Отчет по слесарно-механической практике
СЛЕСАРНЫЕ РАБОТЫ.
Основные инструменты, применяемые при плоскостной разметке. Для нанесения рисок и кернения при разметке применяют чертилки, рейсмусы и кернеры.
Чертилкой с закаленным и остро заточенным концом наносят на поверхности детали разметочные риски. При проведении рисок чертилка должна иметь двойной наклон: один – в сторону от линейки и другой – по направлению перемещения чертилки. Риску следует проводить только один раз ; она должна быть как можно тоньше.
Рейсмус, или чертилка на штативе, служит для нанесения горизонтальных и вертикальных рисок, а также для проверки заготовок, устанавливаемых на разметочной плите на кубиках или других приспособлениях.
Кернер служит для нанесения вдоль рисок небольших конических углублений (керн), обозначающих разметочные риски, их пересечения и центры окружностей размечаемых заготовок и деталей. Кернерование производят для того, чтобы разметочные риски были хорошо видны.
Кернер берут тремя пальцами левой руки и с наклоном от себя острым концом прижимают к намеченной на риске точке так, чтобы острие кернера совпало с серединой риски. Перед ударом молотком кернер ставят в отвесное положение, А затем фиксируют упором пальца в деталь и наносят по кернеру легкий удар молотком весом 50 – 100 г.
Разметочные циркули используют для разметки окружностей и дуг, деления окружностей и отрезков на части и других геометрических построений при разметке заготовки. Их применяют также для переноса размеров с измерительной линейки на заготовку.
Измерительные инструменты. Для измерения при разметке длин применяют стальные измерительные линейки с миллиметровыми деле-
ниями. Для прочеркивания прямых рисок рекомендуется пользоваться стальной линейкой со скошенной стороной; такую линейку прикладывают скошенной стороной непосредственно к размечаемой детали и переносят с нее размеры. При измерениях больших длин рекомендуется пользоваться стальной рулеткой.
При откладывании размеров по вертикали удобно пользоваться масштабной линейкой с подставкой. Точность измерения с помощью этой линейки – 0,5 – 1,0 мм.
Угловой штангенциркуль позволяет по заданным катетам без вычислений определять гипотенузу прямоугольного треугольника. Этим штангенциркулем удобно пользоваться в тех случаях, когда нужно откладывать размер между двумя точками, не лежащими в одной плоскости, но связанными между собой размерами L и l.
Подготовка деталей к разметке. Прежде чем приступить к разметке, тщательно проверяют, нет ли у заготовки пороков: трещин, раковин, газовых пузырей, перекосов и других дефектов, а также сверяют с чертежом размеры и припуски на обработку. Заготовки из листового, полосового и круглого материала обязательно должны быть отрихтованы на специальной плите ударами молотка или под прессом.
До установки заготовки или детали на разметочную плиту те поверхности, на которых должны быть нанесены разметочные риски, покрывают мелом, разведенным вводе до густоты молока; в этот раствор добавляют столярный клей (для связи) и сиккатив (для быстрого высыхания). Поверхности чисто обработанных заготовок окрашивают раствором медного купороса. После высыхания раствора на поверхности детали остается тонкий и очень прочный слой меди, на котором хорошо видны разметочные риски.
Разметочные детали приходится окрашивать, потому что чертилка, рейсмус или циркуль оставляют на неокрашенных поверхностях очень тусклый след. Если размечаемые места покрыть одним из вышеуказанных растворов, то риски на фоне краски отчетливо видны и сохраняются продолжительное время.
Риски обычно наносят в следующем порядке: сначала все горизонтальные риски, затем вертикальные, после этого наклонные риски и в последнюю очередь – окружности, дуги и закругления.
Пространственная разметка применяется для графических построений, осуществляемых на поверхностях заготовок и деталей, расположенных в разных плоскостях под разными углами друг к другу. По своим приемам пространственная разметка существенно отличается от плоскостной. Трудность пространственной разметки заключается в том, что слесарю приходится не просто размечать отдельные поверхности детали, расположенные в различных плоскостях и под различными углами друг к другу, но и увязывать разметку этих поверхностей между собой.
Правка. Инструмент, применяемый при правке. Правка - операция, посредством которой устраняются неровности, кривизна или другие недостатки формы заготовок.
Основным оборудованием для ручной правки металлов являются стальные или чугунные правильные плиты, отливаемые, как правило, монолитными. В качестве инструмента для ручной правки используют стальные молотки с круглым бойком; молотки из мягких материалов применяют для правки окончательно обработанных поверхностей, а также для правки заготовок и деталей из цветных металлов и сплавов.
Рубка. Инструменты, применяемые при рубке. Рубка представляет собой операцию холодной обработки металлов резанием. Ударным инструментом при рубке служат слесарные и пневматические молотки, а режущим – зубила, крейцмейсели и канавочники.
Слесарное зубило изготавливается из инструментальной углеродистой стали. Оно состоит из трех частей: ударной, средней и рабочей. Ударная часть выполняется суживающейся кверху, а вершина ее (боек) – закругленной; за среднюю часть зубило держат во время рубки; рабочая часть имеет клиновидную форму. Угол заострения выбирается в зависимости от твердости обрабатываемого материала.
Для наиболее распространенных материалов рекомендуется следующие углы заострения: для твердИзм.
Лист
№ докум.
Подпись
Дата
Лист
1
НАЗВАНИЕ ДОКУМЕНТА
ых материалов (твердая сталь чугун) – 70°; для материалов средней твердости (сталь) – 60°; для мягких материалов (медь, латунь) – 45°; для алюминиевых сплавов – 35°.
Для вырубания узких пазов и канавок пользуются зубилом с узкой режущей кромкой – крейцмейселем. Такое зубило может применяться и для снятия широких слоев металла: сначала прорубают канавки узким зубилом, а оставшиеся выступы срубают широким зубилом.
Слесарные молотки, используемые при рубке металлов, бывают двух типов: с круглым и с квадратным бойком. Основной характеристикой молотка является его масса. Для рубки металлов применяют молотки массой 400…600 г.
Для облегчения труда и повышения его производительности используют механизированные инструменты. Среди них наибольшее распространение имеет пневматический рубильный молоток.
Опиливание. Классификация напильников. Опиливание - операция, при выполнении которой с поверхности заготовки снимается слой металла при помощи режущего инструмента – напильника. Цель опиливания – придание деталям требуемой формы, размеров и заданной шероховатости поверхности.
Классификация напильников. Напильники различаются по числу насечек, профилю сечения и длине. По количеству зубьев, насеченных на 10 мм длины, напильники делятся на 6 классов (0, 1, 2, 3, 4, 5).
В зависимости от выполняемой работы напильники подразделяются на следующие виды: слесарные – общего назначения и для специальных работ, машинные, надфили и рашпили.
Слесарные напильники общего назначения по ГОСТу 1465-69 изготавливают восьми типов: плоские, квадратные, трехгранные, полукруглые, ромбические и ножовочные длиной от 100 до 400 мм с насечкой №0-5. Напильники имеют двойную насечку, образованную способом насекания.
Слесарные напильники для специальных работ предназначаются для удалениИзм.
Лист
№ докум.
Подпись
Дата
Лист
1
НАЗВАНИЕ ДОКУМЕНТА
я весьма больших припусков при опиливании пазов, фасонных и криволинейных поверхностей; для обработки цветных металлов, неметаллических материалов и т. п. В зависимости от выполняемых работ напильники этого вида напильники этого вида делятся на пазовые, плоские с овальными ребрами, брусовки, двухконцевые и др.
Машинные напильники по своей конструкции подразделяются на стержневые, дисковые, фасонные головки и пластинчатые. В процессе работы стержневым напильника сообщается возвратно поступательное движение, дисковым напильникам и фасонным головкам - вращательные, а пластинчатым – непрерывное движение вместе с непрерывно движущейся металлической лентой.
Надфили согласно ГОСТу 1513-67 изготавливаются десяти типов: плоские, трехгранные, квадратные, полукруглые овальные, ножовочные и др. длиной 40, 60 и 80 мм с насечкой 5 номеров. Длина надфиля определяется длиной рабочей части. Ребра плоских надфилей имеют одинарную или двойную насечку. Боковые стороны и верхнее ребро ножовочных надфилей имеют двойную насечку.
Надфили применяются для опиливания небольших поверхностей и узких мест, недоступных для обработки слесарными напильниками.
Рашпили соответственно ГОСТу 6876-54 изготавливают несколько типов: общего назначения, сапожные и копытные. В зависимости от профиля рашпили общего назначения подразделяются на плоские, круглые и полукруглые с насечкой № 1-2 и длиной от 259 до 350 мм.
Шабрение поверхностей. Заточка и заправка шаберов. Заточку шаберов выполняют на заточных станках с соблюдением известных требований безопасности.
В начале затачивают торцовую часть шабера, а затем заточку плоскости. После заточки производят заправку шабера на мелкозернистом бруске или ровной чугунной плите, покрытой жидкой пастой или микропорошоком с машинным маслом.
При заточке торцовой части шабера его берут правой рукой за рукоятку, а левой охватывают стержень на расстоянии 25…30 мм от режущих кромок. Опираясь плоской гранью шабера на подручник, его устанавливают перпендикулярно к периферии заточного круга. Плавным движением правой руки, не отнимая конец шабера от круга, его двигают в горизонтальной плоскости для образования на торцовой части шабера криволинейной режущей кромИзм.
Лист
№ докум.
Подпись
Дата
Лист
1
НАЗВАНИЕ ДОКУМЕНТА
ки.
Заправку (доводку) шаберов с пластинками из твердых спеченных
сплавов производят на заточном круге из мелкого карбида кремния аналогичными приемами, что и заточку. Доводку шаберов на мелкозернистых брусках выполняют в следующем порядке. Поверхность бруска смазывают тонким слоем машинного масла или смачивают водой. Удерживая шабер в вертикальном положении за рукоятку левой рукой и слегка прижимая его к бруску, правой рукой берутся ближе к режущей части и сообщают шаберу колебательные движения по всей криволинейной торцовой поверхности.
Притирка. Материалы, применяемые при притирке. При притирке используют абразивные и смазочные материалы. Под абразивно-доводочными материалами следует понимать такие составы (смеси), под действием которых в процессе доводки происходит съем металла. Основными характеристиками абразивно-доводочных материалов являются твердость, строение, размер и форма зерна.
Наиболее эффективными доводочными средствами являются алмазные пасты, состоящие из 30-40% алмазного порошка и 60-70% оливкового, касторового или прованского масла.
Притиром называется инструмент, которым производят притирку деталей. В зависимости от формы притиры можно разделить на несколько групп: плоские – в виде дисков, плит и брусков; цилиндрические – для доводки и притирки наружных и внутренних цилиндрических поверхностей; притиры для конических поверхностей и специальные притиры.
Материалы, приспособления и инструменты, применяемые при лужении и паянии. Лужение – процесс покрытия поверхности детали (изделия) тонким слоем расплавленного олова или оловянно-свинцовистыми сплавами (припоем). Олово не подвергается окислению, поэтому оно издавна применяется для защиты от коррозии консервные тары, столовых приборов, кухонИзм.
Лист
№ докум.
Подпись
Дата
Лист
1
НАЗВАНИЕ ДОКУМЕНТА
ных приборов, кухонной посуды и других изделий, связанных с хранением, приготовлением пищевых продуктов. Для лужения пищевых котлов и посуды пользуются только чистым оловом марок 01 и 02.
Пайкой называется технологический процесс соединения металлов
в твердом состоянии припоями, которые при расплавлении смачивают паяемые поверхности и проникают в основной металл, заполняя капиллярный зазор между ними и образуя паяный шов.
В промышленном производстве для паяния деталей и изделий применяются печи различных конструкций: индукционные, сопротивления, печи-ванны, при радиационном нагреве – кварцевые лампы, а также газовые горелки, паяльники и др.
Припои делятся на: Мягкие припои состоят из сплавов, которые в своей основе содержат олово и свинец и отличаются низкой температурой плавления – в пределах от 180 до 300°C.
Легкоплавкие припои обладают чрезвычайно низкой температурой плавления. В состав таких припоев в различных количествах вводят свинец, олово, висмут, кадмий, сурьму, индий, ртуть и другие металлы.
Твердые припои представляют собой тугоплавкие металлы и сплавы с температурой плавления от 700 до 1100°С. Они используются в тех случаях, когда необходимо получить высокую прочность соединений.
ТОКАРНЫЕ РАБОТЫ.
Черновое обтачивание цилиндрических деталей.
Чистовое обтачивание.
Торцевая обточка и отрезка.
К плоским торцевым поверхностям предъявляются следующие требования: плоскостность, т. е. отсутствие выпуклости или вогнутости; перпендикулярность к оси; параллельность плоскостей торцов между собой. Перед обработкой торцовых плоскостей заготовку закрепляют в патроне, при этом вылет заготовки должен быть по возможности минимальным.
Для подрезания торцов и уступов применяют резцы: проходной прямой, проходной отогнутый, проходной упорный, а также специальный подрезной (торцовый).
Торец подрезают упорным резцом при поперечной подаче с установкой режущей кромки под небольшим углом (5-10) к торцевой поверхности. Если при подрезании торца проходным упорным резцом приходится срезать большой припуск, то подача в направлении к центру вызывает отжимающую силу, углубляющую резец в торец, в результате чего торец может получиться вогнутым. Чтобы этого не произошло, срезают большую часть припуска несколькими проходами с продольной подачей, а чистовой проход выполняют поперечной подачей от центра.
Плоскость торца после подрезания проверяют прикладыванием к нему ребра линейки или угольника. Перпендикулярность торца к наружной поверхности определяют угольником.
Режимы резания при отрезании.. Подача при отрезании принимается меньшей, чем при наружном обтачивании или подрезании торца. Так, при отрезании заготоИзм.
Лист
№ докум.
Подпись
Дата
Лист
1
НАЗВАНИЕ ДОКУМЕНТА
вок диаметром до 60 мм рекомендуется подача 0,1–0,15 мм/об, при больших диаметрах – до 0,3мм/об. Скорость резания при отрезании на 15–20% меньше чем при наружном точении.
Отрезание происходит в более тяжелых условиях, чем обтачивание, так как резец как бы заклинивается в прорезаемой канавке, что вызывает значительное трение между поверхностями резца и детали. Поэтому при отрезании стальных деталей в качестве смазочно-охлаждающей жидкости применяют минеральное масло или сульфофрезол.
Обработка цилиндрических отверстий.
Цилиндрические отверстия служат рабочими полостями двигателей, насосов, компрессоров, применяют их для подвода смазки или охлаждающей жидкости. По форме цилиндрические отверстия бывают гладкие, ступенчатые и с канавкой; отверстия также могут быть сквозными и глухими.
Предварительно просверленные отверстия или отверстия в заготовках, полученные литьем или ковкой, часто подвергают растачиванию с целью увеличения диаметра, обеспечения высокой точности размера и малой шероховатости.
Растачивание менее производительно, чем сверление, но позволяет получить точные отверстия диаметральный допуск размера до 0,02 мм, и исправить положение оси отверстия. Этот способ является наиболее универсальным способом обработки отверстий на токарном станке.
Расточные резцы. Они бывают: проходные для сквозных отверстий и упорные для глухих отверстий. Применяют также расточные резцы, оснащенные твердосплавной коронкой «улиткой». Расточной резец закрепляют в резцедержателе параллельно оси заготовки. У стандартных резцов режущая кромка расположена на уровне верхней образующей цилиндрической державки и поэтому резец устанавливают ниже центра заготовкИзм.
Лист
№ докум.
Подпись
Дата
Лист
1
НАЗВАНИЕ ДОКУМЕНТА
и.
Расточные оправки (борштанги). Отверстия Ø80-100 мм и более обычно растачивают расточными резцами, которые закрепляют в оправках. Резец в оправке зажимается винтом с торца или с наружной поверхности оправки. В оправке можно крепить как резцы, так и пластины. На оправке выфрезерована канавка, по которой охлаждающая жидкость падает непосредственно на резец. Канавка служит и для стопорения болтами.
Мерные расточные пластины («ножи»). Расточная пластина (нож) имеет размер, соответствующий размеру растачиваемого отверстия. Растачивание пластиной обеспечивает получение отверстия правильной формы за один проход, так как действующие с двух сторон на пластину усилия взаимно уравновешиваются.
Приемы растачивания. Заданную глубину отверстия обеспечивают в процессе растачивания измерением линейкой, штангенглубинометром, шаблоном или настройкой при помощи лимба продольной подачи. Для облегчения обработки на резце наносят риску, соответствующую заданной глубине отверстия. Точность диаметра растачиваемого отверстия обеспечивается так же, как и при наружном точении: пробными проходами с замером штангенциркулем, настройки по лимбу поперечной подачи, по линейке поперечных салазок суппорта, при помощи индикатора, по поперечному упору.
Внутренние торцы и уступы подрезают расточным упорным резцом подачей к центру, для этого расточной резец должен иметь главный угол в плане более 90°.
Широкие внутренние канавки обрабатывают последовательным врезанием на глубину канавки поперечной подачей и расширением канавки продольной подачей. Ширину канавки в отверстии контролируют штангенциркулем и шаблоном. Диаметр выточек измеряют штангенциркулем со специальными губками. К прочитанному на штангенциркуле размеру прибавляют Изм.
Лист
№ докум.
Подпись
Дата
Лист
1
НАЗВАНИЕ ДОКУМЕНТА
двойную ширину ножек (2h).
Обработка конических отверстий.
Конические отверстия растачивают при подаче резца повернутыми верхними салазками суппорта, а также при помощи конусной линейки. Предварительно сверлят отверстие, диаметр которого меньше малого диаметра конуса. Для облегчения растачивания отверстие подготавливают ступенчатым рассверливанием.
Стандартные конические отверстия с небольшим углом (например, конус Морзе) могут быть обработаны набором конических зенкеров и разверток. После сверления отверстия обрабатывают двумя ступенчатыми зенкерами, затем окончательно – конической разверткой с гладкими зубьями. Для обработки стандартных инструментальных внутренних конусов применяют специальный инструмент – двухперый конический зенкер. Короткие внутренние конусы обрабатывают резцом или зенковкой. Конические отверстия под стандартные штифты сверлят специальными коническими сверлами.
В серий ном и массовом производстве конические отверстия контролируют предельными конусными калибрами: пробками и втулками. расстояние между рисками или размер уступа на торце калибра соответствует допуску на конусность. Если одна риска на пробке зашла в контролируемое отверстие, а вторая не вошла, то конус правильный. Аналогично для калибра-втулки с уступом: если торец контролируемого конуса окажется в пределах рисок на уступе, то конус правильный. БолееИзм.
Лист
№ докум.
Подпись
Дата
Лист
1
НАЗВАНИЕ ДОКУМЕНТА
точный контроль конусов при помощи специальных приборов выполняют в измерительных лабораториях.
Нарезание резьбы.
Нарезание резьбы – операция, выполняемая со снятием стружки или методом накатывания, в результате которой образуются винтовые канавки на цилиндрических и конических поверхностях.
Нарезание резьбы плашками. Для нарезания наружной поверхности крепежной резьбы треугольного профиля с шагом до 2 мм применяют плашки. Иногда плашки применяют для калибрования резьбы крупного шага, предварительно нарезанной резцом. Плашка похожа на гайку, изготовленную из инструментальной стали и имеющую такую же резьбу, для нарезания которой она предназначена. Резьбонарезная плашка крепится в ручном плашкодержателе или в самоустанавливающемся плашкодержателе, который вставляют в пиноль задней бабки.
При нарезании резьбы плашкой, закрепленной в ручном плашкодержателе, ее подводят к заготовке, подпирая плашкодержатель торцом пиноли задней бабки; рукоятка плашкодержателя упирается в суппорт. После нарезания двух-трех витков с поджимом дальнейшая подача плашки происходит самонавинчивание.
Стержень под нарезание резьбы плашкой обтачивают на диаметр меньший, чем диаметр нарезаемой резьбы, для компенсирования некоторого выдавливания металла.Изм.
Лист
№ докум.
Подпись
Дата
Лист
1
НАЗВАНИЕ ДОКУМЕНТА
Перед началом нарезания резьбы на конце заготовки протачивают фаску для облегчения захода плашки. нарезание резьбы плашками выполняют со скоростью резания 2 м/мин по стали и чугуну и до 10 м/мин по цветным металлам. В качестве смазки для стали используют эмульсию, минеральное масло, для чугуна – керосин.
По такому же принципу, как и плашки, работают самораскрывающиеся резьбонарезные головки. Скорость резания при нарезании резьбы резьбонарезными головками 15-20 м/мин. Резьбонарезные головки обладают высокой стойкостью.
Нарезание резьбы резцами.
Подготовка заготовки к нарезанию. При обтачивании заготовки под последующее нарезание резьбы учитывают, что при нарезании происходит некоторое выдавливание металла из впадин. Поэтому диаметр вала под резьбу должен быть несколько меньше наружного диаметра резьбы, а диаметр отверстия – больше внутреннего.
Диаметры вала и отверстия при подготовке поверхности под нарезание резьбы определяют по справочникам. В конце резьбового участка протачивают канавку (проточку) для входа резца. Ширина канавки быть не менее шага резьбы. Глубина канавки должна быть больше глубины резьбы на 0,1-0,2 мм.
Установка резца. Резьбовой резец устанавливают точно по центру заготовки: установка ниже центра приводит к искажению профиля, а установка выше центра – к «затиранию» резца. Для получения правильного профиля резьбы резец устанавливают по шаблону.
Шаблон прикладывают к заготовке на уровне ее оси, и резец вводят в профильный врез. Правильное положение режущих кромок резца проверяют на «просвет», а затем резец закрепляют и убирают шаблон.
Нарезание резьбы. Резьбу нарезают за несколько рабочих ходов; после каждого рабочего хода резец выводят из канавки, суппорт возвращают в исходное положение и вновь начинают рабочий ход. Число рабочих ходов и глубина врезания для каждого рабочего хода зависят от шага нарезаемой резьбы и материала резьбового резца.
При нарезании длинных резьб целесообразнИзм.
Лист
№ докум.
Подпись
Дата
Лист
1
НАЗВАНИЕ ДОКУМЕНТА
о возвращать суппорт в исходное положение вручную или автоматической подачей при разомкнутой разъемной гайке. Однако при этом возникает необходимость обеспечить попадание резьбового резца в нитку резьбы после каждого
рабочего хода.
Боковое врезание. Резьбу большого шага (2 мм и более) нарезают не с поперечным, а с боковым врезанием резца, при котором работает только одна режущая кромка. При боковом врезании облегчается процесс резания, повышается качество.
Для осуществления бокового врезания верхние салазки суппорта разворачивают под углом (для метрической резьбы =30°) относительно своего нормального положения. Врезание осуществляют рукояткой верхних салазок суппорта. Последние один - два чистовые рабочие ходы выполняют с поперечной подачей. В момент врезания резьбовой ре резец под действием осевой силы несколько отжимается, и первый виток резьбы получается более полным, чем остальные. Последний виток также получается более полным.
Нарезание левой резьбы осуществляют при вращении ходового винта в сторону, противоположную вращению шпинделя. Для этого переключают механизм реверсирования вращения ходового винта - транзель. При нарезании левых резьб врезание производят в зарезьбовную канавку, а суппорт с резцом перемещается слева направо.
Режимы резания при нарезании резьбы резцом. Глубина резания определяется числом проходов. Подача при нарезании резьбы равняется шагу резьбы, а при резании многозаходной резьбы – ходу (H = KS, где K – число заходов).
Скорость резания зависит от обрабатываемого материала резьбового резца: при обработке стали быстрорежущими резцами она составляет 20–35 м/мин, при обработке чугуна 10–15 м/мин, при обработке твердосплавными резцами – соответственно 100–15Изм.
Лист
№ докум.
Подпись
Дата
Лист
1
НАЗВАНИЕ ДОКУМЕНТА
0 и 40–60 м/мин. Для чистовых проходов скорость резания увеличивают в 1,5–2 раза. Для нарезания внутренних резьб скорость резания снижают на 20-30%.
Сверлильные работы.
Изм.
Лист
№ докум.
Подпись
Дата
Лист
1
НАЗВАНИЕ ДОКУМЕНТА
Сверление отверстий.
Сверление – является одним из самых распространенных методов получения отверстия резанием. При сверлении на токарном станке сверло, закрепленное в пиноли задней бабки, подают вручную, только вращением маховика. Чтобы сверло не уходило от горизонтальной оси в начале сверления, торец заготовки предварительно засверливают коротким сверлом большего диаметра, чем просверливаемое отверстие. Важно, чтобы торец заготовки был подрезан, т. е. был перпендикулярен к оси.
Режимы резания при сверлении. Глубиной резания при сверлении является половина диаметра сверла, а при рассверливании - полуразность диаметров отверстия до и после обработки:
tсверл = мм; tрассверл = мм.
Подача при сверлении – это путь сверла за один оборот заготовки.
Фактическая скорость резания, как и при точении, зависит от диаметра сверла и частоты вращения заготовки:
U = м/мин.
Охлаждающая жидкость при сверлении направляется непосредственно в отверстие.
Приемы сверления. В зависимости от точности и величины партии обрабатываемых деталей сверление отверстий может выполняться по разметке с кернением центров отверстий или по кондукторам.
Сверление по разметке при относительно точном положении отверстия производят в два приема: сначала сверлят отверстие предварительно, а затем окончательно. Предварительное сверление выполняют ручной подачей на глубину 0,25 диаметра отверстия, потом сверло поднимают, удаляют стружку и проверяют совпадение окружности надсверленного отверстия с разметочной окружностью. Если они совпадают, то можно продолжать сверление, включив механическую подачу, и довести его до конца. Если же надсверленное отверстие оказалось не в центре, то его исправляют путем прорубания двух-трех канавок от центра с той стороны центрового углубления, куда нужно сместить сверло.
Сверление по кондуктору производят в тех случаях, когда требуется получить долее высокую точность, а также при достаточно большой партии одинаковых деталей. Этот способ намного производительнее сверления по разметке, так как отпадает надобность в самой разметке, в выдержке детали перед ее обработкой; крепление детали производится надежно и быстро; снижается утомляемость рабочего и т. п. Наличие постоянных установочных баз и направляющих инструмент кондукторных втулок повышает точность обработки и обеспечивает взаимозаменяемость деталей.
Сверление сквозных отверстий отличается от сверления глухих отверстий. Когда сверло подходит к выходу из отверстия, сопротивление металла значительно уменьшается, и соответственно должна быть уменьшена подача. Если подачу не уменьшить, то сверло резко опустится, захватит большой слой материала, заклинится и может сломаться. Во избежание этого в конце сверления включают механическую подачу сверла и досверливают отверстие с ручной замедленной подачей.
Сверление глухих отверстий на заданную глубину требует предварительной настройки по специальному приспособлению, имеющемуся на сверлильном станке. Если же такого приспособления нет, пользуются упорной втулкой, закрепленной в нужном месте непосредственно на сверле.
К операции рассверливания прибегают, когда в сплошном металле требуется просверлить отверстие диаметром более 25 мм. С увеличением диаметра сверла утолщается его перемычка и удлиняется поперечная режущая кромка, вследствие чего возрастает осевое давление и процесс резания затрудняется. Поэтому такие отверстия сверлят за два прохода: вначале сверлом меньшего диаметра, а затем рассверливают сверлом большего диаметра.
Рассверливание отверстия ведут при подаче в 1,5-2 раза большей, чем при сверлении в сплошном металле сверлом того же диаметра.
Сверление глубоких отверстий. Глубокими называются отверстия,
длина которых превышает диаметр в пять и более раз. Сверление глубоких отверстий является сложной и трудоемкой операцией. Вследствие малой жесткости длинных сверл под действием сил резания возникает их продольный изгиб, что может привести к искривлению оси отверстия. Кроме того, с увеличением длины отверстия создаются неблагоприятные условия образования сИзм.
Лист
№ докум.
Подпись
Дата
Лист
1
НАЗВАНИЕ ДОКУМЕНТА
тружки и затрудняется извлечение ее из отверстия во время работы. Поэтому для сверления глубоких отверстий применяют специальные – «пушечные» сверла с прямой стружечной канавкой. Сверло хорошо направляется в отверстии благодаря большой поверхности соприкосновения спинки сверла с обратной поверхностью отверстия. Охлаждающая жидкость от насоса поступает к режущей кромке через сквозной канал в сверле, охлаждает режущую кромку сверла и принудительно удаляет стружку.
Применяют также шнековые и четырехленточные сверла, работающие с минимальным «уводом», благодаря большой поверхности соприкосновения ленточек со стенками отверстия.
Точность диаметра отверстий контролируют штангенциркулем с точностью отчета до 0,1 мм или 0,5 мм. Отверстия диаметром Ø120 мм и выше можно измерять микрометрическим нутромером с точностью до 0,01 мм. В крупносерийном и массовом производстве отверстия контролируют предельными калибрами-пробками.
Изм.
Лист
№ докум.
Подпись
Дата
Лист
1
НАЗВАНИЕ ДОКУМЕНТА
Зенкерование и развертывание отверстий.
Зенкерованием называется процесс обработки зенкерами цилиндрических отверстий после отливки, штамповки или после сверления. Зенкерование обеспечивает получение отверстий 4-5 –го класса точности. Зенкером обрабатываются предварительно просверленные отверстия или отверстия, имеющиеся в отливках или поковках. Такая обработка придает отверстию сторгую цилиндрическую форму и чистоту поверхности.
Зенкеры бывают: хвостовые и насадные, цельные и сборные со вставными ножами, быстрорежущие и твердосплавные. По количеству перьев различают трех- и четырехперые зенкеры.
Припуск на зенкерование отверстий оставляют 0,5 – 2 мм на сторону в зависимости от диаметра. Подача при работе зенкерами (мм/об): из быстрорежущей стали 0,3-1,2; твердосплавными зенкерами 0,4-1,5; скорость резания соответственно 20-35 м/мин и 60-200 м/мин.
Развертывание является завершающей операцией обработки отверстий, обеспечивающей высокую точность по диаметру (7-8-й квалитеты) и наименьшую шероховатость обработанной поверхности. Она производится после сверления и зенкерования. При развертывании снимается незначительный слой металла одновременно несколькими зубьями развертки.
Развертывание отверстий можно выполнять на сверлильных или токарных станках, а также вручную. Развертки, применяемые для станочного развертывания отверстий, называются машинными. Машинные развертки отличаются от ручных более короткой рабочей частью. Они закрепляются в качающихся державках, установленных в патроне или непосредственно в шпинделе станка.
Приемы развертывания. Отверстия под развертку сверлят с малым припуском, составляющим по диаметру не более 0,2-0,3 мм на черновую развертку и не более 0,05-0,1 мм на чистовую.
При ручном развертывании развертку закрепляют в воротке, смазывают и затем вводят заборной частью в отверстие, направляя ее так, чтобы оси отверстия и развертки совпали. Убедившись в правильности
Изм.
Лист
№ докум.
Подпись
Дата
Лист
1
НАЗВАНИЕ ДОКУМЕНТА
положения развертки, начинают медленно вращать ее вправо и одновременно слегка нажимают сверху. Вороток нужно вращать медленно, плавно и без рывков. Развертывать отверстия нужно развертками определенного диаметра за один проход и обязательно с одной стороны. Развертывание можно считать законченным, когда рабочая часть развертки полностью пройдет отверстие.
При машинном развертывании на сверлильном станке развертка закрепляется так же, как и сверло, и работа производится аналогично сверлению. Развертывание на сверлильном станке следует вести с автоматической подачей и достаточно хорошей смазкой. Скорость резания при развертывании на станках должны быть в 2-3 раза меньше, чем при сверлении сверлом такого же диаметра. При меньшем числе оборотов повышается не только чистота и точность развертываемого отверстия, но и стойкость развертки.
Подачи при развертывании отверстий в стальных деталях диаметром до 10 мм составляют 0,5-1,2 мм/об., а в остальных деталях диаметром от 10 до 30 мм – 0,5-2 мм/об. При развертывании деталей из чугуна подачи для отверстий диаметром до 10 мм принимаются равными 1-2,4 мм/об., а для отверстий диаметром от 10 до 31 мм – 1-4 мм/об.
В качестве охлаждающей жидкости следует применять при развертывании отверстий в стальных деталях минеральное масло, в деталях из меди, латуни, дюралюминия – мыльную эмульсию; детали из чугуна и бронзы развертывают всухую. Охлаждение применяют как при машинном, так и при ручном развертывании.
Изм.
Лист
№ докум.
Подпись
Дата
Лист
1
НАЗВАНИЕ ДОКУМЕНТА
Нарезание резьбы метчиками.
Нарезание резьбы метчиками. Внутренние резьбы до 20 мм нарезают на токарном станке метчиками. Метчик представляет собой винт такого же диаметра, шага и угла профиля резьбы, что и нарезаемая им резьба, изготавливается из инструментальной стали и имеет продольные стружечные канавки.
Работа резания выполняется заборной, т. е. конической частью метчика, у которой высота режущих зубцов гребенки постепенно повышается. По мере ввинчивания метчика в отверстии заборная часть прорезает резьбовые канавки: каждый зубец срезает небольшую часть припуска, и после прохода заборной части резьба приобретает полный профиль.
По числу перьев различают трехперые и четырехперые метчики. Метчики бывают ручные (слесарные), машинные (станочные) и гаечные с удлиненным хвостовиком.
После подготовки отверстия под резьбу и выбора воротка деталь закрепляют в тисках, черновой метчик смазывают и вертикальном положении (без перекоса) вставляют в нарезаемое отверстие. Надев на метчик вороток, и слегка прижимая его к детали, правой осторожно поворачивают вороток вправо до тех пор, пока метчик не врежется в металл и его положение в отверстии не станет устойчивым. Затем вороток берут двумя руками и плавно вращают. После одного - двух полных оборотов возвратным движением метчика примерно на четверть оборота ломают стружку, что значительно облегчает процесс резания. Закончив нарезание, вращением воротка в обратную сторону вывертывают метчик из отверстия или пропускают его насквозь.
Второй и третий метчики смазывают маслом и вводят в отверстие без воротка; только после того как метчик правильно установится по резьбе, накладывают вороток и продолжают нарезание резьбы.
При нарезании глубоких отверстий необходимо в процессе нарезания два – три раза полнИзм.
Лист
№ докум.
Подпись
Дата
Лист
1
НАЗВАНИЕ ДОКУМЕНТА
остью вывинчивать метчик и очищать его от стружки, так как избыток стружки в канавках может вызвать срыв резьбы.
ФРЕЗЕРНЫЕ РАБОТЫ.
Фрезерование плоскостей.
Фрезерование цилиндрическими фрезами. Цилиндрические фрезы применяют для обработки плоскостей. Цилиндрические фрезы изготавливают цельными из быстрорежущей стали с мелкими и крупными зубьями. По направлению вращения фрезы делят на право- и леворежущие.
Выбор типа и размера фрезы зависит от конкретных условий обработки. Фрезы с крупным зубом применяют для черновой и получистовой обработки плоскостей, фрезы с мелким зубом – для получистовой и чистовой обработки.
Если требуется обработать плоскую поверхность, расположенную под углом к горизонтальной плоскости, то заготовку устанавливают на универсальной поворотной плите. Поворотные плиты позволяют обрабатывать плоскости с любым углом наклона в пределах от 0 до 90°.
Фрезерование торцевыми фрезами. Торцевые фрезы предназначены для обработки плоскостей на вертикально- и горизонтально-фрезерных станках, в отличие от цилиндрических имеют зубья, распложенные на цилиндрической поверхности и на торце.
Для черновой обработки выбирают торцовые насадные фрезы со вставленными ножами. При чистовой обработке следует применять торцовые насадные фрезы с мелкими зубьями. При чистовом фрезеровании стали и чугуна твердосплавными фрезами для получения поверхности с меньшей шероИзм.
Лист
№ докум.
Подпись
Дата
Лист
1
НАЗВАНИЕ ДОКУМЕНТА
ховатостью подачу на зуб уменьшают, а скорость резания соответственно повышают.
Наклонные плоскости и скосы можно фрезеровать торцовыми фрезами с помощью накладной вертикальной головки, которая является специальной принадлежностью горизонтальной плоскостях.
Фрезерование пазов.
Паз – выемка в детали, ограниченная плоскостями или фасонными поверхностями.
Фрезерование пазов дисковыми фрезами. Различают дисковые фрезы цельные и со вставными зубьями. Основным типом дисковых фрез являются трехсторонние. Их применяют для обработки более глубоких пазов. Они обеспечивают более высокий параметр шероховатости боковых стенок паза.
Тип и размер дисковой фрезы выбирают в зависимости от обрабатываемых поверхностей и материала заготовки. Для заданных условий обработки выбирают тип фрезы, материал режущей части, и число зубьев. Для фрезерования легкообрабатываемых материалов и материалов средней трудности обработки с большой глубиной фрезерования применяют фрезы с нормальным и крупным зубом. При обработке труднообрабатываемых материалов и фрезеровании с небольшой глубиной резания рекомендуется применять фрезыИзм.
Лист
№ докум.
Подпись
Дата
Лист
1
НАЗВАНИЕ ДОКУМЕНТА
с нормальным и мелким зубом.
При фрезеровании прямоугольных пазов ширина дисковой фрезы должна быть равна ширине фрезеруемого паза в том случае, когда биение торцовых зубьев равно нулю.
Установка на глубину резания может осуществляться по разметке. Установку на глубину резания по линии разметки осуществляют пробными рабочими ходами. При этом следят затем, чтобы фреза срезала припуск только на половину углублений от кернера.
Фрезерование пазов также может осуществляться концевыми фрезами.
СТРОГАЛЬНЫЕ РАБОТЫ
Строгание плоскостей.
Строгание открытых горизонтальных плоскостей крупных размеров обычно производят двумя суппортами, при этом широкие плоскости целесообразно обрабатывать в такой последовательности: резцом 1 начинают строгание с одного края детали, а резцом 2 в это время на расстоянии одной четверти ширины детали от другого ее края врезаются и строгают с противоположным направлением подачи. После того как резец 2 дойдет до середины обрабатываемой поверхности, а резец 1 займет положение, показанное на рис. 1 б, суппорт с резцом 2 перемещают в крайнее положение и прострагивают участки, оставшиеся необработанными.
При строгании горизонтальных плоскостей на тонких деталях возникают трудности, связанные с их закреплением на станке. В эти случаях прибегают к использованию прижимов либо же временно приклеивают заготовку к столу. В последнем случае опорные поверхности и заготовки зачищают абразивной шкуркой, а затем после удаления ребер, жировых пятен заготовку укладИзм.
Лист
№ докум.
Подпись
Дата
Лист
1
НАЗВАНИЕ ДОКУМЕНТА
ывают на стол станка и заливают по контуру расплавленной канифолью. После застывания канифоли обработку ведут при малых глубинах резания и подачах.
Строгание пазов и канавы.
Пазы обрабатывают при вертикальной подаче резца. Прямоугольные пазы строгают прорезным резцом. При обработке пазов крупных размеров в целом металле вначале прорезают узкий паз, оставляя небольшой припуск по его дну, а затем мерным резцом прорезают и зачищают дно паза.
Последовательность строгания паза трапецеидальной формы: вначале прирезным резцом обрабатывают прямоугольный паз на полную глубину, а затем правым и левым подрезными резцами последовательно прорезают обе наклонные стороны паза; поворотная часть суппорта при этом устанавливается на угол, соответствующий углу наклона стенки паза.
Строгание Т-образных пазов проИзм.
Лист
№ докум.
Подпись
Дата
Лист
1
НАЗВАНИЕ ДОКУМЕНТА
изводится в последовательности: вначале прорезным резцом обрабатывают прямоугольными паз, втором и третьем переходах специальными резцами прорезают правый и левый боковые пазы, в четвертом – двухлезвийным резцом прострагивают фаски и, наконец, в пятом переходе круглым резцом паз калибруют.
ШЛИФОВАЛЬНЫЕ РАБОТЫ.
Шлифование цилиндрических поверхностей деталей.
Все операции круглого наружного шлифования цилиндрических деталей по интенсивности съема припуска делят на обдирочное, предварительное, окончательное и тонкое шлифование.
Обдирочное шлифование предназначено для удаления с заготовок дефектного слоя материала после литья, ковки, штамповки, прокатки. Припуск на обработку составляет более 1 мм на диаметр. Такой припуск снимается на режимах скоростного шлифования со скоростью круга 35-60 м/с и высокоскоростного шлифования со скоростью свыше 60 м/с. После обдирочного шлифования точность обработки соответствует 8-9 квалитетам, а параметр шероховатости Ra=2,5-5 мкм.
Предварительное шлифование выполняют после токарной обработки, но перед термообработки заготовки. Предварительное шлифование производится со скоростью круга 40-60 м/с. Точность обработки в пределах 6-9 квалитетов, параметр шероховатости Ra=1,2-2,5 мкм.
Окончательное шлифование выполняют после термической обработки со скоростью круга 35-40 м/с. Точность окончательного шлифования соответствует 5-6 квалитетам, параметр шероховатости Ra=0,2-1,2 мкм.
Тонкое шлифование предназначено для получения малой шероховатости обрабатываемой поверхности (параметр Ra=0,025-0,1 мкм). Снимается припуск при тонком шлифовании 0,05-0,10 мм на диаметр.
В зависимости от диаметра шлифуемой поверхности выбирают скорость вращения заготовки, назИзм.
Лист
№ докум.
Подпись
Дата
Лист
1
НАЗВАНИЕ ДОКУМЕНТА
начают продольную подачу стола и определяют рекомендуемую подачу на глубину шлифования. Если поперечная подача осуществляется на двойной ход стола, то табличное значение удваивают.
Шлифование плоскостей.
Шлифование плоских поверхностей называется плоским шлифованием. Существуют два основных вида плоского шлифования: периферией и торцом круга. Шлифование периферией круга обеспечивает более высокую точность обработки по сравнению с шлифованием торцом круга. Шлифование периферией круга рекомендуется применять при высоких требованиях к точности обработки, малой жесткости деталей, а также закаленных деталей, склонных к образованию прожогов.
Показателями режима резания при плоском шлифовании периферией круга являются: скорость круга; скорость заготовки; поперечная подача и глубина шлифования.
Скорость шлифованного круга зависит от вида шлифования и возможности станка. Скорость заготовки совпадает при плоском шлифовании с продольной или круговой подачей стола, на котором они закрепляются. Увеличение скорости заготовки приводит к увеличению производительности обработки. Поэтому рекомендуется выбирать высокие скорости заготовки, особенно при предварительных операциях и снятии больших припусков. ПовышениеИзм.
Лист
№ докум.
Подпись
Дата
Лист
1
НАЗВАНИЕ ДОКУМЕНТА
скорости заготовки приводит к уменьшению нагревания и деформации изделия. На чистовых операциях рекомендуется снижать скорость заготовки.
При увеличении поперечной подачи повышается производительность, но увеличивается шероховатость и износ круга. Поэтому рекомендуется на чистовых операциях применять меньшую величину поперечной подачи.
Глубина резания определяет в основном производительность обработки, однако величина ее зависит от зернистого круга, требуемой шероховатости поверхности, мощности двигателя привода шлифовальной бабки и ряда других факторов. При обработке крупнозернистыми кругами можно применять большую глубину резания. При шлифовании мелкозернистыми кругами с большой глубиной наблюдается значительный износ мягких кругов или быстрое засаливание твердых кругов. Черновые операции следует производить с большими скоростями и глубинами, а на чистовых - снижать скорость и глубину резания.
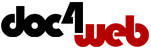
Нравится материал? Поддержи автора!
Ещё документы из категории технология:
Чтобы скачать документ, порекомендуйте, пожалуйста, его своим друзьям в любой соц. сети.
После чего кнопка «СКАЧАТЬ» станет доступной!
Кнопочки находятся чуть ниже. Спасибо!
Кнопки:
Скачать документ