Эксплуатационная база механизированной дистанции
ВВЕДЕНИЕ
Эксплуатационная база механизированной дистанции – это комплекс зданий и сооружений с оборудованием, приспособлениями, приборами и инструментами, предназначенными для технического обслуживания, ремонта, хранения и транспортирования погрузочно – разгрузочных машин, а также подготовки их использованию по назначению.
В зависимости от времени действия на одном месте ремонтные базы разделяют: на постоянные, временные и передвижные.
В зависимости от задач решаемые предприятиями они имеют разный состав парка машин и оборудования т. к. в грузовых районах железнодорожных станций погрузочно – разгрузочные работы выполняются в основном силами механизированных дистанций.
В современных погрузочно – разгрузочных машинах широко применяют унифицированные детали и сборочные единицы (редукторы, муфты тормозные устройства, двигатели, грузозахватные приспособления), позволяющие получать значительный технико-экономический эффект при их изготовлении и эксплуатации, упростить техническое обслуживание и ремонт. Повышение уровня комплексной механизации на железнодорожном транспорте происходит в условиях непрерывного увеличения парка средств механизации и реализации комплекса мер по улучшению его технической эксплуатации и сокращение сроков простоя различных машин в техническом обслуживании и ремонте. Совершенствование организации технологии выполнения профилактического обслуживания и ремонта погрузочно – разгрузочных машин в соответствии с установленной на железнодорожном транспорте плановой предупредительной системы является важным направлением улучшения и использования средств механизации.
На основе системы ППР происходит развитие ремонтно – эксплуатационной базы обеспечивающей высокую готовность парка машин, сокращается простой при внеплановых ремонтах и технического обслуживания.
Четкая и заранее регламентируемая организация работ способствует снижению, уменьшает расход запасных частей и материалов.
Целью данного курсового проекта является проектирование современных ремонтных мастерских оснащенных необходимым оборудованием и инструментом, а также разработка карты технологического процесса диагностирования и восстановления узлов погрузочно – разгрузочных машин.
1 ОПРЕДЕЛЕНИЕ КОЛИЧЕСТВА ТЕХНИЧЕСКИХ ОБСЛУЖИВАНИЙ И РЕМОНТА ДЛЯ ЗАДАННОГО ПАРКА МАШИН
Целью планирования технических обслуживаний и ремонтов является определение объемов работ и установление времени постановки машин на техническое обслуживание и текущий ремонт.
Таблица 1.1
Продолжительность технического обслуживания и текущего ремонта.
-
Машина
Продолжительность ремонта, сут
ТО-1
ТО-2
ТР
КР
Стреловой кран
0.3
2
4
22
Значение объемов работ по техническому обслуживанию и ремонту машин является основной предпосылкой для расчета оборудования и контингента рабочих, производственных площадей и других параметров ремонтных предприятий.
Таблица 1.2
Периодичность технических обслуживаний и текущего ремонта.
-
Машина
Периодичность ремонта
ТО-1, сут
ТО-2, сут
текущего
капитального
месяцы
тыс. т
годы
тыс. т
Стреловой кран
15
90
9
30
3
120
Согласно этой таблице два норматива периодичности технического обслуживания и ремонта – это продолжительность по времени и наработка по времени тоннажа между ремонтами.
Количество технического обслуживания и ремонта
где TО – число суток, месяцев, лет или наработка в тоннах от последнего одноименного ремонта, или с начала эксплуатации до начала планируемого периода;
Тn - число суток, месяцев, лет или наработка в тоннах в течении планируемого года;
ti – периодичность выполнения технического обслуживания и ремонта;
nnp – суммарное число всех видов технических обслуживаний и ремонта;
TО = 1/3суток, Tn = 1 день, ti = 3, nnp = 0
В планируемом периоде капитального ремонта не будет.
Число текущих ремонтов
TО = 20/9суток, Tn = 20дней, ti = 9, Тnp = 0
В планируемом периоде принимаем один текущий ремонт.
Число технических обслуживаний ТО-2.
TО = 365/90суток, Tn = 365дней, ti = 90, nnp = 1
В планируемом периоде принимаем три ТО-2.
Число технических обслуживаний ТО-1
TО = 1сутки, Tn = 365дней, ti = 15, nnp = 4
В планируемом периоде принимаем двадцать ТО-1.
2 ПЛАНИРОВАНИЕ РЕМОНТНОГО ЦИКЛА ТЕХНИЧЕСКИХ ОБСЛУЖИВАНИЙ И РЕМОНТОВ
В понятие планирования ремонтного производства входят вопросы, связанные с выполнением задач по ремонту машины в кротчайшей срок и минимальными затратами. Планирование организацией технического обслуживания и ремонта предусматривает разработку двух основных документов годового и месячного планов графиков технического обслуживания и ремонта.
Целью этих документов является определение количества технического обслуживания и ремонтов сроков их выполнения потребность в рабочей силе количество передвижных средств и эксплуатационных материалов.
Продолжительность работы машин устанавливается в отработанных часах, поэтому календарные постановки машин на ремонт зависят от сменности производства и реализации продукции, плана по труду и заработной платы, планы себестоимости продукции и финансового плана. Задачу этого планирования входит задания материальных предпосылок для бесперебойной и эффективной работы всех подразделений Взависимости от вида работ, а также наличие материалов, инструментов и запасных частей. При ремонте различных машин необходимо устанавливать очередность выпуска их из ремонта с учетом неравномерности поступления объектов ремонта на предприятии и различие в трудоемкости по отдельным этапам технологического процесса.
В основе оперативного планирования лежит график работы цеха.
Сменно – суточное планирование обуславливает постоянный контроль за процессом ремонта, т. е. заказы распределяют по рабочим местам Взависимости от трудоемкости работ на основе данных технологических карт.
Проект годового план – графика ремонта составляется на основе структуры циклов и продолжительности межремонтных периодов в соответствии с числом часов, смен и циклов, которые машина должна отработать с момента в течение планируемого периода. При составлении планов из общего времени должно исключаться, время простоя машины определяемое по нормативам.
Продолжительность простоя машины в ремонте зависит от вида ремонта, численности ремонтной бригады, технологии и организации ремонтных работ, а также от степени сложности ремонта данной машины.
Для сокращения простоя погрузо – разгрузочных машин, занятых на основном производстве допускается ремонтировать их в три смены. Для изменения загрузки площадей существенную роль играют технологические запасы агрегатов, накопленные для восстановления партии деталей, что сокращает подготовительно - заключительное время и использования площади мастерских.
При составлении плана необходимо определить число технических обслуживаний и ремонтов, запланировать трудовые затраты и время простоя. Наряду с планированием важным элементом является учет и отчетность.
Первичным учетным и контрольным документом, отражающим работу в течении всей смены является сменный рапорт, подтвержденный ответственным лицом.
Данные сменного рапорта обрабатываются, и полученные наработки устанавливают план постановки машины на технические обслуживания и ремонты.
Учет выполнения технических обслуживаний и ремонтов в каждой механизированной дистанции ведется в журнале.
3 ОПРЕДЕЛЕНИЕ ТРУДОЕМКОСТИ ТЕХНИЧЕСКИХ ОБСЛУЖИВАНИЙ И РЕМОНТОВ. РАСПРЕДЕЛЕНИЕ ПО ВИДАМ РАБОТ
3.1 Суммарная трудоемкость по каждому типу по всем видам машин технических обслуживаний и ремонтов.
где ni – число машин данного типа;
nTO-1, nTO-2, nTР, nKР – количество технических обслуживаний и текущих ремонтов;
tTO-1, tTO-2, tTР, tKР - трудоемкость технических обслуживаний и текущих ремонтов;
Таблица 3.1
Трудоемкость технических обслуживаний и ремонтов.
-
Машина
Грузоподъ-
емность
Трудоемкость
ТО-1
ТО-2
ТР
КР
Д -443
-
14
40
240
520
ТЛ -3А -ЦИНС
-
16
44
270
600
ТО-1
-
24
60
420
810
Механический погрузчик Д - 443 – 12 единиц
чел·ч
чел·ч
чел·ч
чел·ч
Механический погрузчик ТЛ -3А -ЦИНС – 10единиц
чел·ч
чел·ч
чел·ч
чел·ч
Механический погрузчик ТО-1 – 9единиц
чел·ч
чел·ч
чел·ч
чел·ч
Таблица 3.2
Результаты расчетов.
-
Тип машины
Количе
ство
ТО-1
ТО-2
ТР
Количество
Трудоемкость
Суммарная
Количество
Трудоемкость
Суммарная
Количество
Трудоем
кость
Суммарная
Д -443
12
21
14
3528
3
40
1440
2
240
5760
ТЛ -3А -ЦИНС
10
21
16
3360
3
44
1320
2
270
5400
ТО-1
9
21
24
4536
3
60
1620
2
420
7560
ВСЕГО
Дополнительная программа для мастерских механизированной дистанции включает в себя монтаж и демонтаж машин 3%, ремонт и содержание собственного оборудования 2% от общей трудоемкости в сумме 5%.
чел∙ч
3.2 Распределение трудоемкости технических обслуживаний и ремонтов по видам работ.
чел∙ч
Таблица 3.3
Трудоемкость технических обслуживаний.
-
Вид работ
Трудоемкость
%
чел∙ч
Уборочно – моечные
5
829,71
Диагностирование
26
4314,49
Крепежные
21
3484,78
Регулировочные
7
1161,59
Смазочно - заправочные
19
3152,9
Электротехнические
6
995,65
Аккумуляторные
2
331,88
Шиномонтажные
-
-
Обслуживание систем питания и гидравлики
14
2323,19
Всего
100
16594,19
3.3 Распределение трудоемкости текущего ремонта по видам работ.
чел·ч
Таблица 3.4
Трудоемкость текущего ремонта.
-
Вид работ
Трудоемкость
%
чел∙ч
Крепежные
3
589,68
Регулировочные
3
589,68
Разборочно - сборочные
29
5700,24
Ремонт сборочных единиц
19
3734,64
Ремонт систем питания
4
786,24
Шиномонтажные и вулканизированные
-
-
Медницко - жестянческие
5
982,8
Электротехнические и аккумуляторные
7
1375,92
Сварочные
4
786,24
Кузнечно - рессорные
3
589,68
Станочные
18
3538,08
Столярно - обивочные
2
393,12
Малярные
3
589,68
Всего
100
19656
.4 Общая трудоемкость по однотипным работам.
Таблица 3.5
Сводная таблица.
-
Вид работ
Общая трудоемкость
Уборочно – моечные
829,71
Диагностирование
4314,49
Крепежные
4074,46
Регулировочные
1751,27
Смазочно – заправочные
3152,9
Электротехнические, аккумуляторные, обслуживание систем питания и гидравлики
4051,7
5812,88
Шиномонтажные и вулканизированные
-
Разборочно - сборочные
5700,24
Ремонт сборочных единиц
3734,64
Медницко - жестянческие
1572,48
Станочные
786,24
Столярно - обивочные
393,12
Малярные
589,68
Сварочные
786,24
Всего
36250,19
4 ВЫБОР ФОРМЫ И МЕТОДА ОРГАНИЗАЦИИТЕХНОЛОГИЧЕСКОГО ПРОЦЕССА ТЕХНИЧЕСКИХ ОБСЛУЖИВАНИЙ И РЕМОНТА
На данном предприятии целесообразно использовать обезличенный метод структура парка машин в механизированной дистанции целесообразна.
При необезличенном ремонте сохраняется принадлежность восстановления основных частей к определенному экземпляру изделия.
Это значит снятая с данной машины сборочная единица, узел после их восстановлении они устанавливаются на ту же машину, с которой они были сняты.
Второстепенные детали: (крепеж, прокладки, кольца), как правило, меняются.
Основным недостатком необезличенного ремонта является, продолжительность ремонта машины включает время, затраченное на ремонт деталей и необходимость больших производственных площадей на ремонтном предприятии.
Этот метод применяют, когда ремонтируется большая номенклатура машин малыми силами.
Обезличенный ремонт характерен тем, что отрегулированные сборочные единицы и детали устанавливают на любую машину данной марки, т. е. принадлежность восстановленных частей к определенному экземпляру не сохраняется. Этот метод ремонта более прогрессивный и поэтому он является основным
Разновидностью обезличенного метода является агрегатный метод, при которому восстановления машин ведется путем замены крупных изношенных частей машин – заранее отремонтированными.
В основе агрегатного метода лежит периодического плановая замена агрегатов после достижения такой степени износа, при котором дальнейшая эксплуатация машины становится экономической нецелесообразной или не обеспеспечивающей безопасное выполнения работ. Практика создания обменных фондов сборочных единиц, накопление партии деталей сборочных единиц предполагает, что при ремонте машин в отличие от необезличенного ремонта происходит обезличивание деталей,
когда снятые с машины детали в дальнейшем употребляются в другой погрузочно – разгрузочной машине, что существенно сокращает простой машин при ремонте. Особенно наглядно это проявляется при ремонте машин транспортировка, которых в дорожные мастерские невозможна и оправдана, в этом случае проводится агрегатный метод ремонта, основанный на обезличенных деталей и сборочных единиц.
Разновидностью необезличенного метода является тупиковый метод ремонта, он выполняется специальными универсальными бригадами. Универсальные бригады выполняют весь комплекс работ кроме восстановления деталей. Такая организация требует высокой квалификации рабочих, т. к. каждый член бригады должен уметь отрегулировать каждый узел. При этом каждая бригада должна иметь запасные инструменты и запасные части для всех машин. Для такой организации характерна низкая производительность труда и высокая стоимость.
Более прогрессивным является метод специализированной бригады; собирает и разбирает одна, а ремонтирует сборочные единицы другая, которая специализируется на этом.
Этот вид ремонта имеет ряд преимуществ:
Повышение производительности труда, т. к. квалификация рабочих используется более правильно.
Продолжительность ремонта снижается.
Снижение стоимости ремонта.
Теоретически основой агрегатного метода служит эксплуатационно-ремонтное резервирование. Для этого имеется некоторое количество запасных единиц, называемое оборотным фондом, который обеспечивает все категории ремонта, обслуживаемые парком машин. Вместе с тем он должен быть в обороте в разных стадиях технологического цикла. В демонтаже, реверсе, транспортировании и монтаже.
Технологический процесс агрегатного метода ремонта разделен на два самостоятельные фазы (ремонт и восстановление) сборочных единиц и их монтаж и демонтаж.
5 ОПРЕДЕЛЕНИЕ НЕОБХОДИМОГО КОЛИЧЕСТВА ОБОРУДОВАНИЯ И ПЕРЕДВИЖНЫХ ТЕХНИЧЕСКИХ СРЕДСТВ
По уровню оснащения ремонтных предприятий по технологическим оборудованиям судят об их возможностях в плане ремонта.
Технологическое оборудование это материальная основа и средства, которые регулируют выполнение технологического процесса, механизируют и автоматизируют его. При выборе оборудования очень важно, чтобы оно было исправно т. к. этим достигается качество ремонта.
В соответствии с технологическим процессом все отделения мастерских оборудуют необходимыми инструментами и оборудованием.
В станочном отделении размещают: токарно-винторезный станок типа 1К62, шлифовальный 3М152, зубофрезерный 6Т104, сверлильный 2N125.
В электротехническом отделении размещают: козлы, стеллажи, стенды для сборки и испытания приборов, зарядные устройства, установки для слива электролита, станки.
В сварочном отделении: сварочный преобразователь, стол для электродуговой сварки, сварочный полуавтомат, стеллаж для деталей.
В кузнечном отделении размещают: горно-кузнечный огонь Р-923, печь камерная электрическая, наковальня двурогая, молот поворотный пневматический типа М-127, электроножницы, верстаки, вентиляторы высокого давления, стенды для рессор, стеллажи.
В малярном отделении размещают: верстак, ванну, сушильный шкаф, краскораспылители, ларь для обтирочных материалов.
В столярном отделении размещают: циркулярная пила, верстаки, ящик для песка, шкаф для хранения инструментов.
В уборочно-моечном отделении размещают: моечную машину, выварочные ванны, насосную станцию, установку для очистки деталей для расплава солей. В диагностическом отделении размещают: верстак электромагнитный и ультразвуковой дефектоскоп.
В разборочно - сборочном отделении все рабочие места снабжаются верстаками и необходимым слесарным, мерительным инструментом и оборудованием. Для подъема деталей при разборке предусматриваются: кран - балка, домкраты, гидравлические подъемники, тележки для снятия и поставки колес, электрокара, стенды.
Для технического обслуживания и ремонта погрузочно - разгрузочных машин расположенных на разных участках механизированной дистанции используется передвижная автомобильная установка.
Автомобильная передвижная мастерская – это оперативное средство, находящееся в ведении механизированной дистанции, для выполнения ремонтных работ на линии. Оборудование и инструмент, которыми оснащена мастерская, позволяют выполнять разборку и резку, обработку и сварку металла, столярные и другие работы. Приборы и приспособления мастерской позволяют осуществлять ряд операций контроля и диагностирования различных систем (топливной, электрической и др.) ДВС и гидравлических систем машин.
6 ОПРЕДЕЛЕНИЕ КОНТИНГЕНТА РАБОЧИХ И ИНЖЕНЕРНО-ТЕХНИЧЕСКИХ РАБОТНИКОВ
6.1 Определение годового фонда времени рабочих
где dр = 251 - число рабочих дней в 2007г. При пятидневной неделе.
Тсм = 8ч - продолжительность смены
dp = 14 - число праздничных дней
Тс = 1ч - время, на которое сокращается смена в предпраздничные дни
nсм = 1 - количество смен
ч
Таблица 6.1
Годовой фонд времени рабочих при односменном рабочем дне.
Наименование профессии
Фоб (ч)
Фр(ч)
Слесари (разборка, мойка, деффектация, сборка, обкатка, испытание ).
2070
1840
Станочники, столяры, электрики, жестянщики.
2070
1860
Испытатели машин и двигателей ДВС.
2070
1830
Маляры.
1830
1610
Электросварщики, медники.
2070
1820
Рабочие-гальваники.
2070
1820
Кузнечные рабочие
2030
1810
6.2 Определение количества постов и оборудования
Количество постов для станочного оборудования:
где ТСТ - общая трудоемкость станочных работ
ФР = 1860ч - годовой фонд времени станочника
КВ = 0,85 - коэффициент использования оборудования по времени.
Принимаю 2 поста для станочного оборудования.
Количество станков для каждого вида определяется по соответствующему виду станочных работ (токарные, фрезерные, шлифовальные)
Принимаем примерное распределение по видам:
Токарные работы - (66 - 82)%
Фрезерные - (17- 20)%
Шлифовальные - (10 - 12)%
Сверлильные – (12- 20)%
Количество постов сварки.
где ТСВ - общая трудоемкость сварочных работ.
ФР= 1860ч - годовой фонд времени сварочных работ.
КВ = 0,7 - коэффициент использования оборудования по времени.
Принимаю 1 пост для сварочного оборудования.
Количество постов для механической и ручной ковки, а также для медницких -жестянческих работ
где ТК - общая трудоемкость кузнечных работ.
ФР = 1810ч - годовой фонд времени кузнечных работ.
КВ = 0,75 - коэффициент использования оборудования по времени.
Принимаю 1 пост для кузнечных, медницких - щестянческих работ.
Количество постов для столярных, электротехнических и аккумуляторных работ, обслуживания и ремонта систем питания и гидравлики.
где ТЭ - общая трудоемкость столярных, электротехнических и аккумуляторных работ.
ФР = 1860ч - годовой фонд времени столярных, электротехнических и аккумуляторных работ.
КВ = 0,7 - коэффициент использования оборудования по времени.
Принимаю 4 поста для столярных, электротехнических и аккумуляторных работ.
Количество постов для малярных постов.
где ТМ - общая трудоемкость малярных работ.
ФР = 1610ч - годовой фонд времени малярных работ.
КВ = 0,8 - коэффициент использования оборудования по времени.
Принимаю 1 пост малярных работ.
Количество постов для слесарно-обивочного оборудования.
где ТС-О - общая трудоемкость столярно-обивочных работ.
ФР = 1860ч - годовой фонд времени слесарно-обивочных работ.
КВ = 0,85 - коэффициент использования оборудования по времени.
Принимаем 1 пост для слесарно-обивочного оборудования.
Количество постов для крепежных, регулировочных, уборочно-моечных, диагностических, смазочно-заправочных, шиномонтажных, разборочно-сборочных и ремонта сборочных единиц.
где ТСЛ - общая трудоемкость слесарных работ
ФР = 1840ч - годовой фонд времени слесарно-обивочных работ.
КВ= 0,9 - коэффициент использования оборудования по времени.
ТСЛ=4074,48+1751,28+829,7+4314,5+3152,9+5700,24+3734,64=23557,74
Принимаем 13 постов с учетом совмещения профессий.
Общее число основных производственных работ.
РО = 2+1+1+4+1+1+13 =23
6.3 Количества вспомогательных работников счетно-конторского и обслуживающего персонала.
Все работающие на ремонтном предприятии взависимости от исполнительной работы условно разделяют на следующие категории: основные производственные рабочие, вспомогательные рабочие, обслуживающие основное производство,( инструментальщики, заточники, транспортные рабочие, кладовщики, подсобные рабочие и инженерно-технические работники, счетно-конторский и младший обслуживающий персонал).
Принимаю 4 вспомогательных работника.
Численность инженерно - технических работников.
Принимаю 3 инженерно - технических работника.
Численность счетно - конторского персонала.
Принимаю 1 работника счетно - конторского персонала.
Численность младшего обслуживающего персонала.
Принимаю 1 работника младшего обслуживающего персонала.
Общее количество работающих в ремонтных мастерских:
чел
7 РАСЧЕТ И ПЛАНИРОВКА ПРОИЗВОДСТВЕННОЙ И ВСПОМОГАТЕЛЕЛЬНОЙ ПЛОЩАДЕЙ
К производственным относятся площади занятые оборудованием и рабочими местами, а также проходами и проездами между ними.
7.1 Расчет производственных площадей.
Станочное отделение
где - количество оборудования определенного типа.
- удельная площадь для оборудования, данного типа.
Принимаем в своем станочном отделении:
шлифовальный станок типа 3М153S = 6,8м²
зубофрезерный станок типа 6Т104S = 1,6м²
сверлильный станок типа 2N125 S = 0,7м²
токарно-винторезный станок типа 1К62S = 3,7м²
Полезная площадь, занимаемая станками.
м²
Общая площадь с учетом проходов и проездов.
где К= 3,5 - коэффициент учитывающий рабочие зоны и проходы станочного отделения.
м²²
Для определения площади участков и отделений, в которых выполняются определенные работы необходимо учитывать удельную площадь приходящиеся на одного производственного рабочего.
Таблица 7.1
Удельная площадь помещений.
-
Вид работ
Удельная площадь (м²)
Наружная мойка, узлов и деталей, испытание
35
Разборочно - сборочные, кузнечные аккумуляторные
25
Медницкое-заливочные, малярные
20
Ремонт ДВС
18
Столярные, сварочно-наплавочные, дефектовочные
15
Электроремонтные, станочные, вулканизационные
15
Слесарно-ремонтные
8
Площадь участков и отделений, в которых выполнение работ мало связано с использованием оборудования.
( м²)
где N - количество производственных рабочих занятых в одну смену на данном участке.
а - удельная площадь для одного производственного рабочего.
Площадь для электротехнических и аккумуляторных работ.
Принимаю 3 рабочих для выполнения электротехнических работ и одного аккумуляторщика
м²
С учетом установленного оборудования добавляем к Fэ-6м²
м²²
Площадь для сварочных работ.
м² ²
В связи с установкой оборудования добавляем к Fc-3м²
м²
Площадь для кузнечных работ.
м²
В связи установкой оборудования добавляем к FК-7м²
м²
Площадь для малярных работ.
м²
В связи установкой оборудования добавляем к FМ-1м²
м²
Площадь для столярно-обивочных работ
м²
Площадь для столярно-обивочного отделения с учетом установления оборудования добавляем - 2м².
м²²
Площадь для разборочно – сборочных работ
где FCЛ1 – площадь для выполнения слесарных работ.
Принимаю 3 работников для разборочно – сборочных работ, 2 для выполнения уборочно – моечных работ, 1 для диагностирования, 7 для восстановления и ремонта деталей и машин.
м²
В связи с установкой оборудования добавляем к FCЛ1 - 10 м².
м²
FCЛ1 – площадь для выполнения слесарных работ.
FCЛ2 – площадь занимаемая машинами подлежащих ремонту.
где n = 2 – число машин ожидающих ремонта
l= 7,2м - длина стрелового крана
b = 2,44м- ширина стрелового крана
м² ²
Принимаю площадь для автокрана кс-5363.
м² ²
Общая площадь основных производственных участков.
м² ²
7.2 Расчет вспомогательных площадей.
Расчет конторских площадей определяется по нормам на одного человека.
Для инженерно - технического работника 5м²
Для сменно - конторского персонала 3,25м²
м² ²
Площадь бытовых помещений.
Эти площади рассчитывают по нормам в соответствии санитарно - техническими требованиями на одного работающего в мастерским;
умывальники - 0,1м²
душевые - 0,45м²
туалет - 0,15м²
разделка - 0,8 м²
буфет - 0,3 м²
м²
Таблица 7.2
Площади вспомогательных помещений.
-
Наименование складов
Трудоемкость рем. раб
Удельная площадь склада
Площадь склада
м²
металлов
запасных частей
материалов
горючесмазочных
утиля
лесоматериалов
топливо
хранение агрегатов и двигателей
29823,2
0,5
0,7
0,3
0,13
0,17
0,4
0,95
0,35
14,9
20,8
8,9
3,8
29,8
11,9
28,3
10,4
Итого:
= 128,8
Таблица 7.3
Сводные ведомости площадей.
-
Категория площадей
Площадь м²
²
Производственные
Вспомогательные
Бытовые
Конторские
343,14
128,8
95,7
18,25
Итого:
585,89
Принимаю типовые мастерские следующих размеров:
Длина - , ширина -, общая площадь - м²
7.3 Планировка производственных мастерских.
По результатам расчета производится планировка ремонтного предприятия с его участками и отделениями.
При планировки производственных помещений следует:
1. Учитывать расположение участков, отделений и складских помещений отразить их влияние на технологическую схему проектируемого объекта.
2. Обеспечить последовательность технологического процесса, расположить оборудование, по цепочке избегая возвратных частей узлов и деталей машин.
3. Не допускать перекрещивающихся потоков.
4. Выдерживать размеры рабочих зон и проходов.
5. Обеспечивать лучшую освещенность в дневное время, тех рабочих мест, на которых производится сложная и точная работа.
6. Обеспечивать возможность создания необходимой частоты рабочих мест.
Наиболее целесообразной считается прямоугольная конфигурация производственного здания. Ширина здания применяется стандартной: 12, 18, 24, 36, 48, 54, 72м. Отношение длины здания к его ширине должно быть не более двух. Длина здания должна быть кратной длине строительных плит, т.е. делиться на шесть и связана с линией разборочно - сборочных работ.
Основные строительные элементы должны иметь следующие ремонтные размеры:
Толщина капитальных стен 300-500мм
Толщина перегородочных стен200-300мм
Ширина окон 1,5, 2, 3, 4м
Ширина дверных проемов1,5м
Высота разборочно - сборочного отделения определяется габаритами ремонтируемых машин, кузнечно-термического и сборочного оборудования - не менее 6м, а остальных производственных помещений - не менее 4 - 5м.
В производственных зданиях предусматриваются взаимно перпендикулярные основные проезды, которые располагаются против въездных ворот. Планировка дистанционных мастерских определяет принятым методом технического обслуживания и ремонта, а также схемой производственного процесса. В грузовом хозяйстве, как правило, принят тупиковый метод, согласно которому в центральной части мастерских располагаются зоны текущего ремонта.
В разборочно - сборочном отделении располагаются централизированные посты машин. Это посты - диагностирования пайки узлов и деталей, а также участки для их восстановления. Смотровые канавы должны иметь хорошее освещение и вентиляцию. Отработку трансмиссионных масел, размещают вне здания.
Станочное отделение размещается в части здания
противоположенному кузнечному отделению, что предотвращает вредное влияние ударов и вибраций на точность механической обработки.
Сварочное отделение должно изолироваться от других, а участки, требующие большое количество воды размещаются в другом месте.
Слесарное оборудование расставляют с учетом норм расстояний.
Сварочно - наплавочное отделение предназначено для ремонта и восстановления деталей размеры кабины, зависящие от габаритов деталей, чтобы оставалось свободно 4м. Кабину изолируют огнестойкими стенами и располагают вдоль наружных стен. Рядом с отделением нельзя располагать участки с легковоспламеняющим производством и складами.
8 ПРОЕКТИРОВАНИЕ ЭНЕРГЕТИЧЕСКОЙ ЧАСТИ МАСТЕРСКИХ
Оно включает в себя расчет потребления предприятием основных видов энергии: сжатого воздуха, пара, газа, топлива, электроэнергии.
8.1 Установленная мощность предприятия.
При укрупненных ориентировочных расчетов, ориентировочную мощность определяется определяем по формуле.
где 0,14 - количество кВт приходящие на каждые 100 чел∙ч годовой трудоемкости предприятия.
кВт
8.2 Среднегодовой расход осветительной энергии по каждому участку.
где Тос - 800ч - число часов работы осветительных приборов при односменном рабочем дне в мастерских.
F - принятая площадь отделения
Руд - удельная мощность осветительной нагрузки
Таблица 8.1
Удельная мощность осветительной нагрузки
-
Наименование отделения
Руд кВт/м²
Разборочно - сборочное, моечное, медняцкое
15-18
Сварочное, кузнечно- термическое
14-16
Станочное, слесарно - механическое
25-35
Малярное, ремонт электрооборудования и ДВС
20-25
Столярное
15-18
Электротехническое, аккумуляторное
16-18
Административное, лабораторное
20-25
Склады и бытовое помещение
6-8
Станочное отделение.
кВт·ч
Разборочно - сборочное отделение.
кВт·ч
Кузнечное отделение.
кВт·ч
Сварочное отделение.
кВт·ч
Электротехническое отделение.
кВт·ч
Столярно -обивочное отделение.
кВт·ч
Малярное отделение.
кВт·ч
Бытовое помещение.
кВт·ч
Счетно - конторский персонал.
кВт·ч
Склады.
кВт·ч
Проходы и проезды.
кВт·ч Суммарный расход осветительной энергии в мастерских.
кВт·ч
8.3 Потребность в сжатом воздухе.
Сжатый воздух используется для пневмоинструмента, испытательных стендов и в технологических процессах на плавкие работы обработки деталей.
где кс = 0,4 - 0,6 - коэффициент спроса на воздух потребителей.
кэ = 1,3 - коэффициент, учитывающий условия эксплуатации пневмоприемников.
кn = 1,5 - коэффициент, учитывающий потери воздуха в воздушной сети.
Qср - суммарный расход воздуха при распределительной работе пневмоприемника составляющий для каждого 2,5 - 4,5м/ч, краскораспылителя 12 м³/ч, для обдувки деталей 24 - 42 м/ч
м/ч
ФОБ - годовой фонд рабочего времени
п =1 – число рабочих смен
Для станочного, электротехнического, столярно-обивочного. разборочно - сборочного отделений, сварочного.
м³·ч ³
Для кузнечного отделения
м³·ч ³
Для малярного отделения.
м³·ч ³
8.4 Расход воды на производственные и бытовые нужды.
где 4м³ - среднегодовой расход на 100 чел·ч годовой программы.
ТГ - общая трудоемкость
м³³
8.5 Годовой расход пара на воду и вентиляцию.
где qТ - расход тепла на 1м³ зданий
qТ = 15 - 20 ккал/ч - при отсутствии искусственной вентиляции
qТ = 25 - 35 ккал/ч - при искусственной вентиляции
ТОТ = 180дней - 4320ч - число часов в определенном периоде
V - объем здания, м³³
i - 540 ккал/ч - теплосодержание пара.
Определяем объем здания
где Fn = 1,1∙ Fобщ - площадь предприятия по наружным стенам
h = 4,6м - усредненяя высота здания мастерских
м³³
м³³
м³³
8.6 Требуемая производительность вентилятора.
где V - объем здания, м³
К - кратность объема воздуха, ч
F - площадь помещения
Таблица 8.2
Часовая кратность обмена воздуха вентиляторами
Участки
Воздухообмен к
Гальваническое, аккумуляторное
Сварочное, кузнечное, малярное
Слесарно-механическое, уборочное
Медницко-заливочное, ремонт оборудования, испытание ДВС
Столярно- обивочное
6-8
4-6
2-3
3-4
1,5-2
Электротехническое отделение.
м³·ч
Малярное отделение.
м³·ч
Сварочное отделение.
м³·ч
Кузнечное отделение
м³·ч
Столярно- обивочное отделение
м³·ч
8.7 Мощность электродвигателей для приводов вентиляторов.
Таблица 8.3
Технические характеристики центробежных вентиляторов.
Показатели
Значение
Вентилятор №2 электродвигатель АОЛ 21-4 nдв. = 1500 об./мин.
Производительность м³/ч
Напор вентилятора кг/м³
КПД
200
20
0,35
300
25
0,45
400
25
0,48
500
25
0,52
600
25
0,54
700
25
0,56
800
23
0,5
900
21
0,48
Вентилятор №2 электродвигатель АО 31-2 nдв. = 3000 об./мин.
Производительность м³/ч
Напор вентилятора кг/м³
КПД
800
93
0,52
1000
92
0,55
1200
91
0,55
1400
90
0,54
1600
86
0,52
1800
70
0,5
Вентилятор №3 электродвигатель А 41-6 nдв. = 1000 об./мин.
Производительность м³/ч
Напор вентилятора кг/м³
КПД
800
25
0,45
1200
27
0,52
1600
26
0,53
2000
25
0,43
Вентилятор №3 электродвигатель А 32-4 nдв. = 1500 об./мин.
Производительность м³/ч
Напор вентилятора кг/м³
КПД
1500
66
0,45
2000
68
0,5
2500
68
0,55
3000
65
0,5
Электротехническое отделение.
кВт·ч
Малярное отделение
кВт·ч
Сварочное отделение
кВт·ч
Кузнечное отделение
кВт·ч
Столярно- обивочное отделение
кВт·ч
9 ОХРАНА ТРУДА И ОКРУЖАЮЩЕЙ СРЕДЫ ПРИ ВЫПОЛНЕНИИ ТЕХНИЧЕСКИХ ОБСЛУЖИВАНИЙ И РЕМОНТА
Охрана труда на механизированной дистанции обеспечивается комплексом организационных и технических мероприятий, разрабатываемых и внедряемых в соответствии с требованиями Государственной системы стандартов безопасности труда и предупреждающих профессиональные заболевания и травматизм работающих. Технологические процессы технического обслуживания и ремонта должны предусматривать полную безопасность выполнения всех производственных процессов.
Обслуживание и ремонт машин могут выполняться только обученным персоналом после проверки знаний в объеме соответствующих инструкций по технике безопасности, а так же медицинского освидетельствования. Кроме того, каждого рабочего необходимо проинструктировать по мерам безопасности при получении отдельных работ. На посту обслуживание машины на пневматическом ходу должны стоять с включенным ручным тормозом и задней передачей. При разборке гусеничного полотна под катки подкладывают упоры. Перед снятием колес необходимо поставить под машину козелки, а под неснятые колеса-упоры. Выполнять какие-либо работы на машине, вывешенной только на домкратах, воспрещается.
Регулировать, ремонтировать, смазывать вручную или выполнять какие-либо другие работы по обслуживанию во время работы машины категорически запрещается. При работающем двигателе допускается обслуживание системы питания и зажигания, а также испытания тормозов. Перед разборкой металлоконструкций грузоподъемных машин части, которые могут прийти в движение под действием силы тяжести или других причин, необходимо привести в положение, обеспечивающее безопасное ведение работ. Под обслуживаемой конструкцией не должны находиться люди. Ремонтные работы, особенно распасовку и запасовку канатов, разматывание их из бухт, необходимо выполнять в рукавицах. Рабочие должны быть снабжены исправными инструментами и приспособлениями.
Гаечные ключи должны соответствовать размерам гаек, не иметь трещин, заусенцев. Применять различные подкладки между гранями гайки и ключа, различного рода удлинители запрещается. Электрические дрели, электрогайковерты должны быть исправны и работать от сети напряжением 36 В.
Горючие и смазочные материалы хранят на специально отведенных площадках или в помещениях, оборудованных в соответствии с правилами и нормами пожарной безопасности. Нельзя открывать пробки у металлических бочек с горючим металлическим молотком и зубилом - это может привести к образованию искры. Заправлять топливо следует только закрытой струей при неработающем двигателе. При работе с этилированным бензином, а также жидкостью, не замерзающей при низкой температуре запрещается засасывать жидкости ртом.
После работы с бензином и антифризом необходимо вымыть руки теплой водой с мылом.
Смазочные работы следует выполнять с использованием механизированного оборудования (маслораздаточные колонки и баки, солидолонагнетатели, пистолеты)
Устройства для зарядки и ремонта аккумуляторных батарей должны располагать помещениями для раздельной работы со щелочными и кислотными батареями. Приготовлять и хранить кислотный и щелочной электролит следует в разных помещениях. Все зарядные устройства должны устанавливаться в разных помещениях. Помещения для зарядки аккумуляторов оборудуют приточно-вытяжной вентиляцией 5 - 10 - кратный обмен воздуха при зарядке щелочных батарей и 10 - 15 - кратный - при зарядке кислотных. Вытяжные вентиляционные устройства должны иметь блокировку, предусматривающую отключение зарядного тока при прекращении работы вентилятора. Двери аккумуляторных помещений должны открываться наружу. У входа вывешивают надпись « Аккумуляторная - огнеопасно - не курить! ». Приготовлять кислотный электролит нужно только в эбонитовой, фаянсовой или керамической посуде, вливая кислоту в дистиллированную воду при помощи качалок или сифонов.
Работы по обслуживанию и ремонту машин персонал должен выполнять в специальной одежде и обуви с применением предусмотренных для каждого рабочего места индивидуальных средств защиты.
Безопасность работы на производственных участках требует, чтобы помещения для ремонта машин были светлыми, чистыми, сухими, теплыми имели принудительною вентиляцию.
Запрещается загромождать проходы и проезды. Высота штабелей, в которые уложены агрегаты и детали, не должна превышать 1м. При мойке машин растворами кальцинированной или каустической соды необходимо соблюдать меры предосторожности.
Сварочные работы организуются таким образом, чтобы сварщики и окружающий персонал были защищены от вредного воздействия электрического тока, выделяющихся при сварки газов и пыли, от ожогов лучами электрической дуги и расплавленным и нагретым металлом.
При сварочных работах необходимо заземление оборудования, пускорегулирующей аппаратуры и свариваемых изделий, а также защита кабеля от механических повреждений.
Металлорежущее, деревообрабатывающее и другое оборудование должно быть прочно укреплено к фундаменту и заземлено, оборудовано защитными кожухами и экранами от разлетающейся стружки.
Абразивные круги перед установкой на заточные станки испытывают на разрыв, на стенде с частотой вращения, на 50% превышающей рабочую. Установленный на станок круг закрепляют зажимными фланцами с эластичными прокладками.
Помещения, где производят малярные работы, оборудуют приточно - вытяжной вентиляцией с 6 - 10 - кратным обменом воздуха. Работающим на окраске необходимо пользоваться средствами индивидуальной защиты (респераторы, перчатки и др.)
Все отделения, которые относятся к категориям производства с вредными условиями труда должны размещаться в изолированных от других участков помещениях, а работающим выдается соответствующий комплект спецодежды.
При использовании подъемно - транспортного оборудования и механизмов в процессе ремонта машин следует соблюдать установленные правила. Масса поднимаемого груза должна соответствовать номинальной грузоподъемности применяемых оборудования и механизмов, которую необходимо обозначать на месте. Запрещается транспортировать грузы над работающими людьми, а также поднимать грузы, масса которых не может определена. Применяемые грузозахватные приспособления, а также стропы систематически контролируются и подвергаются их установленным испытаниям. На каждом грузоподъемном механизме должна быть указана дата его последнего освидетельствования.
На каждом производственном участке, на видном месте помещаются инструкция по безопасным методам работы, а также плакаты и необходимые схемы выполнения отдельных операций.
Для предотвращения или уменьшения вредного воздействия на окружающую среду на каждом предприятии разрабатывают комплекс природоохранительных мероприятий, направленных на защиту атмосферы, почвы, растительного мира, на борьбу с шумом. С целью сокращения расхода свежей воды и объема сбрасываемых стоков внедряют технологические процессы, позволяющие уменьшить объем и загрязненность образующихся стоков, применяют оборотное и многократное использование воды для производственных нужд, а для сокращения концентрации загрязнений в стоках, выпускаемых в водоемы, создают более совершенные очистные сооружения. Осуществляются сбор и регенерация отработанных масел.
СПИСОК ЛИТЕРАТУРЫ
1. Правила устройства и безопасной эксплуатации грузоподъемных кранов (машин) М.:Профиздат, АСОТ, 2004,224с.
2. Инструкция по эксплуатации погрузочно-разгрузочных машин. № ЦММ-20 М.:Транспорт 2002, стр. 144.
3. Абгафоров В.А., Сатановский В.Г., Матюшин Л.Н. Техническое обслуживание и ремонт погрузочно-разгрузочных машин. М.: Транспорт,1989.
4. Голай Э.И. Коверин В.В. Монтаж ,Эксплуатация и ремонт подъемно-транспортных машин. Машиностроение 1991, 320с.
5. Игнатов А.П. Погрузочно-разгрузочные машины на железнодорожном транспорте. М.: УМК МПС России,2002,384с.
6. Клочкова Е.А.Охрана труда на железнодорожном транспорте. М.: Маршрут, 2004,412с.
7. Зубрер Н.И. Охрана окружающей среды и экологии, безопасность на железнодорожном транспорте М.: УМК МПС России,1999,320с.
8. Теремин В.С. Охрана труда в путевом хозяйстве М.: Транспорт,1989,320с.
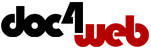
Нравится материал? Поддержи автора!
Ещё документы из категории транспорт :
Чтобы скачать документ, порекомендуйте, пожалуйста, его своим друзьям в любой соц. сети.
После чего кнопка «СКАЧАТЬ» станет доступной!
Кнопочки находятся чуть ниже. Спасибо!
Кнопки:
Скачать документ