Система технического осмотра и ремонта
Содержиние
Методы формирования системы ТО и ремонта
Износ и изнашивание сопряженных деталей. Классификация видов изнашивания
Коэффициент технической готовности как основной показатель работы технической службы АТП
Качество автомобиля как совокупность его технико-эксплуатационных свойств. Закономерности изменения показателей качества во времени
Экономико-вероятностный метод ТО
Методы формирования системы ТО и ремонта
Основой системы ТО и ремонта являются ее структура и нормативы. Структура системы определяется видами (ступенями) соответствующих воздействий и их числом. Нормативы включают конкретные значения периодичности воздействий, трудоемкости, перечни операций и ряд других.
Структура системы ТО и ремонта определяется: уровнем надежности и качества автомобилей; целью, которая поставлена перед автомобильным транспортом и ТЭА; условиями эксплуатации; имеющимися ресурсами; организационно-техническими ограничениями
Для эксплуатируемого в настоящее время подвижного состава автомобильного транспорта уровень влияния отдельных элементов структуры системы ТО и ремонта на затраты по обеспечению работоспособности (без организационно-планировочных затрат) следующий: перечень профилактических операций и их периодичность 80-87%; число ступеней (видов) ТО и кратность их периодичности 13-20%. Таким образом, главными факторами, определяющими эффективность системы ТО и ремонта, являются правильно определенные перечни (что делать) и периодичности (когда делать) профилактических операций, затем количество видов ТО и их кратность (как организовать выполнение совокупности профилактических операций).
Сложность при определении структуры системы ТО состоит в том, что ТО включает в себя 8-10 видов работ (смазочные, крепежные, регулировочные, диагностические и др.) и более 150-280 конкретных объектов обслуживания, т.е. агрегатов, механизмов, деталей, требующих предупредительных воздействий.
Каждый узел, механизм, соединение могут иметь свою оптимальную периодичность ТО, определяемую методами, изложенными в гл.3. Если следовать этим периодичностям, то автомобиль в целом практически непрерывно должен направляться для технического обслуживания каждого соединения, механизма, агрегата, что вызовет большие сложности с организацией работ и дополнительные потери рабочего времени, особенно на подготовительно-заключительных операциях. При этом объектом воздействий будет не автомобиль как транспортное средство, а его составные элементы.
Поэтому после выделения из всей совокупности воздействий тех, которые должны выполняться при ТО, и определения оптимальной периодичности каждой операции (см. гл.3) производят группировку операции по видам ТО. Это дает возможность уменьшить число заездов автомобиля на ТО и время простоев на ТО и в ремонте. Однако надо иметь в виду, что группировка операций неизбежно связана с отклонением периодичности ТО данного вида от оптимальной периодичности ТО отдельных операций. При определении периодичности ТО группы операций ("групповую" периодичность) применяют следующие методы.
Рисунок 1. Схема группировки воздействий по стержневым операциям ТО
Группировка по стержневым операциям ТО основана на том, что выполнение операций ТО приурочивается к оптимальной периодичности lСТ так называемых стержневых операций, которые обладают следующими признаками:
а) влияют на безопасность движения автомобиля;
б) невыполнение их снижает безотказность, экономичность, экологичность и влияет на работоспособность автомобиля;
в) характеризуются большой трудоемкостью, требуют специального оборудования и обустройства постов;
г) регулярно повторяются.
Примерами подобных стержневых операций или групп операций являются: смазка деталей и узлов автомобилей через пресс-масленки - признаки в), г); регулирование тормозной системы - все признаки; смена масла в картере двигателя - признаки в), г). Таким образом, по этому методу периодичность ТО стержневой операции lСТ принимается за периодичность вида ТО или группы операций, т.е. (lТО) 1= lСТ (рисунок 1). Причем одновременно с данной стержневой операцией могут выполняться те операции, которые имеют периодичность , где - периодичность последующей стержневой операции.
Рисунок 2. Схема применения технико-экономического метода для определения групповой оптимальной периодичности ТО: 7, 2,3 - суммарные удельные затраты на ТО и ремонт по отдельным объектам; 4 - то же, по группе объектов
Операции, оптимальная периодичность которых Io. i больше периодичности стержневой операции, выполняются с коэффициентов повторяемости
, где (1)
Такие операции, как правило, состоят из двух частей - контрольной (диагностической) и исполнительской. Причем контрольная часть производится каждый раз при направлении автомобиля на данный вид обслуживания, а исполнительская - по потребности в зависимости от фактического технического состояния объекта обслуживания. В действующей системе ТО более 65-70% всех операций выполняются с коэффициентом повторяемости, зависящим от результатов контроля в пределах установленной периодичности.
При технико-экономическом методе определяют такую групповую периодичность l, которая соответствует минимальным суммарным затратам С на ТО и ремонт автомобиля по всем рассматриваемым объемам (рисунок 2):
,
т е. оптимальная периодичность при , где СIi, СIIi - удельные затраты на ТО и ремонт i-го объекта, s - число операций в группе (виде ТО). Если в группу входит операция, периодичность которой ограничена в рассматриваемых пределах условиями безопасности, экологии или техническими критериями, то выбранная групповая периодичность должна удовлетворять требованиям , где j - номер операции с периодичностью, ограниченной требованиями безопасности движения или другими техническими критериями (например, прекращение функционирования механизма при )
Рисунок 3. К оценке рациональности профилактических воздействий при заданной периодичности
Используя экономико-вероятностный метод, можно определить целесообразность выполнения данной операции не с оптимальной для нее, а с заданной периодичностью стержневой операции. Воспользовавшись картой профилактической операции, определяют зону наработок, в которой удельные затраты при предупредительной стратегии остаются ниже, чем при устранении возникшего отказа (см. рисунок 9). Если в этой зоне находится периодичность стержневой операции, то изменение периодичности для данной операции допустимо.
На рисунке 3 приведены графики, позволяющие определить предельно допустимое значение коэффициента относительных затрат на ТО и ремонт kпд, превышение которого при изменении периодичности нецелесообразно по экономическому критерию, Определим целесообразность выполнения ранее рассмотренной в качестве примера операции не с оптимальной для нее периодичностью lо = 12 тыс. км, а с периодичностью lТО = 5,5 тыс. км. При выполнении операции с заданной периодичностью коэффициент периодичности , Для этого значения и коэффициента вариации vx = 0,4 предельное значение коэффициента kпд = 0,27 при фактическом значении kп = 0,4. Так как kп > kпд, то по экономическому критерию проведение данной операции по профилактической стратегии с периодичностью 5,5 тыс. км нерационально. Нижняя граница периодичности ТО, при которой данную операцию еще целесообразно проводить профилактически, составляет , т.е.7,75 тыс. км. Таким образом определяется интервал периодичностей, внутри которого выполнение операции по предупредительной стратегии целесообразно. Для рассматриваемого примера этот интервал составляет 7,75 - 12 тыс. км.
Таблица 1 - Оценка изменения суммарных затрат (%) на ТО и ремонт и организацию производства в зависимости от стратегии и числа ступеней обслуживания
Удельный вес организационных затрат,%
Стратегия I при числе ступеней
Стратегия II
1
2
3
4
5
10
0
91
83
81
80
80
79
141
5
95
89
88
90
92
99
148
10
100
95
96
98
104
119
155
20
109
108
111
116
126
159
169
Если ряд объектов обслуживания имеют весьма близкие рациональные периодичности, то используется так называемая естественная группировки. Например, вся совокупность несамоконтрящихся крепежных соединений современных грузовых автомобилей обнаруживает два
пика потребности в возобновлении предварительной затяжки в интервалах 3-5 и 10-15 тыс. км. Достаточно близкую периодичность регулирования обнаруживают тормозные механизмы (10-15 тыс. км), клапанные механизмы (9-14 тыс. км), углы установки колес (9-12 тыс. км). Возможны и другие методы группировки, например линейное программирование, метод статистических испытаний. Таким образом, применяя соответствующие методы ТО, производят группировку операции по видам ТО. Ранее отмечалось, что увеличение числа ступеней (видов ТО) теоретически благоприятно сказывается на надежности и суммарных затратах на обеспечение работоспособности, но одновременно увеличиваются затраты, связанные с организацией производственного процесса (подготовительно-заключительное время, планирование постановки на ТО и др.). В таблице 1 приведены данные по изменению трех групп затрат (на ТО, ремонт и организационные), которые подтверждают преимущества предупредительной стратегии и показывают нецелесообразность чрезмерного увеличения числа ступеней (видов) ТО. При увеличении числа ступеней свыше 2-3 удельные затраты собственно на ТО и ремонт практически стабилизируются, приближаясь к условиям выполнения всех операций с оптимальными для них периодичностями.
Таблица 2 - Периодичность ТО автомобилей (I категория условий эксплуатации)
Автомобили
Периодичность, тыс. км
ТО-1
ТО-2
Легковые
4,0
16,0
Автобусы
3,5
14,0
Грузовые и автобусы на базе грузовых автомобилей
3,0
12,0
При учете организационных затрат (планирование, организация производства) существует минимум суммарных затрат, соответствующий (без ежедневного обслуживания) 2-3 видам ТО. Характерно, что рост организационных затрат не только увеличивает общие затраты, но сдвигает, как и следовало ожидать, оптимум в область более простых структур системы ТО и ремонта. Поэтому при наведении порядка в организации и выполнении профилактических работ допустимо начинать и с более простых систем, например единого обслуживания, а затем переходить к рациональным структурам системы ТО и ремонта, обеспечивающим оптимальные затраты и работоспособность.
Действующая в стране система предусматривает следующие виды ТО, отличающиеся по периодичности (таблица 2), перечню и трудоемкости выполненных работ: ежедневное техническое обслуживание (ЕО); первое техническое обслуживание (ТО-1), второе техническое обслуживание (ТО-2); сезонное обслуживание (СО).
Износ и изнашивание сопряженных деталей. Классификация видов изнашивания
Изнашивание - процесс разрушения и отделения материала с поверхности твердого тела и накопления его остаточной деформации пря трении, проявляющийся в постепенном изменении размеров и формы тела. Поверхности трения не являются абсолютно ровными; они обладают микронеровностями, величина которых зависит от точности обработки (точение - до 80 мкм, шлифование - 2...20 мкм, полирование - 0,8...1,3 мкм). При трении возникает взаимодействие микронеровностей трущихся поверхностей между собой и с абразивными частицами, попавшими в масло. Разрушение нескольких слоев микронеровностей приводит к микроповреждениям - изменениям формы поверхности, размеров и формы деталей.
Изнашивание включает целый ряд физико-химических процессов. Происходит снятие тончайших слоев металла - микрорезание и смятие отдельных микронеровностей - пластическая и упругопластическая деформация. В результате многократного упругого деформирования микровыступов возникает усталость образуются трещины и происходит; выкрашивание поверхности. Взаимодействие микронеровностей npfc больших давлениях и скоростях вызывает выделение, тепла. Высокие локальные температуры могут достигать значений, вызывающих изменение структуры металла и повышение его хрупкости, а также приводить к термическим трещинам и даже расплавлению. Одновременно происходит молекулярное взаимодействие поверхностей, заключающееся в сращивании отдельных участков контакта, микронеровностей и в переносе частичек металла с одной поверхности на другую.
Химическая активность поверхностей вызывает коррозию. Скорость изнашивания резко меняется в зависимости, от коррозионной агрессивности среды. Следует также отметить расклинивающее действие масла (эффект акад. П.А. Ребиндера), заключающееся в разрушении поверхностных слоев высоким давлением масла при затекании его в микротрещины,.
С целью управления процессом изнашивания деталей разработана классификация видов изнашивания деталей в зависимости от ведущих процессов разрушения поверхностей трения. Детали автомобилей подвержены практически всем видам изнашивания, которые делят на три группы: механическое, коррозионно-механическое, и электроэрозионное.
Механическое изнашивание является результатом механических действий и включает резание, царапание, деформирование, отслаивание и выкрашивание микрообъемов материала. Основными видами механического изнашивания деталей автомобилей являются: абразивное, гидро и газоабразивное, эрозионное, кавитационное, усталостное, и изнашивание при заедании...
Абразивное изнашивание состоит в основном в режущем и царапающем действии на деталь твердых частиц, находящихся в свободном или закрепленном состоянии. Царапание заключается в образовании углублений на поверхности в направлении. скольжения под воздействием выступов сопряжений детали или свободных твердых частиц; при этом могут происходить многократная пластическая деформация н цикличное образование хрупкого слоя, который затем разрушается,
Изменение структуры материала происходит из-за высокого местного нагрева, ударов, неравномерного изнашивания отдельных зерен металла и т.д. В подшипники с антифрикционным слоем абразивные частицы вдавливаются и при трении увеличивают износ сопряженного вала. Абразивному изнашиванию в сочетании с другими видами подвержены практически все трущиеся детали автомобиля.
Гидроабразивному изнашиванию, происходящему под действием твердых частиц, взвешенных в жидкости и перемещающихся относительно изнашивающейся детали, подвержены водяные, топливные и масляные каналы, а также детали, смазываемые под давлением. При этом абразивными частицами являются не только частицы кварца и других соединений, попадающие на трущиеся поверхности снаружи, но и частицы нагара и продукты износа, образующиеся внутри агрегатов автомобиля.
Газоабразивное изнашивание возникает под воздействием частиц, взвешенных в газе. Этому виду изнашивания подвержены впускные и выпускные системы автомобильных двигателей, а также наружные лакокрасочные покрытия кузовов автомобилей особенно при работе в запыленных условиях. Наибольший износ трущихся поверхностей деталей автомобиля вызывают частицы кварца, поэтому обеспечение чистоты воздуха и эксплуатационных жидкостей, поступающих во внутренние полости агрегатов автомобиля, является важнейшим методом уменьшения интенсивности различных видов абразивного изнашивания.
Трение потоков жидкостей и газов о поверхности деталей вызывает их эрозионное и кавитационное изнашивание.
Эрозионное изнашивание является механическим видом изнашивания в результате воздействия на поверхность детали потока жидкости - гидроэрозионное изнашивание - или газа - газоэрозионное изнашивание. Гидро- и газоэрозионное изнашивания представляют собой процесс вымывания и вырыва отдельных микрообъемов материала. Топливная аппаратура дизелей, жиклеры карбюратора, клапаны газораспределения двигателей подвержены эрозионному изнашиванию;
Кавитация представляет собой образование, а затем поглощение парогазовых пузырьков в движущейся по поверхности детали жидкости при определенных соотношениях давлений и температур в переменных сечениях потока. Разрушение кавитационных пузырьков сопровождается гидравлическими ударами по поверхности детали и образованием каверн, полостей. Иногда кавитационное изнашивание наблюдается на наружных поверхностях гильз цилиндров двигателя, на полостях водяных насосов.
Усталостное изнашивание является механическим изнашиванием в результате усталостного разрушения при повторном деформировании микрообъемов материала поверхностного слоя детали. Усталостное разрушение проявляется в виде выкрашивания - отделения частиц материала, приводящего к образованию ямок (питтинга) на поверхности трения. На развитие питтинга большое влияние оказывает расклинивающее действие масла. На поверхностях, где возможен выход масла из усталостных трещин, питтинги практически не наблюдаются. Усталостное разрушение имеет место на поверхностях кулачков и зубьев шестерен, в подшипниках качения трансмиссии, в антифрикционном слое вкладышей подшипников коленчатого вала двигателя.
На износ некоторых деталей, особенно выполненных из одинаковых материалов, большое влияние оказывает явление местного соединения в местах контакта, происходящее вследствие действия молекулярных сил - схватывание при трении. При этом происходит перенос материала, так как материал одной детали, соединившись с другой, отрывается от первой и остается на поверхности второй детали. Процесс возникновения и развития повреждений поверхностей трения вследствие схватывания и переноса материала называют заеданием.
Изнашиванием при заедании, таким образом, является изнашивание в результате схватывания, глубинного вырывания материала, переноса его с одной поверхности трения на другую и воздействия возникших неровностей на сопряженную поверхность.
Изнашивание при заедании определяется свойствами материалов трущихся деталей и зависит от скорости скольжения поверхностей, а также от температуры. Для деталей автомобиля, когда материал трущихся деталей подобран правильно, схватывание поверхностей может быть вызвано в основном повышением температуры при сухом трении и определяется налипанием и переносом частиц размягченного и даже расплавленного металла. Заедание может завершаться прекращением относительного движения деталей и вызывать их задир - повреждение поверхностей трения в виде широких и глубоких борозд в направлении скольжения. При аварийных отказах систем охлаждения и смазки автомобильных двигателей могут происходить заедание и, как следствие, наблюдаться задиры поршневых колец, поршней, гильз цилиндров, коренных и шатунных подшипников.
Коррозионно-механическое изнашивание является результатом механического воздействия, сопровождаемого химическим или электрическим взаимодействием материала со средой. Для деталей автомобиля коррозия при трении в основном связана с окислением материала поверхностей деталей, т.е. ведущее значение имеет окислительное изнашивание, при котором основное влияние на изнашивание имеет химическая реакция материала с кислородом или окисляющей окружающей средой. При окислительном изнашивании кислород воздуха или растворенный в масле образует на металле окисную пленку, которая механически удаляется при трении. Затем процесс повторяется. Пластическая деформация поверхностных слоев усиливает окисление. Изнашивание в условиях агрессивного действия жидкой среды имеет аналогичный механизм, однако пленки, как правило, малостойкие при трении и скорость процесса резко возрастает. Следует отметить, что пленки окислов и других соединений из-за неметаллической природы не способны к схватыванию. Это используют при разработке противозадирных присадок к маслам - образующиеся достаточно стойкие к стиранию пленки исключают молекулярное схватывание поверхностей. Долговечность, например, основных деталей цилиндропоршневой группы двигателя ограничивается коррозионно-механическим износом, возникающим вследствие выделения в цилиндрах из продуктов сгорания сернистой, серной, угольной, азотной и других кислот.
Электроэрозионное изнашивание является видом эрозионного изнашивания поверхности в результате воздействия разрядов при прохождении электрического тока. Этому виду изнашивания подвержены контакты прерывателя и свечей системы зажигания автомобильного карбюраторного двигателя.
Интенсивность изнашивания, являющаяся отношением величины износа к объему выполненной работы или к наработке, на которой происходило изнашивание детали, зависит, как видно из описания процессов разрушения деталей, от различных факторов. Поэтому обеспечение износостойкости деталей требует различных мероприятий как на стадиях конструирования и изготовления автомобилей, так и при эксплуатации.
Величина износа (И мкм) повышается в течение всего пробега (L, км) автомобиля до предельного состояния детали, но интенсивность изнашивания (vn, мкм/1000 км) различна на разных этапах работы (рис.1.3). Детали после сборки сопрягаются по выступам микронеровностей, образовавшихся при изготовлении. Размеры деталей, хотя и в пределах заданных чертежом допусков, имеют отклонения, что приводит к макро неровностям деталей - овальности, конусности, не плоскостности и т.д. Фактическая площадь контакта трущихся деталей в начальный период мала, поэтому происходит их приработка (см. рис.1.3). Приработка - это процесс изменения геометрии поверхностей трения и физико-механических свойств поверхностных слоев материала в начальный период трения, обычно проявляющийся при постоянных внешних условиях в уменьшении работы трения, температуры и интенсивности изнашивания. Уменьшение приработочных износов достигается работой деталей в облегченных нагрузочных и скоростных режимах, применением специальных масел и усиленной очисткой их от продуктов износа. На период приработки деталей (в течение 1...5 тыс. км) назначают режим обкатки автомобиля.
Период установившегося изнашивания (см. рис.1.3) характеризуется постоянной интенсивностью U= const и, следовательно, линейным возрастанием износа Я при постоянном угле наклона а прямой на графике. В этот период, составляющий для различных деталей 60...500 тыс.км пробега автомобиля, происходят срабатывание и воссоздание пример но стабильных по величине микро неровностей поверхностей и посте пенное накопление макроповреждений - изменение размеров и формы детали.
Износ увеличивает зазоры в сопряжениях деталей, что приводит к ухудшению условий смазывания и повышению динамических, ударных нагрузок; разрушаются специально обработанные износостойкие поверхностные слои. Интенсивность изнашивания повышается - наступает период аварийного изнашивания (см. рис.1.3). Чтобы не допустить полного разрушения детали и всего сопряжения, предельный износ Имах, соответствующий предельному состоянию детали, назначают на начало этого периода.
На работоспособность подвижных сопряжений решающее влияние оказывают зазоры между деталями, которые, как отмечалось выше, увеличиваются в процессе работы вследствие изнашивания деталей. Как правило, в сопряжение входят детали, различной стоимости и сложности, с различной интенсивностью изнашивания. В автомобилях такими сопряжениями являются: коленчатый вал и подшипники; распределительный вал и подшипники; цилиндры и поршневые кольца двигателя; тормозные барабаны и накладки колодок и. т.д.
Схема типичного случая изменения зазора S в течение пробега Lp автомобиля до предельного износа Итах деталей сопряжения представлена на рис.1.4, где видны основные закономерности изменения зазора в сопряжении деталей:
изнашивание деталей А и Б в периоды I, II увеличивает зазор от номинального SH, полученного при сборке, до приработочного Stt и предельного Snp, соответствующего предельному износу Итах быстроизнашивающейся детали;
интенсивность изнашивания деталей сопряжения, как правило, различна (р>а), поэтому быстро изнашиваемую деталь Б сопряжения заменяют па запасную часть Б1, стремясь восстановить зазор примерно до номинального 5;
при значительном износе детали А на пробеге автомобиля до замены детали Б для восстановления зазора S'H целесообразно установить запасную часть Б1 не с номинальным, а с ремонтным размером; при этом, если деталь типа вал (поршень, поршневое кольцо), ремонтный
Рис.1.4 Схема изменения зазора в сопряжении деталей размер должен быть больше номинального, а если типа отверстие (шатунные и коренные вкладыши) - меньше номинального; периоды процесса изнашивания после восстановления зазора повторяются - I', II' - до предельного износа ИмахА, однако вследствие накопления повреждений не замененной деталью А интенсивность изнашивания деталей может несколько возрастать; наработка до замены запасной части Б', как правило, меньше ресурса детали Б из-за возрастания интенсивности изнашивания и несовпадения ресурсов деталей.
В течение длительной эксплуатации автомобиля на процесс изнашивания каждого сопряжения оказывает влияние большое количество переменных факторов, связанных с особенностями изготовления и условиями эксплуатации. Рассмотренная природа изнашивания показывает, что на интенсивность процессов влияют молекулярная структура и другие свойства материалов, точность выполнения деталей, наличие и качество масла, его чистота; нагрузочный, скоростной и тепловой режимы работы, агрессивность среды, конструкция узла. Поэтому при конкретных реализациях изнашивания деталей неизбежны существенные отклонения от рассмотренной схемы (см. рис.1.4) изнашивания: изменение количества замен деталей, изменение длительности периодов (/, /', //, // '), изменение величин зазоров (Sн, Sп, Sпр), и, как следствие, ресурсов деталей. Вместе с тем общие закономерности процессов изнашивания, усталости и коррозии деталей выявляют основные направления повышения их ресурсов и в целом обеспечения надежности автомобильных конструкций при изготовлении и эксплуатации.
Коэффициент технической готовности как основной показатель работы технической службы АТП
Коэффициент технической готовности т определяет долю календарного времени, в течение которого автомобиль (или парк автомобилей) находится в работоспособном состоянии и может осуществлять транспортную работу. Он выражается через отношение числа дней Дэ или автомобиле-дней АДэ эксплуатации автомобилей к сумме числа дней эксплуатации и дней простоя Др на ТО и в ремонте:
; .
Коэффициент технической готовности является одним из показателей, характеризующих работоспособность автомобиля и парков.
Рассмотрим соотношение
, откуда .
Таким образом, коэффициент выпуска непосредственно зависит от коэффициента технической готовности и коэффициента нерабочих дней.
На транспорте общего пользования фактически сложившееся отношение в/т равно для грузовых перевозок 0,75-0,78; для пассажирских 0,91-0,95.
В свою очередь, годовая производительность W, например, при грузовых перевозках (в т-км) непосредственно определяется при прочих равных условиях коэффициентом выпуска и, следовательно, коэффициентом технической готовности:
,
где q - номинальная грузоподъемность, т, - коэффициент использования грузоподъемности, - коэффициент использования пробега; lсс - среднесуточный пробег.
Состояние
Продолжительность пребывания в состоянии, дни
Вероятность состояния (коэффициенты)
Исправен, работает (в эксплуатации)
Дэ
в = Дэ / Дц
Исправен, простаивает в ожидании работы (нерабочие дни, нет водителя)
Дн
н = Дн / Дц
Неисправен (ремонт, ТО, ожидание ремонта)
Др
р = Др / Дц
Все состояния - полный цикл
Дц = Дэ + Дн + Др
в + н + р = 1
Таким образом, увеличение коэффициента технической готовности способствует повышению производительности автомобилей.
Рассмотрим связь коэффициента технической готовности с показателями надежности и организацией технического обслуживания и ремонта.
,
или применительно к эксплуатационному циклу
,
где Др. ц - число дней простоя автомобиля в ремонте за цикл; Дэ. ц - число дней эксплуатации автомобиля за цикл.
Продолжительность эксплуатационного цикла в днях зависит от планируемого пробега или наработки за цикл lК и среднесуточного пробега lсс:
.
Простой на ТО и ремонт за цикл Др. ц складывается из простоя в капитальном ремонте, если он производится, и простоя на ТО и ТР: Др. ц = ДКР + ДТР, ТО. Простой в капитальном ремонте обычно нормируется в календарных днях, а простой в ТО и ТР - в виде удельной нормы dТР в днях на 1000 км пробега. Таким образом, ДТР, ТО=dТРLK/1000.
Следует обратить внимание, что основная доля простоев (до 85-95%) приходится на текущий ремонт на АТП. Поэтому сокращение простоев в ремонте, производимое на АТП, является главным резервом увеличения в и т.
Продолжим анализ коэффициента технической готовности и рассмотрим следующее выражение:
,
где Вр = Др. ц/LК - простои автомобиля во всех видах ТО и ремонта за счет рабочего времени, дней/1000 км. В этом случае
,
где vэ - эксплуатационная скорость, км/ч; Тн - продолжительность рабочей смены (или нарядного времени), ч.
Влияние простоев в ремонте Bр и среднесуточного пробега на т показано на рисунке 1. Необходимо отметить, что с увеличением пробега автомобиля с начала эксплуатации (с его старением) простои в ремонте возрастают, а коэффициент технической готовности уменьшается. На простой при устранении неисправностей и, следовательно, на т влияют также условия эксплуатации, уровень организации ТО и ремонта, квалификация персонала и другие факторы.
Общий простой автомобилей с потерей рабочего времени за период его работы складывается из п простоев. В этом случае средняя наработка на отказ, вызывающий простой, xnp = LK/n. Тогда при средней продолжительности одного простоя продолжительность простоя автомобиля за эксплуатационный цикл.
Следует, что на αт и Вр влияют, во-первых: tпр, характеризующее уровень технологии и организации производства, а также приспособленность автомобиля и его агрегатов к ТО и ремонту (или эксплуатационная технологичность); хпр, определяющее надежность автомобиля, условия эксплуатации, а также качество проведения ТО и ремонта; /сс, характеризующий интенсивность эксплуатации автомобилей. Во-вторых, появляется возможность управления технической готовностью автомобилей на основе количественной оценки мероприятий, которые следует провести для обеспечения заданного уровня коэффициента выпуска и технической готовности, т.е. в конечном итоге работоспособности и производительности. В этом случае возможны решения двух задач. Первая, прямая задача рассматривает конкретные мероприятия, проводимые в технической эксплуатации, влияющие на повышение показателей эффективности, например коэффициента технической готовности. Подобные мероприятия должны влиять на изменение (увеличение) наработки на случай простоя (хпр) и уменьшение продолжительности простоя (tпр), т.е. сокращение Вр.
Как следует, где удельный простой в ремонте определяется тангенсом угла наклона линий I и II к оси абсцисс, переход от исходного значения Вр (I) к необходимому (II) возможен: при сокращении средней продолжительности простоя в ремонте (I) - улучшение ПТБ, механизация, совершенствование технологии и организации; при увеличении средней наработки на случай ремонта (2) - повышения качества ТО и ремонта; многочисленными комбинациями этих способов (3)
Качество автомобиля как совокупность его технико-эксплуатационных свойств. Закономерности изменения показателей качества во времени
Большинство задач, решаемых технической эксплуатацией, связано с понятием качества изделия или материала, т.е. автомобиля, агрегата, детали, технологического оборудования, эксплуатационных материалов при их функционировании или использовании в определенных условиях эксплуатации. Качество - это совокупность свойств, определяющих степень пригодности автомобиля, агрегата, материала к выполнению заданных функций при использовании по назначению. Каждое свойство характеризуется одним или несколькими показателями, которые могут принимать различные количественные значения.
Структура понятия качество
Например, одним из показателей долговечности автомобиля является ресурс до капитального ремонта, составляющий для автомобиля МАЗ-5335 320 тыс. км. Следует отметить, что группа свойств может объединяться в одно комплексное свойство. Например, надежность является сложным свойством, состоящим из таких свойств, как безотказность, долговечность, ремонтопригодность и сохраняемость.
Часть показателей свойств автомобиля, например габаритные размеры, грузоподъемность или вместимость, остаются практически неизменными в течение всего периода эксплуатации. Однако показатели большинства свойств, определяющих качество автомобилей, например экономичности, безопасности, динамичности, производительности, комфортабельности, изменяются в процессе работы (старения) автомобилей. Эти свойства можно поддерживать и восстанавливать, т.е. управлять ими при условии знания закономерностей их изменения.
Изменение основных показателей качества автомобиля средней грузоподъемности.
Срок работы,
лет
Годовая производительность, %
Трудоемкость поддержания в исправном состоянии, %
1
100 (условно)
4
75-80
160-170
8
55-60
200-215
12
45-50
280-300
Автомобиль представляет собой сложную систему, совокупность действующих элементов - сборочных единиц и деталей, обеспечивающих выполнение ее функций. По отношению к автомобилю элементами являются агрегаты, узлы и механизмы, а по отношению к последним - детали. Автомобиль, агрегат, механизм, деталь могут объединяться общим понятием - объект или изделие. Современный автомобиль состоит из 15-20 тыс. деталей, из которых 7-9 тыс. теряют свои первоначальные свойства при работе, причем около 3-4 тыс. деталей имеют срок службы меньше, чем автомобиль в целом. Из них 80-100 деталей влияют на безопасность движения, a 150-300 деталей "критических" по надежности чаще других требуют замены, вызывают наибольший простой автомобилей, трудовые и материальные затраты в эксплуатации. Две последние группы деталей являются главным объектом внимания технической эксплуатации, а также производства и снабжения. У современных автомобилей на 2-3% номенклатуры запасных частей приходится 40-50% общей стоимости потребляемых запасных частей, на 8-10-80-90% и на 20-25 - 96-98%. Отсюда ясна важность информации по объектам, от которых зависит техническое состояние автомобиля.
В процессе эксплуатации автомобиль взаимодействует с окружающей средой, а его элементы взаимодействуют между собой. Это взаимодействие вызывает нагружение деталей, их взаимные перемещения, вызывающие трение, нагрев, химические и другие преобразования и, как следствие, изменение в процессе работы физико-химических свойств и конструктивных параметров: состояния поверхностей, размеров деталей и их взаимного расположения, зазоров, электрических и других свойств. Техническое состояние автомобиля или его элемента определяется совокупностью изменяющихся свойств, характеризуемых текущими значениями, т.е. количественными показателями конструктивных параметров: y1; y2; y3…y4. Например, для двигателя это размеры деталей цилиндро-поршневой группы и кривошипно-шатунного механизма, для тормозов - размеры тормозных накладок, барабанов и зазоры между ними.
Рисунок.2. Изменение показателя технического состояния у и диагностического параметра st в зависимости от пробега: / - зона работоспособности; 2 - зона отказа; /о - оптимальная периодичность регулировки
Возможность непосредственного измерения конструктивных параметров без частичной или полной разборки узла чаще всего ограничена. Для этих изделий при определении технического состояния пользуются косвенными величинами, так называемыми внешними или диагностическими параметрами, которые связаны с конструктивными и дают о них определенную информацию. Например, о техническом состоянии двигателя можно судить по изменению его мощности, расходу масла, компрессии, содержанию продуктов износа в масле.
Различают параметры выходных рабочих процессов, определяющие основные функциональные свойства автомобиля или агрегата (мощность двигателя, тормозной путь автомобиля); параметры сопутствующих процессов (температура нагрева, уровень вибрации, содержание продуктов износа в масле); геометрические (конструктивные) параметры, определяющие связи между деталями в сборочной единице и между отдельными агрегатами и механизмами (зазор, ход, посадка и др.).
В процессе работы автомобиля показатели его технического состояния изменяются от начальных или номинальных значений уН сначала до предельно допустимых уП.Д., а затем и до предельных уП,, что обусловливает соответствующее изменение и диагностических параметров от sН до sП.Д. и sП. Значения уП и sП соответствуют предельному состоянию изделия, при котором его дальнейшее применение по назначению недопустимо или нецелесообразно. Например, при работе тормозов в результате изнашивания тормозных накладок и барабанов происходит увеличение зазора у между накладками и тормозными барабанами, что вызывает рост тормозного пути SТ (рисунок 2). Предельному значению тормозного пути SТ. П, который регламентирован технической документацией (в данном случае Правилами дорожного движения), соответствует предельное значение зазора уП в тормозном механизме.
Этому зазору, в свою очередь, соответствует пробег lP, при котором зазор и тормозной путь достигают предельного значения. Продолжительность работы изделия, измеряемая в часах или километрах пробега, а в ряде случаев в единицах выполненной работы, называется наработкой. Наработка до предельного состояния, оговоренного технической документацией, называется ресурсом. Таким образом, в рассматриваемом примере это lP - ресурс, а в интервале пробега 0 li lP (зона работоспособности) изделие по этому показателю исправно и может выполнять свои функции.
Если изделие удовлетворяет требованиям нормативно-технической документации по всем показателям, то оно считается исправным. Если параметры изделия, характеризующие его способность выполнять заданные функции, соответствуют установленным нормативно-технической документацией требованиям, то оно признается работоспособным. Отсюда следует, что когда автомобиль может выполнять свои основные функции, но не отвечает всем требованиям технической документации (например, помято крыло), он работоспособен, но неисправен.
Если продолжать эксплуатировать автомобиль за пределами lP (например, до lj), то наступит отказ, т.е. событие, заключающееся в нарушении работоспособности. При этом прекращается транспортный процесс (остановка на линии, преждевременный возврат с линии).
Роль предельно допустимого значения параметра заключается в том, чтобы своевременно информировать (предупредить) о приближении момента отказа для принятия соответствующих мер, которые будут рассмотрены ниже.
Показатели качества автомобиля, агрегата, детали ухудшаются с увеличением пробега. Однако сферу эксплуатации интересуют не только начальные значения показателей свойств, характеризующих качество автомобиля, но и характер изменения их в течение всего периода эксплуатации. Для ряда показателей, например производительности, работоспособности, наработки на отказ, характерно изменение от времени эксплуатации или пробега автомобиля по экспоненциальной зависимости
, (1)
где Пк (t), Пк1 - показатели качества на t-м и первому году эксплуатации; k - коэффициент, определяющий интенсивность изменения показателя качества по времени (пробегу); t - продолжительность эксплуатации, годы.
Чем интенсивнее изменение показателей качества автомобилей по времени, тем ниже его эксплуатационные свойства. Поэтому оценка этих показателей должна проводиться с учетом времени эксплуатации изделия. Реализуемый показатель качества - это среднее значение показателя качества за заданный или фактически сложившийся срок службы или пробег автомобиля. Так, реализуемые значения для показателей, приведенных в табл.2.1, составят 68,5-72,5 для производительности и 185-196 для трудоемкости. Реализуемый показатель для условий, описанных формулой (1), определяется так:
.
Реализуемый показатель качества управляем на народнохозяйственном, межотраслевом и отраслевом уровнях. Начальное значение показателя качества определяется с учетом требований эксплуатации сферой производства. Срок службы изделия зависит не только от его конструкции и условий эксплуатации, но и от баланса между потребностью и' объемом производства данных моделей автомобилей, а также от правильно реализуемой эксплуатацией политики обновления основных фондов. Интенсивность изменения первоначальных показателей качества изделия зависит от сферы производства и эксплуатации.
Автомобильная промышленность влияет на интенсивность изменения показателей качества повышением износостойкости и прочности деталей, качества применяемых материалов и т.п. Сфера эксплуатации влияет на интенсивность изменения показателей качества, а следовательно, и на реализуемый показатель, совершенствуя методы и средства обеспечения работоспособности, квалификацию персонала ИТС регулируя возрастной состав парка и другими способами.
Методы управления реализуемым значением показателя качества.
Таким образом, не только сфера производства, но и сфера эксплуатации, в частности техническая эксплуатация, могут активно влиять на реализуемые значения показателей качества, т.е. управлять ими. Считается, что их вклад в эти значения соотносится как 3: 2.
Техническая эксплуатация автомобилей является важнейшей подсистемой автомобильного транспорта. Если сфера производства обеспечивает потенциальную возможность осуществления транспортного процесса, то техническая эксплуатация делает эту возможность фактической, поставляя для перевозочного процесса исправные автомобили.
Место технической эксплуатации в транспортном процессе
Количественное измерение процесса изменения показателей качества автомобиля во времени (или по пробегу) оценивается надежностью. Надежность - это свойство объекта, в том числе и автомобиля, сохранять во времени в установленных пределах значения всех параметров, характеризующих способность выполнять требуемые функции в заданных режимах и условиях применения, технического обслуживания, ремонтов, хранения и транспортирования.
При этом надежность является сложным свойством, которое зависит от сочетания таких свойств, как безотказность, долговечность, ремонтопригодность и сохраняемость.
Допустимые пределы эксплуатационных показателей определяются соответствующей документацией (стандартами, правилами, положениями, техническими условиями), а в ряде случаев - сложившимся опытом. Надежность как свойство характеризует и позволяет количественно оценить, во-первых, текущее состояние, во-вторых, насколько быстро происходит изменение показателей качества автомобиля при его работе в определенных условиях эксплуатации.
Экономико-вероятностный метод ТО
Используя экономико-вероятностный метод, можно определить целесообразность выполнения данной операции не с оптимальной для нее, а с заданной периодичностью стержневой операции. Воспользовавшись картой профилактической операции, определяют зону наработок, в которой удельные затраты при предупредительной стратегии остаются ниже, чем при устранении возникшего отказа (см. рисунок 9). Если в этой зоне находится периодичность стержневой операции, то изменение периодичности для данной операции допустимо.
Приведены графики, позволяющие определить предельно допустимое значение коэффициента относительных затрат на ТО и ремонт kпд, превышение которого при изменении периодичности нецелесообразно по экономическому критерию, Определим целесообразность выполнения ранее рассмотренной в качестве примера операции не с оптимальной для нее периодичностью lо = 12 тыс. км, а с периодичностью lТО = 5,5 тыс. км. При выполнении операции с заданной периодичностью коэффициент периодичности , Для этого значения и коэффициента вариации vx = 0,4 предельное значение коэффициента kпд = 0,27 при фактическом значении kп = 0,4. Так как kп > kпд, то по экономическому критерию проведение данной операции по профилактической стратегии с периодичностью 5,5 тыс. км нерационально. Нижняя граница периодичности ТО, при которой данную операцию еще целесообразно проводить профилактически, составляет , т.е.7,75 тыс. км. Таким образом определяется интервал периодичностей, внутри которого выполнение операции по предупредительной стратегии целесообразно. Для рассматриваемого примера этот интервал составляет 7,75 - 12 тыс. км.
Если ряд объектов обслуживания имеют весьма близкие рациональные периодичности, то используется так называемая естественная группировки. Например, вся совокупность несамоконтрящихся крепежных соединений современных грузовых автомобилей обнаруживает два
пика потребности в возобновлении предварительной затяжки в интервалах 3-5 и 10-15 тыс. км. Достаточно близкую периодичность регулирования обнаруживают тормозные механизмы (10-15 тыс. км), клапанные механизмы (9-14 тыс. км), углы установки колес (9-12 тыс. км). Возможны и другие методы группировки, например линейное программирование, метод статистических испытаний. Таким образом, применяя соответствующие методы ТО, производят группировку операции по видам ТО. Ранее отмечалось, что увеличение числа ступеней (видов ТО) теоретически благоприятно сказывается на надежности и суммарных затратах на обеспечение работоспособности, но одновременно увеличиваются затраты, связанные с организацией производственного процесса (подготовительно-заключительное время, планирование постановки на ТО и др.). В таблице 1 приведены данные по изменению трех групп затрат (на ТО, ремонт и организационные), которые подтверждают преимущества предупредительной стратегии и показывают нецелесообразность чрезмерного увеличения числа ступеней (видов) ТО. При увеличении числа ступеней свыше 2-3 удельные затраты собственно на ТО и ремонт практически стабилизируются, приближаясь к условиям выполнения всех операций с оптимальными для них периодичностями.
Таблица 2 - Периодичность ТО автомобилей (I категория условий эксплуатации)
Автомобили
Периодичность, тыс. км
ТО-1
ТО-2
Легковые
4,0
16,0
Автобусы
3,5
14,0
Грузовые и автобусы на базе грузовых автомобилей
3,0
12,0
При учете организационных затрат (планирование, организация производства) существует минимум суммарных затрат, соответствующий (без ежедневного обслуживания) 2-3 видам ТО. Характерно, что рост организационных затрат не только увеличивает общие затраты, но сдвигает, как и следовало ожидать, оптимум в область более простых структур системы ТО и ремонта. Поэтому при наведении порядка в организации и выполнении профилактических работ допустимо начинать и с более простых систем, например единого обслуживания, а затем переходить к рациональным структурам системы ТО и ремонта, обеспечивающим оптимальные затраты и работоспособность.
Действующая в стране система предусматривает следующие виды ТО, отличающиеся по периодичности (таблица 2), перечню и трудоемкости выполненных работ: ежедневное техническое обслуживание (ЕО); первое техническое обслуживание (ТО-1), второе техническое обслуживание (ТО-2); сезонное обслуживание (СО).
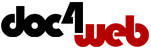
Нравится материал? Поддержи автора!
Ещё документы из категории транспорт :
Чтобы скачать документ, порекомендуйте, пожалуйста, его своим друзьям в любой соц. сети.
После чего кнопка «СКАЧАТЬ» станет доступной!
Кнопочки находятся чуть ниже. Спасибо!
Кнопки:
Скачать документ