Техническое перевооружение автотранспортного предприятия
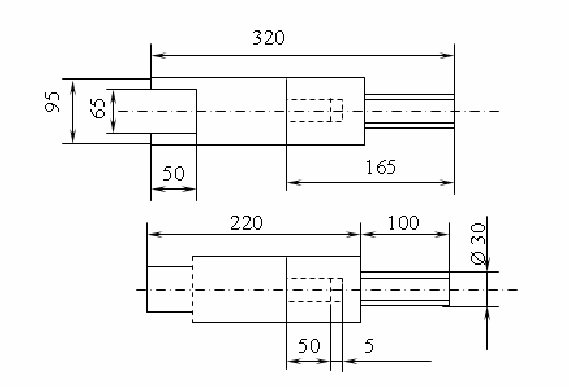



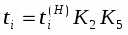

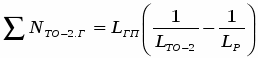
Содержание
Введение
1. Анализ существующей организации и технологии ТО и Р автобусов и их техническое оснащение
1.1 Характеристика подвижного состава
1.2 Технологический процесс ТО и Р
1.3 Оснащенность ремонтной базы
2. Технологическое проектирование цеха автобусного парка в целях повышения производительности труда, охраны окружающей среды и повышения механизации технологических процессов
2.1 Основные показатели работы подвижного состава
2.2 Корректировка нормативов ресурсного пробега и периодичности ТО
2.3 Расчет коэффициента технической готовности
2.4 Расчет годовых пробегов подвижного состава и производственной программы ТО
2.5 Корректирование нормативных трудоемкостей ТО и ТР
2.6 Расчет годовых объемов работ ЕО, ТО и ТР
2.7 Расчет объема вспомогательных работ и численности основных и вспомогательных рабочих
3. Проектирование нестандартного технологического оборудования, в целях совершенствования ТО и Р
3.1 Назначение, устройство и принцип действия оборудования (приспособления)
3.2 Расчет детали на прочность
4. Организация и технология диагностирования автобусов
4.1 Организация работ по диагностированию
4.2 Диагностирование автобусов перед ТО-1 и ТО-2
5. Экономическая эффективность от внедрения результатов проекта
5.1 Выбор базы для сравнения
5.2 Расчет плановой калькуляции себестоимости ТО-1, ТО-2, ТР
5.3 Стоимость общепроизводственных расходов определяем по статьям общепроизводственных расходов
5.4 Расчет инвестиционной эффективности
6. Безопасность жизнедеятельности при проведении ТО и ремонта
6.1 Организационно-правовые основы охраны труда
6.2 План мероприятий по улучшению условий и охране труда
6.3 Инструкция по технике безопасности для работы в цехе АТП
6.4 Охрана окружающей среды
Заключение
Список литературы
Приложение 1
Приложение 2
Приложение 3
Введение
На современном этапе развития мировой экономики автомобильный транспорт для большинства развитых стран является основным видом внутреннего транспорта и ключевым элементом транспортной системы страны, который играет главную роль в обеспечении экономического роста и социального развития. На этапе становления рыночных отношений в Российской Федерации сложились объективные предпосылки для ускоренного развития автомобильного транспорта. Автомобильному транспорту нет адекватной замены при перевозках на небольшие и средние расстояния или, например, пассажирских перевозок в пределах населенного пункта.
Процесс автомобилизации нашей страны не должен ограничиваться только увеличением парка автомобилей, он так же вызывает необходимость решения ряда вопросов, направленных на дальнейшее развитие материально-технической базы для хранения, технического обслуживания и ремонта транспортных средств. Одной из важнейших задач в области эксплуатации автомобильного парка является дальнейшее совершенствование организации технического обслуживания и текущего ремонта автомобилей с целью повышения их работоспособности и вместе с тем снижение затрат на эксплуатацию. Актуальность указанной задачи подтверждается и тем, что на техническое обслуживание автомобиля затрачивается во много раз больше труда и средств, чем на его производство.
Задача повышения эффективности капитальных вложений и снижения издержек является частью проблемы рациональной организации автомобильного транспорта и охватывает широкий круг эксплуатационных, технологических и строительных вопросов. Решение этой задачи обеспечивается в первую очередь качественным перепроектированием предприятий, которое в значительной мере предопределяет рациональное использование основных фондов и высокую эффективность капитальных вложений.
В современных условиях успешное выполнение перевозок грузов и пассажиров немыслима без коренного улучшения способов и механизмов проведения своевременной диагностики транспортного средства, а так же его ремонта и технического обслуживания. В настоящее время дальнейшее развитие получила планово-предупредительная система технического обслуживания и ремонта подвижного состава АТП.
Среди основных направлений улучшения процесса ТО и Р можно выделить повышение уровня автоматизации и механизации на постах ТО, совершенствование методов в управлении ремонтом и диагностики, а так же внедрение управления качеством технического обслуживания парка.
Как в области организации автомобильных перевозок, так и в области технической эксплуатации автомобилей начинают применяться различные экономико-математические методы анализа, планирования и проектирования. Все шире разрабатываются и внедряются новые методы и средства диагностирования технического состояния и прогнозирования ресурсов безотказной работы автомобилей. Создаются новые виды технологического оборудования, позволяющие механизировать, а в ряде случаев и автоматизировать трудоемкие операции по обслуживанию и ремонту подвижного состава. Разрабатываются современные формы управления производством, которые рассчитаны на применение электронно-вычислительных машин с дальнейшим переходом на автоматизированную систему управления.
В данной дипломной работе была предпринята попытка создания программы переоснащения ремонтного участка АТП. С этой целью был проведен анализ существующего порядка проведения ТО и Р, выявлены некоторые моменты, требующие реорганизации. Определен список технологического оборудования, требующего усовершенствования. Был составлен план дооснащения некоторых участков цеха новыми техническими средствами, была рассчитана экономическая эффективность от внедрения данных нововведений.
В план переоснащения так же были заложены ряд параметров для улучшения условий труда на АТП. Был проанализирован комплекс мер по обеспечению безопасности жизнедеятельности на данном АТП.
В ходе проведения расчетов и исследований мы сознательно не учитывали программу переоснащения парка автотранспортного предприятия, так как уже не первый год проходит плановая замена парка. Подвижной состав, выработавший свой ресурс постепенно списывается и на смену ему приходят новая техника, отвечающая всем современным требованиям. На предприятии широкое применение стали получать автобусы малого класса, что позволяет существенно сократить ремонтные расходы, используя технологическое оборудование пригодное для проведения осмотров легковой части парка АТП
В целом весь комплекс мер, предложенных в данной работе должны оптимизировать порядок проведения То и Р, снизить текущие затраты и повысить работоспособность автопарка.
Важнейшей задачей в любом хозяйстве является организация технического обслуживания и текущего ремонта автомобилей. Этой актуальной теме и посвящается дипломный проект.
1. Анализ существующей организации и технологии ТО и Р автобусов и их техническое оснащение
1.1 Характеристика подвижного состава
Подвижной состав автомобильного транспорта классифицируется в зависимости от вида применяемого топлива для двигателя, а также от характера использования автомобилей в народном хозяйстве. По характеру использования подвижной состав разделяется на транспортный (грузовой и пассажирский) и специальный. Транспортный подвижной состав предназначен для перевозки грузов или пассажиров, специальный - для выполнения различных, преимущественно нетранспортных работ, производимых с помощью установленного на нем оборудования. К транспортному подвижному составу относятся грузовые автомобили, седельные тягачи с полуприцепами, грузовые прицепы, легковые автомобили, автобусы и пассажирские прицепы, а к специальному - пожарные автомобили, автокраны, машины для уборки городских территорий, передвижные ремонтные мастерские, автомагазины и т. п. Транспортный подвижной состав в свою очередь делится на подвижной состав общего назначения и специализированный (по виду и характеру перевозок).
Для каждого вида пассажирских перевозок должен выбираться подвижной состав с соответствующими техническими характеристиками.
На предприятии существует необходимость иметь три класса техники. С одной стороны нужны автобусы среднего и большого классов для перевозки пассажиров, с другой – автобусы малого класса (типа ГАЗель) для непосредственной доставки людей на место работы. А так же достаточный парк легковых автомобилей. Использование автобусов малого класса оправдано экономически, так как резко сокращаются затраты на проведение То и Р.
Пассажирские автомобили в зависимости от вместимости, конструкции и назначения разделяются на легковые автомобили и автобусы. Автобусы классифицируются по длине кузова, определяющей вместимость, и по назначению. По длине автобусы подразделяются на:
По назначению автобусы подразделяются на: городские и пригородные; местного сообщения; междугородные; туристские и экскурсионные. В исследуемом АТП присутствуют не только автобусы, но так же фургоны и легковые автомобили, грузовики.
Характеристика подвижного состава имеющегося на предприятии приведена в таблице 1.
Таблица 1.
Подвижной состав
№ п/п
Гаражный №
Марка а/м
Тип а/м
Гос.№
Год выпуска
Вид топл.
1
2179
Шевроле Нива
л/а
Е477КУ
2006
АИ92
2
2180
Шевроле Нива
л/а
Е478КУ
2006
АИ92
3
2181
Форд Фокус
л/а
О692ОО
2006
АИ95
4
2182
Шевроле Экспр
л/а
Е236НТ
2004
АИ95
5
2183
ВАЗ 21214
л/а
Е158АУ
2005
АИ92
6
2184
ВАЗ 21214
л/а
Е157АУ
2005
АИ92
7
2186
Шевроле Нива
л/а
Е043АВ
2004
АИ92
8
2187
ГАЗ 31105
л/а
Е300АВ
2004
АИ92
9
2189
ГАЗ 31105
л/а
Е181АВ
2004
АИ92
10
2190
Вольво S80
л/а
В703УТ
2000
АИ95
11
2191
ВАЗ 21310
л/а
В249ВЕ
2000
АИ92
12
2192
ГАЗ 311000
л/а
В545ЕО
1999
АИ92
13
2193
ГАЗ 3102
л/а
В695НС
2003
АИ92
14
2194
Вольво S70
л/а
А400ХЕ
1998
АИ95
15
2195
Volkswagen
л/а
В282УН
2000
АИ95
16
2197
ГАЗ 311000
л/а
В352ВЕ
1997
АИ92
17
2198
УАЗ 31514
л/а
А017СМ
1997
АИ92
18
2199
ГАЗ 2217
микроавтобус
В694НС
2003
АИ92
19
2200
ГАЗ 322100
микроавтобус
В042ПРОФ
1999
АИ92
20
2201
ГАЗ 31105
л/а
Е452КУ
2006
АИ92
21
2202
ГАЗ 311000
л/а
А336ХХ
1998
АИ92
22
2203
ГАЗ 3102
л/а
В455УН
2000
АИ92
23
2204
ВАЗ 21213
л/а
А482ХХ
1999
АИ92
24
2205
ГАЗ 3102
л/а
В442УУ
2000
АИ92
25
2206
Volkswagen
л/а
О466ОО
2002
АИ95
26
2208
ГАЗ 3102
л/а
А500ХХ
1999
АИ92
27
2209
Honda GR-V
л/а
В255НК
2003
АИ95
28
2210
ВАЗ 21213
л/а
В453УН
2000
АИ92
29
2211
ВАЗ 21213
л/а
В851СН
1999
АИ92
30
2212
ГАЗ 311000
л/а
В400ЕО
2002
АИ92
31
2214
ВАЗ 21214
л/а
Е004АО
2005
АИ92
32
2215
Honda GR-V
л/а
О004ОО
2003
АИ95
33
2216
ВАЗ 2121
л/а
В785ВК
1999
АИ92
34
2217
ВАЗ 2121
л/а
В048ОУ
1999
АИ92
35
2218
ВАЗ 2121
л/а
В049ОУ
1999
АИ92
36
2219
Toyota
л/а
О880ОО
2003
Д/Т
37
2220
Toyota
л/а
О878ОО
2003
Д/Т
38
2222
ВАЗ 21310
л/а
Е159АУ
2005
АИ92
39
2224
ВАЗ 21214
л/а
Е175АВ
2004
АИ92
40
2225
ВАЗ 21214
л/а
Е173АВ
2004
АИ92
41
2229
ВАЗ 21214
л/а
Е188АВ
2004
АИ92
42
2230
УАЗ 390902
грузовой фургон
В687СТ
2004
А80
43
2231
ВАЗ 32106
учебный
Е186АВ
2004
АИ92
44
2233
ВАЗ 32106
учебный
Е174АВ
2004
АИ92
45
2236
УАЗ 31519
л/а
Е176АВ
2004
А80
46
2237
УАЗ 31519-01
л/а
А336УВ
1997
АИ92
47
2239
ВАЗ 21070
учебный
В389ОУ
1999
АИ92
48
2240
УАЗ 3962-01
спецфургон
А302ЕУ
1994
АИ92
49
2241
УАЗ 3962-01
спецфургон
В805СН
1994
А80
50
2242
УАЗ 31514
л/а
В058НТ
2003
А80
51
2243
ГАЗ 2217
микроавтобус
В750ОУ
2000
АИ92
52
2244
РАФ 22031
скорая помощь
А661ЕА
1993
АИ92
53
2245
УАЗ 22069
микроавтобус
В197УН
2000
А80
54
2246
ГАЗ 2217
микроавтобус
Е041АВ
2004
АИ92
55
2247
ГАЗ 31105
л/а
В939ХО
2004
АИ92
56
2248
ГАЗ 31105
л/а
В 949ХО
2004
АИ92
57
2250
ГАЗ 2217
микроавтобус
Е042АВ
2004
АИ92
58
2251
УАЗ 31519
л/а
Е179АВ
2004
А80
59
2252
УАЗ 39094
бортовая
Е178АВ
2004
А80
60
2253
УАЗ 39099
грузовой фургон
Е321ЕУ
2005
А80
61
2254
УАЗ 39094
бортовая
Е196АВ
2004
А80
62
2255
УАЗ 3909
грузовой фургон
Е184АВ
2004
А80
63
2256
УАЗ 3909
грузовой фургон
Е193АВ
2004
А80
64
2258
УАЗ 3909
грузовой фургон
Е195АВ
2004
А80
65
2259
УАЗ 39099
грузовой фургон
В194УН
2000
АИ92
66
2260
УАЗ 3909
грузовой фургон
Е190АВ
2004
А80
67
2261
Фольксваген
грузовой фургон
В890СН
1976
АИ92
68
2262
УАЗ 3909
грузовой фургон
Е185АВ
2004
А80
69
2263
УАЗ 39099
грузовой фургон
В196УН
2000
А80
70
2264
УАЗ 3909
грузовой фургон
Е182АВ
2004
А80
71
2265
УАЗ 3909
грузовой фургон
Е187АВ
2004
А80
72
2266
УАЗ 2206-030
грузопассажирский
А594СР
1997
А80
73
2268
ВАЗ 21214
л/а
Е236АВ
2004
АИ92
74
2269
ГАЗ 270500
грузовой фургон
В416ОК
1999
АИ92
75
2270
ГАЗ 322100
микроавтобус
В386ОУ
1999
АИ92
76
2271
ВАЗ 21214
л/а
Е239АВ
2004
АИ92
77
2272
УАЗ 31519
л/а
Е241АВ
2004
А80
78
2273
ГАЗ 33027-415
грузовой фургон
Е015КА
2005
АИ92
79
2274
ГАЗ 33027-415
грузовой фургон
Е014КА
2005
АИ92
80
2275
UAZ PATRIOT
л/а
Е091КУ
2006
АИ92
81
2276
УАЗ 331519
л/а
Е089КУ
2006
АИ92
82
2277
УАЗ 39099
грузовой фургон
Е088КУ
2006
А80
83
2278
УАЗ 39099
грузовой фургон
Е092КУ
2006
А80
84
2279
ГАЗ 328111-002
Аварийно спасательн.
Е087КА
2005
АИ92
85
2280
УАЗ 3909
грузовой фургон
Е183АВ
2004
А80
86
2281
УАЗ 396259
грузовой фургон
Е240АВ
2004
А80
87
2282
УАЗ 22069
грузовой фургон
Е192АУ
2005
А80
88
2283
УАЗ 39099
грузовой фургон
Е193АУ
2005
А80
89
2284
3260С
скорая помощь
2005
АИ92
90
2285
ВАЗ 21213
л/а
А481ХХ
1999
АИ92
91
2286
УАЗ 39094
бортовая
Е411КУ
2006
А80
92
2287
УАЗ 39094
бортовая
Е412КУ
2006
А80
93
2290
УАЗ 3962-01
грузовой фургон
А308ЕУ
1992
АИ92
94
2292
УАЗ 3909
грузовой фургон
В751ОУ
2000
А80
95
2293
УАЗ 3909
каратажная
А641ЕА
1994
А80
96
2294
ГАЗ 22177
микроавтобус
Е115АВ
2004
АИ92
97
2296
УАЗ 31512
л/а
В553МК
1994
А80
98
2299
УАЗ 3909
спецфургон
А239ХХ
1994
А80
99
2300
УАЗ 39099
грузовой фургон
В207ВЕ
2000
А80
100
2302
УАЗ 3909
спецфургон
А061СМ
1995
АИ92
101
2303
УАЗ 39099
грузовой фургон
В213ТМ
2000
АИ92
102
2305
УАЗ 31514
л/а
Е044АВ
1999
А80
103
2851
Икарус 280
автобус
А307ХХ
1992
Д/Т
104
2852
Икарус 280
автобус
В442ОУ
1992
Д/Т
105
2853
Икарус 280
автобус
А143ХХ
1990
Д/Т
106
2855
Икарус 280
автобус
А336ЕУ
1995
Д/Т
107
2860
Икарус 280
автобус
АА610
1989
Д/Т
108
2861
Икарус 280
автобус
АА611
1989
Д/Т
109
2862
Волжанин
автобус
АА961
2001
А80
110
2863
Волжанин
автобус
АА963
2001
Д/Т
111
2864
Волж.527004
автобус
АА618
2004
Д/Т
112
2865
Волж.527004
автобус
АА619
2004
Д/Т
113
2866
Волж.527004
автобус
АС451
2005
Д/Т
114
2867
Волж.527004
автобус
АС452
2005
Д/Т
115
2868
Волж.527004
автобус
АС453
2005
Д/Т
116
2869
Волж.527004
автобус
АС454
2005
Д/Т
117
2876
Икарус 260
автобус
АА609
1989
Д/Т
118
2877
Икарус 260
автобус
АА972
1989
Д/Т
119
2878
Икарус 260
автобус
АА605
1982
Д/Т
120
2879
Икарус 260
автобус
АА606
1982
Д/Т
121
2880
Икарус 260
автобус
АА607
1982
Д/Т
122
2881
Икарус 260
автобус
АА968
1982
Д/Т
123
2884
Икарус 260
автобус
АА969
1982
Д/Т
124
2885
Икарус 260
автобус
АА608
1982
Д/Т
125
2886
Икарус 260
автобус
АА604
1982
Д/Т
126
2887
Икарус 260
автобус
АА970
1982
Д/Т
127
2921
Икарус 260
автобус
АА964
1982
Д/Т
128
2923
Икарус 260
автобус
АА960
1982
Д/Т
129
2925
Икарус 260
автобус
АА612
1982
Д/Т
130
2926
Икарус 260
автобус
АА974
1982
Д/Т
131
2927
Икарус 260
автобус
АА603
1982
Д/Т
132
2928
МаРЗ 52661
автобус
АА962
1999
Д/Т
133
2930
ЛАЗ-695
автобус
АА971
1994
А80
134
2931
ЛАЗ-695
автобус
АА976
1994
А80
135
2935
ЛАЗ-695
автобус
АА965
1994
А80
136
2936
Икарус 256
автобус
АА959
1989
Д/Т
137
2937
Икарус 256
автобус
АА957
1989
Д/Т
138
2938
Икарус 256
автобус
АА958
1989
Д/Т
139
2941
ПАЗ 32051
автобус
В671ВК
1994
А80
140
2942
ПАЗ 32051
автобус
АА975
1995
А80
141
2958
ПАЗ 32051
автобус
АА966
1994
А80
142
2959
ПАЗ 32051
автобус
АА973
1994
А80
143
2960
ПАЗ 32051
автобус
АА967
1994
А80
144
2990
ГАЗ 3307
Бортовой
7672 КСМ
1992
А80
145
2991
ЗИЛ 4514
Самосвал
В246УМ
1993
Д/Т
146
5004
МТЗ 82
Трактор
б/н
1993
Д/Т
147
5000
4045
Погрузчик
б/н
А80
148
ГА 2705
грузовой фургон
2006
АИ92
Вывод: Из таблицы 1 видно, что парк подвижного состава имеет небольшую разномарочность. Это в свою очередь повышает качественное обеспечение запасными частями и проведение работ по ТО и ремонту. Среди автобусов преобладает марка «Икарус» с достаточно большим пробегом и сроком эксплуатации. Разномарочность легковых автомобилей выше.
1.2 Технологический процесс ТО и Р
Техническое обслуживание подвижного состава по периодичности, перечню и трудоемкости выполняемых работ подразделяется на:
ежедневное техническое обслуживание (ЕО);
первое техническое обслуживание (ТО-1);
второе техническое обслуживание (ТО-2);
сезонное техническое обслуживание (СО).
Ежедневное обслуживание (ЕО) включает в себя: проверку прибывающего с линии и выпускаемого на линию подвижного состава, внешний уход за ним и заправочные операции. Для проверки подвижного состава в автотранспортном предприятии создается контрольно-технический пункт (КТП) с осмотровой канавой и комплектом необходимых, инструментов, приспособлений и оборудования. Проверка подвижного состава входит в обязанности водителя и работников отдела технического контроля (ОТК).
Первое техническое обслуживание (ТО-1) включает контрольные, крепежные, регулировочные и смазочные операции, выполняемые, как правило, без снятия с подвижного состава или частичной разборки (вскрытия) обслуживаемых приборов, узлов и механизмов.
Второе техническое обслуживание (ТО-2) включает в себя все операции ТО-1, производящиеся в расширенном объеме, причем в случае необходимости обслуживаемые приборы, узлы и механизмы вскрывают или снимают с подвижного состава.
Сезонное техническое обслуживание (СО) проводится 2 раза в год. Оно является подготовкой подвижного состава к эксплуатации в холодное и теплое время года, преимущественно совмещается с ТО-2 с соответствующим увеличением трудоемкости работ.
На исследуемом АТП применяется обычная схема работы с подвижным составом во время приема автобусов с линии. Рассматриваем только работу с автобусами, так как именно этот вид транспорта непосредственно связан с технологическим процессом. Процесс технического обслуживания грузового транспорта, а так же легковых автомобилей, имеющихся в наличии на АТП, описывается в соответствующих графиках (план проведения ТО). Схема работы с подвижным составом осуществляется по схеме, приведенной в рисунке 1.
Рисунок 1.
Прием с линии
Выпуск на линию
Контроль технического состояния
ЕО
Х
Р
А
Н
Е
Н
И
Е
ТР
Контроль качества ремонта
ТО
По возвращении подвижного состава с линии, устанавливается время прибытия, показание счетчика пройденного расстояния и остаток топливав баке автобуса. Данные фиксируются в отдельной таблице. Кроме того проверяется наличие неисправностей, поломок, повреждений и определяется потребность в текущем ремонте (ТР).
В случае необходимости составляется заявка на текущий ремонт с перечнем неисправностей, подлежащих устранению, и акт о повреждении подвижного состава с указанием характера, причин поломки и лиц, ответственных за нее.
Заправочные операции ЕО — заправку автомобилей топливом, доливку масла в картер двигателя и охлаждающей жидкости в радиатор производят водители за счет своего рабочего времени, предусмотренного режимом их работы. Заправка топливом производится, как правило, на автозаправочных станциях, доливка масла и воды в автотранспортном предприятии.
ТО-1 выполняется между рабочими сменами подвижного состава (в межсменное время). Для проведения ТО-2 подвижной состав может сниматься с эксплуатации.
Техническое обслуживание ТО-1 и ТО-2 выполняется через определенный пробег, устанавливаемый в зависимости от условий эксплуатации подвижного состава. Нормативная частота проведения ТО определяется по пробегу автомобиля. (таблица 2).
Таблица 2.
Типы автомобилей
Переодичность технического обслуживания, км
ТО-1
ТО-2
Легковые
Автобусы
Грузовые автобусы на базе грузовых автомобилей
3 500
2 600
2 200
14 000
13 000
11 000
Сроки постановки подвижного состава в обслуживание указываются в планах-графиках по общему пробегу от начала эксплуатации по показаниям счетчика пройденного расстояния. Данные счетчика фиксируются в тех. картах.
На исследуемом АТП существует график проведения обязательного капитального ремонта (КР) подвижного состава, в целях соблюдения сроков которого по необходимости проводится текущий ремонт (ТР). Он выполняется путем проведения разборочно-сборочных, слесарно-подгоночных и других необходимых работ с заменой: у агрегата отдельных изношенных или поврежденных деталей кроме базовых (корпусных); у автомобиля отдельных узлов и агрегатов, требующих текущего или капитального ремонта. На АТП существует достаточный запас готовых узлов и агрегатов, как новых, так и восстановленных после КР.
К базовым (корпусным) деталям автомобиля относятся блок цилиндров, картер коробки передач, трубы карданного вала, картер ведущего моста, балка переднего моста или поперечина при независимой подвеске, картер рулевого механизма и гидроусилителя, каркас кабины, продольные балки рамы.
Далее автобус поступает на хранение в отапливаемый гараж. На территории АТП «Карельский окатыш» есть гараж на 50 автобусов, а так же открытая площадка для стоянки.
При выпуске на линию подвижного состава проверяется его внешний вид, комплектность и техническое состояние, а также выполнение назначенного для него накануне обслуживания или ремонта (по данным внешнего осмотра и учетной документации).
Проверка производится по определенному перечню операций, составляемому в автотранспортном предприятии с учетом конструкции нспользуемого подвижного состава и условий его эксплуатации. Перечень предусматривает обязательную проверку исправности систем, агрегатов, узлов и деталей подвижного состава, влияющих на безопасность движения, в том числе рулевого управления, тормозов, подвески, колес и шин, кузова и кабины, приборов наружного освещения, световой и звуковой сигнализации, стеклоочистителей.
При смене водителей на линии техническое состояние подвижного состава на момент его передачи проверяется водителем, закончившим смену, совместно с водителем, приступающим к работе. Исправность подвижного состава подтверждается подписями водителей в путевом листе с указанием времени передачи и показаний спидометра.
Для выполнения операций внешнего ухода за подвижным составом, заключающихся в уборке кузова и кабины, мойке и обтирке или обсушке, в автотранспортном предприятии существует пост внешнего ухода с моечными установками и другим необходимым оборудованием.
Таким образом, на исследуемом АТП введена планово-предупредительная система технического обслуживания. Для поддержания машин в работоспособном состоянии проводится весь комплекс мер по выявлению и предупреждению неисправностей. На предприятии специально оборудованы посты для проведения текущего ремонта и диагностики. Отдельно оборудован участок для проведения ТО 1 и ТО 2. Кроме этого совмещены малярный и сварочный участки, что позволяет выполнять работы на кузове «в потоке».
1.3 Оснащенность ремонтной базы
Техническое обеспечение АТП представляет собой процесс снабжения автопредприятий агрегатами, запасными частями, автомобильными шинами, аккумуляторами и материалами, необходимыми для нормальной их работы. Но самой главной его составляющей считается комплекс вспоогательного оборудования, необходимого для проведения всех предусмотренных технологией операций с подвижным составом. Правильная организация постов обслуживания играет важную роль в поддержании парка в исправном состоянии.
Оснащенность ремонтной базы предприятия технологически необходимым оборудованием показано в таблице 3
Таблица 3
Ведомость наличия ОС.
№ п/п
Наименование, обозначение, тип, модель оборудования, оснастки
Кол-во
Стоимость
Процент износа
1.
Hастольно-свеpлильный станок СФ-16-01
1
16826,00
5
2.
Автопогpузчик г/п 5тн
1
55370,00
18,9
3.
Аппарат высокого давления без нагрева 1.286-501
1
70232,80
16,667
4.
Аппарат моечный высокого давления НД 10/25
1
71186,44
14,286
5.
Вентиляционная установка "Плимут"
1
21327,77
10
6.
Вытяжное устройсво "ПЛИМУТ"
2
43073,34
10
7.
Газоанализатор Инфакар-08,01
1
33972,88
11,111
8.
Дистилятор Д - 4 (Б-6199 руб.)
1
6199,00
0
9.
Домкрат гидравлический Y421000 г/п 10т
1
56605,00
8,333
10.
Домкрат реечный 5 тн
2
1154
0
11.
Дрель ручная
4
666,68
0
12.
Заpядное устpойство 3М 1 - У 350х900
3
5865
7,1
13.
Заpядное устpойство УЗ - 3М
4
7820
7,1
14.
Заpядное устpойство УЗО - 1М 1.5кв 230х320
1
1955,00
7,1
15.
Загрузчик ПАК - 2
1
6640,68
14,286
16.
Измеритель комплекта сцепления ИКСп
1
55084,75
14,286
17.
КДС -5К Стенд - развал компьютерный
1
178700,00
14,286
18.
Комплект для головок блоковГАЗ/ВАЗ
1
29828,73
14,286
19.
Компрессометр К-1(0-15кг/см)
1
1649,75
0
20.
Компрессометр К-74-36
1
10174,83
11,111
21.
Компьютер Pentium 4
1
32685,00
20
22.
Краскораспылитель SB-2000
1
2750,00
0
23.
Маслораздатчик передвижной RAASM-32024 (34k/)
1
24152,54
14,286
24.
Маслосборник отработтаного масла с 508
1
10887,50
5
25.
Моечная установка высого давления
1
52891,30
14,286
26.
Мойка BOSCH AQUATAK 115 (для мойки автомашин)
1
6990,00
20
27.
Мойка высокого давления
1
3660,00
0
28.
Мотор-тестер МТ-4 с осцилографом
1
67488,05
14,286
29.
Нутромер индикаторный 10-18
1
2525,83
10
30.
Пpесс Р - 337 2 квт 400 х 1500
1
5601,00
7,7
31.
ПК Celeron 2000/845 PE/256/40/CD
1
20280,00
20
32.
Пневмогайковерт Airtec AT 37DLL
1
28533,90
40
33.
Пневмогайковерт DINO PAOLI
1
98389,83
40
34.
Пневмомолоток FRH-3-2
1
10364,50
40
35.
Пневмошлифмашинка эксцентр.FOR-150
2
31093,5
40
36.
Пневмошлифмашинка эксцентр.FOR-175
1
16423,74
40
37.
Подъемник типа "Жиpаф"
1
4003,00
18,9
38.
Подъемник электромеханический П-178 Д-04
1
96101,69
10
39.
Подьемник СДО-25 двухстpоечный г/п 2,5тн.
1
10000,00
5,9
40.
Полуавтомат сварочный ПДГ-300
1
39830,51
14,286
41.
Пресс гидравлический настольный Р 338
1
101640,00
6,667
42.
Прибор "Карат-4"
1
20161,02
11,111
43.
Прибор КИ - 582
1
6583,33
0
44.
Прибор сканер - тестер ТСТ - 10
1
23516,95
16,667
45.
Принтер HP LJ 1010
1
6150,00
0
46.
Пускозарядное устройство BLUEWED-MAJOR 1500
1
41237,29
6,667
47.
Пылесос NT 561 (ЕCО)
1
11406,10
10
48.
Пылесос- воздуходувка Viking BE 600 (для сушки машин)
2
6600
14,286
49.
Радиостанция возимая Р 020
3
19658,34
0
50.
Радиотелефон Panasonic KX - TCD 715/KX- TCD 235
1
3630,51
20
51.
Сварочный выпрямитель ВДУ - 506 УЗ
1
61016,95
14,286
52.
Сварочный полуавтомат У-200П
1
33550,00
14,286
53.
Сканер универсальный сист. PDL 2000
1
161000,00
48
54.
Солидолонагнетатель RAASM - 68213
3
62203,39
14,286
55.
Солидолонагнетатель пневматический 14 кг
1
12500,00
14,286
56.
Станок балансиpовочный К-623А
1
9200,00
14,3
57.
Станок веpтикально-свеpлильный унивеpсальный одношпиндельный 2H135
1
6815,00
5
58.
Станок для расточки тормозных барабанов Р- 185
1
144067,80
5
59.
Станок для расточки тормозных барабанов Р- 185
1
199152,54
14,118
60.
Станок настольно-свеpлильный вес 85кг.
1
22896,00
5
61.
Станок свеpлильный /наибольший объем свеpления 6 мм/
1
60491,00
5
62.
Станок свеpлильный HС - 1.5квт
1
23641,00
5
63.
Станок токаpно-винтоpезный 1К62 з.н.68722
1
4170,00
5
64.
Станок токаpный 1К 62 Д 12.22квт
1
6410,00
5
65.
Станок точильно-шлифовальный SE-408
1
7574,15
0
66.
Станок фpезеpный 6Р81
2
32253
5
67.
Стенд 532-2М
1
12501,00
11
68.
Стенд балансиров. Oebuna 480
1
296949,15
9,091
69.
Стенд балансировочный HW - 130
1
102000,00
14,3
70.
Стенд для выпресовки шкворней П-5
1
87152,54
14,286
71.
Стенд для притирки клапанов Р23-74
1
78559,32
14,286
72.
Стенд для срезания тормозн. накладок Р-174
1
157309,32
14,286
73.
Стенд К - 245
1
73229,70
14,286
74.
Стенд КИ - 22210
1
141000,00
14,3
75.
Стенд Р-184М для пpавки колес
1
15750,00
11
76.
Стенд р/с диз. (эл. мех.) Р-660
1
39728,81
14,286
77.
Стенд рихтов. Эксперт-2000-2
1
144427,97
9,091
78.
Стенд шиномонтажный для груз.автомобилей Golden 1557
1
237288,14
16,667
79.
Стенд шиномонтажный НТ-320 универсальный
1
78342,97
16,667
80.
Стробоскоп М-3Д для дизельного двигателя
1
3122,71
0
81.
Съемник гидравлический СГА32-15П
1
39680,00
8,333
82.
Тpактоp МТЗ-82
1
57192,00
11,1
83.
Тележка 536 М
1
2257,00
12,5
84.
Тележка г/п 200 кг
3
35054,01
12,5
85.
Тележка КУ - 200
2
17095,64
0
86.
Телефонный аппарат KX - TCD 205
1
2098,31
20
87.
Тестер ДСЕ - 6С
1
20040,68
14,286
88.
Тиски 125мм
1
1486,23
0
89.
Тиски слесарные 125 (Б-1420 руб.)
2
2840
0
90.
Тиски слесарные стальные 160 мм
2
5360,16
0
91.
Тиски станочные 160 мм с откр винтом
1
17345,21
40
92.
Установка 4Ш-1А шиномонтажная для монтажа и демонтажа колес
1
12600,00
11
93.
Установка для мойки двигателей "Тайфун"
1
14628,00
14,3
94.
Установка моечная Magibol-90
1
138347,46
14,286
95.
Устройство вытяжное с э/п и вент MERF-M-75-5/10/SP
2
61440,1
10
96.
Шлифовальная установка Р- 186
1
76240,00
5
97.
Электродрель БЭС
1
181,70
0
98.
Электродрель ДУ 780 ЭР
1
1384,74
40
99.
Электродрель ДУ 800 ЭР
1
1471,00
40
100.
Электродрель ИЭ - 1519Э
1
1458,00
40
101.
Электродрель МЭС - 600 ЭРУ
1
1490,00
40
102.
Электродрель с уд-м Е 132 АТ - 60
1
1462,03
40
103.
Электроточило ДSC - 175 (Б-2850 руб.)
1
2850,00
0
104.
Электрошлифмашинка BOSCH 230
1
5083,91
0
105.
Электрошлифмашинка угловая AGP 125-10 Protool
2
7447,06
40
106.
Электрошуруповерт DS18DMR HITACHI
1
8650,00
40
Итого
130
4329009,08
Общая стоимость оборудования
3458188,97
Общая стоимость приборов, инструмента
840355,11
Вывод: из таблицы 3 видно, что единиц технологического оборудования насчитывается более 107 наименований. В целом в цехе АТП достаточно оборудования для выполнения необходимых операций, предусмотренных программой То и Р. Следует отметить невысокий процент износа оборудования.
2. Технологическое проектирование цеха автобусного парка в целях повышения производительности труда, охраны окружающей среды и повышения механизации технологических процессов
2.1 Основные показатели работы подвижного состава
В современных условиях к работе АТП предъявляются все более высокие требования. Основное из которых - высокий уровень технологического оборудования и сооружений, достигаемый путем максимального использования современных материалов и техники. Современные АТП должны иметь высокие показатели по производительности, условиям труда и уровню механизации. Кроме того, должна быть обеспечена высокая эффективность капитальных вложений.
Прежде чем приступить к разработке технологического и планировочного решения производственного корпуса, необходимо составить схему расположения помещений с указанием площадей. (схема 1)
Исходными данными для технологического проектирования являются:
списочное количество подвижного состава Аи;
среднесуточный пробег единицы подвижного состава lсс, км;
число дней работы подвижного состава в году Драб. г;
категория условий эксплуатации Ку.э.;
климатический район Кл.р.;
количество подвижного состава, фактический пробег которого не превысил нормативного до списания (ресурсного) Аи'; то же после достижения ресурса Аи'';
пробег подвижного состава с начала эксплуатации в долях х от ресурсного пробега Lр; для подвижного состава, пробег которого не превысил нормативного до списания xLi' и для подвижного состава, пробег которого превысил нормативный до списания xLi''
Таблица 4
Исходные данные
Подвижной состав (марка, модель)
Аи, шт.
lcc, км
Тн, ч
Драб.г
Ку.э
Кл.р
Аи, шт.
xLi
Аи'
Аи''
xLi'
XLi''
ГАЗ 2217
4
80
8
254
III
Умеренн.
4
-
ГАЗ 322100
2
80
8
254
III
Умеренн.
2
-
УАЗ 22069
1
80
8
254
III
Умеренн.
1
-
ГАЗ 22177
1
80
8
254
III
Умеренн.
1
-
Икарус 280
6
200
8
254
III
Умеренн.
-
6
Волжанин
2
200
8
254
III
Умеренн.
2
-
Волж. 527004
6
200
8
254
III
Умеренн.
6
-
Икарус 260
15
200
8
254
III
Умеренн.
-
15
МаРЗ 52661
1
200
8
254
III
Умеренн.
-
1
ЛАЗ-695
3
200
8
254
III
Умеренн.
-
3
Икарус 256
3
200
8
254
III
Умеренн.
-
3
ПАЗ 32051
5
150
8
254
III
Умеренн.
-
5
Вывод: Из таблицы 4 видно, что на АТП достаточно высокая разномарочность ТС. Большая часть парка выработала свой ресурс и требует замены. Количество рабочих дней в году (2009) принимаем равным 254 дням. Время пребывания ТС в наряде принимаем равным восьми часам.
2.2 Корректировка нормативов ресурсного пробега и периодичности ТО
Корректировка пробега Lp подвижного состава осуществляется по формуле:
Lp = Lp(н) К1К2К3
где Lp(н) – соответственно нормативный пробег до списания, км;
K1, K2, K3 - коэффициенты, соответственно учитывающие категорию условий эксплуатации, модификацию подвижного состава и организацию его работы, климатические условия. Подставляем данные в формулу и получаем:
Для ГАЗ 2217 Lp = 150*0,8*1,0*1,0 = 120 тыс.км
Для ГАЗ 322100 Lp = 150*0,8*1,0*1,0 = 120 тыс.км
Для УАЗ 22069 Lp = 150*0,8*1,0*1,0 = 120 тыс.км
Для ГАЗ 22177 Lp = 150*0,8*1,0*1,0 = 120 тыс.км
Для Икарус 280 Lp = 250*0,8*1,0*1,0 = 200 тыс.км
Для Волжанин Lp = 250*0,8*1,0*1,0 = 200 тыс.км
Для Волж. 527004 Lp = 250*0,8*1,0*1,0 = 200 тыс.км
Для Икарус 260 Lp = 250*0,8*1,0*1,0 = 200 тыс.км
Для МаРЗ 52661 Lp = 250*0,8*1,0*1,0 = 200 тыс.км
Для ЛАЗ-695 Lp = 250*0,8*1,0*1,0 = 200 тыс.км
Для Икарус 256 Lp = 250*0,8*1,0*1,0 = 200 тыс.км
Для ПАЗ 32051 Lp = 250*0,8*1,0*1,0 = 200 тыс.км
Корректировка периодичности ТО–1 и ТО–2 осуществляется по формуле
Li = Li(н)К1К3,
где Li – скорректированная периодичность i-го вида обслуживания, км;
Li(н) – нормативная периодичность i-го вида обслуживания, км.
Подставляем данные в формулу и получаем:
Для ГАЗ 2217 LТО-1=2600*0,8*1,0 = 2080км
LТО-2=13000*0,8*1,0 =10400 км
Для ГАЗ 322100 LТО-1=2600*0,8*1,0 = 2080 км
LТО-2=13000*0,8*1,0 = 10400 км
Для УАЗ 22069 LТО-1=2600*0,8*1,0 = 2080 км
LТО-2=13000*0,8*1,0 = 10400 км
Для ГАЗ 22177 LТО-1=2600*0,8*1,0 = 2080 км
LТО-2=13000*0,8*1,0 = 10400 км
Для Икарус 280 LТО-1=2600*0,8*1,0 = 2080 км
LТО-2=13000*0,8*1,0 = 10400 км
Для Волжанин LТО-1=2600*0,8*1,0 = 2080 км
LТО-2=13000*0,8*1,0 = 10400 км
Для Волж. 527004 LТО-1=2600*0,8*1,0 = 2080 км
LТО-2=13000*0,8*1,0 = 10400 км
Для Икарус 260 LТО-1=2600*0,8*1,0 = 2080 км
LТО-2=13000*0,8*1,0 = 10400 км
Для МаРЗ 52661 LТО-1=2600*0,8*1,0 = 2080 км
LТО-2=13000*0,8*1,0 = 10400 км
Для ЛАЗ-695 LТО-1=2600*0,8*1,0 = 2080 км
LТО-2=13000*0,8*1,0 = 10400 км
Для Икарус 256 LТО-1=2600*0,8*1,0 = 2080 км
LТО-2=13000*0,8*1,0 = 10400 км
Для ПАЗ 32051 LТО-1=2600*0,8*1,0 = 2080 км
LТО-2=13000*0,8*1,0 = 10400 км
Таблица 5
Нормативы ресурсного пробега и периодичности ТО
Подвижной состав
Lp(н), тыс км
LТО–1(н), км
LТО–2(н), км
К1
К2
К3
Lp,тыскм
LТО–1, км
LТО–2, км
ГАЗ 2217
150
2600
13000
0,8
1,0
1,0
120
2080
10400
ГАЗ 322100
150
2600
13000
0,8
1,0
1,0
120
2080
10400
УАЗ 22069
150
2600
13000
0,8
1,0
1,0
120
2080
10400
ГАЗ 22177
150
2600
13000
0,8
1,0
1,0
120
2080
10400
Икарус 280
250
2600
13000
0,8
1,0
1,0
200
2080
10400
Волжанин
250
2600
13000
0,8
1,0
1,0
200
2080
10400
Волж. 527004
250
2600
13000
0,8
1,0
1,0
200
2080
10400
Икарус 260
250
2600
13000
0,8
1,0
1,0
200
2080
10400
МаРЗ 52661
250
2600
13000
0,8
1,0
1,0
200
2080
10400
ЛАЗ-695
250
2600
13000
0,8
1,0
1,0
200
2080
10400
Икарус 256
250
2600
13000
0,8
1,0
1,0
200
2080
10400
ПАЗ 32051
250
2600
13000
0,8
1,0
1,0
200
2080
10400
2.3 Расчет коэффициента технической готовности
Если для подвижного состава не предусматривается выполнение КР, то коэффициент технической готовности определяется по формул
αт = 1 / (1 + lcc * ДТО–ТР * К4/1000),
где αт – коэффициент технической готовности;
ДТО–ТР – удельная норма простоя подвижного состава в днях на 1000 км;
К4 – коэффициент, учитывающий пробег автомобиля с начала эксплуатации.
Подставляем данные в формулу и получаем
Для ГАЗ 2217 αт = 1/ (1+80*0,18 *1,0/1000)=0,98
Для ГАЗ 322100 αт = 1/ (1+80* 0,18 *1,0/1000) =0,98
Для УАЗ 22069 αт = 1/ (1+80* 0,18 *1,0/1000) =0,98
Для ГАЗ 22177 αт = 1/ (1+80* 0,18 *1,0/1000) =0,98
Для Икарус 280 αт = 1/ (1+200* 0,18 *1,0/1000)=0,97
Для Волжанин αт = 1/ (1+200* 0,18 *1,0/1000) =0,97
Для Волж. 527004 αт = 1/ (1+200* 0,18 *1,0/1000) =0,97
Для Икарус 260 αт = 1/ (1+200* 0,18 *1,0/1000) =0,97
Для МаРЗ 52661 αт = 1/ (1+200* 0,18 *1,0/1000) =0,97
Для ЛАЗ-695 αт = 1/ (1+200* 0,18 *1,0/1000) =0,97
Для Икарус 256 αт = 1/ (1+200* 0,18 *1,0/1000) =0,97
Для ПАЗ 32051 αт = 1/ (1+150* 0,18*1,0/1000) =0,97
Таблица 6
Коэффициент технической готовности
Подвижной состав
lcc, км
ДТО–ТР, дни/1000км
Αт
ГАЗ 2217
80
0,18
0,98
ГАЗ 322100
80
0,18
0,98
УАЗ 22069
80
0,18
0.98
ГАЗ 22177
80
0,18
0.98
Икарус 280
200
0,18
0.97
Волжанин
200
0,18
0.97
Волж. 527004
200
0,18
0.97
Икарус 260
200
0,18
0.97
МаРЗ 52661
200
0,18
0.97
ЛАЗ-695
200
0,18
0.97
Икарус 256
200
0,18
0.97
ПАЗ 32051
150
0,18
0.97
2.4 Расчет годовых пробегов подвижного состава и производственной программы ТО
Годовой пробег единицы подвижного состава определяется
Lг = Драб.г* lcc*αт,
где Lг – годовой пробег единицы подвижного состава, км,
а годовой пробег группы подвижного состава –
Lгп = Аи *Lг,
где Lгп – годовой пробег группы подвижного состава, км
В данном методе расчета простой подвижного состава по организационным причинам не учитывается. Поэтому при расчете годового пробега используется не коэффициент выпуска автомобилей, а коэффициент технической готовности.
Подставляем данные в формулы:
Для ГАЗ 2217 Lг =254*80*0,98 = 19913,6км
Lгп =4*19913,6=79654,4км
Для ГАЗ 322100 Lг =254*80*0,98= 19913,6км
Lгп =2*19913,6= 39827,2км
Для УАЗ 22069 Lг =254*80*0,98 = 19913,6км
Lгп =1*19913,6 = 19913,6км
Для ГАЗ 22177 Lг =254*80*0,98= 19913,6км
Lгп =1*19913,6 = 19913,6км
Для Икарус 280 Lг =254*200*0,97= 49276км
Lгп =6*49276= 295656км
Для Волжанин Lг =254*200*0,97= 49276км
Lгп =2*49276= 98552км
Для Волж. 527004 Lг =254*200*0,97= 49276 км
Lгп =6*49276= 295656км
Для Икарус 260 Lг =254*200*0,97=49276км
Lгп =15*49276 = 739140км
Для МаРЗ 52661 Lг =254*200*0,97=49276км
Lгп =1*49276= 49276км
Для ЛАЗ-695 Lг =254*200*0,97=49276км
Lгп =3* 49276= 147828км
Для Икарус 256 Lг =254*200*0,97=49276км
Lгп =3* 49276= 147828 км
Для ПАЗ 32051 Lг =254*150*0,97 =36957км
Lгп =5*36957= 184785км
Годовое число обслуживаний ΣNEO.сг, выполняемых ежедневно при возврате подвижного состава с линии и выпуске на линию, определяется из выражения
Для ГАЗ 2217 ΣNЕОсг = 4*254*0,98= 995,68
Для ГАЗ 322100 ΣNЕОсг = 2*254*0,98= 497,84
Для УАЗ 22069 ΣNЕОсг = 1*254*0,98= 248,92
Для ГАЗ 22177 ΣNЕОсг = 1*254*0,98= 248,92
Для Икарус 280 ΣNЕОсг = 6*254*0,97= 1478,28
Для Волжанин ΣNЕОсг = 2*254*0,97= 492,76
Для Волж527004 ΣNЕОсг = 527004 6*254*0,97= 1478,28
Для Икарус 260 ΣNЕОсг = 15*254*0,97= 3695,7
Для МаРЗ 52661 ΣNЕОсг = 1*254*0,97= 246,38
Для ЛАЗ-695 ΣNЕОсг = 3*254*0,97= 739,14
Для Икарус 256 ΣNЕОсг = 3*254*0,97= 739,14
Для ПАЗ 32051 ΣNЕОсг = 5*254*0,97= 1231,9
Годовое число обслуживаний ΣNЕОтг, выполняемых перед ТО и ТР,
где NТО-1.Г, NТО-2.Г – соответственно годовое количество ТО–1 и ТО–2; 1,6–коэффициент, учитывающий проведение ЕО при ТР.
Суммарное годовое количество технических обслуживаний можно определить по выражениям
Подставляем данные в формулу и получаем
для ГАЗ 2217:
для ГАЗ 322100:
для УАЗ 22069:
для ГАЗ 22177:
для Икарус 280:
для Волжанин:
для Волжанин527004:
для Икарус 260:
для МаРЗ 52661:
для ЛАЗ-695:
для Икарус 256:
для ПАЗ 32051:
Суточная производственная программа по видам обслуживаний
где ∑NiГ – суммарное годовое количество обслуживаний i-го вида;
ДРАБ.Гi – годовое число рабочих дней рассматриваемой зоны обслуживания.
Подставляем данные в формулу и получаем
Для ГАЗ 2217 NEOc.c=3.92
NEOт.c=0.281
NEOTO–1.c=0.148
NTO–2.c=0.0275
Для ГАЗ 322100 NEOc.c=1.96
NEOт.c=0.281
NEOTO–1.c=0,007
NTO–2.c=0.138
Для УАЗ 22069 NEOc.c=0.98
NEOт.c=0.281
NEOTO–1.c=0.037
NTO–2.c=0.007
Для ГАЗ 22177 NEOc.c=0.98
NEOт.c=0.281
NEOTO–1.c=0.037
NTO–2.c=0.007
Для Икарус 280 NEOc.c=5,82
NEOт.c=0.283
NEOTO–1.c=0.06
NTO–2.c=0.03
Для Волжанин NEOc.c=1,92
NEOт.c=0.283
NEOTO–1.c=0.184
NTO–2.c=0.04
Для Волж. 527004 NEOc.c=5,82
NEOт.c=0.283
NEOTO–1.c=0.06
NTO–2.c=0.03
Для Икарус 260 NEOc.c=14.55
NEOт.c=0.283
NEOTO–1.c=1,37
NTO–2.c=0.27
Для МаРЗ 52661 NEOc.c=0.97
NEOт.c=0.283
NEOTO–1.c=0.09
NTO–2.c=0.02
Для ЛАЗ-695 NEOc.c=2.91
NEOт.c=0.283
NEOTO–1.c=0.27
NTO–2.c=0.05
Для Икарус 256 NEOc.c=2.91
NEOт.c=0.283
NEOTO–1.c=0.27
NTO–2.c=0.05
Для ПАЗ 32051 NEOc.c=4.85
NEOт.c=0.283
NEOTO–1.c=0.34
NTO–2.c=0.07
Суточная производственная программа является критерием выбора метода организации ТО.
Исходные данные и результаты расчета годовой производственной программы ТО можно оформить в форме таблицы.
Таблица 7
Годовые пробеги подвижного состава и годовая производственная программа ТО
Подвижной состав
LГ,км
LГП,км
∑NЕОс.г
∑NЕОт.г.
∑NТО-1.Г
∑NТО-2.Г
ГАЗ 2217
19913,6
79654,4
995,68
71.4
37.63
6.995
ГАЗ 322100
19913,6
39827,2
497.84
71.4
1,8
3,5
УАЗ 22069
19913,6
19913,6
248.92
71.4
9,4
1,7
ГАЗ 22177
19913,6
19913,6
248.92
71.4
9,4
1,7
Икарус 280
49276
295656
1478.28
71.824
14,01
7,3
Волжанин
49276
98552
492.76
71.824
46,6
9
Волж. 527004
49276
295656
1478.28
71.824
14,01
7,3
Икарус 260
49276
739140
3695.7
71.824
349,2
67,4
МаРЗ 52661
49276
49276
246.38
71.824
23,3
4,5
ЛАЗ-695
49276
147828
739.14
71.824
69,8
13,5
Икарус 256
49276
147828
739.14
71.824
69,8
13,5
ПАЗ 32051
36957
184785
1231.9
71.824
87,3
16,8
Таблица 8
Суточная производственная программа
Подвижной состав
ДРАБ.Г
NЕОс.с
ДРАБ.Г
NЕОт.с
ДРАБ.Г(ТО-1)
NТО-1.С
ДРАБ.Г(ТО-2)
NТО-2.С
ГАЗ 2217
254
3.92
254
0.281
254
0.148
254
0.0275
ГАЗ 322100
254
1.96
254
0.281
254
0.007
254
0.138
УАЗ 22069
254
0.98
254
0.281
254
0.037
254
0.007
ГАЗ 22177
254
0.98
254
0.281
254
0.037
254
0.007
Икарус 280
254
5,82
254
0.283
254
0.06
254
0.03
Волжанин
254
1,92
254
0.283
254
0.184
254
0.04
Волж. 527004
254
5,82
254
0.283
254
0.06
254
0.03
Икарус 260
254
14.55
254
0.283
254
1,37
254
0.027
МаРЗ 52661
254
0.97
254
0.283
254
0.09
254
0.02
ЛАЗ-695
254
2.91
254
0.283
254
0.27
254
0.05
Икарус 256
254
2.91
254
0.283
254
0.27
254
0.05
ПАЗ 32051
254
4.85
254
0.283
254
0.34
254
0.07
2.5 Корректирование нормативных трудоемкостей ТО и ТР
Корректирование нормативных трудоемкостей ежедневных и плановых технических обслуживаний производится по выражению
,
где ti, - скорректированная трудоемкость i-го вида обслуживания, чел-ч, ti(H) -нормативная трудоемкость i-го вида обслуживания, чел-ч (приложение В), К2, К5 - коэффициенты, учитывающие соответственно модификацию подвижного состава и число автомобилей в АТП.
Корректирование удельной трудоемкости текущего ремонта производится так
,
где tТР - скорректированная удельная трудоемкость текущего ремонта, чел-ч/1000 км, tТР(Н) - нормативная удельная трудоемкость ТР, чел-ч/1000 км, K1, К3, К4 - коэффициенты, учитывающие соответственно категорию условий эксплуатации, климатический район и пробег подвижного состава с начала эксплуатации.
Нормативные трудоемкости ЕО, ТО и ТР, коэффициенты корректирования и скорректированные нормативные трудоемкости ЕО, ТО и ТР необходимо оформить в виде таблицы
Таблица 9
Трудоемкости ЕО, ТО и ТР
Подвижной состав
Вид техни
ческо
го воздействия
Нормативные трудоемкос
ти ЕО, ТО (чел-ч) и ТР (чел-ч.1000 км)
Коэффициенты корректирования
Скорректи рованные значения трудоемкости ЕО, ТО (чел-ч) и ТР (чел-ч.1000 км)
К1
К2
К3
К4
К5
1
2
3
4
5
6
7
8
9
ГАЗ 2217
ГАЗ 322100
УАЗ 22069
ГАЗ 22177
Икарус 280
Волжанин
Волж. 527004
Икарус 260
МаРЗ 52661
ЛАЗ-695
Икарус 256
ПАЗ 320
ЕО
0,2
1,2
1,2
1,2
1,2
1,2
1,2
1,2
1,2
1,2
1,2
1,2
1,2
1,0
1,0
1,0
1,0
1,0
1,0
1,0
1,0
1,0
1,0
1,0
1,0
1,0
1,0
1.0
1.0
1.0
1.0
1.0
1.0
1.0
1.0
1.0
1,0
1,0
1,0
1.0
1.0
1.0
1.0
1.0
1.0
1.0
1.0
1.0
1,0
4
2
1
1
6
2
6
15
1
3
3
5
0.8
0.4
0.3
0.3
10.8
1.4
1.4
18
1.4
2.4
4.2
3.5
0,2
0.3
0.2
1.8
0.7
0.7
1.2
1.4
0.8
1.4
0.7
ГАЗ 2217
ГАЗ 322100
УАЗ 22069
ГАЗ 22177
Икарус 280
Волжанин
Волж. 527004
Икарус 260
МаРЗ 52661
ЛАЗ-695
Икарус 256
ПАЗ 32051
ТО–1
1,8
1,8
1.5
1,8
13.5
5.5
5.5
9.5
10.0
5.8
10.0
5.5
1,2
1,2
1,2
1,2
1,2
1,2
1,2
1,2
1,2
1,2
1,2
1,2
1,0
1,0
1,0
1,0
1,0
1,0
1,0
1,0
1,0
1,0
1,0
1,0
1,0
1,0
1,0
1,0
1,0
1,0
1,0
1,0
1,0
1,0
1,0
1,0
1,0
1,0
1.0
1.0
1.0
1.0
1.0
1.0
1.0
1.0
1.0
1,0
4
2
1
1
6
2
6
15
1
3
3
5
7.2
3.6
1.5
1,8
81
11
33
142.5
10.0
17.4
30
27.5
ГАЗ 2217
ГАЗ 322100
УАЗ 22069
ГАЗ 22177
Икарус 280
Волжанин
Волж. 527004
Икарус 260
МаРЗ 52661
ЛАЗ-695
Икарус 256
ПАЗ 32051
ТО–2
7,2
7,2
7.7
7,2
47.0
18.0
18.0
35.0
40.0
24.0
40.0
18.0
1,2
1,2
1,2
1,2
1,2
1,2
1,2
1,2
1,2
1,2
1,2
1,2
1,0
1,0
1,0
1,0
1,0
1,0
1,0
1,0
1,0
1,0
1,0
1,0
1,0
1,0
1,0
1,0
1,0
1,0
1,01,0
1,01,0
1,0
1,0
1,0
1,0
1.0
1.0
1.0
1.0
1.0
1.0
1.0
1.0
1.0
1,0
4
2
1
1
6
2
6
15
1
3
3
5
28.8
14.4
7.7
7.2
282
36
108
525
40
72
120
90
ГАЗ 2217
ГАЗ 322100
УАЗ 22069
ГАЗ 22177
Икарус 280
Волжанин
Волж. 527004
Икарус 260
МаРЗ 52661
ЛАЗ-695
Икарус 256
ПАЗ 32051
ТР
1,8
1,8
3.7
1.8
11.0
5.3
5.3
8.5
9.0
6.5
9.0
5.3
1,2
1,2
1,2
1,2
1,2
1,2
1,2
1,2
1,2
1,2
1,2
1,2
1,0
1,0
1,0
1,0
1,0
1,0
1,0
1,0
1,0
1,0
1,0
1,0
1,0
1,0
1,0
1,0
1,0
1,0
1,01,0
1,01,0
1,0
1,0
1,0
1,0
1.0
1.0
1.0
1.0
1.0
1.0
1.0
1.0
1.0
1,0
4
2
1
1
6
2
6
15
1
3
3
5
8.64
4.32
4.44
2.16
79.2
12.72
38.16
153
10.8
23.4
32.4
31.8
2.6 Расчет годовых объемов работ ЕО, ТО и ТР
Годовой объем работ ЕО и ТО можно определить по выражению
,
где ТiС.Г – годовой объем работ i-го вида обслуживания, чел-ч; NiГ - суммарное годовое количество обслуживании i-го вида, t, - трудоемкость i-го вида обслуживания, чел–ч.
Годовой объем работ по ТР определяется по выражению
.
Результаты расчета в таблице:
Таблица 10
Подвижной состав
ТЕОс.г
ТЕОт.г
ТТО-1.Г
ТТО-2.Г
ТТР.Г
ГАЗ 2217
796.544
57.12
271
201.456
688.21
ГАЗ 322100
199.136
28.56
6,48
50,4
172.05
УАЗ 22069
74.676
21.42
14,1
13,09
88.4
ГАЗ 22177
74.676
21.42
16,92
12,24
43.01
Икарус 280
15965.424
775.7
1134,81
2058,6
23416
Волжанин
689.864
100.6
512,6
324
1253.6
Волж. 527004
2069.592
100.6
462,33
788,4
11282.2
Икарус 260
66522.6
1292.832
49761
35385
113088,42
МаРЗ 52661
344.932
100.6
233
180
532,18
ЛАЗ-695
1773.936
172.38
1214,52
972
3459,18
Икарус 256
3104.388
301.7
2094
1620
4789,63
ПАЗ 32051
4311.65
251.384
2400,75
1512
5876,163
Итого
95927,418
3224,316
58121,51
43072,186
164689,043
2.7 Расчет объема вспомогательных работ и численности основных и вспомогательных рабочих
К производственным рабочим относятся рабочие зон и участков, непосредственно выполняющие работы по ТО и ТР подвижного состава. Различают технологически необходимое (явочное) и штатное (списочное) число рабочих. Технологически необходимое число рабочих обеспечивает выполнение суточной, а штатное- годовой производственных программ по ТО и ТР
Технологически необходимое (явочное) число рабочих Рт и штатное Рш определяются по выражениям
;
,
где ТiГ - годовой объем работ по зоне ТО, ТР или участку, чел -ч,
Фт -годовой фонд времени технологически необходимого рабочего при односменной работе, ч,
Фш - годовой фонд времени штатного рабочего, ч
В практике проектирования для расчёта технологически необходимого числа рабочих годовой фонд времени Фт принимают 2070 ч. -для производств с нормальными условиями труда, 1830 ч. –для производств с вредными условиями труда Годовой фонд времени штатного рабочего определяет фактическое время отработанное исполнителем непосредственно на рабочем месте. Фонд времени штатного рабочего Фш меньше фонда технологического рабочего Фт за счёт выходных, праздничных дней, отпусков и невыходов рабочих по уважительным причинам (выполнение государственных обязанностей, по болезням и др.), принимаем: Фшм=1610 ч. –для маляров; Фшост=1820 ч. –для всех остальных рабочих
Для зоны ТО-1 количество рабочих равно:
Рт= 58121.51/2070=28 чел;
Рш= 58121.51/1820=32 чел.
Для зоны ТО-2 количество рабочих равно:
Рт= 43072.186/2070=21 чел;
Рш=43072.186/1820=24 чел.
Таким образом, общее количество рабочих на ТО1 и ТО2 составит:
-технически необходимое 49 чел;
-штатное 56 чел.
Численность вспомогательных рабочих определяется аналогично числу штатных или технологически необходимых. Число вспомогательных рабочих принимаем равным 20% от общего числа рабочих
Вид работ
%
Число рабочих
расчетное
принятое
Ремонт и обслуживание технологического оборудования, оснастки и инструмента
Ремонт и обслуживание инженерного оборудования, сетей и коммуникаций
Транспортные
Перегон автомобилей
Приёмка, хранение и выдача материальных ценностей
Уборка производственных помещений и территории
Обслуживание компрессорного оборудования
20
15
10
15
15
20
5
2,2
1,7
1,1
1,7
1,7
2,2
0,6
2
2
1
2
2
2
1
ИТОГО
100
11,2
12
К вспомогательным работам относятся работы по ремонту и обслуживанию технологического оборудования, оснастки и инструмента различных зон и участков, содержание инженерного оборудования, сетей и коммуникаций, обслуживание компрессорного оборудования. Объем вспомогательных работ обычно составляет 20-30 % от общего объема работ по ТО и ТР подвижного состава (при числе штатных производственных рабочих до 50 -30 %, от 100 до 125 - 25 % и свыше 260 - 20 %).
При небольшом объеме работ (до 10000 чел.-ч в год) часть вспомогательных работ может выполняться на соответствующих производственных участках. В этом случае годовой объем работ участка следует увеличить на величину выполняемых на нем вспомогательных работ. Примерное распределение вспомогательных работ, связанных с ремонтом и обслуживанием оборудования и выполняемых на участках следующее: электротехнические – 25 %, механические –10%, слесарные -16%, кузнечные - 2 %, сварочные - 4 %, жестяницкие- 4 %, медницкие - 1 %, трубопроводные (слесарные) - 22 %, ремонтно-строительные и деревообрабатывающие - 16 %.
3. Проектирование нестандартного технологического оборудования, в целях совершенствования ТО и Р
3.1 Назначение, устройство и принцип действия оборудования (приспособления)
Предприятие ОАО «Карельский окатыш» специализируется на производстве железорудного сырья. В структуре данной организации предусмотрен автотранспортный отдел УАТ (управление автотранспортом).
В ведомстве данного подразделения находится два подотдела: ЦПА и ЦТА. Цех пассажирского транспорта имеет собственные производственные мощности, ремонтную базу и обслуживающий персонал.
К основным функциям ЦПА относится пассажирские перевозки посредством автобусов, но кроме того так же в парке предусмотрены единицы легкового транспорта для решения прочих производственных задач. Заметим, что легковых автомобилей в парке ЦПА более пятидесяти единиц. (приложение 2)
Для поддержания подвижного состава в рабочем состоянии на предприятии предусмотрено достаточное число технологического оборудования. (приложение 3).
В числе прочих автомобилей в состав автопарка входят несколько автомобилей ГАЗ 2217(Соболь) и ГАЗ 3221 (ГАЗель), а так же УАЗ 22069, следовательно проще было бы проводить обслуживание данного вида транспорта совместно с обслуживанием легковой части автопарка.
Таким образом, для расширения производственных возможностей АТП и в целях экономии времени на техническое обслуживание и текущий ремонт, в конструкторской части мы предлагаем приспособление, которое позволит обслуживать автомобили ГАЗель на подъемнике П-97М, предназначенном для обслуживания легковых отечественных автомобилей.
В целях экономии времени на техническое обслуживание и текущий ремонт автомобилей ГАЗель, целесообразно использовать подъемник. Автомобиль ГАЗель невозможно поднимать для обслуживания под пороги как легковые автомобили, поэтому предлагаем поднимать автомобили такого типа за раму, для чего представляем следующее приспособление.
Приспособление для поднятия автомобиля ГАЗель за раму представляет собой составной металлический цилиндр переменного сечения с фрезерованным пазом с одного торца и резьбой с другого, и представлено на рисунке (2). Приспособление выполнено из Ст. 3 σт = 200 Н/мм2; [σсж] = 157Н/мм2; ГОСТ 380–60.
Рисунок 2
Приспособление ввинчивается в подъемный рычаг подъемника.
3.2 Расчет детали на прочность
Нагрузка распределяется по оси цилиндра, поэтому поверять надежность приспособления будем следующими методами:
Проверка цилиндра приспособления на сжатие;
Проверка резьбы приспособления на смятие.
Проверка цилиндра приспособления на сжатие
Определим наибольшую величину груза Q, который может быть поднят подъемником при помощи предложенного приспособления, не учитывая прочности самого подъемника.
Определим значение допустимых усилий в цилиндре приспособления:
N = S*[σсж],
где S – площадь поперечного сечения цилиндра приспособления, S = 7088,2мм2;
[σсж] – допустимое напряжение при сжатии, для Ст 3 [σсж] = 157 Н/мм2;
N = 7088,2*157 = 1,1 МН = 110 т.
Из результата видно, что приспособление не только выдержит массу автомобиля ГАЗель (2,6 т.), но и имеет огромный ресурс работы.
Проверку резьбы приспособления на смятие
Характеристика резьбы:
Резьба общего назначения, треугольная, однозаходная ГОСТ 9150–59
шаг резьбы Р = 3,5 мм
наружный диаметр резьбы винта d = 30 мм;
внутренний диаметр резьбы винта d1 = 26,211 мм;
средний диаметр резьбы винта и гайки d2 = 27,73 мм;
высота гайки Н = 100 мм;
высота резьбы h = 1,89 мм;
материал – Ст 3
Из условия износостойкости резьбы по напряжениям смятия:
где F – сила, действующая на резьбу винта и гайки.
Так как используем четыре приспособления к подъемнику П-97М то силу, действующую на резьбу винта и гайки, найдем следующим образом:
где G – нагрузка, действующая на подъемник, G = m*g =2600*9.8= 25480 Н.
d2 – средний диаметр резьбы винта и гайки d2 = 27,73 мм;
h – высота резьбы, h = 1,89 мм;
z – число рабочих витков.
Число рабочих витков находится следующим образом:
где Н – высота гайки, или глубина ввинчивания винта в деталь, Н = 100 мм;
P – шаг резьбы, для резьбы М30х3,5 р = 3,5 мм.
[σсм] – допускаемое напряжение при смятии, допускаемое напряжение при смятии находится по формуле:
где [σт] – предел прочности материала, для Ст 3 [σт] = 200 Н/мм2;
n – коэффициент запаса, n = 1,5
Подставив данные в формулу получим напряжениям смятия:
1,41 ≤ [σсм] = 133
Напряжение смятия полностью удовлетворяет условию износостойкости резьбы по напряжениям смятия и имеет достаточный ресурс работы.
Проверочный расчет подъемника
Так как масса автомобиля ГАЗель примерно в полтора раза больше массы среднестатистического легкового отечественного автомобиля, необходимо произвести проверочный расчет подъемного рычага и винта подъемного механизма подъемника П-97М, а так же анкерных болтов.
Так же планируется использование подъемника для снятия двигателей с автомобилей. Использование подъемника для снятия двигателей в нашем случае весьма целесообразно, так как в данном помещении это ускорит процесс обслуживания ТС. Но так как вес самого тяжелого силового агрегата автомобиля, планируемого для обслуживания и ремонта данным подъемником (а/м ГАЗель GДВ = 4700 H) меньше максимальной нагрузки на один подъемный рычаг подъемника, то дополнительный проверочный расчет проводить не будем.
Проверочный расчет подъемного рычага подъемника на изгиб
Проверочный расчет подъемного рычага подъемника на изгиб ведем по расчету балки.
Ми.мах = Ми*n,
где Ми – изгибающий момент;
n – коэффициент запаса, n = 1,5;
Из определения изгибающий момент находим по формуле:
где G – сила, прикладываемая к балке;
G =m*g,
m = 2600 кг
g = 9.8 м/с2
G = 2600*9,8 = 25400 Н
Так как у подъемника 4 подъемных рычага то сила действующая на 1 подъемный рычаг будет равна:
G1 =G/4 = 25400/4 = 6370 Н;
l – плечо, равное длине подъемного рычага подъемника, l = 1,5 м.
Подставив данные в формулу получим:
Ми = 6370*1,5 = 9555 Н*м = 9555000 Н*мм
Подставив данные в формулу получим наибольший изгибающий момент:
Ми.мах = 9555000*1,5 = 143322500 Н*мм
Wx – момент сопротивления; так как сечение балки – полый прямоугольный брус, то расчет момента сопротивления ведем по формуле:
где b – ширина наружной стенки бруса, = 150 м;
h – высота наружной стенки бруса, = 100 м;
b0 – ширина внутренней стенки бруса, b0 = 140 м;
h0 – высота внутренней стенки бруса, h0 = 90 м.
Подставив данные в формулу получим момент сопротивления:
Подставив данные в формулу получим напряжение при изгибе:
[σu] – допускаемое напряжение при изгибе;
где σол – предельное (опасное) напряжение, т.к. балка выполнена из металла Сталь 45 (σт = 360 Н/мм2, σв = 610 Н/мм2) и испытывает деформацию – изгиб то предельное напряжение будет равно:
[σ] = 1,2 σт,
де σт – предел текучести материала из которого выполнена балка, σт = 360 Н/мм2;
[σ] = 1,2*360 = 432 Н/мм2;
n – коэффициент запаса, n = 1,5;
Подставив данные в формулу получим допускаемое напряжение при изгибе:
Допускаемое напряжение удовлетворяет условию и даже имеет небольшой запас:
234,96 Н/мм2 ≤ 288
Следовательно, подъемник выдержит массу автомобиля ГАЗель, и будет обладать достаточным ресурсом работы.
Проверочный расчет резьбового соединения подъемного механизма на смятие.
Характеристика резьбового соединения подъемного механизма подъемника П-97М:
Резьба винта прямоугольная, однозаходная
шаг резьбы Р = 8 мм
наружный диаметр резьбы винта d = 52 мм;
внутренний диаметр резьбы винта d1 = 43 мм;
средний диаметр резьбы винта и гайки d2 = 48 мм;
наружный диаметр резьбы гайки d’= 53 мм;
внутренний диаметр резьбы гайки d’1 = 44 мм;
высота гайки Н = 64 мм;
высота резьбы h = 4 мм;
площадь сечения стержня винта S = 14,52 см2;
материал – Сталь 40Х
Гайка изготовлена из литейной латуни марки ЛАЖМц66-6-3-2, σв = 700 Н/мм2; δ = 7 %; НВ = 160 кг/мм2. Прямоугольная резьба не стандартизирована. Так же как и трапецеидальная, она предназначена для передачи движения. Диаметры и шаг прямоугольной резьбы рекомендуется принимать по ряду диаметров и шагов трапецеидальных резьб.
Проведем проверочный расчет резьбы на смятие.
Из условия износостойкости ходовой резьбы по напряжениям смятия:
где F – сила, действующая на резьбу винта и гайки.
Так как подъемник П-97М имеет два винта то силу, действующую на резьбу винта и гайки, найдем следующим образом:
где G – нагрузка, действующая на подъемник, G = 25480 Н.
d2 – средний диаметр резьбы винта и гайки d2 = 48 мм;
h – высота резьбы, h = 4 мм;
z – число рабочих витков.
Число рабочих витков находится следующим образом:
(15)
P – шаг резьбы, P = 8 мм.
[σсм] – допускаемое напряжение при смятии, в сопряжении сталь–латунь допускаемое напряжение при смятии принимается равным допускаемому напряжению латуни [σсм] = σв /n =700/3.5=200 Н/мм2.
Подставив данные в формулу получим
Напряжение смятия полностью удовлетворяет условию износостойкости ходовой резьбы по напряжениям смятия, более того имеет запас более 100%.
Проверочный расчет резьбового соединения подъемного механизма на растяжение.
Расчет на прочность резьбовых соединений выполняют следующим образом. Площадь поперечного сечения стержня болта по заданному внешнему усилию определяют по формуле:
где d1 – внутренний диаметр резьбы винта, d1 = 43 мм;
Р – растягивающее усилие, действующее на винт подъемного механизма;
где G – нагрузка, действующая на подъемник, G = 25480 Н.
Подставив данные в формулу, получим:
[σв]р= σв/n,
где σв – предел прочности материала винта, σв = 980 Н/мм2;
n – коэффициент запаса, для статически нагруженного хрупкого материала n = 3,2.
[σв]р= 980/3,2 = 300 Н/мм2
Подставим данные в формулу и получим:
Из результатов расчета видно, что площадь поперечного сечения стержня болта гораздо больше площади, необходимой для сохранения целостности винта при нагрузке Р = 12740 Н. Это означает, что прочность при растяжении анкерного болта удовлетворяет условию прочности при данных условиях эксплуатации.
Проверочный расчет анкерных болтов
Анкерные болты – это болты крепления стойки подъемника к полу производственного корпуса ПТО.
Характеристика резьбы:
Резьба общего назначения, треугольная, однозаходная М14х2 ГОСТ 9150–59
шаг резьбы P = 2 мм
наружный диаметр резьбы болта d = 14 мм;
внутренний диаметр резьбы болта d1 = 11,84 мм;
средний диаметр резьбы болта и гайки d2 = 12,7 мм;
высота гайки Н = 11 мм;
высота резьбы h = 1,082 мм;
площадь сечения стержня винта A = 110.05 мм2;
материал – автоматная сталь А12 σв = 420 Мпа, δ = 22 %, НВ = 160
Каждая стойка подъемника крепится четырьмя болтами. При не нагруженном подъемнике будем считать болты ненагруженными. Рассмотрим одну стойку: при подъеме подъемником автомобиля ГАЗель нагруженными будут два внешних болта, поэтому необходимо произвести проверочный расчет анкерных болтов на прочность и смятие резьбы.
Проверочный расчет анкерного болта на прочность
Расчет на прочность резьбовых соединений выполняют следующим образом. Площадь поперечного сечения стержня болта по заданному внешнему усилию определяют по формуле:
где d1 – внутренний диаметр резьбы винта, d1 = 11,84 мм;
Р – растягивающее усилие, действующее на болт,
растягивающее усилие, действующее на один болт, найдем следующим образом:
где G – нагрузка, действующая на подъемник, G = 25480 Н.
Подставив данные в формулу, получим:
[σв]р – допускаемое напряжение на растяжение, допускаемое напряжение при растяжении находится по формуле:
[σв]р= σв/n,
где σв – предел прочности материала болта, σв = 420 Н/мм2;
n – коэффициент запаса, для статически нагруженного пластичного материала n = 2,5.
[σв]р= 420/2,5 = 168 Н/мм2
Подставим данные в формулу и получим:
Из результатов расчета видно, что площадь поперечного сечения стержня болта гораздо больше площади, необходимой для сохранения целостности болта при нагрузке Р = 6370 Н. Это означает, что прочность при растяжении анкерного болта удовлетворяет условию прочности при данных условиях эксплуатации.
Проверочный расчет анкерного болта на смятие
Из условия износостойкости резьбы по напряжениям смятия:
где F – сила, действующая на резьбу винта и гайки.
Так как подъемник П-97М имеет четыре нагруженных анкерных болта то силу, действующую на резьбу болта и гайки, найдем следующим образом:
где G – нагрузка, действующая на подъемник, G = 25480 Н.
d2 – средний диаметр резьбы винта и гайки d2 = 48 мм;
h – высота резьбы, h = 4 мм;
z – число рабочих витков.
Число рабочих витков находится следующим образом:
где Н – высота гайки, Н = 11 мм;
Р – шаг резьбы, Р = 2 мм.
[σсм] – допускаемое напряжение при смятии, допускаемое напряжение при смятии находится по формуле:
[σсм] = σв/n,
где σв – предел прочности материала болта, σв = 420 Н/мм2;
n – коэффициент запаса, для статически нагруженного пластичного материала n = 2,5.
[σсм] = 420/2,5 = 168 Н/мм2
Подставив данные в формулу и получим
Напряжение смятия полностью удовлетворяет условию износостойкости ходовой резьбы по напряжениям смятия.
Вывод: Предложенное приспособление просто в использовании, функционально и имеет огромный ресурс работы. Оно позволит расширить производственные возможности АТП и сократить время на ТО и ТР автомобилей ГАЗель а так же легкового парка. Что в свою очередь позволит не использовать для осмотра другие технические приспособления. Нипример такие как домкрат П 304.
4. Организация и технология диагностирования автобусов
4.1 Организация работ по диагностированию
Хорошо организованный процесс диагностирования дает значительный экономический эффект и обеспечивает безопасность эксплуатации автомобилей. Важное значение имеет и рациональное использование оборудования, повышение уровня механизации и автоматизации процессов ТО и диагностирования.
На предприятии ОАО «Карельский Окатыш» имеются некоторые особенности, которые влияют на проведение диагностики транспорта.
В мелких автохозяйствах нецелесообразен разрыв между выявлением неисправностей и местом их устранения. Во всех случаях следует стремиться к более полной загрузке средств диагностирования, максимально снижать непроизводительные затраты средств и рабочей силы. Следует учитывать использование средств диагностирования при внезапных отказах машин, что невозможно планировать, а также постов диагностирования при сезонных и контрольных осмотрах автомобилей. Соблюдая оптимальную последовательность измерения параметров, можно в 1,5...2 раза снизить трудоемкость диагностирования автомобиля.
Техническое диагностирование проводят при вводе машины в эксплуатацию, при техническом обслуживании и ремонте машин. Результаты каждого диагностирования заносят в диагностическую и накопительную карты.
Диагностическая карта служит для регистрации результатов диагностирования во всех случаях проведения диагностирования и принятия решения о необходимых работах при ТО и ремонте машины.
Накопительная карта предназначена для накопления информации об изменениях диагностических параметров в процессе эксплуатации машины, для сбора исходных данных для прогнозирования остаточного ресурса и вероятности безотказной работы в пределах межконтрольного периода. Накопительная карта ведется на каждую машину в течение всего срока ее эксплуатации. При передаче машины в другую организацию накопительную карту передают вместе с машиной. Данные накопительной карты могут быть использованы для статистического анализа надежности машины в целом и ее составляющих частей.
Форма и сведения диагностической и накопительной карт должны быть пригодными для обработки на ЭВМ.
В целях лучшего использования диагностического оборудования работу постов диагностирования целесообразно организовать не в одну смену. Диагностирование автомобилей в хозяйствах как минимум должно обеспечивать проверку технического состояния в объеме требований «Правил дорожного движения» к технически исправному автомобилю. Обязательной во всех случаях является проверка работы агрегатов и систем автомобиля на ходу. Особого внимания требуют органы управления, приборы освещения и сигнализации, прочность крепления всех агрегатов и механизмов (приборов) и комплектность их.
Приборы для диагностирования систем питания, электрооборудования, смазки, охлаждения могут быть общими для автобусных и автомобильных двигателей. Состояние цилиндропоршневой группы и газораспределительного механизма двигателя измеряют приборами КИ-13671 (КИ-4887-1) и К-2.72 (К-69М). Техническое состояние сопряжений коленчатого вала с подшипниками для автомобильных и тракторных двигателей определяют по давлению масла в магистрали, кроме того, виброакустическими установками при неработающем и работающем двигателе. Для проверки давления воздуха в шинах колесных тракторов и измерения сходимости управляемых колес и других параметров ходовой части и трансмиссии (пробуксовка механизма сцепления, люфт в коробке передач, в карданной и главной передаче) используют те же приборы и приспособления, что и для автомобилей.
На исследуемом предприятии отведено предусмотрен специальный участок для диагностики.. На данном посту выполняют только диагностические операции. В ходе проведения плановых работ с автотранспортным средством заполняется диагностическая карта автомобиля. Для этого необходимо определить следующие параметры:
Угол поворота вала двигателя, соответствующий замкнутому состоянию контактов прерывателя, град
Начальный угол опережения зажигания, град
Угол опережения зажигания, создаваемый центробежным или вакуумным автоматом, град
Суммарный угол опережения зажигания при 1000 об/мин, град
Напряжение аккумуляторной батареи при включенном стартере, В
Вторичное электрическое напряжение, кВ
Давление топливного насоса, кПа
Минимально устойчивая частота вращения коленчатого вала, об/мин
Содержание окиси углерода в отработавших газах %
Суммарный люфт коробки передач на передаче, град: второй прямой
Расход топлива, кг/ч:, на холостом ходу при скорости 100 (60) км
Суммарный угловой зазор карданной передачи, град
Биение карданного вала, мм
Суммарный зазор главной передачи, град
Мощность на прокручивание трансмиссии и колес, кВт, или выбег при 50...30 км/ч, м
Мощность на ведущих колесах, кВт
Радиальный зазор в шкворневых соединениях, мм: слева справа
Осевой зазор в шкворневых соединениях мм: слева справа
Асинхронизм искрообразования, град
Зазор между втулкой и валиком распределителя высокого напряжения, мм
Прорыв газов в картер, л/мин
Компрессия, МПа
Тормозная сила на колесах, Н: передних задних
Суммарный люфт рулевого колеса, град
Для автомобусов с дизельными двигателями из диагностической карты следует исключить 1...6, 9, 19, 20-й параметры. Дополнительно включить дымность отработавших газов, %; угол начала нагнетания топлива, град-; давление начала впрыскивания топлива форсункой, МПа; давление, создаваемое секцией топливного насоса, МПа; давление подкачивающего насоса, МПа; сопротивление фильтра тонкой очистки топлива, МПа.
После определения всех этих параметров следует определить интенсивность изменения диагностических параметров за период между двумя или более ТО-2 и рассчитать интенсивность на 10 тыс. км пробега автомобиля.
4.2 Диагностирование автобусов перед ТО-1 и ТО-2
Как правило, перед ТО-1 проводят только часть диагностических операций, обеспечивающих в первую очередь безопасность движения автомобиля и направленных на выявление причин отказов. Перед ТО-2 объем диагностирования значительно больший. Кроме определения технического состояния систем и механизмов, обеспечивающих безопасность движения автомобилей, проверке подлежат все агрегаты и механизмы.
Диагностирование автобуса перед ТО-1 проводят на одном посту, основным оборудованием которого являются стенд для проверки тормозов и переносные диагностические приборы для контроля приборов освещения и сигнализации, рулевого управления, а также инструмент для регулировки этих приборов.
Порядок выполнения операций, проводимых с автобусом:
Установить автомобиль передними колесами на ролики стенда КИ-4998. Заглушить двигатель. Колеса не должны касаться отбойных роликов
Проверить давление воздуха в шинах. Давление воздуха в шинах должно соответствовать паспортным данным. Не допускаются глубокие порезы, вспучивание, наличие посторонних предметов в протекторе шин
Проверить свободный ход педалей тормоза и сцепления, используя линейку. Заедание педалей не допускается
При необходимости отрегулировать свободный ход педалей тормоза и сцепления, используя линейку; набор инструмента.
При необходимости прокачать тормоза Тормоза прокачивать в следующем порядке: задний правый, передний правый, передний левый, задний левый
Проверить давление воздуха в пневмосистеме и падение давления при одном нажатии на педаль тормоза,
Проверить силу сопротивления качению колес переднего моста на стенде КИ-4998. Шины и накладки тормозных колес должны быть сухими. Без нажатия на педаль тормоза отклонение стрелки показывающего прибора от начальной отметки не должно превышать двух-трех делений Проверить эллипеность тормозных барабанов.
Запустить двигатель. Установить автомобиль задними колесами на ролики стенда. Заглушить двигатель. Колеса не должны касаться отбойных роликов
Проверить силу сопротивления качению задних колес, проверить эллипсность тормозных барабанов, проверить тормозную силу на колесах, проверить время срабатывания тормозов, при необходимости отрегулировать тормоза на максимальную силу торможения и минимальную одновременность срабатывания.
Проверить тормозную силу ручного тормоза на задних колесах. Проверить перемещение рычага ручного тормоза. При необходимости отрегулировать ручной тормоз.
Проверить состояние и действие приборов освещения, световой и звуковой сигнализации. Световое пятно должно иметь четко очерченные границы. Звуковой сигнал должен быть исправлен При необходимости отрегулировать установку фар, заменить лампочки
Проверить люфт рулевого колеса. При повышенном люфте проверить сочленения привода рулевого управления и при необходимости отрегулировать зазоры.
Часто необходимость в проведении диагностики возникает непосредственно в момент проведения ТО-1 и ТО-2. в таком случае проведение диагностики возможно и на посту ТО наряду с проведением диагностики на специальном участке.
Непригодное состояние автобуса к эксплуатации вызывается неисправностями, возникновение которых зависит от различных дефектов деталей, узлов, механизмов автобуса. Дефекты являются результатами недоработок конструкции, нарушения технологии изготовления и эксплуатации деталей и узлов автобуса и их естественного изнашивания. Диагностирование служит для определения технического состояния автобуса его агрегатов и узлов без разборки и является технологическим элементом ТО и ремонта, основным методом выполнения контрольных работ. В основе диагностирования лежит определение изменения параметров автобуса или его агрегатов по признакам, которые отражают их техническое состояние. Именно для этого в ходе проведения диагностических работ важно использовать точное оборудование и стенды. Диагностические признаки определяют три основных метода диагностирования: по параметрам рабочих процессов (мощность двигателя, расход топлива, тормозной путь и др.); по параметрам сопутствующих процессов, косвенно определяющих состояние механизмов автобуса (нагрев, шум, вибрация и др.); по структурным параметрам (износ деталей, зазоры в сопряжениях, люфты и др.). Для объективной оценки технического состояния автобуса и его узлов имеются переносное оборудование и специализированные стенды, которые измеряют тяговые и тормозные качества автобусов, определяют расход топлива и т. д. Переносное оборудование применяют для измерения состава отработавших газов, компрессии, частоты, амплитуды и. уровня шумов; электрических параметров. Это стетоскопы, компрессометры, щупы, специальные линейки, люфтомеры, динамометрические ключи, динамометры, ареометры, нагрузочные вилки, экраны для проверки света фар и др. Эти средства, несмотря на свою простоту, дают возможность быстро и качественно определить состояние агрегатов автобуса. Диагностирование технического состояния автомобилей подразделяется на общее и поэлементное. Общее (комплексное) — это определение расхода топлива, тормозного пути, выбега автобуса по инерции, мощности двигателя, ускорения и других, по которым оценивают общее состояние автобуса, определяют эффективность его эксплуатационных показателей и соответствие требованиям безопасности движения. Поэлементное диагностирование — это определение состояния каждого узла и агрегата автобуса.
Таким образом можно сделать вывод, что на исследуемом предприятии процесс проведения диагностики автобусов организован по традиционной схеме. Наряду с участками ТО-1 и ТО-2, ТР предусмотрен отдельный для проведения диагностики.
5. Экономическая эффективность от внедрения результатов проекта
В данной главе мы проводим анализ технико-экономических показателей, с целью выявления степени технического совершенства и экономической целесообразности разработанных проектных решений АТП. Эффективность проекта оценивается путём сравнения его технико-экономических показателей с нормативными (эталонными) показателями.
5.1 Выбор базы для сравнения
В качестве аналога обычно принимается агрегат того же назначения с близкими технико-эксплуатационными характеристиками. По своим параметрам аналог должен быть сопоставим с проектируемым агрегатом (производственным подразделением).
Условием сопоставимости вариантов является тождество следующих конечных результатов: состава и характера конечных результатов (продукции, работ, услуг), их качественных показателей (мощность, скорость, точность, грузоподъемность).
Для исследуемого АТП в качестве нового оборудования выбран подъемник автомобильный П-97М. Покраска изделия обладает повышенной прочностью к механическим воздействиям, высокими антикоррозийными свойствами, стойкостью к органическим растворителям, высокой декоративностью (2-3) кл. Данный агрегат имеет ряд преимуществ при использовании для ремонта автомобилей марки ГАЗель а так же легковых автомобилей. Так его использование позволяет сократить время обслуживания, разгрузить участок ремонта автобусов среднего и крупного класса. Устройство имеет электромеханический привод, обеспечена синхронизация кареток (привода соединены цепной передачей). Данный подъемник усовершенствован для поднятия автомобилей за раму.
Кроме подъемника предусмотрено приобретение стенда КИ 4998. Это стенд для контроля тормозных систем автотранспортных средств. Предназначен для измерения параметров эффективности торможения автотранспортных средств: тормозной силы, силы, создаваемой на органе управления тормозной системой. В результате использования данного стенда существенно повышается безопасность движения, а так же уменьшается износ тормозной системы на 22%. Использование данного стенда предусмотрено планом проведения диагностики автомобильного парка на предприятии. Сумма издержек на приобретение данного оборудования учтена при подсчете капитальных вложений. (см. гл 4 и гл. 5)
5.2 Расчет плановой калькуляции себестоимости ТО-1, ТО-2, ТР
Цеховая себестоимость рассчитывается по формуле
Сц=Спрп+Сзп+Срм+ Соп,
где Спрр – полная заработная плата производственных рабочих;
Сзп – нормативные затраты на запасные части
Соп – стоимость общепроизводственных накладных расходов.
Полная заработная плата производственных рабочих
Спрр=Спр+Сдоп+Ссоц,
где Cпр – основная зарплата;
Сдоп – дополнительная, Сдоп=0,07…0,1 Спр
Ссоц – отчисленная на соцстрах Ссоц=0,38(Спр+Сдоп).
Спр=tизд·Cr·Kt,
где tизд – нормативная трудоемкость ремонта изделия, чел-ч (таблица 10);
Сr – часовая ставка рабочих, исчисляемая по среднему разряду руб. за 1 час.
Средний разряд рабочих производственного корпуса по ТО и ТР составляет:
при техническом обслуживании 3,2
при текущем ремонте 3,6
Часовая ставка для разряда 3,2 составляет
СR=10,4 руб.;
Часовая ставка для разряда 3,6 составляет
СR=10,8 руб.;
Kt – коэффициент, учитывающий доплату за сверхсрочные и другие работы
Kt=1,03
Основная заработная плата при обслуживании и ремонте автомобилей
ТО-1 Спр=10,4·1,03·58121,51=622597,6 руб.;
TO-2 Cпр=10,4·1,03·43072,186=461389,3 руб.;
ТР Спр=10,8·1,03·164689,043=1832000,9 руб.
Полная заработная плата производственных рабочих
ТО-1 Спрр=622597,6 +62259,7+0,38(622597,6 +62259,7)= 945103,074 руб.;
ТО-2 Спрр=461389,3 +46138,9+0,38(461389,3 +46138,9)= 700388,916 руб.;
ТР Спрр=1832000,9+183200,1+0,38(1832000,9+183200,1)=2780977,38 руб.
Определяем стоимость запасных частей
Сзzтр=,
где Smi – норма затрат на запасные части на 1000 км пробега,
Lr - годовой пробег единицы подвижного состава, км.
S=78,9 руб.
Cзz=78,9· 461543,4= 36415,8руб.
Определяем стоимость ремонтных материалов
Ср.м=С'рм·Ni,
где С'рм – нормы затрат материалов на одно обслуживание
ТО-1 С'рм=31,4 руб.;
ТО-2 С'рм=49,7 руб.;
Ni – количество ремонтов;
ТО-1 Срм=31,4·732=22984 руб.;
ТО-2 Срм=49,7·153=7604,1 руб.
Количество ТО1 и ТО2 определяем по таблице 7.
5.3 Стоимость общепроизводственных расходов определяем по статьям общепроизводственных расходов
Основная зарплата общепроизводственного персонала
Звсп=12Кр·Киз·,
где Кр – коэффициент начисления на зарплату по соцстрахованию Киз=1,053
Зmi – среднемесячная зарплата работников [Принимается по данным базового предприятия];
Nвспi – число работников (см. приложение 1)
Звпс=12·1,03(17·12000+2·5000+6·7500)= 3201240 руб.
Амортизация здания
Стоимость здания по данным бухгалтерии составляет 2787600 руб.
Азд=0,025·Сзд,
Азд=0,025·2787600=69690 руб.
Амортизация оборудования
Аоб=0,1·Соб,
Соб=С'об·Fn
где С'об и– удельная стоимость оборудования на 1м2
Fn – производственная площадь Fn=3194,4 м2 (см. Генплан)
С'об=1082,6 руб/м2 Соб=1082,6 ·3194,4 =3458257,44 руб.
Аоб=0,1·3458257,44=345825,744 руб.
Амортизация приборов, инструмента.
Ап.и=0,13·Сп.и
Сп.и= С'п.и·Fn
где С'п.и – удельная стоимость приборов, инструментов на 1м2
Fn – производственная площадь Fn=3194,4 м2 (см. Генплан)
С'п.и =263,1 руб/м2 Сп.и=263,1 ·3194,4 =840446,64 руб.
Ап.и=0,13·840446,64 =109258,1 руб.
Текущий ремонт оборудования
Стоимость установленного оборудования составляет 3458257,44 руб.
Собтр=0,035·Соб,
Собтр=0,035·3458257,44 =121039руб.
Отчисления на содержание оборудования
Соб=0,004·Соб,
Собс=0,004·3458257,44 =13833,03руб.
Определяем затраты на рационализацию и изобретательство
Сп.р.=150·Рсп,
где Рсп – списочное число работающих (см. приложение 1)
Спр=150 ·27=4050 руб
Определяем затраты на охрану труда
Сот=100·Рсп, Сor=100·27=2700руб.
Определяем прочие расходы
Сп=0,05,
Сп=0,05(3458257,44+840446,64+121039+13833,03+4050+2700)= 4440326
Определяем процент общепроизводственных затрат к фонду зарплаты основных рабочих.
Рнак=(%),
Рнак==119%
Тогда общепроизводственные расходы по видам обслуживания будут:
Соп=,
ТО-1
Соп==740891,2 руб.
ТО-2
Соп==549053,3руб.
ТР
Соп==2180081руб.
Цеховая себестоимость по видам обслуживания.
ТО-1
Сц=945103,074 +22984+740891,2 =1708978 руб.;
ТО-2
Сц=700388,916 +7604,1+549053,3 =1257046,1руб;
ТР
Сц=2780977,38 +256819+2180081=5217877руб.
Определяем себестоимость одного обслуживания или ремонта
ТО-1
Свп==2334,7руб.
ТО-2
Свп==8215,9 руб.
ТР
Свп==5896руб./100км
5.4 Расчет инвестиционной эффективности.
Для определения экономической эффективности определяем срок окупаемости капитальных вложений.
Qr=,
Для этого определяем величину капитальных вложений, предусмотренных планом.
Стоимость подъемника П 97М составляет 43000 руб. с учетом доработки 44200 руб. (затраты на покупку металлопроката и крепежного элемента (2 п.м. железной арматуры 400руб; стоимость крепежа 200руб; стоимость монтажных работ 600руб) Стоимость металлопроката и крепежа, а так же проведение монтажных работ определяем по прейскуранту СПИКА-Металл по ценам марта 2009года. Стоимость стенда КИ 4998 составляет 230000 руб.
Переоснащение цехов с целью улучшения условий труда (см гл.6) составит 1455000 руб. Эту сумму мы не будем учитывать при расчете срока окупаемости так как финансирование данных мероприятий проводится по плану переоснащения производственных помещений, принятым и утвержденным в ОАО «Карельский окатыш».
Итого капитальные вложения на покупку нового оборудования составят 274200.
Определяем разницу в стоимости проведения ТО и Р до и после внедрения производственных решений. В результате внедрения предложенных решений ожидается снижение производственных затрат на 23%.
= 732,25*475,5 + 153,1*1782 = 607828,57 руб.
П2 = 470728,57 руб.
П1-П2 = 137100 руб.
Qr=,
Qt = 274200 / 137100 = 2.
Срок окупаемости нововведений – 2 года.
6. Безопасность жизнедеятельности при проведении ТО и ремонта
6.1 Организационно-правовые основы охраны труда
Основной структурой, выполняющей организацию охраны труда на АТП, является отдел охраны труда. Согласно типовому положению, отдел охраны труда является самостоятельным структурным подразделением и подчиняется непосредственно руководителю предприятия и главному инженеру. На отдел возлагается ответственность за подготовку и организацию работы на АТП по созданию здоровых и безопасных условий труда работающих, по предупреждению несчастных случаев на производстве и профессиональных заболеваний. Кроме отдела по охране труда за создание здоровых и безопасных условий труда несут ответственность руководители всех структурных подразделений.
В качестве основного элемента и метода предупреждения травматизма сред рабочих является система инструктажей. По характеру и времени проведения инструктажи бывают:
Вводный инструктаж
Проводится для всех работников, поступающих на работу на предприятие. Проводит инженер по охране труда в кабинете по охране труда в виде лекции или беседы. Освещаются вопросы: специфика работ на предприятии, режим работы, расположение производственных участков, порядок движения по территории, нормы выдачи спецодежды, спецпитания, электробезопасность, пожарная безопасность, приемы оказания первой медицинской помощи.
О проведении инструктажа делают запись в журнале регистрации вводного инструктажа (контрольном листе) с обязательными подписями инструктирующего и инструктируемого.
Первичный инструктаж на рабочем месте
Проводит непосредственный руководитель работ, к которому поступает работник.
Освещаются вопросы: безопасные приемы труда на оборудовании на данном месте, правила пользования спецодеждой, инструментом, проходами, сигнализацией.
После проведения первичного инструктажа заполняется вторая часть контрольного листа и журнал. Контрольный лист сдается в отдел кадров (в личное дело работника).
Повторный инструктаж
Проводится один раз в 6 месяцев, для работников, работающих на участках с повышенной опасностью – раз в 3 месяца.
Освещаются вопросы вводного инструктажа и инструктажа на рабочем месте. Его проводят с целью закрепления знаний безопасных приемов и методов труда.
Дополнительный инструктаж
Проводят в объеме первичного инструктажа на рабочем месте при изменении правил по охране труда, технологического процесса, при вводе в эксплуатацию нового оборудования, при несчастных случаях, при изменении места работы.
Целевой инструктаж
Проводится для работников перед выполнением работ с повышенной опасностью, допуск к которым оформляется нарядом-допуском.
Этот инструктаж фиксируют в наряде-допуске на производство работ и в журнале регистрации инструктажа на рабочем месте.
На предприятии постоянно осуществляется административно-общественный контроль за состоянием охраны труда. Контроль проводится в пять этапов:
Первая ступень
Ежедневно перед работой мастер, старший мастер, механик или бригадир совместно с общественным инспектором по охране труда обходят все рабочие места. Проверяют подведомственные участки. Замеченные недостатки устраняются.
Вторая ступень
Еженедельно начальником цеха, начальником гаража, колонны или отряда, главным механиком совместно с представителем профкома. Проверяют состояние охраны труда в цехе, гараже, мастерских. Выявленные недостатки устраняются.
Третья ступень
Ежемесячно комиссия в составе руководителя или главного инженера предприятия, председателя профсоюзного комитета, инженера по охране труда, главного механика, проверяет предприятие. Замеченные недостатки устраняются или записываются в журнал, где указывают недостатки, ответственного за исполнение и срок исполнения.
Четвертая ступень
Выполняется два раза в год руководством генерального директора объединения, председателя профсоюзного комитета комиссией, в состав которой входят все члены комиссии при третьей ступени контроля. Проверяется все предприятие.
Пятая ступень
Проводится ежегодно в порядке внутриведомственного контроля при проведении ревизий или других проверок комиссией из министерства, представителями пожарного надзора, техническим инспектором профсоюзов, представителем Гостехнадзора.
6.2 План мероприятий по улучшению условий и охране труда
Для того чтобы улучшить условия труда и снизить травматизм на предприятии ОАО «Карельский окатыш» разрабатывается план мероприятий. В плане предусматривается закупка нового технологического оборудования, закупка оборудования в кабинет медицинского контроля, оборудование комнаты отдыха водителей.
В разработке данного плана участвуют главные специалисты хозяйства. В хозяйстве все рабочие регулярно проходят медицинский осмотр.
Физические факторы являются основными опасными и вредными производственными факторами. Они приводят к профессиональным заболеваниям. В хозяйстве разрабатывается целый ряд мероприятий для снижения этих факторов.
На предприятии строго соблюдаются правила техники безопасности. На рабочих местах развешаны соответствующие инструкции по эксплуатации оборудования. В специально отведенных местах имеются ящики с песком и огнетушители.
Спецодеждой обеспечиваются все работники организации. За спецодеждой ведется строгий учет и по мере износа ее заменяют.
В настоящее время принят план по улучшению условий труда, в котором предусмотрено переоснащение ряда помещений а так же закупка нового оборудования.
Наименование мероприятия
Цех, подразделение
Срок выполнения
Капитальные вложения (тыс.руб)
Оборудовать кабинет медицинского контроля, оснащение: кушетка медицинская, письменный стол, стулья, настольная лампа, шкаф для одежды, вешалка для одежды, настольный коврик, прибор для определения артериального давления, термометр - 3 шт., фонендоскоп, алкометры - 2 шт., шпателя мед. – 10 шт., сумка с набором медикаментов для оказания неотложной мед. помощи – 1 шт., средства связи, умывальник.
УАТ
Гараж
1 кварт.
150
Оборудовать комнаты для выдачи нарядов аппаратурой для просмотра и записи видеоматериалов по ОТ и ПБ (видеодвойками) – 5 комплектов
УАТ
УР
Гараж
Стоянка груз. парка
1 кв.
75
Аппарат для раздачи воды – 2 шт.
УАТ
Гараж
Стоянка груз. парка
1 кв.
30
Кондиционеры – 10 шт.
УАТ
Гараж
АБК УАТ
2 кв.
150
Оборудование комнаты отдыха водителей
УАТ
Гараж
Стоянка груз. парка
3 кв.
350
Приобретение вагончика для механиков
ОТК, стоянка грузового парка
УАТ
Стоянка груз. парка
3 кв.
300
Вытяжная система типа «совплим» Flex-max
УАТ
РММ
2 кв.
60
Пряморельсовая вытяжная сиcтема MRP «совплим»
На 3 раб. месте
3 кв.
250
Пылеулавливающая установка УВП 1200 А
Гараж
1 кв.
100
6.3 Инструкция по технике безопасности для работы в цехе АТП
Общие требования безопасности.
1.1. К работе слесарем по ремонту оборудования, допускаются липа мужского пола не моложе 18 лет, прошедшие медицинское освидетельствован не.
1.2. Слесарь по ремонту оборудования, поступающий вновь на работу, обязан проходить предварительный и периодический медицинский осмотр.
1.3- При поступлении на работу, слесарь по ремонту оборудования, обязан пройти вводный инструктаж по ОТ и ПБ в отделе охраны труда предприятия, первичный инструктаж на рабочем месте по установленной программе.
1.4. Не реже одного раза в 3 месяца слесарь по ремонту оборудования обязан пройти повторный инструктаж с проверкой знаний правил эксплуатации обслуживаемого оборудования и требований ОТ и ПБ в комиссии цеха. Перед допуском слесаря к самостоятельной работе после стажировки не менее 2-х смен результаты проверки и инструктажа оформляются в личной карточке прохождения обучения по ОТ и ПБ.
1.5. Слесарь обязан проходить ежегодную проверку знаний правил безопасности в комиссии цеха по утвержденным экзаменационным билетам.
1.6. Слесарь по ремонту оборудования, обязан работать в установленное время и выполнять только порученную им работу по письменному наряду.
1.7. Запрещается, исключая аварийные ситуации, выполнять не порученные ответственным руководителем работы.
1.8. Слесарь по ремонту оборудования обязан:
1.8.1 Выполнять правила внутреннего распорядка;
1.8.2 Помнить о личной ответственности за соблюдение правил охраны труда и за безопасность окружающих па работе;
1.8.3 Во время работы пользоваться спецодеждой, спецобувью, предохранительными приспособлениями, средствами индивидуальной защиты согласно установленным нормам:
1.8.4 Не допускать присутствия на рабочем месте посторонних лиц;
1.8.5 Не выполнять распоряжений, если они противоречат правилам безопасности;
1.8.6 Уметь оказать первую (доврачебную) помощь пострадавшему согласно «Инструкции по оказанию первой помощи» на производстве, доложить руководителю работ о допускаемых нарушениях и самому принять все меры по устранению нарушений правил ОТ к ПБ:
1.9 В процессе работы на слесаря воздействуют следующие опасные и вредные производственные факторы:
1.9.1 Движущиеся автомобили, машины и механизмы; незащищенные подвижные и вращающие части производственного оборудования;
1.9.2 Повышенные запыленность и загазованность воздуха рабочей зоны;
1.9.3 Повышенные уровни шума и вибрации на рабочем месте при ремонтных операциях;
1.9.4 Незащищенные токоведущие части электрооборудования
1.9.5 Вредный компонент в применяемых материалах, воздействующий через кожный покров, дыхательные пути, пищеварительную систему и слизистые оболочки зрения и обоняния;
1.10. С целью предохранения от воздействия опасных и вредных производственных факторов слесарь обязан применять средства защиты в соответствии с «Типовыми отраслевыми нормами ».
Наименование спецодежды, спецобуви и др. средств индивидуальной защиты
Сроки носки
Ботинки кожаные с жестким подноском или сапоги кожаные жестким подноском
12
Костюм хлопчатобумажный для защиты от общих производственных загрязнений и механических воздействий или костюм из смешанных тканей для защиты от общих производственных загрязнений и механических воздействий
12
Куртка утепленная
18
П/комбинезон утепленный
18
Сапоги резиновые с жестким подноском
12
Валенки с резиновым низом или ботинки кожаные утепленные с жестким подноском
24
Каска защитная с подшлемником
36
Защитные очки, респиратор «Лепесток», беруши (каска с антифонами)
До износа
1.11. Слесарь но ремонту оборудования. обязан выполнять правила пожарной безопасности в соответствии с требованиями Инструкции пожарной безопасности на ОАО «Карельский окатыш».
1.12. Запрещается курение вне специально отведенного для этих целей места, пользование открытым огнем для подогрева емкости и агрегатов, заполненных горюче-смазочными материалами.
1.13.Рабочее место должно содержаться в чистоте; подтеки, и проливы ГТМ должны быть немедленно убраны.
1.14.Все легко воспламеняющие материалы (горюче-смазочные, обтирочные) должны хранится в закрытой металлической таре. 1.15.Запрещается загромождать проезды, подъезды к пожарным гидрантам, подступы к пожарным кранам, щитам и огнетушителям.
1.16.Прн обнаружении пожара, слесарь по ремонту оборудования обязан: 1.16.1. Немедленно сообщить об этом в подразделение пожарной охраны по телефону 01 или.
1.16.2 Приступить к тушению очага пожара имеющими средствами пожаротушения;
1.16.3 Принять меры по вызову к месту пожара непосредственного руководителя работ;
1.17. При несчастном случае необходимо оказать первую помощь пострадавшему, доложить непосредственному руководителю работ о травме, вызвать медпомощь по телефону 3-03, принять меры к сохранению обстановки на месте происшествия.
1.18.На рабочем месте или вблизи него использовать медицинскую аптечку, которую своевременно должны пополнять необходимыми медикаментами. 1.19.Лица, виновные в нарушении настоящей инструкции, привлекаются к ответственности в установленном законодательном порядке.
Требования безопасности перед началом работ.
2.1.Перед началом работы, слесарь по ремонту оборудования обязан: получить письменный наряд на производство работе росписью в книге нарядов, а на работах повышенной опасности - наряд-допуск установленной формы. Привести в порядок спецодежду, чтобы одежда была хорошо подогнана и застегнута, не мешала движению, иметь головной убор, подобрать необходимый инструмент, средства защиты, проверить их исправность, сроки их очередной проверки или испытания.
2.2. Осмотреть рабочее место, привести его в порядок, убрать посторонние предметы, устранить разлитые горюче-смазочные материалы при помощи опилок.
2.3.Рабочее место должно быть хорошо освещено, не загромождено деталями, соблюдать необходимые габариты проходов.
2.4.Выполнять только ту работу, которую поручил мастер, предварительно получив инструктаж по безопасным приемам ее выполнения с росписью в журнале нарядов, знать и соблюдать технологическую инструкцию на данный вид работ.
Требования безопасности во время работы
3.1.Ремонт оборудования и их агрегатов должен выполняться в предназначенных для этого местах, оборудованных устройствами, необходимыми для выполнения установленных работ, а также подъемно- транспортными механизмами.
3.2.Работы по постановке оборудования на ремонт или ТО производятся под непосредственным руководством мастера или начальника смены, согласно установленному порядку.
3.3.Перед тем, как приступить к ремонту, слесарь обязан убедиться в том, что оборудование установлено на предназначенное место, надежно закреплено и находится в устойчивом положении.
З.4 Агрегаты, узлы и детали весом более 15 кг. необходимо транспортировать с помощью специальных тележек. Разбирать автомобили и агрегаты, подвешенные на подъёмно-транспортных устройствах, без установки их на специальные устойчивые опоры, не разрешается. Нельзя также использовать в качестве опор случайные предметы (детали автомобиля, оборудование и т.к.), не приспособленные для этой цели.
3.5.Перед снятием агрегатов и деталей, влекущих за собой вытекание масла и воды, необходимо предварительно слить их в ёмкости, не допуская расплескивания и пролива жидкостей. При проливе жидкостей зги места необходимо посыпать своевременно опилками и убрать.
З.6 Если демонтаж агрегатов, и деталей связан с большим физическим напряжением, и создает неудобства в работе, следует применять приспособления (съемники), обеспечивающие безопасность при выполнении этих работ.
3.7. При ремонте оборудования необходимо демонтировать, устанавливать, транспортировать узлы и агрегаты при помощи подьемно-транспортных механизмов, оборудованных приспособлениями (захватами), гарантирующими полную безопасность работ.
3.8.Установку, демонтаж и транспортировку агрегатов производить грузозахватными приспособлениями, согласно схем строповки, технологических карт или проекта производства работ.
3.9.1 Подьем, опускание, и перемещение грузов осуществлять согласно установленных схем строповки, категорически запрещается натяжение грузовых канатов крана под острым углом.
3.10 При установке агрегатов на оборудование, запрещается проверять совмещение отверстий или поправлять регулировочные шайбы (прокладки) пальцем руки. Эту работу нужно выполнять при помощи конусной оправки.
3.11 Требования к оборудованию и механизмам:
3.11.1 Все эксплуатируемое оборудование должно находиться и полной исправности. Опасные места должны быть ограждены;
3.11.2 Оборудование, изготавливаемое собственными средствами, а также все оборудование после капитального ремонта должно отвечать требованиям правил техники безопасности, предъявляемым к новому оборудованию. Пуск в эксплуатацию нового оборудования, а также оборудования, прошедшего капитальный ремонт, должен производиться только после принятия его комиссией в эксплуатацию по приказу. Вес эксплуатируемое оборудование должно быть исправным и находиться под постоянным контролем руководителя производственного участка;
3.11.3.В случае неисправного оборудования руководитель участка проверяет наличие таблички, указывающей, на неисправность данного оборудования. Такое оборудование должно быть отключено (выключен привод, разобрана электросхсма)
3.11.4 Запрещается работать на оборудовании со снятым, незакрепленным или неисправным ограждениями;
3.11.5 Во время работы оборудования не допускается его чистка, смазка и ремонт;
3.11.6 Все передачи (ременные, цепные, шарнирные и другие) должны иметь сплошные предохранительные ограждения;
3.11.7 Передачи, размещённые внутри оборудования и агрегатов, должны быть закреплены со всех сторон;
3.11.8 Подающие валики, ролики и другие устройства должны быть снабжены предохранительными приспособлениями, препятствующими захвату одежды и пальцев рук рабочего;
3.11.9 Пусковые приспособления должны обеспечивать быстроту и плавность включения оборудования, удобство пользования. Кнопки остановки должны быть красного цвета, иметь надпись «СТОП» и выступать над панелью на 3 мм.
3.11.10 Электротельферы, лебёдки и другое оборудование, применяемое для перемещения агрегатов и тяжелых деталей, должно соответствовать требованиям правил безопасности, утвержденных органами Ростехнадзора;
3.11.11.Всё оборудование и механизмы, как стационарные, так и переносные, обслуживаются только обученными и проинструктированными рабочими;
3.11.12. Подъемно-транспортные устройства и вспомогательные приспособления (краны, тали, тельферы, съемники колес) должны ежегодно проходить испытания и освидетельствование с оформлением акта или записью в журнале, иметь табличку с ясно указанной на них датой последующего испытания и допустимой грузоподъемности;
3.12. Требования к инструменту:
3.12.1. К ручным инструментам (молоткам, зубилам, пробойникам.) предъявляются следующие требования безопасности: рабочие концы не должны иметь повреждения (выбоин, сколов);
3.12.2 Для выпрессовки закаленных деталей, оправки и выколотки необходимо изготавливать из латуни, чтобы в прессе работы исключить возможность откола твердых частиц металла:
3.12.3 Запрещается пользоваться напильником, стамеской и другими инструментами с заостренной нерабочей частью, с плохо укрепленной деревянной ручкой, а также с неисправной ручкой или без металлического кольца на ней;
3.12 4 При работе с зубилами, отрезными машинками и иными инструментами для рубки металла, применять защитные очки;
3.12.5. Ключи подбираются соответственно размерам гаек и болтов. Запрещается:
работать гаечными ключами с непараллельными изношенными губками;
увеличивать длину гаечного ключа за счет применения дополнительных рычагов (одевание труб, ключей и т.п.);
отвертывать гайки с помощью молотка и зубила;
3.12 6 Раздвижные ключи не должны иметь слабины в подвижных частях. Грани гаек и болтов, а также резьбы должны быть правильными и неизношенными.
3.12.7 Слесарные тиски должны быть в полной исправности, крепко захватывать изделие и иметь на губках несработанную насечку.
3.12.8 Электроинструменты хранятся в инструментальной и выдаются после предварительной проверки.
Запрещается присоединять электрический инструмент выше 42 V к электросети без штепсельного соединения.
3.12.9. При работе с пневматическим инструментом подавать воздух разрешается только после того, как инструмент установлен в рабочее положение. Присоединять и отсоединять шланги с пневматическим инструментом, разрешается после выключения подачи воздуха.
3.12.10. Паяльные лампы, пневматические и электрические инструменты, разрешается выдавать липам, прошедшим инструктаж и знающим правила обращения с ними.
3.13. При работе на верстаке, слесарь обязан знать, что верстаки имеют жесткую и прочную конструкцию, устойчивость. Поверхность верстака строго горизонтальна, оббивается сталью, не имеет выбоин, заусениц, ширина - не менее 750мм, высота 800-900мм. Верстак имеет защитный экран для защиты рядом работающего персонала.
Требования безопасности в аварийных ситуациях
4.1. В аварийной ситуации, слесарь по ремонту оборудования обязан знать: Расположение щитов освещения, рубильников отключения оборудования от сети напряжения.
4.2. При возникновении пожара, принять меры к тушению всеми имеющимися средствами, а при невозможности тушения своими силами, покинуть здание согласно плана эвакуации, вызвать ПЧ-5 потел. 01;
4.3 При оказании первой доврачебной помощи необходимо выполнять « Инструкцию по оказанию первой помощи»
4.4 Знать и соблюдать все требования, изложенные в планах ликвидации возможных аварий на участке и в цехе.
Требования безопасности по окончании работ
5.1 привести в порядок инструменты и приспособления, протереть и уложить на постоянные места хранения
5.2. Произвести уборку рабочего места, при сменной работе сдать его сменщику, расписаться в книге приема-сдачи смен.
5.3 Снять одежду и повесить ее в специально отведенный для этой цели шкаф.
5.4 Вымыть руки и лицо теплой водой с мылом или принять душ.
5.5 Обо всех недостатках, обнаруженных во время работы, слесарь но ремонтуоборудования, обязан сообщить мастеру или начальнику участка.
6.4 Охрана окружающей среды
Охрана природы – система государственных, международных и общественных мероприятий, направленных на рациональное использование, охрану и обновление природных ресурсов, на защиту окружающей среды от загрязнения и разрушения для создания оптимальных условий существования человеческого поколения, удовлетворения материальных и культурных потребностей живущих поколений человечества.
Основным направлением и задачей охраны природы является охрана в процессе ее использования.
В отношении автотранспортных предприятий разработка мероприятий по охране атмосферного воздуха, водоемов и почв ведется на основе СНиП 2.04.03-85, ВСН 01-89 Минавтотранса РСФСР и других нормативно-методических документов.
Охрана водоемов и почв от загрязнений сточными водами автотранспортного предприятия предполагает устройство твердого покрытия проездов и стоянок автомобилей, озеленение свободных от застройки площадей, очистку дождевых вод, сточных вод при мойке автомобилей с устройством оборотного водоснабжения.
Так например пост окраски ТС оснащен отсосом и аппаратом очистки. Очистка осуществляется в гидрофильтре типа С-840. Эффективность очистки по красочному аэрозолю достигает 90%, а по компонентам растворителя – 30%.
Для наружной мойки автомобилей и автобусов предусмотрена, малосточная система оборотного водоснабжения с использованием оборотной воды.
Концентрация загрязнения в воде, подаваемой для мойки с помощью оборотной системы водоснабжения находится в пределах нормы и не превышает: взвешенных частиц - 70 мг/л при мойке грузовиков, 40 мг/л - легковых автомобилей и автобусов; нефтепродуктов — соответственно 20 и 15 мг/л, тетраэтилсвинца — 0,001 мг/л.
При сливе сточных вод в канализационные коллекторы в них должно быть не более 0,25—0,75 мг/л взвешенных веществ и 0,05—0,3 мг/л нефтепродуктов; наличие тетраэтилсвинца в сточных водах не допускается.
Доставка ГСМ для автотранспорта и технологического процесса завода осуществляется бензовозами. На территории завода имеется механизированная заправка машинотракторного парка.
Сбор отработанных масел осуществляется в отдельную емкость, которая по мере наполнения отправляется на переработку. Нормы расхода смазочных масел на АТП строго выдерживаются
Работа двигателя с неисправной топливной системой, подтеканием ГСМ в системе питания и смазки не допускается. За этим в производстве следит и отвечает начальник ОТК, а в автопарке – механик автопарка.
Контроль за газораспределительной выхлопной и топливной системой отремонтированных автомобилей осуществляет начальник ОТК, а за автомобилями заводского автопарка механик автопарка. На АТП регулярно проводятся обследования автомобилей на выброс вредных газов с последующей их регулировкой до норм. В рамках проведения диагностических работ, а так же плановых осмотров.
За невыполнение установленных требований по охране природы на предприятии, к ответственным за это лицам, комитетом по "Охране природных ресурсов" применяются меры наказания: составление актов, наложение штрафов и т. д.
Заключение
В данном дипломном проекте проведен анализ существующей деятельности и технологии ТО и ремонтов автобусов. Сделан вывод о необходимости проведения технического переоснащения цеха АТП.
В данной работе разработан план внедрения нового технологического оборудования в целях повышения производительности труда, охраны окружающей среды и повышения механизации технологических процессов
В конструктивной части разработано приспособление для поднятия автомобилей под раму с помощью усовершенствованного подъемника П 97М.
Разработаны мероприятия по безопасности труда, охране природы. Запланированы мероприятия по улучшению условий труда на предприятии.
Капитальные затраты на технологическое переоснащение составят 274200 руб. Срок окупаемости нововведений — 2года.
Список литературы
Напольский Г.М. Технологическое проектирование АТП и СТО. – М.: Транспорт, 1993 – 272с.
НИИАТ Краткий автомобильный справочник. – М.: Транспорт, 1985 – 220с.
Положение о техническом обслуживании и ремонте подвижного состава автомобильного транспорта./Минавтотранс РСФСР – М.: Транспорт, 1986 – 73с.
. Табель технологического оборудования и специализированного инструмента для АТП, АТО и БЦТО. — М.: ЦБНТИ Минавтотранса РСФСР, 1983. — 98 с.
. Табель технологического оборудования и специнструмента для станций технического обслуживания легковых автомобилей. М.: НИИИНАвтопром. 1980 — 78 с.
Руководство по диагностике технического состояния подвижного состава автомобильного транспорта; РД-200-РСФСР-15-0150-81. М.: ЦБНТИ Минавтотранса РСФСР, 1982. — 87 с.
СНиП II-93-74: Предприятия по обслуживанию автомобилей /Госстрой СССР. — М.: Стройиздат, 1975. — 18 с.
Техническая эксплуатация автомобилей: Учебник для ВУЗов / Ю.П. Баранов, А.П. Болдан, В.М. Власов, Г.В. Крамаренко, Г.М. Напольский. Под ред. Г.В Крамаренко, — 2-у изд. Переработанное и дополненное — М.: Транспорт, 1983. — 488 с.
Инструкции по составу, учету и калькуляции затрат, включаемых в себестоимость перевозок (работ, услуг) предприятий автомобильного транспорта Министерства транспорта Российской Федерации. М. 1995.
Ф.Н. Авдонькин «Текущий ремонт автомобилей» М.: «Транспорт» 1978 - 271с
Межотраслевые правила по охране труда на автомобильном транспорте ПОТ РМ-027-2003./М.:НЦЭНАС, 2004.-168с.
Бураев Ю.В. Безопасность жизнедеятельности на транспорте: учеб. Дне студентов высших учебных заведений / Ю.В. Бураев – М.:Академия 2004.-288с.
В.И. Чернякевич Автомобильные перевозки Й-Ола. 2006 - 67с.
В.И. Чернякевич В.В. Багнюк Планирование АТП Й-Ола. 2006 - 113с
В.И. Чернякевич В.В. Багнюк В.В. Макаров Проведение ТО и Р Й-Ола. 2006 - 205с
В.В. Макаров Организация технического обслуживаия и ремонта автобусов. Й-Ола 2005 - 167с
Грибков В.М., Карпенкин П.А. Справочник по оборудованию для технического обслуживания и текущего ремонта автомобилей: - М: Россельхозиздат, 1984, 225 с.
Приложение 1
Наименование профессии
общецеховый
автоколона
гараж пассажирского транспорта
по ш.р.
по ш.р.
по ш.р.
Рабочие
Основной персонал
водитель автомобиля
29
водитель автомобиля (легкового)
19
водитель автомобиля (автокрана)
водитель автомобиля (автоб.разл.вмест.)
9
водитель автомобиля (автоб.на рег.гор.пасс.маршр.)
44
водитель погрузчика
машинист автогрейдера
бригадир на участках ОП
1
1
Итого
0
102
1
Ремонтный персонал
слесарь по ремонту автомобилей
17
слесарь по топл.аппаратуре
аккумуляторщик
1
токарь
2
маляр
1
шлифовщик
электрогазосварщик
2
вулканизаторщик
1
паяльщик
1
Итого
0
0
25
Итого рабочих
0
102
26
РСиС
Основной персонал
начальник управления
1
энергетик управления
1
механик управления
1
заместитель начальника управления по производству
1
начальник отд.эксплуатации
1
начальник автоколонны
1
начальник гаража
1
начальник смены
4
диспетчер
4
начальник транспортного отдела
1
ведущий инженер по транспорту
1
инженер по транспорту 1 кат.
1
начальник ОРП
1
ведущий инженер по О и НТ
2
специалист по кадрам 1 кат.
1
механик ОТК
2
Ремонтный персонал
начальник участка ремонта
мастер
2
Прочий персонал
зам.нач.по социально-труд.вопр.
1
ведущий инженер по ОТ, ПБ и БД
1
секретарь руководителя
1
Итого РСиС
23
1
5
Приложение 2
№ п/п
Гаражный №
Марка а/м
Тип а/м
Гос.№
Год выпуска
Вид топл.
1
2179
Шевроле Нива
л/а
Е477КУ
2006
АИ92
2
2180
Шевроле Нива
л/а
Е478КУ
2006
АИ92
3
2181
Форд Фокус
л/а
О692ОО
2006
АИ95
4
2182
Шевроле Экспр
л/а
Е236НТ
2004
АИ95
5
2183
ВАЗ 21214
л/а
Е158АУ
2005
АИ92
6
2184
ВАЗ 21214
л/а
Е157АУ
2005
АИ92
7
2186
Шевроле Нива
л/а
Е043АВ
2004
АИ92
8
2187
ГАЗ 31105
л/а
Е300АВ
2004
АИ92
9
2189
ГАЗ 31105
л/а
Е181АВ
2004
АИ92
10
2190
Вольво S80
л/а
В703УТ
2000
АИ95
11
2191
ВАЗ 21310
л/а
В249ВЕ
2000
АИ92
12
2192
ГАЗ 311000
л/а
В545ЕО
1999
АИ92
13
2193
ГАЗ 3102
л/а
В695НС
2003
АИ92
14
2194
Вольво S70
л/а
А400ХЕ
1998
АИ95
15
2195
Volkswagen
л/а
В282УН
2000
АИ95
16
2197
ГАЗ 311000
л/а
В352ВЕ
1997
АИ92
17
2198
УАЗ 31514
л/а
А017СМ
1997
АИ92
18
2199
ГАЗ 2217
микроавтобус
В694НС
2003
АИ92
19
2200
ГАЗ 322100
микроавтобус
В042ПРОФ
1999
АИ92
20
2201
ГАЗ 31105
л/а
Е452КУ
2006
АИ92
21
2202
ГАЗ 311000
л/а
А336ХХ
1998
АИ92
22
2203
ГАЗ 3102
л/а
В455УН
2000
АИ92
23
2204
ВАЗ 21213
л/а
А482ХХ
1999
АИ92
24
2205
ГАЗ 3102
л/а
В442УУ
2000
АИ92
25
2206
Volkswagen
л/а
О466ОО
2002
АИ95
26
2208
ГАЗ 3102
л/а
А500ХХ
1999
АИ92
27
2209
Honda GR-V
л/а
В255НК
2003
АИ95
28
2210
ВАЗ 21213
л/а
В453УН
2000
АИ92
29
2211
ВАЗ 21213
л/а
В851СН
1999
АИ92
30
2212
ГАЗ 311000
л/а
В400ЕО
2002
АИ92
31
2214
ВАЗ 21214
л/а
Е004АО
2005
АИ92
32
2215
Honda GR-V
л/а
О004ОО
2003
АИ95
33
2216
ВАЗ 2121
л/а
В785ВК
1999
АИ92
34
2217
ВАЗ 2121
л/а
В048ОУ
1999
АИ92
35
2218
ВАЗ 2121
л/а
В049ОУ
1999
АИ92
36
2219
Toyota
л/а
О880ОО
2003
Д/Т
37
2220
Toyota
л/а
О878ОО
2003
Д/Т
38
2222
ВАЗ 21310
л/а
Е159АУ
2005
АИ92
39
2224
ВАЗ 21214
л/а
Е175АВ
2004
АИ92
40
2225
ВАЗ 21214
л/а
Е173АВ
2004
АИ92
41
2229
ВАЗ 21214
л/а
Е188АВ
2004
АИ92
42
2230
УАЗ 390902
грузовой фургон
В687СТ
2004
А80
43
2231
ВАЗ 32106
учебный
Е186АВ
2004
АИ92
44
2233
ВАЗ 32106
учебный
Е174АВ
2004
АИ92
45
2236
УАЗ 31519
л/а
Е176АВ
2004
А80
46
2237
УАЗ 31519-01
л/а
А336УВ
1997
АИ92
47
2239
ВАЗ 21070
учебный
В389ОУ
1999
АИ92
48
2240
УАЗ 3962-01
спецфургон
А302ЕУ
1994
АИ92
49
2241
УАЗ 3962-01
спецфургон
В805СН
1994
А80
50
2242
УАЗ 31514
л/а
В058НТ
2003
А80
51
2243
ГАЗ 2217
микроавтобус
В750ОУ
2000
АИ92
52
2244
РАФ 22031
скорая помощь
А661ЕА
1993
АИ92
53
2245
УАЗ 22069
микроавтобус
В197УН
2000
А80
54
2246
ГАЗ 2217
микроавтобус
Е041АВ
2004
АИ92
55
2247
ГАЗ 31105
л/а
В939ХО
2004
АИ92
56
2248
ГАЗ 31105
л/а
В 949ХО
2004
АИ92
57
2250
ГАЗ 2217
микроавтобус
Е042АВ
2004
АИ92
58
2251
УАЗ 31519
л/а
Е179АВ
2004
А80
59
2252
УАЗ 39094
бортовая
Е178АВ
2004
А80
60
2253
УАЗ 39099
грузовой фургон
Е321ЕУ
2005
А80
61
2254
УАЗ 39094
бортовая
Е196АВ
2004
А80
62
2255
УАЗ 3909
грузовой фургон
Е184АВ
2004
А80
63
2256
УАЗ 3909
грузовой фургон
Е193АВ
2004
А80
64
2258
УАЗ 3909
грузовой фургон
Е195АВ
2004
А80
65
2259
УАЗ 39099
грузовой фургон
В194УН
2000
АИ92
66
2260
УАЗ 3909
грузовой фургон
Е190АВ
2004
А80
67
2261
Фольксваген
грузовой фургон
В890СН
1976
АИ92
68
2262
УАЗ 3909
грузовой фургон
Е185АВ
2004
А80
69
2263
УАЗ 39099
грузовой фургон
В196УН
2000
А80
70
2264
УАЗ 3909
грузовой фургон
Е182АВ
2004
А80
71
2265
УАЗ 3909
грузовой фургон
Е187АВ
2004
А80
72
2266
УАЗ 2206-030
грузопассажирский
А594СР
1997
А80
73
2268
ВАЗ 21214
л/а
Е236АВ
2004
АИ92
74
2269
ГАЗ 270500
грузовой фургон
В416ОК
1999
АИ92
75
2270
ГАЗ 322100
микроавтобус
В386ОУ
1999
АИ92
76
2271
ВАЗ 21214
л/а
Е239АВ
2004
АИ92
77
2272
УАЗ 31519
л/а
Е241АВ
2004
А80
78
2273
ГАЗ 33027-415
грузовой фургон
Е015КА
2005
АИ92
79
2274
ГАЗ 33027-415
грузовой фургон
Е014КА
2005
АИ92
80
2275
UAZ PATRIOT
л/а
Е091КУ
2006
АИ92
81
2276
УАЗ 331519
л/а
Е089КУ
2006
АИ92
82
2277
УАЗ 39099
грузовой фургон
Е088КУ
2006
А80
83
2278
УАЗ 39099
грузовой фургон
Е092КУ
2006
А80
84
2279
ГАЗ 328111-002
Аварийно спасательн.
Е087КА
2005
АИ92
85
2280
УАЗ 3909
грузовой фургон
Е183АВ
2004
А80
86
2281
УАЗ 396259
грузовой фургон
Е240АВ
2004
А80
87
2282
УАЗ 22069
грузовой фургон
Е192АУ
2005
А80
88
2283
УАЗ 39099
грузовой фургон
Е193АУ
2005
А80
89
2284
3260С
скорая помощь
2005
АИ92
90
2285
ВАЗ 21213
л/а
А481ХХ
1999
АИ92
91
2286
УАЗ 39094
бортовая
Е411КУ
2006
А80
92
2287
УАЗ 39094
бортовая
Е412КУ
2006
А80
93
2290
УАЗ 3962-01
грузовой фургон
А308ЕУ
1992
АИ92
94
2292
УАЗ 3909
грузовой фургон
В751ОУ
2000
А80
95
2293
УАЗ 3909
каратажная
А641ЕА
1994
А80
96
2294
ГАЗ 22177
микроавтобус
Е115АВ
2004
АИ92
97
2296
УАЗ 31512
л/а
В553МК
1994
А80
98
2299
УАЗ 3909
спецфургон
А239ХХ
1994
А80
99
2300
УАЗ 39099
грузовой фургон
В207ВЕ
2000
А80
100
2302
УАЗ 3909
спецфургон
А061СМ
1995
АИ92
101
2303
УАЗ 39099
грузовой фургон
В213ТМ
2000
АИ92
102
2305
УАЗ 31514
л/а
Е044АВ
1999
А80
103
2851
Икарус 280
автобус
А307ХХ
1992
Д/Т
104
2852
Икарус 280
автобус
В442ОУ
1992
Д/Т
105
2853
Икарус 280
автобус
А143ХХ
1990
Д/Т
106
2855
Икарус 280
автобус
А336ЕУ
1995
Д/Т
107
2860
Икарус 280
автобус
АА610
1989
Д/Т
108
2861
Икарус 280
автобус
АА611
1989
Д/Т
109
2862
Волжанин
автобус
АА961
2001
А80
110
2863
Волжанин
автобус
АА963
2001
Д/Т
111
2864
Волж.527004
автобус
АА618
2004
Д/Т
112
2865
Волж.527004
автобус
АА619
2004
Д/Т
113
2866
Волж.527004
автобус
АС451
2005
Д/Т
114
2867
Волж.527004
автобус
АС452
2005
Д/Т
115
2868
Волж.527004
автобус
АС453
2005
Д/Т
116
2869
Волж.527004
автобус
АС454
2005
Д/Т
117
2876
Икарус 260
автобус
АА609
1989
Д/Т
118
2877
Икарус 260
автобус
АА972
1989
Д/Т
119
2878
Икарус 260
автобус
АА605
1982
Д/Т
120
2879
Икарус 260
автобус
АА606
1982
Д/Т
121
2880
Икарус 260
автобус
АА607
1982
Д/Т
122
2881
Икарус 260
автобус
АА968
1982
Д/Т
123
2884
Икарус 260
автобус
АА969
1982
Д/Т
124
2885
Икарус 260
автобус
АА608
1982
Д/Т
125
2886
Икарус 260
автобус
АА604
1982
Д/Т
126
2887
Икарус 260
автобус
АА970
1982
Д/Т
127
2921
Икарус 260
автобус
АА964
1982
Д/Т
128
2923
Икарус 260
автобус
АА960
1982
Д/Т
129
2925
Икарус 260
автобус
АА612
1982
Д/Т
130
2926
Икарус 260
автобус
АА974
1982
Д/Т
131
2927
Икарус 260
автобус
АА603
1982
Д/Т
132
2928
МаРЗ 52661
автобус
АА962
1999
Д/Т
133
2930
ЛАЗ-695
автобус
АА971
1994
А80
134
2931
ЛАЗ-695
автобус
АА976
1994
А80
135
2935
ЛАЗ-695
автобус
АА965
1994
А80
136
2936
Икарус 256
автобус
АА959
1989
Д/Т
137
2937
Икарус 256
автобус
АА957
1989
Д/Т
138
2938
Икарус 256
автобус
АА958
1989
Д/Т
139
2941
ПАЗ 32051
автобус
В671ВК
1994
А80
140
2942
ПАЗ 32051
автобус
АА975
1995
А80
141
2958
ПАЗ 32051
автобус
АА966
1994
А80
142
2959
ПАЗ 32051
автобус
АА973
1994
А80
143
2960
ПАЗ 32051
автобус
АА967
1994
А80
144
2990
ГАЗ 3307
Бортовой
7672 КСМ
1992
А80
145
2991
ЗИЛ 4514
Самосвал
В246УМ
1993
Д/Т
146
5004
МТЗ 82
Трактор
б/н
1993
Д/Т
147
5000
4045
Погрузчик
б/н
А80
148
ГА 2705
грузовой фургон
2006
АИ92
Приложение 3
№ п/п
Наименование, обозначение, тип, модель оборудования, оснастки
Кол-во
Стоимость
Процент износа
1.
Hастольно-свеpлильный станок СФ-16-01
1
16826,00
5
2.
Автопогpузчик г/п 5тн
1
55370,00
18,9
3.
Аппарат высокого давления без нагрева 1.286-501
1
70232,80
16,667
4.
Аппарат моечный высокого давления НД 10/25
1
71186,44
14,286
5.
Вентиляционная установка "Плимут"
1
21327,77
10
6.
Вытяжное устройсво "ПЛИМУТ"
2
43073,34
10
7.
Газоанализатор Инфакар-08,01
1
33972,88
11,111
8.
Дистилятор Д - 4 (Б-6199 руб.)
1
6199,00
0
9.
Домкрат гидравлический Y421000 г/п 10т
1
56605,00
8,333
10.
Домкрат реечный 5 тн
2
1154
0
11.
Дрель ручная
4
666,68
0
12.
Заpядное устpойство 3М 1 - У 350х900
3
5865
7,1
13.
Заpядное устpойство УЗ - 3М
4
7820
7,1
14.
Заpядное устpойство УЗО - 1М 1.5кв 230х320
1
1955,00
7,1
15.
Загрузчик ПАК - 2
1
6640,68
14,286
16.
Измеритель комплекта сцепления ИКСп
1
55084,75
14,286
17.
КДС -5К Стенд - развал компьютерный
1
178700,00
14,286
18.
Комплект для головок блоковГАЗ/ВАЗ
1
29828,73
14,286
19.
Компрессометр К-1(0-15кг/см)
1
1649,75
0
20.
Компрессометр К-74-36
1
10174,83
11,111
21.
Компьютер Pentium 4
1
32685,00
20
22.
Краскораспылитель SB-2000
1
2750,00
0
23.
Маслораздатчик передвижной RAASM-32024 (34k/)
1
24152,54
14,286
24.
Маслосборник отработтаного масла с 508
1
10887,50
5
25.
Моечная установка высого давления
1
52891,30
14,286
26.
Мойка BOSCH AQUATAK 115 (для мойки автомашин)
1
6990,00
20
27.
Мойка высокого давления
1
3660,00
0
28.
Мотор-тестер МТ-4 с осцилографом
1
67488,05
14,286
29.
Нутромер индикаторный 10-18
1
2525,83
10
30.
Пpесс Р - 337 2 квт 400 х 1500
1
5601,00
7,7
31.
ПК Celeron 2000/845 PE/256/40/CD
1
20280,00
20
32.
Пневмогайковерт Airtec AT 37DLL
1
28533,90
40
33.
Пневмогайковерт DINO PAOLI
1
98389,83
40
34.
Пневмомолоток FRH-3-2
1
10364,50
40
35.
Пневмошлифмашинка эксцентр.FOR-150
2
31093,5
40
36.
Пневмошлифмашинка эксцентр.FOR-175
1
16423,74
40
37.
Подъемник типа "Жиpаф"
1
4003,00
18,9
38.
Подъемник электромеханический П-178 Д-04
1
96101,69
10
39.
Подьемник СДО-25 двухстpоечный г/п 2,5тн.
1
10000,00
5,9
40.
Полуавтомат сварочный ПДГ-300
1
39830,51
14,286
41.
Пресс гидравлический настольный Р 338
1
101640,00
6,667
42.
Прибор "Карат-4"
1
20161,02
11,111
43.
Прибор КИ - 582
1
6583,33
0
44.
Прибор сканер - тестер ТСТ - 10
1
23516,95
16,667
45.
Принтер HP LJ 1010
1
6150,00
0
46.
Пускозарядное устройство BLUEWED-MAJOR 1500
1
41237,29
6,667
47.
Пылесос NT 561 (ЕCО)
1
11406,10
10
48.
Пылесос- воздуходувка Viking BE 600 (для сушки машин)
2
6600
14,286
49.
Радиостанция возимая Р 020
3
19658,34
0
50.
Радиотелефон Panasonic KX - TCD 715/KX- TCD 235
1
3630,51
20
51.
Сварочный выпрямитель ВДУ - 506 УЗ
1
61016,95
14,286
52.
Сварочный полуавтомат У-200П
1
33550,00
14,286
53.
Сканер универсальный сист. PDL 2000
1
161000,00
48
54.
Солидолонагнетатель RAASM - 68213
3
62203,39
14,286
55.
Солидолонагнетатель пневматический 14 кг
1
12500,00
14,286
56.
Станок балансиpовочный К-623А
1
9200,00
14,3
57.
Станок веpтикально-свеpлильный унивеpсальный одношпиндельный 2H135
1
6815,00
5
58.
Станок для расточки тормозных барабанов Р- 185
1
144067,80
5
59.
Станок для расточки тормозных барабанов Р- 185
1
199152,54
14,118
60.
Станок настольно-свеpлильный вес 85кг.
1
22896,00
5
61.
Станок свеpлильный /наибольший объем свеpления 6 мм/
1
60491,00
5
62.
Станок свеpлильный HС - 1.5квт
1
23641,00
5
63.
Станок токаpно-винтоpезный 1К62 з.н.68722
1
4170,00
5
64.
Станок токаpный 1К 62 Д 12.22квт
1
6410,00
5
65.
Станок точильно-шлифовальный SE-408
1
7574,15
0
66.
Станок фpезеpный 6Р81
2
32253
5
67.
Стенд 532-2М
1
12501,00
11
68.
Стенд балансиров. Oebuna 480
1
296949,15
9,091
69.
Стенд балансировочный HW - 130
1
102000,00
14,3
70.
Стенд для выпресовки шкворней П-5
1
87152,54
14,286
71.
Стенд для притирки клапанов Р23-74
1
78559,32
14,286
72.
Стенд для срезания тормозн. накладок Р-174
1
157309,32
14,286
73.
Стенд К - 245
1
73229,70
14,286
74.
Стенд КИ - 22210
1
141000,00
14,3
75.
Стенд Р-184М для пpавки колес
1
15750,00
11
76.
Стенд р/с диз. (эл. мех.) Р-660
1
39728,81
14,286
77.
Стенд рихтов. Эксперт-2000-2
1
144427,97
9,091
78.
Стенд шиномонтажный для груз.автомобилей Golden 1557
1
237288,14
16,667
79.
Стенд шиномонтажный НТ-320 универсальный
1
78342,97
16,667
80.
Стробоскоп М-3Д для дизельного двигателя
1
3122,71
0
81.
Съемник гидравлический СГА32-15П
1
39680,00
8,333
82.
Тpактоp МТЗ-82
1
57192,00
11,1
83.
Тележка 536 М
1
2257,00
12,5
84.
Тележка г/п 200 кг
3
35054,01
12,5
85.
Тележка КУ - 200
2
17095,64
0
86.
Телефонный аппарат KX - TCD 205
1
2098,31
20
87.
Тестер ДСЕ - 6С
1
20040,68
14,286
88.
Тиски 125мм
1
1486,23
0
89.
Тиски слесарные 125 (Б-1420 руб.)
2
2840
0
90.
Тиски слесарные стальные 160 мм
2
5360,16
0
91.
Тиски станочные 160 мм с откр винтом
1
17345,21
40
92.
Установка 4Ш-1А шиномонтажная для монтажа и демонтажа колес
1
12600,00
11
93.
Установка для мойки двигателей "Тайфун"
1
14628,00
14,3
94.
Установка моечная Magibol-90
1
138347,46
14,286
95.
Устройство вытяжное с э/п и вент MERF-M-75-5/10/SP
2
61440,1
10
96.
Шлифовальная установка Р- 186
1
76240,00
5
97.
Электродрель БЭС
1
181,70
0
98.
Электродрель ДУ 780 ЭР
1
1384,74
40
99.
Электродрель ДУ 800 ЭР
1
1471,00
40
100.
Электродрель ИЭ - 1519Э
1
1458,00
40
101.
Электродрель МЭС - 600 ЭРУ
1
1490,00
40
102.
Электродрель с уд-м Е 132 АТ - 60
1
1462,03
40
103.
Электроточило ДSC - 175 (Б-2850 руб.)
1
2850,00
0
104.
Электрошлифмашинка BOSCH 230
1
5083,91
0
105.
Электрошлифмашинка угловая AGP 125-10 Protool
2
7447,06
40
106.
Электрошуруповерт DS18DMR HITACHI
1
8650,00
40
Итого
130
4329009,08
Общая стоимость оборудования
3458188,97
Общая стоимость приборов, инструмента
840355,11
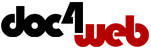
Нравится материал? Поддержи автора!
Ещё документы из категории транспорт :
Чтобы скачать документ, порекомендуйте, пожалуйста, его своим друзьям в любой соц. сети.
После чего кнопка «СКАЧАТЬ» станет доступной!
Кнопочки находятся чуть ниже. Спасибо!
Кнопки:
Скачать документ