Автоматизация процесса поперечной резки электротехнической стали
ВВЕДЕНИЕ
Под гидроприводом понимают совокупность устройств (в число которых входит один или несколько объемных гидродвигателей), предназначенную для приведения в движение механизмов и машин посредством рабочей жидкости под давлением. В качестве рабочей жидкости в станочных гидроприводах используется минеральное масло.
Широкое применение гидроприводов определяется рядом их существенных преимуществ перед другими типами приводов и, прежде всего возможностью получения больших усилий и мощностей при ограниченных размерах гидродвигателей. Гидроприводы обеспечивают широкий диапазон бесступенчатого регулирования скорости, возможность работ в динамических режимах с требуемым качеством переходных процессов, защиту системы от перегрузки и точный контроль действующих усилий.
К основным преимуществам гидропривода следует отнести также высокое значение коэффициента полезного действия, повышенную жесткость и долговечность.
Гидроприводы имеют и недостатки, которые ограничивают их использование в станкостроении. Это потери на трение и утечки, снижающие коэффициент полезного действия гидропривода и вызывающие разогрев рабочей жидкости. Внутренние утечки через зазоры подвижных элементов в допустимых пределах полезны, поскольку улучшают условия смазывания и теплоотвода, в то время как наружные утечки приводят к повышенному расходу масла, загрязнению гидросистемы и рабочего места. Необходимость применения фильтров тонкой очистки для обеспечения надежности гидроприводов повышает стоимость последних и усложняет техническое обслуживание.
Наиболее эффективно применение гидропривода в станках с возвратно-поступательным движением рабочего органа, в высокоавтоматизированных многоцелевых станках и т.п. Гидроприводы используются в механизмах подач, смены инструмента, зажима, копировальных суппортах, уравновешивания и т.д. гидроприводами оснащаются более трети выпускаемых в мире промышленных роботов.
Современное развитие производства технической продукции требует совершенствования её технология изготовления, модернизации технологического оборудования и повышения её качества.
Поэтому вопросы разработки высокоэффективного технологического оборудования резки тонколистовой рулонной стали являются актуальной.
Целью дипломного проектирования является автоматизация процесса поперечной резки электротехнической стали 0,1…0,6х800мм.
Дипломный проект выполняется по заданию ООО НЭВЗ
1. Анализ и обоснование выбранной конструкции
1.1 Обзор аналогов автоматической линии поперечной резки рулонной стали
Линия автоматизированная для поперечной разки рулонной стали предназначена для качественной правки тонколистового материала и поперечного раскроя рулона на карты (листы).
В состав линии входят:
Устройство разматывающие.
Машина правильная.
Подача валковая.
Ножницы специальные.
Устройство стапелирующие.
Линия автоматизированная для поперечной резки электротехнической стали, включая в себя отдельные машины, устройства и комплекты, указанные выше, предназначена для автоматической правки в пределах заданных величин поперечного раскроя рулонного материала на листы требуемой длины.
Операции, предшествующие технологическому процессу на линии:
Транспортировка рулона к линии внутренним транспортом.
Предварительная распаковка рулона.
Укладка распакованного рулона цеховым краном на платформу подъемника разматывающего устройства.
Описание технологического процесса получения листовой карты.
В устройстве разматывающем, подъем рулона и перемещение на уровень оси шпинделя осуществляется гидроподъемником. Перемещение устройства на позицию загрузки рулона и обратно на рабочую позицию размотки осуществляется гидроцилиндром. Фиксация рулона на поверхности шпинделя осуществляется разжимом секторов гидроцилиндром зажима. Прижим ленты и предохранение от самопроизвольного раскручивания осуществляется роликом прижимным с приводом от гидроцилиндра через систему рычагов. Вращение шпинделя при заправке и торможение в процессе работы осуществляется гидромотором через зубчатое зацепление.
В машине правильной, предварительное устранение кривизны листа, полученной в намотанном рулоне, осуществляется устройством натяжным. Вытягивание ленты и её правка осуществляется валками рамы правильной и механизма правки, имеющих общий привод, состоящий из электродвигателя и редуктора.
Правка листа в ленте осуществляется при помощи изменения перекрытия валков, путём поворота эксцентрикового вала, перемещающего раму правильную. При поднятии вверх величина перекрытия правильных валков уменьшается, что можно визуально отслеживать по шкале, установленной на лицевой стороне машины, и наоборот.
Прижатие правильных валков верхнего ряда и раскрытие правильной рамы осуществляется гидроцилиндрами и тягами привода рамы.
В подаче валковой осуществляется периодическое перемещение ленточного материала на величину шага, в зависимости от заданной ей программы системой управления линией. Перемещение ленты осуществляется при помощи привода и редуктора и валков подающих. Одновременно подаваемая на шаг лента при необходимости может дополнительно правиться при помощи группы валков правильных. Боковое смещение свободной полосы ограничивается роликами направляющими ленту. Лента на период резки карты останавливается, её избыток собирается в компенсаторе петлевом, работа которого осуществляется от гидроцилиндров.
Длина карты определяется роликом отсчетным через систему управления линией.
В ножницах специальных осуществляется прижим полосы листа и периодическая рубка по команде системы управления, транспортировка отрезанной карты транспортёром до стапелера.
Привод ножниц осуществляется от электродвигателя, ременную передачу, шкив – маховик и муфту – тормоз.
Верхняя балка ножевая перед каждым резом в верхнем положении удерживается при помощи двух уравновешивателей. Периодической работой ножниц управляют выключатели бесконтактные, работающие от экранов.
Привод транспортёра осуществляется от электродвигателя рольганга стапелера.
Для периодической смазки трущихся частей ножниц использована импульсивная система смазки с собственным электроприводом.
В устройстве стапелирующем карта, нарезанная из ленты, попадает на рольганг, имеющий общий приводной электродвигатель с ленточным транспортёром ножниц специальных. Для лучшего контакта карты с роликами применяются наддув воздухом сверху от вентилятора. Часть воздуха этого вентилятора используется на создание воздушной подушки под картой при укладке с стопу. Распределение объемов воздуха осуществляется распределителем воздуха. Кроме воздушного прижима карты к рольгангу предусмотрен прижимной ролик с приводом имеющий три скорости: равную скорости рольганга, замедляющую и быстрого противовключения. Прижимной ролик имеет пневмоприжим двумя цилиндрами. Карта, прошедшая рольганг, укладывается в стопу на тележку между стенками механизма боковых ограничителей и упором передним. По мере роста высоты стопы тележка опускается вниз при помощи подъемников, а затем выкладывается за счет собственного привода по рельсам для разгрузки стопы заготовок краном.
Аналогом является автоматическая линия поперечной резки рулонной стали выпускаемая ООО «Аркада-Инжиниринг» г. Смоленск.
Рисунок 1. Схема автоматической линии поперечной резки рулонной стали.
Обозначения на схеме:
1 Разматыватель
2 Устройство загрузочное
3 Устройство гидравлическое
4 Кромкоотгибатель
5 Устройство базирующее
6 Машина правильная
7 Петлеобразователь
8 Устройство электрическое
9 Устройство подающее
10 Узел счётчика
11 Ножницы поперечной резки
12 Стол приёмный
Рисунок 2. Общий вид автоматической линии поперечной резки рулонной стали.
1.2 Анализ валковой подачи
Известны аналогичные подачи, выпускаемые зарубежными фирмами например: фирма «Шулер» Германия, линия поперечной резки рулонной стали 0,65..2х1600мм в которую входит валковая подача эксплуатируется на ВАЗ г. Тольятти.
Фирма «Комацу» Япония поставила на КАМАЗ г. Набережные челны автоматическую линию для поперечной резки рулонной стали 0,8..4х2000 в которую также входит валковая подача.
Азовское ОАО «Донпессмаш» с 1979г. изготавливает валковую подачу модели ВП-41 (по типу валковой подачи фирмы «Шулер») для ленты 0,6..2х1600. Данные подачи входят в состав линии поперечной резки рулонной стали модели Л116, которые эксплуатируются «Комбайновый завод» г. Тула, Красноярский комбайновый завод и др.
Конструкция и компоновка механизмов разрабатываемой подачи валковой, в основном принята аналогичной подаче валковой модели ВП-41 за исключением следующих особенностей:
в разрабатываемом проекте изменены диаметры правильных и подающих валков.
изменён шаг валков для обеспечения качественной правки.
изменена конструкция мерительного ролика и применен серийно выпускаемый датчик ВЕ-178
Все составные части и отдельные детали подачи не представляют затруднений при изготовлении их на машиностроительных заводах.
Аналогичная валковая подача использовалась в автоматической линии поперечной резки рулонной стали 0,6..1.5х1250. Листы стали изготовленные этой линией использовались для производства холодильников, стиральных машин. Электротехническая сталь используемая в моей автоматической линии предназначена для производства трансформаторов.
В состав валковой подачи, входящей в автоматическую линию поперечной резки рулонной стали 0,6..1.5х1250, входят следующие узлы и механизмы:
Станина.
Привод.
Тормоз.
2 гидроцилиндра.
Мерительные ролики.
Конечный выключатель.
Валки правильные верхние.
Валок подающий.
Валки нижние.
Прижим.
Петлевой компенсатор.
Направляющие ленты.
Процесс работы валковой подачи происходит следующим образом:
Перемещение ленточного материала осуществляется при помощи пары подающих валков.
Вращение этих валков осуществляется от двух индивидуальных электродвигателей асинхронных через зубчатые шестерни и карданный вал. Перемещение ленты на шаг от двигателя производится по программе заданной системой управления линии. Для затормаживания подающих валков предусмотрены колодочные тормоза.
Под нижним подающим валком и над верхним подающим валком
установлены охватывающие их с двух сторон опорные ролики регулируемые при помощи резьбовых штоков и винтов. По длине этих валков расположено по пять комплектов опорных роликов, которые воспринимают нагрузку при зажатии ленты между верхним и нижним валками и не допускают большого прогиба этих валков.
Два верхних валка и три нижних предназначены для правки ленты, также как и подающие валки они опираются на регулируемые опорные ролики. Каждый верхний правильный валок установлен на траверсе, которые размещены в направляющих станины. Траверсы соединены со штоками гидроцилиндров, при помощи которых верхние валки перемещаются вверх и вниз. В нижнем положении траверсы опираются на регулируемые по высоте штыри, которые опираются на клинья, регулируемые при помощи винтовой передачи. Этой регулировкой выставляется зазор между верхними и нижними валками правильными.
Прижим ленты балкой к валку при помощи пружины обеспечивает предохранение ленты от сползания под собственным весом. Подъем прижимной балки, т.е. освобождение ленты, осуществляется гидроцилиндрами.
Мерительные ролики вращаются от перемещения ленты, зажатой при помощи гидроцилиндра. Нижний мерительный ролик соединён с датчиком, который через каждые 0,3мм пройденного пути выдаёт сигнал в систему управления линией.
Горизонтальные ролики служат для поддержания ленты на уровне подачи, а ролики для направления её в петлевом компенсаторе при движении ленты от машины правильной. От смещения ленты относительно оси подачи предусмотрены две пары вертикальных роликов, которые регулируются в поперечном направлении в зависимости от ширины ленты вращением ходовых винтов при помощи маховиков.
2. РАСЧЕТНО-КОНСТРУКТОРСКАЯ ЧАСТЬ
2.1 Расчет силовых гидроцилиндров подачи валковой
Выполним расчет гидроцилиндров привода валка подающего, валка правильного и тормоза барабана.
Рабочее давление рц =10 МПа.
Расчет гидроцилиндров валка подающего.
Нагрузка на шток гидроцилиндров привода валка подающего при рабочем ходе составляет Fнм1 = 60 кН.
Ход гидроцилиндров привода валка подающего составляет L1 =0,5 м.
Нагрузка на шток при опускании валка подающего определяется силой вредных сопротивлений:
Fнр1 = 0,2 Fнм1 = 0,260 =12 кН
Для перемещения валка подающего применяем два гидравлических цилиндра. Для того, чтобы их поршни двигались одновременно, штоки гидроцилиндров соединяем механически. Эффективная площадь поршня одного гидроцилиндра:
м2
где м = 0,88 - механический КПД цилиндра.
Диаметр поршня цилиндра:
м
По ГОСТу 12447-80 принимаем стандартное значение диаметра поршня D1 = 0,07 м.
Уточним максимальное рабочее давление в цилиндре:
Па
Диаметр штока гидроцилиндра перемещения валка подающего:
dш1 = 0,5D1 = 0,50,07 = 0,04 м
Рассчитанное значение диаметра штока гидроцилиндра является стандартным по ГОСТу 12447-80.
Давление в штоковой камере цилиндра при реверсе.
Па
Расчет гидроцилиндров перемещения валка правильного.
Нагрузка на шток гидроцилиндров перемещения валка правильного при рабочем ходе составляет Fнм2 = 75 кН.
Ход гидроцилиндров перемещения валка правильного составляет
L2 =0,5 м.
Нагрузка на шток при реверсе определяется силой вредных сопротивлений:
Fнр2 = 0,2 Fнм2 = 0,275 = 15 кН
Для перемещения валка правильного применяем два гидравлических цилиндра. Для того чтобы их поршни двигались одновременно, штоки гидроцилиндров соединяем механически.
Эффективная площадь поршня одного гидроцилиндра:
м2
Диаметр поршня цилиндра:
м
По ГОСТу 12447-80 принимаем стандартное значение диаметра поршня D2 = 0,08 м.
Уточним максимальное рабочее давление в одном цилиндре:
Па
Диаметр штока гидроцилиндра перемещения валка правильного:
dш2 = 0,5D2 = 0,50,08 = 0,04 м
Рассчитанное значение диаметра штока является стандартным по ГОСТу 12447-80.
Давление в штоковой камере цилиндра при реверсе:
Па
Расчет гидроцилиндров привода тормоза валка.
Привод тормоза валка состоит из двух гидравлических цилиндров одностороннего действие. Давление масла используется в них только при отводе тормозных колодок от барабана. В режиме торможения прижим тормозных колодок к барабану и перемещение поршней гидроцилиндров осуществляется пружинами.
Для обеспечения жесткости при перемещениях тормозных колодок диаметр штока гидроцилиндров привода тормоза валка принимаем по ГОСТу 12447-80 dш3 =0,025 м.
Ход гидроцилиндров привода тормоза валка составляет L3 =0,05 м.
Нагрузка на шток гидроцилиндра при отводе тормозных колодок зависит от силы упругости пружины и сил трения. Для расчета принимаем Fнр3 = 1 кН.
Диаметр поршня гидроцилиндра привода тормоза:
м
Так как при работе тормоза валков на поршень действует сжатая пружина, то по ГОСТу 12447-80 принимаем D3 = 0,032 м.
авление в штоковой камере цилиндра при отводе колодок от барабана:
Па
В справочной литературе нет стандартных гидроцилиндров на давление питания 10 МПа с диаметрами поршня, штока и ходом поршня как требуется для привода механизмов подачи валковой. Поэтому для ее гидропривода гидроцилиндры должны быть изготовлены.
2.2 Расчет нагрузок на привод валков подающих и выбор гидромотора
Перемещение ленты валковой подачи происходит с помощью валков подающих. Привод валков подающих в валковой подаче разработанной ООО «Спецпроект» осуществляется двумя электрическими двигателями через двухступенчатый редуктор. В дипломной работе предлагается заменить электрический привод валков подающих на гидравлический. Для привода валков используем один гидромотор.
Для выбора конкретной модели гидромотора надо знать момент нагрузки и частоту вращения его вала.
Момент на валу гидромотора:
,
где М1 – крутящий момент на подающих валках при перемещении и правке полосы наибольших размеров;
– крутящий момент от инерции вращающихся масс на валу гидромотора;
iр = 1 – передаточное число редуктора;
= 0,9 – КПД редуктора.
Крутящий момент на подающих валках при перемещении и правке полосы:
,
где Fп – наибольшее потребное тянущее усилие на подающих валках;
r = 0,08 м – радиус подающих валков.
Наибольшее потребное тянущее усилие на подающих валках:
,
где Fпр – усилие, необходимое для протягивания ленты через валки правильного устройства;
Qп - усилие, необходимое для преодоления инерции ленты.
Усилие, необходимое для протягивания ленты через валки правильного устройства:
,
где dв = 0,060 м – диаметр правильного валка;
- суммарный момент нагрузки на подающих валках.
Суммарный момент нагрузки:
,
где М1 – момент, затрачиваемый на упругую и пластическую деформацию материала листа;
М2 – момент сил трения качения валков по ленте;
М3 – момент сил трения в опорах валков.
Момент, затрачиваемый на упругую и пластическую деформацию материала прокатываемого листа:
,
где Ми2 – момент, затрачиваемый на пластическую деформацию под 2-м и 3-м валком;
Ми4 – момент, затрачиваемый на упругую деформацию под 4-м и 3-м валком;
пл – минимально допустимый радиус кривизны при пластическом изгибе;
упр – минимально допустимый радиус кривизны при упругом изгибе.
Момент, затрачиваемый на пластическую деформацию:
,
где s = 260106 Па – предел текучести материала листа;
s – пластический момент сопротивления.
м3 ,
где b = 0,08 м – максимальная ширина ленты;
h = 0,0006 м – максимальная толщина ленты.
Момент, затрачиваемый на пластическую деформацию:
Нм
Момент, затрачиваемый на упругую деформацию:
,
где W – упругий момент сопротивления.
м3
Рассчитаем момент, затрачиваемый на упругую деформацию:
Нм
Минимально допустимый радиус кривизны при пластическом изгибе:
,
где Е = 2,11011 Па – модуль упругости материала листа;
I – момент инерции сечения листа;
Рассчитаем значения момента инерции сечения листа и изгибающего момента:
м4 ,
Рассчитаем минимально допустимый радиус кривизны при пластическом изгибе:
м
Рассчитаем минимально допустимый радиус кривизны при упругом изгибе:
м
Рассчитаем значение момента, затрачиваемого на упругую и пластическую деформацию материала прокатываемого листа:
Нм
Момент сил трения качения правильных валков по ленте:
,
где - суммарное давление листа на правильные валки;
т = 0,0008 м – плечо трения качения с учетом трения скольжения для листовой стали и полосового материала.
Рассчитаем значения давления листа на каждый из роликов правильного устройства:
- давление ленты на первый валок
Н ,
- давление ленты на второй валок
Н ,
- давление ленты на третий валок
Н ,
- давление ленты на четвертый валок
Н ,
- давление ленты на пятый валок
Н ,
где t = 0,08 м – расстояние между осями правильных валков.
Рассчитаем численное значение момента сил трения качения правильных валков по ленте:
Нм
Момент сил трения в опорах валков:
,
где d = 0,04 м – диаметр дорожки подшипника качения;
f = 0,01 – коэффициент трения в подшипниках качения опор правильных валков.
Рассчитаем численное значение момента сил трения в опорах валков:
Нм
Рассчитаем усилие, необходимое для протягивания ленты через валки правильного устройства:
Н
Усилие, необходимое для преодоления инерции ленты рассчитаем по формуле:
,
где G3 = 370 Н – сила тяжести половины петли;
G10 = 1470 Н – сила тяжести ленты, лежащей на горизонтальном участке длиной 10 м;
f = 0,1 – коэффициент трения;
Fин – усилие инерции.
,
где g = 9,8 м/с2 – ускорение свободного падения;
а – ускорение подачи.
м/с2
Рассчитаем численные значения усилия инерции и усилия, необходимого для преодоления инерции ленты:
Н,
Н
Рассчитаем наибольшее потребное тянущее усилие на подающих валках:
Н
Рассчитаем крутящий момент на подающих валках при перемещении и правке полосы:
Нм
Крутящий момент от инерции вращающихся масс на валу гидромотора определяется по формуле:
,
где Iд.в.м. – момент инерции вращающихся масс, приведенный к валу гидромотора;
- угловое ускорение на валу гидромотора.
Момент инерции вращающихся масс, приведенный к валу гидромотора определяется формулой:
где I1 = 0,13 кгм2 – момент инерции подвижных частей гидромотора;
т1, т2, т3, т4, т5, т6, т7 – масса муфты, шестерни, зубчатого колеса, карданов, барабана тормоза и подающих валков;
D2 , D3 , D4 , D5 , D6 , D7 – диаметры муфты, делительных окружностей шестерни и зубчатого колеса, карданных валов, барабанов тормоза и подающих валков.
Рассчитаем численное значение момента инерции вращающихся масс, приведенный к валу гидромотора
кгм2
Рассчитаем численное значение углового ускорения на валу гидромотора:
рад/с2
Тогда крутящий момент от инерции вращающихся масс на валу гидромотора составит:
Нм
Рассчитаем момент нагрузки на валу гидромотора:
Нм
Рассчитаем число оборотов подающих валков:
,
где vнаиб = 1 об/с (60 об/мин) наибольшая паспортная скорость подачи ленты;
D = 0,139 м – диаметр подающих роликов.
об/с
Число оборотов гидромотора:
об/с (120 об/мин)
Расчеты показали, что для привода подающих валков подачи валковой необходим гидромотор, обеспечивающий момент Мсопр = 328,6 Нм и частоту вращения поб = 2 об/с (120 об/мин).
Этим требованиям отвечает высокомоментный радиально-поршневой гидромотор типа МР-0,25/10 с параметрами:
Рабочий объем - 250 см3.
Номинальный вращающий момент - 380 Нм.
Номинальное давление - 10 МПа.
Максимальное давление - 12 МПа.
Минимальная частота вращения – 8 об/мин.
Максимальная частота вращения – 240 об/мин.
Максимальный расход - 65 л/мин.
КПД:
объемный - 0,94.
полный - 0,89.
Мощность - 9,3 кВт.
Момент инерции - 0,13 кгм2.
Расчетная долговечность - 5000 ч.
Масса - 70 кг.
Рассчитаем давление перед гидромотором.
Па
2.4 Расчет параметров и выбор насоса
По скоростям перемещения гидроцилиндров и частоте вращения гидромотора подачи валковой определим требуемые расходы в напорной и сливной гидролиниях.
Гидроцилиндры перемещения валка подающего.
Максимальная скорость перемещения при рабочем ходе
Vраб1 = 0,04 м/с.
Максимальная скорость перемещения при реверсе Vрев1 = 0,04 м/с.
Рабочий ход:
- напорная линия
м3/с
- сливная линия
м3/с
Реверс:
- напорная линия
м3/с
- сливная линия
м3/с
Гидроцилиндры перемещения валка правильного.
Максимальная скорость перемещения при рабочем ходе
Vраб2 = 0,05 м/с.
Максимальная скорость перемещения при реверсе Vрев2 = 0,05 м/с.
Рабочий ход:
- напорная линия
м3/с
- сливная линия
м3/с
Реверс:
- напорная линия
м3/с
- сливная линия
м3/с
Гидроцилиндры тормоза валка.
Максимальная скорость перемещения при рабочем ходе Vраб3 = 0,1 м/с.
Отвод тормозных цилиндров:
- напорная линия
м3/с
Гидромотор привода валков подающих.
Частота вращения при рабочем ходе nраб = 120 об/мин.
Рабочий ход:
Напорная линия.
м3/с
Расчет и выбор насоса проводим по максимальному расходу.
Максимальный из рассчитанных расходов будем в гидролинии гидромотора привода валков подающих.
Qраб.н4 = 5,31910-4 м3/с.
Найдем подачу и давление в линии гидромотора привода валков подающих.
Подачу (производительность) насоса рассчитываем по уравнению:
,
где - суммарные потери в гидроаппаратуре;
Qкл - расход масла через предохранительный клапан, необходимый для обеспечения устойчивой работы привода. Qкл=3-5 л/мин.
м3/с
Объемные потери в гидроаппаратах определяются по уравнению:
Qн.га = r га i р ц i
где r га i - удельная утечка (ориентировочно для гидроаппаратуры r га = 0.017 см3/(МПа с), для гидромотора r м = 0,8 – 1,2 см3/(МПа с));
р м - максимальное рабочее давление в гидромоторе.
В гидролинии, соединяющей насос с гидромотором привода правильных валков и механизма правки установлены обратный клапан, фильтр и гидрораспределитель.
м3/с
Потребное наибольшее давление, развиваемое насосом, рассчитывают по уравнению:
,
где - суммарные потери давления в гидроаппаратуре;
- суммарные потери давления в трубопроводе;
рпр - противодавление на сливе гидромотора рпр = 0,3 – 0,8 МПа.
Потери давления в проточной части гидроаппаратов принимаем из справочной литературы [3]: для обратных клапанов - рн.кл = 0,05 МПа, для распределителя - рн.р = 0,2 МПа, для фильтра рн.ф = 0,15 МПа.
Суммарные потери давления в гидролиниях на этом этапе расчета
принимаем ориентировочно равным (0,1-0,2) .
Па
Мощность источника питания
N = Qн рн = 6,06210-4 9,773106 = 5,9 103 Вт
В результате расчета получены значения расхода и давления гидростанции Qн = 6,06210-4 м3/с (36,4 л/мин) и рн = 9,773106 (9,77 МПа).
Для гидростанции по выбираем нерегулируемый аксиально-поршневой насос типа НПА 32/32-01 ТУ2-053-1826-87 с параметрами:
Рабочий объем насоса - 32 см3.
Частота вращения:
номинальная - 1450 об/мин.
максимальная - 1800 об/мин.
минимальная - 1000 об/мин.
Номинальная подача - 48 л/мин.
Мощность номинальная, не более - 27 кВт.
Номинальное давление на выходе - 32 МПа.
Давление на входе - 0,02 - 0,15 МПа.
КПД:
объемный - 0,87
полный - 0,7
Средний уровень звука, не более - 68 дБ(А).
Масса, не более - 48 кг.
2.5 Выбор гидроаппаратуры
По величинам расхода и давления выбираем типоразмеры регулирующей, управляющей и вспомогательной аппаратуры, устанавливаемой в напорной и сливной гидролиниях.
Для управления гидроцилиндрами перемещения валка подающего, валка правильного и гидромотора привода валков подающих выбираем распределители типа ВЕ10.574А 41/ОФ. В220-50. НД ГОСТ 24679-81 с параметрами:
Диаметр условного прохода – 10 мм.
Расход масла:
номинальный – 33 л/мин.
максимальный – 80 л/мин.
минимальный – 25 л/мин.
Давление:
номинальное – 32 МПа.
в сливной линии, не более – 15 МПа.
Потери давления - 0,25 .
Масса – 3,4 – 6,5 кг.
Для управления гидроцилиндрами отвода тормозных колодок от барабана выбираем распределитель типа ВЕ10.573 41/ОФ. В220-50. НД ГОСТ 24679-81. Он отличается от распределителя ВЕ10.574А 41/ОФ. В220-50. НД только типом гидросхемы. Все остальные характеристики этих распределителей одинаковы.
Для разгрузки гидравлической схемы после остановки выбираем гидрораспределитель типа ВЕ6.542 41/ОФ. В220-50. НД ГОСТ 24679-81 с параметрами:
Диаметр условного прохода – 6 мм.
Расход масла:
номинальный – 16 л/мин.
максимальный – 30 л/мин.
минимальный – 10 л/мин.
Давление:
номинальное – 32 МПа.
в сливной линии, не более – 6 МПа.
Потери давления - 0,15 .
Масса – 1,3 – 2,2 кг.
Регулирование скорости всех гидроцилиндров происходит с помощью регулируемых дросселей с обратными клапанами.
Для регулирования скорости гидроцилиндров перемещения валка подающего и валка правильного по справочнику выбираем сдвоенные гидродроссели с обратным клапаном типа ДКМ 102 ТУ 2-053-1446-79Е с параметрами:
Диаметр условного прохода – 10 мм.
Расход масла: номинальный – 40 л/мин.
максимальный – 60 л/мин.
Номинальное давление – 20 МПа.
Давление: открытия обратного клапана - 0,08 МПа.
в сливной линии, не более – 20 МПа.
Перепад давления при номинальном потоке, не более
через полностью открытый дроссель - 0,4 МПа.
через обратный клапан - 0,55 МПа.
Внутренние утечки при номинальном
авлении через полностью закрытый дроссель - 80 см3/мин.
Масса – 2,1 кг.
Для регулирования скорости отвода гидроцилиндров тормоза валка и регулирования подачи масла в поршневые камеры гидроцилиндров перемещения валка подающего и валка правильного от аккумуляторов по авочнику выбираем сдвоенные гидродроссели с обратным клапаном типа ДКМ 6/3 ТУ 2-053-1397-78Е с параметрами:
Диаметр условного прохода – 6 мм.
Расход масла: номинальный – 12,5 л/мин.
максимальный – 30 л/мин.
Номинальное давление – 32 МПа.
Давление: открытия обратного клапана - 0,15 МПа.
в сливной линии, не более – 32 МПа.
Перепад давления при номинальном потоке, не более
через полностью открытый дроссель - 0,15 МПа.
через обратный клапан - 0,25 МПа.
Внутренние утечки при номинальном
давлении через полностью закрытый дроссель - 300 см3/мин.
Масса – 1,3 кг.
Для создания потока масла только в одном направлении выбираем по справочнику обратный клапан типа КОМ-102 ТУ2-053-1533-80Е с параметрами:
Диаметр условного прохода – 10 мм.
Давление: номинальное – 20 МПа.
открытие клапана – 0,05 МПа.
Расход масла: номинальный – 40 л/мин.
максимальный – 70 л/мин.
Внутренние утечки в сопряжении клапан-седло, не более – 0,5 см3/мин.
Перепад давления при номинальном потоке, не более – 0,3 МПа
Масса – 1,65 кг.
Для установки в линии слива гидромотора выбираем по справочнику клапан давления типа КЕМ 102-2 1 УХЛ 4 ТУ 2-053-1679-84Е с параметрами:
Диаметр условного прохода – 10 мм.
Давление настройки – 0,6-7 МПа.
Внутренние утечки, не более - 65 см3/мин.
Давление на входе: номинальное – 20 МПа.
максимальное – 23 МПа.
Расход масла: номинальный – 40 л/мин.
минимальный – 1 л/мин.
Номинальный перепад давлений – 0,5 МПа.
Масса, не более – 3,3 кг.
Для защиты линии нагнетания от перегрузки выбираем по справочнику предохранительный клапан непрямого действия типа 10-20-1-132 ТУ 2-053-1748-85 с параметрами:
Диаметр условного прохода – 10 мм.
Расход масла: номинальный – 40 л/мин.
максимальный – 56 л/мин.
минимальный – 3 л/мин.
Суммарные утечки, не более – 200 см3/мин.
Давление настройки – 1-20 МПа.
Максимальное давление – 25 МПа.
Установленный ресурс - 2400 час.
Для очистки масла в линии нагнетания выбираем по справочнику фильтр напорный типа 20-25-КВ ГОСТ 16026-80 с параметрами:
Диаметр условного прохода – 20 мм.
Номинальный расход – 63 л/мин.
Номинальный перепад давлений – 0,12 МПа.
Номинальное давление – 20 МПа.
Номинальная тонкость фильтрации – 25 мкм.
Перепад давлений: срабатывания сигнализатора – 0,3 0,02 МПа.
открытия перепускного клапана – 0,360,03 МПа.
Масса – 6,8 кг.
очистки масла в линии слива выбираем по справочнику фильтр типа с параметрами:
Диаметр условного прохода – 32 мм.
Номинальный расход – 100 л/мин.
Номинальная тонкость фильтрации – 25 мкм.
Номинальное давление – 0,63 МПа.
Перепад давлений: номинальный – 0,1 МПа.
срабатывания сигнализатора – 0,3 0,03 МПа.
открытия перепускного клапана – 0,380,03 МПа.
Масса – 4,5 кг.
2.6 Расчет параметров и выбор сортамента гидролиний
Параметры всасывающих, напорных, сливных и управляющих гидролиний определяются по максимальному расходу, давление, скорости движения потока на рассчитываемом участке магистрали.
Максимальный расход в гидравлической системе подачи валковой будет в гидролиниях гидромотора привода валков подающих.
Диаметр гидролинии определяется выражением:
,
где скорость потока жидкости рекомендуется принимать
- для всасывающих линий vжв = 1,2 м/с.
- для сливных линий vжс = 2 м/с.
- для напорных линий vжн = 5 м/с.
Толщину стенки гидролинии (трубопровода) определяем из выражения
,
где k3 - коэффициент запаса, учитывающий возможные пульсации давления; k3 = 1,3;
рн - давление в гидролинии;
рнв = 0,2 МПа - давление во всасывающей гидролинии;
рнс = 0,2 МПа - давление в сливной гидролинии;
р - допускаемые напряжения на разрыв сечения гидролинии,
р = 500 МПа.
Всасывающая линия
м
м
По сортаменту [ выбираем для линии всасывания стальную бесшовную холоднодеформированную трубу по ГОСТ 8734-75: внутренний диаметр трубопровода dтр в = 0,025м, наружный диаметр трубопровода Dтр в = 0,028 м, толщина стенки трубопровода в = 0,0015 м.
Напорная линия.
м
м
По сортаменту выбираем лля линии нагнетания стальную бесшовную холоднодеформированную трубу по ГОСТ 8734-75: внутренний диаметр трубопровода dтр н = 0,01м, наружный диаметр трубопровода Dтр н = 0,014 м, толщина стенки трубопровода н = 0,002 м.
Сливная линия
Давление на сливе принимаем рсл = 0,2106 МПа.
м
м
По сортаменту выбираем для линии слива стальную бесшовную холоднодеформированную трубу по ГОСТ 8734-75: внутренний диаметр трубопровода dтр с = 0,017м, наружный диаметр трубопровода Dтр с = 0,02 м, толщина стенки трубопровода с = 0,0015 м.
Уточним скорости движения жидкости в гидролиниях гидромотора привода валков подающих:
- всасывающая линия.
м/с
- линия нагнетания
м/с
- линия слива
м/с
Уточним скорости движения жидкости в гидролиниях гидроцилиндров перемещения валка подающего при рабочем ходе:
- линия нагнетания
м/с
- линия слива
м/с
Уточним скорости движения жидкости в гидролиниях гидроцилиндров перемещения валка правильного при рабочем ходе:
- линия нагнетания
м/с
- линия слива
м/с
Уточним скорости движения в гидролиниях гидроцилиндров привода тормоза валка при рабочем ходе:
- линия нагнетания
м/с
2.7 Выбор марки рабочей жидкости
В соответствии с рекомендациями справочной литературы выбираем марку рабочей жидкости - масло индустриальное И-30А ГОСТ 20799-74.
Вязкость кинематическая при 50 0 С = 2810-6 - 3310-6 м2/c
Температура вспышки, не ниже 1900 С.
Температура застывания, не выше - 150 С.
Рекомендуемый предел рабочих температур - -5 - + 600 С.
Плотность при 200 С - 900 кг/м3.
Определим режим движения жидкости во всасывающей, сливной и напорной гидролиниях по числу Рейнольдса.
В линиях гидромотора привода валков подающих.
Во всасывающей гидролинии
< 2300
Режим движения - ламинарный.
В напорной гидролинии
> 2300
Режим движения - турбулентный.
В сливной гидролинии
< 2300
Режим движения – ламинарный.
Определим режимы течения в гидролиниях гидроцилиндров перемещения валка подающего.
В напорной гидролинии
< 2300
Режим движения - ламинарный.
В сливной гидролинии
< 2300
Режим движения – ламинарный.
Определим режимы течения в гидролиниях гидроцилиндров перемещения валка правильного.
В напорной гидролинии
< 2300
Режим движения - ламинарный.
В сливной гидролинии
< 2300
Режим движения – ламинарный.
Определим режимы течения в гидролиниях гидроцилиндров привода тормоза валка.
В напорной гидролинии
< 2300
Режим движения – ламинарный.
2.8 Уточненный расчет потерь давления в гидромагистралях привода
Расчет ведут по уравнениям
;
,
где рн , рс - суммарные потери в напорной и сливной линиях;
рс.га , рс.тр, рс.мс - потери давления от сопротивлений гидроаппаратуры, трения жидкости о стенки гидролинии, местных сопротивлений.
Найдем потери в напорной линии гидромотора привода валков подающих.
В напорной линии гидромотора привода валков подающих установлены обратный клапан, фильтр и распределитель.
Потери давления на обратном клапане рн.ко = 0,3 МПа.
Потери давления на фильтре рн.ф = 0,12 МПа.
Потери давления на распределителе рн.р = 0,25 МПа.
В сливной линии гидромотора установлены распределитель, клапан давления и фильтр.
Потери давления на распределителе рс.р = 0,25 МПа.
Потери давления на клапане давления рс.кд = 0,5 МПа.
Потери давления на фильтре рс.ф = 0,1 МПа.
Потери давления от местных сопротивлений выражаются через суммарный коэффициент местных сопротивлений и скоростной напор.
,
где i - коэффициент местных потерь.
В напорной гидролинии находятся местные сопротивления с коэффициентами сопротивлений [4]: 8 штуцеров - н1 = 0,15, 4 прямоугольных тройника - н2 = 0,1, 13 плавных колен - н3 = 0,12.
В сливной гидролинии установлены: 7 штуцеров - с1 = 0,15, 1 прямоугольный тройник - с2 = 0,1, 8 плавных колен - с3 = 0,12.
vжi - скорость движения потока на участке;
- удельный вес рабочей жидкости ( = 8829 Н/м3).
Линейные потери давления в гидролиниях (за счет трения жидкости о стенки трубопровода) рассчитывают по уравнению
,
где l - длина сливной или напорной гидролинии. Для напорной гидролинии lн = 8 м, для сливной гидролинии lc = 5 м.
- коэффициент сопротивления гидролинии.
Для турбулентного потока
= 0,316Re-0,25
Для ламинарного потока
Потери давления в напорной линии
МПа
Потери давления в сливной гидролинии
МПа
Потери давления в напорной гидролинии гидроцилиндров перемещения валка подающего.
В напорной линии гидроцилиндр гидроцилиндров перемещения валка подающего установлены два обратных клапана, фильтр и распределитель.
Потери давления на обратном клапане рн.ко1 = 0,55 МПа.
В сливной линии гидроцилиндр гидроцилиндров перемещения валка подающего установлены регулируемый дроссель, распределитель и фильтр.
Потери давления на регулируемом дросселе рн.др = 0,4 МПа.
В напорной гидролинии установлены: 10 штуцеров, 3 прямоугольных тройника, 9 плавных колен.
В сливной гидролинии установлены: 7 штуцеров, 1 прямоугольный тройник, 5 плавных колен.
Длина напорной гидролинии lн = 11 м,
для сливной гидролинии lc = 9 м.
Потери давления в напорной линии
МПа
Потери давления в сливной гидролинии
МПа
Приведем потери на сливе к эффективной площади поршня:
МПа
В сливной линии гидроцилиндров перемещения валка правильного установлены регулируемый дроссель, распределитель и фильтр.
В напорной гидролинии установлены: 10 штуцеров, 3 прямоугольных тройника, 11 плавных колен.
В сливной гидролинии установлены: 7 штуцеров, 1 прямоугольный тройник, 9 плавных колен.
В напорной гидролинии установлены: 15 штуцеров, 3 прямоугольных
тройника, 8 плавных колен.
В сливной гидролинии установлены: 5 штуцеров, 4 прямоугольных тройника, 9 плавных колен.
Длина напорной гидролинии lн = 8 м,
для сливной гидролинии lc = 10 м.
Потери давления в напорной линии
МПа
Потери давления в сливной гидролинии
МПа
Приведем потери на сливе к эффективной площади поршня:
МПа
Потери давления в напорной гидролинии гидроцилиндров перемещения тормоза валка.
В напорной линии гидроцилиндров перемещения тормоза валка установлены обратный клапан, фильтр, распределитель и обратный клапан.
В напорной гидролинии установлены: 7 штуцеров, 3 прямоугольных тройника, 15 плавных колен.
Длина напорной гидролинии lн = 15 м.
Потери давления в напорной линии
МПа
2.9 Расчет рабочего давления гидропривода
Рабочее давление гидропривода подачи валковой рассчитывается по максимальному давлению в гидросистеме.
Давление в гидросистеме при рабочем ходе гидроцилиндров перемещения валка подающего:
рр1 = р1 + рн1 + рн.п1 = 6,782+1,709+0,589 = 9,079 МПа
Давление в гидросистеме при рабочем ходе гидроцилиндров перемещения валка правильного:
рр2 = р2 + рн2 + рн.п2 = 8,478+1,691+0,599 = 10,768 МПа
Давление в гидросистеме при вращении гидромотора:
рр4 = р4 + рн = 8,993+1,691 = 10,684 МПа
Максимальное давление будет в гидросистеме при перемещении гидроцилиндров валка правильного.
Определим давление настройки предохранительного клапана насосной установки.
ркп = 1,1 р21 = 1,1 10,768 = 11,845 МПа
2.10 Расчет энергетических характеристик
Гидромотор привода валков подающих.
Мощность гидромотора найдем по формуле:
N4 = p4 Qpаб.н4 = 8,993106 5,31910-4 = 4784 Вт
Мощность, на выходе из гидростанции:
,
где рн - рабочее давление насоса;
Qн - расход насоса;
н = 0,7 - полный КПД насоса.
Вт
При работе подачи валковой вся подача насоса расходуется только при вращении гидромотора. При перемещении гидроцилиндров к гидроцилиндрам поступает только часть подачи насоса, остальное масло сливается через предохранительный клапан.
Мощность, на выходе из гидростанции при перемещении гидроцилиндров:
Вт
Мощность на гидроцилиндрах перемещения валка подающего:
N1 = ( pкп - pн1 - pн.п1) Qpаб.н1 =
= (11,845 –1,709 – 0,589)106 4,02110-4 = 3839 Вт
Мощность на гидроцилиндрах перемещения валка правильного:
N2 = ( pкп - pн2 - pн.п2) Qpаб.н2 =
= (11,845 – 1,691 – 0,599)106 5,02710-4 = 4803 Вт
Мощность на гидроцилиндрах перемещения тормоза валка:
N3 = ( pкп - pн3) Qpаб.н3 =
= (11,845 – 1,318 )106 6,26710-5 = 660 Вт
КПД гидропривода валка подающего:
КПД гидропривода валка правильного:
КПД гидропривода тормоза валка:
КПД гидропривода валков подающих:
Среднецикловой КПД гидропривода.
,
где t1...ti - время рабочего цикла.
Определим время движения гидроцилиндров.
Гидроцилиндры перемещения валка подающего:
с
Гидроцилиндры перемещения валка правильного:
с
Гидроцилиндры перемещения тормоза валка:
с
Время работы гидромотора привода валков подающих t4 = 60 с.
Среднецикловой КПД гидропривода подачи валковой.
Суммарные потери мощности гидропривода за весь рабочий цикл определяются уравнением:
Суммарные потери мощности гидропривода за цикл работы подачи валковой:
кВт
2.11 Обеспечение рационального теплового режима работы гидропривода
Превышение установившейся температуры масла в баке над температурой окружающей среды составляет:
,
где Sб - площадь поверхности бака;
Кт - коэффициент теплопередачи в атмосферу.
Площадь боковой поверхности бака определяется формулой.
,
где Wб - объем масла в баке.
При максимально допускаемом Т = 35 0С необходимый объем масла в баке W определяется выражением
л
Площадь боковой поверхности бака определяется формулой.
м2
Для уменьшения объема маслобака применяем принудительное водяное охлаждение.
Кт = 200 Вт/(м2с) - коэффициент теплопередачи при принудительном водяном охлаждении.
Тогда при Т = 35 0С.
м2
Объем маслобака.
м3 (2.144)
2.12 Расчет мощности приводного электродвигателя насосной установки
Электродвигатель насоса выбирается по эквивалентной мощности:
кВт
По справочнику [9] выбираем электрический двигатель типа 4А 132М4У3.
Техническая характеристика электрического двигателя.
Частота вращения – 1500 об/мин.
Мощность – 11 кВт.
Cos - 0,87.
Ммах / Мн - 2,2.
Мпуск / Мн – 2,0.
3. ДИНАМИЧЕСКИЙ РАСЧЕТ ГИДРОПРИВОДА ПОВОРОТА ВАЛКОВ ПОДАЮЩИХ
3.1 Математическое описание гидропривода поворота валков подающих
Расчет динамики гидравлического привода валков подающих выполним с помощью программы Hydrocad.
В гидравлический привод валков подающих входят гидромотор, регулируемый насос, фильтр с установленным параллельно обратным клапаном, предохранительный клапан, обратный клапан линии нагнетания и трехпозиционный распределитель. На сливе гидромотора установлен клапан давления.
Расчетная схема гидравлического привода в программе Hydrocad показана на рисунке 4
Рисунок 4 – Расчетная гидравлическая схема привода валков подающих
Работа регулируемого насоса в математической модели описана формулами.
Расход на входе в насос:
,
где Рар_рег – параметр регулирования;
qнас – номинальный рабочий объем;
nном – номинальная частота вращения.
Расход на выходе из насоса:
,
где о ном – КПД объемный при номинальном режиме работы;
Рном – номинальное давление насоса;
Р2 – давление на выходе насоса.
Работа фильтра описана формулами.
Площадь проходного отверстия фильтра.
,
где dусл – диаметр условного прохода фильтра.
Расход на входе и выходе фильтра.
Р1 – давление на входе в фильтр;
Р2 – давление на выходе из фильтра.
Работа обратного клапана описана формулами.
Если
Р1 > Р2
То расход на входе и выходе обратного клапана описывается формулой
,
где dусл – диаметр условного прохода обратного клапана;
- коэффициент расхода обратного клапана;
- плотность масла;
Р1 – давление на входе в обратный клапан;
Р2 – давление на выходе из обратного клапана.
Иначе
Q1 = 0
Работа предохранительного клапана описана формулами.
Если
Р1 > Рнастр 106 ,
где Рнастр - давление настройки предохранительного клапана;
Р1 – давление на входе в предохранительный клапан.
То расход на входе и выходе предохранительного клапана описывается формулами.
,
где - коэффициент расхода предохранительного клапана;
dусл – диаметр условного прохода предохранительного клапана;
Р2 – давление на выходе из предохранительного клапана.
Иначе
Q1 = 0
Работа распределителя описана формулами.
Площадь проходного отверстия распределителя.
,
где dусл – диаметр условного прохода распределителя.
Расход через распределитель зависит от его позиции.
Если
Рос = 0,
то
Q1 =0 ;
Q2 =0 ;
Q3 =0 ;
Q4 =0 ;
Если
Рос = 1,
то
;
Q2 = Q1 ;
;
Q4 = - Q3 ;
Если
Рос = 2,
то
;
Q3 = Q1 ;
;
Q4 = - Q2 ;
где Рос - позиция распределителя;
Р1 – давление на входе в распределитель;
Р2 – давление на входе в распределитель;
Р3 – давление на выходе из распределителя;
Р4 – давление на выходе из распределителя
Гидравлический мотор описан формулами.
Мтр1 = Мтр ,
где Мтр - момент трения гидромотора.
Если
и 1=0
То движущий момент меньше момента трения.
,
где Р1 – давление на входе в гидромотор;
Р2 – давление на выходе из гидромотора;
qгм – рабочий объем гидромотора;
м_ном - КПД механический при номинальном режиме;
М1 - вращательный момент гидромотора.
Угловое ускорение гидромотора описано формулой.
,
где Jгм - момент инерции вращающихся масс гидромотора;
- коэффициент вязкого трения;
1 – угловая скорость гидромотора.
Угол поворота гидромотора описан формулой.
d1 = 1
Расход до гидромотора.
Расход после гидромотора.
,
где о_ном - КПД объемный при номинальном режиме;
Рном – номинальное давление гидромотора.
Работа клапана давления описана формулами.
Если
Р3 > Рнастр 106 ,
где Рнастр - давление настройки гидравлически управляемого клапана;
Р3 – давление в линии управления клапана.
То расход до и после клапана определяется формулами.
,
где dусл – диаметр условного прохода гидравлически управляемого клапана;
Р1 – давление на до гидравлически управляемого клапана;
Р2 – давление после гидравлически управляемого клапана.
Иначе клапан закрыт и расход до и после клапана рассчитывается по формуле.
Q1 = 0
Давление в трубопроводах описаны формулами.
Dery[1] := c1 (Q[9] - Q[12]);
Dery[2] := c2 (Q[13] + Q[11]);
Dery[3] := c3 ( - Q[10] + Q[14]);
Dery[4] := c4 (Q[15] - Q[16]);
Dery[5] := c5 (Q[5] + Q[3] - Q[8] - Q[0]);
Dery[6] := c6 ( - Q[4] - Q[2] + Q[7]),
где c1 – с6 – жесткости трубопроводов;
Q[i] - расходы в трубопроводах.
Текст программы расчета динамики гидропривода валков подающих приведен в приложении к дипломному проекту.
3.2 Результаты расчета динамики гидропривода валков подающих
Результаты расчета динамики гидропривода валков подающих показаны на рисунках 5 – 13
На рис. 5 показан расход масла перед гидромотором. На рис 6 показан расход масла после гидромотора. На рис. 7 показано давление масла перед гидромотором. На рис. 8 показано давление масла после гидромотора. На рис. 9 показана угловая скорость гидромотора. На рис. 10 показан угол поворота гидромотора. На рис. 11 показана нагрузка на гидромоторе. На рис. 12 показан расход после насоса. На рис. 13 показано давление после насоса
Q, м3/с
t,c
Рисунок 5 – Расход масла перед гидромотором
Q, м3/с
t,c
Рисунок 6 – Расход масла после гидромотора
Р, Па
t,c
Рисунок 7 – Давление перед гидромотором Р, Па
t,c
Рисунок 8 – Давление после гидромотора , с-1
t,c
Рисунок 9 – Угловая скорость гидромотора , рад
t,c
Рисунок 10 – Угол поворота гидромотора
М, Нм
t,c
Рисунок 11 – Нагрузка на гидромоторе Q, м3/с
t,c
Рисунок 12 – Расход после насоса Р, Па
t,c
Рисунок 13 – Давление после насоса
Максимальная нагрузка на гидромотор при вращении гидромотора привода валков подающих составляет 329 Нм. В динамических расчетах принимаем изменение нагрузки по циклограмме, показанной на рисунке 11. Нагрузка на гидромоторе плавно нарастает за время от 0 с до 2 с от 0 до 329 Нм. В дальнейшем нагрузка остается постоянной – 329 Нм. Через 5 секунд после начала расчета мы моделируем плавное возрастание момента нагрузки до 370 Нм. Такое значение момента сохраняется до 6,5 секунд и затем плавно уменьшается до 329 Нм.
В начале расчета после запуска привода расход насоса начинает расти. Мы устанавливаем такое значение параметра регулирования насоса, чтобы обеспечить заданную частоту вращения 120 об/мин (12,6 с-1). На рисунке 12 видно, что при работе привода расход насоса уменьшается. Часть расхода тратится на утечки в насосе. Они описаны в программе объемным КПД насоса.
Масло от регулируемого насоса поступает через фильтр к обратному клапану. Предохранительный клапан настроен на давление 16 МПа.
Далее масло поступает к распределителю масло и к гидромотору.
Позиция гидрораспределителя в программе задается постоянной.
Давление на выходе из насоса на рисунке 13 и перед гидромотором на рисунке 4 начинает расти. Сначала давления растут быстро до величины 2,5 МПа. В это время гидромотор вращается медленно. Постепенно частота вращения гидромотора увеличивается и рост давления замедляется. Расчетному значению момента нагрузки на валу гидромотора соответствует давление 11 МПа. При увеличении нагрузки давление в линии его питания и после насоса плавно возрастает до 12,2 МПа и затем уменьшается до 11 МПа.
Давление на сливе гидромотора показано на рисунке 8. Его величина определяется настройкой клапана давления и за все время расчета остается практически постоянной и равной 2 МПа.
Предохранительный клапан не открывается, так как он настроен на давление 16 МПа.
Угловая скорость гидромотора на рисунке 6 тесно связана с расходом гидромотора на рисунке 5.
В начале вращения гидромотора нагрузка на него определяется моментом трения в его подвижных частях, который задается в программе. В это время его вал начинает быстро вращаться и угловая скорость достигает 18 с-1. Это вызывает рост расхода до 7,110-4 м3/с, который на какое-то время становится больше подачи насоса 610-4 м3/с. В дальнейшем угловая скорость уменьшается до 12 с-1 и наконец устанавливается на значении 13,2 с-1.
Изменение нагрузки вызывает кратковременное изменение угловой скорости гидромотора. Но потом она становится равной 13,2 с-1.
Расход после гидромотора на рисунке 6 меньше расхода перед гидромотором на рисунке 5. Часть расхода тратится на утечки в моторе. Утечки описаны в программе объемным КПД мотора.
На рисунках 5 – 13 видно, что переходные процессы при разгоне гидромотора привода валков подающих и при изменении нагрузки носит затухающий характер. Это позволяет сделать вывод об устойчивости системы гидропривода валков подающих.
Время выхода гидромотора на установившийся режим работы – 2,1 с.
4. ТЕХНОЛОГИЧЕСКАЯ ЧАСТЬ
4.1 Служебное назначение, конструкция гидравлического цилиндра и технологические требования к нему
Гидравлический цилиндр – гидравлическая машина, предназначенная для преобразования энергии потока рабочей жидкости в энергию движения выходного звена, рабочий процесс которой основан на попеременном заполнении рабочей камеры жидкостью и вытеснении его из рабочей камеры. На рисунке 5.1 показана конструкция гидроцилиндра.
Рисунок 14 – Конструкция гидравлического цилиндра
Гидроцилиндр состоит из: цилиндра (1), плунжера (2), втулки (3,6), кольца (4), кольца фторопластового (5), крышки (7), шайбы (8) и болта (9).
Технические требования к цилиндру: не допускается овальность и конусность цилиндрических поверхностей, их относительное смещение должно составлять не более половины допуска на размер; давление, необходимое для перемещения штока в крайнее правое положение равно 0,5МПа; рабочий ход штока: 700±1мм; рабочее давление изменяется ступенчато от 0,8 до 18МПа.
4.2 Анализ размерной цепи гидравлического цилиндра
Размерная цепь – замкнутый контур, расположенных друг за другом независимых размеров, участвующих в решении поставленных задач. При проектировании технологических процессов, выборе средств и методов измерения возникает необходимость в проведении размерного анализа, с помощью которого достигается правильное соотношение взаимосвязанных размеров и определяются допустимые ошибки (допуски).
На рисунке 15 приведена размерная цепь гидравлического цилиндра.
Рисунок 15 – Размерная цепь гидравлического цилиндра
В таблице 1 приведены результаты расчета звеньев размерной цепи гидравлического цилиндра.
Проверка правильности назначения номинальных размеров осуществляется по формуле:
где А0 – номинальный размер замыкающего звена, мм;
- передаточное отношение составляющих звеньев;
Аi – номинальный размер составляющих звеньев, мм.
Таблица 1 – Результаты расчета размерной цепи гидроцилиндра
№
Номинальный размер А(I)
Передаточное отношение KSI I
Верхнее отклонение ES A(I)
Нижнее отклонение EI A(I)
Допуск TA (I)
Координата середины поля допуска
Ec A(I)
A0
0
-
0.3
0
0.3
0.15
A1
950
1
-0.15
-0.45
0.3
-0.15
A2
960
-1
0
-0.3
0.3
-0.15
Точность замыкающего звена обеспечивается неполной взаимозаменяемостью c корректировкой середины поля допуска 1-го звена на 0.01500мм.
Процент риска расчетный 8.3265 %.
Расчётное значение допуска замыкающего звена соответствует действительным значениям, следовательно, метод неполной взаимозаменяемости обеспечивает требуемую точность сборки гидроцилиндра. Для расчёта размерной цепи применялась программа RCW2. В этой программе необходимо ввести следующие параметры рассчитываемой размерной цепи:
1. Число звеньев.
2. Номинальные размеры каждого звена и их верхние и нижние предельные отклонения.
3. Задать передаточное отношение каждого звена.
4. Выбрать тип производства.
4.3 Определение типа производства плунжера гидравлического цилиндра
Такт выпуска рассчитывается по формуле:
,
где m = 1 – сменность работы;
Wд – годовая программа выпуска деталей;
Fд – действительный годовой фонд времени работы оборудования в часах.
Рассчитаем годовой фонд рабочего времени.
час
где В = 104 дня - количество выходных дней;
П = 8 дней - количество праздничных дней;
С = 8,2 ч - продолжительность смены;
Пр = 8 дней - количество предпраздничных дней;
с = 1 ч - время укорочения смены в предпраздничные дни;
n = 1 - количество рабочих смен в сутки;
Пв = 7 % - потери времени на проведение ремонтов, обслуживание, настройку и подналадку оборудования.
Рассчитаем годовую программу выпуска плунжера гидравлического цилиндра:
где Wпц = 1000 шт – годовой объем выпуска гидроцилиндров;
nд = 1 шт – количество плунжеров, входящих в гидравлический цилиндр;
1 = 10 % - процент деталей, выпускаемых на запасные части;
2 = 10 % - процент деталей, учитывающий выход в брак.
шт
Тогда такт выпуска деталей составит:
мин/шт
Рассчитаем коэффициент серийности по формуле:
где - среднее время выполнения операции на деталях разных наименований (мин/операция)
Принимаем в расчетах: t = 6 мин/операция
Условно и очень приблизительно приняты следующие распределения типов производства в зависимости от :
- поточно-массовое;
- крупносерийное;
- среднесерийное;
- мелкосерийное;
Следовательно, производство принимаем среднесерийным, т.к.
ксер = 16.
4.4 Описание технологического процесса сборки гидравлического цилиндра
При проектировании технологического процесса общей и узловой сборки важное место занимает технический контроль качества производимой продукции. Качество обеспечивается предупреждением и своевременным выявлением брака продукции на всех этапах производственного процесса.
При сборке гидравлического цилиндра проверяют:
- наличие необходимых деталей в собранных соединениях (выполняют осмотром);
- правильность положения сопрягаемых деталей (выполняют осмотром);
- герметичность соединения и плотность прилегания;
- затяжку резьбовых соединений;
- размеры, заданные в сборочном чертеже;
- внешний вид гидравлического цилиндра (отсутствие повреждений деталей, загрязнений и других дефектов, которые могут возникнуть в процессе сборки).
В функцию контроля входит также проверка предписанной последовательности выполнения сборочных переходов.
Выберем вид сборки и форму организационного технологического процесса сборки гидравлического цилиндра.
Выделяют следующие организационные формы технологического процесса сборки:
- Поточная, характерная для сборочных цехов, работающих по крупносерийному и массовому типу производства. Эта сборка обличается высокой степенью непрерывности производственного процесса и широким внедрением автоматизации и механизации.
- не поточная, характерная для сборочных цехов единичного и мелкосерийного типа производства.
В зависимости от конкретных производственных технологических условий сборка может быть:
- стационарной, которая осуществляется без перемещения собираемого изделия, на одном рабочем месте;
- подвижной, при которой изделие после окончания одной сборочной операции на одном рабочем месте перемещается на другое рабочее место, где выполняется следующая операция технологического сборочного процесса.
В технологической части дипломного проекта рассматривается изготовление мелкой партии гидравлических цилиндров в количестве 1000 штук. Поэтому выбираем не поточный стационарный вид сборки.
Для облегчения трудоемкого процесса сборки рабочие места оборудуются универсальными и специальными приспособлениями и инструментами.
Составим технологический процесс сборки гидравлического цилиндра.
На рисунке 16 приведена структурная схема сборки гидравлического цилиндра.
Рисунок 16 – Структурная схема сборки гидравлического цилиндра
Описание технологического процесса сборки гидравлического цилиндра приведено в таблице 2.
Таблица 2 - Описание технологического процесса сборки гидравлического цилиндра
№
операции
Эскиз операции
Наименование деталей, подаваемых на сборку
Последовательность сборки
Время сборочных операций, мин
Оборудование и оснастка
1
Цилиндр (1), втулка (3).
В корпус цилиндра (1), установить втулку (3), предварительно смазав тонким слоем смазки ЦИАТИМ – 201.
7
Слесарный стол
2
Плунжер (2), цилиндр (1), кольцо (4).
Установить плунжер (2) в корпус цилиндра (1) и надеть на него кольцо (4), смазав тонким слоем смазки ЦИАТИМ – 201
7
Слесарный стол
3
Кольцо фторопласт (5)
Произвести уплотнение плунжера (2) кольцом фторопластовым (5).
7
Слесарный стол
4
Втулка (6), крышка (7), шайба (8),
болт (9)
Установить на плунжер (2) втулку (6), крышку (7) и закрепить на корпусе цилиндра (1) с помощью шайбы (8) и болта (9).
7
Слесарный стол
4.5 Технологический процесс изготовления гильзы
4.5.1 Анализ технологичности конструкции детали
Технологичность – соответствие требованиям экономичной технологии изготовления. Технологичной называется такая конструкция изделия, которая обеспечивает заданное эксплуатационное качество и позволяет изготавливать ее с наименьшими затратами труда и материалов.
Гильза предназначена, как правило, для установки в него шпинделя. Поскольку наружная поверхность выполнена гладкой с проточками, то гильза является неперемещаемой в узле.
Габаритные размеры детали: наружный диаметр 180 мм, внутренний диаметр 160мм, длина 410 мм. Масса детали составляет 1 килограмм. На наружной поверхности гильзы имеются проточки шириной 4, 6, 15 мм. И наружная, и внутренняя поверхности гильзы имеют фаски.
Выбор способа получения заготовки установлен конструктором. В качестве заготовки используется горячекатаный бесшовный трубный прокат с наружным диаметром D=194мм и внутренним диаметром d=154мм (ГОСТ 8732-78). Заготовку изготавливают путем отрезки на ленточно-отрезном станке от проката. Точность горячекатаного проката ориентировочно соответствует 12-14 квалитету.
4.5.2 Выбор вида и метода получения заготовки. Определение припусков на обработку и размеров заготовки
Припуском называют слой материала, который снимают с заготовки для получения готовой детали. Назначение рациональных припусков имеет важное технико-экономическое значение. Завышенный припуск при обработке резанием приводит к росту числа проходов и толщины снимаемой стружки, что соответственно вызывает увеличение усилий резания, увеличивает возможность возникновения значительных деформаций деталей процессе обработки и уменьшает точность их изготовления, повышает износ инструмента и перерасход электроэнергии. Заниженный припуск не позволяет удалять дефектный слой материала и получать требуемую точность и шероховатость обрабатываемых поверхностей. Важно не только правильно выбрать припуск, но и добиться постоянства его размеров.
При определении припуска необходимо учитывать конфигурацию и размеры заготовки, назначенные методы обработки, характеристику выбранного оборудования и его фактическое состояние. Допускаемые отклонения величины припуска на обработку партии деталей определяются допуском на припуск, который представляет собой разность между наибольшим и наименьшим припуском. Слишком малые допуски усложняют обработку, слишком большие допуски увеличивают припуск на последующие операции. Допуск на общий припуск является одновременно и допуском на заготовку.
Произведём расчёт для поверхности 180h6. Результаты вычислений приведем в виде таблицы (приложение А). Значения Rz и Т определяем по т. 4.3-4.6 [3].
Расчётный минимальный припуск на обработку:
Далее для конечного перехода в графу “Расчётный размер” записываем наименьший предельный размер детали по чертежу. Для перехода, предшествующего конечному, определяем расчётный размер прибавлением к наименьшему предельному размеру по чертежу расчётного припуска:
Записываем наименьшие предельные размеры по всем технологическим переходам, округляя их до того знака десятичной дроби, с каким дан допуск на размер для каждого перехода.
Определяем наибольшие предельные размеры прибавлением допуска к округлённому наименьшему предельному размеру:
Записываем предельные значения припусков как разность наибольших предельных размеров и как разность наименьших предельных размеров предшествующего и выполняемого переходов:
(4)
Расчет по указанным формулам сведен в таблицу 5.
Определяем общие припуски, суммируя промежуточные припуски на обработку:
мм.
мм.
Рассчитываем общий номинальный припуск:
, (5)
где Нз – нижнее отклонение размера заготовки. Из т.3, стр. 120 [1]
Нз=0,4мм.
Нд – нижнее отклонение размера диаметра. По чертежу Нд=0,025 мм.
мм.
Рассчитываем номинальный диаметр заготовки:
(6)
мм.
Произведём проверку правильности выполнения расчётов:
(7)
мкм.
мкм.
Аналогично и для остальных равенство выполняется.
Приведём схему расположения припусков и допусков на обработку поверхности 140h6.
Таблица 5 – Расчёт припусков поверхности 180h6:
Технологические переходы обработки поверхности 140g6().
Элементы припуска, мкм.
Расчётный припуск 2zmin, мкм.
Расчётный размер dp, мм.
Предельный размер, мм.
Предельное значение припуска, мкм.
Допуск , мкм
Rz
T
dmin
dmax
1.Заготовка
300
400
410
--
182,641
182,6
183,5
--
–
900
2.Обтачивание предварительное
50
50
21
2220
180,481
180,5
180,9
2100
2600
400
3.Обтачивание чистовое
30
30
14
242
180,179
180,179
180,204
321
696
25
4.Шлифование тонкое
5
15
8
148
180,031
180,031
180,039
148
165
8
4.5.3 Обоснование выбора технологических баз
Базирование – это придание заготовке или изделию требуемого положения относительно выбранной системы координат. Базами могут служить плоскости, отверстия, наружные и внутренние диаметры, центральные фаски и даже профильные поверхности, если по отношению к ним следует выдерживать размер, ограниченный допуском.
По назначению базы подразделяются на конструкторские (основные и вспомогательные), технологические и вспомогательные. Конструкторские базы используются для определения положения детали в изделии. Технологические базы используют в процессе изготовления или ремонта для определения положения заготовки или детали при обработке относительно инструмента. Технологическими базами заготовка устанавливается в приспособление станка. Измерительные базы используют при проведении измерений. Технологические базы подразделяются на черновые и чистовые. Черновые базы (необработанные поверхности) заготовки соприкасаются с установочными элементами приспособления, чистовые базы (обработанные поверхности) служат для установки в приспособление.
При базировании заготовок и деталей необходимо соблюдать основные правила: 1) постоянство баз; 2) единство (совмещение) конструкторских, технологических и измерительных баз.
В качестве черновых баз выбираются поверхности:
обеспечивающие устойчивое положение заготовки в приспособлении;
необрабатывающиеся и обрабатывающиеся поверхности с наименьшим припуском, от которых задаются размеры или положение других обрабатываемых поверхностей;
наиболее чистые и точные;
используемые только один раз, т.к. после первой операции появляются более чистые и точные поверхности.
В первой технологической операции необходимо обрабатывать поверхности, которые будут основными чистовыми базами. Это позволяет обеспечить принцип единства баз. Для чистовых баз выбирают поверхности, руководствуясь следующими правилами:
выбранная поверхность должна использоваться на всех технологических операциях, кроме первой;
при отделочных операциях установка должна производиться на основные базы, чтобы при обработке деталь занимала то же положение, что и при работе в изделии;
базой должна быть поверхность, от которой размер задаётся с наименьшим допуском.
Операция
Схема базирования
Обработка торцов
Обработка наружной цилиндрической поверхности и канавок
Обработка внутренней цилиндрической поверхности
Таблица 4 ― Схемы базирования
От способа базирования будут зависеть смещения и погрешности при обработке, а, следовательно, и качество готовой детали.
Для третьей схемы базирования пространственное отклонение заготовки (проката) равно:
,
где кор – величина коробления обрабатываемой поверхности, мм.
Величину коробления обрабатываемой поверхности определяем по формуле:
,
где к – удельная кривизна заготовок (при токарной обработке), мкм/мм.
Значение к берём из т. 4.8 [3]; к = 1 мкм/мм.
мм.
Определим погрешность установки:
,
где б – погрешность базирования, мм.
Так как деталь устанавливается по длине, то погрешность базирования равна допуску на размер L: б=4 мм;
з – погрешность закрепления, мм. Из таблицы 4.11 [3] в осевом направлении з=0,13 мм, в радиальном направлении з=0,8 мм.
пр – погрешность положения заготовки в приспособлении.
Принимаем пр=0,05 мм. Тогда погрешность установки заготовки в центрах будет равна:
мм.
мм.
4.5.4 Выбор применяемого оборудования
Выбор оборудования и инструмента является одним из основных этапов разработки технологического процесса.
Выбор оборудования производится по главному параметру, в наибольшей степени выявляющему его функциональное значение и технические возможности. При выборе оборудования учитывается минимальный объём приведенных затрат на выполнение технологического процесса при максимальном сокращении периода окупаемости затрат на механизацию и автоматизацию.
Станки для проектируемого технологического процесса выбираются по результатам предварительного анализа возможных методов обработки поверхности, точности, шероховатости поверхности, припуска на обработку, режущего инструмента и типа производства.
С учётом вышеизложенных фактов для изготовления детали “гильза” целесообразно выбрать токарно-револьверный станок модели 1К341. Его основные характеристики приведены в таблице 3.
Таблица 3 ― Характеристики токарно-револьверного станка 1К314
Цена и технические характеристики
Цена, руб
3500
Наибольший диаметр обрабатываемой заготовки, мм
над станиной
над суппортом
400
―
Наибольший диаметр обрабатываемого прутка, мм
40
Наибольшая длина обрабатываемой заготовки, мм
100
Частота вращения шпинделя, мин-1
60; 100; 150; 265; 475; 800; 1180; 2000
Подача револьверного суппорта, мм/об
0,03; 0,06; 0,12; 0,25; 0,5; 1; 2
Поперечная подача, мм/об
0,15; 0,3; 0,6
Расстояние от шпинделя до револьверной головки, мм
82…630
Габариты станка, мм
3000×1200
Мощность электродвигателя, кВт
5,5
Категория ремонтной сложности
26
Данный станок предназначен для обработки деталей из прутка и штучных заготовок в условиях серийного и крупносерийного производства. На станке могут выполнятся такие виды обработки, как обтачивание, растачивание, протачивание канавок (наружных и внутренних), сверление, зенкерование, нарезание резьбы плашками, метчиками, самораскрывающимися резьбонарезными головками и устройствами. С помощью копировального устройства на станке можно также производить обтачивание конических поверхностей. Точность обработки на револьверных станках – 9-го квалитета, параметр шероховатости обработанной поверхности – до Ra 2,5.
Для фрезерования торцов используем горизонтально-фрезерный станок 6Р10. Для шлифования используем круглошлифовальный станок-полуавтомат ЗМ185А.
Для обработки детали из [2] выбираем следующие инструменты и приспособления:
фреза торцовая насадная со вставными ножами ТУ2.035.0224638.1155-88 или с механическим креплением пятигранных пластин ГОСТ 22087-76;
проходной отогнутый резец с пластинами из быстрорежущей стали ГОСТ 18877-73 (для обработки цилиндрических поверхностей и снятия фасок поперечной подачей);
расточной резец с напайными пластинами ГОСТ 18882-73;
резец расточной с механическим креплением многогранных минералокерамических пластин ГОСТ 26612-85;
шлифовальный круг прямого профиля (тип ПП) на керамической связке ГОСТ 2424-83;
трехкулачковый самоцентрирующийся патрон с люнетом
ГОСТ 2675-80;
оправка разжимная с гофрированными втулками ГОСТ 2778-80;
штангельциркуль ШЦ-1 ГОСТ 166-80;
образцы шероховатости ГОСТ 9378-75.
4.5.5 Режимы обработки детали
Основными элементами резания при токарной обработке являются: скорость резания V, подача S и глубина резания t.
Режимы резания при обработке детали рассчитаем расчетным методом.
а) При точении скорость резания рассчитываем по формуле:
;
где Т - среднее значение стойкости, мин;
(при одноинструментной обработке Т=60 мин)
t - глубина резания;
S – подача;
Cv = 56; m = 0,125; y =0,66; x=0,25.
Значение величины подачи S берём из т. 11-14 [2].
Значение коэффициентов C и показателей степеней выбираем из т. 8 [2]
Коэффициент K определяется по формуле
где Km - коэффициент учитывающий влияние материала заготовки;
Kп - коэффициент учитывающий состояние поверхности заготовки;
Ku - коэффициент учитывающий материал инструмента;
Значение коэффициентов Km, Ku и Kп выбираем из т. 1-6 [2].
Km = 0,8; Ku = 1; Kп = 0,8.
Определим число оборотов шпинделя станка.
где V – cкорость резания;
D – диаметр обрабатываемой поверхности;
Определяем основное технологическое время
где lр.х. - длина рабочего хода резца, мм;
i - количество проходов, шт.
б) Скорость резания при фрезеровании:
v = Cv·Kv·Dq/(Tm·tx·sy·Bp·Zp);
где Bp и Zp – справочные коэффициенты.
Для отрезания, прорезания пазов:
KMv = 0,80; KПv = 0,85; KИv = 1,68.
Результаты расчётов по приведенным выше формулам заносим в таблицу 10.
Таблица 6. Расчет режимов резания
наименование переходов
t мм
l p.x.
i шт
S ммоб
V ммин
n обмин
nпр
обмин
То
Фрезерная черновая
0,30
180,00
1
0,60
18,5
48
80
0,104
Точение черновое
3,10
410,00
1
1,20
87,2
225,7
250
0,08
Точение чистовое
0,25
410,00
1
1,10
173,2
448,5
400
0,06
Точение черновое
3,10
15,00
1
1,20
87,2
225,7
250
0,08
Точение чистовое
0,25
15,00
1
1,10
173,2
448,5
400
0,06
снятия фаски 1х45 черновое
1
1,00
1
1,1
122,5
317,2
315
0,003
снятия фаски 1х45 черновое
1
1,00
1
1,1
122,5
317,2
315
0,003
Растачивание черновое
3,10
40,00
1
1,20
87,2
198,4
200
0,17
Растачивание чистовое
0,25
40,00
1
1,10
173,2
394
400
0,091
шлифование
-
40
1
0,5
18
40,95
80
1
В итоге имеем То,общ= 1,66 мин.
4.5.6 Разработка технологического маршрута изготовления
При разработке технологического процесса следует руководствоваться следующими принципами:
при обработке у заготовок всех поверхностей в качестве технологических баз для первой операции целесообразно использовать поверхности с наименьшими припусками;
в первую очередь следует обрабатывать те поверхности, которые являются базовыми в дальнейшей обработке;
в начале технологического процесса следует осуществлять те операции, в которых велика вероятность получения брака из-за дефекта.
Технологический процесс записывается по операционно, с перечислением всех переходов.
005 Операция фрезерная
Оборудование – горизонтально-фрезерный станок марки 6Р10.
Фреза торцовая насадная со вставными ножами ТУ2.035.0224638.1155-88 или с механическим креплением пятигранных пластин ГОСТ 22087-76. Фрезеровать торцы в размер 410.
010. Операция токарная.
Оборудование - токарно-револьверный станок марки 1К341.
Деталь устанавливаем в оправку разжимную с гофрированными втулками.
В качестве базы используем внутреннюю поверхность заготовки 165. Используется проходной отогнутый резец с пластинами из быстрорежущей стали ГОСТ 18877-73. Обточить начерно поверхность 182.
015. Операция токарная.
Оборудование - токарно-револьверный станок марки 1К341.
Деталь устанавливаем в самоцентрирующий патрон по наружнему диаметру.
В качестве базы используем необработанную наружнюю поверхность 182. Используется расточной резец с напайными пластинами ГОСТ 18882-73. Расточить начерно поверхность 163.
020. Операция токарная.
Оборудование - токарно-револьверный станок марки 1К341.
Деталь устанавливаем в оправку разжимную с гофрированными втулками.
В качестве базы используем внутреннюю поверхность заготовки 163. Используется проходной отогнутый резец с пластинами из быстрорежущей стали ГОСТ 18877-73. Обточить начисто поверхность 180. Проточить канавки 175. Обточить фаски.
025. Операция токарная.
Оборудование - токарно-револьверный станок марки 1К341.
Деталь устанавливаем в самоцентрирующий патрон по наружнему диаметру.
В качестве базы используем наружнюю поверхность 180. Используется расточной резец с напайными пластинами ГОСТ 18882-73. Расточить начисто поверхность 163. Расточить фаски.
030. Операция шлифовальная.
Оборудование - круглошлифовальный станок-полуавтомат ЗМ185А.
Деталь устанавливаем в оправку разжимную с гофрированными втулками.
В качестве базы используем внутреннюю поверхность заготовки 160.. Используется шлифовальный круг прямого профиля (тип ПП) на керамической связке ГОСТ 2424-83.
045. Контрольно-измерительная.
Используется штангельциркуль ШЦ-1 ГОСТ 166-80.
Проверить размеры 410, 180, 160, 175.
5. БЕЗОПАСНОСТЬ И ЭКОЛОГИЧНОСТЬ ПРОЕКТА
Задача безопасности жизнедеятельности состоит в защите человека от негативных воздействий антропогенного и естественного происхождения и достижение комфортных условий жизнедеятельности.
B современных условиях, для реализации поставленных задач, особое значение приобретает применение принципов обеспечения безопасности труда на базе совершенствования техносферы и снижения ее негативного влияния на человека и природу до допустимых уровней.
Достижение этих целей взаимосвязано. Решая задачи обеспечения безопасности человека в техносфере, одновременно решаются задачи защиты природы от губительного влияния техносферы.
Первопричиной многих негативных процессов в природе и обществе явилась антропогенная деятельность, не сумевшая создать техносферу необходимого качества как по отношению к человеку, так и по отношению к природе.
Постоянная борьба за свое существование вынуждала человека находить и совершенствовать средства защиты от естественных негативных воздействий среды обитания. K сожалению, появление жилища, применение огня и других средств защиты, совершенствование способов получения пищи - все это не только защищало человека от естественных негативных воздействий, но и влияло на среду обитания.
На протяжении многих веков среда обитания человека медленно изменяла свой облик и как следствие, мало менялись виды и уровни негативных воздействий. Так продолжалось до середины ХIХ века - начала активного роста воздействия человека на среду обитания. В ХХ веке на Земле возникли зоны повышенного загрязнения биосферы, что привело к частичной, a в ряде случаев к полной региональной деградации. Этим изменениям во многом способствовали:
высокие темпы роста численности населения на Земле (демографический взрыв) и его урбанизация;
рост потребления и концентрация энергетических ресурсов;
интенсивное развитие промышленности и сельскохозяйственного производства;
−массовое использование средств транспорта;
рост затрат на военные цели и ряд других вопросов.
B своей деятельности человек, как правило, не осознает, что нарушает закономерности протекания природных процессов, вызывает нежелательные для себя изменения и не предвидит последствия, которые могут вызвать частичную, a иногда и полную деградацию экосистем. Но если до некоторых пор механизмы саморегуляции компенсировали возмущающие антропогенные воздействия, то особенностью современного этапа развития планеты является то, что система производства и размах человеческой деятельности достигли масштабов, сопоставимых c масштабами природных явлений. Разрушительная деятельность человека породила конфликт между обществом и природой, создала проблемы, которые получили название экологических.
Человек и окружающая среда гармонично взаимодействуют и развиваются лишь в условиях, когда потоки энергии, вещества, информации находятся в пределах, благоприятно воспринимаемых человеком и природной средой.
Эволюция природных процессов и явлений, в том числе и человека, в конечном счете привела сообщество к озабоченности судьбой биосферы, представляющей собой ныне неразделенное единство природных, техногенных, дyxовных элементов.
Основная цель безопасности жизнедеятельности - защита человека в техносфере от негативных воздействий антропогенного и естественного происхождения и достижения комфортных условий жизнедеятельности.
5.1 Микроклимат рабочей зоны производственных помещений
Организм человека постоянно находится в состоянии теплового обмена c ОС
Основную роль в этом процессе играет система терморегуляции человека. Она регулирует теплообмен организма с окружающей средой и поддерживает почти постоянную температуру около 37 °C. Отдача теплоты организмом человека в ОС происходит в результате теплопроводности через одежду, конвекции, излучения на окружающие поверхности, испарения влаги с поверхности кожи. Часть теплоты расходуется на нагрев вдыхаемого воздуха.
На процесс теплообмена оказывают влияние метеорологические условия среды ( микроклимат) и характер работы.
Показатели, характеризующие микроклимат в производственных помещениях:
температура воздуха;
-температура поверхностей;
относительная влажность воздуха;
-скорость движения воздуха:
интенсивность теплого облучения.
Санитарные нормы и правила (Сан ПиН 2.2.4.548-96) предназначены для предотвращения неблагоприятного воздействия микроклимата рабочих мест производственных помещений на самочувствие , функциональное состояние, работоспособность и здоровье человека. Санитарные правила устанавливают гигиенические требования к показателям микроклимата рабочих мест c учетом периодов года (теплый - среднесуточная температура наружного воздуха более +10 ° C, холодный ниже этой температуры.)
Разграничение работ по категориям осуществляются на основе интенсивности энергозатрат организма в ккал/ч (Вт). Характеристика работ -1а,16,11а, 11Б. 111.
Таблица 1.1 Оптимальные величины показателей микроклимата на рабочих местах
Периодгода
Категория работ по уровню
энергозатрат,ВТ
Температура
воздуха
°С
Температура
Поверхностей°С
Относительная
влажнось %
Скорость
движ.
Воздуха
м/с
Холодный
11 а (175-232)
19-21
18-22
60-40
0,2
116 (233-290)
17-19
16,20
0,2
Теплый
11а (175-232)
20-22
19-23
0,2
116 (233-290)
19-21
18-22
0,2
Оптимальные микроклиматические условия установлены по критериям оптимального теплового и функционального состояния человека. Эти показатели микроклимата необходимо соблюдать на рабочих местах производственных помещений, на которых проводятся работы операторского типа. B помещениях, оборудованных системами кондиционирования воздуха, метеорологические условия в пределах оптимальных условий следует обеспечивать в соответствии c данными таблицы 1.1.
B нашей стране нормируются два уровня метеорологических условий: оптимальный и допустимый. Оптимальными являются такие сочетания параметров микроклимата, которые обеспечивают ощущение теплового комфорта и создают предпосылки для высокого уровня работоспособности; допустимыми - такие, при которых не возникает нарушения состояния здоровья, но могут наблюдаться дискомфортные ощущения ухудшающие самочувствия и снижение работоспособности.
Анализ опасных и вредных факторов автоматической линии для резки рулонной стали c гидроприводом подачи.
Используемые в автоматизированном производстве электрические системы c электромагнитными муфтами, создают электромагнитные поля (ЭМП), излучения которых могут превышать нормативно - допустимые значения. Для снижения излучений электрической и магнитной напряженности, плотности потока энергии необходимо использовать поглощающие и отражающие экраны, индивидуальные средства защиты, очки.
Для защиты операторов от электростатических полей необходимо зaземлять экраны или устанавливать нейтрализаторы.
Помещения в которых проводят настройку, регулирование и испытание управляющих систем необходимо устраивать так, чтобы при включении на полную мощность , излучение не проникало в смежные помещения и окружающую среду. Для уменьшения мощности излучения используют коаксиальные или волноводные поглотители мощности.
Допустимые параметры электромагнитных излучений и напряженность электрического поля не должны превышать:
для напряжения электрического поля в диапазоне частот 2Гц-2кгц - 25 В/м
для плотности магнитного потока
диапазоне частот 5Гц – 2 кГц -250 н Тл,
в диапазоне частот 2кГц –400 кГц –25 н Тл;
- для поверхностного электростатического потенциала - 500 B
Электрооборудование автоматизированной линии резки рулонной стали включает дистанционный пульт управления. Электросхема позволяет работать в следующих режимах: наладочном, заправки, автоматическом. Работа автоматической линии для резки рулонной стали осуществляется системой управления по заданному технологическому циклу c соблюдением блокировок по программе в памяти свободно программируемого контроллера . Режимы работы линии задаются c центрального пульта переключателями.
Рукоятки рубильников изготавливаются из изоляционного материала от случайного прикосновения обслуживающего персонала при открытых дверях шкафа или ниши и попадания под действие электрического тока.
Каждая единица станочного оборудования, объединенная в автоматическую линию должна иметь вводной выключатель ручного действия ,размещенный в удобном для обслуживания и безопасном месте и предназначенный для подключения к питающей сети.
5.2 Электробезопасность при работе с гидроприводом автоматической линии поперечной резки электротехнической стали
Действие электрического тока на организм человека носит разносторонний и своеобразный характер. Проходя через организм человека, электроток производит термическое, электролитическое, механическое и биологическое действия.
Исход поражения человека электротоком зависит от многих факторов: силы тока, времени прохождения тока через организм ,характеристики тока (переменный или постоянный), пути тока в теле человека, при переменном токе от частоты колебаний.
Ток, проходящий через организм, зависит от напряжения прикосновения, под которым может оказаться работник, а так же от суммарного сопротивления, в которое входит сопротивление тела человека. На сопротивление организма воздействию электрического тока оказывает влияние физическое, психическое состояния. Нездоровье, утомление, голод, эмоциональное возбуждение приводят к снижению сопротивления.
Допустимым считается ток, при котором человек может самостоятельно освободиться от электрической цепи. Переменный ток опаснее постоянного, однако, при высоком напряжении (более 500 B) опаснее постоянный ток.
Напряжение прикосновения (ГОСТ12.1.О38-82)
Таблица
Род
пере
мен
50 Гц
Нормируемая
Величина
п,М/С
I, м A
Предельно допустимые уровни, при продолжительности
воздействия тока, c ( секундах)
00
1
65
0
01
02
0,з
04
О5
О6
07
08
09
10
СВ
1
Температура, влажность ) увеличивают опасность поражения током.
B отношении опасности поражения током помещение механической обработки токарными полуавтоматами относится к особо опасным. K Техническим способами средствам защиты относятся: изоляция токоведущих частей c устройством непрерывного контроля, ограждения, электрическое разделение сетей , применение малых напряжений. B сети c изолированной нейтралью сопротивление заземляющего устройства не должно быть более 4 Ом, а при мощности генераторов (трансформаторов) 100 кВ. А не более 10 Ом при сопротивлении изоляции 0,5 M Ом.
При напряженности электростатического поля менее 20 кВ/м время пребывания на участках механической обработки не регламентируется. Используемые в автоматизированной системе электрические системы c
электромагнитными муфтами создают электромагнитные поля (ЭМП), излучения которых могут превышать нормативно допустимые значения. Для снижения излучений электрической и магнитной напряженности, плотности потока энергии необходимо использовать поглощающие и отражающие экраны. Для защиты операторов от электростатических полей необходимо заземлять экраны и устанавливать нейтрализаторы напряжений. Помещения, в которых проводят настройку, регулирование и испытание управляющих систем необходимо устраивать так, чтобы при включении на полную мощность, излучение не проникало в смежные помещения и в окружающую среду (ОС). Для уменьшения мощности излучения целесообразно использовать коаксиальные или волновые поглотители мощности. Рукоятки рубильников изготавливают из изоляционного мате- риала от случайного прикосновения при открытых дверях шкафа или ниши и попадания под действие тока.
Для предотвращения попадания человека в опасную зону применяют оградительные устройства , которые подразделяются по конструктивному исполнению на: -кожухи, дверцы, щиты, щитки, козырьки, экраны, по способу изготовления на: сплошные, сетчатые, решетчатые, комбинированные по способу их установки: стационарные , передвижные.
Предохранительные защитные устройства предназначены для автоматического отключения рабочих органов и машин при отклонении какого-либо параметра, характеризующего режим работы оборудования за пределы допустимых значений.
B соответствии c ГОСТ12.4.125-83 они по характеру действия подразделяются на блокировочные и оградительные.
Блокировочные устройства препятствуют проникновению человека в опасную зону , либо на время пребывания его в этой зоне устраняют опасные факторы. По принципу действия они делятся на механические, электрические, электронные, электромагнитные , пневматические и т.д.
При работе со стендом используется электромагнитная блокировка самовыключения насосной установки при открытой крышке силовых электроприводов и при отключении и включении напряжения сети.
Устройства дистанционного управления позволяют контролировать работу оборудования c безопасного расстояния от стенда. На стенде применено дистанционное включение электродвигателя насосной установки, дистанционное управление электромагнитами, гидрораспределителем и порошковым электромагнитным тормозом.
Средства автоматического контроля и сигнализации подразделяются по назначению на информационные, предупреждающие, аварийные и ответные; по способу срабатывания: на автоматические и полуавтоматические.
Мероприятия электробезопасности обеспечиваются недоступностью токоведущих частей путем использования изоляции, ограждений, применением низких напряжений (менее 42 B) , разделением цепей на участки при помощи трансформаторов, выравниванием потенциала земли для устранения шагового напряжения за счет использования групповых зaземлителей, применением средств индивидуальной и Коллективной защиты.
Освещение регламентируется строительными нормами и правилами СНиП 23.05-95 «Естественное и искусственное освещение», согласно которым в зависимости от категории зрительной работы нормируется освещенность . Искусственная освещенность при работе со стендом на дистанционном пульте управления составляет 300 лк.
Коэффициент естественного освещения обеспечивается через боковые световые проемы и составляет кео =1 .
Необходимо обеспечить достаточно равномерное распределение яркости на рабочей поверхности, a также в пределах окружающего пространства.На рабочей поверхности должны отсутствовать резкие тени, в поле зрения должна отсутствовать прямая и отраженная блескость. Показатель ослепленности для категории зрительной работы V разряда, подразряда «a» составляет 40 , a коэффициент пульсации к=20 %..
Для повышения уровня автоматизации необходимо иметь автоматизиро ванные приводы, содержащие автономные регуляторы и автоматические устройства. Применение гидроприводов позволяет повысить точность, надежность,
Гидропривод имеет ряд преимуществ перед другими приводами:
получение больших усилий и мощностей при ограниченном размере гидродвигателя;
широкий диапазон бесступенчатого регулирования скорости;
возможность работы в динамических режимах;
защиту системы от перегрузок;
точный контроль действующих усилий;
получение прямолинейных движений без кинематических
преобразований.
Однако, наряду c огромными преимуществами, гидроприводы имеют недостатки.
Прежде всего это загрязнение окружающего пространства утечками рабочей жидкости в результате интенсивного износа подвижных уплотнений и потери герметичности неподвижных уплотнений, рaзрыва рукавов высокого давления от циклического воздействия гидроударов и забросов давления. При утилизации рабочих жидкостей гидросистем имеют место отходы ,так как они практически не поддаются полной переработке.
Тепловое загрязнение, возникающее из-за больших энергетических потерь и обусловленные низким коэффициентом полезного действия гидроприводов .
Потеря герметичности уплотнений возникает в результате износа резиновых элементов. Интенсивность износа резиновых элементов сильно зависит от рабочей температуры в зоне контакта резины и других частей оборудования. При повышении температуры стойкость резиновых уплотнений резко падает, причем обвальный износ происходит уже на верхней границе допустимых температур для гидросистем. Это явление весьма значительно сказывается при повышении температуры рабочей жидкости и приводит к потере герметичности соединения, сопровождаемой утечками рабочей жидкости в окружающее пространство, рабочую зону, a при работе гидросистем на открытом месте - засорение почвы и проникновением в грунтовые воды. Во избежание этих последствий необходимо уменьшить рабочую температуру гидросистем установкой охлаждающих устройств.
5.3 Защита от шума и вибрации на участке автоматической линии поперечной резки электротехнической стали
Малые механические колебания ,возникающие в упругих или находящихся под воздействием переменного физического НОЛЯ телах
нaзываются вибрацией. Воздействие вибрации человека классифицируют: по способу передачи колебаний , по направлению воздействия ,по временной характеристике вибрации.
Вибрация относится к факторам, обладающим высокой биологической активностью. Мощность колебательного процесса в зоне контактаи время этого контакта являются главными параметрами деляющими развитие вибрационных патологий, структура которых зависит от частоты и амплитуды колебаний, продолжительности воздействия, места приложения ,направления сил вибрационного воздействия, демпфирующих свойств тканей , явлений резонанса и других условий.
Гигиеническое нормирование вибраций регламентирует параметры производственных вибраций и правила работы c виброопасным оборудованием, ГОСТ 12 1 .012-90 «Вибрационная безопасность. Общие требования», Санитарные нормы СН 2.2.4./2.1.8.556-06 «Производственная вибрация в помещениях жилых и общественных зданий».
Вид
вибрации
Допустимый уровень вибрации, Дб в октавньгх полосах
со среднегеометрическими частотами ,Гц
2 4 8 16 31.5 63 125 250 500 1000
Технологическая
108 99 93 92 92 92 - - -
Локальная
-115 109 109 109 109 109 109 109
Производствен-
ных помещениях
100 91 85 84 84 84
Интенсивный шум на производстве способствует снижению внимания и увеличению числа ошибок при выполнении работы, исключительно сильное влияние оказывает шум на быстроту реакции, сбор информации и аналитические процессы, из-за шума снижается производительность труда и ухудшается качество работы. Шум затрудняет своевременную реакцию работающих на предупредительные сигналы внутрицехового транспорта (автопогрузчики, мостовые краны и др.), что способствует возникновению несчастных случаев на производстве..
Нормируемые параметры шума на рабочих местах определены ГОСТ12.1.003-83 и Санитарными нормами СН2.22.4/2.1.8.562-96 «Шум на рабочих местах, в помещениях жилых ,общественных зданий и на территории жилой застройки.».
Таблица Допустимые уровни звукового давления, уровни звука
Рабочие места
Уровни звукового давления. ДБ в октавных
полосах среднегеометрических частот ,Гц
Уровень
звука
31.5
63
125
250
500
1000
2000
4000
8000
Дб A
Постоянные
рабочие места
110
99
92
86
83
80
78
76
74
85
Помещения
Лабораторий
107
94
87
82
78
75
73
71
70
80
Технологичесие
процессы метал
лорежущего обо-
рудования
107
95
87
82
78
80
73
71
69
80
Кабины
наблюдений и
дистанционного
управления
99
83
74
68
63
60
57
55
54
65
Фактический уровень шума при работе оборудования незначительно превышает допустимые значения, что требует проведения мероприятий по снижению на пути распространения за счет использования звукоизолирующих перегородок, a также звукопоглощающих материалов для облицовки перегородок.
Шум c уровнем звукового давления до 30-35 дб привычен для человека и не беспокоит его. Повышение этого уровня до 40-70 дб при работе операторов АСУ создает значительную нагрузку на нервную систему ,вызывая ухудшение самочувствия и при длительном воздействии может стать причиной неврозов. Воздействие шума выше 90дб может привести к потере слуха - профессиональной тугоухости. Оптимaльные уровни звука предназначены в целях улучшения условий труда операторов АСУ.
Для улучшения условий труда эффективно использовать кабины наблюдения и дистанционное управление,что предусмотрено проектом, для снижения неблагоприятного акустического воздействия на обслуживающий персонал.
Оценка состояния слуховой функции базируется на количественномопределении потерь слуха и проводится по показателям аудиометрического исследования. При оценке слуховой функции определяющими приняты средние показатели порогов слуха в области воспринимаемых речевых частот. Критерием профессионального снижения слуха принят показатель средней арифметической величины снижения слуха в речевом диапазоне, равный 11дБ и более.
Интенсивный шум на производстве способствует снижению внимания и увеличению числа ошибок, при выполнении работы, исключительно сильное влияние оказывает шум на быстроту реакции, сбор информации и аналитические процессы, что затрудняет своевременную информацию операторов.
5.4 Анализ опасных и вредных факторов при работе гидропривода
На человека в процессе труда могут воздействовать опасные и вредные производственные факторы. Производственные факторы, воздействие которых на работающих приводят к травме или к резкому ухудшению .состояния здоровья называются опасными, a факторы, которые приводят к заболеванию или снижению работоспособности называются вредным. По природе действия на организм человека опасные и вредные факторы подразделяются на четыре группы: физические, химические, биологические и психофизиологические. K физическим опасными вредным факторам относятся:
-факторы, характеризующие оборудование, технологию - движущиеся механизмы и машины, подвижные части оборудования, передвигающиеся заготовки материалы, повышенное напряжение в электрической цепи, замыкание которой может произойти через тело человека, повышенная или пониженная температура оборудования и другие факторы, характеризующие производственную среду повышенная запыленность и загазованность воздуха рабочей зоны, повышенная или пониженная температура воздуха рабочей зоны, повышенный уровень шума . инфра и ультразвука на рабочем месте, повышенная напряженность электрического поля, повышенный уровень электромагнитных излучений и др.
Химические вредные опасные производственные факторы по воздействию на человека подразделяются на: токсичные, раздражающие, канцерогенные, сенсибилизирующие, мутагенные.
Биологические опасные и вредные факторы включают следующие биологические объекты: патогенные микроорганизмы (бактерии, вирусы грибы), продукты их жизнедеятельности, макроорганизмы (растения, животные)
5.5 Расчет виброизоляции гидропривода
B качестве виброизоляторов используются стальные пружины диаметром D=13..2 см, диаметром прутка d=1.6 см , высотой ненагруженной пружины Н о =26.4 см c числом рабочих витков i= 3.5.
Определить количество стальных виброизоляторов кабины массой
Q = 72000 кг
1. Определим индекс пружины С
C=D/d = 13.2/ 1.6=8.25
Модуль упругости на сдвиг G для всех пружинных сталей
G= 8. 106
3. Определим жесткость одной пружины в продольном направлении
К=0 d/ 8 с 2 I= 8 10' 1/6 / 8 (8/25 ) 2 5/5=518 Н/см
4 Определяем отношение
Н о / D=2.64/ 13.2=2
5. По графику найдем коэффициент K, учитывающий повышение напряжений в средних точках сечения прутка вследствие деформации сдвига K= 1,18 для C= 8.25
6. Определим статическую нагрузку Р с,,, принимая допустимое напряжение на кручение 6 = 40000 H/см 2
Р сп, = ггд2г / 8xD=3.14 (1.62)) 40000/ 8 1.18 13.2=4128.6 Н
7. Определим количество витков пружины
n = Q/Р = 72000/4128/6= 2,09 принимаем 4 пружины
8. Общая жесткость стальных виброизоляторов
к= п K =4 *518=2072 H/см
B качестве виброизоляторов насоса можно рекомендовать четыре пружины общей жесткостью 2072 H/ см
5.6 Расчет вентиляции на участке гидропривода валковой подачи автоматической линии поперечной резки электротехнической стали
Определить количество воздуха( производительность вентилятора c учетом избытков явного тепла на участке работы гидропривода вaлковой подачи автоматической линии для резки рулонной стали
Для определения производительности вентилятора найдем количество воздуха, для обеспечения установленной санитарно-гигиеническими нормами температуры.
Количество воздуха (L) определяем c учетом избытка явного тепла
Где избыточные тепловыделения, ккал ,
C-теплоемкость сухого воздуха , ккал/кг;
p -плотность приточного воздуха - 1,2 кг/м2 ;
- температура удаляемого из помещения воздуха и приточного.
Qиз6-Qчел + Qоборуд , ккал ,
Qчел- тепловыделения человека ,выполняющего работу средней тяжести (11 а,11 б.) при температуре окружающей среды 25 °C на одного человека составляют 70 ккал.
На участке работает 10 человек, поэтому тепловыделения от работников составляют
Qчел= 70 x 10= 700 ккал
Тепловыделения от нагретых поверхностей систем управления гидроприводом составляют
Qнп JF (tнп - tel);
J=8,1 + 0,061x(55-25) = 9,93
F =0,0061 x 10 =0,061
Qоборуд= 9,93 x 0,061 (55-25) = 18,1кВт
Где n = 10- Количество источников нагретого оборудования при его эксплуатации, температура нагретых поверхностей на участке испытаний 60 °C , a удаляемого воздуха-25 °C
Избытки явного тепла составляют : оИзб = 18,1 +700 =718 , 1 кВт
2. Количесто воздуха необходимого для вентиляции от избытков явного тепла
Lизб теп 718,1 x 3600 / 0,24x1,2(55-25) х103 =299тыс /ч
3. Подбираем вентилятор радиальный Ц4-70 №63 , производительностью 299,0 м3/ч ,при p=440 Па.
6. ЭКОНОМИЧЕСКАЯ ЧАСТЬ ПРОЕКТА
Характерной особенностью разрабатываемого проекта является разработка гидропривода валковой подачи, которая входит в состав линии, автоматизированной для поперечной резки электротехнической стали 0,1…..0,6800 мм.
Экономическая оценка проекта базируется на многих показателях, отражающих научно-технические, производственно-организационные и рыночные критерии.
Оценка эффективности проекта производится параллельно с разработкой гидропривода валковой подачи, что необходимо для внесения в проект своевременных изменений с целью повышения эффективности технического предложения.
Экономическая оценка эффективности технического проекта производится комплексно по системе показателей, принятых в мировой практике. Этими показателями являются:
Чистый дисконтированный доход (ЧДД).
Индекс доходности.
Критический объем продаж.
Срок окупаемости.
Внутренняя норма доходности.
Проект будет считаться положительным в том случае, когда каждый из этих показателей отвечает определенным экономическим критериям и требованиям. Эта система показателей отражает также и финансовые критерии проекта.
6.1 Концепция проекта
Предлагаемый научно-технический продукт представляет собой гидропривод валковой подачи, которая входит в состав линии, автоматизированной для поперечной резки рулонной стали.
Главной целью проекта является получение прибыли за счет разработанного гидропривода валковой подачи и определение точки безубыточности по ее выпуску. Реализация данного проекта позволит:
- удовлетворить потребность субъектов рыночной экономики;
- значительно повысить эксплуатационные качества подачи валковой без снижения технических возможностей;
- изменить диаметр правильных валков для обеспечения качественной правки;
- изменить конструкцию мерительного ролика и применить в проекте серийно выпускаемый датчик ВЕ-78.
Для экономического обоснования проекта необходимо рассмотреть предлагаемый научно-технический продукт с позиции маркетингового синтеза и принять решение для стратегического планирования модификаций и сопровождения предлагаемого продукта.
Для организации производства валковой подачи, организационных мероприятий и рекламной кампании необходимы кредитные ресурсы на сумму 17641,3 тыс.руб.
Срок возврата кредита 1,2 года.
6.2 Проектируемый продукт (Товар по замыслу, в реальном исполнении и с подкреплением)
Предлагаемый гидропривод валковой подачи предназначен для периодического перемещения ленточного материала на величину шага, в зависимости от заданной ей программы системой управления линией. Одновременно подаваемая на шаг лента при необходимости может правиться при помощи пятивалкового правильного механизма.
Внедрение валковой подачи позволяет снизить трудоемкость и материалоемкость конструкции, улучшить эксплуатационные качества подачи повышением технического уровня автоматизированной линии по сравнению с существующими аналогами.
При разработке гидропривода валковой подачи используем идею маркетинговой ориентации на четырех уровнях.
Рисунок 6.1 - Маркетинговая модель гидропривода валковой подачи
Основополагающим является уровень подачи валковой по замыслу , т.е. что в действительности будет приобретать потребитель и основная выгода, которую он будет иметь. Как видно из рисунка 6.1, научно-ехнический продукт по замыслу – сердцевина понятия разрабатываемой подачи.
На втором уровне разрабатываемый продукт по замыслу превращается в гидропривод валковой подачи для периодического перемещения ленточного материала на величину шага, в зависимости от заданной ей программы системой управления линией.
На третьем уровне разработкой предусматривается поперечная резка рулонной стали с различной шириной ленты (т.е. универсальное использование).
Четвертый уровень предусматривает простоту обслуживания, освоения и внедрения разработанного гидропривода валковой подачи.
6.3 Исследование и анализ рынка
автоматическая линия сталь гидравлический цилиндр
В целях изучения спроса и выявления потенциальных потребителей было проведено маркетинговое исследование в масштабах Российской Федерации , стран СНГ и предприятий Ростовской области. Результаты исследований приведены в таблице 6.1.
Таблица 6.1 - Данные о емкости рынка сбыта.
№
п/п
Сегменты рынка
2010
2011
2012
2013
2014
1
Предприятия г. Ростова и Ростовской обл.
5
6
6
7
8
2
Российская Федерация
20
24
26
28
32
3
Страны СНГ
5
6
8
10
15
Итого
30
36
40
45
55
6.4 Определение затрат на создание проекта
Затраты на создание проекта Зпр включают затраты на выполнение собственно научно-исследовательских и проектных работ, т.е. исследовательских, конструкторских и технологических – Зк.т.р, а также затраты на изготовление опытного образца Зоп.о.
Зпр.=Зк.т.р. + Зоп.о.
а) Расчет затрат на выполнение конструкторских и технологических работ.
Затраты на конструкторские и технологические работы рассчитываются по статьям и включаются в систему затрат (см. таблицу 6.2).
Таблица 2 - Смета затрат на выполнение конструкторских и технологических работ.
№
п/п
Статьи расходов
Сумма, руб.
1
Стоимость материалов.
2000
2
Основная заработная плата
инженерно-технического персонала.
111375
3
Дополнительная заработная плата ИТР.
16706,2
4
Отчисления на социальное страхование
работников.
33941,5
5
Стоимость специального оборудования
(или амортизация оборудования для
проведения исследований)
9000
6
Стоимость услуг сторонних организаций.
5568,75
7
Накладные расходы.
66825
Итого :
245416,5
В стоимость материалов включаются затраты на приобретение принадлежностей для выполнения чертежных работ, а также расходы на бумагу и канцелярские принадлежности. Затраты по данной статье устанавливаем на основе действующих цени потребности в названных элементах на разрабатываемый гидропривод. Затраты по статье «Стоимость материалов» принимаем в сумме 2000 руб.
Основная заработная плата инженерно-технического персонала (Зо)
Основная заработная плата определяется на основе численности ИТР по формуле:
Зо = Сд Ритр Дп,
где Ритр- численность ИТР, чел., Ритр = 3 чел.;
Дп- количество дней для проектирования , Дп = 90 ;
Сд- дневная ставка по оплате персонала определяется по формуле :
,
где Смi –месячная ставка по оплате ИТР i-той квалификации ;
Дн – месячный номинальный фонд рабочего времени в днях (принимаем 24 дня)
руб/день
Ритр=3 чел.; Дн=90 дней.
Зо = 416,6 3 90 = 111375 руб.
Дополнительная заработная плата ИТР (Зд) определяется в процентах от основной заработной платы этой категории персонала. Она включает оплату отпусков, премий и других выплат из фонда заработной платы в соответствии с трудовым законодательством.
,
- процент дополнительной заработной платы, = 15 %.
Тогда Зд = 111375 0,15 = 16706,2 руб.
Отчисления на социальные страхования (Осс) с заработной платы (основной и дополнительной) определяется в соответствии с установленным в данный период времени процентом, одинаковым для всех организаций.
,
где - процент отчислений на социальное страхование, = 26,5 %.
Тогда
руб
К статье «Стоимость специального оборудования» относятся затраты, связанные с приобретением или изготовлением этого оборудования, предназначенного только для выполнения данной работы.
В случае, если проектные работы не требуют специального оборудования, но используется другое лабораторное оборудование, то определяется сумма амортизационных отчислений от использования лабораторного оборудования Ал.об.
;
,
где : Ол- стоимость лабораторного оборудования, руб.
а - норма амортизации данного вида оборудования ;
Дп, Fп - плановый годовой фонд времени работы лабораторного оборудования соответственно в днях и часах.
6. Статья «Стоимость услуг сторонних организаций», т.е. для выполнения теоретических исследований необходимо воспользоваться услугами других научно-исследовательских организаций, а также в эту статью включаются затраты на информационные услуги и т.д. Принимаем в процентах от основной заработной платы (5%).
, = 5 %,
руб
7. В статью «Накладные расходы» включаются затраты , связанные с управлением и хозяйственным обслуживанием той организации или подразделения, где выполняются проектные работы. Величина этих расходов определяется в процентах от основной заработной платы ИТР, занятых выполнением данной работы. В проектных организациях накладные расходы принимают в размере от 60 до 100 % от основной заработной платы ИТР.
Знакл.расх. = 111375 0,6=66825 руб.
Данные расчета сводим в таблицу 6.2.
6.5 Расчет себестоимости изготовления опытного образца
Себестоимость является одним из основных экономических показателей при оценке эффективности гидропривода валковой подачи. Чем ниже себестоимость гидропривода валковой подачи, тем при прочих равных условиях экономичнее она. Как правило, на разных этапах конструкторской и технологической подготовки производства используются различные методы определения себестоимости. В разрабатываемом проекте возможно применение следующих методов :
1. Возможно определение себестоимости на основе использования удельных показателей затрат, в частности затрат на единицу веса конструкции. Для использования этого метода необходимо знать удельную себестоимость конструкции подобного типа (Су) и вес новой конструкции. При этом укрупненном расчете себестоимость новой конструкции (С) определяется как :
C = Су q1 ,
где Су - себестоимость, приходящаяся на единицу веса существующих гидроприводов однотипных валковых подач;
q1 – проектируемый вес новой конструкции.
2. Определение себестоимости по чистой массе.
,
где G – чистая масса конструкции, без покупных и кооперированных поставок, кг;
= 1,3 – коэффициент конструктивной сложности;
Н - затраты на производство приходящихся на 1 кг чистой массы однотипной по технологии конструкции;
М – стоимость одного килограмма чистой массы материалов ;
d – стоимость покупных узлов и деталей.
В данной формуле различие себестоимости разрабатываемой валковой подачи будет иметь место за счет изменения затрат на проведение конструкторско-технологических работ, возможного изменения коэффициента конструктивной сложности , стоимости используемых для их изготовления материалов, покупных изделий d, а также инфляционного процесса.
При изменении спроса на разработанную валковую подачу также изменится коэффициент изменения затрат на производство валковой подачи (Н) Км.
Определяем себестоимость разрабатываемой валковой подачи укрупненным методом по чистой массе:
С = 3680 (1,3 60 1,1 + 20) + 155737,6 = 545081,6 руб.
6.6 Затраты на проект
руб.
С учетом затрат на налаживание производства и исследование конъюнктуры рынка затраты составят
Сполн = 545081,6 + 545081,6 0,2 + 5 45081,6 0,15 = 746903,97 руб.
6.7 Определение цены гидропривода валковой подачи
Цена представляет собой оценку потребительной стоимости конкретной валковой подачи и подвержена колебаниям вокруг ее стоимости, а колеблется она под влиянием спроса и предложения.
Оценка потребительной стоимости научно-технического продукта одна из функций маркетинговой деятельности. Связь между ценами и потребительскими свойствами товара всегда существует, и лишь их соотношение, а не просто «новое качество» гидропривода может свидетельствовать о потенциальных возможностях валковой подачи сбываться на рынке. Процесс формирования потребительной стоимости может быть представлен несколькими уровнями или этапами. На рисунке 2 представлены четыре уровня формирования потребительной стоимости научно-технического продукта.
Рисунок 2 - Уровни формирования потребительной стоимости продукта
В условиях рынка цена научно-технического продукта – величина переменная. На нее влияют жизненный цикл продукта, конъюнктура рынка, конкуренты, посредники и потребители, перемены курса обмена валют, инфляционный процесс и т.д.
Поэтому для успеха на рынке разрабатываем ценовую политику и постоянно проверяем ее эффективность , изменяя ее по мере необходимости .
Следовательно, вопросы формирования цены возникают в следующих случаях :
- при разработке новой техники и технологии ;
-при выходе на новый рынок.
При определении цены на валковую подачу могут быть применены следующие основные методы:
Определение цены гидропривода валковой подачи, исходя из себестоимости и принятого уровня рентабельности.
Цена определяется исходя из себестоимости и минимально приемлемой для организации доли прибыли в цене.
3. Цена определяется, исходя из общей суммы дисконтированной прибыли за весь срок использования проекта и других параметрах конструктивного решения.
4. Цена определяется на основе изучения спроса, предложения и конкуренции на рынке.
В проекте используем наиболее простой метод, т.е. определяем цену гидропривода валковой подачи, исходя из себестоимости и принятого уровня рентабельности (30 - 50%)
Lh= C + П ,
где П - прибыль на валковую подачу , руб., определенную по формуле:
где Р - принятый уровень рентабельности производства подачи валковой.
Мо – стоимость материалов, руб;
Мо = G М = 3680 20 = 73600 руб.
руб
Следовательно:
Ц = 746903,97 + 207026,2 = 953930,2 руб.
Определяем оптовую цену с учетом того, что НДС составит 18 % от цены.
Цопт = Ц + Нндс = 953930,2 + 953930,20,18 = 1125637,5 руб.
6.8 Развертывание коммерческого производства
В рыночных условиях хозяйствования, для развертывания коммерческого производства, необходимо иметь достаточный объем информации для принятия окончательного решения о целесообразности выпуска гидропривода валковой подачи. Когда предприятие приступает к развертыванию коммерческого производства, ему предстоят значительные капиталовложения в производство гидропривода валковых подач.
Необходимо строить или брать в аренду целый производственный комплекс.
Кроме того, предприятию потребуются значительные усилия и издержки на рекламу и стимулирование сбыта. При выходе на рынок с новым научно-техническим продуктом предприятие должно решить КОГДА, ГДЕ и КАК его предложить.
6.9 Оценка эффективности проекта
Расчет эффективности проекта представляет собой описание ожидаемых результатов от запланированных капиталовложений. Для оценки эффективности валковой подачи используем показатели, принятые в мировой практике.
Определяем чистый дисконтированный доход, который предполагает, что организация заранее задает минимально допустимую ставку процента, при котором капиталовложения могут считаться эффективными. Такая «заданная» ставка процента называется расчетной ставкой предприятия.
Базисом для установления расчетной ставки процента может быть ставка процента на заемный капитал, который предприятие само должно выплачивать своим кредиторам.
Чистый дисконтированный доход определяется как сумма текущих дисконтированных доходов (ТЧДД) за весь период реализации проекта, приведенная к начальному шагу, или как превышение интегральных результатов над интегральными затратами.
Текущий ЧДД - это разность между дисконтированной прибылью ( Пq общ.) каждого года и величиной капиталовложений (платежи по капиталовложениям каждого года)
Тогда:
В проекте используем расчетные данные, произведенные выше и определяем ЧДД как:
где Rt - результаты , достигнутые на t-ом шаге расчета (в нашем проекте – это объем продаж в t-ом году;
Зt - затраты капиталовложений, осуществляемых на t-ом шаге (году) ;
Т - горизонт (количество лет) расчета.
t - номер шага расчета (t = 0,1,2,3…..Т)
Е - норма дисконта, равная приемлемой для инвестора норме дохода на капитал.
К- сумма дисконтированных капиталовложений.
Выражение (1+Е)t представляет собой коэффициент дисконтирования, который зависит от нормы дисконта ( процентной ставки) и количества лет расчета-Т.
В формуле разность (Rt - Зt) представляет собой эффект, достигнутый на t-ом шаге расчета.
При этом:
Rt = Qпр.t Цt
Зt = Qпр.t Сt,
где Qпр.t – объем производства и реализации на t-ом шаге расчета, шт.;
Цt – цена единицы изделия на t-ом шаге расчета, руб.;
Сt – себестоимость единицы изделия на t-ом шаге расчета, руб.
Для проведения расчетов ЧДД используем результаты проведенных маркетинговых исследований рынка (таблица 6.1), а также расчет себестоимости и цены гидропривода валковой подачи и сводим в таблицу 6.3.
Таблица 6.3 - Объем производства и, цена и средние переменные издержки на ед. изделия на t-ом шаге расчета.
№
п/п
Наименование показателя
Шаг расчета (год)
2010
2011
2012
2013
2014
1
Объем реализации,
шт./год
30
36
40
45
55
2
Цена реализации, тыс.руб.
1125,6
1125,6
1125,0
1123
1120
3
Средние переменные издержки , тыс.руб.
560,2
560,2
560,0
560,0
560
1 Определяем капиталовложения в производственные фонды.
Капитальные вложения, необходимые для производства гидропривода валковых подач «К» могут быть определены исходя из коэффициента эффективности (прибыльности) капиталовложений (Ен), объема производства и нормы дисконта.
= 0,3÷0,4
2 Определение ликвидационной стоимости проекта.
После определения жизненного цикла проекта, определяем его ликвидационную стоимость (Лд). Ликвидационная стоимость проекта характеризуется возвратом средств от продажи валковых подач по остаточной стоимости. Ориентировочно остаточную стоимость валковых подач можно рассчитать по стоимости материалов и комплектующих , уменьшенной на 85-90% с последующим дисконтированием (Лд) или по формуле :
3 Расчет добавочной прибыли от капиталовложений (тыс.руб.)
Для определения эффективности проекта определяем добавочную прибыль от возможной реализации гидропривода валковых подач.
Таблица 6.4 - Добавочная прибыль от возможной реализации валковых подач.
№
п/п
Наименование показателя
Шаг расчета (год)
2010
2011
2012
2013
2014
1
Выручка от реализации
33768
40608
45120
50760
62150
2
Переменные издержки
16806
20167,2
22400
25200
30800
3
Величина покрытия
16962
20440,8
22720
25560
31350
4
Расходы на рекламу
508,86
1022
1136
1278
1567,5
5
Добавочная прибыль
16453
19418,8
21584
24282
29782,5
После определения добавочной прибыли проводим расчет дисконтированной стоимости (эффективности разработанного гидропривода валковой подачи) с учетом коэффициента дисконтирования. Чистую дисконтированную стоимость определим перемножением соответствующей величины добавочной прибыли от капиталовложений на коэффициент дисконтирования.
4 Эффективность разработанного проекта
Шаг (год)
расчета
Платежи по капиталовложениям, тыс.руб.
Добавочная прибыль от кап.вложений,
тыс.руб.
Ряд платежей и поступлений ,тыс.руб.
Процентные ставки –6%
Коэф-т
дисконтирования
Текущая дисконтированная стоимость , тыс.руб.
0
-17641,3
-17641,3
-17641,3
2010
+16453
16453
0,9434
15521,8
2011
+19418,3
19418,3
0,89
17282,3
2012
+21584
21584
0,8396
18121,9
2013
+24282
24282
0,7921
19233,8
2014
+375,3
+29782,5
30157,8
0,7473
22536,9
Всего
-17266,0
111519,8
111895,1
+75055,4
6.10 Определение индекса доходности (рентабельности)
Показатель срока окупаемости характеризует степень эффективности проекта.
(
где: - общая величина капиталовложений
Вывод. Если , то проект эффективен, следовательно, принимается к реализации.
6.11 Определение срока окупаемости капиталовложений
Показатель срока окупаемости характеризует степень эффективности проекта
6.12 Анализ безубыточности предприятия
Сущность этого метода состоит в том , что при установлении цены на валковую подачу за основу принимается прогнозируемый спрос на нее и себестоимость ее изготовления Контрольной точкой является точка пересечения линии доходов-расходов при заданной цене. Такую точку называют «точкой безубыточности». Она определяет тот объем продаж, которого надо добиться при анализируемом (или заданном ) уровне цены, чтобы убытки изготовления были нулевыми.
Точка безубыточности (Тб) используется для характеристики степени устойчивости проекта, а аналитический метод предусматривает расчет по формуле:
где W - условно-постоянные расходы в структуре себестоимости валковой подачи, руб.
Ц - цена валковой подачи , руб.
V - величина переменных издержек в себестоимости валковой подачи, руб.
Q - объем производства и продаж по периодам в соответствии с исследованным рынком, шт./год.
шт
Принимаем Тб = 10 штук.
Если же предприятие сможет обеспечить продажу большего объема своей продукции, то оно начнет получать от этого вида деятельности прибыль. В процессе реализации гидропривода валковой подачи важно знать разницу между безубыточным объемом продаж и максимальным , который может быть достигнут согласно исследованиям рынка и производственной мощности предприятия. Эта разница носит название запаса финансовой безопасности.
Графический метод построения точки безубыточности позволяет наглядно представить процесс погашения капиталовложений (представлен на экономическом листе графической части проекта).
Таблица 6.6. Основные расчетные показатели эффективности проекта.
№п/п
Наименование показателей
Величина
показателя
1
Чистый дисконтированный доход, тыс.руб.
75055,4
2
Индекс доходности, коэффициент.
4,2
3
Срок окупаемости капиталовложений, лет
1,2
4
Выручка от реализации, тыс.руб.
(Первый шаг расчета)
33768
5
Точка безубыточности, шт.
10
1
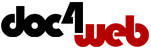
Нравится материал? Поддержи автора!
Ещё документы из категории промышленность, производство:
Чтобы скачать документ, порекомендуйте, пожалуйста, его своим друзьям в любой соц. сети.
После чего кнопка «СКАЧАТЬ» станет доступной!
Кнопочки находятся чуть ниже. Спасибо!
Кнопки:
Скачать документ