого, жидкого и газообразного топлива.
Категория Д. Производства, связанные с обработкой несгораемых веществ и материалов в холодном состоянии.
Для тушения пожара используют следующие средства пожаротушения: ручные пенные огнетушители типа ОП, углекислотные огнетушители ОУ-2, пенопроизводящие установки – пеномесителя, воздушнопенные стволы, генераторы высококоратной пены, гидранты и другие средства.
Первичные средства пожаротушения размещают в легко доступных местах. Огнетушители защищают от солнечных лучей, осадков.
Для улучшения условий труда необходимо намечать как можно большее количество позитивных мероприятий и соответствовать ГОСТам.
5.7.Прогнозирование чрезвычайных ситуаций и
их предотвращение.
Одной из наиболее частых аварий является взрыв.
При выборе электрооборудования для объектов добычи нефти и газа необходимо учитывать специфические условия работы электрических установок, связанных с наличием взрывоопасных газов и паров.
К взрывоопасным относятся смеси с воздухом горючих газов и паров горючих жидкостей с температурой вспышки 450С и ниже, а также горючей пыли или волокон с нижним пределом взрываемости не выше 65 г/см3.
В зависимости от температуры самовоспламенения устанавливаются 5 групп взрывоопасных смесей:
Таблица 5.2.
Группа взрывоопасной смеси
Температура самовоспламенения С
Т1
Свыше 450
Т2
300 до 450
Т3
200 до 300
Т4
135 до 200
Т5
100 до 135
Распределение некоторых смесей по категориям и группам приведено в таблице 5.3.
Таблица 5.3.
Категория взрывоопасных смесей
Группа взрывоопасных смесей
Т 1
Т 2
Т 3
Т 4
Т 5
1
Аммиак, метан, дихлорэтан, изобутилен, метилстирол, метил хлористый, метил хлористый, метилацетат.
Амилацетат, бутилацетат, винилацетат, изопропен, метилметакрилат, спирты: бутиловый, изоамиловый, изопропиловый и др.
Скипидар, уайтспирит, циклогексан, спирт амиловый, полиэфир ТГМ-3 и др.
-
-
2
Ацетон, бензин-100, бензол, толуол, стирол, пропан, этан, этилбензол, окись углерода и др.
Бензин Б-95/130, бутан, дивинил, диоксан, метиламин, метилфуран, пентан, пропилен и др.
Бензин: А-66, А-72, А-76, Б-70, гексан, топливо Т-1, ТС-1 и др.
Ацетальдегид, этиленглиголь, диэтиловый эфир, дибутиловый эфир.
-
3
Коксовый газ (метана 40%, водорода 60%), светильный газ, этилен.
Окись этилена, окись пропилена, этилтрихлорсилан.
Винилтрихлормилан, этилдиххлорсилан.
Диэтиловый (серный) эфир.
-
4
Водород, водяной газ.
-
Ацетилен, метиодихлорсилан.
Сероводород
Трихлорсилан
-
-
Сероуглерод
-
При взрыве газовоздушной смеси весом в 10 т находится на расстоянии менее 65 м от эпицентра взрыва опасно для жизни.
Для насосов и другого оборудования:
Слабые разрушения при Δpф =0,25-0,4 атм.
Средние разрушения при Δpф =0,4-0,6 атм.
Сильные разрушения при Δpф =0,6-0,7 атм.
На рис. 5.1. изображена примерная схема распространения ударной волны по зонам.
Рис.5.1.
R2
3 2
R1 1
r2
r3
Условные обозначения на схеме:
1 – зона детонации
2 – зона действия продуктов взрыва
3 – зона ударной волны
R1 - радиус первой зоны
R2 - радиус второй зоны
r2 - расстояние от центра взрыва до элемента предприятия (во 2 зоне)
r3 -расстояние от центра взрыва до элемента предприятия (в 3 зоне)
R1=17,5 3√Q=17,5√10=37,7 м
где Q -количество газа, т.
R2=1,7R1=1,7*37,7=64,1 м
Разность давлений в 1 зоне Δpф =1700 кПа
Разность давлений во 2 зоне:
Δpф=1300 (R1 / r2)3+50= 1300 (37,7/50)3+50=607 КПа
Ψ=r3/R1=85/37,7=2,3
При Ψ> 2 разность давлений в третьей зоне:
Δpф=22/ Ψ√lg Ψ+0,155 =13,3 Кпа
Радиус Зоны, опасной для жизни человека:
Rсм=30 3√Q=64,4 м
5.8.Основные мероприятия по предотвращению опасностей,
связанных с особенностями оборудования.
Технологические процессы, идущие под высоким давлением, оборудование, находящиеся под большими нагрузками, в определенных условиях представляют опасность для работающих.
Основные мероприятия по предотвращению опасностей, обусловленные повышением давления и нагрузкам, сводится к следующим:
осмотр и испытание установки, оборудования, механизмов;
использование ослабленных элементов и устройств для механизации опасности;
применение средств блокировки, исключающих аварии при неправильных действиях работающих.
автоматизация производственных процессов, позволяющая вывести из опасных зон, осуществление контроля за показаниями приборов и дистанционные управления;
учитывать розу ветров. Нельзя допускать возможность попадания опасных по взрыву и пожару смесей в огнедействующие установки;
на каждом предприятии с числом работающих более 300 человек организуют фельдшерский здравпункт, а более 800 человек – врачебный здравпункт.
5.9.Выводы.
На основании анализа условий труда обслуживающего персонала, характеристики вредных веществ, загрязняющих природную среду и прогнозирования возможных чрезвычайных ситуаций на данном объекте можно сделать следующие выводы:
В основном объект отвечает требованиям ГОСТов по условиям труда, намечены мероприятий по условиям труда. Анализируя возможные чрезвычайные ситуации, в данном проекте выявлены вероятные параметры ударной волны при взрыве газовоздушной смеси, и намечены мероприятия по предотвращению возникающих поражающих вредных факторов: взрыва и др. факторов.
Литература
Бухаленко Б.И. Справочник по нефтепромысловому оборудованию М., Недра, 1983 г., 390 с.
Бабаев С.Г. Надежность нефтепромыслового оборудования. М., Недра, 1987 г., 265 с.
Бухаленко Е.И., Абдуллаев Ю.П. Монтаж, обслуживание и ремонт нефтепромыслового оборудования.М., Недра, 1985 г., 390 с.
Богданов А.А. Погружные центробежные электронасосы для добычи нефти. М., Недра, 1986 г., 272 с.
Бочарников В.Ф., Чижиков Ю.Н. Методические указания по дипломному проектированию для студентов специальности (0508). Машины и оборудование нефтяных и газовых промыслов. Тюмень, 1987 г., 33 с.
Беззубов Д.В и др. Насосы для добычи нефти. М., Недра, 1986 г., 224 с.
Говорова Г.Л. Разработка нефтяных месторождений и добыча нефти с
США. М., Недра, 1970 г., 272 с.
Иванов М.Н., Детали машин М., Высшая школа, 1991 г., 350 с.
Казак А.С., И.И. Росин, Л.Г. Чичеров Погружные бесштанговые насосы для добычи нефти. М., Недра, 1973 г, 230 с.
Лутошкин Г.С. Сбор и подготовка нефти, газа и воды. М., Недра, 1974
г, 184 с.
Сулейманов М.М. и др. Охрана труда в нефтяной промышленности. М., Недра, 1980 г, 392 с.
12.Чичеров Л.Г. Расчет и конструирование нефтепромыслового оборудова-
ния М., Недра, 1987 г., 280 с.
13.Паспорт погружного центробежного модульного насоса. 211. НМЛ
03.000 ПС 1. Лебядянский машиностроительный завод. 15 с.
14.Анализ отказов по ЭЦН. СЦБПО ЭПУ, Сургут, 1998 г.
15.Руководство по эксплуатации УЭЦНМ. БПТО и КО № 3, Сургут. 118 с.
Приложение 5
Сведения о наработке и количестве отказов установок, оборудованных ЭЦН
НГДУ,
Месторождение
Тип оборудования
Общая наработка
Кол-во отказов
Наработка на отказ
Быстринскнефть
ЭЦН – 20
50
80
130
200
250
400
FS
Итого:
19224
117828
75781
80062
45203
11898
3828
13581
367405
65
349
192
178
122
24
6
24
960
295
337
394
449
370
495
638
565
382
Федоровскнефть
ЭЦН – 20
50
80
130
200
250
400
500
FS
ODI
Итого:
53552
274536
180361
148510
82399
27369
10262
7396
14403
11464
810252
209
1047
537
422
285
84
50
27
25
36
2722
256
262
335
351
289
325
205
273
576
318
297
Сургутнефть
ЭЦН – 20
50
80
130
200
250
ODI
Итого:
1966
93900
63829
40291
13234
3499
187
216906
8
239
124
76
35
13
2
497
245
392
514
530
378
269
93
436
Лянторнефть
ЭЦН – 20
50
80
130
200
250
FS
ODI
Итого:
7029
577040
167271
56011
9850
2964
12472
3278
835915
53
2160
453
145
34
9
27
15
2896
132
267
369
386
289
329
461
218
288
СНГ
ЭЦН – 20
50
80
130
200
250
400
500
FS
ODI
Итого:
70548
1193103
484640
288976
119629
37549
12056
7414
26875
15261
22561
314
4386
1359
752
388
112
53
28
52
56
7500
224
272
356
384
308
335
227
264
516
272
300
ANNOTATION
In the diplom project there is the main information about the electro-centrifugal pump’s plant. There was analysis home and foreign plans plant, analysis of refusal by know. Jugested improvement the of pump. There was necessary hydraulic and durable calculations and computation waiting economical effect.
АННОТАЦИЯ
В данном дипломном проекте даны основные сведения об установках электроцентробежных насосов. Произведен анализ отечественных и зарубежных схем установок, анализ отказов по узлам. Предложено усовершенствование насоса.
Произведены необходимые гидравлические и прочностные расчеты и расчет ожидаемого экономического эффекта.
Приложение 1
Техническая характеристика насосов типов ЭЦНМ и ЭЦНМК
Типоразмер
Подача, м3/сут
Напор, м
Мощность, кВт
КПД, %
Частота вращения, об/мин
Количество
Длина, мм
Давление на оптимальном режиме, кг/см2
ступеней
секций
ЭЦНМ5-50-1300
ЭЦНМ5-50-1300
50
1360
1775
17,94
23,42
43
264
344
2
2
8252
10252
133,4
174,1
ЭЦНМ5-50-1200
ЭЦНМК5-80-1200
ЭЦНМ5-80-1550
ЭЦНМК5-80-1550
ЭЦНМ5-80-1800
80
1235
1235
1615
1615
1800
12,77
21,77
28,46
28,46
31,73
51,5
286
286
351
351
392
2
2
2
2
2
8252
8252
10252
10252
11252
121,2
121,2
158,4
158,4
176,6
ЭЦНМ5-125-1200
ЭЦНМК5-125-1200
ЭЦНМ5-125-1300
ЭЦНМК5-125-1300
ЭЦНМ5-125-1800
125
1180
1180
1335
1335
1770
28,61
28,61
32,37
32,37
42,92
58.5
262
262
296
296
393
2
2
2
2
2
9252
9252
10252
10252
13617
115,8
115,8
131
131
173
ЭЦНМ5-200-800
ЭЦНМ5-200-1400
200
830
1395
36,76
64
50
235
393
2
3
10252
17986
81,3
136,8
ЭЦНМ5А-160-1450
ЭЦНМ5А-160-1750
160
1415
1705
42,11
50,75
61
285
345
2
3
10251
12615
138,8
167,3
ЭЦНМ5А-250-100
ЭЦНМ5А-250-1400
ЭЦНМК5А-250-1400
ЭЦНМ5А-250-1700
ЭЦНМК5А-250-1700
250
1000
1400
1400
1695
1695
46,13
64,57
64,57
78,18
78,18
61,5
2910
184
257
257
311
311
2
3
3
4
4
11252
15617
15617
18982
19982
98,1
137,3
137,3
166,3
166,3
ЭЦНМ5А-400-950
ЭЦНМК5А-400-950
ЭЦНМ5А-400-1250
ЭЦНМК5А-400-1250
400
980
980
1255
1255
74,75
74,75
95,74
95,74
59,5
240
240
308
308
4
3
4
4
15617
15617
19982
19982
96,1
96,1
123,1
123,1
ЭЦНМ5А-500-800
ЭЦНМ5А-500-1000
500
825
1010
85,88
105,1
54,5
202
248
3
4
14617
17982
81
99,1
ЭЦНМ6-250-1400
ЭЦНМ6-250-1600
250
1450
1650
65,29
74,29
63
232
263
2
2
9252
10252
142,2
162
ЭЦНМ6-500-1150
500
1160
109,69
60
218
3
14617
113,8
ЭЦНМ6-800-700
ЭЦНМ6-800-1000
800
725
965
109,68
145,99
60
153
204
3
4
13617
17982
71,1
94,7
ЭЦНМ6-1000-900
1000
900
170,21
60
208
4
21982
88,3
Приложение 4
Основные технические параметры кабельных линий
Типоразмер кабельной линии
Кабель в сборе
Типоразмер кабеля в сборе
Кабель основной
Удлинитель с муфтой
Количество X сечение жил (мм2)
Длина, м
Количество X сечение жил (мм2)
Длина, м
КПБК
КПБП
К43.000-04
К43.010-04
3Х10
-
900
3Х6
50
К43.000-06
К43.010-06
3Х10
-
1000
3Х6
50
К43.000-08
К43.010-08
3Х10
-
1100
3Х6
50
К43.000-10
К43.010-10
3Х10
-
1200
3Х6
50
К43.000-12
К43.010-12
3Х10
-
1300
3Х6
50
К43.000-14
К43.010-14
3Х10
-
1400
3Х6
50
К43.000-16
К43.010-16
3Х10
-
1500
3Х6
50
К43.000-18
К43.010-18
3Х10
-
1600
3Х6
50
К43.000-20
К43.010-20
3Х10
-
1700
3Х6
50
К43.000-35
К43.010-35
3Х16
-
900
3Х6
50
К43.000-41
К43.010-41
3Х16
-
1100
3Х6
50
К43.000-45
К43.010-45
-
3Х16
1200
3Х6
50
К43.000-47
К43.010-47
3Х16
-
1300
3Х6
50
К43.000-50
К43.010-50
3Х16
-
1400
3Х6
50
К43.000-51
К43.010-51
-
3Х16
1400
3Х6
50
К43.000-53
К43.010-53
3Х16
-
1500
3Х6
50
К43.000-56
К43.010-56
3Х16
-
1600
3Х6
50
К43.000-59
К43.010-59
3Х16
-
1700
3Х6
50
К43.000-61
К43.010-61
3Х16
-
1800
3Х6
50
К43.000-63
К43.010-63
3Х16
-
1900
3Х6
50
К43.000-67
К43.010-67
3Х16
-
2100
3Х6
50
К43.000-91
К43.010-91
3Х25
-
1100
3Х16
50
К43.000-92
К43.010-92
-
3Х25
1100
3Х16
50
К43.000-97
К43.010-97
3Х25
-
1300
3Х16
50
К43.000-110
К43.010-110
3Х25
-
1800
3Х6
50
К43.000-112
К43.010-112
3Х25
-
1900
3Х6
50
СМЕТНАЯ КАЛЬКУЛЯЦИЯ № 1
на ЭЦНМ5 – 50-1300 (две секции)
№
п/п
СТАТЬЯ ЗАТРАТ
Сумма (руб)
1
Сырье и материалы
275842
2
Покупные изделия (запчасти)
2890014
3
Транспортные расходы
237268
4
Возвратные отходы (минусы)
ИТОГО:
3203124
5
Заработная плата
104520
6
Дополнительная зарплата
13588
7
Начисления на соцстрах
45472
8
Услуги и работы вспомогательных служб
47034
9
Инструмент и приспособления целевого назначения
6271
10
Электроэнергия
10452
11
Расходы на подготовку и освоение производства
10445
12
Цеховые расходы
58531
13
Расходы по содержанию оборудования
15678
14
Общезаводские расходы
290566
15
Расходы на подготовку и освоение производства.
Итого заводская себестоимость
16
Внепроизводственные расходы
17
Полная себестоимость
3796281х1,23
18
Прибыль
4669426х1,1
19
Отпускная цена
5136369
Расшифровка материалов к
сметной калькуляции № 1
на ЭЦНМ5 – 50-1300 (две секции)
№
Наименование материалов
марка
Единица измерения
Цена
Количество
Сумма
1
Колесо рабочее НМ003.015
Шт.
12940
41,0
530540
2
Аппарат направляющий НМ003.016
Шт
17404
60,0
1044240
3
Шайба верхняя УЭ155.058-01
Шт
3610
41,0
148010
4
Шайба колеса УЭ152.022
Шт
3911
164,0
641404
5
Втулка защитная УЭ155.024
Шт
25156
1
25156
6
Втулка защитная вала УЭ155.031
Шт
3420
110,0
376200
7
Втулка подшипная УЭ102.077
Шт
26508
1,5
39762
8
Вал d-17, l – 4342 НМ003.007-06
Шт
140996
0,05
7050
9
Вал d-20, l-303
НМ003.029
Шт
115425
0,05
5771
10
Шпонка УЭ102.039
М/Шт
12360
2,0 / 1
12360
11
Втулка УЭ186.009-02
М/Шт
17940
0,2
3588
12
Муфта шлицевая
НМ003.120-11
М/Шт
6168
0,05
308
13
Муфта шлицевая
НМ003.130
М/Шт
6168
0,05
308
14
Подпятник УЭ102.025
М/Шт
50751
0,4
20300
15
Шайба пяты
УЭ102.026
Шт
16893
1,0
16893
16
Шайба УЭ102.027
Шт
9062
2,0
18124
17
Ветошь ГОСТ 5354-79
Кг
815
0,6
489
18
Масло МА ПЭД ГОСТ 20799-75
Кг
6800
1,0
6800
19
Моющее вещество МС-15
Кг
33388
2,0
66776
20
Смазка: УТ ГОСТ 1957-79
Кг
11624
0,06
697
21
Солидол УС ГОСТ 1033-79
Кг
6000
0,18
1080
22
Графит ГС-4 ГОСТ 8295-73
Кг
-
0,36
-
Итого: 2965856
СМЕТНАЯ КАЛЬКУЛЯЦИЯ № 2
Текущий ремонт гидрозащиты 1Г-51
(протектора 1Г-51 и компенсатора ГД-51)
№ п/п
Статьи затрат
Сумма
1
Запчасти
524,42
2
Сырье и материалы
73,83
3
Транспортно заготовительные расходы
5,98
ИТОГО:
604,23
4
Заработная плата
70,42
5
Отчисления на соц.страх
27.11
6
Накладные расходы
1079,54
ВСЕГО
1781,30
РАСШИФРОВКА СТАТЬИ «Сырье и материалы»
№
Наименование
Обозначение
Ед.
Изм.
Цена
Кол-во
Сумма
1
Масло I категории Омского НПЗ
ГОСТ101210-76
Кг
3,28
10
32,80
2
Нефрас с50/170 (Бр-2)
ГОСТ85505-80
Кг/л
1,80
4,38/6
7,88
3
Пленка ПМФС-352,0,06Х30
ТУ 6-19-226-83
Кг
127,46
0,032
4,08
4
Проволока ДКРНМ2Л63
ГОСТ1066-90
М
3,00
8
24,00
5
Порошок притирочный АСМ 28/20
ГОСТ9206-80
Кг
2,10
0,001
0,002
6
Салфетки х/б
ГОСТ21220-75
Шт.
1,10
1,1
1,21
7
Полотно нетканное
кг
0,01
0,2
0,002
8
Мс-15
ТУ10-980-92
кг
12,62
0,13
1,64
9
Шкурка шлифовальная 1,830х2 СГТ 15А80МА
ГОСТ6456-82
м2
22.50
0,04
0,90
10
Силикагель КСКГ
ГОСТ3956-76Е
кг
12,00
0,11
1,32
ИТОГО:
73,8
РАСШИФРОВКА СТАТЬИ «Запчасти»
№
Наименование
Обозначение
Ед.
изм.
Цена
Кол-во
Сумма
1
Корпус пяты
8ТЩ001.365
Шт.
14,00
0,05
0,70
2
Втулка подшипника
8ТЩ007.036-01
Шт.
19,90
0,09
17,91
3
Вал
8ТЩ200.351
Шт.
265,40
0,2
53,08
4
Кольцо
8ТЩ217.514
Шт.
2,20
0,1
0,22
5
Кольцо пружинное
8ТЩ218.416
Шт.
1,60
5
8,00
6
Головка верхняя
8ТЩ253.294Э
Шт.
210,80
0,05
10,54
7
Пята
ЕЮТИ052.004
Шт.
46,60
0.3
13,98
8
Кожух
8ТЩ300.018
Шт.
5,20
0,5
2,60
9
Крышка
ЭД139.013
Шт.
51,80
0,2
10,36
10
Крышка
ЭД139.021
Шт.
26,50
0,1
2,65
11
Пробка
ЭД139.154
Шт.
4,70
1,4
6,68
12
Пробка
ЭД139.011
Шт.
8,70
0,3
2,61
13
Кольцо 075-081-36-2-2
ГОСТ18829-73
Шт.
2,40
9
21,60
14
Кольцо 034-040-36-2-2
ГОСТ18829-73
Шт.
1,90
4
7,60
15
Кольцо 052-058-36-2-2
ГОСТ18829-73
Шт.
2,20
7
15,40
16
Шпилька
ЭД139.017
Шт.
3,20
4,2
13,44
17
Шпилька
ЭД139.017-01
Шт.
3,20
1,05
3,36
18
Гайка
8ТЩ948.295
Шт.
3,00
0,4
1,20
19
Шайба
ЭД139.015
Шт.
1,00
8
8,00
20
Шайба
ЭД139.015-02
Шт.
1,20
2
2,40
21
Шпонка
ЭД139.018-01
Шт.
2,00
0,7
1,40
22
Шпонка
8ТЩ979.080-05
Шт.
3,30
0,35
1,16
23
Шпонка
8ТЩ979.128-01
Шт.
0,50
0,35
0,18
24
Кольцо
ЕЮТТИ052.003
Шт.
14.60
0,6
8,76
25
Винт М4.10.58.019
ГОСТ17473-80
Шт.
0,72
2,1
1,51
26
Гайка М10.12.40х019
ГОСТ2524-70
Шт.
3,00
7,2
21,60
27
Шайба пружинная 10.65Г.019
ГОСТ6402-70
Шт.
0,15
4,5
0,68
28
Уплотнение торцовое 2Р25В
ТУ16.305.028-85
Шт.
91,40
0,2
18,28
29
Подпятник
ЕЮТИ052.600
Шт.
75,10
0,6
45,06
30
Клапан
5ТЩ456.055-01
Шт.
24,80
0,3
7,44
31
Каркас
5ТЩ080.035.
СБ
Шт.
17,00
0,05
0,85
32
Корпус
ЕЮТИ347.000
Шт.
25,00
0,05
1,25
33
Сильфон ( к торц. Уплот.)
8ТЩ258.004
Шт.
8,00
0,05
16,00
34
Шайба
8ТЩ950.283
Шт.
7,60
0,9
4,56
35
Втулка защитная
8ТЩ219.232
Шт.
7,00
0,05
0,35
36
Пробка
ЕЮТИ060.000-01
Шт.
3,20
0,7
0,16
37
Головка нижняя
8ТЩ253.205
Шт.
210,80
0,05
10,54
38
Втулка
8ТЩ294.143
Шт.
13,80
0,7
12,42
39
Ниппель нижний
8ТЩ454.081
Шт.
16,00
0,05
0,80
40
Кольцо 009-013-25-2-2
ГОСТ18829-73
Шт.
1,80
1
1,40
41
Ниппель верхний
8ТЩ454.086
Шт.
25,00
0,05
0,80
42
Кольцо 004-007-19-2-2
ГОСТ18829-73
Шт.
75,00
1
1,26
43
Корпус
5ТЩ000.176СБ
Шт.
30,00
0,3
1,25
44
Диафрагма
8ТЩ456.039
Шт.
80,00
1
75,00
45
Каркас диафрагмы
8ТЩ.456.050
Шт.
30,00
1,50
46
Диафрагма
8ТЩ.456.040
Шт.
80,00
80,00
47
Клапан
ЭД139.012
Шт.
20,60
6,18
48
Кольцо 008-012-25-2-2
ГОСТ18829-73
Шт.
1,80
1,80
.
0,00
ИТОГО:
524,42
РАСШИФРОВКА СТАТЬИ «Трудовые затраты»
№
Наименование работ
Разряд
Норма врем.
Расценка
Сумма
1
Разборка протектора Г-51м
4-5
0,88
4,56
4,01
2
Разборка компенсатора ГД-51
3-4
0,44
3,66
1,61
3
Сквозные работы
3-4
2,8
3,66
10,25
4
Сборка протектора 1Г-51
4-5
1,7
4,56
7,75
5
Сборка компенсатора ГД-51
4
0,88
3,87
3.41
6
Обкатка протектора 1Г-51
3
0,68
3,87
2,63
7
Гидравлическое испытание
4
0,68
3,87
2,63
Протектора 1Г-51
ИТОГО:
8,06
32,01
Премия (25%)
0,00
Районный к-т и сев. надб.
38,41
ВСЕГО
70,42
СМЕТНАЯ КАЛЬКУЛЯЦИЯ № 3
Текущий ремонт кабельной линии КППБ, КПБК для УЭЦН
№ п/п
Статьи затрат
Сумма
1
Запчасти
838,13
2
Сырье и материалы
10502,21
3
Транспортно заготовительные расходы
1,01
ИТОГО:
11341,35
4
Заработная плата
110,51
5
Отчисления на соц.страх
42,55
6
Накладные расходы
1694,12
ВСЕГО
13188,53
РАСШИФРОВКА СТАТЬИ «Запчасти»
№
Наименование
Обозначение
Ед.
изм.
Цена
Кол-во
Сумма
1
Удлинитель с муфтой модульной кабельного ввода.
к№93
Шт.
838,13
1
838,13
ИТОГО:
838,13
РАСШИФРОВКА СТАТЬИ «Трудовые затраты»
№
Наименование работ
Разряд
Норма времени
Расценка
Сумма
1
Разборка
3-4
5,45
3,66
19,95
2
Сборка
3-4
3,65
3,66
13,36
3
Сквозные работы
3-4
0,7
3,66
2,56
4
Испытание на стенде
3-4
3,15
4,56
14,36
ИТОГО:
12,95
50,23
Премия (25%)
0,00
Районный к-т и сев.надб.
60,28
ВСЕГО:
110,51
РАСШИФРОВКА СТАТЬИ «Сырье и материалы»
№
Наименование
Обозначение
Ед.
изм.
Цена
Кол-во
Сумма
1
Пленка фторопластовая Ф-4ЭО
ТУ6-05-2004-86
Кг
365
0,045
16,43
2
Лента полиэтиленовая липкая 0,1х20
ГОСТ5974-81
Кг
19
0,16
3,04
3
Пленка ПМФС-352 0,06х30
ТУ19-226-83
Кг
127,5
0,06
7,65
4
Припой МФСу
92-6-2
ТУ46-21-584-76
Кг
60,1
0,06
3,61
5
Нефрас С50/170 (Бр-2)
ГОСТ85505-80
Кг/л
1,8
0,37/0,5
0,67
6
Шкурка шлифовальная 1,830х2СГТ 15А80МА
ГОСТ6456-82
М2
22,5
0,02
0,45
7
Салфетки х/б
ГОСТ21220-75
Шт
1,1
1
1,10
8
Лента киперная х/б 0,45х20
ГОСТ4514-78
М
0,2
20
4,00
9
Броня «S»-профиль
Кг/м
30,0
2,07/39
63,96
10
Кабель КПБП, КПБК
м
21
495,3
10401,30
11
Полотно нетканное
м
0,010
0,4
0,004
ИТОГО:
10502,21
СМЕТНАЯ КАЛЬКУЛЯЦИЯ № 4
на текущий ремонт насоса ЭЦНМ 5-50-1700
№
Наименование
Обозначение
Ед.
изм.
Цена
Кол-во
Сумма
1
Аппарат
направляющий
НМ003.016
Шт.
23,70
103
2441,10
2
Втулка защитная вала
УЭ155.031
Шт.
3,84
105
403,20
3
Колесо рабочее
НМ003.015
Шт.
19,20
103
1977,60
4
Шайба колеса верхняя
УЭ155.058
Шт.
0,48
152
72,96
5
Шайба колеса нижняя
УЭ152.022
Шт.
1,20
152
182,40
6
Втулка защитная
УЭ155.024
Шт.
39,60
2
79,20
7
Опора верхняя
УЭ196.120
Шт.
69,12
0,6
41,47
8
Опора нижняя
УЭ196.016
Шт.
88,32
0,6
52,99
9
Вал d=17, l=4 м
НМ003.007-06
Шт.
330,00
0,3
99,00
10
Вал d=17, l=5 м
НМ003.007-02
Шт.
559,68
0,3
167,90
11
Шпонка дл. 1 м
УЭ102.039
Шт.
5,76
3
17,28
12
Шайба пяты
УЭ102.026
Шт.
12,00
2
24,00
13
Подпятник
УЭ102.025
Шт.
28,08
1,1
33,70
14
Втулка
подшипника
УЭ102.077
Шт.
38,40
2
76,80
15
Муфта шлицевая
НМ003.120-11
Шт.
97,20
0,3
29,16
16
Муфта шлицевая
НМ003.130
52,20
0,6
31,32
17
Шайба
УЭ102.027
Шт.
4,80
4
19,20
18
Втулка
УЭ155.027-05
Шт.
0,00
1
0,00
19
Основание
УЭ185.003
Шт.
0,00
0,1
0,00
20
Головка
УЭ186.002
Шт.
0,00
0,1
0,00
21
Втулка
дистанционная
УЭ155.022-04
Шт.
0,00
0,6
0,00
22
Кольцо опорное вала
УЭ188.009
Шт.
0,96
6
5,76
23
Корпус насоса
УЭ196.021
Шт.
0,00
0,1
0,00
24
Подшипник
верхний
УЭ186.080
Шт. Шт.
0,00
0,6
0,00
25
Крышка
упаковочная
Э2-81
Шт.
0,00
0,1
0,00
26
Гайка М12
Э2-62
Шт.
1,74
4
6,96
27
Болт М12-6gх60
ГОСТ 7808-70
Шт.
4,44
2,8
12,43
28
Шайба пружинная 12
ГОСТ 6402-70
Шт.
0,26
4
1,04
29
Кольцо 060- 065-30-2-2
ГОСТ 18829-73
Шт.
2,40
3
7,20
30
Кольцо 075-080-30-2-2
ГОСТ 18829-73
Шт.
2,40
6
14,40
31
Подшипник
нижний
УЭ155.110
Шт.
180,00
0,6
108,00
32
Шайба опорная
УЭ102.042
Шт.
26,40
0,6
15,84
33
Отбойник
УЭ196.023
Шт.
0,00
0,6
0,00
34
Сетка
УЭ186.011
Шт.
0,00
0,3
0,00
35
Крышка
упаковочная
НМ003.001
Шт.
0,00
0,05
0,00
36
Шайба
УЭ102.084
Шт.
16,80
1
16,80
37
Втулка
НМ003.008-01
Шт.
0,00
0,3
0,00
38
Шайба опорная
НМ003.009-01
Шт.
0,00
0,3
0,00
39
Шпонка
НМ003.011
Шт.
0,00
0,3
0,00
40
Втулка
УЭ155.027-04
Шт.
0,00
0,3
0,00
41
Вал
НМ003.012
Шт.
0,00
0,3
0,00
42
Втулка распорная
УЭ155.026
Шт.
0,00
0,6
0,00
43
Шпилька М12 8gх30.88.55
ГОСТ 22038-76
Шт.
4,80
2,1
10,08
44
Клапан обратный КО-73
УЭ196.020СБ
422,40
0,25
105,60
ИТОГО:
6053,39
РАСШИФРОВКА СТАТЬИ «Сырье и материалы»
№
Наименование
Обозначение
Ед.
изм.
Цена
Кол-во
Сумма
1
Масло индустриальное И-20А
ГОСТ 20799-75
кг
2,78
0,69
1,92
2
МС-15
ТУ10-980-92
кг
5,00
1,239
6,20
3
Шкурка
шлифовальная 1,830х2 СГТ
ГОСТ 6456-82
м2
45,53
0,08
3,64
4
Салфетка х/б
ГОСТ 21220-75
шт.
0,76
0,8
0,61
5
Полотно нетканное
м2
5,54
1
5,540
6
Смазка графитная
УСсА
ГОСТ 3333-80
кг
33,41
0,53
17,71
7
Краска масляная
кг
25,00
0,005
0,13
ИТОГО:
35,75
РАСШИФРОВКА СТАТЬИ «Трудовые затраты»
№
Наименование работ
Разряд
Норма времени
Расценка
Сумма
1
Разборка
3-4
1,29
3,66
4,72
2
Сборка
3-4
3,4
3,66
12,44
3
Сквозные работы
3
9,95
3,45
34,33
4
Испытание секций и консервация
3-4
3,22
4,56
14,68
ИТОГО:
17,86
66,17
Премия (25%)
0,00
Районный к-т и сев.надб.
79,40
ВСЕГО:
145,57
-
Погружное оборудование
Наземное оборудование
Типооборудование
тип
установки
Насоса
двигателя
газосепара-тора
кабельной линии
трансформатора
комплектного устройства
комплектной трансформаторной подстанции
УЭЦНМ5А-250-1000
ЭЦНМ5А-250-1000
ПЭДУ63-117В5
ПЭДУ63-117ДВ5
МНГ5А
-
К43.000-06
К43.000-10
ТМПН-100/3-73У1
(УХЛ1)
U=1,61 кВ
КТППН – 100/10-82УХЛ1 на 6(10) кВ
5 ЛТППНКС – 650/10/1,6-85УХЛ1
на 6(10) кВ
УЭЦНМ5А-250-1400
ЭЦНМ5А-250-1400
ПЭДУС90-117В5
ПЭДУС90-117ДВ5
МНГ5А
-
К43.000-50
К43.000-56
ТМПН-100/3-73У1
(УХЛ1)
U=2,05 кВ
ШГС5805-
49А3У1
КТППН-250/10-82УХЛ1
на 6(10) кВ
5ЛТППНКС – 125/10/2,4-85УХЛ2
на 6(10) кВ
УЭЦНМК5А-250-1400
ЭЦНМ5А-250-1400
ПЭДУСК90-117В5
ПЭДУСК90-117ДВ5
МНГК5А
-
К43.000-50
К43.000-56
УЭЦНМ5А-250-1700
ЭЦНМ5А-250-1700
ПЭДУС90-117В5
ПЭДУС90-117ДВ5
МНГ5А
-
К43.000-110
К43.000-112
УЭЦНМК5А-250-1700
ЭЦНМК5А-250-1700
ПЭДУС90-117В5
ПЭДУСК90-117ДВ5
МНГК5А
-
К43.000-110
К43.000-112
УЭЦНМ5А-400-950
ЭЦНМ5А-400-950
ПЭДУС90-117В5
ПЭДУС90-117ДВ5
МНГ5А
-
К43.000-41
К43.000-47
УЭЦНМК5А-400-950
ЭЦНМК5А-400-950
ПЭДУСК90-117В5
ПЭДУСК90-117ДВ5
МНГК5А
-
К43.000-41
К43.000-47
УЭЦНМ5А-400-1250
ЭЦНМ5А-400-1250
ПЭДУ63-117В5
ПЭДУ63-117ДВ5
МНГ5А
-
К43.000-53
К43.000-59
УЭЦНМК5А-400-1250
ЭЦНМК5А-400-1250
ПЭДУС125-117В5
ПЭДУС125-117ДВ5
МНГК5А
-
К43.000-53
К43.000-59
УЭЦНМ5А-500-800
ЭЦНМ5А-500-800
ПЭДУС125-117В5
ПЭДУС125-117ДВ5
К43.000-45
УЭЦНМ5А-500-1000
ЭЦНМ5А-500-1000
ПЭДУС125-117В5
ПЭДУС125-117ДВ5
К43.000-51
-
Погружное оборудование
Наземное оборудование
Типооборудование
тип
установки
насоса
двигателя
газосепара-тора
кабельной линии
Трансформатора
комплектного устройства
комплектной трансформаторной подстанции
УЭЦНМ6-250-1400
ЭЦНМ6-250-1400
ПЭДУ90-123В5
ПЭДУ90-123ДВ5
1МНГ6
-
К43.000-50
К43.000-56
КТППН – 250/10-82УХЛ1 на 6(10) кВ
1250/10/2,4-85УХЛ1
УЭЦНМ6-250-1600
ЭЦНМ6-250-1600
ПЭДУ90-123В5
ПЭДУ90-123ДВ5
1МНГ6
-
К43.000-56
К43.000-61
На 6(10) кв
УЭЦНМ6-500-1150
ЭЦНМ6-500-1150
ПЭДУС180-117В5
ПЭДУС180-117ДВ5
1МНГ6
-
К43.000-91
К43.000-97
ТМПН-400/6-У1-
(УХЛ1)
320кВА
КУПНА83-29
А2У1
КУПНА700-
79А1ХЛ1
УЭЦНМ6-800-700
ЭЦНМ6-800-700
ПЭДУС125-117В5
ПЭДУС125-117ДВ5
-
К43.000-35
-
КТППН-250/10-82УХЛ1 на 6(10) кВ
5 ЛТППНКС – 1250/10/2,4-85УХЛ1
на 6(10) кВ
УЭЦНМ6-800-1000
ЭЦНМ6-800-1000
ПЭДУС180-130В5
ПЭДУС180-130ДВ5
-
К43.000-97
ТМПН-400/6-У1-
(УХЛ1)
320кВА
УЭЦНМ6-1000-900
ЭЦНМ6-1000-900
ПЭДУС250-130В5
ПЭДУС250-130ДВ5
-
К43.000-92
ТМПН-400/6-У1-
(УХЛ1)
400кВА
-
Погружное оборудование
Наземное оборудование
Типооборудование
тип
установки
насоса
двигателя
газосепара-тора
кабельной линии
Трансформатора
комплектного устройства
комплектной трансформаторной подстанции
УЭЦНМ5-125-1200
ЭЦНМ5-125-1200
ПЭД45-117ЛДВ5
ПЭД45-117ЛГВ5
ПЭДУ45-103В5
ПЭДУ45-103ДВ5
1МНГ5
-
К43.000-10
К43.000-14
КТППН – 250/10-82УХЛ1 на 6(10) кВ
1250/10/2,4-85УХЛ1
УЭЦНМК5-125-1200
ЭЦНМК5-125-1200
ПЭДУ45-103В5
ПЭДУ45-103ДВ5
1МНГК5
-
К43.000-10
К43.000-14
На 6(10) кв
УЭЦНМ5-125-1300
ЭЦНМ5-125-1300
ПЭД45-117ЛДВ5
ПЭД45-117ЛГВ5
ПЭДУ45-103В5
ПЭДУ45-103ДВ5
1МНГ5
-
К43.000-14
К43.000-18
ТМПН-400/6-У1-
(УХЛ1)
320кВА
КУПНА83-29
А2У1
КУПНА700-
79А1ХЛ1
УЭЦНМК5-125-1300
ЭЦНМК5-125-1300
ПЭДУ45-103В5
ПЭДУ45-103ДВ5
1МНГК5
-
К43.000-14
К43.000-18
-
КТППН-250/10-82УХЛ1 на 6(10) кВ
5 ЛТППНКС – 1250/10/2,4-85УХЛ1
на 6(10) кВ
УЭЦНМ5-1250-1800
ЭЦНМ5-125-1800
ПЭДУС63-103В5
ПЭДУС63-103ДВ5
1МНГ5
-
К43.000-97
ТМПН-400/6-У1-
(УХЛ1)
320кВА
УЭЦНМ5-200-800
ЭЦНМ5-200-800
ПЭДУ45-103В5
ПЭДУ45-103ДВ5
1МНГ5
-
К43.000-92
ТМПН-400/6-У1-
(УХЛ1)
400кВА
УЭЦНМ5-200-1400
ЭЦНМ5-200-1400
ПЭДУС90-103В5
ПЭДУС90-103ДВ5
1МНГ5
-
К43.000-92
ТМПН-400/6-У1-
(УХЛ1)
400кВА
УЭЦНМ5А-160-14500
ЭЦНМ5А-160-1450
ПЭДУ63-117В5
ПЭДУ63-117ДВ5
МНГА5
-
К43.000-92
ТМПН-400/6-У1-
(УХЛ1)
400кВА
УЭЦНМ5А-160-17500
ЭЦНМ5А-160-1750
ПЭДУС90-117В5
ПЭДУС90-117ДВ5
МНГА5
-
К43.000-92
ТМПН-400/6-У1-
(УХЛ1)
400кВА
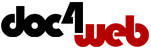
Нравится материал? Поддержи автора!
Ещё документы из категории геология :
Чтобы скачать документ, порекомендуйте, пожалуйста, его своим друзьям в любой соц. сети.
После чего кнопка «СКАЧАТЬ» станет доступной!
Кнопочки находятся чуть ниже. Спасибо!
Кнопки:
Скачать документ