Детали машин
СОДЕРЖАНИЕ
Выбор электродвигателя и кинематический расчет привода.
3
Расчет зубчатых колес редуктора
4
Предварительный расчет валов
6
Конструктивные размеры шестерни и колеса
7
Конструктивные размеры корпуса редуктора
7
Расчет цепной передачи
8
Первый этап компоновки редуктора
10
Проверка долговечности подшипника
11
Второй этап компоновки редуктора
14
Проверка шпоночного соединения
15
11. Уточненный расчёт валов
15
12. Выбор сорта масла
17
13. Сборка редуктора
18
14. Список используемой литературы
19
1. Выбор электродвигателя и кинематический расчёт
Технические данные
P2=4,5 кВт
n2=100 об/мин
1.1 Определение общей КПД установки
, где
=0,98 - КПД цепной передачи
=0,99 - Две пары подшипников качения
=0,92 - КПД зубчатой передачи
=0,99 - КПД муфты
1.2 Определяем требуемую мощность электродвигателя.
1.3 Определяем требуемую частоту вращения.
где Uц.п. =3 ;Uред =4
nдв =nз×Uобщ=100×12=1200
1.4 Выбираем тип двигателя по таблице П1. Это двигатель 4А100L4УЗ с ближайшим большим значением мощности 4 кВт, с асинхронной частотой вращения 1500 об/мин и S =4,7%. Этому значению номинальной мощности соответствует частота вращения nном =1500-47=1453 об/мин.
1.5 Определяем общее передаточное число установки.
1.51 По ГОСТ 2185-66 принимаем Uред =4
1.6 Пересчитываем Uц.п.
1.7 Определяем вращающий момент на валах
1.71 Вращающий момент на валу шестерни
1.72 Вращающий момент на валу колеса
2. Расчет зубчатых колёс редуктора
2.1 Выбор материалов для передач
Так как в задании нет особых требований в отношении габаритов передачи, выбираем материалы со средними механическими характеристиками по таблице 3.3: для шестерни сталь 45, термообработка – улучшение, твёрдость НВ 230; для колеса сталь 45, термообработка – улучшение, но твёрдость на 30 единиц ниже – НВ 200.
Допускаемые контактные напряжения
где н lim b – предел контактной выносливости при базовом числе циклов. По табл. 3.2[1] для углеродистых сталей с твёрдостью поверхностей зубьев менее
НВ 350 и термообработкой (улучшение)
КHL – коэффициент долговечности; при числе циклов нагрузки больше базового, что имеет место при длительной эксплуатации редуктора, принимают КHL=1; [n]H=1,1
2.2Принимаем допускаемое напряжение по колесу
Для колеса
Тогда расчетное допускаемое напряжение
Коэффициент нагрузки , несмотря на симметричное расположение колес относительно опор, примем выше для этого случая, так как со стороны клиноременной передачи действуют силы, вызывающие дополнительную деформацию ведомого вала и ухудшающие контакт зубьев. Принимаем предварительно по табл. 3.1[1], как в случае несимметричного расположения колес, значение =1,25.
Принимаем коэффициент ширины венца по межосевому расстоянию
Межосевое расстояние из условия контактной выносливости активной поверхности зубьев (по формуле (3.8) [1]).
Здесь принято . Ближайшее стандартное значение . Нормальный модуль зацепления
; принимаем (стр.36 [1])
2.3 Угол наклона зубьев . Определим число зубьев шестерни и колеса:
; принимаем z1=28
тогда принимаем z2=112
2.4 Основные размеры шестерни и колеса:
2.41 Диаметры делительные:
; .
Проверка: .
2.42 Диаметры вершин зубьев:
;
ширина колеса ;
ширина шестерни .
2.43 Определяем коэффициент ширины шестерни по диаметру:
.
2.44 Окружная скорость колес и степень точности передачи
м/с,
где - ω1=
При такой скорости следует принять 8-ю степень точности (стр.32 [1])
2.5 Коэффициент нагрузки
Значения даны в табл.3.5[1]: при , твердости и несимметричном расположении колес относительно опор с учетом изгиба ведомого вала от натяжения цепной передачи .
По табл. 3.4[1] при и 8-й степени точности . По табл.
3.6[1] для прямозубых колес при имеем . Таким образом,
.
2.6 Проверка контактных напряжений по формуле (3.6)[1]:
2.7Силы, действующие в зацеплении:
2.71 Окружная ;
2.72 Радиальная ;
2.73 Осевая
2.8 Проверяем зубья на выносливость по напряжениям изгиба по формуле (3.25)[1]:
Здесь коэффициент нагрузки .
По табл. 3.7[1] при , твердости и несимметричном расположении зубчатых колес относительно опор . По табл. 3.8[1] . Таким образом, коэффициент .
2.81–коэффициент прочности зуба по местным напряжениям, зависящий от эквивалентного числа зубьев :
у шестерни ;
у колеса .
При этом и (стр.42 [1]).
Допускаемое напряжение – по формуле (3.24)[1]:
.
По табл. 3.9[1] для стали 45 улучшенной при твердости .
Для шестерни ;
для колеса .
–коэффициент запаса прочности(3.24)[1], где ; . Следовательно, .
Допускаемые напряжения:
для шестерни ,
для колеса .
Находим отношения ;
для шестерни ;
для колеса .
Дальнейший расчет следует вести для зубьев колеса, для которого найденное отношение меньше.
Определяем коэффициенты и КF
β=1, т.к. β=0
Проверяем прочность зуба колеса по формуле (3.25)[1]:
Условие прочности выполнено.
3. Предварительный расчет валов редуктора
Предварительный расчет проведем на кручение по пониженным допускаемым напряжениям.
Ведущий вал:
диаметр выходного конца при допускаемом напряжении (учитывая влияние изгиба вала от натяжения ремней привода) по формуле (6.16)[1]
.
Принимаем ближайшее большее значение из стандартного ряда(ГОСТ 6636-69): .
Примем под подшипниками . Шестерню выполним за одно целое с валом.
Ведомый вал:
Учитывая влияние изгиба вала от возможных натяжений, принимаем .
Диаметр выходного конца вала
.
Принимаем ближайшее большее значение из стандартного ряда: . Диаметр вала под подшипниками принимаем , под зубчатым колесом .
Диаметры остальных участков назначают исходя из конструктивных соображений при компоновке редуктора.
4. Конструктивные размеры шестерни и колеса
Шестерню выполняем за одно целое с валом, ее размеры: , , .
Колесо кованое, , , .
Диаметр ступицы ; длина ступицы , из конструктивных соображений принимаем .
Толщина обода , принимаем .
Толщина диска .
5. Конструктивные размеры корпуса редуктора
5.1 Толщина стенок корпуса и крышки:
, принимаем ; , принимаем .
5.2 Толщина фланцев поясов корпуса и крышки:
5.21 Верхний пояс корпуса и пояс крышки:
;
;
5.22 Нижний пояс корпуса
, принимаем .
5.3 Диаметры болтов:
5.31 Фундаментных , принимаем болты с резьбой М20;
5.32 Крепящих крышку к корпусу у подшипников , принимаем болты с резьбой М16;
5.33 Соединяющих крышку с корпусом , принимаем болты с резьбой М10.
6. Расчет цепной передачи
Выбираем приводную роликовую однорядную цепь (табл. 7.15)
6.1 Вращающий момент на ведущем валу:
Т3 = Т2 =97 Н∙мм
6.2 Передаточное отношение было принято Uц =3,6
6.3 Число зубьев:
6.31 Ведущей звёздочки
6.32 Ведомой звёздочки
Принимаем
Тогда фактическое
6.4 Отклонение δ%
, что допустимо.
6.5 Расчётный коэффициент нагрузки (табл.7.38)
,
Где Кэ =динамический коэффициент при спокойной нагрузке; Ка =1 учитывает влияние межосевого расстояния; Кн =1-учитывает влияние угла наклона линии центров; Кр= 1,25 при периодическом регулировании натяжения цепи, Кр - учитывает способ регулирования цепи; Ксм =1 при непрерывной смазке; Кп =учитывает продолжительность работы в сутки, при односменной работе Кп =1.
6.6 Частота вращения звездочки (7.18)[1]
,
где
Среднее значение допускаемого давления при
Шаг однорядной цепи:
Подбираем по табл. 7.15[1] цепь ПР 15,875-22,70 по ГОСТ 13568-75, имеющую t =31,75 мм; разрушающую нагрузку
6.7 Скорость цепи.
6.8 Окружная сила.
6.9 Давление в шарнире проверяем по формуле (7.39)[1]
,
уточняем по тал 7.18 допускаемое давление [p]= 34[1+0.01(Z3-17)] =36,38.
Условие выполнено.
6.10 Определяем число звеньев по формуле (7.36)[1]
где at ==50;
Тогда
округляем до чётного числа
6.11 Уточняем межосевое расстояние цепной передачи по формуле (7.37)[1]
=
Для свободного провисания цепи предусматривает возможность уменьшения межосевого расстояния на 0,4% т.е. на
6.12 Определим диаметры делительных окружностей звёздочек (см формулу(7.34)[1]
6.13 Определим диаметры наружных поверхностей звездочек (7.35)[1]
,
где d1 =10,16 мм- диаметр ролика цепи (табл.7.15)[1]
6.14 Силы, действующие на цепь:
6.14.1 Окружная
6.14.2 От центробежных сил
6.14.3 От провисания
6.15 Расчетная нагрузка на валы
6.16 Проверяем коэффициент запаса прочности
6.17 Размеры ведущей звездочки:
ступица звездочки dст =;
принимаем =40 мм
толщина диска звёздочки 0,93 Ввн =,
где Ввн –расстояние между пластинками внутреннего звена
6.18 Размеры ведомой звездочки
, принимаем =60 мм
7. Первый этап компоновки редуктора
Компоновку обычно проводят в два этапа. Первый этап служит для приближенного определения положения зубчатых колес относительно опор для последующего определения опорных реакций и подбора подшипников.
Компоновочный чертеж выполняем в одной проекции — разрез по осям валов при снятой крышке редуктора; желательный масштаб 1:1, чертить тонкими линиями.
Примерно посередине листа параллельно его длинной стороне проводим горизонтальную осевую линию; затем две вертикальные линии — оси валов на расстоянии .
Вычерчиваем упрощенно шестерню и колесо в виде прямоугольников; шестерня выполнена за одно целое с валом; длина ступицы колеса равна ширине венца и не выступает за пределы прямоугольника.
Очерчиваем внутреннюю стенку корпуса:
а) принимаем зазор между торцом шестерни и внутренней стенкой корпуса ;
б) принимаем зазор от окружности вершин зубьев колеса до внутренней стенки корпуса ;
в) принимаем расстояние между диаметром окружности вершин зубьев шестерни и внутренней стенкой корпуса (наружный диаметр подшипника меньше диаметра вершин зубьев шестерни).
Предварительно намечаем радиальные шарикоподшипники средней серии; габариты подшипников выбираем по диаметру вала в месте посадки подшипников и .
По табл. П3[1] имеем:
Условное обозначение подшипника
d
D
B
Грузоподъемность, кН
Размеры, мм
C
C0
304
307
20
35
52
80
15
21
15,9
33,2
7,8
18
Решаем вопрос о смазке подшипников. Принимаем для подшипников пластичную смазку. Для предотвращения вытекания смазки внутрь корпуса и вымывания пластичной смазки жидким маслом из зоны зацепления устанавливаем мазеудерживающие кольца. Их ширина определяет размер .
Замером находим расстояния на ведущем валу и на ведомом валу .
Замером находим расстояние , определяющее положение шкива относительно ближайшей опоры ведомого вала. Примем окончательно .
8. Проверка долговечности подшипника.
Ведущий вал. Из предыдущих расчетов имеем и ;из первого этапа компоновки .
Реакции опор:
вертикальная плоскость:
в плоскости XZ
В плоскости YZ
Проверка:
.
Суммарные реакции:
Намечаем радиальные шариковые подшипники 304 (табл. П3)[1]:
;С=1939 кН и С0=7,8 кН.
Эквивалентная нагрузка по формуле (9.3)[1]
,
в которой радиальная нагрузка Pr1=500H; осевая нагрузка Pa=0H; V=1 (вращается внутреннее кольцо); Кб=1 (табл. 7.2)[1]; Кт=1.05.
Отношения ;
Отношение
.
Расчетная долговечность, млн. об. :
Расчетная долговечность, ч,
.
Ведомый вал.Из первого этапа компоновки и ;
Реакции опор:
В плоскости XZ
Проверка:
В плоскости YZ
Проверка:
Суммарные реакции:
;
.
Выбираем подшипник по более нагруженной опоре 3.
Шариковые радиальные подшипники 307 средней серии(см.П3):
;С=33,2 кН и С0=18 кН.
Отношения ;
Отношение
Расчетная долговечность, млн. об. :
Расчетная долговечность, ч,
;
Для зубчатых редукторов ресурс работы подшипников принимают от 36 000 ч (таков ресурс самого редуктора) до 10 000 ч (минимально допустимая долговечность подшипника). В нашем случае подшипники ведомого вала 304 имеют ресурс , а подшипники ведомого вала 307 имеют .
Строим эпюры:
Ведущий вал:
Ведомый вал:
10. Второй этап компоновки редуктора
Второй этап компоновки имеет целью конструктивно оформить зубчатые колеса, валы, корпус, подшипниковые узлы и подготовить данные для проверки прочности валов и некоторых других деталей.
Вычерчиваем шестерню и колесо по конструктивным размерам, найденным ранее. Шестерню выполняем за одно целое с валом.
Конструируем узел ведущего вала:
а) наносим осевые линии, удаленные от середины редуктора на расстояние . Используя эти осевые линии, вычерчиваем в разрезе подшипники качения;
б) между торцами подшипников и внутренней поверхностью стенки корпуса вычерчиваем мазеудерживающие кольца. Их концы должны выступать внутрь корпуса на 1-2мм от внутренней стенки. Тогда эти кольца будут выполнять одновременно роль маслоотбрасывающих колец. Для уменьшения числа ступеней вала кольца устанавливаем на тот же диаметр, что и подшипники (Ø40мм). Фиксация их в осевом направлении осуществляется заплечиками вала и торцами внутренних колец подшипников;
в) вычерчиваем крышки подшипников с уплотнительными прокладками (толщиной 1мм) и болтами. Болт условно заводится в плоскость чертежа, о чем говорит вырыв на плоскости разъема.
Используем фетровые уплотнения, т. к. допускаемое значение скорости <5м/с.
г) переход вала Ø40мм к присоединительному концу Ø32мм выполняют на расстоянии 10-15мм от торца крышки подшипника.
Длина присоединительного конца вала Ø32мм определяется длиной шкива.
Аналогично конструируем узел ведомого вала.
На ведущем и ведомом валах применяем шпонки призматические со скругленными торцами по ГОСТ 23360-78. Вычерчиваем шпонки, принимая их длины на 5-10мм меньше длин ступиц.
Непосредственным измерением уточняем расстояния между опорами и расстояния, определяющие положение зубчатых колес относительно опор. При значительном изменении этих расстояний уточняем реакции опор и вновь проверяем долговечность подшипников.
11. Проверка прочности шпоночных соединений
Шпонки призматические со скругленными торцами. Размеры сечений шпонок и пазов и длины шпонок по ГОСТ 23360-78.
Материал шпонок - сталь 45 нормализованная.
Напряжение смятия и условие прочности по формуле (6.22)[1]
Допускаемое напряжение смятия при стальной ступице , при чугунной ступице
Ведущий вал
;
Условие выполнено.
Ведомый вал
;длина шпонки ; момент на ведущем валу ;
Условие выполнено.
12. Уточненный расчет валов
Примем, что нормальные напряжения от изгиба измеряются по симметричному циклу, а касательные от кручения – по отнулевому (пульсирующему).
Уточненный расчет состоит в определении коэффициентов запаса прочности n опасных сечений и сравнении их с требуемыми (допускаемыми) значениями [n]. Прочность соблюдена при n[n].
Будем производить расчет для предположительно опасных сечений каждого из валов.
Ведущий вал.
Материал вала тот же, что и для шестерни (шестерня выполнена заодно с валом), т.е. сталь 45, термообработка улучшение.
По табл. 3.3 при диаметре заготовки до 90мм (в нашем случае da1=78,96 мм) среднее значение
Предел выносливости при симметричном цикле изгиба
.
Предел выносливости при симметричном цикле касательных напряжений
Сечение А–А. В этом сечении при передаче вращающего момента от электродвигателя через муфту возникают только касательные напряжения. Концентрацию напряжений вызывает наличие шпоночной канавки.
Коэффициент запаса прочности
,
где амплитуда и среднее напряжение отнулевого цикла
.
При d=32 мм; b=10 мм; t1=5 мм
;
.
Принимаем , и .
После подстановки
.
Такой большой коэффициент запаса прочности объясняется тем, что диаметр вала был увеличен при конструировании для согласования по размеру с диаметром вала электродвигателя.
По той же причине проверять прочность в сечениях Б–Б и В–В нет необходимости.
Ведомый вал.
Материал вала – сталь 45 нормализованная, .
Пределы выносливости и .
Сечение А–А.
Изгибающий момент в горизонтальной плоскости
;
изгибающий момент в вертикальной плоскости
;
суммарный изгибающий момент в сечении А–А
.
Момент сопротивления кручению (;)
.
Момент сопротивления изгибу
.
Амплитуда и среднее напряжение цикла касательных напряжений
.
Амплитуда нормальных напряжений изгиба
; среднее напряжение .
Коэффициент запаса прочности по нормальным напряжениям
.
Коэффициент запаса прочности по касательным напряжениям
.
Результирующий коэффициент запаса прочности для сечения А–А
.
13. Посадки зубчатого колеса, звездочки и подшипников
Посадки назначаем в соответствии с указаниями, данными в табл. 8.11[1].
Посадка зубчатого колеса на вал Н7/р6 по ГОСТ 25347-82.
Посадка звездочки цепной передачи на вал редуктора Н7/h6.
Шейки валов под подшипники выполняем с отклонением вала к6. Отклонения отверстий в корпусе под наружные кольца по Н7.
Остальные посадки назначаем, пользуясь данными табл. 8.11[1].
14. Выбор сорта масла
Смазка зубчатого зацепления производится окунанием зубчатого колеса в масло, заливаемое внутрь корпуса до уровня, обеспечивающего погружение колеса примерно на 10 мм. Объем масляной ванны Vм определяем из расчета 0,25 дм3 масла на 1 кВт передаваемой мощности: .
По табл. 10.8[1] устанавливаем вязкость масла. При скорости рекомендуемая вязкость .Принимаем масло индустриальное И-30А по ГОСТ 29799-75.
Подшипники смазываем пластичной смазкой, которую закладывают в подшипниковые камеры при сборке. Периодически смазку пополняют через пресс-масленки. Сорт смазки – УТ-1.
15. Сборка редуктора
Перед сборкой внутреннюю полость корпуса редуктора тщательно очищают и покрывают маслостойкой краской.
Сборку производят в соответствии с чертежом общего вида редуктора, начиная с узлов валов:
на ведущий вал насаживают мазеудерживающие кольца и шарикоподшипники, предварительно нагретые в масле до 80-100 С;
в ведомый вал закладывают шпонку 181150 и напрессовывают зубчатое колесо до упора в бурт вала; затем надевают распорную втулку, мазеудерживающие кольца и устанавливают шарикоподшипники, предварительно нагретые в масле.
Собранные валы укладывают в основание корпуса редуктора и надевают крышку корпуса, покрывая предварительно поверхности стыка корпуса и крышки спиртовым лаком. Для центровки устанавливают крышку на корпус с помощью двух конических штифтов; затягивают болты, крепящие крышку к корпусу.
После этого на ведомый вал надевают распорное кольцо, в подшипниковые камеры закладывают пластичную смазку, ставят крышки подшипников с комплектом металлических прокладок; регулируют тепловой зазор, подсчитанный по формуле (7.1)[1]. Перед постановкой сквозных крышек в проточки закладывают войлочные уплотнения, пропитанные горячим маслом. Проверяют проворачиванием валов отсутствие заклинивания подшипников (валы должны проворачиваться от руки) и закрепляют крышки винтами.
Далее на конец ведомого вала в шпоночную канавку закладывают шпонку, устанавливают звездочку и закрепляют ее торцовым креплением; винт торцового крепления стопорят специальной планкой.
Затем ввертывают пробку маслоспускного отверстия с прокладкой и жезловый маслоуказатель. Заливают в корпус масло и закрывают смотровое отверстие крышкой с прокладкой; закрепляют крышку болтами.
Собранный редуктор обкатывают и подвергают испытанию на стенде по программе, устанавливаемой техническими условиями.
Список используемой литературы
1.Курсовое проектирование деталей машин: Учебно-справочное пособие для
ВУЗов / С.А.Чернавский и др.-М.: Машиностроение, 1984.
2 Шейнблид А.Е. Курсовое проектирование деталей машин: Учебное пособие для техникумов.-М.: Высшая школа, 1991.
Батманов А.В. гр. Т-32
Незаконное копирование тиражирование преследуется по закону All right received
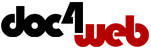
Нравится материал? Поддержи автора!
Ещё документы из категории технология:
Чтобы скачать документ, порекомендуйте, пожалуйста, его своим друзьям в любой соц. сети.
После чего кнопка «СКАЧАТЬ» станет доступной!
Кнопочки находятся чуть ниже. Спасибо!
Кнопки:
Скачать документ